18.浪费.ppt
《18.浪费.ppt》由会员分享,可在线阅读,更多相关《18.浪费.ppt(46页珍藏版)》请在冰豆网上搜索。
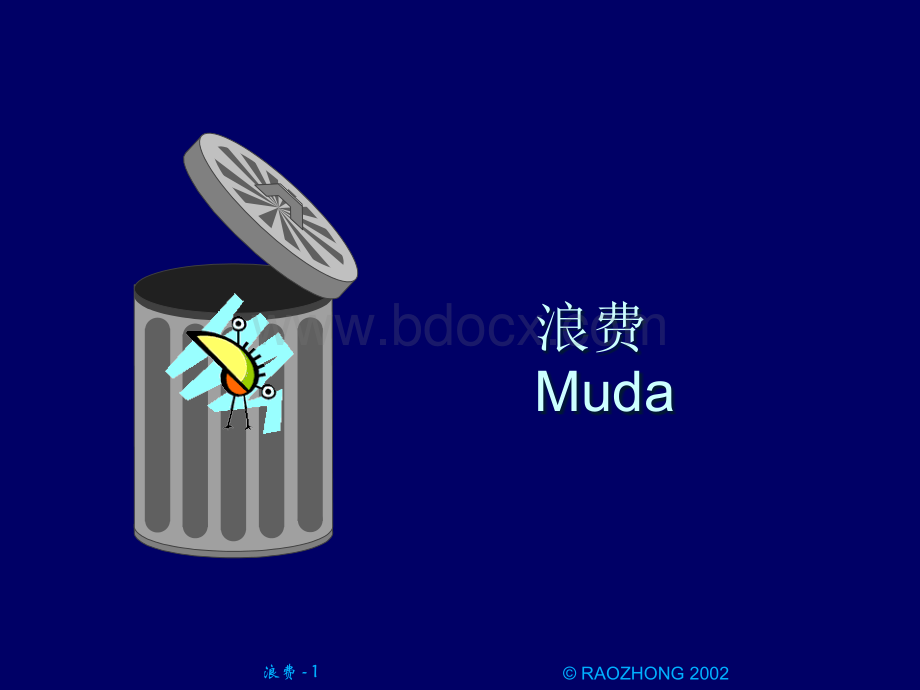
浪费-1RAOZHONG2002浪费Muda浪费-2RAOZHONG2002利润的源泉成本利润售价=成本+利润利润成本成本利润利润=售价-成本成本=售价-利润价格浪费-3RAOZHONG2002利润的源泉价格成本利润成本利润利润成本浪费-4RAOZHONG2002浪费MudalMuda是日文浪费的意思。
但Muda还带有更深一层的内涵。
l工作是由一系列的流程或步骤所构成的。
从原材料开始,到最终产品或服务为止,在每一个流程,将价值加入产品内(在服务业里,是把价值加入文件或其他的信息内),然后再送到下一个流程。
在每一个流程里的人力或机器资源,若不是从事有附加价值的动作,就是进行无附加价值的动作。
浪费-5RAOZHONG2002Muda的三种形态1.勉强勉强:
超过能力界限的超负荷状态。
2.浪费浪费:
有能力,但未给予充足的工作量的未饱和状态。
3.不均衡不均衡:
有时超负荷有时又不饱和的状态。
即差异状态。
浪费-6RAOZHONG2002Muda的三种状态不不均均衡衡勉勉强强合合适适浪浪费费浪费-7RAOZHONG2002不饱和vs超负荷l不饱和指的是生产计划安排散乱,工作量不足,造成生产力浪费的现象(人员方面的工作负荷量,设备方面的机器稼动率)。
l超负荷指的是对于机械设备及人的能力来说,过度的负荷。
超负荷导致机械设备的故障、品质的低下及人员的不安全行为。
浪费-8RAOZHONG2002Muda的分类1.制造过多的Muda。
2.存货的Muda。
3.不良重修的Muda。
4.动作的Muda。
5.加工的Muda。
6.等待的Muda。
7.搬运的Muda。
浪费-9RAOZHONG2002制造过多的Mudal制造过多又称中间在库过多,就是在一个工序到下一个工序的中间准备了过多的量。
浪费-10RAOZHONG2002制造过多的Muda:
原因l担心机器故障l担心生产不合格品l担心员工缺席l浪费-11RAOZHONG2002制造过多的Muda:
后果l提早耗用原材料l浪费人力及设施l增加机器负荷l增加利息负担l增加额外的空间以储存多余的存货l增加搬运和管理成本浪费-12RAOZHONG2002l零件、半成品需要先行生产而导致不同步的时间和空间浪费;l生产用电、气、油、水等能源的浪费;l货架台、材料搬运等的增加;l放置地、仓库等存储空间的占用;l在库的发生与管理工时的增加;l利率负担的增加;浪费-13RAOZHONG2002制造过多的Muda:
对策l要考虑到下一个流程或下一条生产线的正确生产速要考虑到下一个流程或下一条生产线的正确生产速度;而不要只尽所能,在本流程生产过多的产品。
度;而不要只尽所能,在本流程生产过多的产品。
l不要让作业员有生产伸缩的充分空间。
不要让作业员有生产伸缩的充分空间。
l不要让每一流程或生产线有提高自己的生产力的利不要让每一流程或生产线有提高自己的生产力的利益。
益。
l不要因为有不合格品而想提高直通率。
不要因为有不合格品而想提高直通率。
l不要因为有多余的产能而容许机器生产多于所需之不要因为有多余的产能而容许机器生产多于所需之量。
量。
l不要因为引进了昂贵的机器设备,而为折旧费的分不要因为引进了昂贵的机器设备,而为折旧费的分摊,提高稼动率,生产过多的产品。
摊,提高稼动率,生产过多的产品。
浪费-14RAOZHONG2002存货的Muda库存包括:
l零部件、材料的库存l半成品的库存l成品的库存l已向供应商订购的在途物料l已发货的在途成品浪费-15RAOZHONG2002存货的Mudal成品、半成品、零件及物料的存货,是不会产生任何附加价值的,反而增加了营运的成本。
库库库库存存存存生产问题生产问题生产问题生产问题机器延迟机器延迟机器延迟机器延迟供应商供应商供应商供应商的过失的过失的过失的过失废料废料废料废料在制品堆积在制品堆积在制品堆积在制品堆积工程设计工程设计工程设计工程设计重复重复重复重复改变改变改变改变顺序顺序顺序顺序检查检查检查检查延迟延迟延迟延迟文件文件文件文件延迟延迟延迟延迟订单处订单处订单处订单处理延迟理延迟理延迟理延迟决策决策决策决策缓慢缓慢缓慢缓慢浪费-16RAOZHONG2002欧美VS日本欧美的观点:
l通过库存可以得到:
4平稳的生产过程平稳的生产过程4及时交货及时交货4避免故障的影响避免故障的影响4经济性地生产经济性地生产4高利用率高利用率日本的观点:
l库存掩盖的问题:
4不稳定的生产过程不稳定的生产过程4生产能力不平衡生产能力不平衡4缺乏灵活性缺乏灵活性4易产生废品易产生废品4按时交货能力差按时交货能力差浪费-17RAOZHONG2002存货的Muda存货的浪费主要表现在:
l零部件、产品陈旧导致削价与报废损失;l流动资金占用损失;l人工场地损失;l隐藏不良品损失;l隐藏产能不平衡与过剩损失;l隐藏机器故障损失;l浪费-18RAOZHONG2002不良重修的Mudal不良重修的浪费指在工厂内发生不良,需要进行处置的时间、人力和物力的浪费:
4产品报废产品报废4降价处理降价处理4材料损失材料损失4人工设备资源损失人工设备资源损失4出货延误取消订单出货延误取消订单4信誉下降信誉下降4市场份额萎缩市场份额萎缩浪费-19RAOZHONG2002不良重修的Mudal干扰生产活动l耗费昂贵的重修费用l资源及设备的最大浪费l浪费-20RAOZHONG2002动作的Mudal任何人体的动作,若是没有直接产生附加价值,就是没有生产力。
浪费-21RAOZHONG2002动作的Mudal人在走路时,并没有增加价值。
l提起或持着一个重物,需用到作业员身体的一部分的特别体力的动作,应予以避免。
l可以借由工作地点的重新安排,来剔除作业员手持重物走路的动作l重新安排物料放置的方式,开发适当的工具及夹具。
浪费-22RAOZHONG200212种动作上的浪费1.两手空闲的浪费2.单手空闲的浪费3.作业动作停止的浪费4.作业动作太大的浪费5.拿的动作交替的浪费6.步行的浪费7.转身角度太大的浪费8.动作之间没有配合好的浪费9.不了解作业技巧的浪费10.伸背动作的浪费11.弯腰动作的浪费12.重复动作的浪费浪费-23RAOZHONG2002加工的Mudal机器加工作行程过长或过分加工l冲床没有生产力的冲击时l去毛边的动作ll“过分精确加工的浪费”浪费-24RAOZHONG2002等待的Mudal作业员停滞不动时,就是等待的Muda发生浪费-25RAOZHONG2002等待的Mudal生产线的机种切换l每天的工作量变动很大,工作量少时无所事事l因缺料而使机器闲置l因过程上游发生延误,导致下游无事可做l因早会、开会占用太多的时间l机器设备时常发生故障l生产线未能平衡,导致等待发生l劳逸不均浪费-26RAOZHONG2002等待的Muda:
原因l生产线不平衡l缺料l机器故障l机器在进行附加价值的加工,作业员在旁监视l作业员员在拼命工作,机器在等待浪费-27RAOZHONG2002搬运的Mudal物料及产品的移动,并不能产生附加值;l搬运过程中,经常会发生物品的损伤;ll离岛作业应尽可能并入主生产线内浪费-28RAOZHONG2002Muda的分类表MudaMuda类别类别类别类别MudaMuda性质性质性质性质MudaMuda去除去除去除去除半成品半成品没有立即需求的库存品没有立即需求的库存品流水线化库存流水线化库存不合格品不合格品生产不合格的产品生产不合格的产品降低不合格品降低不合格品设施设施闲置机器,故障,换模时间过长闲置机器,故障,换模时间过长提高设备利用率提高设备利用率费用费用对需要的产能做过度的投资对需要的产能做过度的投资削减费用削减费用间接员工间接员工由于不合格的间接员工的体制,由于不合格的间接员工的体制,形成人员过多形成人员过多有效地安排工作有效地安排工作设计设计生产超过需求功能的产品生产超过需求功能的产品降低成本降低成本才能才能雇用员工从事可以被机械化的工雇用员工从事可以被机械化的工作或派至低级技术的工作作或派至低级技术的工作建立劳力节约及最佳化建立劳力节约及最佳化的衡量的衡量动作动作不依照标准作业工作不依照标准作业工作改进作业标准改进作业标准新产品上市新产品上市新产品生产的稳定化开始过慢新产品生产的稳定化开始过慢更快地转变为全能生产更快地转变为全能生产浪费-29RAOZHONG2002发现MUDA的五个要点1.3现原则2.对作业反问3.讲究技能4.本质技能以外全部是浪费5.对浪费作业的反问(5WHY)浪费-30RAOZHONG2002作业效率低下分析表作业效率低工时浪费机种之间不平衡工程之间不平衡制造过多的制造过多的MudaMuda存货的存货的MudaMuda不良重修的不良重修的MudaMuda动作的动作的MudaMuda。
加工的加工的MudaMuda等待的等待的MudaMuda搬运的搬运的MudaMuda平衡性浪费浪费-31RAOZHONG2002消除浪费降低成本的过程第一层次的浪费(过剩的生产能力)过多的人员过剩的设备过剩的库存多余的劳务费多余的折旧费多余的利息支出第二层次的浪费(最大的浪费)制造过剩的浪费(工作进展过度)用能销售的速度制造(丰田生产方式的中心课题)等待时间显在化消除制造过剩的浪费第三层次的浪费过剩库存的浪费利息支出(机会成本)的增加第四层次的浪费多余的仓库多余的搬运工多余的搬运设备多余的库存管理、质量维护人员多余的电脑消除第三和第四层次的浪费以作业的再分配减少人员设备折旧费和间接劳务费等的增加产品成本增加间接制造费降低劳务费降低产品成本降低浪费-32RAOZHONG2002向MUDA挑战!
l流线化生产l安定化生产l平稳化生产l超市化生产浪费-33RAOZHONG2002流线化生产的要点1.按工程顺序排列制程与设备。
2.一个一个的生产。
3.多能工的多工程操作。
4.站立作业是流动的根本。
5.生产线U型化。
6.善用小型化、廉价的设备。
7.配合循环时间来生产。
浪费-34RAOZHONG2002安定化生产的要点:
l人员的安定。
l设备的安定。
l品质的安定。
l物量的安定。
l管理的安定。
浪费-35RAOZHONG2002平稳化生产的要点1.破除批量生产的神话。
2.学习快速换线的能力。
3.建立少量化的供料方式。
4.追求混流生产的最高境界。
浪费-36RAOZHONG2002改革的十项阻力1.那些是没有作用的2.虽然的确如此,但对我们不适合3.办法是不错,但是.4.成本已无法再降低5.我们也都是那样做的6.经由别人劝说才做,大家都很不喜欢7.成本若降低,品质也会下降8.不是都很顺利吗?
为什么要改变?
9.那些是行不通的!
我们早就做过了10.我们对那些事情再清楚不过了浪费-37RAOZHONG2002推动改善的基本精神l舍弃作法上的固定观念。
l提出不能做的理由,还不如去思考做的方法。
l不要太要求完美。
l没有遇到困扰,就不会产生智能。
l追求真因。
l改善是永无止境的。
浪费-38RAOZHONG2002消除浪费的七种基本方法1.集中工厂网络2.成组技术3.源头质量的控制4.JIT生产5.均衡生产负荷6.看板生产控制系统7.最小化换模时间浪费-39RAOZHONG20021.集中的工厂网络l日本人更喜欢建立小规模专业化工厂而不是大型纵向一体化的制造厂。
l按照同一目标设计的多家工厂可以更好地组织起来,并使经营更加经济。
l在日本企业中,约有60000个企业的规模在301000个员工之间。
浪费-40RAOZHONG20022.成组技术l产生于美国,最成功的应用却是在日本。
l成组技术单元减少了不同操作间的移动、等待时间和在制品库存。
l减少了所需的员工人数。
浪费-41RAOZHONG2002锯锯锯车削车削热处理模压模压磨磨车削12345专业化分工单元浪费-42RAOZHONG2002成组技术生产单元锯车削磨锯车削热处理模压模压车削1A车削磨B2浪费-43RAOZHONG20023.源头质量的控制l工作之初就要做的十分正确l出现错误立即停止该工序或装配线l工人成为自己工