CA6140车床对开螺母体上部文档格式.docx
《CA6140车床对开螺母体上部文档格式.docx》由会员分享,可在线阅读,更多相关《CA6140车床对开螺母体上部文档格式.docx(17页珍藏版)》请在冰豆网上搜索。
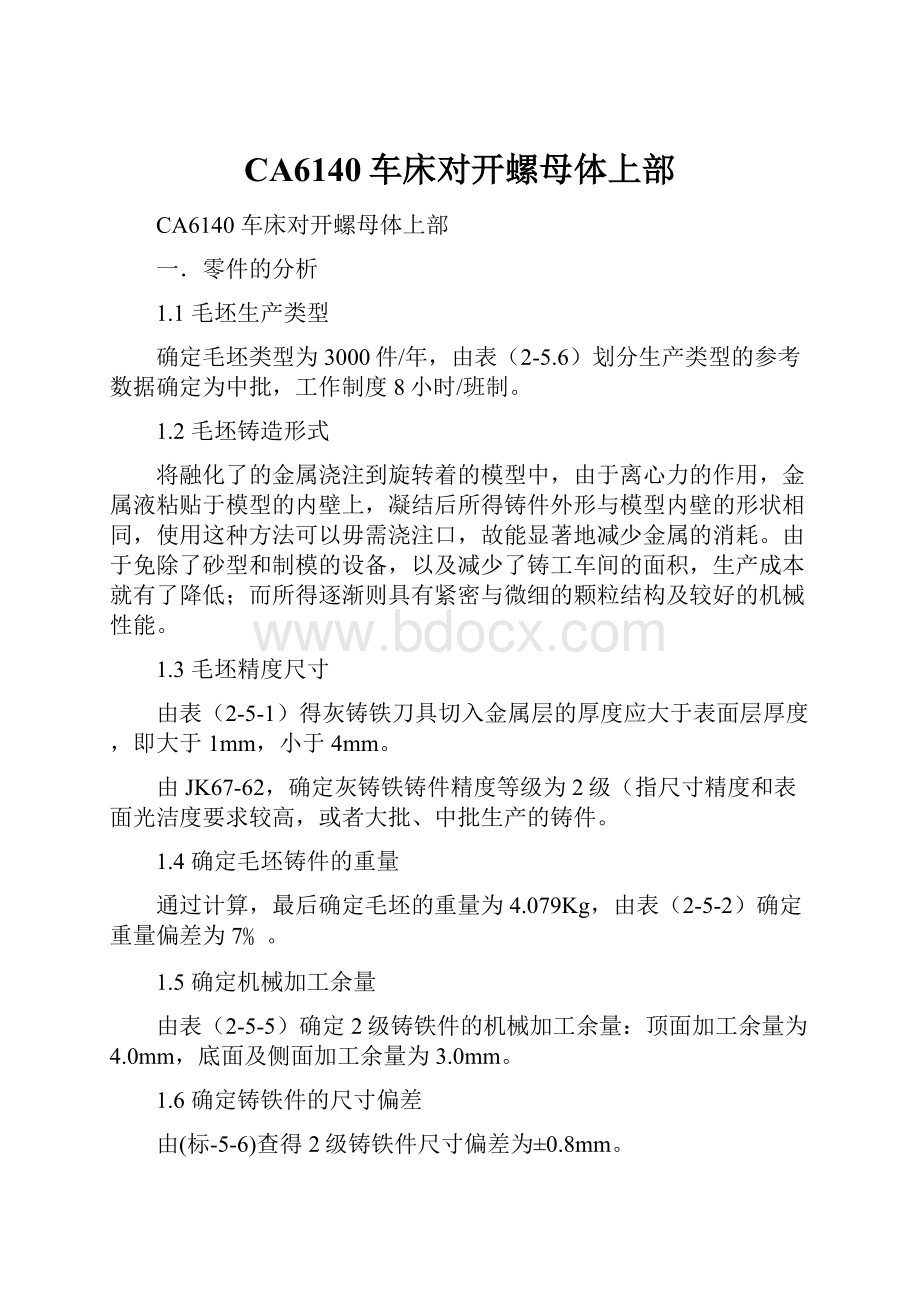
因此采用离心铸造,这从提高生产率、保证加工精度来考虑也是应该的。
2.2基面的选择
基面选择是工艺规程设计中的重要工作之一。
基面选择的正确与合理,可以使加工质量得到保证、生产率得到提高。
否则不但加工工艺过程中的问题百出,更有甚者,还会造成零件大批报废,使生产无法正常进行。
粗基准的选择:
对象对开螺母体这样的零件来说,选择好粗基准是至关重要的。
按照有关粗基准的选择原则,即当零件有不加工表面时,应以这些不加工表面作粗基准;
若零件有若干个不加工表面时,则应以与加工表面要求相对位置精度较高的不加工表面作为粗基准。
我现在选取燕尾为粗基准,利用左、右两个定位块和一个削边销对其进行限制,以消除六个不定度,达到过定位。
对于精基准而言,主要应该考虑基准重合的问题。
2.3制定工艺路线
制定工艺路线的出发点,是应该使零件的几何形状、尺寸精度及位置精度等技术要求能得到妥善的保证。
在生产纲领已确定为成批生产的条件下,可以考虑采用万能性机床配以专用工夹具,并尽量使工序集中来提高生产率。
除此之外,还应当考虑经济效果,以便使生产成本尽量下降。
2.4工艺路线方案:
工序Ⅰ.铸造。
Ⅱ.热处理。
Ⅲ.粗,精铣底面
Ⅳ.半精铣燕尾座
Ⅴ.粗,精车中心孔Φ52H7
Ⅵ.粗,精车外圆端面并倒角1.5x45º
Ⅶ.精铣对开螺母体燕尾
Ⅷ.对开螺母体钻铰底面孔2xΦ12孔
Ⅸ.钻,粗铰沉头螺钉孔2xΦ7并倒角
Ⅹ.钻螺纹孔,攻螺纹2xΦ12孔。
Ⅺ.刮研对开螺母体燕尾(钳工)
Ⅻ.粗铣切割端面。
2.5机械加工余量、工序尺寸及毛坯尺寸的确定
“对开螺母体”零件材料为HT15-33灰铸铁。
毛坯重量为4公斤,生产类型为中批生产,采用离心铸造毛坯,2级精度。
根据上述原始材料及加工工艺,分别对各加工表面的机械加工余量、工序尺寸及毛坯尺寸确定如下:
1.Φ52H7孔
精铰至Φ52H7,表面粗糙度为Ra1.6um,工序余量为2z=0.08;
粗铰至51.92mm2z=0.42;
精车至51.5mm2z=1.5;
粗车第二次至50mm2z=3;
粗车至47m2z=7;
2.2×
Φ12孔
铰至Φ12mm2z=0.15;
扩钻至Φ11.85mm2z=0.85;
钻至Φ112z=11;
3.一端面
精车至972z=0.8;
半精车至97.82z=1.2;
粗车至992z=6;
4.另一端面
精车至952z=0.5;
半精车至96.52z=0.5;
粗车至962z=1;
2.6确定切削用量及基本工时
工序Ⅰ:
铣燕尾及空刀槽
2.6.1粗铣燕尾
v=6m/min(0.1m/s)(表1-10-151)
ns=1000v/πdw=1000×
×
40=0.8r/s(47.8r/min)
按机床选取nw=0.79r/s(47.5r/min)
∴实际切削速度
切削工时:
l1=8.7(表1-11-12)
t0=
=158.3s(2.64min)
2.6.2精铣燕尾
ns=
=0.8r/s(47.8r/min)
∴实际切削速度v=πdwnw/1000=3.14×
40×
0.79/1000=0.43m/s
l1=6.3(表1-11-12)
=153s(2.6min)
2.6.3铣退刀槽
s=0.02~0.03(表1-10-142)
选s=0.02mm
v=47m/min(0.78m/s)(表1-10-144)
=4.14r/s(248r/min)
按机床选取nw=4r/s(240r/min)
∴实际切削速度v=
=0.75m/s(45m/min)
l1=5.9,l2=4(表1-11-12)
sm=szzn=0.02×
4×
36=2.88
=3.785s(0.06min)
2.6.4粗铣端面
选择高速钢套式面铣刀
每齿进给量:
sz=0.1-0.2(10-113)
选sz=0.1mm
v=56m/min(0.92m/s)
=3.7r/s(222r/min)
按机床选取nw=4.2r/s(252r/min)
=1.01m/s(61m/min)
l1=37.5,l2=2(表1-11-15)
sm=szzn=0.1×
18×
3.7=0.37
t0=(
=185s(3min)
2.6.5精铣端面
铣刀每转进给量0.10~0.12
选s0=0.12mm
v=56m/min=0.9m/s
=3.7r/s(222r/min)
sm=szzn=0.1×
18×
2.6.6钻Φ52H7孔并倒角1.5×
45º
(1)粗镗第一次至47mm
选择硬质合金可调节浮动镗刀B=25,H=12(表8-32)
进给量S=1.6-2.0,选S=1.6mm/r(10-97)
v=62.6m/min,n=398r/min(6.63r/min)(表10-98)
切削工时
l1=1.7,l2=3.0,l=105(表11-9)
t=(D-d1)/2=(47-40)/2=3.5mm
=10.34s(0.17min)
1粗镗第二次至50mm
S=1.6-2.0,选S=2.0mm/r(10-97)
v=56.6m/min,n=360r/min(6r/min)(表10-98)
l1=0.87,l=105(表11-9)
t=(D-d1)/2=(50-47)/2=1.5mm
=9.07s(0.15min)
2精镗至52m
S=1.6-2.0,选S=1.6mm/r(10-97)
l1=0.58,l=105(表11-9)
t=(D-d1)/2=(51.5-50)/2=0.75mm
=10.24s(0.17min)
2.6.7钻2×
选择直柄麻花钻(GB1436-78)
1钻到11.0mm
S=0.22-0.28,S=0.25mm/r(10-67)
v=28m/min(0.47m/s),n=894r/min(7.95r/s)
ns=1000v/
l1=0.05,l2=39,l=105(表11-10)
t=(D-d1)/2=(52-51.92)/2=0.04mm
=13.6r/s(816r/min)
按机床选取nw=800r/s(13.3r/min)
∴实际切削速度v=
=0.46m/s
l1=3.4,l2=1.5,L=20(表11-6)
=7.49s(0.13min)
②扩孔钻至11.85
S=0.7-0.9,S=0.7mm/r(10-75)
v=22.2m/min,n=472r/min(表10-76)
按机床选取nw=460r/min=7.67r/s
实际切削速度
=0.29m/s
l1=0.58,l2=1.5,l=20
=4.11s(0.07min)
③铰至Φ12
选用锥柄机用铰刀D=12(表8-34)
S=1.7mm/r(10-81)
v=10m/min,n=318r/min(5.3r/s)(表10-84)
l1=0.05,l2=18,l=20
=5.14s(0.09min)
2.6.8车端面
1粗车至99mm
S=(0.3~0.5)mm/r(10-19)
选s=0.4mm/r
V=118m/min(1.97m/s)
=9.65r/s(597r/min)
按机床选取nw=8.6r/s(516r/s)
∴实际切削速度为
=1.76m/s(105m/min)
l=(105-99)/2=3mm,l1=3,l2=2,l3=5(11-4)
L=d/2+l1+l2+l3=32.5+3+2+5=42.5mm
t0=(L/s.n).i=(42.5/0.4×
8.6)×
2=24.72s(0.4min)
2半精镗至97.8mm
选s=0.3mm/r
V=35m/min(0.58m/s)
=2.84r/s(171r/min)
按机床选取nw=2.5r/s(150r/s)
=0.51m/s(30.615m/min)
l=0.6,l1=1,l2=1,l3=5(11-4)
L=d/2+l1+l2+l3=32.5+1+1+5=39.5mm
t0=(L/s.n).i=(39.5/0.3×
2.5)×
1=52.7s(0.88min)
3精车至97mm
S=(0.3~0.5)mm/r(10-19)
l=0.4,l1=1,l2=1,l3=5(11-4)
4倒角1.5×
45°
S=(0.15~0.25)mm/r(10-90)
选s=0.2mm/r
v=(12~25)m/min(0.58m/s),选v=20m/min=0.33m/m
=2.02r/s(121r/min)
按机床选取nw=120r/min(2r/s)
l=0.75,l1=0.4(11-9)
tm=(l+l1)/nw.s=(0.75+0.4)/(2×
0.2)=2.87min(172.5s)
2.6.9切断
选用锯片铣刀,D=175mm(8-38),齿数(8~38)
S=(0.03~0.04)mm/r(10-142)
选s=0.03mm/r
v=34m/min(0.57m/s),
=2.412r/s(144r/min)
=0.59m/s(35m/min)
l1=6,l2=4mm(11-12)
Sm=Sz·
Z·
n=0.03×
2.5=3mm
=49s(0.82min)
三、机床夹具设计
1.工序尺寸精度分析
由工序图知,本道工序为钻、锪两个φ6.5径向孔。
由工序尺寸精度可知此工序精度要求较低。
保证φ6.5孔中心轴线与φ55孔中心线垂直。
应限制X旋转,Z旋转
保证φ6.5锥孔为90°
应限制Z移动
保证φ6.5孔的轴向位置应限制y移动
保证φ6.5孔相对于φ55孔中心线的对称度应限制X移动
保证φ6.5与φ12孔垂直分布应限制Y旋转
综合结果应限制X移X转,Y移Y转,Z移Z转
2.定位方案确定
根据该工件的加工要求可知该工序必须限制:
x移动、X转动、y移动、z移动z转动,共计6自由度,采用φ55心轴与工件φ55孔H7/h7配合,限制X移X转Z移Z转
菱形销限制Y转,心轴轴肩限制Y移
综合结果:
限制X移X转,Y移Y转,Z移Z转
3.定位元件的确定
1.:
心轴φ55h7
2.菱形销与φ12孔配合H7/h7
△2=2b/D2(△k+△j-△1/2)
=2×
3/12(0.15+0.05-0.021/2)=6/12×
0.1895=0.095
d2=(12-0.095)h7(0-0.018)
4.定位误差分析计算
(1)分析同轴度误差
用用心轴定位,设计基准与定位基准重合
△jb=0
△db=1/2*(55.025-54.975)=0.025
所以△dw=2*△db+△jb=0.05<
1/3TT=0.4mm
(2)分析菱形销的定位误差
Dmax-dmin=12.013-11.887=0.126<
(3)分析轴向尺寸,心轴轴肩定位,设计基准与工序基准重合
△db=0
所以△dw=0
5.夹紧方案及元件的确定
(1)计算切削力及所需加紧力:
查《机械工程师夹具手册》表1-2-7切削扭矩计算公式M=0.34*D
S
KP得
M=0.34*10
*0.2
*
=10.91N*M
切削力计算公式PX=667*10*0.2
*(900/736)
=2514.03n
查《机械工程师夹具手册》表1-2-11得Wk=K*P*L/(µ
*H+L)得
Wk=
=5774.27N
加紧如图所示
夹具体选用灰铸铁的铸造夹具体.
四、体会总结
本次课程设计是对我们这些年来在学校所学知识的复习和巩固。
通过课程设计可以检验出我们在校期间的学习水平。
从而使我们对所学专业知识理解的更透彻,运用的更熟练。
从我们拿到零件图纸的第一天开始,我们的老师就详细给我们讲了设计的步骤,还安排了辅导时间。
为我们圆满的完成任务制定了详细的计划。
我们以前所接触的只是课本上的知识,对实际的机械加工工艺了解的不很透彻。
但是通过这次设计,我们才全方位的懂得了什么是机械设计,从而更加提高了我们的专业素养,和实践水平。
刚开始设计的时候,总觉的难度很大,不知道从什么地方下手,对一些设计的步骤根本不知道怎么安排,怎么设计。
老师给我们详细讲解了机械设计应注意的问题,让我们先从分析零件图开始,然后在得出零件技术要求,在根据零件的技术要求画出毛坯和零件合图。
然后运用所学的工艺机加工知识,编排出工件的工艺过程。
再进行工装设计。
在设计期间,我们亲身体验了机械加工工艺的设计,对我们有了很大提高。
遇到不懂的问题时,指导老师们都能细心的帮助我。
同学之间虽然每个人的设计课题不一样,但我们之间还是会经常讨论,互相帮助,不紧学会了知识,而且还锻炼了我们的团队精神。
在这次设计中,要感谢我们的指导老师,他们在设计期间为我们的解决了很多难题。
相信我们通过这次设计,一定会在以后的工作岗位中干的更出色。
参考文献:
【1】机械加工工艺设计手册张耀宸航空工业出版社
【2】机械制造工艺设计手册王绍俊机械工业出版社
【3】机械设计手册《机械设计手册》联合编写组化学工业出版社
【4】机床夹具设计实例教程李名望化学工业出版社
【5】机械制造技术基础卢秉恒机械工业出版社