坐式型材液压机飞剪机的设计文档格式.docx
《坐式型材液压机飞剪机的设计文档格式.docx》由会员分享,可在线阅读,更多相关《坐式型材液压机飞剪机的设计文档格式.docx(17页珍藏版)》请在冰豆网上搜索。
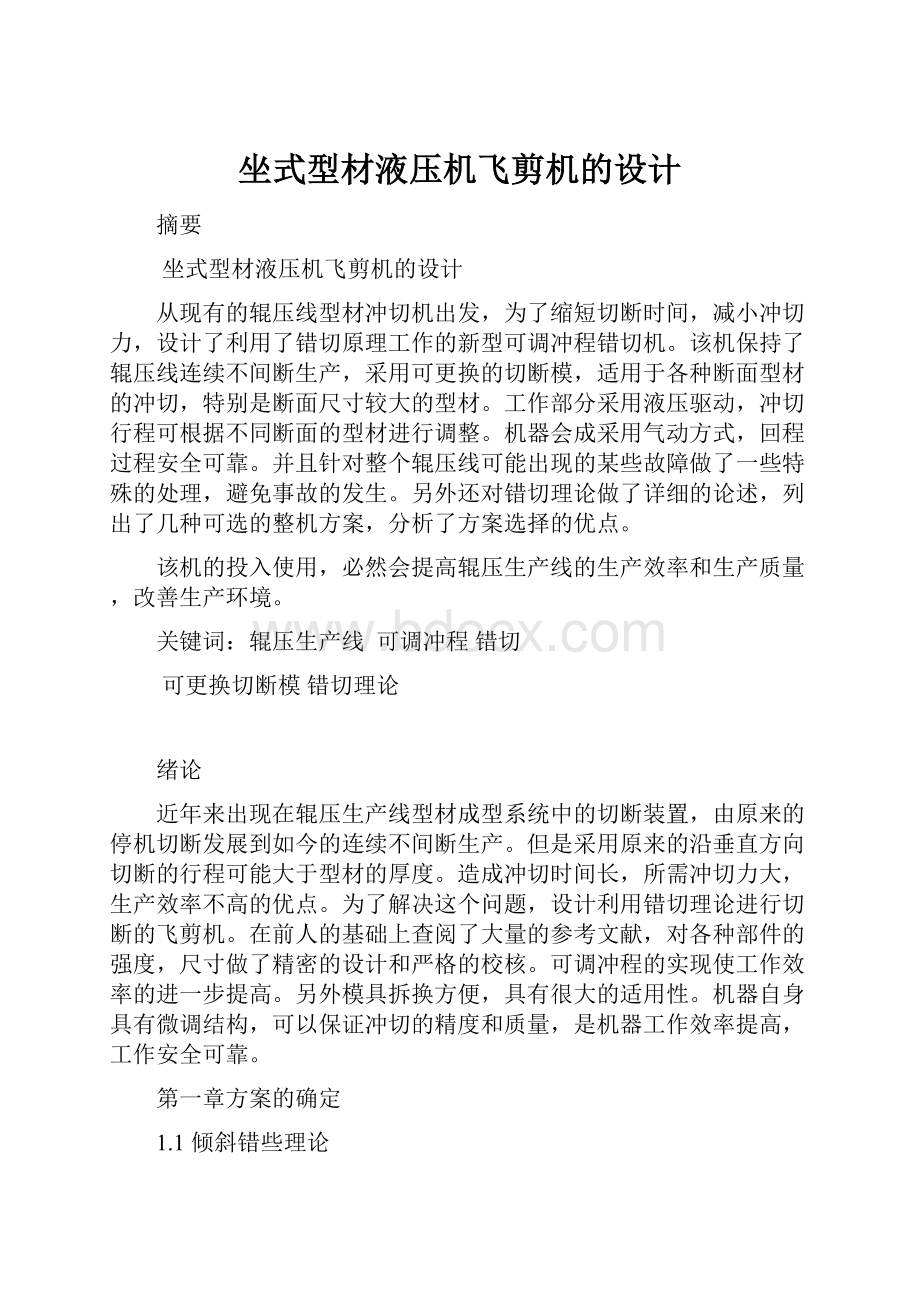
α=26.56。
在此处使倾斜角为30。
,主要是考虑切向力不能太大,即斜滑块对右侧模块作用力不能太大,否则会造成冲切困难,右侧磨损严重。
1.1.2倾斜错切的优点:
由以上分析可知,倾斜错切比垂直错切的行程要小得多,冲切力也大大减小,由此达到节省时间提高效率优化设备,节约能源的目的。
1.2几种不同设计方案的提出
1.2.1线上作业与独立作业
a.线上作业即指冲切机在辊压线工作台上工作。
不另加专门的工作台,其回程装置也放在辊压线上,如图1.3所示:
图1.3线上作业简图
b.独立作业:
指冲切机在辊压线外,单独成为一台上机器,有专门的工作台,回程装置放在自己的工作台上,如图1.4所示:
图1.4独立线上作业
第一种方式,即线上作业的冲切机多为冲切截面积较少,冲切力不大的型材。
外型尺寸较小占地空间小
第二种方式,冲切机由于型材在一定的高度,要自行设计工作台,使机器造价较高,占地面积较大,但可以冲切型材横截面积大,形状复杂,厚度也较厚,冲切力可以很大。
合理的设计可以使机器外形紧促,工作可靠。
根据设计任务所绘图纸的要求,截面积较大,形状复杂,需要的冲切力也较大,因此既定了方案选择了独立作业方式。
1.2.2直立机身和倾斜机身
a.直立机身的外形如图1.5所示:
这种形式的冲切机在随型材移动时,导轨两侧受力均匀,在加上铜垫,摩擦不至于过大,不用过多的考虑导轨的特殊形式。
另外容易实现可调冲程,节约资源,提高效率
b.倾斜式冲切机,外形如图1.6所示
这种冲切在运动时两侧受力不均,尤其当轨道以上重量较大时,磨损很严重。
如果所需的冲切力不大,整个机器体积减小,重量减轻,在优化导轨设计的基础上可采用此种方式。
另外此放式不易实现可调冲程。
根据任务书所给的条件,冲切型材横截面积较大,需要的力也较大,且还要实现可调冲程,因此采用直立机身。
1.2.3停机共作和连续共作
a.停机工作是指在切断型材时整个辊压线停止共组,等待冲压机切断型材时在开机运转。
这种方式开关机频繁,浪费时间,工作效率较低。
b.连续方式指切断机随型材一起运动,在切断型材后,在气压缸的作用下回到原位,为下一次冲切做准备,这种方式使整个生产线不间断共作,提高生产率。
1.2.4
a.气动回程指冲切机在完成切断后由气缸作用回到原位
b.机械回程即利用机械运动带动冲切机回到原位,比如用齿轮和链条回程。
a和b相比较气动回程和机械回程相比可靠性较好,设计简便
压回气缸和拉回气缸
指冲切机在完成切断后由气缸作用回到原位。
可以分为两种情况,第一种如图1.7机器被气缸拉回原位
第二种方式如图1.8,有气缸压回原位
两种方式均可采用,效果相同,但前者可以节省厂房空间和方便工作人员操作。
故采用拉力回程较好。
综上以上的分析结合设计的要求最后决定采用:
直立机身、独立工作台、连续工作、气动拉回的整机设计方案。
该方案综合了上述的优点,对局部细节做了一些优化,结构简图如1.9所示:
第二章冲切机工作部分的设计
2.1冲切驱动装置——油缸的设计和计算
2.1.1计算剪切力
给定的型材为0Cr18Ni9查机械手册第一卷3.1-87的0Cr18Ni9的σb=520N/mm2
由公式:
τ=0.8*σb=416N/mm2
τ材料的抗剪强度
σb材料的抗拉强度
给定型材最大横截面积为F0=132.83mm2
取F0=150mm2
由公式P0=F*τ=150*416=62.4KN
P=K*P0=1.1*62.4=68.8KN
其中:
P0理论剪切力
P实际剪切力
K安全系数
2.1.2计算活塞杆的实际用力
由图2.1列平衡方程为:
F=P1Cos300+P2Sin300+μP2Cos300
μF+μP2Sin300+P1Sin300=P2Cos300
F活塞杆实际作用力
P1弹簧作用力
μ摩擦系数
P2右侧滑块的支持力
Cos300=0.866Sin300=0.5
解得:
F=90.552KN
P2=0.755*68.6=53.165KN
2.1.3缸筒的设计
确定缸筒与端盖的连接形式为拉杆连接,其优点为缸体最易加工,易装卸。
结构通用性大,但重量加大,外型尺寸大。
查液压气动技术手册P574选择后端带螺纹孔式MX6
缸筒的材料选为45号钢。
强度刚度足够,足以保证在最高的压力下不至于变、弯曲。
磨损少,可焊接性好。
缸筒设计:
a.液压杆理论作用力P
P=F/ηt=90.552/0.85=106.53KN
其中ηt
液压缸工作效率取为0.9(液压气动技术手册)
b.缸筒的内径D:
D=
-3m=
-3m=122.8mm
p供油压力由经验取为9MPa
P1液压缸理论推力N
据标准系列取D=125mm
选取缸筒外径D1=146mm
缸筒的外形如图2.2所示,
其中S为油缸的行程此处取为30mm
2.1.4活塞杆的设计
有手册表19-6-5取d=70mm
校核公式σ=
=27.68N/mm2
[σ]=100N/mm2
其中
[σ]为许用拉应力[σ]=100~110N/mm2
取为100N/mm2
校核通过
图2.1计算活塞杆的实际作用力图
图2.2缸筒的外形简图
活塞杆的结构有手册表19-6-17,考虑实际要求定为图2.3所示形式
图2.3活塞杆的前端形式
2.1.5活塞
活塞的结构形式采用整体式,O型密封
活塞与活塞杆做成整体式,形式如图2.7所示
活塞与活塞杆均采用45号钢
运动速度由表19-6-4续表,速度过低可能造成爬行,液压缸不能正常工作油缸内径选取Vmax=0.4m/s.最后取
V=0.1m/s在此速度下工作不用加缓冲装置
2.1.6导向套
活塞杆的导向套在液压缸有杆侧端盖内,用以对活塞杆的导向,内装有密封装置以保证缸筒由杆腔的密封。
外侧装有防尘圈,以防止活塞杆在后退时把杂质、灰尘及水分带到密封装置处,损坏密封装置,导向套结构选为轴套式。
形式如图2.7所示。
导向套由青铜制作,外形如图2.4所示
图2.4导向套外形图
2.1.7密封
油缸密封选用O型密封圈及Yx型密封圈,标准号分别为GB1235-76和Q12B248-77,位置如图2.7所示
2.1.8拉杆设计
拉杆的设计可以归结为受拉紧力和工作载荷作用的紧螺栓连接
F=P/4=10653.4/4=26.633KN
其中F工作载荷(单个螺栓所受),KN
P活塞杆作用力,N
据机械设计教材
当F有变化时,F//=(0.6~1.0)F取为0.7F
其中F//——剩余预紧力,KN
F//=0.7F=0.7*26.633=21.306KN
F0=F+F//=47.94KN
其中F0——螺栓总拉力,KN
d
2
其中[σ]——许用拉应力,取为240Mpa
d——拉杆直径mm
1.3——由第四强度理论得到的系数
d
=18.18mm
取四个拉杆直径为20mm,并确定其位置关系如图2.5
图2.5拉杆位置示意图
2.1.9油口尺寸的计算
有口包括有口孔和油口连接螺纹。
液压缸进出口可布置在端盖或缸筒上。
查表19-6-29进出油口M22
1.5
2.1.10油缸的固定方式
油缸用法兰固定在上横梁上,法兰用螺纹固定形式
螺钉为M24
30
图2.6法兰尺寸图
2.1.11油缸简图如图2.7油缸总质量约为40Kg
图2.7油缸
2.2模具部分的设计
2.2.1镶块的设计
镶块的结构形式如图2.8所示:
镶块的型孔采用电火花采用线切割加工,先在前端用铣刀铣出厚60mm的虚线框形状的孔洞。
而后剩余20mm用电火花加工,这样加工容易,成本减低,镶块用螺钉与滑块固定。
镶块重量约为2.17Kg
图2.8镶块
2.2.2斜滑块的设计
斜滑块左侧导轨基本不受力,所以将导轨宽度做的较小。
而右侧导轨受到较大的力,导轨较宽。
同时为了减小摩擦导轨两侧都要加铜衬,用开槽沉头不脱出螺钉固定在左右两个固定在模块上。
斜滑块在左右两模块中滑动,依靠下部弹簧的力量回程。
2.2.3滑块回程装置——弹簧的设计
(中国设计师下册表27-22圆柱螺旋压缩弹簧设计)
选取材料为碳素弹簧钢丝B级
P1:
未冲切时弹簧所受的力,等于弹簧所支持的滑块重量引起的K为安全系数1.2
P1=G*Cos300*K=20*9.8*0.866*1.2=203.7N
粗取D=20mmd=4mmC=
=5
查图27-3K为1.34
许用切应力由表27-13B查的σb=1520Mpa
由表27-12得[τ]=0.4*σb=603.8Mpa
弹簧刚度要求P/选取有效圈数为6.
查表27-6.G=79*103MpaG为剪切弹性模量
P/=
=
=52.67N/mm
试验载荷切应力:
Ts=1.2[τ]=1.2*608=729.6Mpa
试验载荷Ps=
Ts=916.37Mpa
弹簧在冲切时所受的力
P2=P1+P/
L=203.7+52.6
6=519.72Mpa<
916Mpa=Ps
即弹簧工作时未超过工作极限载荷Ps.弹簧不会破
设计合理
表2.1弹簧各参数
项目
单位
数据
最小工作载荷
N
P1=203.7N
工作行程L
mm
L=6
负载种类
Ⅱ类
端部形式
端部并紧并磨平,支撑圈为1圈
弹簧材料
碳素弹簧钢丝B级
弹簧丝直径d
4
弹簧中径D
20
旋转比C
C=
曲度系数K
1.34
有效圈数n
6
圈数n1
n1=n+2=6+2=8
自由高度H0
H0=nt+1.5d=6*5+1.5*4=36mm
工作极限载荷Ps
N
Ps=
弹簧刚度P/
P/=
=52.67N/mm
2.2.4滑动块
模具上部的滑动块是与活动衡量接触的部分,它在活动衡量上沿水平方向滑动,将斜滑块压下,使之在导轨中运动。
滑动块上有铜衬,用内六角螺钉与斜滑块相连,外形如图2.11所示:
图21.1滑块外形尺寸
2.2.5可调冲程垫块
实现可调冲程的方法是在模块加放调整垫块,当所冲切的型材厚度较厚,要求液压缸有较大的行程时,调整垫块应相应减薄。
其厚度为t=s-d
其中s——液压缸行程(固定),mm
d——考虑其他一些因素在内的液压缸所需工作行程,它保证型材被切断
当所冲切型材较薄,液压缸行程较小,就用较厚的垫块。
调整垫块用45号制成,放在后面长方形模块上,,一侧一块。
安装时用内六角螺钉拧紧在方型模块上。
2.2.6弹簧的支撑柱
为防止弹簧失稳,在弹簧中加入支撑柱,拧紧在下方三角块上。
有手册表11-1-7当D=18~30,取支撑柱与弹簧间隙为3
因此弹簧柱直径d/d/=D-2
3=20-6=14mm
三角块用内六角螺钉连接在过渡板上。
2.2.7模具部分的安装、固定
a.镶块的安装
镶块的安装有两种方案,第一种
4.2.1立柱的强度校核
立柱受到拉力作用这个拉力油缸的作用引起的。
油缸活塞杆理论作用力P=106.53KN而F=P/2=53.28KN
F即为拉杆所受的拉力
σ拉=F/S
[σ]
为立柱危险截面的面积
为许用拉应力
[σ]=0.35σs=355*0.35=124.25N/mm2
σ拉=F/As=117.8N/mm2
[σ]
拉伸强度核通过
2.2.7模具部分的安装和固定
a.镶块的安装
镶块的安装有两种方案,第一种是两镶块大端对大端,如图.2.12所示
图2.12镶块的安装方法
(一)
这种方式切断模接触面积大,剪切时模具两端受力不大,用M8的螺钉把镶块固定住就走够了.但这种方式也有缺点,即不好装拆,不宜调整两镶块的间隙.在冲切过程中间隙过大或过小都会直接影响冲切质量.
第二种是镶块小端对小端,如图2.13所示:
图2.13镶块安装方法
(二)
这种方式正好与第一种方法相反,由于剪切力对模具的小端影响不可忽略,因此必须用大螺钉将镶块固定住.但此种方式容易拆装,只要将外面的螺钉拧下即可.对于间隙的调整可以在一端加垫块来实现.因此选用第二种方式即可
图2.14模具装配关系
C.圆柱销的选定
由于冲切时,滑块对右侧的模块有压力,因此在固定模具时要用,用圆柱销来定位,并承受一定的压力.
圆柱销承受的压力力为2.1.2中计算出来的P2的反力.大小与之相等.粗略估计后初选为四个,据手册查销的强度计算公式:
τ=
[τ]
F横向力,N
D销的直径,mm
Z柱销数量
[τ]销的许用剪应力,Mpa,常用材料取[τ]=80Mpa
将此公式转变为:
=14.54mm选取销的直径为16mm
左侧模块受力不大,但考虑到定为作用,选用16的销两个。
因此总共6个销,另外还用5个M12的螺钉,将模具部分固定,如图2.15所示。
第三章运动部件的设计
为保证生产线的连续共作,冲切机必须随着生产线一起运动一段距离。
运动部件的设计包括导轨的设计和汽缸部件的设计。
3.1导轨
3.1.1导轨的设计有两种方案
第一种如图3.1所示
图3.1导轨方案的设计
(一)
这种导轨是分两部分加工的,加工后分别安装在两侧。
这一方案的优点是节省材料,安装方便。
缺点是分开安装之后就不能保证安装精度,而安装精度对材料的加工精度影响很大。
若装配时两者不在同一水平线上,机体在冲切的工程中会发生倾斜,使冲切过程受到影响。
导轨设计方案二如图3.2所示
这种方案的有缺点正好与第一种方案相反,虽然材料耗费量大,但能保证安装精度,满足冲切要求,因此最后选用第二种方案
再导轨上加上铜衬,以利于滑动,减小摩擦,连接在机体上的导轨架在导轨上滑动,导轨用内六角螺钉与调整板固定在一起。
3.1.2导轨长度的计算:
a.冲切时间:
t=
其中L冲切行程mm,此处为5mm
U油缸活运动速度m/s,在2.1.5中取为0.1m/s.
t=
=0.5s
导轨长度L1=U/*t
其中U/型材的运动速度m/s.给定为12m/min,即为0.2m/s
T运动总时间
t/回程时间s.模具随油缸一起回到初始位置。
此时间等于冲切时间0.5s.
t//油缸液压系统反映滞后s,取为1s.
T=t+t/+t//=0.5+0.5+1=2m/s
L1=U/*t=0.2*2=0.04m=40mm
由计算结果可知,导轨理论上只需要40mm.但由于冲切过程可能出现诸如未切断,机体随型材一起向前运动,