油缸设计规范企业标准文档格式.docx
《油缸设计规范企业标准文档格式.docx》由会员分享,可在线阅读,更多相关《油缸设计规范企业标准文档格式.docx(90页珍藏版)》请在冰豆网上搜索。
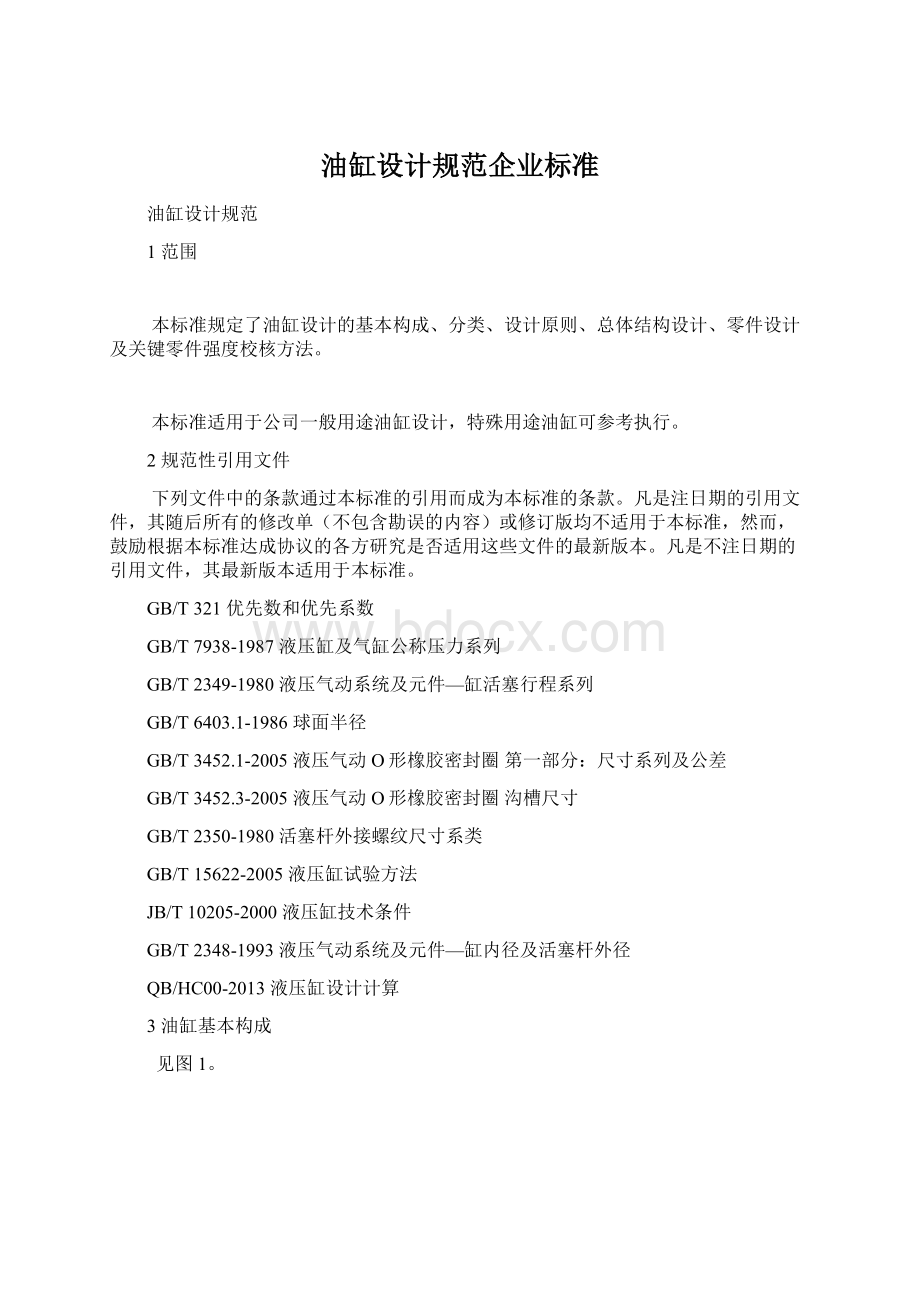
支腿展开油缸、支腿伸缩油缸、水平油缸等
特殊油缸
不能归入上述五类之外的油缸,如单作用缸(弹簧回程)、柱塞缸(自重回程)、多级缸等
前置顶油缸、减振油缸、增压缸、推板油缸
5油缸设计原则
油缸设计按以下原则:
a)满足工况和安装要求;
b)满足作用力、行程、速度要求;
c)零部件有足够的强度、刚度,满足使用寿命和可靠性要求;
d)密封可靠;
e)充分考虑零件加工和装配工艺性;
f)安装、维修方便;
g)油缸性价比高;
h)轻量化设计;
i)标准化设计。
6油缸总体结构设计
6.1油缸主参数确定
主要确定的油缸主参数包括:
工作压力、缸径、杆径、行程和安装距。
6.1.1工作压力确定
根据系统压力和负载需要计算油缸的工作压力,再按照《油缸主要参数优选表》(附录A)确定油缸设计的工作压力。
6.1.2油缸缸径确定
6.1.2.1根据载荷力和油缸工作压力计算油缸缸径
其中:
F—载荷力,N;
Pn—油缸工作压力,MPa;
D—油缸缸径,mm
6.1.2.2根据油缸运行速度和油缸油液流量计算油缸缸径
Q—进入油缸无杆腔的流量,L/min;
v—油缸运行速度,mm/s;
将计算出的油缸缸径值圆整为《油缸主要参数优选表》(附录A)中油缸缸径优选值。
6.1.3油缸杆径确定
6.1.3.1根据强度要求计算油缸杆径
a)稳定状态下活塞杆仅受轴向载荷,活塞杆直径按拉、压强度计算油缸杆径d:
式中:
[σs]—材料的许用屈服应力,MPa,
;
n—安全系数,n
1.4;
d—油缸杆径,mm
b)当活塞杆受到较大弯曲作用时,则按压弯强度联合计算油缸杆径d:
σ—活塞杆所受应力,MPa;
A—活塞杆截面积,mm2,其中:
实心活塞杆
空心活塞杆
—活塞杆外径,mm
—活塞杆空心直径,mm
—活塞杆最大挠度,mm,
其中:
F—载荷力,N;
L—活塞杆完全伸出时,其外伸长度,mm;
E—弹性模量,MPa,碳钢弹性模量取为2.06×
105;
I—惯性矩,mm4,其中:
W—活塞杆断面的抗弯模量,mm3,其中:
实心活塞杆
6.1.3.2根据速比要求计算油缸杆径
式中:
—速比,即油缸两端面积比,可按速比表进行选取。
将计算出的杆径值圆整为《油缸主要参数优选表》(附录A)中油缸杆径优选值。
6.1.4行程、安装距确定
6.1.4.1油缸行程根据主机所要求的动作距离确定,推荐选用附录A中的《油缸主要参数优选表》中行程优选值。
6.1.4.2安装距由油缸在主机上安装要求确定,与油缸各零部件的长度尺寸相适应。
6.2油缸安装形式确定
根据公况及其安装环境选择合适的油缸安装形式,常用的共6种,见表二。
表2油缸安装方式
安装方式
应用
耳环式
1、耳环内可配轴套或关节轴承,油缸可在垂直面内摆动;
2、有头部耳环、尾部耳环、两端耳环三种形式,尾部耳环型活塞杆受弯曲作用较大。
应用最为广泛
法兰式
1、包括头部法兰、中间法兰、尾部法兰;
形状有方形和圆形两种;
2、头部法兰型安装时,安装螺钉受拉力较大;
尾部法兰型安装螺钉受力较小。
广泛应用于主机支腿油缸等。
铰轴式
1、包括头部铰轴、中间铰轴、尾部铰轴;
2、采用头部铰轴时,活塞杆受弯曲作用较小;
中间铰轴型次之;
尾部铰轴型最大。
主要用于起重机油缸、环卫车辆油缸、桩机油缸等。
球头式
1、油缸可在一定空间范围内摆动;
2、能减少作用面不平整对油缸的影响。
杆端球头大量用于支腿油缸;
缸底端球头用于泵车摆阀油缸及TG型套筒缸。
卡槽式
与主机部件采用卡环连接。
主要用于泵车主油缸等。
底座式
1、包括径向底座、轴向底座、切向底座;
2、径向底座型油缸受倾翻力矩较小;
其余两种较大。
主要用于转向油缸等。
6.3油缸内部结构确定
6.3.1活塞与活塞杆连接方式
a)螺纹连接
常用的一种连接方式。
防松措施采用将紧定螺钉涂抹螺纹紧固胶后锁紧活塞。
此种防松方法的缺点是配钻时产生的碎屑不易清洗,建议采用《内螺纹式活塞防松的两种新方法》中提到的两种防松措施。
b)卡键连接
制造安装简单方便;
卡键的使用会影响活塞杆的局部强度,需校核卡键槽强度;
制造时应严格控制各配合零件的长度尺寸,以免使得装配时活塞与卡键之间出现间隙或配合过紧现象;
此种连接方式一般在杆径较大时采用。
如图2所示。
图2
c)整体结构
当缸径较小、缸径与杆径的相差不大、活塞杆较短时采用;
整体强度较前两种好;
减少了零件数量,利于加工。
如图3所示。
图3
6.3.2导向套与缸筒连接方式
a)卡键连接
结构紧凑,重量轻;
安装时注意避免密封圈被卡键槽及油孔边缘擦伤;
设计时请参考《内卡键连接式液压油缸的优化设计》一文。
b)螺纹连接
在中小油缸中使用广泛;
缸筒上的安装螺纹加工时确保与缸筒内孔同心,装配时注意防止密封圈扭曲和被螺纹刮伤;
设计时请参考《螺纹连接式缸筒与导向套设计及加工注意点》。
c)螺纹压盖连接
结构简单,易保证装配后的活塞杆与缸筒内孔同心;
因增加螺纹压盖,径向尺寸稍大。
如图4所示。
图4
d)法兰连接
结构较简单,易加工,易装卸,使用广泛;
径向尺寸大,缸筒需增加焊法兰工序,用厚料时原材料浪费大,成本较高。
如图5所示。
图5
6.4油缸密封系统确定
油缸密封系统由动密封和静密封两部分组成。
6.4.1动密封
动密封包括活塞密封和活塞杆密封两类。
6.4.1.1活塞密封方式
见表3。
表3活塞密封方式
油缸类型
密封方式
应用场合
U形圈+格莱圈
单向保压严格
SUMPS+CKW
山形圈
双向保压、尺寸紧凑
SZHTPM-5
山形圈+U形圈
行程特别长的油缸
SZHTPM-5+SUMPS
双U形圈(靠背装)
双向保压、大缸径
SUMPS+SUMPS
格莱圈
高压、高速
CKW
组合圈
高压、高速、工况恶劣
SZHSPGW-4
转向油缸
双杆双作用油缸
辅助油缸
特殊油缸
U形圈
单作用缸、增压缸
SUMPS
多级缸
6.4.1.2活塞杆密封方式
见表4。
表4活塞杆密封方式
使用条件
P≤16MPa
Y形圈
CKG
16MPa<P≤25MPa
Y形圈+斯特封
CKG+CK
P>25MPa
Y形圈+挡圈+斯特封
CKG+F4+CKS
当对摩擦力要求极其严格,例如伺服缸;
动作频率快、性能要求高,例如精密机床用油缸;
工作行程较短时,经常采用串联斯特封的形式,如“CKS+CKS”。
当大型油缸承受高压、高温、重载,工作环境恶劣,对速度稳定性要求不高时,采用V形密封件,如大型冶金设备用油缸。
6.4.1.3防尘密封方式
见表5。
表5防尘密封方式
防尘方式
图例
无骨架防尘圈
结构简单,安装方便,成本低,但易发生翻转,防尘效果欠佳
一般安装在杆头或缸底孔内用于轴套防尘
骨架防尘圈
结构简单,安装方便,成本较高
工作环境较差情况下使用,如挖机油缸
双作用防尘圈
结构简单,安装方便,成本低,并兼有密封功能
工作环境较好情况下使用,与串联斯特封组合使用,效果尤佳
防尘罩
防尘效果好,成本低
用于粉尘多的地方
6.4.2静密封方式
见表6。
表6静密封方式
类型
方式
活塞静密封
装1个O形圈,空间足够时,装2个
导向套静密封
1、工作压力<16MPa时,装1个,空间足够,装2个;
2、工作压力≥16MPa时,加装挡圈。
导向套防水密封
1、螺纹式导向套,在退刀槽处采用1个O形圈作防水密封;
2、卡键式导向套,在卡键挡圈上设计1个O形圈作防水密封。
国外油缸的静密封大量采用一种哑铃形密封件,倒8字形,其实质是两个O形圈固结在一起,不用加挡圈,装配时不会在沟槽里发生扭转,稳定性好,密封性能好,成本较低,设计时可考虑采用。
6.5油缸支撑系统确定
6.5.1支撑环材料确定
油缸支撑系统由活塞支撑和活塞杆支撑两部分组成。
常用的支撑环材料见表7。
表7常用支撑环材料
材料名称
特征
应用
聚甲醛
耐疲劳强度、刚性高于一般尼龙,强度、硬度较高。
自润滑性、耐磨性、尺寸稳定性较好,吸收杂质颗粒的能力较夹布强,但不及聚四氟乙烯,不耐高温,价格低。
油缸中应用较普遍,可承受一定的载荷,无润滑或少润滑条件下仍能工作。
夹布酚醛
机械性能高,耐油性好,热稳定性好,使用温度广(-40~135C),但冲击韧性低,质脆。
用于重载荷、油温较高、活塞杆表面经过热处理的油缸中,一般在有润滑的条件下使用。
填充聚四氟乙烯
(F-4)
自润滑性好,耐热,耐寒(-180~250C),摩擦系数极小,机械性能低,刚性差,流动性大,可吸附一定的颗粒。
用于轻载荷、侧向力不大、行程较短、动作频率较快、性能要求较高的场合,常作为油缸辅助支撑。
铸造铜合金
(ZQAL9-4等)
强度高,耐磨性、耐蚀性好,成本高
用于重载、长行程、偏载大、性能要求高的油缸
球磨铸铁
(QT450等)
强度高,耐磨性好,成本较低,但因其铸造缺陷问题,易对油液形成污染
重载荷、尺寸要求较紧凑的油缸中使用。
无油轴承
(三层复合自润滑材料)
该材料以钢板为基体,青铜为中间层,以塑料为表面的自润滑材料,既有金属的刚性,又有塑料的自润滑性,尺寸稳定,干摩擦性能好,强度高,耐磨
用在性能较高的场合(例如挖机油缸),可有效地克服因支撑环材料而造成的爬行抖动。
降低启动压力,是替代非金属支撑环的理想材料。
设计时,应根据油缸实际使用工况选择支撑环材料。
a)工作时侧向受力且缸径≥360时,应在活塞外圆表面堆铜焊。
如图6所示。
图6
(1环形垫圈槽,2活塞本体,3铜熔焊镀层,4内螺纹,5焊接工艺环槽)
其制造工艺包括以下步骤:
(1)在活塞本体外圆表面车环形垫圈槽和焊接工艺环槽;
(2)在焊接工艺环槽上采用铜焊粘结剂和铜条在火焰枪的高温条件下进行焊接,焊接温度达到铜的熔点温度,从而在焊接工艺环槽内形成一层铜熔焊镀层,并使铜熔焊镀层高于活塞本体外圆表面0.8mm-1.2mm(优选1mm);
(3)通过精加工,使铜熔焊镀层表面光清洁度达到设计要求;
(4)在环形垫圈槽中安放起密封作用的橡胶垫圈。
焊接工艺环槽的结构如图7所示。
图7
采用铜条焊层的活塞外圆表面的承载能力是一般普通支承环的8倍,普通聚四氟乙稀材料支承环支承能力约为15N/mm2,采用铜条焊层处理技术后的承载能力达到120N/mm2。
这种加工工艺使活塞表面成功获得一层单边厚度约3mm的铜材料组织结构,不管偏载的情况有多复杂,都能彻底解决液压缸在运行时拉伤缸筒的问题,大大延长油缸的使用寿命。
b)工作时侧向受力且杆径≥200时,应考虑采用内嵌铜套式导向套。
如图8、9所示。
图8
(1紧定螺钉,2螺纹,3内嵌铜套,4密封垫圈槽,5支撑环,6固定螺孔)
图9
(6紧定螺孔,13半圆形螺旋油槽,12导向套本体)
如图8、9所示,导向套本体内壁设有内嵌铜套,内嵌铜套外端设有紧定螺钉,内嵌铜套内表面设有螺旋油槽,内嵌铜套内表面的螺旋油槽截面为半圆形,螺距、槽深分别优先为24mm,0.8mm。
(1)按图纸要求加工好导向套本体;
(2)按图纸要求加工青铜套,注意内孔应留0.4-0.5mm左右的精加工量,外圆注意控制好尺寸,保证与导向套本体为过盈或过渡配合。
(3)用油压机将铜套压人导向套本体内,端面打紧定螺钉;
(4)精车铜套内孔,拉螺旋油槽。
由于内嵌铜套内表面的螺旋油槽内充满了润滑油,对活塞杆和内嵌铜套的相对运动起到了润滑作用,减少了活塞杆与内嵌铜套内表面之间的摩擦力,减少了活塞杆、内嵌铜套和支撑环的单边磨损,削弱了单边磨损效应;
消除了滑动面间的断油现象,解决了液压油缸在侧向载荷作用下的爬行和抖动问题,提高了活塞杆的最大载荷。
c)工作时侧向受力且杆径<200时,可考虑采用SF-1无油轴承,特别是当杆径小时,安装较方便。
6.5.2支撑环参数确定
6.5.2.1支撑环厚度确定
非金属支撑环的厚度一般为2.5mm,铜支撑环厚度一般取5mm。
6.5.2.2支撑环宽度确定
支撑环宽度的计算公式为:
T—导向环宽度,mm;
f—安全系数,一般取2-3;
d—活塞杆直径,mm;
pr—材料承载能力,N/mm2;
常用非金属支撑环材料的Pr值:
填充聚四氟乙烯-15;
聚甲醛-60;
酚醛夹布-90
Fc—侧向载荷,mm,
a)对于细长油缸,侧向载荷主要由挠度引起
L1—油缸最小导向长度,mm,
S—油缸工作行程,mm;
D—油缸缸径,mm;
其它参数参照6.1.3.1b)
b)对于活塞杆为球头或耳环(内装关节轴承)式时,Fc≈Fsin15°
=0.26F。
c)对于活塞杆为耳环(内装衬套)式时,它的侧向载荷主要由以下两部分组成:
1.耳环孔与销轴间隙引起的侧向力
见图10。
图10
由图10可以得出:
δ—单边间隙,mm;
L—耳环宽度,mm
由上式可以看出:
侧向力的大小与载荷、间隙成正比,与耳环宽度成反比。
因此设计加工时,在保证安装方便的前提下,应尽量减少间隙、增加耳环宽度,以减少侧向力。
2.耳环孔中心与活塞杆中心不垂直引起的侧向力
见图11。
图11
由图11可以得出:
F—销轴对耳环的力,N;
Fz—轴向分力,N;
β—耳垂直度误差偏角,°
侧向力与误差偏角成正比,所以设计加工时,垂直度误差应控制在0.05-0.1,以减少侧向力。
当耳环与活塞杆采用焊接时,耳环孔因留加工余量,待焊接后,以活塞杆为基准加工到位;
当耳环与活塞杆采用螺纹连接时,应控制螺纹加工精度为6-7级,必要的时候,添加定位止口配合以保证垂直度要求。
如图12所示。
图12
1活塞杆2耳环
添加定位止口的另外一个好处是:
改善耳环的受力状况。
当耳环由于偏载而受到较大弯矩作用的时候,把危险截面由原来的螺纹退刀槽A面转移到了定位止口B面,大大提高了耳环的抗弯强度。
综上所述:
一般地,当导向套或活塞长度尺寸足够时,支撑环宽度应尽量取大值,且至少安排两道。
为少支撑环种类规格,增强通用性,现规定如下:
对于活塞支撑部分,见表8:
表8活塞支撑环推荐宽度
缸径
宽度
40、50、63
6.1
70、80、90、100、110
9.4
125、140、150、160、180
14.7
200、220
19.7
250、280、320
24.7
360以上
29.7(铜支撑环)或堆铜焊
对于活塞杆支撑部分,见表9:
表9活塞杆支撑环推荐宽度
杆径
20、22、25、28、32、36
6.1或SF-1无油轴承
40、45、50、56、63、70、80
90、100、110、125
140、160
19.7或SF-1无油轴承
180、200、220
24.7或镶铜套
250以上
镶铜套
注:
铜套的材料为ZCuAL10Fe3(ZQAL9-4)或ZCuPb10Sn10。
6.6油缸其它装置确定
油缸其它装置由缓冲装置和排气装置两部分组成。
6.6.1缓冲装置确定
当活塞速度达到0.1-0.3m/s时,可以考虑设置缓冲装置;
当活塞速度大于0.3m/s时,必须设置缓冲装置。
根据缓冲过程中油液通道是否改变其节流面积,缓冲装置常分为恒节流型,变节流型和自调节流型三大类,其中恒节流型应用最为普遍。
6.6.1.1恒节流型缓冲装置
恒节流型缓冲装置包括以下两种:
a)圆柱头环隙缓冲装置
见图13。
图13
工作原理:
当
开始进入导向套凹腔时,缓冲腔油液只能通过间隙δ挤压出去。
因此,活塞受到一个很大的阻力,缸的运动速度
减慢。
这种缓冲装置的特点是:
结构简单,开始缓冲时效果显著,但整个缓冲过程中缓冲效果逐渐减弱;
对零部件的加工精度要求高,特别是δ值既不能太大也不能太小,太大无缓冲效果,太小则缓冲柱塞容易“憋劲”。
适用于惯性较小、速度较低的场合。
设计时,一般取δ=0.1,其它缓冲参数按《油缸缓冲设计计算》进行设计选取。
b)单向节流阀缓冲装置
见图14。
图14
当缓冲柱塞进入缸盖内孔时,排油腔被封堵,油液只能通过节流阀排油,排油腔缓冲压力升高,使活塞制动减速。
调节节流阀的通流面积,可以改变回油流量,从而改变活塞速度。
单向阀的作用是当活塞返程时,能迅速向油缸供油,以避免活塞推力不足而启动缓慢或困难的现象发生。
由于安装了节流阀,制动力可根据负载进行调节,因此适用范围广。
但它同样有圆柱形环隙式缓冲装置的缺点,且加装了单向节流阀,成本较圆柱头环隙缓冲装置高。
设计时,缓冲柱塞与缸盖应为滑动配合,δ值应较圆柱头环隙缓冲装置小。
在系列化的油缸设计中,由于事先无法知道活塞的运行速度以及运动部分的质量和载荷,因此为了使结构简单,降低成本,多采用恒节流型缓冲装置。
尤其是单向节流阀缓冲装置,应用更为普遍,如力士乐油缸。
图14为这种装置在拖泵摆阀油缸上的应用。
6.6.1.2变节流型缓冲装置
在恒节流缓冲装置的基础上,为了使节流面积随缓冲行程的增大而减小,使动能的吸收更加均匀,通过改进缓冲柱塞,可实现变节流缓冲。
常用的主要有抛物线、铣槽、圆锥形、双圆锥形、两级缓冲、多级缸筒、多孔柱塞等结构型式。
见图15。
(a)抛物线(b)铣槽(c)阶梯形(d)圆锥形
(e)双圆锥形(f)两级缓冲(g)多孔缸筒(f)多孔柱塞
图15
其中,(a)抛物线缓冲效果最好,需要数控机床或仿形车床加工,成本较高,应用较少;
(b)节流槽形,直接由铣床铣出,加工方便,应用较多;
(c)阶梯形,车床上车出三个台阶,加工方便,缓冲压力峰值较小,不及恒节流
圆柱形的一半,国外Parker油缸无杆腔缓冲经常采用;
(d)圆锥形,缓冲效果和阶梯型差不多,应用较少;
(e)双圆锥形,缓冲效果好于圆锥形,挖机油缸上经常采用;
(f)多孔缸筒和(g)多孔柱塞用于对精度要求更高的液压设备,合理布置小孔的
数量和各排间的距离,缓冲效果可更接近于理想抛物线的水平。
其中(g)多孔柱塞的
原理已应用于我司客户重庆新明和的产品设计中,并加以改进,后面将做重点介绍。
图16为节流槽和双圆锥形组合的变节流型在挖机油缸上的应用。
图16
从图16可以看出,缓冲销的形状为双圆锥形,并且铣出3条轴向沟槽,节流面积随
缓冲行程的增大而逐渐减小,缓冲压力变化较平稳,缓冲效果较好。
在重庆新明和油缸设计中,采用了一种新型的节流型缓冲装置,见图17。
图17
这种新型的节流缓冲机构,根据应用场合的不同可设计成恒节流缓冲与变节流缓冲两种型式,如图17,在图17a中,当活塞3向缸盖7方向运动时,缓冲块5在挡圈6和弹簧4的作用下也随着活塞3向缸盖方向运动。
当缓冲块与缸盖平面复合时,无杆腔内形成缓冲油腔。
被封闭的油液只能从节流孔排出,从而实现节流缓冲。
图17b是在图17a的基础上加以改进的,在缓冲块的进油管上增设小孔,当活塞3向缸盖7方向运动时,通过改变节流孔的数量来改变节流面积,从而达到变节流的效果。
从图17可以看出,当活塞反向运动时,活塞也不会因推力不足而产生起动缓慢或困难的现象。
新型节流型缓冲装置的特点:
①采用圆锥形弹簧与变节流缓冲结构。
圆锥形弹簧与圆柱形弹簧相比,具有较大的横向稳定