固定管板式换热器管箱设计Word下载.docx
《固定管板式换热器管箱设计Word下载.docx》由会员分享,可在线阅读,更多相关《固定管板式换热器管箱设计Word下载.docx(18页珍藏版)》请在冰豆网上搜索。
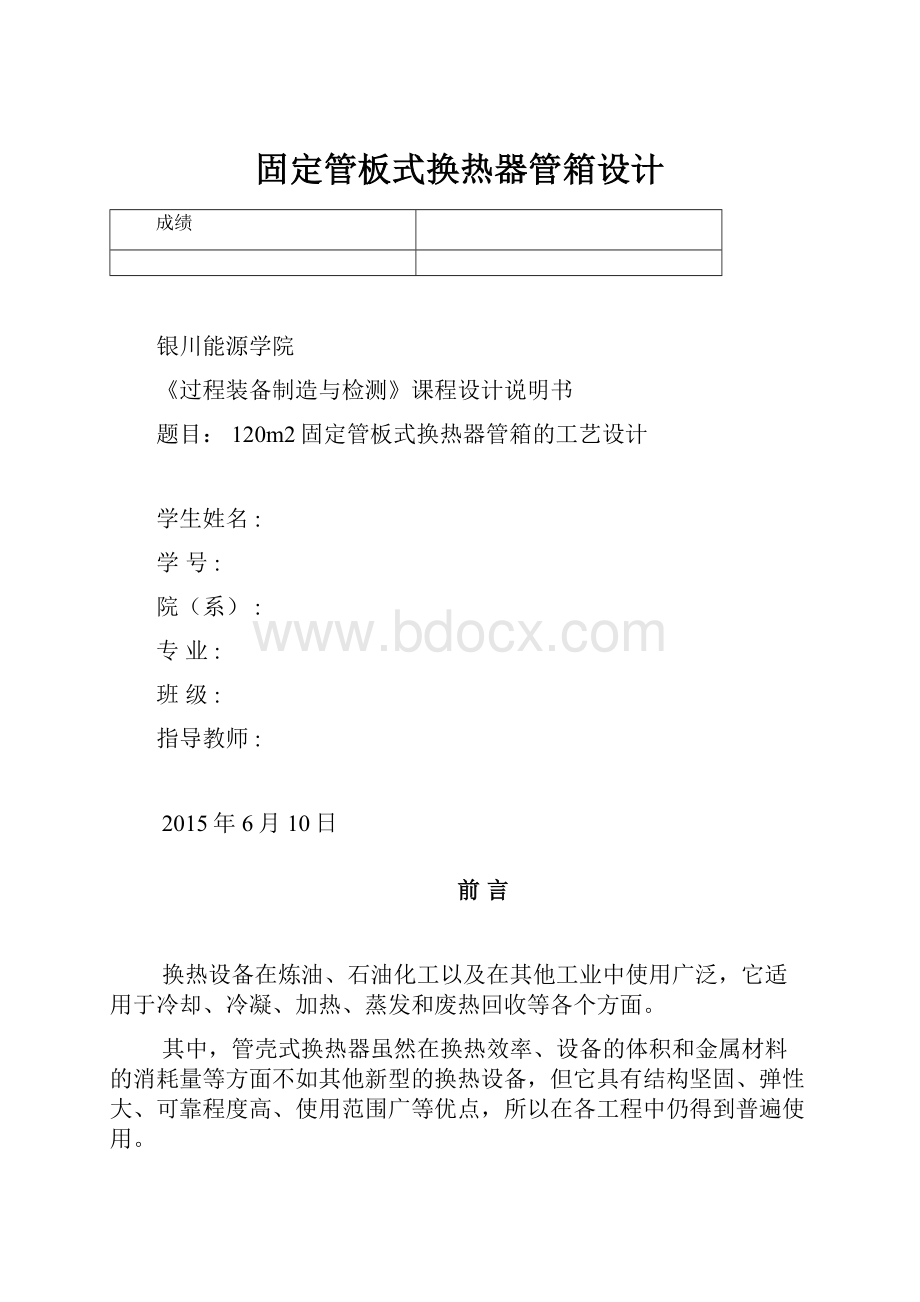
工作温度
180—200℃
375℃
工作压力
1.3MPa
2.5MPa
换热面积:
换热器材料:
设计寿命:
15年
封头公称直径:
封头壁厚:
采用标准椭圆形封头
封头直边段高度:
封头曲面高度:
直径:
1.3.设计内容
(1)工艺设计:
坯料准备;
材料的净化;
成形加工;
典型缺陷分析;
组对焊接;
成形后热处理及其检测等;
(2)工艺设计小结;
(3)绘制设备结构简图以及焊缝结构详图(A4图纸)及编写课程设计说明书
二、封头成型的主要步骤及工序
随着石油化工设备的大型化发展,对大型封头的需要量也相应增多,这给冲压成型带来了困难。
此外,大型封头有多属单件,模具成本高,故且对于大型封头采用旋压成型较为优越。
当然旋压成型制造小型封头也有特色。
一个标准封头的成型要经过一下几个步骤及工序:
将经检验合格的钢板进行矫形和净化→钢板的划线→切割→旋压→封头端面加工(切余量,切坡口)。
三、材料的预处理
钢材的预处理是对钢板,管子和型钢等材料的净化处理,矫正和涂保护处理,钢材在加工前(即原材料状态)进行表面抛丸除锈并涂上一层保护底漆的加工工艺。
钢材经过预处理可以提高机械产品和金属构件的抗腐蚀能力,提高钢板的抗疲劳性能,延长其使用寿命;
同时还可以优化钢材表面工艺制作状态,有利于数控切割机下料和精密落料。
此外,由于加工前钢材形状比较规则,有利于机械除锈和自动化喷漆,因此采用钢材预处理可大大提高清理工作的效率,减轻清理工作的劳动强度和对环境的污染。
3.1净化处理
a喷砂法:
是目前国内常用的一种机械净化方法,主要用于钢材和设备大表面的净化处理。
可除锈、氧化皮等,效率较高,但粉尘大对人体有害,应在封闭的喷砂室内进行。
b抛丸法:
主要特点是改善了劳动条件,容易实现自动化,被处理材料表面质量控制方便。
c化学净化法:
金属表面的化学净化处理主要是对材料表面进行除锈,除污物和氧化、磷化和钝化处理,后者即在除锈、除污物的基础上根据不同材料,将清洁的金属表面经化学处理(氧化、磷化和钝化)形成保护膜,以提高防腐能力和增加金属与漆膜的附着力。
由于以上各种处理方法综合考虑使用喷砂法对Q245R进行表面净化处理。
3.1.1喷砂发操作规程:
1、工作前必须穿戴好防护用品,不准赤裸膀臂工作。
工作时不得少于两人。
2、储气罐、压力表、安全阀要定期校验。
储气罐每两周排放一次灰尘,沙罐里的过滤器每月检查一次。
3、检查通风管及喷砂机门是否密封。
工作前五分钟,须开动通风除尘设备,通风除尘设备失效时,禁止喷砂机工作。
4、压缩空气阀要缓慢打开,气压不准超过0.8MPa。
5、喷砂粒度应与工作要求相适应,一般在十至二十号之间适用,砂子应保持干燥。
6、喷砂机工作时,禁止无关人员靠近。
清扫和调整运转部位时,应停机进行。
7、不准用压缩空气吹身上灰尘或开玩笑。
8、工作完后,通风除尘设备应继续运转五分钟再关闭,以排出室内灰尘,保持场地清洁。
9、发生人身、设备事故,应保护现场,并报告有关部门。
3.2矫形
原理矫正就是使钢板或工件在外力的作用下产生与原来变形相反的塑性变形,已消除弯曲、扭曲、皱折、表面不平等变形,从而获得正确形状的过程。
矫形原因钢材由于生产、贮运等原因,以及经过冲、剪分离等初加工制成零件毛坯料后,可能会出现各种各样的变形。
在转下道工序前,工艺要求需对其进行矫正,这个工序称为钢材变形的矫正。
矫形方法机械矫正和火焰矫正。
机械矫正又分为手工矫正、拉伸机矫正、压力矫正、辊式矫板机矫正、斜辊矫管机矫正、型钢矫正机矫正。
由于以上几种矫正方法的特点,综合选用火焰矫正。
3.2.1火焰矫正
在轴类零件弯曲的最高点区域内,用氧乙炔焰进行点热,由于加热点受热膨胀,使轴的弯曲程度增大,但立即浇水冷却,工件骤冷收缩,使轴两端上挠,而且上挠量超过加热时增加的弯曲度,超过部分就是矫正量。
校正方法:
A)角变形的校正,在角变形板上面(对准焊缝外)纵向线状加热(加热温度控制在650度以下),注意加热范围不超过两焊脚所控制的范围,所以不用水冷却。
线状加热时要注意:
a不应在同一位置反复加热;
b加热过程中不要进行浇水。
B)上拱与下挠及弯曲变形的校正,对着纵长变形处,由中间向两端作线状加热,即可校正弯曲变形。
为避免产生弯曲和扭曲变形,两条加热带要同步进行。
可采取低温校正或中温校正法。
C)波浪变形校正,波浪变形首先要找出凸起的波峰,用圆点加热法配合手锤校正。
加热圆点的直径一般为50~90mm,当钢板厚度或波浪形面积较大时直径也应放大,烤嘴从波峰起作螺旋形移动,采用中温校正。
当温度达到600~700度时,将手锤放在加热区边缘处,再用大锤击手锤,使加热区金属受挤压,冷却收缩后被拉平。
校正时应避免产生过大的收缩应力。
校完一个圆点后再进行加热第二个波峰点,方法同上。
为加快冷却速度,可对钢材进行加水冷却。
这种校正方法属于点状加热法,加热点的分布可呈梅花形或链式密点形。
注意温度不要超过750度。
火焰校正注意事项
1、烤火位置不得在最大应力截面附近;
2、校正处烤火面积在一个截面上不得过大,要多选几个截面;
3、宜用点状加热方式,以改善加热区的应力状态;
4、加热温度最好不超过700度。
四、下料
4.1换热器封头的壁厚计算
由于椭圆形封头属于不可展的零件,但生产中冲压加工或旋压加工是毛坯料展开后的图形都为圆形,所以只需要求出展开后的半径或直径即可
故采用经验法进行计算
---为包括了加工余量的展开直径;
---为经验系数
---封头中性层处直径
---封头的直边高
经查《过程装备制造与检测》表6-20,由椭圆封头
∶
,所以K取1.19
封头的公称直径
,
选取800mm,厚度6.7mm
中性层直径
根据《化工设备课程设计指导》表3-3查得标准椭圆形封头工称直径是800时总深度为225mm又公式
计算得直边高度h=25mm
展开直径
划线完成后,为保证加工尺寸精度及防止下料尺寸模糊不清等,在切割线、刨边线、开孔中心及装配线等处均匀打上冲眼,用油漆标明标号、产品工号和材料标记移植等,以指导切割,成型,组焊等后续工序的进行。
五、设备选用及模具设计
5.1计算冲压力
计算冲压力时影响因素较多,且冲压过程是变化的较复杂,目前计算冲压力常用下面公式:
C——压边力影响系数,无压边力C=1,有压边力C=1.2;
K——封头形状影响系数,椭圆封头K=1.25-1.35;
D0——封头外径,mm
Dw——筒节外径,mm
采用压边圈是毛坯料只能在压边圈与下模之间滑动,可以防止折皱的产生,而且在有压边圈产生的摩擦力作用下,增加了经向拉应力,也有利于防止封头鼓包的尝试。
因此,确定在什么条件下需要采用压边圈是关系到封头质量好坏的重要因素。
采用压边圈的条件主要决定与Do,Dn,与δ的关系条件如下公式
~
Do:
毛坯直径,1009.973mm;
Dn:
封头内径,800mm;
δ:
钢板厚度,6.7mm
Do—Dn=1009.973-800=209.973≥134因此需不采用压边圈
故取C=1,椭圆封头取K=1.3
冲压力
封头的冲压成型通常是在50~8000t水压机或油压机上进行,此处选择2000t
的水压机。
5.2模具设计
上模(冲头)其结构及主要设计参数
a)上模直径
根据封头内径和热冲压的收缩率
或冷冲压的回弹率
计算,主材为Q245R取
%
~
b)上模曲面部分高度
c)上模直边高度
----封头直边高度,25mm
----封头高度修边余量,一般为15-40mm,取H1=20mm
----卸料板厚度,一般为40-80mm,取H2=50mm
----保险余量,一般为40-100mm,取H3=50mm
所以
d)上模上部分直径
e)上模壁厚δ
当水压机吨位小于等于400t时,δ=30~40mm
当水压机吨位大于等于1500t时,δ=70~80mm,取δ=75mm
f)上下模间隙a,附加值z——热冲压时
z=(0.1~0.2)δ=(0.1~0.2)×
6.7=5-10mm
椭圆封头取较大值Z=10mm。
a=δ+z=6.7+10=16.7mm
g)下模内径
---下模制造公差,取δm=2mm
=(794.4~805.6)+2×
16.7+2=(829.8~841)mm
h)下模圆角半径r
根据经验选取,不采用压边圈时,r=(4~6)δ=5×
6.7=33.5mm
i)下模直边高度h1
=(40~70)mm,取
=50mm
j)下模总高度h
h=(100-250)mm,取h=200mm
k)下模外径D1
=
+(200~400)mm=(1229.8~1241)mm
l)下模座
外径D应大于毛坯直径D0,,高度H=h+(60-100)=25+70=95mm
下口内径D2应比与之配套的最大壁厚封头的下模内径Dxm大(5-10)mm
m)压边圈
其主要尺寸为;
内径Dn’=Dxm+(50~80)mm;
外径Dw’=D下模座外径mm;
厚度δ’=70~120mm
六、封头的成型及其方法
封头的成形方法主要有:
冲压成形、旋压成形、爆炸成形
图1
6.1封头冲压
1).封头冲压时,板坯塑性变形很大,且为厚壁中压封头封头冷热冲压与相对厚度的关系见表2。
表2封头冷热冲压与相对厚度的关系
冲压状态
碳素钢,低合金钢
合金钢,不锈钢
冷冲压
δ/Do×
100≤0.5
100≤0.7
热冲压
100≥0.5
100≥0.7
100=6.7/1009.973×
100=0.7≥0.7故用热冲压。
2).冲压前,把板坯加热至始锻温度放在压力机上冲压,到终锻温度时停止冲压毛坯热冲压的加热温度的选择。
封头冲压时,板坯塑性变形很大,且为厚壁高压封头,故用热冲压,冲压前,把板坯加热至始锻温度,放在压力机上冲压,到终锻温度时停止冲压。
3).冲压加工常用的润滑剂润滑剂选取石墨粉+水
4).冲压过程:
椭圆形下封头采用厚板在2000t水压机上整体冲压成形,关键条件是有合适吨位、开档、行程的水压机和相应的工装模具,高温加热炉以及合理的冲压工艺。
将毛坯对中放在下模(冲环)上,然后开动水压机使活动横梁空程向下,上模(冲头)空程下降,当与毛坯接触时,开动主缸使上模向下冲压,对毛坯进行拉伸,至毛坯完全通过下模后,封头便冲压成形。
最后开动提升缸和回程缸,将上模向上提起,与此同时用脱模装置将包在上模上的封头脱下,并将封头从下模支座中取出,冲压过程即告结束。
6.1.1封头冲压及其应力分析、典型缺陷分析
封头的冲压过程属于拉延过程,在冲压过程中各部分的应力状态和变形情况都不同,处于压边圈下部分的毛坯边缘部分,由于封头的下压力使其经受径向拉伸应力,并向中心流动,坯料外直径减小;
边缘金属沿切向收缩,产生切向压缩应力,会使毛坯边缘丧失稳定而产生褶皱;
常用压边圈将边缘压紧,则在板厚方向又产生压应力,即材料承受三向应力状态。
处于下模圆角部分的材料,除受到径向拉伸应力和切向压缩应力外,还受到弯曲而产生弯曲应力。
考虑到该板相对厚度较大,固没有采用压边圈。
在冲头与下模空隙的部分金属材料,仍受径向拉伸应力和切向压缩应力,而板厚方向不受力,处于自由状态;
封头底部的金属材料,径向和切向都受到拉应力,有较小的伸长,所以壁厚略有减薄。
6.1.2封头冲压时常出现的缺陷
有拉薄、褶皱和鼓包等,其影响因素很多,简要分析如下:
a).拉薄碳钢封头冲压后,其壁厚会产生不等程度的变化球形封头深度大,底部拉伸减薄最多。
b).褶皱冲压时板坯周围的压缩量最大,其值为△L=∏(Dp-Dm)式中Dp——坯料直径;
Dm——封头中径。
封头越深,毛坯直径越大,周围缩短量也越大,周向缩短产生两个结果,一个是工件周边区的厚度和径向长度均有所增加,另一个是过分的压应变使板料产生失稳而褶皱。
板热加热不均、搬运和夹持不当造成坯料不平,也会造成褶皱。
c).鼓包产生原因与褶皱类似,但主要影响因素是拼接焊缝余量的大小以及冲压工艺方面的原因,如加热不均匀,压边力太小或不均匀、封头与下模间隙太大以及下模圆角太大等。
6.1.3采取措施:
板坯加热均匀;
选定合适的下模圆角半径;
降低模具(包括压边圈)表面的粗糙程度;
合理润滑以及在大批量冲压封头时应适当冷却模具。
超声波检测,冲压成型后的封头要进行超声波检测测其厚度,使其厚度达到标准值,因为其热冲压成型后厚度有减薄。
6.3旋压成型
特点:
1)适合制造尺寸大,壁薄的大型封头。
2)旋压机比水压机轻巧,制造相同尺寸的封头,比水压机轻约2.5倍。
3)旋压模具比冲压模具简单,尺寸小,成本低。
4)工艺制备更换时间短,占冲压加工的1/5左右,适合于单件小批生产。
5)封头成型质量好,不易产生减薄和折皱。
6)压鼓机配有自动操作系统,翻边机的自动化程度也很高,操作条件好。
七.焊接
7.1焊接接头的分类
焊接,也称作熔接、镕接,是一种以加热、高温或者高压的方式接合金属或其他热塑性材料如塑料的制造工艺及技术。
a)壳体圆筒部分的纵向接头、球形接头与圆筒连接的环向接头、各类凸形封头中的所有拼焊接头以及嵌入式接管与壳体对接连接的接头,均属A类焊接接头。
b)壳体部分的环向接头、锥形封头小端与接管连接的接头、长颈法兰与接管连接的接头,
均属B类焊接接头,但已规定为A类的焊接接头除外。
c)平盖、管板与圆筒非对接连接的接头,法兰与壳体、接管连接的接头,内封头与圆筒的搭接接头,均属C类焊接接头。
d)接管、人孔、凸缘、补强圈等与壳体连接的接头,均属D类焊接接头,但已规定为A、B类的焊接接头除外。
e)非受压元件吊耳、支座垫板与压力容器连接的焊缝,均属E类焊接接头。
图2
7.2焊接方法的分类
焊接方法的分类很多,按照焊接过程中金属所处状态的不同,可以把焊接方法分为熔化焊、压力焊和钎焊三类。
每类又分为各种不同的焊接方法。
至于金属热切割、喷涂、碳弧气刨等均是跟焊接方法相近的金属加工方法,通常也属于焊接专业的技术范围。
(a)熔化焊
焊接过程中,将焊件接头加热至熔化状态,不加压力完成焊接的方法称为熔焊。
常用的熔焊方法有电弧焊、气焊、电渣焊等。
(b)压力焊
焊接过程中,必须对焊件施加压力(加热或不加热),以完成焊接的方法称为压焊。
常用的压焊方法有电阻焊(对焊、点焊、缝焊)、摩擦焊、旋转电弧焊、超声波焊
(c)钎焊
焊接过程中,采用比母材熔点低的金属材料作钎料,将焊件和钎料加热到高于钎料熔点、低于母材熔点的温度,利用液态钎料润湿母材,填充接头间隙并与母材相互扩散实现连接焊件的方法称为钎焊。
常用的钎焊方法有火焰钎焊、感应钎焊、炉中钎焊、盐浴钎焊和真空钎焊等。
7.2.1手工电弧焊有以下特点:
(1)操作方便,使用灵活,适应性强。
适用于各种钢种,各种XX,各种位置和各种结构的焊接。
特别是对不规则的焊缝,短焊颖,仰焊缝,高空和位置狭窄的焊缝,均能灵活运用,操作自如。
(2)焊接质量好。
因电弧温度高,焊接速度较快,热影响区小,焊接接头的机械性能较为理想。
另外,由于焊条和电焊机的不断改进,在常用的低碳钢和低合金钢的焊接结构中,焊缝的机械性能能够有效地控制,达到与母材等强的要求。
对于焊缝缺陷,在一定范围内可以通过提高焊工水平、改进工艺措施得到克服。
(3)手工电弧焊易于分散应力和控制变形。
所有焊接结构中,因受热应力的作用,都存在着焊接残余应力和变形,外形复杂的焊缝、长焊缝和大工件上的焊缝,共残余应力和变形问题更为突出。
采用手工电弧焊,可以通过工艺调整,如跳焊、逆向分段焊、对称焊等方法,来减少变形和改善应力分布。
(4)设备简单,使用维护方便。
无论交流电焊机还是直流电焊机,焊工都容易掌握,使用可靠,维护方便。
不象埋弧焊、电渣焊设备那样复杂。
(5)由于手工操作,生产效率低,焊工的劳动强度也比较大。
(6)焊接质量不稳定。
手工电弧焊的焊接质量,与焊工的技能有关,培训焊工技能的难度较大,也由于手工操作的随意性比较大,使焊接质量不稳定,这是手工电弧焊的最大缺点。
所以采用手工电弧焊,它的优点突出
7.3焊接坡口的种类
为了保证焊接质量,在焊接前对工件需要焊接处进行的加工,可以气割,也可以切削而成,一般为斜面,有时也为曲面。
!
比如两块厚10mm的钢板要对焊到一起,为了焊缝牢固,会在板边缘铣出倒角,这个就叫开坡口。
由于材料厚度和焊接质量要求的不同,其焊接接头形式与坡口形状也不尽相同,一般坡口形式分为K型、V型、I型、U型、X型等。
见下图3(图3-12)
焊条电弧焊常用坡口形式和尺寸.
图3
焊接坡口是为了保证工件根部焊透,便于清理焊渣,获得较好的焊缝成形。
焊件开坡口时,沿焊件接头坡口根部的端面直边部分,叫钝边。
钝边的作用是防止根部烧穿,但钝边值太大,又会使根部焊不透。
常规的坡口手段有比较原始的砂轮机打磨,半自动火焰切割机开坡口,直流焊机碳弧气刨,大型铣边机,刨边机或者就是比较现代的带有无限旋转火焰三割炬切割机或者VBA无限旋转等离子切割机在下料时就把坡口开好。
以上几种坡口手段往往都存在效率低,成本高,粉尘,飞溅,热变形或者占地面积大等多种缺点;
机械加工制造能力生产制造出自动行进式钢板坡口机,解决相当部分的中薄板材的坡口问题,具有高效,环保,低成本,低能耗等多项优点。
本文通过采用I形坡口
八、检测
8.1.检测方式
检测方式有:
:
X光射线探伤、超声波探伤、磁粉探伤、渗透探伤、涡流探伤、γ射线探伤、萤光探伤、着色探伤等方法。
本次采用荧光检测
8.2.荧光检测的介绍及其原理
将溶有荧光染料的渗透剂渗入工件表面的微小裂纹中,清洗后涂吸附剂,使缺陷内的荧光油液渗出表面,在紫外线灯照射下显现黄绿色荧光斑点或条纹,从而发现和判断缺陷的方法。
荧光探伤应属于液体渗透探伤。
荧光探伤用来检验零件表面的缺陷。
可检验磁性和非磁性金属材料,也可以检验非金属材料。
探伤原理:
利用荧光物质在紫外丝照射下发光的性质,将荧光物质涂在零件表面上,借助荧光检验零件表面缺陷。
九.小结
1本次采用的材料为Q245R,公称直径为Dn=800mm,长L=4500mm,筒体名义厚度为16mm.封头的名义厚度为8mm.
2卷纸的方法为三辊卷板机
3检测方法为荧光检测
4焊接的方法为埋弧自动焊,焊接的坡口形式为I型
参考文献
[1]邹广华,刘强.过程设备制造与检测.北京:
化学工业出版社,2002.12
[2]方书起.化工设备课程设计.北京:
化学工业出版社,2010.5
[3]郑津洋,董其伍,桑芝富.过程设备设计.第2版.北京:
化学工业出版社,2005.
[4]GB150-1998《钢制压力容器》
[5]GB150-1999《钢制压力容器》
图4换热器封头