表面工程化学镀Word文件下载.docx
《表面工程化学镀Word文件下载.docx》由会员分享,可在线阅读,更多相关《表面工程化学镀Word文件下载.docx(16页珍藏版)》请在冰豆网上搜索。
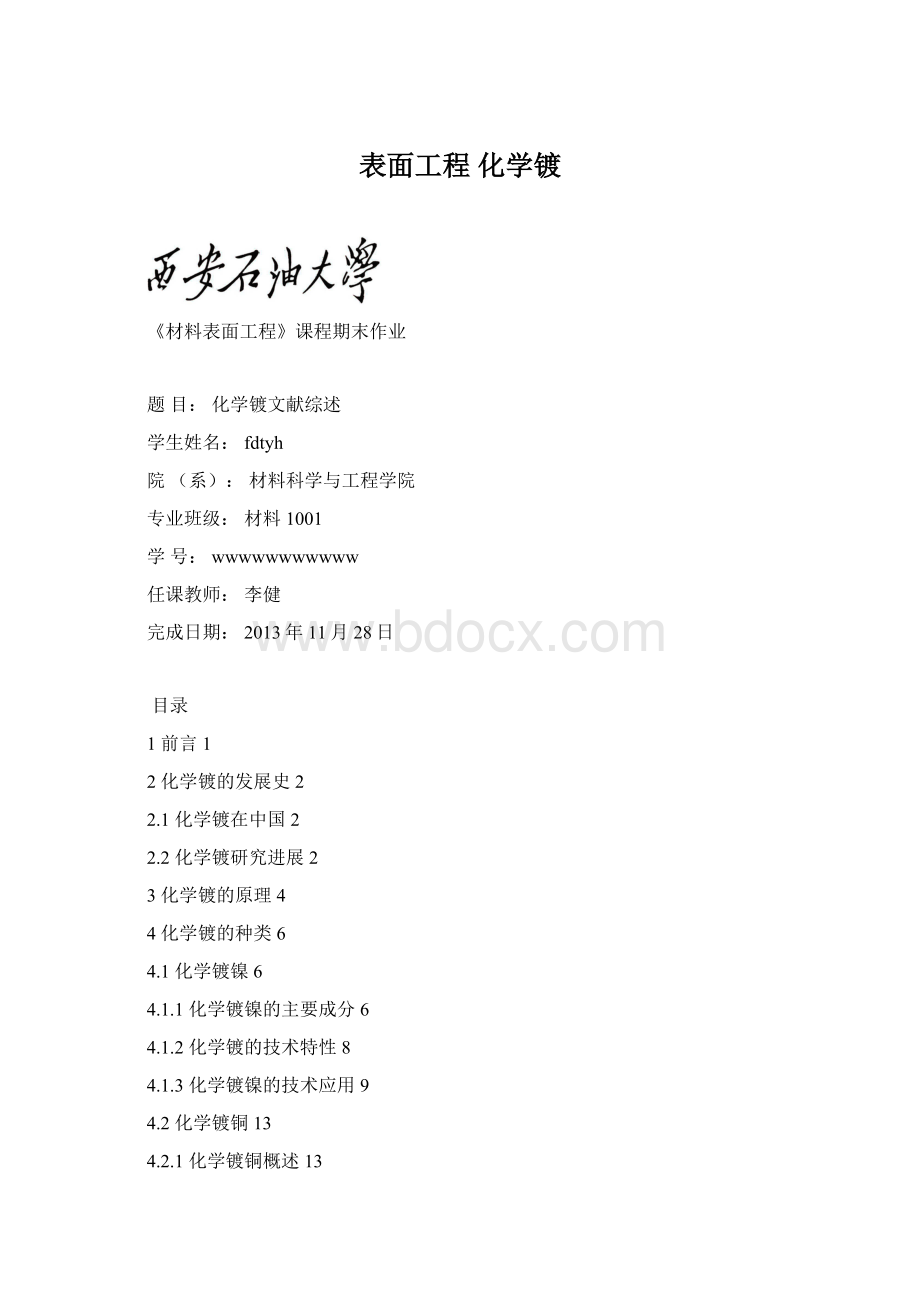
4.1.1化学镀镍的主要成分6
4.1.2化学镀的技术特性8
4.1.3化学镀镍的技术应用9
4.2化学镀铜13
4.2.1化学镀铜概述13
4.2.3化学镀铜的用途14
4.2.4化学镀铜的应用及优势14
4.3化学镀其他金属15
4.3.1化学镀银15
4.3.2化学镀金15
4.3.3化学镀钴15
4.3.4化学镀钯15
5总结16
6参考文献17
1前言
化学镀(ChemicalPlating)又称无电解镀(ElectrolessPlating),只在无外加电流的状态下,借助合适的还原剂,使镀液中的金属离子还原成金属,并沉积到表面的一种镀覆方法。
化学镀技术历史悠久,以往由镀层的性能和溶液较昂贵等方面的原因,工业化应用受到较大的限制。
自20世纪70年代以来,化学镀在镀层结合力、直接镀取光亮镀层和镀液的使用寿命等方面得到了突破性进展,使成本大幅降低,因此在工业上得到越来越广泛的应用。
2化学镀的发展史
2.1化学镀在中国
80年代,欧美等工业化国家在化学镀技术的研究,开发和应用得到了飞跃发展,平均每年有15–20%表面处理技术转为使用化学镀技术,使金属表面得到更大的发展,并促使化学镀技术进入成熟时期。
为了满足复杂的工艺要求,解决更尖端的技术难题,化学镀技术不断发展,引入多种合金镀层的化学复合技术,即三元化学镀或多元化学镀技术,得到了一些成果。
例如在Ni-P(镍—磷)镀层中,引入SiC或PTFE的复合镀层比单一的Ni-P镀层有更佳的耐磨性及自润滑性能。
在Ni-P(镍—磷)镀层中引入金属钨,使到Ni-W-P(镍—钨—磷)镀层进一步提高硬度,在耐磨性能方面得到很好的效果。
有Ni-P(镍—磷)镀层中引入铜,使Ni-Cu-P镀层较好的耐蚀性能。
还有Ni-Fe-p(镍—铁—磷)、Ni-Co-p(镍—钴—磷)、Ni-Mo-p(镍—钼—磷)等镀层在电脑硬碟及磁声记录系统中及感测器薄膜电子方面得到广泛的应用。
化学镀技术由于工艺本身的特点和优异性能,用途相当广泛。
中国在80年代才开始在化学镀方面进行探讨,国家在1992年分布了国家标准(GB/T13913——92),称之为自催化镍——磷镀层。
中国已将化学镀技术广泛用在汽车工业、石油化工行业、机械电子、纺织、印刷、食品机械、航空航太、军事工业等各种行业,由于电子电脑、通讯等高科技产品的应用和迅速发展,为化学镀提供了广阔的市场。
2000年以后,一方面由于国家注重环保,另一方面中国的工业发展了对金属表面处理要求提高了,加快了化学镀这一技术的发展,国家的高新技术目录也新增了化学镀。
化学镀虽然在中国的起步比较晚,但近年发展相当快,有些性能的技术指标完全可以与欧美的化学镀媲美,加上价格低、适应中国企业的工艺流程,发展前景备受注目。
2.2化学镀研究进展
近年来,世界发达国家利用化学镀工艺技术进行材料表面镀覆平均每年以12%-15%的速度递增。
起初化学镀只限于镀覆镍、铜和金,它们占表面镀覆的半数以上。
后来随着化学镀技术的优越性逐渐被人们认识,研究和发展了钯、铂、银、钴等的化学镀工艺技术,并已经逐步工业化。
现在多元合金、复合材料的化学镀,无论从种类范围和镀覆规模都在大力开发之中。
虽然我国起步较晚,但也处于迅速发展阶化学镀中,金属的沉积和在基底表面上的镀覆过程不同于电镀,工艺过程无需外界供给电能,而是依赖于镀液中发生的氧化还原反应将欲镀覆金属离子还原为单质而沉积在基底表面。
镀层的性质与化学镀液的组成、配方、化学镀的工艺条件,以及镀层的化学组成和微观结构等均有密切的关系。
化学镀层具有高的致密度、薄厚均一,具有良好的抗腐蚀性和耐磨损、好的可焊性、高的硬度、低的摩擦系数。
根据需要的不同,可以分别镀覆出具有非磁性的磁性的镀层。
鉴于它有众多的优越性,在发达国家中,化学镀工艺技术已经渗透工农业生产和高科技的各个领域,应用十分广泛。
我国随着经济建设的高速度发展,化学镀也在各个领域逐步发展;
如塑料的化学镀、电子工业中陶瓷化学镀镍电容器,石油仪器制造工业中化学镀镍内衬、耐酸泵中的耐酸部件及耐腐蚀的阀门等。
化学镀工艺的形成与理论的完善也只有近20-30年的历史。
它的问世追溯于1946年美国电化学协会(AES)第34届年会上Abneor和GraceRiddell报告了他们在电镀镍时,为了避免惰性阳极发生氧化而在镀槽内加入还原剂次亚磷酸钠后,发现阴极沉积的镍量多于按照法拉第(M.Faraday)电解定律所计算的,一年以后的另一次年会上,他们首次较全面地报告了利用还原剂还原镍离子的化学方法镀覆镍时,温度、镀液的化学组成、pH值等各种参数与所得镀覆层组成间的关系。
此后,该领域新观点、新工艺不断涌现,由此也产生了许多专利。
为了区别于电镀而将该工艺起名为化学镀或无电镀、自催化镀(electrolessplating,auto-catalyticchemicalplating)。
化学镀逐步达到和电镀并驾齐驱,两种工艺技术相辅相成。
3化学镀的原理
化学镀就是在不通电的情况下,利用氧化还原反应在具有催化表面的镀件上,获得金属合金的方法。
与电镀相比,化学镀技术具有镀层均匀、针孔小、不需直流电源设备、能在非导体上沉积和具有某些特殊性能等特点。
另外,由于化学镀技术废液排放少,对环境污染小以及成本较低,在许多领域已逐步取代电镀,成为一种环保型的表面处理工艺。
在美、英、日、德等国,其工业产值正以每年15%的速度递增。
它广泛地应用于机械、电子、塑料、模具、冶金、石油化工、陶瓷、水力、航空航天等工业部门,是一项很有发展前途的高新技术。
化学镀是一种新型的金属表面处理技术,该技术以其工艺简便、节能、环保日益受到人们的关注。
化学镀使用范围很广,镀金层均匀、装饰性好。
在防护性能方面,能提高产品的耐蚀性和使用寿命;
在功能性方面,能提高加工件的耐磨导电性、润滑性能等特殊功能,因而成为全世界表面处理技术的一个发展。
化学镀是一种不需要通电,依据氧化还原反应原理,利用强还原剂在含有金属离子的溶液中,将金属离子还原成金属而沉积在各种材料表面形成致密镀层的方法。
化学镀常用溶液:
化学镀银、镀镍、镀铜、镀钴、镀镍磷液、镀镍磷硼液等。
目前以次亚磷酸盐为还原剂的化学镀镍的自催化沉积反应,已经提出的理论有“原子氢态理论”、“氢化物理论”和“电化学理论”等。
在这几种理论中,得到广泛承认的是“原子氢态理论”。
化学镀原理
M2++2e(由还原剂提供)--->
M
在化学镀中,溶液内的金属离子是依靠得到所需的电子而还原成相应的金属。
例如,在酸性化学镀镍溶液中采用次磷酸盐作还原剂,它的氧化还原反应过程如下:
Ni2++2e--->
Ni(还原)
(H2PO2)-+H2O--->
(H2PO3)-+2e-+2H+(氧化)
两式相加,得到全部还原氧化反应:
Ni2++(H2PO2)-+H2O--->
(H2PO3)-+Ni+2H+
还原剂的有效程度可以用它的标准氧化电位来推断。
由上述可知,次磷酸盐是一种强还原剂,能产生一个正值的标准氧化一还原电位。
但不应过分地信赖E°
值,因为在实际应用上,由于溶液中不同离子的活度、超电位和类似因素的影响,会使E°
值有很大的差异。
但氧化和还原电位的计算仍有助于预先估算不同还原剂的有效程度。
若全部标准氧化还原电位太小或为负值,则金属还原将难以发生。
化学镀溶液的组成及其相应的工作条件必须是反应只限制在具有催化作用的制件表面上进行,而溶液本身不应自发地发生还原氧化作用,以免溶液自然分解,造成溶液很快失效。
如果被镀的金属(如镍、钯)本身是反应的催化剂,则化学镀的过程就具有自动催化作用,使上述反应不断地进行,这时,镀层厚度也逐渐增加,获得一定的厚度。
除镍外,钴、铑、钯等都具有自动催化作用。
对于不具有自动催化表面的制件,如塑料、玻璃、陶瓷等非金属,通常需经过特殊的预处理,使其表面活化而具有催化作用,才能进行化学镀。
化学镀与电镀比较,具有如下优点:
①不需要外加直流电源设备。
②镀层致密,孔隙少。
③不存在电力线分布不均匀的影响,对几何形状复杂的镀件,也能获得厚度均匀的镀层;
④可在金属、非金属、半导体等各种不同基材上镀覆。
化学镀与电镀相比,所用的溶液稳定性较差,且溶液的维护、调整和再生都比较麻烦,材料成本费较高。
化学镀工艺在电子工业中有重要的地位。
由于采用的还原剂种类不同,使化学镀所得的镀层性能有显著的差异,因此,在选定镀液配方时,要慎重考虑镀液的经济性及所得镀层的特性。
目前,化学镀镍、铜、银、金、钴、钯、铂、锡以及化学镀合金和化学复合镀层,在工业生产中已被采用。
4化学镀的种类
4.1化学镀镍
4.1.1化学镀镍的主要成分
化学镀镍化学镀中发展最快的一种。
镀液一般以硫酸镍、乙酸镍等为主盐,次亚磷酸盐、硼氢化钠、硼烷、肼等为还原剂,再添加各种助剂。
在90℃的酸性溶液或接近常温的中性溶液、碱性溶液中进行作业。
以使用还原剂的不同分为化学镀镍-磷、化学镀镍-硼两大类。
镀层在均匀性、耐蚀性、硬度、可焊性、磁性、装饰性上都显示出优越性。
主盐:
化学镀镍溶液中的主盐就是镍盐,一般采用氯化镍或硫酸镍,有时也采用氨基磺酸镍、醋酸镍等无机盐。
早期酸性镀镍液中多采用氯化镍,但氯化镍会增加镀层的应力,现大多采用硫酸镍。
目前已有专利介绍采用次亚磷酸镍作为镍和次亚磷酸根的来源,一个优点是避免了硫酸根离子的存在,同时在补加镍盐时,能使碱金属离子的累积量达到最小值。
但存在的问题是次亚磷酸镍的溶解度有限,饱和时仅为35g/L。
次亚磷酸镍的制备也是一个问题,价格较高。
如果次亚磷酸镍的制备方法成熟以及溶解度问题能够解决的话,这种镍盐将会有很好的前景。
还原剂:
化学镀镍的反应过程是一个自催化的氧化还原过程,镀液中可应用的还原剂有次亚磷酸钠、硼氢化钠、烷基胺硼烷及肼等。
在这些还原剂中以次亚磷酸钠用的最多,这是因为其价格便宜,且镀液容易控制,镀层抗腐蚀性能好等优点。
络合剂:
化学镀镍溶液中的络合剂除了能控制可供反应的游离镍离子的浓度外,还能抑制亚磷酸镍的沉淀,提高镀液的稳定性,延长镀液的使用寿命。
有的络合剂还能起到缓冲剂和促进剂的作用,提高镀液的沉积速度。
化学镀镍的络合剂一般含有羟基、羧基、氨基等,常用的络合剂有柠檬酸钠、酒石酸钠等。
在镀液配方中,络合剂的量不仅取决于镍离子的浓度,而且也取决于自身的化学结构。
在镀液中每一个镍离子可与6个水分子微弱结合,当它们被羟基,羧基,氨基取代时,则形成一个稳定的镍配位体。
如果络合剂含有一个以上的官能团,则通过氧和氮配位键可以生成一个镍的闭环配合物。
在含有0.1mol的镍离子镀液中,为了络合所有的镍离子,则需要含量大约0.3mol的双配位体的络合剂。
当镀液中无络合剂时,镀液使用几个周期后,由于亚磷酸根聚集,浓度增大,产生亚磷酸镍沉淀,镀液加热时呈现糊状,加络合剂后能够大幅度提高亚磷酸镍的沉淀点,即提高了镀液对亚磷酸镍的容忍量,延长了镀液的使用寿命。
不同络合剂对镀层沉积速率、表面形状、磷含量、耐腐蚀性等均有影响,因此选择络合剂不仅要使镀液沉积速率快,而且要使镀液稳定性好,使用寿命长,镀层质量好。
缓冲剂:
由于在化学镀镍反应过程中,副产物氢离子的产生,导致镀液pH值会下降。
试验表明,每消耗1mol的Ni2+同时生成3mol的H+,即就是在1L镀液中,若消耗0.02mol的硫酸镍就会生成0.06mol的H+。
所以为了稳定镀速和保证镀层质量,镀液必须具备缓冲能力。
缓冲剂能有效的稳定镀液的pH值,使镀液的pH值维持在正常范围内。
一般能够用作PH值缓冲剂的为强碱弱酸盐,如醋酸钠、硼砂、焦磷酸钾等。
稳定剂:
化学镀镍液是一个热力学不稳定体系,常常在镀件表面以外的地方发生还原反应,当镀液中产生一些有催化效应的活性微粒——催化核心时,镀液容易产生激烈的自催化反应,即自分解反应而产生大量镍-磷黑色粉末,导致镀液寿命终止,造成经济损失。
在镀液中加入一定量的吸附性强的无机或有机化合物,它们能优先吸附在微粒表面抑制催化反应从而稳定镀液,使镍离子的还原只发生在被镀表面上。
但必须注意的是,稳定剂是一种化学镀镍毒化剂,即负催化剂,稳定剂不能使用过量,过量后轻则降低镀速,重则不再起镀,因此使用必须慎重。
所有稳定剂都具有一定的催化毒性作用,并且会因过量使用而阻止沉积反应,同时也会影响镀层的韧性和颜色,导致镀层变脆而降低其防腐蚀性能。
试验证明,稀土也可以作为稳定剂,而且复合稀土的稳定性比单一稀土要好。
加速剂:
在化学镀溶液中加入一些加速催化剂,能提高化学镀镍的沉积速率。
加速剂的使用机理可以认为是还原剂次磷酸根中氧原子被外来的酸根取代形成配位化合物,导致分子中H和P原子之间键合变弱,使氢在被催化表面上更容易移动和吸附。
也可以说促进剂能起活化次磷酸根离子的作用。
常用的加速剂有丙二酸、丁二酸、氨基乙酸、丙酸、氟化钠等。
其他添加剂:
在化学镀镍溶液中,有时镀件表面上连续产生的氢气泡会使底层产生条纹或麻点。
加入一些表面活性剂有助于工件表面气体的逸出,降低镀层的孔隙率。
常用的表面活性剂有十二烷基硫酸盐、十二烷基磺酸盐和正辛基硫酸钠等。
稀土元素在电镀液中可以改善镀液的深镀能力、分散能力和电流效率。
研究表明,稀土元素在化学镀中同样对镀液的镀层性能有显著改善。
少量的稀土元素能加快化学沉积速率,提高镀液稳定性,镀层耐磨性和搞腐蚀性能。
化学镀镍磷合金镀层,硬度可高达HV1000,相当HRC69,具有很高的耐磨性和耐腐蚀性,镀层结合力好、厚度均匀。
镀速快,可达20μm/小时。
外国部分研究
Iron/cobaltcore-shellcompositepowdersweresuccessfullyfabricatedbychemicalplatingprocessusinghydrazineasreductant.Theeffectsofreactivetemperature,PHvalue,concentrationofhydrazineandcomplexingagentandFecontentontheweightgainofFepowderwerestudied.Theresultsshowthatthechemicalplatingcannotcarryoutwhenthereactivetemperaturelowerthan70°
CorpH<
12.5.TheweightgainofFepowderdecreaseswiththeincreasingofconcentrationofcomplexingagent.Fecontenthaslittleeffectonthechemicalplating.Theoptimumparametersofchemicalplatingidentifiedthroughmeasuringtheweightgainofpreparedpowdersareasfollows:
reactivetemperatureof78°
C,pHvalueof13,concentrationofcitricacidof15g/L,andhydrazineconcentrationof45mL/L.ThepropertiesofpreparedpowderswithComassfractionof20%werecharacterizedbymeansofXRD,SEMandEDS,itisfoundthatCo/Fecore-shellcompositepowderownsdensificationandhomogeneousmicrostructure.
4.1.2化学镀的技术特性
1、耐腐蚀性强:
该工艺处理后的金属表面为非晶态镀层,抗腐蚀性特别优良,经硫酸、盐酸、烧碱、盐水同比试验,其腐蚀速率低于1cr18Ni9Ti不锈钢。
2、2、耐磨性好:
由于催化处理后的表面为非晶态,即处于基本平面状态,有自润滑性。
因此,摩擦系数小,非粘着性好,耐磨性能高,在润滑情况下,可替代硬铬使用。
3、光泽度高:
催化后的镀件表面光泽度为LZ或▽8-10可与不锈钢制品媲美,呈白亮不锈钢颜色。
工件镀膜后,表面光洁度不受影响,无需再加工和抛光。
4、表面硬度高:
经本技术处理后,金属表面硬度可提高一倍以上,在钢铁及铜表面可达Hv570。
镀层经热处理后硬度达Hv1000,工模具镀膜后一般寿命提高3倍以上。
5、结合强度大:
本技术处理后的合金层与金属基件结合强度增大,一般在350-400Mpa条件下不起皮、不脱落、无气泡,与铝的结合强度可达102-241Mpa。
6、仿型性好:
在尖角或边缘突出部分,没有过份明显的增厚,即有很好的仿型性,镀后不需磨削加工,沉积层的厚度和成份均匀。
7、工艺技术高适应性强:
在盲孔、深孔、管件、拐角、缝隙的内表面可得到均匀镀层,所以无论您的产品结构有多么复杂,本技术处理起来均能得心应手,绝无漏镀之处。
8、低电阻,可焊性好。
9、耐高温:
该催化合金层熔点为850-890度
4.1.3化学镀镍的技术应用
航空航天
航空航天工业为化学镀镍的使用大户之一,比较突出的应用实例是:
美国俄克拉荷马航空后勤中心,自1979年以来,以及西北航空公司自1983年以来均采用化学镀镍技术修复飞机发动机零件。
普拉特-惠特尼公司的JT8D喷气发动机虽已经停产,可是迄今仍有上千台这种发动机在波音727和麦道DC-9飞机上使用,原因是:
一种高磷,压应力的化学镀镍技术用于修复JT8D六种型号的喷气发动机的叶轮,确保了这种发动机的重新使用。
在航空发动机的涡轮机或压缩机的叶片上,通常镍磷合金化学镀厚为25~75um,以防止燃气腐蚀,其疲劳强度的降低比电镀铬少25%。
俄克拉荷马航空后勤中心采用超厚层化学镀镍修复飞机零件,镀厚达275~750um。
原采用电镀工艺时的返工率达50%,采用化学镀镍后合格率达90%以上,可见取得了明显的经济效益。
飞机上的辅助发电机(APU)经化学镀镍后,其寿命提高3~4倍。
重达8.2吨的涡轮发动机的主轴承面经化学镀镍100um,以防止开机和停机所引起的振动损坏。
为减轻重量,航空工业大量使用铝合金件,经化学镀镍表面强化后不仅耐蚀、耐磨,而且可焊,如冲程发动机的活塞头经化学镀镍后提高了使用寿命。
其他还有钛合金件、铍合金件均采用低应力和压应力的化学镀镍表面保护等措施。
镍+铊+硼三元合金化学镀(NTB)被指定为普拉特-惠特尼喷气发动机上160多种零件的表面强化工艺,以抗擦伤和微动磨损,例如:
NTB化学镀用于喷气发动机主轴密封。
美国空军要求发动机制造商提供具有4000次战术周期,此时磨损量达0.178mm,如此必须拆卸重修,经NTB化学镀后主轴密封面磨损显著降低,经4000次战术周期后的磨损量约为0.008mm。
宇航系统广泛使用着金属光镜,其基体为强度高、重量轻的铍或铝,经专用化学镀镍表面强化,这种含磷量为12.2%~12.7%的化学镀镍可抛光至9?
,如此高的精度在需要低惯性的宇宙空间里,有着卓越的性能。
中国的化学镀工业虽然起步较晚,但自九十年代以来经过各科研单位的不懈努力,现已拥有成熟的工艺和经验,在中国洛阳已建成飞机零件化学镀镍加工流水线。
汽车工业
解决使用乙醇、汽油混合燃料问题是汽车工业的发展趋势之一,使用混合燃料,除性能问题之外,还产生了燃油系统的腐蚀问题。
在巴西,使用乙醇作为燃料,应用化学镀镍技术保护锌压铸件,如汽化器免遭腐蚀已成为工艺规范。
在美国,当广泛用甲醇或甲醇和汽油混合燃料时,汽车工业势必应用化学镀镍作为汽化器、燃油泵送系统的表面保护手段。
差速器行星齿轮是汽车的一个重要零件,镀上25um厚的化学镀镍层以提高耐磨性,有的汽车制造厂在轴上采用聚四氟乙烯复合化学镀镍层工艺,这种复合镀层既有一定的硬度,又兼有好的润滑性能,提高了轴的使用寿命。
汽车工业利用化学镀镍层非常均匀的优点,在形状复杂的零件上,如齿轮、散热器和喷油嘴上采用化学镀工艺保护。
镀上10um左右的化学镀镍层的铝质散热器具有良好的钎焊性。
齿轮上化学镀后尺寸误差十分容易地保持在±
0.3~0.5um。
而如果采用电镀工艺,则必须镀后还要进行机加工才能达到合格的工差范围。
用在喷油器上的化学镀镍层,可以提供良好的抗燃油腐蚀和磨损性能。
通常,燃油腐蚀和磨损会导致喷油孔的扩大,因此喷油量增大,使汽车发动机的马力超出设计标准,加快发动机的损坏。
化学镀镍层可以有效地防止喷油器的腐蚀、磨损,提高发动机的可靠性和使用寿命。
化学工业
化学工业应用研究化学镀镍技术代替昂贵的耐蚀合金以解决腐蚀问题,以便改进化学产品的纯度,保护环境,提高操作安全性和生产运输的可靠性,从而获得更有利的技术经济竞争能力。
化学镀广泛地应用于大型反应容器的内壁保护。
当初非常引人关注的应用实例是:
1955年美国通用运输公司(GATX)采用化学镀保护槽车内壁,防止苛性碱的腐蚀。
如今,化学镀镍技术已经获得长足的进步,能够在多种化工腐蚀环境下提供可靠的保护。
应用化学镀镍最为量大面广的是阀门制造业。
钢铁制造的球阀、闸阀、旋阀、止逆阀和蝶阀等等,经高磷化学镀镍25~75um,可提高耐腐蚀性和使用寿命。
化工用泵化学镀镍的效果也同样显著。
在苛性碱腐蚀条件下工作的阀门,应采用镀层含磷量1%~2%的低磷化学镀镍。
因为在苛性碱腐蚀条件下,低磷化学镀镍层的年腐蚀速率约为2.5um,优于中磷或高磷化学镀镍层。
化学镀镍层在强氧化性酸,如浓硝酸、浓硫酸等介质中不耐蚀。
尽管在盐酸中的腐蚀速率低于奥氏体不锈钢,耐蚀性仍然是不够的。
因此,对于上述强酸介质,或者可能水解生成上述强酸的介质中,不适于使用化学镀镍层。
碳钢紧固件镀上25~50um厚的高磷化学镀镍层,代替不锈钢紧固件,既克服了奥氏体不锈钢的应力腐蚀开裂问题,又节省了大量费用。
生产低密度聚乙烯的压力容器内壁25um,以防止铁污染和因此所造成的聚乙烯变色。
如果采用不锈钢建造,其价格大约是化学镀方法的两倍。
石油天然气
石油和天然气是化学镀镍的重要市场之一,油田采油和输油管道设备广泛地采用化学镀镍技术。
典型的石油和天然气工业腐蚀环境为井下盐水、二氧化碳、硫化氢,温度高达170~200℃,并伴有泥沙和其他磨粒冲蚀等等,腐蚀环境相当恶劣。
低碳钢油气管道在如此苛刻的条件下,仅有2~3个月的寿命。
经过50~100um厚的高磷化学镀镍层保护之后,其腐蚀速率降低到与哈氏合金相当的程度。
考虑到耐蚀合金价格昂贵,从性能价格比上讲,碳钢管道采用化学镀镍保护的技术经济性能最好。
泵壳、叶轮和出口管道等油气用泵零件,根据腐蚀环境不同,经化学镀镍镀厚25~75um不等,防腐蚀效果优良。
抽油泵化学镀镍是一种理想的应用实例:
在西得克萨斯油田,经化学镀镍保护的抽油泵,寿命长达4年以上,同样末加保护的抽油泵的寿命不超过6个月。
化学镀镍层耐蚀耐磨,而且由于化学镀镍层的高度均