精益生产及精益工具大纲分享.docx
《精益生产及精益工具大纲分享.docx》由会员分享,可在线阅读,更多相关《精益生产及精益工具大纲分享.docx(15页珍藏版)》请在冰豆网上搜索。
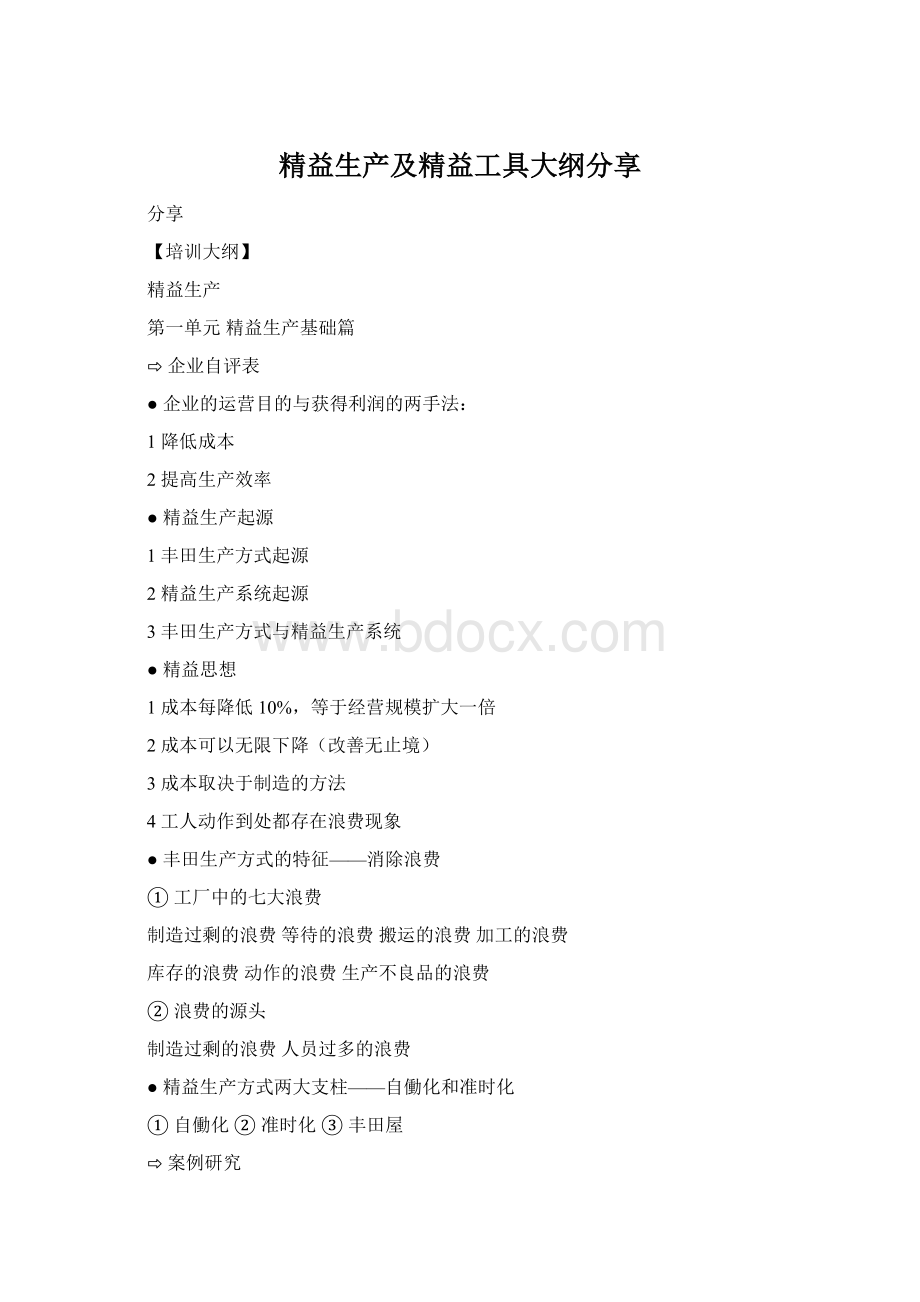
精益生产及精益工具大纲分享
分享
【培训大纲】
精益生产
第一单元精益生产基础篇
⇨企业自评表
●企业的运营目的与获得利润的两手法:
1降低成本
2提高生产效率
●精益生产起源
1丰田生产方式起源
2精益生产系统起源
3丰田生产方式与精益生产系统
●精益思想
1成本每降低10%,等于经营规模扩大一倍
2成本可以无限下降(改善无止境)
3成本取决于制造的方法
4工人动作到处都存在浪费现象
●丰田生产方式的特征——消除浪费
①工厂中的七大浪费
制造过剩的浪费等待的浪费搬运的浪费加工的浪费
库存的浪费动作的浪费生产不良品的浪费
②浪费的源头
制造过剩的浪费人员过多的浪费
●精益生产方式两大支柱——自働化和准时化
①自働化②准时化③丰田屋
⇨案例研究
⇨模拟游戏1:
推动-流动-拉动(观察小结)
第二单元精益生产工具篇
●工具一:
5S——现场改善基础
①5S真经②5S应用③工作场地有序安排(录像)
●工具二:
目视化管理(VisualManagement)
①周期性信息展示②3M的实时监控
③基于“三现主义”的异常管理④目视化管理(录像)
●工具三:
问题解决
①5Why②PDCA循环③快速响应异常管理六要素
●工具四:
全员生产维护(TPM)
①TPM的概念和目的②五大对策和八大策略
③自主维护保养的七个层次④TPM实施的十大步骤
●工具五:
标准化作业
①准作业条件②标准作业三要素(TT,WS,SWIP)
●工具六:
现场改善-Kaizen
①改善步骤②改善ECRS手法③改善突破法—现场改善的利器(录像)
●工具七:
防错(Pokayoke)
①追求零缺陷②品质三不政策③自働化三原则
●工具八:
看板(Kanban)
①看板的种类与工作原理②看板的实施前提③看板六原则
●工具九:
快速换模(SMED原理)
①明确划分内外部因素②将内部因素转化成外部因素
③理顺留下的内部因素④理顺所有外部因素
⑤使用工件更换器(快速夹紧装置或完全去除夹紧装置)
⑥进行平行作业⑦去除调整/校准过程
●工具十:
价值流图析(ValueStreamMapping)
①确定产品系列②现状图绘制
③未来状态图绘制④计划与实施
⇨案例研究
⇨模拟游戏2:
推动-流动-拉动(观察小结)
第三单元精益生产总结篇
●精益改善失败原因
●精益改善-终身之旅
1精益改善路线图
2精益改善的顺序
3精益改善的合理化建议
4精益改善实施绩效指标
5精益企业4项基本标准
6精益企业5项基本特征
⇨案例研究
⇨模拟游戏3:
推动-流动-拉动(观察小结)
精益工具一:
5S-工作场地有序安排
第一部分5S基础篇
一、现场5S改善科学推行
二、现场管理与市场意识
三、5S推行关系与成效
四、5S活动原则与误区
五、生产经理心智修炼
六、建立最优素质模型
七、专业能力与管理提升
八、5S管理技巧分享
第二部分5S推进篇
一、整理推进快刀斩乱麻
二、倡导提领法则
三、整理不良的对策与分析
四、整顿的推进重点
五、目视化定置管理
六、动作经济原则
七、彻底杜绝污染源
八、点检与点检通道优化
九、清洁的最有效推进
十、制度与标准化模型建立
十一、修养的推进重点
十二、标杆推进
十三、团队作战
十四、责任重于泰山
十五、常见不安全现状与行为分析
第三部分5S方法篇
一、现场可视化管理要点
二、3级标准管理方法
三、可视化的合理分类
四、颜色管理与视觉原理
五、企业文化与基础设施
六、看板管理三大要素
七、识别管理大全
八、识别与形迹管理
第四部分5S督导篇
一、建立5S推行组织
二、拟定推进方针和目标
三、拟定计划和实施方法
四、5S推行过程
五、样板区的选择与总结推广
六、5S绩效考核
七、确定评比方法
八、5S纠正与预防
第五部分持续改进篇
一、5S推进中易存在问题
二、问题意识与五现手法
三、PDCA与SDCA递进
四、改善与创新
五、日常管理与改善
六、激发创新思维
七、标准化
八、防错法
九、提案改善活动
第六部分5S延伸篇
一、5S与制造业精益生产LP模式
二、5S与设备维护管理TPM的推行
三、办公室5S
四、文件5S
五、会议5S
六、5S问与答
精益工具二:
目视化管理
第一部分目视化管理
1.什么是目视控制
2.目视化管理的定义和作用
3.目视化Vs.目视化管理
4.案例:
目视化管理
第二部分目视化管理的实施步骤
5.练习活动:
目视化管理
第三部分目视化管理的应用
精益工具三:
问题解决
一、如何看待问题
二、什么是问题?
三、问题的类别
四、如何发现问题
5why分析方法
五、问题解决的步骤
PDCA循环
六、快速响应异常管理六要素
精益工具四:
全员生产维护
第一模块、TPM基础篇
1.TPM的起源和定义
2.TPM的历史沿革
3.TPM在设备维护体制中的定位
①TPM现场设备管理自主维修
②全系统生产维修体制
4.TPM的3个“全”
①总体全效率(盈利能力)
②设备一生的全维护系统
③全员参与
5.人员在TPM中所要起的作用
①使零停机成为现实
②消除浪费源
③提高操作技能,增加机器的性能
6.TPM的5大支柱
①最高设备综合效率
②全系统预防维修
③所有部门全体参加
④从领导到每个员工
⑤小组活动动机管理
7.开展TPM的意义
第二模块、TPM准备篇
1.TPM的目标
2.如何识别生产设备性能
①跟踪七种设备浪费的方法
②综合设备效率计算(OEE)
③设备使用率
④人工效率计算
⑤合格品率计算
⑥企业中的21种损失(LOSS)
3.课堂练习
第三模块、TPM震撼新解篇
11.新一代TPM给企业带来变革的启示
①淡化分工,专业覆盖,工作边界模糊化
②从岗位分工报酬制走向能力报酬制
③企业凝聚力和企业文化作用巨大
④充分发挥教育培训功能,建设学习型和教育型组织
⑤新团队精神的发挥
2.TPM定义新解
①全面效益管理
②全面生产管理
③全面完美生产
④全面生产维护与管理
3.TPM五大支柱新解
①综合效益最大化
②寿命周期损失最小化
③横向全员:
所有部门参与
④纵向全员:
从上至下投入
⑤小组活动:
TPM的基础和细胞
4.TPM和TQM,JIT,ISO的关系
TQM:
设备是质量的保障JIT:
零库存要全员控制
TPM:
设备保障体系ISO:
需要深入细化的执行
5.安全与全员生产维护
6.换型改善流程步骤
①区分外部和内部换型
②内部换型外部化
③缩短内部换型时间
④改善外部换型,缩短总时间
⑤改善后)内部、外部换型作业标准化,确保在规制时间内完成内部换型
7.五个基本的改善领域
①通过消除六大浪费来提高设备效率(团队完成)
②建立维护小团队(遵循七步法)
③质量保证
④维护部门制定维护计划
⑤通过教育训练提高技能水平
8.五大对策
①维护良好规范的基本条件
②遵循适用的操作程序
③复原坏旧设备
④明确和改进设计问题
⑤提高操作和维护技能
第四模块、TPM实施篇
1.TPM推进的三阶段
①准备发动阶段——创造适宜的环境,概念开发,人员培训,全面发动
②落实推进阶段——制订目标,建立组织,制订计划,难题解决,创造榜样
③评价改进阶段——制定标准,检查评估,找出不足,改进提高。
TPM小组活动和激励机制
TPM的评估
2.设备备件管理
3.全员参与管理
4.自主维护的7个层次
5.个别改善的10个步骤
6间接部门效率化
7.中国企业TPM活动推行的25大法宝
精益工具五:
标准化作业
第一部分标准化
一、什么是标准化?
二、标准化的目的
三、标准化的重要性
四、何时需要进行标准化?
五、小组讨论
六、标准化的应用
第二部分标准化作业
一、标准化作业的定义
二、标准化作业的前提条件
三、标准化作业的特征
四、标准化作业的内涵
五、作业标准与持续改进
六、持续改进三要素
1.节拍时间
2.作业顺序
3.标准在制品存量
七、案例分析
第三部分标准化作业的制定
一、制定标准化作业5步
二、制定标准化作业工具
三、操作练习
1.制作标准作业组合表
2.制作标准作业票
第四部分标准化作业的期望
精益工具六:
现场改善
°第一篇体系篇
一、现场管理的五个基本问题
1.我的客户是谁?
2.客户对我的期望是什么?
3.我如何满足客户这些期望?
4.怎样知道客户满足与否?
5.客户不满足时如何改进?
二、现场管理(督导)人员的角色
1.资源输入的管理(人力、材料和机器)2.晨集(晨会、班前会TOP5)
3.最佳质量保证生产线证书4.制定挑战性目标
5.现场督导人员的假想管理功能
三、现场改善:
低成本管理方法
1.现场改善的主要理念
2.现场管理的金科玉律
①当问题(异常)发生时,要先去现场②检查现物
③当场采取暂行处置措施④发掘真正原因并将之排除⑤标准化以防止再发生
四、现场改善屋:
在现场达成QCD
°第二篇基础篇
一、现场改善屋的基础
1.学习型组织2.提案制度及品管圈3.建立自律
二、如何建立学习型组织
1.学习型组织包括五项要素2.团队的构成要素3.高效团队的四部曲
4.员工激励和员工自主10要素5.现场组织架构6.管理4层次
三、消除现场不良的工具
1.不合格品产生原因2.不合格品的类别3.丰田作业员的作业标准小册子
4.最高管理部门每月检讨重点5.最佳质量保证生产线证书
°第三篇维持篇
一、三条基本原则
1.环境维持2.消除Muda3.标准化
二、标准化
1.什么是标准化作业?
2.标准化作业的三要素
3.现场改善的三大表单4.标准化作业的主要特征
5.标准化生产的基本目标6.标准作业应包含的内容
三、提案建议制度及质量圈
1.建立自律
2.现场管理的3书1表
①作业手顺书②作业指导书③作业要领书QC工程表
°第四篇改善篇
一、财务报表“一点通”
二、七种浪费
三、持续改进活动
1.问题解决2.推进作业改善的四个阶段
四、降低现场的成本
1.成本管理2.降低成本必须实施7项活动
3.实践现场改善的10项基本规则4.重要的改善工具——检查表
5.建立改善机制6.IE的追求
五、现场改善七大重点
°第五篇实施篇
一、现场改善活动的实施步骤
1.选择工作任务;2.收集数据和现状把握;
3.应对收集到的数据进行深入分析,以便能弄清事情的真正背景及原因;
4.在分析的基础上研究对策;5.导入、执行对策;
6.观察并记录采用对策后的影响;
7.修改或重新制订标准,以避免类似问题的再次发生;
8.检查从步骤1到7的整个过程,据以引入下一步的行动。
二、走入现场:
两天期的改善
1.两天期的改善目标
2.主要的改