微成型的研究现状与展望文档格式.docx
《微成型的研究现状与展望文档格式.docx》由会员分享,可在线阅读,更多相关《微成型的研究现状与展望文档格式.docx(8页珍藏版)》请在冰豆网上搜索。
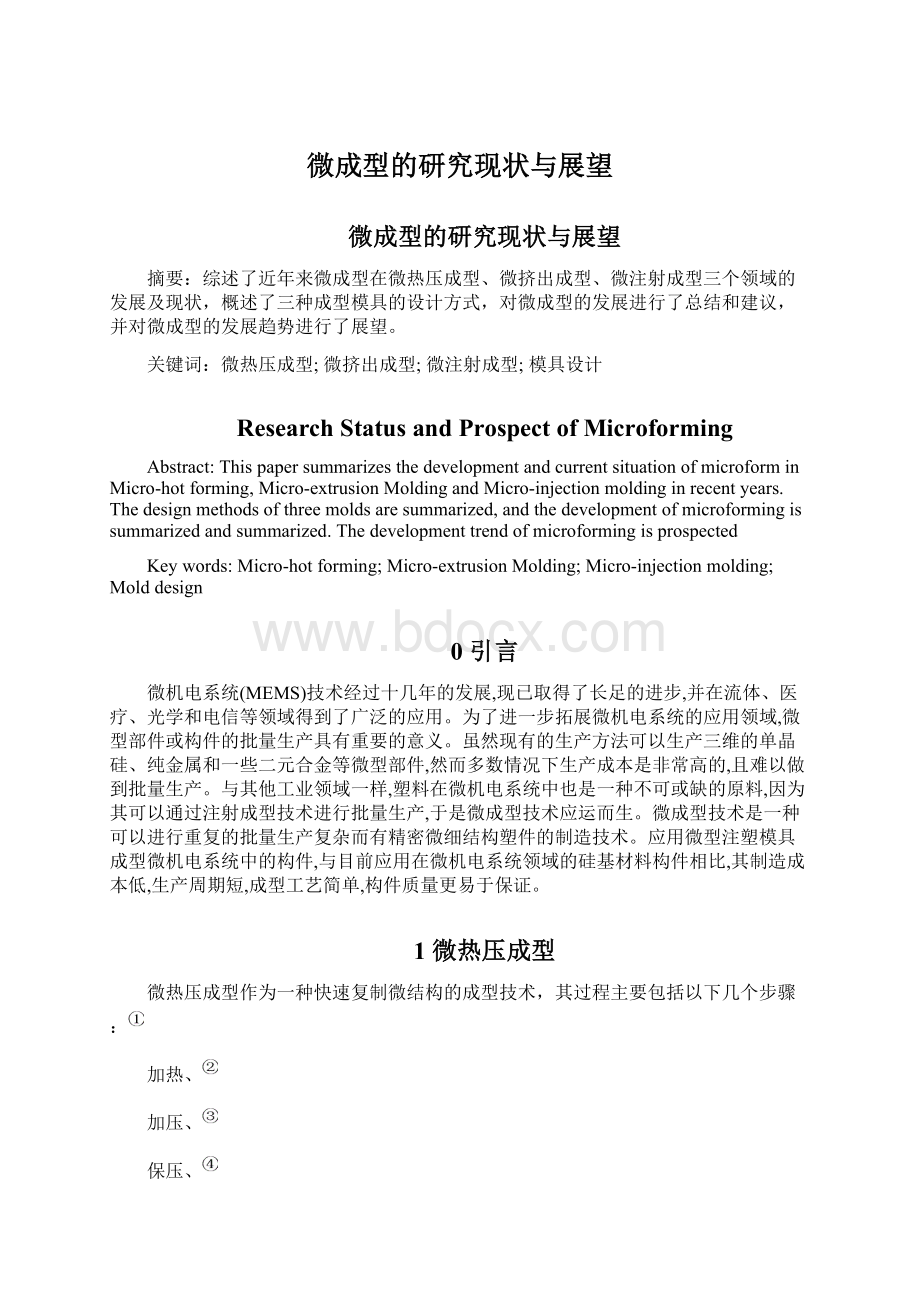
应用微型注塑模具成型微机电系统中的构件,与目前应用在微机电系统领域的硅基材料构件相比,其制造成本低,生产周期短,成型工艺简单,构件质量更易于保证。
1微热压成型
微热压成型作为一种快速复制微结构的成型技术,其过程主要包括以下几个步骤:
加热、
加压、
保压、
冷却脱模。
首先将聚合物放到模具上,把基板加热到温度使其软化,恒温一段时间,施加一定的压力把模具上微结构图案复制到聚合物上,保压一段时间,最后冷却脱模,获得所需制品。
热压成型示意图如图1所示:
图1微热压成型示意图
1.1微热压成型的研究
微热压成型方法最早是在1972年由Ulrich[1]提出发现的。
他利用热压法将宽为7um,深3.5um的微通道压印到高聚物PMMA上,从而制备出光波导元件,但后续研究较少。
接着到1995年美籍华裔科学家chou[2]率先使用热压技术应用于纳米尺度,成功将点阵列微结构复制到PMMA薄膜上,之后很多学者针对热压过程中材料的充填高度、变形特征及产品质量等方面进行了研究。
PanLi-Wei[3]等研究了时间、温度、压力对微透镜成型高度的影响,得出聚合物粘度以及表面张力对微透镜的曲率和成型高度有直接关系;
压力对微透镜的曲率影响较小,但成型高度随着压力增大呈线性增长趋势;
温度对微透镜高度及曲率影响大且复杂;
随时间延长,在相同温度、相同压力下,微透镜的充填高度呈非线性增加,最后趋于平缓。
奥克兰大YaoDong-gang[4]等人研究聚合物在非等温情况下微流道,实验结果表明,当微流道的宽厚比一定时,随着宽度变大,聚合物在成型中逐渐出现爬壁行为,原因是聚合物热压过程快于热传递过程,靠近壁面处聚合物温度较高,充填高度高于中心部位。
浙江大学贺永[5]对聚合物在热压过程中的理论基础和装备技术等方面做了很多工作。
研究了聚合物在微热压成型过程中,模具结构和工艺参数对基板流动形貌、微结构复制精度以及应力分布等影响;
同时也探究了聚合物在小变形脱模阶段,基板的应力场随脱模速率、脱模角度的变化规律。
吉林大学左春柽[6]教授通过热压法成型微流控芯片,研究工艺参数对芯片微结构的影响,同时通过数值仿真模拟芯片在热压过程中的变化规律,得到微结构尺寸与工艺条件之间的相互关系
1.2微热压成型模具设计
微热压成型需要首先在模具表面加工微结构,然后经过热压将微结构转印到聚合物基体。
微热压成型过程大多在专门设计的热压装备上进行。
国外的热压装备研究较早,一些科研院所和公司已经研制出各自的成型试验设备,而且部分已经实现产业化。
国内的一些高校对热压工艺及装备开展了研究,如大连理工大学开发出的RYJ系列热压机及微流控芯片全自动加工系统。
在热压成型装备研究中,合理设计参与压印的微热压模具尤为重要。
平压式热压工艺中,模具被平整地压在基板表面,在一次工艺周期中转印复制出模具上所有特征结构。
步进式热压工艺中,一个小面积模具在大面积基板的一个位置完成转印之后移动到下一个位置,重复进行热压过程。
连续滚压式热压转印工艺成型可以分为辊子—平和辊子—辊子滚压成型2类。
设计辊子—平板热压模具有2种方法:
①加工出圆形辊子模具,接着使模具在聚合物基板上滚压成型;
②将平板模具放在基板上,然后用光滑辊子滚压平板模具。
设计辊子—辊子热压模具时,可以首先将微结构加工在板状模具表面,然后弯曲固定
在辊子上,但难以避免地出现连接缝隙,造成周期性的不连续压印。
因此,可以将微结构直接设计在金属辊子表面,对于保证滚压成型质量更为有利。
微热压成型过程,脱模前需要降低模具温度以保证填充模腔的聚合物充分固化。
冷却阶段会增加成型时间,因此可以通过提高模具的热循环速率来提高微热压成型效率和质量。
例如,美国麻省大学的FAGAN等[7]设计了一种传送带式的变温滚压模具。
传动带模具和聚合物薄膜预热后进入压印系统,充分冷却后脱模进入下一个热压循环,不仅保证了较高的滚压效率,而且提高了微结构复制精度。
采用微热压方法成型大深宽比微结构时,往往需要自动脱模装置。
常规自动脱模装置可能会导致聚合物翘曲变形,因此可以通过设计新型的脱模机构提高微热压制品质量。
例如,浙江大学的贺永等[5]设计了气动脱模机构集成到自行设计的热压装备中,并且通过压印试验验证了该脱模装置的有效。
2微挤出成型
微挤出成型一般是指成型截面尺寸微小(外径≤ϕ2mm)、壁厚为微米量级型材的微成型技术。
由于微挤出制品通常尺寸小、中空内腔、截面形状复杂、壁厚不均匀、几何精度要求高,传统挤出模设计理论不再完全适用于微挤出成型模具设计,同时对模具微小成型流道的加工也提出了更高的要求。
典型的微挤出成型如图2所示。
图2微挤出成型过程示意图
2.1微挤出成型的研究
G.Hetsroni等[7]研究了直径在15~4000μm范围内,圆形、矩形、三角形、梯形等截面微流道中流体的流动行为和热传递现象,研究结果表明,微流道的长径比和流体的雷诺数是影响流体热传递的主要因素,而一定量的热量耗散将导致流体产生不稳定流动,但G.Hetsroni等没有讨论流体的速度波动对层流和湍流的影响。
W.B.Young[8]研究了聚合物熔体在具有微结构型腔中的流动行为,并提出了一种简化的二维数值模型,用于估算聚合物熔体在微流道中的填充能力,并显示填充能力与成型工艺和型腔几何结构之间的关系,虽然W.B.Young提出的二维模型能较好的显示聚合物熔体在具有微结构型腔中的填充能力与成型工艺和型腔几何结构的关系,但用二维模型指导实际中三维模具的设计必然会存在一定的局限性。
徐斌等[9]在分析聚合物熔体的壁面滑移机理和微通道中尺度效应对壁面滑移影响的基础上,建立了微通道的壁面滑移模型,并通过数值模拟的方法,计算出了直径为0.5mm的微通道中在不同剪切速率下的滑移速度和压力降。
L.Meng等[10]研究了微流道直径大小对PP熔体黏度和壁面滑移速度的影响,结果表明,微流道中熔体的流动行为有别于宏观尺度流道中的流动行为,且微流道直径的大小对熔体的流动行为也存在明显影响。
2.2微挤出成型模具设计
在聚合物微挤出成型过程中,模具流道结构是否合理将直接影响制品的成型质量。
模具结构参数设计不合理,可能会导致制品内筋开裂、壁厚不均、熔体破裂、扭曲、翘曲等缺陷。
聚合物微挤出模具设计主要包括模具结构形式设计、非对称流道的流动平衡设计、成型段流道设计和注气系统设计等。
(1)模具结构形式设计。
根据聚合物熔体挤出成型方向和挤出机轴线的关系,微挤出模具主要分为直通式、十字头和补偿式3种结构形式。
直通式模具的成型流动方向与挤出机轴线方向相同。
这种结构可保证聚合物熔体的流动平衡,但是容易产生熔接痕,且模具的注气孔难以加工和密封。
大连理工大学的赵丹阳等[11]和北京化工大学的邹维东等[12]分别设计了无注气系统和具有分路注气系统的直通式双腔挤出模。
十字头模具的挤出成型流动方向与挤出机轴线呈一定角度。
这种结构的优点是制品不会产生熔接痕,注气孔也相对容易加工和密封,然而其转角处的非对称流道结构较难实现熔体流动平衡。
补偿式模具流道过2次转向后,模具成型段流道与挤出机轴线平行。
这种结构通过第2次转向来补偿第1次转向引起的熔体流动不平衡,但模具结构复杂,生产中较少使用。
(2)模具非对称流道的流动平衡设计。
聚合物熔体流动平衡是指在挤出模出口各个区域获得均匀的挤出压力和挤出速度。
国外的微挤出模设计主要是凭借多年试错法获得宝贵的经验,被国Guill、Maillefer、M&
S、Putnam等公司所垄断。
随着计算机仿真技术的快速发展,在模具制造前进行挤出流动模拟及模具结构优化,成为提高挤出模设计质量和效率的有效手段。
华南理工大学的龚炫[13]基于数值模拟进行了微挤出模的流动平衡性设计。
但是由于仿真程的大量简化假设,其计算结果通常与真实的成型过程存在较大差异,还需要建立流动平衡理论。
(3)模具成型段流道设计。
微挤出模成型段流道设计主要包括成型段长度设计和成型段截面设计2个方面。
模具成型段长度较短容易引起显著的挤出胀大,但是成型段长度的增加会导致挤出机压力显著增大而降低生产效率、增加能耗。
大连理工大学的靳国宝等[14]根据力学平衡原理推导了狭缝形、圆形和非规则形3种口模的微挤出模成型段长度模型。
成型段截面设计的合理性是决定微挤出制品精度的重要因素。
具有复杂截面形状的多腔微管具有各向异性的粘弹性挤出胀大,难以通过传统模具设计方法实现模具成型段截面形状的准确设计。
由于制品形状的杂性,对模具成型段截面的设计多基于数值分析和优化设计理论实现。
例如,
(4)注气系统设计。
对于具有中空型腔的微小型材,微挤出模需要引入微细注气系统。
但微细注气系统容易与模具流道发生干涉,增大了模具结构的整体布局难度。
大连理工大学的靳国宝等[15]指出,为实现不同型腔注气参数的分路控制,多腔微挤出模具应该采用十字头模具的结构形式,沿流动方向在芯棒上加工注气孔,以避免流道结构与注气系统的干涉。
另外,为了降低注气孔的加工难度,应当将注气孔设计成沿流动方向直径不断减小的阶梯状结构
3微注射成型
微注射一般是指用来成型尺寸为微米级、质量为毫克级的制品的注射方法,微型制件很难用普通的加工方法成型,因此,微细加工技术在微注射成型技术中具有重要意义。
由于当今社会对微型部件和系统的日益重视,使得微注射成型技术在过去短短几年内便有了很大的发展。
典型的微挤出机如图3所示。
图3微挤出机的结构示图
1-模板;
2-模具模板;
3-塑化单元;
4-驱动装置;
5-柱塞;
6-喷嘴;
7-型腔
3.1微挤出成型的研究
微注射成型与传统注射成型相比具有自身的一些特点,如高速注射和微尺度效应等。
因此工艺参数对微结构特征的复制和微制品质量的影响因素与传统注射成型不完全相同。
工艺参数对微结构特征的复制质量仍然是研究热点。
Chu等[16]利用柱塞式微注射机成型POM、HDPE、PC三种材料的微制品。
自行开发数据采集系统记录工艺参数随时间的变化。
充型实验中,以毫秒为计时单位,使用短射试验同时跟踪注射压、流道压力和柱塞位置化。
采用DOE技术研究了充型和保压阶段,6种工艺参数的影响。
在充型阶段,注射速度是影响柱塞速度和注射压力的主要因素。
而模具和熔体温度的影响与材料和注射机设置有关。
庄俭等[17]对500um和100um微流道的型腔进行工艺实验均值分析,结果表明,成型工艺参数的影响顺序有所不同。
随着塑件微结构特征尺寸的减小,注射压力和模具温度对填充率的影响明显增强;
熔体温度对填充率的影响程度有所增加;
注射行程对填充率的影响程度有所降低;
保压压力和保压时间对填充率的影响相对不明显。
卢振等[18]也研究了影响制品质量的因素,认为高的模具温度和注射压力有利于微结构部分的填充,注射前模具抽真空不仅可以提高微结构的填充性能,还可以改善其表面质量。
其他学者的相关研究[18]也得到了同样的结论。
填充完好的聚丙烯微结构表面粗糙度取决于硅模具表面粗糙度值。
工艺优化对于微注射成型也非常重要。
Attia等[19]利用DOE方法,研究5个工艺参数对制品重量和重量变化这两个质量标准的影响。
结果表明,保压压力,熔体温度和注射速度对制品重量影响最大;
而仅注射速度,对重量变化有显著影响。
注射速度对两个指标影响不同,它的影响正比于重量变化,反比于制品重量。
利用满意度函数寻找一个复合因子,能够在满足规格质量同时满足重量变化。
最后提出了一种针对多重质量标准优化微注射成型工艺条件的统计学方法。
3.2微注射成型模具设计
微注射成型模具的加工精度及成本决定了制品的成本以及大规模生产的可能,因此设计具有合理结构的模具是获得高质量注射制品的关键。
微注射成型模具设计关键技术主要包括变温模具设计、真空排气系统设计、脱模机构设计等。
(1)变温模具设计。
在微注射成型过程中,因模具型腔表面积与体积之比较大,导致熔体温度在填充阶段变化范围大,严重影响制品的成型质量和成型周期,因此,微注射模通常需要设计模具变温系统。
目前,模具变温系统主要有感应加热变模温系统、电热水冷变模温系统等。
例如,美国佐治亚理工学院的YAO等[20]设计的高频感应加热变模温系统,能在5s内使型腔温度从室温提高到240℃,极大地缩短了成型周期。
(2)真空排气系统设计。
由于微模具表面加工精度高,当模具合模后,动模与定模之间的间隙极小,型腔内所残留空气和熔体释放的气体很难从型腔间隙排出,影响制品成型质量和熔体填充率,微模具通常设计真空排气系统。
目前,真空排气方式主要是通过将型腔周围进行密封,在分型面上开设排气通道,再用真空泵将气体从型腔内抽出[21]。
(3)鉴于微制品具有质量轻、壁薄、强度低的特点,传统的脱模机构容易使微结构变形,甚至损坏,严重影响制品的成型质量。
为使制品顺利脱模且保证其成型质量,微注射模需要设计适合微制品结构特点的脱模方式。
研究学者针对不同微制品结构的特点,采用不同的脱模设计机构。
大连理工大学于同敏等[22]设计一种微制品间接脱模机构,该机构的推杆推出作用力不直接作用在制品上,而是直接推出尺寸相对较大的流道,再通过流道和浇口带动制品脱模,从而保证了制品尺寸精度和表面质量。
4总结与展望
微成型技术的发展趋势由于微成型技术是新兴的技术领域,许多基础理论还不够完善,微成型工艺也不够成熟,还需要进一步探索和研究。
同时,机电一体化技术、计算机网络技术等相关技术的不断发展为微注射成型技术的开展提供许多新思路和新方向。
因此,微成型技术的进一步发展还面临着许多挑战,主要表现在如下几方面。
(1)进一步完善新材料的微成型工艺研究,发展适用性广的新型材料。
在微成型选材时,不但要考虑制品的精度要求,还要考虑到材料的可模塑性和脱模性能。
因此,需要开发粘度低、热稳定性更好的材料。
(2)探索新的材料塑化方式,解决现有塑化方式带来的诸多问题,达到整洁、高效塑化注射材料的目的。
(3)研究和改进微成型工艺和成型技术,确保得到合格的制品。
比如温度控制和检测系统、抽真空装置等还有待进一步改进。
(4)微塑机的高精度、高效率产品检测单元的探索为微型注塑机提供可靠的性能测试和评价标准。
(5)新型微型模具制造手段和工艺方法还需不断丰富和完善,目前对三维微注塑模具型腔的加工还是主要依靠光刻技术阁。
(6)智能化和网络化微射成型的开发应用研究,使微型注塑机在计算机和网络的帮助下实现多元控制和远程在线控制生产。
断发展与完善,研究适合微型注塑模具和微型注塑机的成型理论和制造方法,寻找和研制适合微型塑件生产的塑料原料,开发相应的检测元件、装置和技术,扩展其应用范围,已成为目前和今后该领域研究的重点。
参考文献
[1]UlrichR,WeberHP,ChandrossEA,etal.EmbossedOpticalWaveguides[J].AppliedPhysicsLetters,1972,20(6):
213-215.
[2]InzeltG,PineriM,SchultzeJW,etal.Electronandprotonconductingpolymers:
recentdevelopmentsandprospects[A].InAsmeTurboExpo:
TurbineTechnicalConference&
Exposition[C],2000;
2403–2421.
[3]ShenXJ,PanLW,LinL.Microplasticembossingprocess:
experimentalandtheoreticalcharacterizations[J].Sensors&
ActuatorsAPhysical,2002,97(02):
428-433.
[4]YaoD,VirupakshaVL,KimB.Studyonsqueezingflowduringnonisothermalembossingofpolymermicrostructures[J].PolymerEngineering&
Science,2005,45(45):
652-660.
[5]贺永.聚合物微热压过程理论及其装备技术研究[D].浙江大学2007.
[7]G.Hetsroni,A.Mosyak,E.Pogrebnyak,etal.Fluidflowinmicro-channels[J].InternationaljournalofHeatandMassTransfer,2005,48(10):
1982~1998.
[6]文伟力.聚合物微流控芯片的制作、检测及仿真研究[D].吉林大学2007.
[8]W.B.Young.Simulationofthefillingprocessinmoldingcomponentswithmicrochannels[J].MicrosystemTechnologies,2005,11(6):
410~415
[9]徐斌,王敏杰,于同敏,等.微尺度效应对聚合物熔体壁面滑移影响的研究[J].材料工程,2008,(10):
16~20(+24).
[10]L.Meng,D.Wu,A.Kelly,etal.Experimentalinvestigationoftherheologicalbehaviorsofpolypropyleneinacapillaryflow[J].JournalofAppliedPolymerScience,2016,133(22):
43459.
[11]金翼飞.聚合物微挤出流变学理论与试验研究[D].大连:
大连理工大学,2010:
79-97.
[12]邹维东.小截面精密异型管材挤出模拟与实验研究[J].工程塑料应用,2006,34(3):
54-57.
[13]龚炫.微管挤出机头流道数值模拟及微管成型研究[D].广州:
华南理工大学,2009:
33-54.
[14]靳国宝.面向介入医疗导管的聚合物微挤出模具设计制造技术与工艺研究[D].大连:
大连理工大学,2014:
38-94.
[15]靳国宝,王敏杰,赵丹阳,等.聚合物双腔微管挤出成型工艺试验研究[J].机械工程学报,2012,48(24):
19-27.
[16]ChuJS,KamalMR,DerdouriS,etal.Characterizationofthemi-croinjectionmoldingprocess[J].Polym.Eng.Sci.,2010,50(6):
1214-1225.
[17]庄俭,吴大鸣,赵中里,等.微注射成型工艺的实验研究[J].化工学报,2009,60(4):
1040-1045.
[18]卢振,张凯锋,微注射成形制品质量影响因素分析[J].机械工程学报,2009,45(12):
295-299.
[19]AttiaUM,AlcockJR.Optimisingprocessconditionsformultiplequalitycriteriainmicro-injectionmoulding[J].Int.J.Adv.Manuf.Technol.,2010,50(5-8):
533-542.
[20]YAODG,KIMERLINGTE,KIMB.High-frequencyproximityheatingforinjectionmoldingapplications[J].PloymerAngineeringandScience,2006,46(7):
938-945.
[21]徐斌,王敏杰,卢玉斌,等.抽真空对微型制品成型质量影响[J].材料科学与工艺,2011,19(4):
20-23.
[22]杨铎,刘冲,徐征,等.微注塑成型模具设计与制造技术研究进展[J].塑料工业,2010,38(10):
1-5.