设计一座年产150万吨良坯的转炉炼钢车间Word文档下载推荐.docx
《设计一座年产150万吨良坯的转炉炼钢车间Word文档下载推荐.docx》由会员分享,可在线阅读,更多相关《设计一座年产150万吨良坯的转炉炼钢车间Word文档下载推荐.docx(93页珍藏版)》请在冰豆网上搜索。
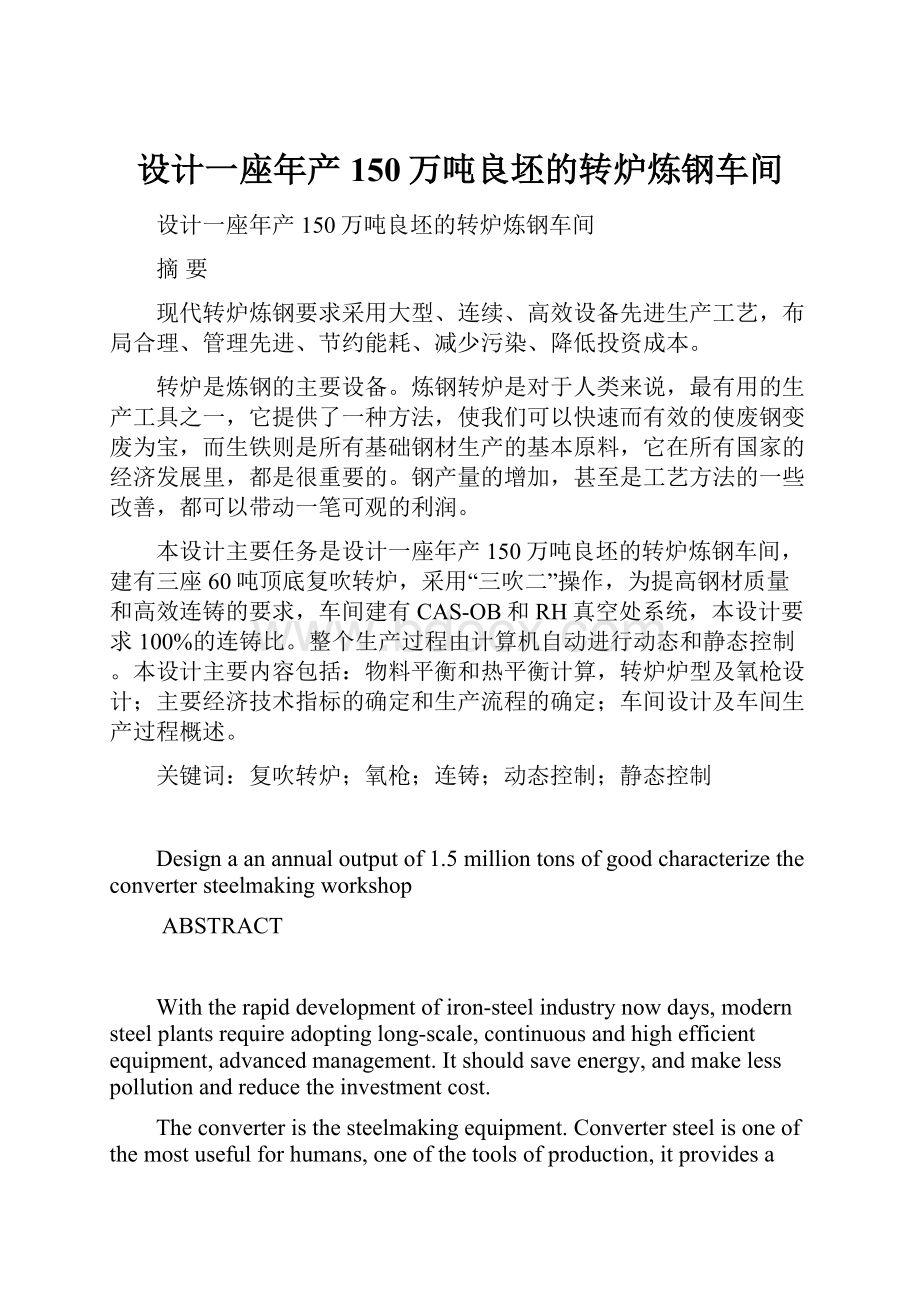
ABSTRACT……………………………………………………………………...Ⅱ
1绪论
1.1本课题来源,意义及国内外研究现状:
来源:
众所周知,炼钢生产环节在钢铁联合企业中处于整个生产流程的中间部位,起承上启下的作用,可谓钢产品生产的中间环节;
而在独立的钢厂,即炼钢—轧钢以及钢的深加工型企业里,炼钢是决定产品产、质量的首要一步。
炼钢环节的任何延误或产、质量波动都会影响前后生产工序的协调运转。
这都与炼钢车间(厂)的设备、工艺、组织管理等因素有关。
所以在新建厂设计或旧厂进行技术改造的起始阶段就应当处理好相关的各种问题,为正常生产,保持良好的运转秩序打下基础。
意义:
基于我对钢铁冶金生产工艺学的了解,通过工艺设计使我对国内外钢铁生产工艺流程、主要技术条件、冶金计算、冶金设备等实际生产情况有较全面的了解和掌握,使自已成为符合钢铁厂需要的合格专业技术人才。
1.2国内外现状:
前言:
2012年中国钢产量达到2.22亿t,是世界上第一产钢大国。
而炼钢是钢铁生产的主要工序,对降低生产成本、提高产品质量、扩大品种范围具有决定性影响。
转炉是目前国内外最主要的炼钢设备,世界上约有600座转炉在运行,约占全球粗钢产量的60%。
在我国,粗钢产量的80%以上由转炉生产。
鞍钢、武钢等大型钢厂多采用全转炉冶炼生产。
全世界现代转炉炼钢技术发展状况参见表1-1。
转炉的分类:
按吹炼设施的布置,转炉大体分为顶吹转炉、底吹转炉和复吹转炉三类。
1952年奥地利的林茨和多纳维茨钢厂合作发明了第一座氧气顶吹转炉,1960年世界氧气顶吹转炉的钢产量占全球粗钢产量的比率不到5%。
20世纪70年代该技术发展较快,占全球粗钢产量的比率提高到40%,到20世纪80年代初提高到60%以上。
1968年德国马克西姆利安钢厂又成功开发了氧气底吹转炉。
到20世纪70年代,底吹转炉生产能力达到3000万吨。
1977年美国琼斯—劳夫林公司芝加哥厂建成了2座225t氧气底吹转炉,接着日本川崎制铁公司千叶厂也投产了230t底吹转炉,称为Q—BOP法。
20世纪70年代中期至80年代初期,法国钢铁研究院、卢森堡阿尔贝德公司等十几个国家的炼钢厂先后开展了顶底复合吹炼转炉实验研究。
1980年3月,日本住友金属工业公司鹿岛厂250t复合吹炼转炉正式投入生产。
顶底复合吹炼转炉的种类繁多,以底部吹人气体的种类划分,可分为强搅拌型和弱搅拌型,如日本新日铁大分厂采用的ID—OB法为强搅拌型,底吹氧气强度为0.15~0.80m3/(t·
min);
而法国钢研院和阿尔贝德公司开发的IBE法为弱搅拌型,该法采用多孔砖底吹N2、Ar,底吹供气强度为0.07~0.15m3/(t·
min)。
表1-1现代转炉炼钢技术的发展历程
时间
特点
说明
1952~1970
大型化
以转炉大型化技术为核心,“三吹二”或“二吹一”模式,逐步完善转炉炼钢工艺与设备。
1970~1990
复合吹炼
连铸技术的迅速发展,对转炉炼钢的稳定性提出更高要求。
1990~现在
洁净钢冶炼
社会对洁净钢的生产需求日益提高,迫切需要建立起一种全新的。
能大规模廉价生产纯净钢的生产体系。
(1)顶吹氧气、底吹惰性气体法。
这种方法为强搅拌型复吹法,代表技术有LBE、ID—KG、LD—OBT和NK一(BIJ)一AB)等。
此技术底部供气元件易维护、寿命长、操作工艺较简单、适应钢种范围广,在世界上广为采用,中国的复吹转炉绝大多数采用该法。
(2)顶底复合吹氧法。
这一方法属于强化冶炼型,代表技术有:
BSC—BAP、LD—HC、SHB、SIB—P和K—(BP)等,欧洲和日本采用此法较多。
(3)顶吹氧气、底吹氧气和燃料法。
此法可显著提高废钢比,代表技术有KMS和KS等,其中KS法在底吹氧的同时喷人煤粉。
钢铁料可100%采用废钢,德国应用了该技术。
1.3国内外复合吹炼技术的最新进展
(1)蒂森公司TBM法
早在20世纪70年代末期,蒂森公司通过一系列的研究试验,确立了TBM法复合吹炼技术。
该法是从转炉底部向熔池吹人N2、Ar。
多年来,蒂森公司的布鲁克豪森厂2座380t转炉、贝克尔韦特厂3座260t转炉和卢森堡阿尔贝德马里蒂姆厂2座300t转炉均采用TBM法复合吹炼,并取得了良好的经济效益,生产成本亦有所降低。
采用IBM法复合吹炼,钢水收得率提高、造渣剂加入量减少、合金回收率高、氧枪及炉衬寿命延长,使钢的生产成本降低约5马克/t钢。
此外,IBM法曾出售给印度一家钢厂,在生产实践中也取得了良好的脱磷效果。
2001年我国梅山冶金公司150t转炉引进了IBM技术,运行结果表明,IBM法具有良好的脱磷能力。
(2)阿尔贝德萨尔钢公司LBE法
伏林根厂3座150t转炉采用LBE法复合吹炼。
生产实践证明,LBE法复吹技术透气元件寿命长,可大幅度调节吹气量;
操作简便;
流经炉底布置的12个透气砖的气流可以保持恒定,透气砖沿炉底呈圆周布置;
搅拌气体的输入管线可从转炉耳轴经球型接头引入转炉炉底;
利用声波对炉内成渣过程进行连续监控。
采用LBE法复合吹炼取得了下列效果:
①炉渣中F(O含量降低约2.5%);
②金属收得率提高约0.5%;
③石灰耗量约减少5kg/t钢;
④不经脱气处理的钢中碳含量可达0.02%;
⑤转炉出钢成分、温度均匀。
由于LBE法复吹具有诸多优点,被欧洲一些钢厂及新日铁室兰厂广泛采用。
(3)新日铁公司ID-AB复吹技术
早在1979年末,新日铁公司大分厂340t转炉、八幡-炼钢150t转炉、八幡三炼钢320t转炉以及名古屋厂均相继把原有顶吹转炉改造成了IJ-OB复吹转炉。
此外,新日铁还开发了IJ-AB复吹技术,从转炉底部吹人惰性气体,如君津二炼钢300t转炉、君津—炼钢220t转炉。
1990年新日铁向宝钢输出了(IJ)-AB技术。
日本新日铁采用预脱磷硫-BOF-精炼-CC工艺生产海洋结构用高级管线钢,达到碳(0.001%)、全氧(0.0025%)、氮(0.0015%)、磷(0.0025%)、硫(0.0003%)和氢(0.0001%)之和为0.0069%。
(4)住友金属SIB法
住友金属发明了SIB复合吹炼技术,从转炉底部吹入N2、Ar、CO2、O2四种混合气体,其中O2约占15%。
底部喷嘴采用双层套管式,炉底安装了4支喷嘴,转炉采用活炉底,可进行更换,炉底采用Mg-C质砖,最初炉底寿命仅为700~1000次。
最近已将透气元件改为透气砖,透气砖为Mg-C砖,每块透气砖内镶嵌56~60根耐热不锈钢管,不锈钢管直径为2mm。
SIB法复吹转炉由于从底部喷入部分氩气,因此,应增设C的制备系统。
一般从转炉废气中回收,要求CO2纯度>
99.25%,水分≤0.0002%。
由于采用S'
IB复合吹炼技术,扩大了转炉冶炼超低碳钢种的范围,同时获得了良好的操作指标。
(5)川崎制铁公司LD—KGC和K—BOP法
川崎制铁公司开发出两种不同类型的顶底复吹转炉,即K—BOP和ID—KGC。
K—BOP在底吹喷嘴喷人石灰的同时,还吹人一部分氧气;
ID—(GC)则在底吹喷嘴喷吹惰性气体的同时,用顶枪吹氧。
(IJ)一KGC通过提高底吹惰性气体流量来增
加熔池的搅拌力;
K—BOP法在精炼末期,混合底吹惰性气体与氧气来增加熔池搅拌。
生产中,LD—KGC法使用CO气体;
K—BOP法使用CO2气体。
(6)日本钢管公司NK—CB复吹技术
日本钢管公司开发了NK—CB复吹技术,并先后在福山一炼钢厂180t转炉和福山二炼钢厂250t转炉上采用。
从转炉底部喷吹CO2气体,冶炼极低碳钢时吹人N2和,底部喷入气体量≤0.1m3/(t·
rain),采用单管喷嘴,炉底设4支喷嘴。
采用NK—CB复吹技术冶炼低碳铝镇静钢时,金属收得率可提高0.6,铁合金消耗有所降低,其中铝降低0.35kg/t钢,Fe-Mn降低1.2kg/t钢;
石灰消耗降低3kg/t钢,转炉吹炼时间可缩短1min。
(7)转炉双联法脱磷
目前,单用转炉工艺磷含量可达到0.004~0.01。
其高低取决于铁水的硅和磷含量。
根据渣量来确定铁水硅含量,在脱磷期间形成的POS是一定的。
在日本,铁水脱磷后再进行少渣吹炼比较普及。
采用转炉双联法脱磷,钢水含磷可达0.004。
然而,在这种情况下必须注意的是,铁水脱磷必须先脱硅,转炉冶炼超低硅铁水,具有少渣操作的优越性。
另一方面,这一工艺废钢比低。
采用双联法,第一座转炉的炉渣扒掉,第二座转炉出钢后炉渣返回到第一座转炉,用于下一炉次铁水脱磷,使转炉吹炼终点磷含量达0.003。
如果出钢时带少量渣,渣中P2O5还原可使钢水回磷。
此外,添加含磷合金元素和锰铁,也能引起磷含量增加,最终产品的磷含量比转炉吹炼终点的磷含量高出0.001左右。
由此表明,选择合适的工艺步骤,可得到磷含量为0.003%~0.004%的钢。
1.4国内转炉炼钢技术的新进展
我国1964年第一座30t转炉在首钢建成投产至今,转炉技术发展迅速,已成为我国最主要的炼钢方法。
目前转炉钢产量已占我国钢产量的80%以上,超过1.6亿t,武钢、鞍钢等大型钢铁厂钢产量的100%采用转炉工艺生产。
(1)铁水预处理
铁水质量的好坏直接影响转炉炼钢的产量和质量。
国外先进钢铁厂一般均采用全量铁水预处理,日本绝大多数钢厂采用铁水全量“三脱”(脱Si、P、S),欧美钢厂以预脱硫为主。
近几年,由于洁净钢的需求日益增加,我国铁水预处理迅速推广,不少钢厂已达到国际先进水平。
如宝钢二炼钢厂250t转炉已实现100%铁水预处理,其中35%进行预脱磷处理,处理后铁水含硫量低于0.00396,含磷量低于0.0025%。
武钢二炼钢厂的KR法在粉剂消耗、搅拌头寿命、处理温降和生产成本等方面的指标已优于德国蒂森钢厂。
我国铁水预处理以预脱硫为主,处理方法多为机械搅拌法和喷吹法。
采用CaO基脱硫剂比一般喷吹法具有脱硫效率高、处理后硫含量低、处理时间短等优势。
但与镁基脱硫剂喷吹法比较,KR法温降大,铁损高。
比较混合喷吹、复合喷吹和纯镁喷吹三种镁基脱硫剂工艺,纯镁喷吹法脱硫效率高,处理后钢水含硫最低可达0.0003,工艺简单、渣量少、温降和铁损小,设备投资少、生产成本低。
如武钢二炼钢厂KR法脱硫成本为20元/t钢,武钢一炼钢厂纯镁喷吹法的处理成本仅为14.96元/t钢。
(2)转炉复合吹炼
我国转炉通过应用溅渣护炉技术,炉龄已达到国际先进水平。
2004年,全国转炉平均炉龄4674炉。
我国自主开发的长寿复吹转炉工艺技术成功地解决了底吹喷嘴与炉龄不同步的技术难题。
2004年2月武钢再次创造了30368次我国最高转炉炉龄纪录,复吹比达100%,全程底部供气元件不更换。
宝钢在300t转炉上开展了少渣炼钢工业性试验。
通过工业试验,掌握了少渣吹炼的工艺特点和规律,宝钢转炉少渣吹炼生石灰单耗达到11.3kg/t,轻烧白云石单耗达到6.3kg/t,转炉渣量仅为常规渣量的三分之一。
通过少渣吹炼,在吹炼终点碳含量大于0.10%的情况下,锰的收得率在50%以上。
本钢150t转炉是原120t转炉扩容改造的,炉容比仅为0.62,采用长寿复吹工艺后,供氧强度从2.3m3/(t·
min)提高到3.7m3/(t·
min),冶炼周期从50分钟缩短到30分钟,年钢产量提高100万吨,经济效益显著。
太钢第二炼钢厂1号转炉是由奥钢联引进的复吹转炉,生产不锈钢,而2号、3号转炉原为传统的80t顶吹转炉,生产碳钢。
为了扩大品种,提高产品质量,太钢与钢铁研究总院合作,在2004年4月将2座顶吹转炉改造为复吹转炉。
2厂址选择
本设计厂址选在吉安区市郊,随着江西省经济的迅速发展,各行业对钢材的需求也在不断上升。
尤其是特种钢材,而且人们的注意力也逐渐移向钢材的高质量,为了充分利用当地资源条件促进其他部门的发展,在吉安附近建立一个钢厂是很迫切的。
同时,优越的地理位置更提供给我们在吉安市郊建设钢厂的条件:
(1)吉安境内有自北向南纵贯的京九铁路,105国道和由东向西的319国道及“三南”公路,是连接北京、西南、华南、福建、港澳地区的天然纽带,交通便利,可以外购废钢,大吨位运输。
(2)吉安市区工业发达,钢资源丰富,而且人口众多,劳动力充足。
(3)吉安市贸易发达,进出口条件优惠,美,澳,日等多国在此均有贸易,有投资优势。
再技术改进上也有优势。
由此,本设计中年产150万吨良坯,以碳结钢、合结钢,弹簧钢为主的转炉钢厂选在吉安市郊的公路铁路沿线处。
3顶底复吹转炉炼钢的物料平衡与热平衡计算
3.1物料平衡计算
3.1.1计算所需原始数据
基本数据有:
冶炼钢种及其成份表(3-1);
金属料——铁水和废钢成分(表3-1)造渣用熔剂及炉衬等原材料的成分(表3-2);
脱氧和合金化用铁合金的成分及其回收率(表3-3);
其它工艺参数设定值表(表3-4)
表3-1冶炼钢种铁水、废钢和终点钢水的成分设定值
成分
类别
CSiMnPS
钢种Q235设定值
铁水设定值
废钢设定值
终点钢水设定值*
0.180.250.55≤0.045≤0.050
4.300.680.590.190.041
0.180.250.550.0300.030
0.10痕迹0.190.0190.029
*[C]和[Si]按实际生产情况选取;
[Mn]、[P]和[S]分别按铁水成分的30%、10%、55%留在钢水中设定。
表3-2原材料成分
CaOSiO2Mg0Al2O3Fe2O3CaF2P2O5SCO2H2OC灰分烧碱
石灰
萤石
轻烧白云
炉衬
焦炭
87.02.503.601.500.500.100.064.640.10
1.304.500.600.601.5089.000.900.101.50
34.70.8027.31.2036.0
1.503.3276.50.281.6016.8
FeO0.5881.712.25.52
表3-3铁合金成分(分子)及其回收率(分母)
CSiMnAlPSFe
硅铁
锰铁
-73.00/750.50/802.5/00.05/1000.03/10023.92/100
6.60/85*0.50/7567.80/80-0.23/1000.13/10024.74/100
*15%的C生成CO2。
表3-4其它工艺参数设定值
名称
参数
终渣碱度
萤石加入度
轻烧白云石
炉衬蚀损量
%CaO/%SiO2=3.0
为铁水的0.5%
为铁水的2%
为铁水的0.3%
渣中铁损
氧气纯度
炉气中自由氧含量
气化去硫量
为渣量的4%
99%余者为N2
0.5%(体积比)
占总去硫量的1/3
终渣含量∑FeO按(FeO)=1.35(Fe2O3)折算
12%,而(Fe2O3)/∑(FeO)=1/3,即(Fe2O3)=4.8%,(FeO)=7.9%
金属中[C]的氧化物
85%C氧化为CO,15%氧化为CO2
烟尘量
为铁水量的1.5%(其中FeO为83%,Fe2O3为
12%
废钢量
由热平衡计算确定,本计算结果为铁水量的21.38%,即废钢比为17.6%
喷溅铁损
为铁水量的0.2%
3.1.2计算步骤:
以100kg铁水为基础进行计算
第一步、计算脱氧和合金化前的总渣量及其成份
总渣量包括铁水中元素氧化,炉衬蚀损和加入熔剂的成渣量。
其各项成渣量及成分分别列于3-5,3-6,3-7。
总渣量及其成分如表3-8所示
第二步:
计算氧气消耗量
氧气消耗量是消耗项目与供入项目之差,详见表3-10所示
表3-5铁水中元素的氧化产物及其成渣量
元素
反应产物元素氧化量(kg)耗氧量(kg)产物量(kg)
备注
C
Si
Mn
P
S
Fe
[C]→{CO}4.20×
85%=3.5704.7608.330
[C]→{CO2}4.20×
15%=0.6301.6802.310
[Si]→(SiO2)0.6800.7771.457
[Mn]→(MnO)0.4000.1160.516
[P]→(P2O5)0.1710.2210.392
[S]→{SO2}0.012×
1/3=0.0040.0040.008
[S]+(CaO)→
(CaS)+(O)0.012×
2/3=0.008-0.004*0.018(CaS)
[Fe]→(FeO)0.821×
56/72=0.6390.1830.821
[Fe]→(Fe2O3)0.821×
112/160=0.3230.1380.461
入渣
入渣(表3-8)
合计
6.4257.875
入渣组分之和:
3.665
成渣量
*由CaO还原出的氧量;
消耗的CaO量0.008×
56/32=0.014kg
表3-6炉衬蚀损的成渣量
成渣组分(kg)
气态产物(kg)
耗氧量(kg)
0.3
(据表2-4)
CaOSiO2MgOAl2O3Fe2O3
0.00450.0100.22950.00080.0048
C→CO
0.3×
16.8%×
85%×
28/12=0.100
C→CO2
15%×
44/12=0.028
C→CO,CO2
16.8%(85%×
16/12+15%×
32/12)=0.077
0.2496
0.128
0.077
表3-7加入熔剂成渣量
加入量
(kg)
CaOMgOSiO2Al2O3Fe2O3P2O5CaSCaF2
H2OCO2O2
轻烧白云山
石灰
0.5
2
4.95*1
0.0060.0030.0220.0080.0080.0050.0010.445
0.6940.5460.0160.024
4.289*20.1780.1240.0740.0250.0050.0067
0.008
0.72
0.0050.22970.001*3
4.9890.7270.1620.1060.0330.0100.0080.