基于dynaform的汽车防撞梁拉延工艺参数影响规律研究毕业论文.docx
《基于dynaform的汽车防撞梁拉延工艺参数影响规律研究毕业论文.docx》由会员分享,可在线阅读,更多相关《基于dynaform的汽车防撞梁拉延工艺参数影响规律研究毕业论文.docx(65页珍藏版)》请在冰豆网上搜索。
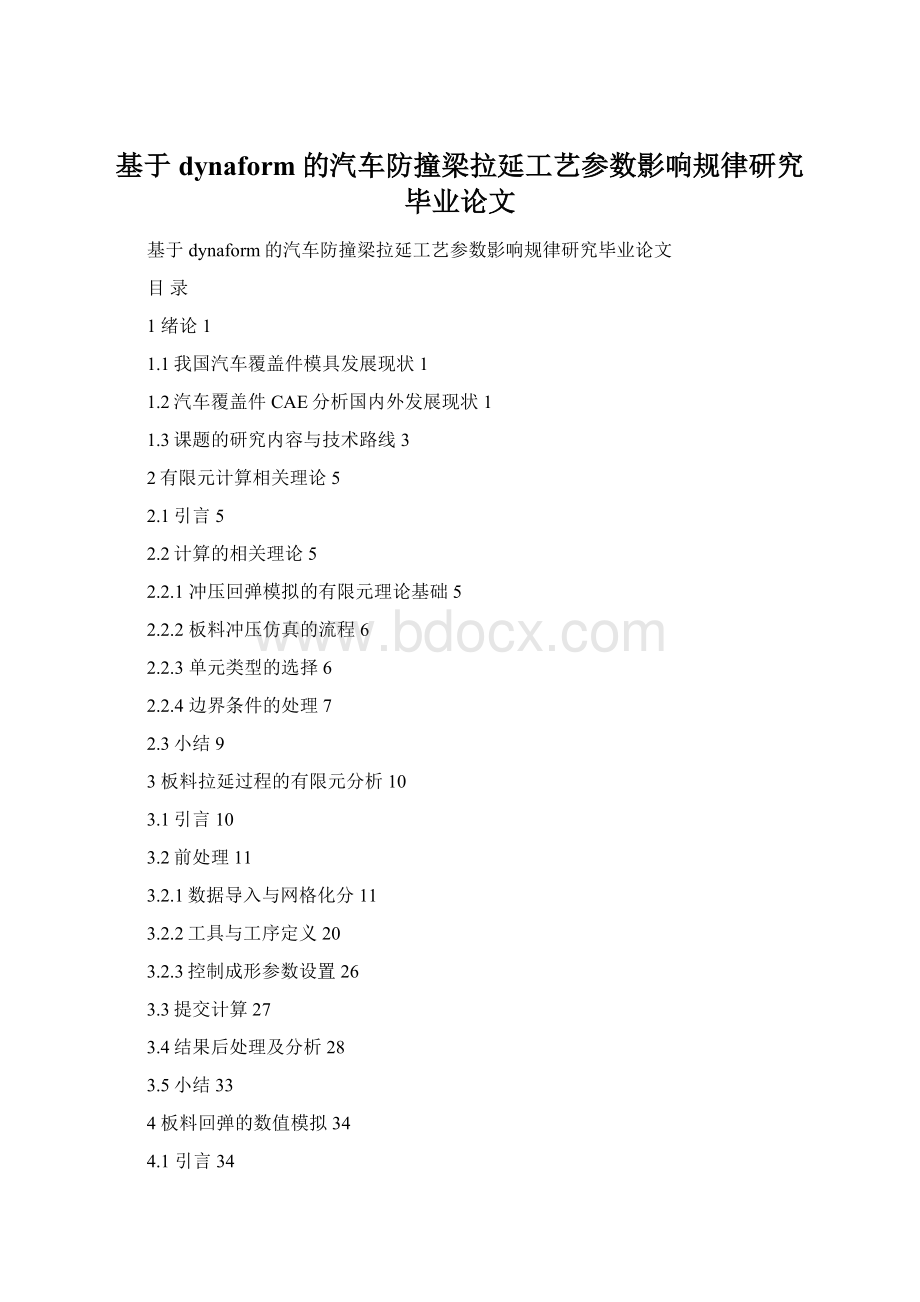
基于dynaform的汽车防撞梁拉延工艺参数影响规律研究毕业论文
基于dynaform的汽车防撞梁拉延工艺参数影响规律研究毕业论文
目录
1绪论1
1.1我国汽车覆盖件模具发展现状1
1.2汽车覆盖件CAE分析国内外发展现状1
1.3课题的研究内容与技术路线3
2有限元计算相关理论5
2.1引言5
2.2计算的相关理论5
2.2.1冲压回弹模拟的有限元理论基础5
2.2.2板料冲压仿真的流程6
2.2.3单元类型的选择6
2.2.4边界条件的处理7
2.3小结9
3板料拉延过程的有限元分析10
3.1引言10
3.2前处理11
3.2.1数据导入与网格化分11
3.2.2工具与工序定义20
3.2.3控制成形参数设置26
3.3提交计算27
3.4结果后处理及分析28
3.5小结33
4板料回弹的数值模拟34
4.1引言34
4.2回弹分析34
4.3回弹数值模拟前处理35
4.3.1导入模型进行回弹分析35
4.3.2导入成形零件边线35
4.3.3回弹分析设置37
4.4提交计算39
4.5回弹计算结果处理及分析39
4.6小结40
5汽车覆盖件回弹因素影响分析41
5.1引言41
5.2压边力的影响41
5.3材料参数的影响44
5.4板料大小的影响46
5.5结论48
6结论与展望49
6.1结论49
6.2展望49
参考文献50
附录1:
英文资料51
附录2:
中文翻译63
致谢69
1绪论
1.1我国汽车覆盖件模具发展现状
自2008年以来,我国汽车产销量以极快速度增长,汽车工业发展为汽车模具发展提供了极大的市场机遇,据有关资料显示,在美国、日本等汽车制造业发达的国家,汽车模具在整个模具制造业中占有50%的份额。
而在我国,只有1/3的模具产品服务于汽车制造业,因此汽车模具市场在我国仍有非常大的发展空间,而汽车覆盖件是整个汽车模具中最重要的组成部分,也是技术最密集加工难度最大的一部分。
由于汽车工业的快速发展,汽车覆盖件及相关产品市场需求量也急剧增加,因此许多企业加大了技术改造力度,一些新建企业也快速发展,是汽车覆盖件生产能力大幅提高,经过技术改造原行业中公认的四大模具厂:
一汽模具,东风汽车模具,天津汽车模具,四川成飞集成都有了生产大中型汽车覆盖件模具500万左右工时的能力。
从近年来看,民营企业发展较快,外资企业也进入中国,其中日资和台资最为活跃,其中被中国机械工业联合会授予“汽车模具之乡”的河北省泊头市已有20多家汽车覆盖件生产企业,上海目前也集中了十几家,比亚迪、长城、瑞丰、屹丰、华庄等一大批民营汽车模具生产企业由于投资力度大、起点高、服务对象明确,已成为异军突起的生力军。
1.2汽车覆盖件CAE分析国内外发展现状
冲压工艺、结构设计和制造技术是汽车模具生产技术的集中体现,这些技术的进步主要取决于CAD/CAM/CAE技术的提高。
在汽车覆盖件模具制造行业,计算机应用技术正越来越显示出其核心技术的作用。
据统计,在欧美国家,汽车覆盖件模具设计制造时,已大量采用三维CAD和有限元仿真技术,比例高达70%-90%,pro/E,UG,autoform,dynaform等软件在其中扮演了不可替代的作用,其效率高,数据库功能强大,设计准确性高等特点使汽车覆盖件模具产业生产效率和经济性大大提升。
因此当前许多大的模具企业纷纷加大对汽车覆盖件制造的资金,人才和硬件设施的投入,但是这些投入必须经过技术的学习、普及以及沉淀以树立基础,在我国汽车模具工业大而不强的背景下,要赶超发达国家并不容易,尤其是在核心技术难以外漏,控制严密的情况下,目前国内模具制造水平同国际先进水平的最大差距就体现在冲压工艺水平的差距上。
以往我们的冲压工艺技术主要靠人的经验,随着国内高品质的车身生产周期变短,靠过去的经验来完成冲压工艺是不可能。
就CAE技术的工业化应用而言,西方发达国家目前已经达到了实用化阶段。
通过CAE与CAD、CAM等技术的结合,使企业能对现代市场产品的多样性、复杂性、可靠性、经济性等做出迅速反应,增强了企业的市场竞争能力。
在许多行业中,计算机辅助分析已经作为产品设计与制造过程中不可或缺的一种工艺规范加以实施。
如,以国外某大汽车公司为例,绝大多数的汽车零部件设计都必须经过很多次的计算机仿真分析,否则就无法设计审查,也就无法试制更别说投入生产。
计算机数值模拟现在已不仅仅作为研究的一种手段,也已经在生产实践中作为必不可少的工具使用。
以有限元模拟分析软件为代表的CAE技术在国际上的应用已有近30年的历史。
近10年来,塑性变形理论在板料成形技术中的应用取得了很大的进步,使CAE技术在汽车模具制造中的应用变得非常成熟,将CAE应用于冲压工艺设计,可使试模时间减少50%以上。
目前,CAE技术已成为国外大型汽车和模具企业必不可少的工具。
CAE的广泛应用,应归功于 CAE商业软件的大力发展,其中代表性的软件有:
● 法国ESI公司的PAM-STAMP软件;
● 美国Lawrence Livemore国家材料实验室的LS-DYNA3D软件;
● 美国ETA公司的Dynaform软件;
● 瑞士Autoform公司的Autoform软件。
这些软件都有各自的长处,针对板料成形分析都已达到实用和专业的要求。
目前,国内所有一流的汽车模具厂商都采用了CAE软件,并以 Autoform的应用最多。
天津汽车模具有限公司通过长时间的的努力,CAE应用比例已经达到了100%,显著地缩短了制模周期。
在分析方面,针对冲压成形,使得确定棱线偏移、冲裁角度、拉延冲击滑痕、面成形品质、成形力、压边力等各种分析得到完善,分析内容的广泛性和作用性都已超出了原来的CAE范筹。
现在,CAE技术发展的重心是工艺参数的自动优化和后置分析,如果解决了这两个问题,将又一次带来革命性的发展。
因为汽车覆盖件具有形状复杂、材料薄、结构尺寸大、表面质量高和多为复杂的空间曲面等特点。
在冲压时毛坯的变形情况复杂,故不能按一般拉深件那样用拉深系数来判断和计算它的拉深次数和拉深可能性,且需要的压料力和拉延力都较大,各工序的模具依赖性强,模具的调整工作量也大。
所以汽车覆盖件模具设计的主要任务就是要解决好冲压过程中板料不同部位之间材料的协调变形问题,既要避免局部区域因变形引起的过薄甚至拉裂,又要避免起皱或在零件表面上留下滑移线,还要将零件的回弹控制在规定允许的范围内。
这时,板料冲压过程的CAE分析与仿真就能在实际工程中解决冲压工艺难题,如计算应力应变、金属的流动、板厚、残余应力、模具受力等,预测可能的缺陷及失效形式,如比较普遍的破裂、起皱、回弹等。
这样在汽车覆盖件的设计中采用数值模拟技术能从设计阶段准确预测各种工艺参数对成形过程的影响,进而优化工艺参数,缩短模具的设计和制造周期,降低产品制造成本,提高冲压件和模具产品质量。
1.3课题的研究内容与技术路线
本课题以某车型汽车防撞梁制件为研究对象,利用数值模拟和理论分析相结合的方法,对制件的冲压过程以及回弹过程进行数值模拟,对拉延中影响制件最终效果的多种因素进行分析,并总结规律。
具体研究步骤如下:
1.用UG8.0对制件进行修改将多面删除,并以.iges格式导出。
2.用Dynaform软件进行制件的拉延有限元分析,对制件进行前处理设置,参数改变,如板料位置,压边力,冲裁速度改变等。
生成.dynain文件为后置处理作铺垫。
3.用Dynaform软件进行制件的减薄率和成形极限图进行分析,对制件进行简单的设置后,进行提交计算结果,最后根据后处理来分析关于各参数影响规律。
4.分别改变压边力,板料位置与冲裁速度等参数依次按照第二步与第三步进行分析,从而总结出关于回弹影响因素的规律,得出结论。
课题的研究技术路线如图1所示:
导入CAD模型
导入Dynain文件
有限元网格化分
导入切边线
定义毛坯材料属性
冲压类型定义成形工具
定义毛坯及材料属性
后置处理分析结果
提交求解器计算
后置处理分析结果
结果评估
图1拉延仿真模拟过程
输出计算结果
2有限元计算相关理论
2.1引言
本章主要叙述的是关于回弹产生的原因,有限元计算所涉及的理论以及减少回弹的策略分析。
2.2计算的相关理论
板料的回弹是板料冲压成形的过程中产生的一种最常见的缺陷形式,其主要的原因是由于板料在冲压成形的结束阶段,当冲压载荷被逐步释放或卸载时,在成形过程中所存储的弹性变形能要释放出来,引起内应力的重组,进而导致零件外形尺寸的改变。
产生回弹主要是由于:
(1)因为当板料内外边缘表面纤维进入塑性状态,而板料中心仍旧处于弹性状态,这时当凸模上升去除外载荷后,板料产生回弹现象。
(2)因为板料在发生塑性变形时总是伴随着弹性变形的消失,所以板料在冲压成形过程中,特别是在进行弯曲成形时,即使内外层纤维完全进入了塑性变形状态,当凸模上升去除载荷后,弹性变形消失了,也会出现回弹现象,因此回弹是板料冲压成形过程中不可避免的一类缺陷,产生回弹将直接影响冲压零件的成形精度,从而增加了调试模具的成本以及成形后进行整形的工作量。
2.2.1冲压回弹模拟的有限元理论基础
板料冲压回弹的模拟从数值计算上分析是一个高度非线性的问题,涉及到材料、几何和接触非线性。
在本文的模拟数值计算中将选用更新Lagrange法和速率型的本构关系去处理冲压回弹过程中的大应变、大变形问题[5]。
采用逐级更新Lagrange法是弹塑性有限元基础,在坐标下以t时刻构形为参考构形的虚功率原理为
(2-1)
式中V,A分别为参考构形的体积和表面积;,分别为参考构形的体积力率和面积力率;为第一类Kirchhoff应力率。
假设塑性变形体积不可压缩,可得与Cauchy应力的关系为
(2-2)
将式(2-2)和本构关系方程式代入式(2-1),得到单元平衡方程并按常规方法组装成总体刚度方程
(2-3)
板料冲压回弹过程是大位移大变形过程,一般采用速率型的本构方程。
经典的基于流动理论正交各项异性希尔二次屈服函数的速率本构方程可表示为
(2-4)
(2-5)
式中为Kirchhoff应力的Jaumann导数;为应变率;为弹性本构矩阵;H为硬化参数;为屈服函数确定的等效应力。
屈服函数为
(2-6)
其中,P、Q、R分别代表材料在90°、45°、0°方向上的各向异性指数。
2.2.2板料冲压仿真的流程
严格地讲,板料的成形和回弹是两个既相互关联又相互独立的过程。
通常所说的成形过程一般不包括回弹在内,而完整的汽车覆盖件冲压成形的回弹仿真过程应包含两个过程:
冲压成形(加载)过程仿真和回弹(卸载)过程仿真。
前一步计算是回弹过程模拟的基础,为其提供应力、应变等数据[9]。
本文所研究的板料成形回弹仿真的主要过程如下:
(1)导入成形仿真的结果文件在Dynaform的前处理器中,导入成形仿真过程中计算生成的结果文件Dyanin文件。
该文件包含成形过程中板料所有的应力、应变等情况;
(2)定义毛坯选择回弹仿真计算用的壳单元公式,积分点个数,定义毛坯的材料属性;
(3)导入切边线对零件进行切边过程的仿真;
(4)设置回弹约束回弹分析时,必须施加适当的位移约束排除刚性运动。
按照零件的变形情况添加边界条件,限制板料刚性位移;
(5)根据计算情况选择单步或多步隐式算法;
(6)后置处理打开回弹仿真的结果文件,查看零件的回弹前情况和回弹后的应变情况。
2.2.3单元类型的选择
在进行板料冲压成形CAE分