水泥粉磨技术Word下载.docx
《水泥粉磨技术Word下载.docx》由会员分享,可在线阅读,更多相关《水泥粉磨技术Word下载.docx(27页珍藏版)》请在冰豆网上搜索。
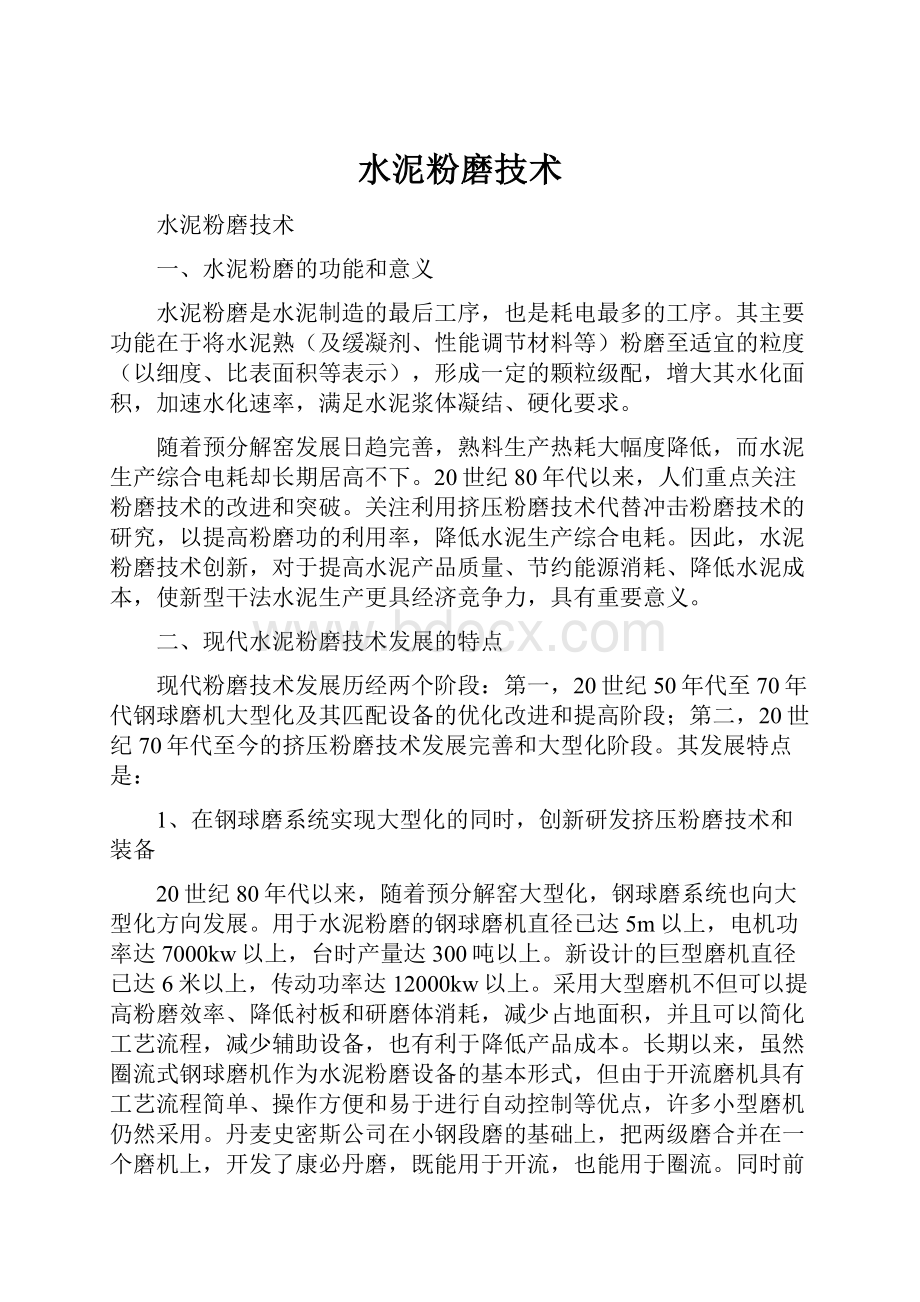
辊压机亦称挤压机、双辊磨,于1985年研制成功用于水泥工业,并逐渐大型化。
20世纪90年代以来,这两种挤压粉磨系统不但在生料、矿渣终粉磨系统得到广泛应用,并且由它们单独或同类型钢球磨、高效选粉机组成的预粉磨、混合粉磨、联合粉磨、半终粉磨以及终粉磨系统得到比较广泛的推广应用,从而使水泥生产综合电耗由120kw.h/t降低到90kw.h/t左右。
2、采有高效选粉设备
为了适应磨机大型化的要求,近年来圈流粉磨作业越来越多,作为其重要的配套设备的选粉机也得到了较大发展。
撒料式选粉机(又称机械空气选粉机)是水泥工业应用最早的具有代表性的空气选粉设备,目前其直径已达11米以上,选粉能力达300吨/小时以上。
为了与大型磨机相匹配,各种新型高效选粉机在水泥粉磨作业中也得到了日益广泛的应用,同时亦可利用它进行水泥冷却,其选粉能力已达500t/h。
目前,选粉机发展的主要趋势是进一步提高分级效率,提高单机物料处理量,结构简单化,机体小型化,可进行遥控操作等。
3、采用新型耐磨材料,改善磨机部件材质
在磨机大型化后,无论钢球磨、辊式磨、辊压机都在不断采用新型耐磨材料制造磨机衬板、磨辊、磨盘等部件,力求在改进磨机结构、提高加工精度的同时,进一步提高磨机综合效率和使用寿命。
4、添加助磨剂,提高粉磨效率
助磨剂能够消除水泥粉磨时物料的结块及黏糊研磨体及衬板的弊端,改善钢球磨粉磨条件,提高粉磨效率,而受到越来越多的重视。
5、降低水泥温度,提高粉磨效率,改善水泥品质
使用钢球磨机粉磨物料时,会使大部分输入能量转变为热能传递给物料,使粉磨物料的温度上升到100℃以上。
这样,不但会使二水石膏脱水,失去作为水泥缓凝剂的作用,而且温度过高还会使物料黏结,黏糊研磨介质,从而降低粉磨效率。
因此,为了降低水泥粉磨时的温度,提高粉磨效率,改善水泥品质,近年来广泛采用了许多新的冷却方法。
例如:
向磨内喷水,在选粉机内通风冷却和采用水泥冷却器对出磨水泥进行冷却等。
6、实现操作自动化
目前,水泥粉磨系统已广泛采用电子定量喂料秤、自动化仪表及电子计算机控制生产,实现操作自动化,以进一步稳定磨机生产,提高生产效率。
磨内作业主要利用电耳、提升机负荷、选粉机回粉量及利用辊式磨内压差等进行磨机的负荷控制,对石膏掺加量等亦可用X-荧光分析仪、电子计算机进行配料控制。
7、采取其他技术措施
如降低入磨物料粒度,保证水泥成品的合理颗粒级配及根据产品标准选择适当的比表面积,改善配料,选择合理的熟料矿物组成,降低入磨物料水分等。
8、开发粉状输送的新型设备
在广泛推广应用挤压粉磨的同时,在粉状物料输送方面,研发机械输送粉状的超高超重提升机、密封皮带机、新型空气斜槽等装备,代替气力输送粉体物料旧模式,力求水泥生产综合电耗的进一步降低。
闭路钢球磨系统
闭路钢球磨系统它是由管磨机、提升机、选粉机和风机等主要设备所组成,在粉磨过程中,粗粒物料几次通过磨机,它具有减少水泥过粉碎,避免发生颗粒凝聚和粘仓、粘研磨体等优点,有利于生产高细度水泥,改变生产水泥的品种,提高粉磨效率。
开流钢球磨系统
开流钢球磨是水泥生产中最普通的粉磨系统,由于水泥成品通过多仓管磨机粉磨一次完成,所以它具有工艺流程简单、附属设备少,建设投资省、操作管理方便和容易实现自动控制等优点。
但是,在生产高细度水泥,比表面积高于3000-3500cm2/g时,物料细粉容易凝聚,影响粉磨功效,因此,在此情况下人们往往要选用闭路粉磨系统。
三、辊压机及粉磨系统
1、国产辊压机发展历程
自上世纪80年代中期,由合肥水泥研究设计院、天津水泥工业设计研究院、洛阳矿山机器厂、唐山水泥机械厂四家单位联合引进德国KHD公司辊压机设计制造技术以来,经过20年的不断完善,国产辊压机的辊径由800mm发展到今天的1600mm;
辊宽由200mm发展到今天的1400mm;
装机功率由90kw×
2发展到今天的1120kw×
2;
整机重量由30多吨发展到今天的200多吨,通过量由40t/h发展到今天800t/h;
配套磨机的产量由20t/h发展到今天的180t/h,辊压机产品质量逐步提高,节能幅度达30%以上。
回顾国产辊压机20年的发展历程,大致可以分成三个阶段。
1.1研究开发阶段(1986年-1992年)
参加引进辊压机设计制造技术的四家单位在做好引进样机的转化设计和制造的同时,相继开发出各自的国产化辊压机,并在1990年前后通过鉴定。
在此期间国内的减速机生产厂家、轴承生产厂家、液压元器件生产厂家、耐磨堆焊生产研发等单位也都为国产化辊压机的研制成功做出了贡献。
合肥水泥研究设计院经国家“七五”重点科技攻关专题研究,推出第一台国产辊压机,并成功地应用于工业性生产,取得了使磨机增产40%,节电15%的效果。
1.2整改提高阶段(1993年-1999年)
在此期间,由于各厂家制造的辊压机在水泥生产中相继出现问题,让一些辊压机用户“既尝到了增产节能甜头、也吃尽了频繁检修的苦头”。
使得许多青睐辊压机增产节能效果的企业想上而不敢上。
合肥水泥研究设计院对此进行了分析和整改、完善。
一是注重加工件、配套件的质量提高;
二是优化工艺系统及设备的选型与配套。
经国家“八五”、“九五”重点科技攻关课题的持续研究,10余年的应用经验,推出了具有自主知识产权,设计更合理、性能更优越,可靠性更高的第三代HFCG系列辊压机。
有效解决了包括辊压机偏辊、偏载、水平振动和传动系统扭振等一系列关键性技术难题。
国内的减速机、轴承、液压元器件、耐磨堆焊材料等研发单位的配套件质量也都大大提高,为国产辊压机的长期安全运转奠定了基础,使主机设备运转率达90%以上,同时还开发出具有自主知识产权的SF系列打散分散机以及“V”型分级机等国家专利产品,使挤压粉磨系统工艺更加完善,参数更加合理。
1.3快速发展阶段(2000年至今)
解决了大型国产化辊压机设备制造和工艺配套两方面的问题,使国产辊压机进入全面推广应用的新阶段。
近年来国家水泥产业结构调整,淘汰立窑,发展新型干法旋窑,5000t/d熟料生产线已成为市场的主流,这就要求国产化辊压机也朝着大型化发展,及时开发出装机功率在1120kw×
2的大型HFCG160-140辊压机,与ф4.2×
13m开路水泥磨配套,产量可达170t/h以上,而ф4.2×
13m闭路水泥磨配套的产量则可达180t/h以上,取得增产100%,节电30%的实际应用效果。
2、辊压机基本工作原理及其特点
2.1辊压机工作原理
辊压机采用的是高压料层粉碎原理使物料得以粉碎,是大能量一次性输入。
为了实现工业生产连续性作业,采用一对相向运动的辊子,(其中一只固定辊一只活动辊)液压力通过活动辊将拉入两辊之间的物料压实粉碎,辊压机磨辊两端设有侧挡板以减少漏料。
2.2辊压机工作中存在的固有缺陷
边缘效应:
1)辊压机磨损两端漏料;
2)向两边逸出的物料。
选择性粉碎:
由于不同物料间物理性能的差异,即使在料饼中仍然存在未得到充分粉碎的物料颗粒。
2.3辊压机配套的分级设备
基于以上辊压机的工作特点,为给下一道工序(球磨机)提供合格的半成品,以充分发挥球磨机的研磨作用,必须设置物料分级装置,将小于一定粒径的物料作为半成品送入经过改造的球磨中继续粉磨至水泥成品,而大于此粒径的物料返回辊压机重新挤压,这就构成辊压机联合粉磨系统。
目前我们配套的分级设备有打散分级机和V型分级机两种,见图1,其各有优缺点。
两种分级系统的主要区别在于:
分级原理、分级精度——“V型分级机”完全靠风力提升分选,分级精度较高。
适合分选0.5mm以下的物料;
“打散分级机”机械与风力结合,分级精度较低,分选粒径可达3.0mm;
分级系统的装机功率、复杂程度和日常维护费用——“V型分级机”设备本身结构简单,无回转部件,但系统复杂。
磨损主要集中在隔板、管道、旋风筒、循环风机等;
“打散分级机”有回转部件,设备结构相对复杂,但系统简单。
磨损主要是内部的风轮、打散盘、衬板等;
系统电耗——“V型分级机”系统辊压机和球磨机主机电耗低,输送和分选电耗高;
“打散分级机”辊压机和球磨机电耗略高,输送和分选电耗低。
分选0.5mm以下物料时,“V型分级机”系统占优,反之“打散分级机”占优。
对辊压机工艺参数的要求——“V型分级机”系统必须采用低压大循环操作方式,否则料饼无法打散,更无法选出料饼中挤压好的细粉。
要求辊压机磨辊长径比大;
“打散分级机”可以采用高压力小循环操作方式。
磨辊长径比应小一些。
两种分级系统的选择条件
装机功率比——“V型分级机”系统中辊压机规格必须足够大,以保证产生足够量0.5mm以下的细粉供“V”型选粉机分选。
因此,辊压机与球磨机功率比应该在1:
1.0-2.5(开路);
1:
1.1-2.0(闭路)。
“打散分级机”系统中,辊压机与球磨机装机功率比在1:
2.5-3.5。
若比值再加大,随着辊压机在粉磨系统中所起作用的降低,系统电耗随之增加。
物料水分——应用于水泥粉磨的“V”系统,水分≤1.0%;
“打散分级”系统水分≤1.5%;
如配料中有高水分原料(如矿渣),则应单独烘干,不允许在磨系统中通热风,以防石膏脱水。
3、水泥磨系统工艺方案
水泥粉磨系统采用挤压联合粉磨系统,这是经过多年研究、试验,结合水泥粉磨原料特点及水泥质量要求,将辊压机和球磨机的各自优势发挥到最大,从而实现系统最优而总结出的实践经验。
四种主要的工艺方案的工艺流程见图2、3、4、5
3.1辊压机配套V型分级机挤压联合粉磨系统(闭路磨)
熟料、石膏及混合材(粉煤灰等粉状料直接入磨)等按一定比例配料后,由皮带机、提升机送入V型分级机,出V型分级后的粗粉返回稳流称重仓进行二次挤压,细粉(半成品)由风带入旋风筒收集后入磨,出磨物料由提升机、斜槽等送到高效选粉机,分选出的粗粉通过斜槽回到磨机,细粉随气流进入高浓度收尘器内,收下的灰即为成品,再由输送设备送入水泥库。
3.2辊压机配V型分极机挤压联合粉磨系统(开路磨)
熟料、石膏及混合材(粉煤灰等粉状料直接入磨)等按一定比例配料后,由皮带机、提升机送入稳流称重仓内,经辊压机挤压后,再由提升机送入V型分级机,出V型分级后的粗粉返回稳流称重仓进行二次挤压,细粉(半成品)由风带入旋风筒收集后入磨,出磨水泥即为成品再由输送设备送入水泥库。
3.3辊压机配打散分级机挤压联合粉磨系统(闭路磨)
熟料、石膏及混合材(粉煤灰等粉状料直接入磨)等按一定比例配料后,由皮带机、提升机送入稳流称重仓内,经辊压机挤压后,再由提升机送入打散分级机,打散分级后的粗粉返回稳流称重仓进行二次挤压,分级出的细粉(半成品)入磨,出磨物料由提升机、斜槽等送到高效选粉机,磨内通风也进入选粉机,分选出的粗粉通过斜槽回到磨机,细粉随气流进入高浓度收尘器内,收下的灰即为成品,再由输送设备送入水泥库。
3.4辊压机配打散分级机挤压联合粉磨系统(开路磨)
熟料、石膏及混合材等按一定比例配料后,由皮带机、提升机送入稳流称重仓内,经辊压机挤压后,再由提升机送入打散分级机,打散分级后的粗粉返回稳流称重仓进行二次挤压,分级出的细粉(半成品)入磨,出磨水泥即为成品,再由输送设备送入水泥库。
上述系统为防止铁件和非磁性金属进入辊压机损坏辊面,在入稳流称重仓的皮带机上均需要安装交叉皮带式除铁器和金属探测仪,当有铁件混入物料中时,除铁器将自动除铁,如有非磁性金属材料通过,金属探测仪将报警并急停皮带机。
3.5球磨机开路系统与闭路系统的比较
挤压联合粉磨系统配V型分级机还是打散分级机都不造成影响水泥的性能指标,而主要取决于磨机是开路还是闭路磨系统。
两种系统各有特点
3.5.1带内筛分的开流粉磨系统的比较
优点:
1、开流粉磨系统的车间主体为单层厂房,在线设备少,操作简单、系统运转率高,一般可达85%以上;
B、开停机时间和系统平衡时间短,非常利于系统避峰操作;
C、系统投资低,单位产能投资比同规模的闭流系统少10%-20%;
D、系统装机功率低,由于电机功率主要用于做粉磨功,分选部分采用机械方式,因此,单位产能装机功率小;
E、使用炉底渣、火山灰、烧结煤矸石、粉煤灰等作为混合材,可多掺混合材;
F、水泥颗粒分布宽,早期强度高,水泥需水量低2%-4%。
缺点:
A、成品中筛余有粗颗粒;
B、水泥成品温度较高,尤其是使用于熟料生产线上的大型磨机时。
但如果在窑系统选用好的篦冷机,有效降低入磨熟料的温度,并适当考虑磨内喷水,则可将出磨水泥温度控制在要求范围内。
但一般高于同样情况的O-Separ选粉机的闭路系统。
3.5.2挤压联合闭路粉磨系统的比较
A、闭流系统适用于普通大型磨机配以经过改进的O-Separ选粉机,生产高标号水泥和特种水泥(52.5#普通硅酸盐水泥);
B、同规格的球磨机闭路磨系统台时产量比普通开流磨机产量高20%,比同规格带内筛分的开流磨机产量一般不高于10%;
C、出磨水泥温度较低,对输送、包装、使用,尤其对大型磨机生产高标号水泥有利;
D、筛余中无粗颗粒,适合生产高层喷浆水泥。
A、增加设备数量,系统工艺复杂,年运转率低;
B、由于系统复杂,开停机过程时间长,如系统为避峰,不能长时间连续运行,其系统电耗增加;
C、单位产能投资、单位产能装机功率均高于开流磨系统。
四、辊压机联合粉磨系统
1、工艺流程
工艺流程:
配料以定量给料机分别计量后由皮带输送至辊压机稳料承重仓上部,经布料器均匀地进入小仓内,物料从小仓底部卸出后以料柱形式进入辊压机两辊之间,被挤压成料饼后经斗提提升进入打散分级机,料饼被打散和分级后,粗粉被收集下返回辊压机小仓重新进行挤压,≤3mm的细粉入磨。
出磨成品经斜槽和库顶水泥分配器均匀入库。
2、系统平衡和生产控制
在操作中,有以下两个调节回路:
2.1水泥细度调节
调节水泥细度主要是通过调节入磨物料量来调节的,而调节打散机转速可以调节入磨物料量。
打散机转速高,入磨物料量大,颗粒粗,水泥细度大,产量高;
打散机转速低效果则相反。
2.2称重仓料位调节
称重仓料位应保持稳定,一般控制在70%-80%为宜,改变配料总量可以控制粒位,配料量增大,仓内料位上升。
3、生产中常见故障分析
3.1辊压机常见故障及分析处理
辊压机是利用高压料层粉碎的机理,采用单颗粒粉碎群体化的工作方式进行连续工作。
常见故障有:
两辊异常振动,动、静辊电流不稳,挤压效果不佳,出辊压机斗提负荷过重,甚至压死斗提等,我们主要从入磨物料的性质和辊压机的操作参数以及设备三个方面进行分析,并采取措施,具体如下:
1)配料中(特别是熟料中)含有大量的细粉,熟料飞砂量较多,这是引起辊压机异常振动的主要原因。
对此从两方面进行调整;
一是减少配料库中熟料的离析现象。
原来两台水泥磨熟料配料共使用一个配料库,因库顶熟料进料口稍微偏离中心位置,库内熟料离析严重,对此将原设计而未用的石灰石库启用改为熟料库,库下的配料秤作相应调整,实现水泥磨双系统分别单独配料,减小了熟料的离析;
二是当熟料中细粉较多时,可增加混合材中沸石掺量,达到调整物料平均粒径的目的。
根据经验,入辊压机物料平均粒径在20mm以上,最好在35mm-45mm之间,辊压机不易振动且挤压效果好,如物料太细,可将动、定辊之间的垫铁加厚,由原来的10mm加为12mm,液压压力也可适当降低,以减小振动。
2)打散分级机分级能力降低,回粉中细粉太多,循环负荷加大,导致总配料量降低,辊压机缓冲小仓中含有较大颗粒的新鲜物料减少。
3)入辊压机小仓皮带处漏风严重,或者系统收尘风机风量过小,造成布料器通风少,收尘效果差,细粉不能被及时抽走,进入小仓内细料较多。
4)入磨物料中综合水分太小。
如物料中平均粒径偏低,含水分也偏低,物料通过辊压机时,两辊之间的啮合角就小,物料很容易顺辊隙冲下,不易形成稳定的料饼,造成辊压机振动和挤压效果差。
根据经验,入辊压机物料综合水分控制在0.8%-1.3%之间比较理想,我们采取在熟料配料秤上增加淋水装置,来控制适宜的物料水分,改善了挤压效果。
5)入辊压机物料粒径不均,夹有较大的颗粒,在两辊挤压过程中,较细的物料下泻过快,容易造成辊压机两端辊缝偏差大,不能形成稳定的料层,从而引起振动或跳停。
我厂配料中较大的颗粒主要来自石膏和沸石,所以要经常对破碎机进行检查、调整和处理,保证物料粒度在60mm以下。
如进辊物料中混有较大铁块或其它异物,会引起辊压机液压系统振荡。
对此应及时卸掉液压系统高压,将动辊退出,检查排除铁块和异物,并仔细分析铁块混入原因,检查除铁器的工作性能。
6)稳流承重仓控制料位过低,辊压机上方不能形成稳定的料柱,使承重仓失去靠物料重力强制喂料的功能,且容易形成物料偏流入辊的现象,而引起振动或跳停。
根据经验,把小仓料位定在60%-80%比较适宜,但应定期清理小仓内壁上因物料潮湿而粘附滞留的积料,否则会影响小仓的实际有效容积。
7)两辊之间辊缝设置过大或两轴承座之间被物料阻塞,造成两辊之间辊缝加大,使液压系统所施加的挤压力未完全作用于被挤压的物料上,造成挤压效果下降。
一般应保持原始辊缝在10mm-12mm之间,另外应设置合适的辊缝偏差,由于我厂采用的是大直径窄辊型辊压机,辊压机在运行时两辊两端间隙偏差较大,如偏差值设置过小,辊压机跳停频繁,我们根据经验设定偏差值在30mm以内,运行比较平稳。
8)进料系统手动调节插板调的过高或插板端部过度磨损,致使物料饼过厚,磨辊两端漏料严重,循环负荷增加,造成辊压机负荷增大;
相反如调节插板调的过低,两辊上方的料柱压力就小,物料容易从辊缝间冲过,不能形成稳定的料层,使液压系统所施加的压力不能完全作用于被挤压的物料,造成挤压效果下降。
根据生产经验,调整辊压机调节插板至合适位置,使挤压出的料饼厚度在25mm-40mm之间波动,挤压效果良好。
9)因辊压机侧档板下端衬板过度磨损或变形外翘,使磨辊边缘影响区扩大,造成大量物料未经挤压就通过磨辊,循环负荷增大。
在生产过程中,要加强对侧挡板的检查,并防止侧挡板的压紧螺栓松动,保持侧挡板与磨辊端面之间间距在2mm之内,效果较为良好。
10)辊面磨损的影响。
磨辊表面的棱型花纹能保证物料啮入而不产生滑移,并充分受到挤压破碎形成料饼。
辊面磨损严重,辊面凹凸不平时或成不规则的圆型时,两辊的间隙会忽大忽小,液压压力则忽高忽低,电机电流相应波动。
我厂的辊压机在运行约一年后,辊面中间磨损比较严重,经停机补焊后挤压效果恢复良好。
选择合适的工作压力也可延长磨辊耐磨层的使用寿命,我公司将辊压机的工作压力设定在7.0-8.0MPa之间,如入辊物料较细,辊压机易振动时,工作压力再适当调低,可较好的保护辊面。
11)出辊压机斗提负荷过大,在辊压机振动和小仓塌方时很容易被物料压死。
原因:
一是辊压机振动时,为保护辊皮,液压系统会自动卸压,辊隙随之增大,并造成小仓塌方,大量物料迅速冲下,斗提电流急剧增大,斗提被压死;
二是磨头斗提属于NE板链式提升机,该斗提在提升粉状物料时,其卸料方式为“流入式”,再加上其料斗较深,回料比较大(达30%左右),容易在斗提底部形成大量积料,造成物料提升不及而负荷增大。
处理措施,首先在辊压机稳流小仓下料管上增加一个自动控制的气动棒阀(原设计为手动棒阀),与小仓料位连锁,当小仓塌方时,料位会急剧下降,气动棒阀自动关闭,断开料流,从而避免斗提压死;
其次我们对磨头斗提进行了改进处理,对斗提出料口部分板链用道轨改变原来运行直线,使运行到下料口的料斗倾斜角度加大,这样就便于接料口前升接料距离,使回灰大大降低。
经改造后斗提电流稳定在90-110A之间,斗提超负荷压死的问题得到了解决。
3.2打散分级机常见故障和分析处理
打散分级机可有效解决辊压机的边缘效应问题,该机是一种集料饼打散和分级于一体的新型分级设备,其打散方式是采用离心冲击破碎的原理,出辊压机的料饼经进料口落入带有锤形凸棱衬板的打散盘上,在高速旋转的打散盘作用下,加速沿切线方向甩出,撞击到反击衬板上被破碎,由于物料的打散过程是连续的,料饼还受到反弹回来的物料相互之间的撞击破碎;
分级方式应用的是惯性原理和空气动力学原理,经打散后的碎料通过环行通道进入风轮四周的风力分选区内,粗颗粒物料由于其运动惯性大,在沉降过程中运动状态改变较小而落入内锥体,在内筒锥体筛板的作用下得到二次分级,部分细粉通过筛板篦缝进入外筒体,粗粉返回辊压机小仓;
细粉由于其运动惯性小,在风轮风力的作用下,运动状态改变较大,落入内、外筒体之间被收集,通过细粉卸料口出入磨。
打散分级机在使用一段时间后,在其它操作参数未变的情况下,发现系统细粉产量降低,回粉增加,原系统生产平衡被打破。
3.2.1打散效果差
1)打散盘衬板磨损:
打散盘衬板的锤形凸棱衬板部分被磨损后,会影响对物料的加速效果,料饼容易在盘面上打滑而失去离心力,粉碎效果变差,部分未打散的料饼以粗料的形式返回辊压机稳流仓。
2)打散电机传动皮带打滑:
因传动皮带老化或松驰会造成打散盘转速丢速,影响对物料的加速效果,造成的负面影响同上。
3)配料太湿或含杂物太多:
太湿的物料经挤压后形成的料饼密实坚硬,不易打碎,会以粗料的形式被内锥筒体收集返回承重仓,造成回料偏多;
柔软性物料(如碎皮带、布头等)容易阻塞打散盘外围的环行通道,影响打散分级机的物料通过能力。
3.2.2分级机分级能力下降
1)打散分级机风轮驱动电机与转子连接失效,传递动力的联轴器尼龙销断裂,风轮失去动力,分级机失去分级能力,打散后的大量合格物料落入收集粗料的内锥筒体,造成回料增多。
2)打散分级机内锥筒体破损或筛板堵塞使筒体内物料淤积,大量粗料以成品的形式进入球磨系统,使球磨机小规格的研磨体难以适应这样的物料粒度,造成磨机产量的明显下滑。
3)风轮磨损严重。
分级机的风轮在使用过程中受含尘气流的冲刷,磨损会逐渐增大,使风轮产生的风力削弱,分级机的分级能力降低,回粉增加。
打散机转速越高,则风轮磨损越快,不利于设备长期运行,打散机转速低于300r/min时,则对物料的分级调节作用不明显。
我们通过调节打