炼油厂火炬废气的环保利用0219 通用docWord格式.docx
《炼油厂火炬废气的环保利用0219 通用docWord格式.docx》由会员分享,可在线阅读,更多相关《炼油厂火炬废气的环保利用0219 通用docWord格式.docx(29页珍藏版)》请在冰豆网上搜索。
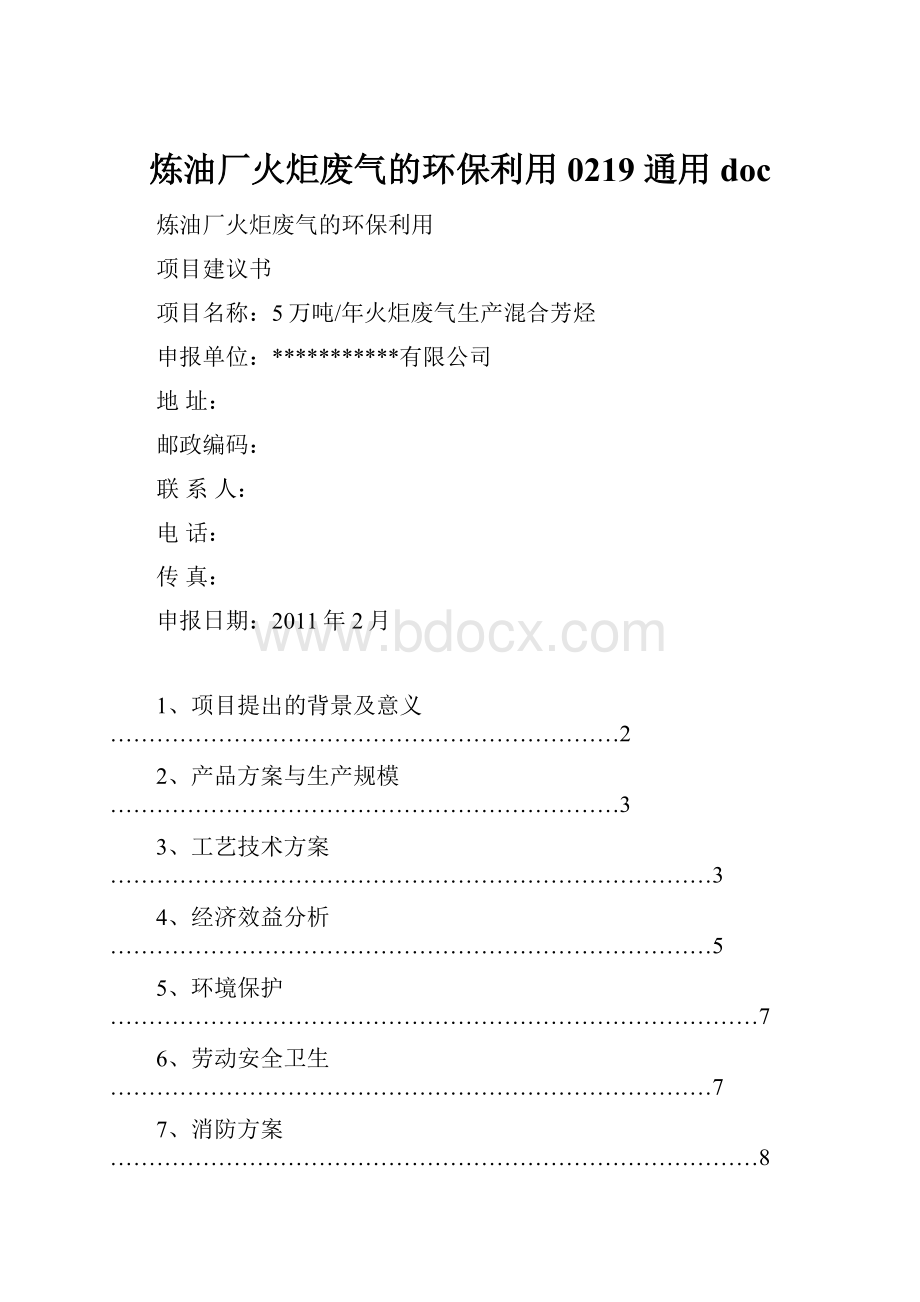
目前,我国炼化企业的催化干气资源还主要是作为工业燃料烧掉,剩余部分约30%左右,全国催化裂化总加工能力约在1.3亿吨/年,催化干气产率5%,全年产干气650万吨左右,也就是剩余195万吨左右的催化干气,为了保证安全生产这部分干气各炼厂都放火炬烧掉了,这既浪费了资源,也严重影响了环境。
由于我国石油资源紧缺、大量依赖进口,加之近年来进口原油价格居高不下,因此低碳烃资源有效利用率低已经严重影响了相关行业的总体经济效益。
因此,在我国利用催化干气等低碳烃资源增产芳烃蕴藏着重大机遇。
用液化气生产三苯的技术在近两年已经得到快速发展,但催化干气的利用却远远落后于液化气。
用催化干气生产三苯的优势在于:
(1)不与铂重整、乙烯装置和催化裂化装置争石油原料。
(2)由于催化干气价格便宜,目前东营市场每方干气0.50~1.0元(运输距离远者运输成本高,干气的出厂价格就便宜),约合600~1300元/吨,而生产出的BTX价格高达6000~7000元/吨(有些厂的催化干气放火炬烧掉了,利用起来效益就更可观了),因此将催化干气转化为BTX,能够有效地利用干气中的高附加值成分,100万吨/年的催化装置所产干气如果经过干气芳构化,每年能为企业带来3000~4000万元的利润,能有效提升炼化企业的经济效益。
(3)催化干气制BTX技术采用沸石分子筛催化剂,此类催化剂无腐蚀无污染,可以反复再生使用,除了催化剂烧炭再生过程中排放含CO2的烟道气之外,没有其它三废排放,对环境友好。
特别是具有较强的抗硫、抗氮能力,能省略原料预精制步骤,从而简化工艺,降低投资。
另外,本工艺采用的固定床反应器在低压下操作,技术成熟,投资少,安全性高。
(4)利用废催化干气生产混合芳烃,将大大减少碳排放,改善环境;
(5)国内催化干气总量在650~700万吨/年,如果利用一半来生产BTX,将可减少进口原油近300万吨,不仅很好地利用了干气资源,还相应减少进口原油量,具有良好的经济效益和社会效益。
2、产品方案与生产规模
2.1产品方案
该项目采用炼油厂放火炬的废催化干气生产混合芳烃。
该项目的原料:
催化裂化装置生产的富含乙烯的干气。
该项目的产品是:
①混合芳烃(苯、甲苯、二甲苯);
②贫干气。
2.2生产规模
该项目建设一套能处理5万吨/年催化干气的工艺装置及配套罐区和公用工程、办公设施等。
项目建成后,每年处理原料干气5万吨,生产混合芳烃1万吨,贫干气3.9万吨(返回炼厂作燃料),自用贫干气0.1万吨。
(装置与100万吨/年催化配套)。
考虑到减少工程投资,因此该项目暂不上混合芳烃精细分离系统,只简单分离成轻芳烃和重芳烃,然后作为中间原料销售。
5万吨/年催化干气生产混合芳烃物料平衡表(年操作时间:
8000小时)
项目
物料组成,wt%
kg/h
t/d
t/a
原料
催化干气
100
6250
150
50000
产品
轻芳烃
15.0
937.5
22.5
7500
重芳烃
1.0
62.5
1.5
500
贫烯燃料气
82.0
5125
123
41000
自用+损耗
加热炉燃料
2.0
125.0
3
1000
2.3、原料来源(如何控制干气资源是该项目的关键)
原料主要是炼油厂催化装置生产的富含乙烯的干气,国内年产量在650万吨左右,由于干气不好运输,因此干气芳构化装置最好依托催化裂化装置建设。
3、工艺技术方案
3.1技术简介
干气芳构化技术是利用干气中的乙烯生产芳烃的技术,该工艺是一种以分子筛新型催化剂为技术核心的芳构化工艺。
它采用固定床反应器切换操作方式,在非临氢条件下,以干气中的乙烯为原料生产芳烃(苯、甲苯、二甲苯)。
干气芳构化工艺在芳烃生产模式下,主产品为苯、甲苯和二甲苯,同时联产C9+重芳烃和贫干气,液收与干气中的乙烯含量有关,一般催化干气中乙烯含量在22%(m)左右,液体产品收率在10~20%(视干气中乙烯含量高低而定),加热炉自用燃料占2%左右,其余产品为贫干气(基本不含乙烯,返回炼厂作燃料)。
催化剂单程运转周期40~70天(与空速有关),催化剂总寿命可达3年。
该工艺的核心技术包含两项专利(正在申请中)和若干专有技术。
3.2技术特点
●操作灵活,工艺方案切换方便、快捷。
干气芳构化工艺采用固定床反应器切换操作方式,三苯生产模式的反应温度为450℃-600℃,主产品为苯、甲苯和二甲苯,同时联产C9+重芳烃。
高清洁汽油添加剂生产方案温度为:
300℃-400℃。
实际运行时可以灵活调整,一般来讲生产高清洁汽油更合适,因为产品质量好:
辛烷值高(目前工业化装置生产的汽油都大于100);
硫含量低,一般低于30ppm,国
标准汽油要求硫含量不能超过50ppm;
在正式上交政府相关部门的材料中红色部分将删除,主要是为了免征汽油燃油税(1333元/吨)。
●催化剂单程运转周期长、产品选择性高、催化剂使用寿命长。
新的催化剂单程运转周期已经达到1500小时以上。
●装置能耗低。
干气芳构化工艺采用了全新的取换热流程,可以回收大部分余热。
单位原料耗燃料气(芳烃方案)低于25kcal/吨原料。
●干气芳构化工艺原料适应性强,抗杂质能力突出,不需做预精制处理。
●干气芳构化工艺与现有炼化装置相容性极强。
干气芳构化装置生产的贫干气烯烃含量低,作为制氢装置的原料时,可以减少制氢装置的投资(不需要原料加氢)。
●环保性能好。
干气芳构化装置,全密闭生产,基本没有废水、废气排放,同时通过利用其中的有效组分,大大减少了炼厂干气放火炬燃烧,一套5万吨/年规模的装置,每年减少碳排放(一吨甲烷相当于21吨CO2)7500*21=157500吨,是真正的绿色化工装置。
3.3生产工艺简介
装置包括下列系统:
①热量回收系统:
高温产品与低温原料换热,回收热能,降低成本。
②加热炉系统:
换热后的原料进入加热炉,进一步加热到需要的温度,以利于下一步的芳构化反应。
③反应系统:
从加热炉出来、达到规定温度的原料进入装有特殊催化剂的反应器,原料在反应器内进行芳构化反应。
④分馏系统:
反应产物从反应器出来后,与低温原料换热,达到规定温度进入分馏塔,塔底出重芳烃,塔顶出轻芳烃和贫干气,塔顶高温油气与原料换热后进入冷却器,冷却后进入气液分离器,气液分离器下部出水,中部出轻芳烃,上部出贫干气,贫干气再进入捕油器,将干气中携带的芳烃再捕集下来,自捕油器出来的贫干气少部分去加热炉作燃料,大部分出装置送至高压瓦斯管网。
⑤催化剂再生系统:
积炭后的催化剂在适宜的温度下,配入氮气和氧气,进行烧焦再生,再生完成后处于备用状态。
4、经济效益分析
4.1、催化干气生产混合芳烃效益分析
出项
进项
年耗量
价格
合计
(万元)
年产量
(吨)
(元/吨)
干气
50000吨
1333
6665
7300
5475
催化剂
25吨
20万元/吨
6200
310
燃料
1000吨
自产自用
优质干气
5465.3
蒸汽
600吨
200元/吨
12
燃料气
电
96万kwh
0.56
53.76
新鲜水
0.4万吨
5元/吨
2
循环水
96万吨
0.2元/吨
19.2
工资
30人
5
折旧
2300万
230
维修
20
管理
50
财务费
总计
7801.96
11250.3
税前利润=11250.3-7801.96=3448.34万元。
原料干气按1333元/吨(相当于1元/立方),催化剂20万元/吨,蒸汽200元/吨,新鲜水5元/吨,电0.56元/度,人工工资按5万元/年.人,年处理5万吨原料,总产值11250.3万元/年,税前利润3448.34万元/年。
当干气价格从1333元/吨上涨到2500元/吨,相应的效益计算如下:
2500
12500
10250
13636.96
16035
税前利润=16035-13636.96=2398.04万元。
可见原料价格上涨将近一倍,产品价格基本不变时,每年的税前利润仍然可以达到2398.04万元,现实中产品价格一般都会水涨船高,原料涨,产品也涨,尤其是作为与原油紧密相关的产品,随着国际油价的上涨,国内汽油大趋势是上行的,因此上述计算是保守的。
该项目固定投资(包括技术费)需1800万元,催化剂500万元(使用三年),流动资金200万元,满负荷生产时年产值(按2011年2月市场含税价)为11250.3万元,总成本7801.96万元,税前利润3448.34万元,收回投资需16个月(建设期8个月,生产期8个月)。
4.2、原材料、动力消耗
①用工程规格与消耗
项目名称
单位
规格等级
单位原料消耗
t/t
1.0MPa
0.012
0.2-0.3MPa
0.02
kWh/t
380V/10000V
0.05
0.5MPa
注:
仪表风等均含于电消耗内。
②催化剂及其它三剂消耗
3年消耗量
吨
25
瓷球
5、三废与环保
废水:
该项目机泵采用先进的屏蔽泵,用工艺介质冷却,因而没有冷却水,工艺过程也不产生废水,因而该项目没有废水。
废气:
该项目基本不产生废气,只有加热炉产生少量烟气,由于燃料为装置自身生产的超低硫(总硫20PPm以下)干气,因而烟气完全能达到排放要求。
废渣:
装置产生少量废催化剂,该项目催化剂全程寿命为3年,5万吨/年装置,催化剂用量为20吨,平均每年产生8废催化剂,该催化剂为分子筛,主要成分为二氧化硅和氧化铝,不含其他有害物质,废催化剂原厂回收,也可以送给水泥厂作原料。
噪声:
主要是由压缩机、加热炉、泵机等产生,声级值在65~85dB(A)左右,机泵采用先进的屏蔽泵,加热炉采用先进的燃烧器,可大幅度降低噪声,压缩机采取隔声可减轻噪声对外界的影响。
减少碳排放:
通过利用干气中的有效组分,大大减少了炼厂干气放火炬燃烧,一套5万吨/年规模的装置,每年减少碳排放(一吨甲烷相当于21吨CO2)7500*21=157500吨。
综上所述该项目为绿色环保项目。
6、劳动安全卫生
6.1生产过程中主要危害因素分析
本项目主要原料为催化干气,工艺生产过程在一定的温度和压力下进行,存在产生燃爆事故的可能,危害人身安全;
又因生产过程中设备及管道连接多而且复杂,有工艺物料泄露的可能,因而存在中毒事故的可能性。
6.2安全卫生防范措施
安全卫生设计要贯彻“安全第一,预防为主,综合治理”的方针。
安全卫生设施必须执行与主体工程同时设计、同时施工、同时投产的“三同时”原则,以保证生产安全,提高生产水平,促进企业生产发展。
(1)有毒有害物的防范措施
在满足工艺条件的前提下,对可能产生泄漏的设备、管道,尽量敞开布置。
为防止厂房内有毒有害物的积累,厂内设计可靠的通风系统或设置有毒气体报警器。
(2)化学腐蚀防范措施
对与腐蚀性物料直接接触的设备、管道、阀门选用合适的耐腐蚀材料制作,电机及仪表选型应考虑防腐,建、构筑物设计采用耐腐蚀的建筑材料。
(3)静电、雷电防范措施
生产装置在防爆区域内设计静电接地。
具有火灾爆炸危害场所以及静电危害人身安全的作业区,金属用具等均设接地。
有火灾爆炸危险的化工装置,电气设施设防雷装置。
(4)化学灼伤防范措施
化学灼伤危害作业区尽量采用机械化、自动化,并安装必要的信号报警、安全连锁和保险装置。
工作人员配备必要的个人防护用品。
(5)火灾、爆炸防范措施
装置内的设备、管道、建构筑物之间保持一定防火间距。
有火灾爆炸危险的建构筑物的结构形式以及选用材料应符合防火防爆要求;
具有火灾爆炸危险的生产装置设计安全阀、水封、阻火器等防爆阻火设施以及防静电接地系统,并安装火灾报警设施。
7消防设施
7.1厂区配备室外消火栓。
7.2配电室、污水提升泵站内设干粉灭火器。
档案室、资料室等配有灭火器。
7.3厂区内道路布置消防通道,消防车辆出入方便
7.4火灾报警系统
对拟建项目设置火灾报警系统,当发现火灾异常现象是自动报警系统启动,警告人们火源的位置。
7.5灭火系统
为了减少火灾造成的损失,有各种类型的灭火剂,如:
水、泡沫、惰性气体、卤代烷烃、化学干粉和固体物质等。
7.6消防水源的建立
对拟建项目的给水系统设计时,要考虑到消防用水量及水压,根据装置大小、高度及灭火能力,选择合适的消防水池,保证30分钟的用水量。
发生火灾时正确选用灭火方法、灭火剂,以及有效地组织灭火,是十分重要的。
8、自动化控制
根据本项目特点,自动控制应以集中监视、控制为主,采用以计算机为基础的DCS集散控制系统,完成生产过程的数据采集、过程控制、安全报警、连锁保护等功能。
对于必须有操作人员现场监视的岗位,可以采取就地岗位集中监控的控制方式,同时将重要工艺参数送至装置控制室,进行集中监视。
自动控制设计具备以下基本功能:
(1)生产过程工艺参数的集中监视
(2)工艺参数的自动控制
(3)过程参数超限报警
(4)重要环节的连锁保护
(5)中央调度室设有与工厂管理网络连接接口,最终实现管、控、营销一体化。
集中监控可采用区域集中监控和全厂集中监控方案:
根据工艺装置的功能和区域分布状况,每个区域设置操作控制室。
根据装置特点和控制要求,每个控制区域分别采用不同的控制系统,将控制站和操作站均放置在区域控制室内,对本区域内的生产装置进行监控。
此外,全厂还设置中央调度室,通过计算机网络将各区域控制室的控制系统连接起来,将各区域控制室的重要信息送至中心调度室。
在中心调度室可以对全厂生产装置进行监视和调度。
各装置控制室可以通过通讯网络调用其它装置控制室的信息,实现信息资源共享和全厂一体化管理。
同时,通过中央调度室的上位计算机,可以实现全厂优化控制。
9工厂制度和定员
9.1工厂运行方式
装置生产按每年8000小时设计。
本装置为连续生产装置,生产系统等相关系统实行四班三运转作业制度,其它实行一班制。
9.2定员
9.2.1管理机构定员
表4厂部管理机构定员表
序号
名称
定员
1
厂长
2
副厂长
3
总工程师
4
生产技术部
5
质检中心
6
财务部
7
供销部
合计
12
一般可以依托原来的机构,如果原来没有机构,可以按照表4设置。
9.2.2生产装置定员
本项目的生产装置为24小时连续运转。
根据生产装置运行特点的不同,将生产班制划分为:
生产管理部门实行白班制;
连续生产的倒班岗位实行四班三运转。
生产装置的人员设置见下表。
表5生产装置定员表
序号
部门
定员
备注
1
生产车间
3人×
4
四班三运转作业
配电仪表及维修
6
值班
18
10投资估算
本项目占地面积20亩,主要布置有自动化生产线、成品储存区、必需的工业建筑厂房(配电室,材料库,控制室,化验室,生产区办公室等)。
行政区占地约10亩,布置办公楼一座。
其它用地作为道路及美化绿化,总体规划成一个花园式工厂。
综合投资列表
序号
项目
投资,万元
设备投资
650
电气、仪表
工程与管道
200
(专利)技术转让、设计
400
催化剂、处理剂等
部分配套公用工程
7
控制室、土地费
8
其它不可预见费
2300万元
11.市场分析
11.1.原料市场
该项目原料为含乙烯的炼厂干气,目前国内催化裂化总加工能力高达1.3亿吨/年,催化干气总产量在650万吨左右,炼厂都将催化干气作为加热炉燃料烧掉了,相当一部分炼厂干气平衡不了,剩余20~30%左右,为了保证安全生产,这部分干气通常放火炬烧掉了;
干气中乙烯含量在20~30%,如果将干气中的乙烯转化为芳烃,这些炼厂的干气就基本平衡了,火炬将熄灭。
近三年东营市场干气价格在0.5~1.0元/立方(相当于625~1250元/吨,干气密度0.8kg/m3)这个价格变化不大,主要原因:
这部分气是炼厂多余的,而利用的途径很少,因而价格相对稳定。
未来2~3年价格涨到2.0元/立方(相当于2500元/吨),原料和产品的价差还在5000元/吨,有足够的空间来抵御市场的波动。
11.2.产品市场分析
11.2.1混合芳烃市场
在2005-2010年间,全球苯、甲苯和二甲苯的平均需求增长率将分别达到4.4%、3-4%和5.4%,而同期中国对苯、甲苯和二甲苯的需求增长率将高达16%、8.2%和19.1%。
11.2.2高辛烷值清洁汽油调和组分
本项目的主要产品是辛烷值高达93~100的混合芳烃,硫含量低于30ppm,是国IV汽油的极佳调和组分,因此混合芳烃产品价格一般略高于93#汽油价格,其价格与93#汽油紧密相关。
2008年12月19日,发改委启动了新的成品油价格形成机制:
当国际市场原油连续22个工作日移动平均价格变化超过4%时,可相应调整国内汽、柴油价格。
因此该项目的产品也与93#汽油一样受到国际原油价格的直接影响。
按照发改委的定价机制,汽油价格完全取决于国际原油价格的变化,因此了解国际原油价格的变化趋势也就基本掌握了汽油及汽油的调和组分的价格变化趋势。
11.2.2.1全球原油价格走势分析
①历史价格回顾
1976-2008年6月19日原油现价走势
自1970年以来,国际原油价格波动,大体经历了以下不同的四个历史阶段:
(1)20世纪70年代两次石油危机驱动油价持续暴涨。
1970年,沙特原油官方价格为1.8美元/桶;
1974年(第一次石油危机),原油价格首次突破10美元/桶;
1979年(第二次石油危机),原油价格首次突破20美元/桶;
1980年,原油价格首次突破30美元/桶;
1981年初,国际原油价格最高达到39美元/桶;
随后,国际油价逐波滑落,从此展开了一轮长达20年的油价稳定期。
(2)1983——2003年初,20年油价一直徘徊在30美元之下。
1986年,国际原油价格曾一度跌落至10美元/桶上方;
1986年初——1999年初,国际原油价格基本上稳定在20美元/桶之下运行,只是在1990年9——10月间,油价出现过瞬间暴涨,并首次突破40美元/桶,但两个月后很快又滑落至20美元/桶之下;
1998年底1999年初,国际原油价格曾一度跌至10美元/桶以下。
2000年,国际原油价格曾短时间内冲至30美元/桶上方,但很快又跌落至20美元/桶之下。
(3)第三次石油危机时期(2003——2008年)。
第一、二次石油危机后,国际原油价格波动经历了长达20年的稳定期。
20年后,国际原油价格再次步入一个全新的快速上升通道,第三次石