提高码头矿石堆场预制轨枕施工效率Word下载.docx
《提高码头矿石堆场预制轨枕施工效率Word下载.docx》由会员分享,可在线阅读,更多相关《提高码头矿石堆场预制轨枕施工效率Word下载.docx(33页珍藏版)》请在冰豆网上搜索。
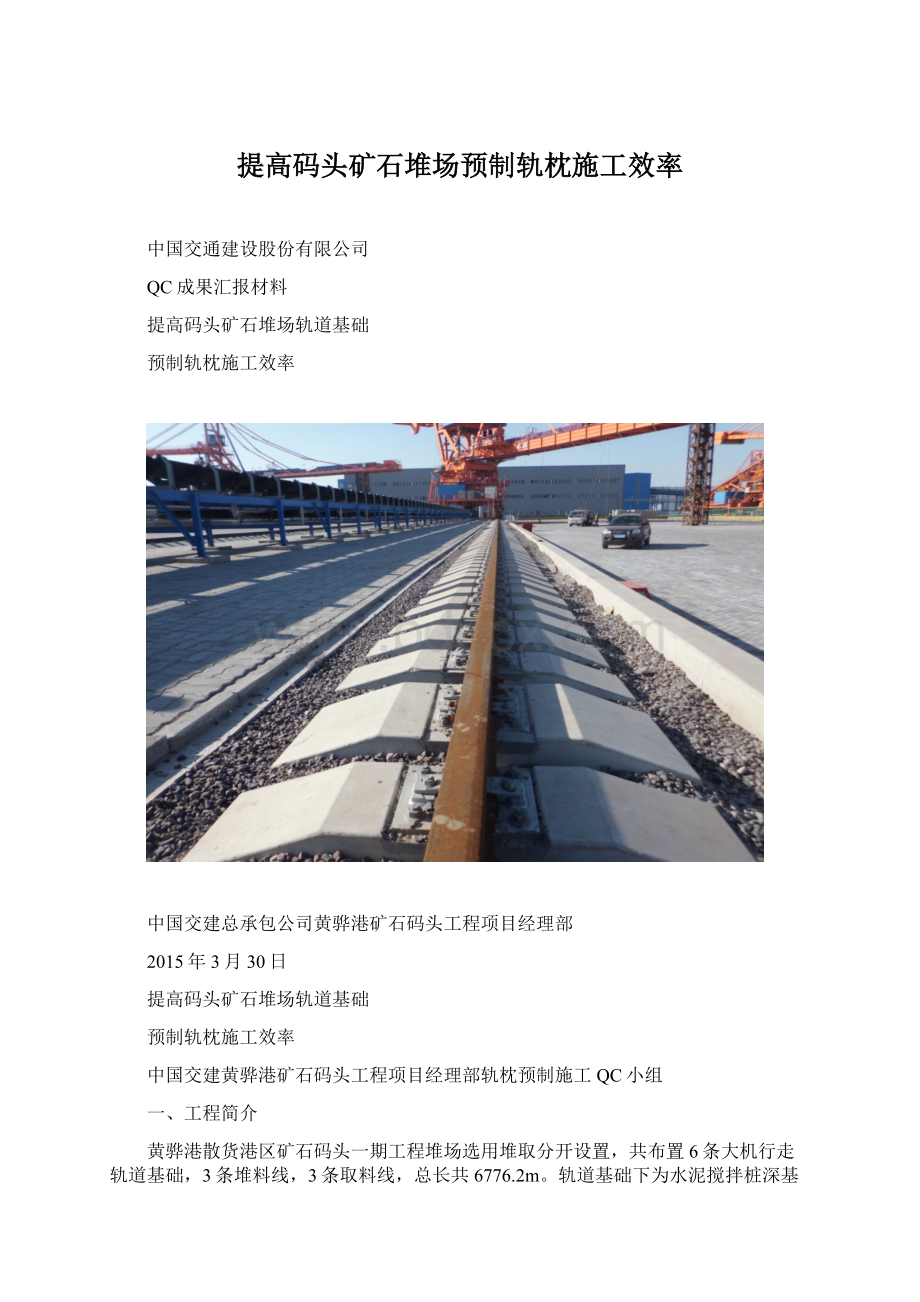
5
取料机BQ2
1113.8
188
3572
6
取料机BQ3
合计
6776.2
1142
21698
760537Kg
黄骅港地区堆场轨道基础工程以往大多采用现浇钢筋砼轨道梁基础,经常因为不均匀沉降影响使用且修复困难,故吸取以往弊端,在矿石码头工程堆场部分首次使用柔性基础作为堆取料机的轨道基础,即由预制轨枕替代刚性混凝土结构,6条轨道基础的轨枕预制数量庞大,且构件小,外观质量要求高,工期紧,原计划工期7个月,214个日历天,为此我们成立了提高码头矿石堆场轨道基础预制轨枕施工效率QC小组。
二、小组概况
黄骅港矿石码头工程项目经理部提高码头矿石堆场轨道基础预制轨枕施工效率QC小组成立于2014年3月1日,由项目经理何文柱任顾问,总工毛泽英任组长,副经理王力彬任副组长,小组成员共计10人。
自小组成立以来,积极开展创新工艺活动,围绕轨枕预制施工效率低,从各施工环节入手,共改进3项工艺,即加工制造1台钢筋加工设备、一个道钉预留孔模具取拔器、提高预制轨枕外观质量,通过本次QC活动的有效实施,大大提高了轨枕预制施工效率,至2014年8月,优质高效的完成了轨枕预制施工任务,比原计划工期提前1个月时间完成。
小组活动时间:
2014年3月-2014年9月。
1、小组信息
表2:
QC小组介绍表
小组名称
中国交建黄骅港矿石码头工程项目经理部提高码头矿石堆场轨道基础预制轨枕施工效率QC小组
成立时间
2014年3月
课题名称
提高码头矿石堆场轨道基础预制轨枕施工效率
课题注册
2014年3月在公司质量安全监督部注册
组长
毛泽英
活动时间
2014年3月至2014年10月
小组成员
10人
小组类型
创新型
注册编号
hhzxmb-2014-03
活动频次
20
出勤率
100%
小组成员基本情况
姓名
性别
年龄
学历
职称或职务
组内职务
组内分工
何文柱
男
50
本科
项目经理(高工)
顾问
女
49
总工(高工)
总体规划、成果撰写和申报
王力彬
36
副经理(高工)
副组长
总体部署、实施
孙忠良
30
技术员(工程师)
组员
现场负责,数据处理
廖永波
28
质检员(助工)
现场技术,质量检查
李芳回
31
副总工(工程师)
现场技术,数据处理
7
赵洪亮
34
试验主管(工程师)
现场试验
8
张志贵
45
大专
工长
现场工长
9
王磊
10
李帅
26
技术员(助工)
现场技术
制表:
孙忠良审核:
毛泽英日期:
2014.3.5
2、小组活动计划表
表3:
小组活动计划表
时间
内容
3月
4月
5月
6月
7月
8月
9月
上旬
中旬
下旬
现状调查
目标确定
原因分析
要因确定
制定对策
对策实施
检查效果
总结
计划进度:
实际进度:
毛泽英时间:
2014年3月15日
三、选题理由
1、工期要求:
小型预制构件数量大,外观质量要求高、工期紧,原计划工期7个月,但受环境、施工条件、天气因素制约,实际有效工期只能按6个月考虑。
2、效益要求:
节约成本、创优增效,又好又快完成预制轨枕施工任务。
3、工艺创新要求:
在黄骅港地区首次采用预制安装轨枕,以前没有成形工艺和特定钢筋加工设备,常规钢筋加工设备和施工工具已不能满足实际施工要求。
图2:
选题理由图
制图:
基于上述情况,我们决定以提高码头矿石堆场轨道基础预制轨枕施工效率为课题,开展QC小组活动。
四、现状调查
小组成员于2014.3.1-2014.3.31,在组长毛泽英的带领下,对轨枕钢筋骨架和已施工完成的轨枕进行现场调查,共检查50根,平均每根轨枕预制施工完成时间约500min,即8.3h,约1.04个工作日。
采用商品混凝土,2个班组施工人员,100套模板同时施工,2台8m3混凝土罐车运输商品砼到预制场,1台罐车砼可同时浇注50根轨枕,每根轨枕为C40砼0.16m3/根,目前共需预制完成轨枕A型和B型共22840根,则需施工日历天22840根÷
100根/1.04d=238d,大于计划工期214个日历天。
表4:
一根轨枕预制施工效率调查汇总表
调查项目
施工完成时间(min)
累计完成时间(min)
占总完成时间百分比(%)
累计完成时间百分比(%)
钢筋加工45根/33Kg
230
46
道钉孔模具拆除
180
410
82
钢筋绑扎成骨架
440
88
混凝土浇筑
25
465
93
钢筋下料
485
97
模板准备:
打磨、刷脱模剂
15
500
100
累计施工完成时间
据调查表,制成要素排列图如下:
图3:
要素排列图
毛泽英审核:
王力彬日期:
2014.3.15
根据排列图,可以看出影响预制轨枕施工效率低的主要问题是:
钢筋加工,道钉孔模具拆除。
五、课题目标
(1)对现有钢筋加工设备和模具取拔器改造升级,加工制造新型适用的钢筋加工设备和道钉孔模具取拔器。
(2)通过对预制轨枕进行设备创新和工艺改造,并在每一道工序施工中进行有效的管理和控制,在保证质量的前提下,提高施工效率,跟原计划工期比,将施工进度提前20%。
(3)各检测项目合格率达到90%以上,分部工程合格率100%,分项工程合格率100%,工序一次验收合格率100%。
六、原因分析
小组全体成员经过多次组织专题会议研究,并大量收集现场操作工人、班组长、机械工程师的意见,寻找导致钢筋加工效率低、道钉孔模具取出困难的原因,通过汇总绘制因果图如下:
图4:
预制轨枕施工效率低原因分析因果图
毛泽英日期:
2014.4.1
七、要因确定
7.1制定要因计划表
2014年4月5日,根据关联图中的末端因素,小组成员制定了要因确认计划表,具体见下表。
表5:
要因确认计划表
末端因素
确认方法
标准
负责人
完成时间
常规钢筋加工机械不适用,钢筋加工效率低,误差大
现场调查、考察设备加工厂
针对轨枕2号钢筋形状,对钢筋加工设备升级改造,采用新型钢筋加工机械多快好省加工钢筋。
2014.4.10
道钉孔模具取拔器设计不合理,取孔困难
现场调查
改进工艺,采用新制作的取拔器取出模具。
模板变形
现场检查
更换已变形模具,重新制作强度、刚度满足要求的新模具
技术交底不到位,针对性不强
内业检查
交底内容要求工艺流程、设备使用、质量要求等都有着详细明确的说明
施工人员质量意识淡薄
提高质量意识,采取奖惩措施
现场操作不规范
现场培训,并做标准问卷调查要求合格率≥80%。
同时统一工艺流程,形成操作规程,提高施工人员操作技能水平和熟练程度。
道钉孔预埋钢筒未刷脱模剂(黄油)
清理轨枕模板时,逐个检查每个预埋钢筒是否涂刷了黄油。
振捣不到位,二次收面时间把握不准
现场检查对比
掌握水泥初凝时间,及时收面
养护不到位,成品保护意识不强
加强监督,保证养护到位。
同时加强教育和宣贯,禁止野蛮施工。
原材料供应不及时,待料时间长
每周到砂石料场、水泥厂敦促一次,或电话联系要求及时供应。
孙忠良赵洪亮
11
脱模剂不合格
不得采用废机油作脱模剂,采用优质脱模剂
12
一个预制场预制施工场地受限
找监理、业主联系,重新划归一块堆场作为构件存放区。
13
海边突风多,施工环境差
完善钢筋棚等设施,提供较好条件的作业环境。
毛泽英制表时间:
2014.4.5
7.2确定要因及采取的措施
根据要因确认计划表,小组成员对13个末端因素逐一进行确认,并确定出主要原因。
确认一:
常规加工机械不适用,轨枕钢筋加工效率低,误差大
采用常规钢筋加工机械弯曲机进行钢筋加工,首先根据图纸的钢筋规格、型号、尺寸进行集中下料,在钢筋加工平台上,用卷尺刻划好刻度,根据2号钢筋的具体尺寸、角度,选取弯头,并采用圆规刻划出角度线,弯折角加工时,根据操作平台上已经刻划好的尺度线,角度线进行加工作业,操作者必须加工技术娴熟,责任心强,尽管如此,由于该2号筋加工时弯折角度较多(每根6个角),操作繁琐,在加工过程中长度与角度时有偏差,因此加工时会耗费较大的人力、物力,施工效率较低。
图5:
轨枕②号主钢筋形状图
一根主筋6个弯折点,逐个弯曲加工费工费时,起弯点和弯折角误差大,轨枕混凝土保护层厚度难以控制,根据轨枕钢筋形状,经反复研究探讨,不断试验,小组全体成员一致认为钢筋加工设备,是导致施工效率低,钢筋弯折点位置和弯折角度误差大,保护层厚度难以控制的主要因素,迫切需要一台新型钢筋加工设备进行轨枕钢筋加工。
结论:
常规钢筋加工设备不适用于加工2号钢筋,是导致轨枕主筋弯折点位置和弯折角度误差大主要因素。
故常规钢筋加工机械不适用,轨枕钢筋加工效率低,误差大是主要因素。
确认二:
第一批轨枕预制时,采用“红酒启子”原理,利用下端车丝的螺杆作为工具,将螺杆下端带丝口部分旋转拧入预埋钢筒丝扣里,然后用力向外拔。
一般在准备轨枕模板时,先将预埋钢筒模具的表面涂上黄油,以方便取出,但在取孔时,由于难以准确把握混凝土初凝时间,钢筒与混凝土之间摩擦力较大,仅靠人工用力向上拔出预埋钢筒模具很费力,钢筒经常被卡在里面,没办法就硬敲硬拔,造成孔口破损,有的预埋钢筒即使硬敲硬拔
,导致丝扣滑脱也很难拔出,而导致部分轨枕报废。
经小组讨论,需要对预埋钢筒模具取拔器进行改进。
图6:
“红酒启子”取拔器
道钉孔模具取拔器设计不合理,取孔困难是主要因素。
确认三:
模板变形图7:
轨枕模板
副经理王力彬对轨枕模板进行检查,发现现有模板,钢板薄,多少有些变形,预制出来的轨枕长度、宽度、厚度、对角线差及外露面平整度均有偏差,但都在规范范围内,不至于影响到钢筋保护层。
前期本来模板制作数量也不够,还需要订制新的模具,故补加工时提高了钢模板的钢板厚度,提高了强度,共增设模板310套,其中A型模板10套,B型模板300套。
确保备用模板50套,方便随时可以更换。
模板变形不是主要因素。
确认四:
毛泽英和孙忠良在2014年4月10日查阅了开工前的技术交底通知单,发现交底内容对工艺流程、设备使用、质量要求等都有着详细明确的说明,并且交底到了每个施工工人,签字齐全。
项目部为避免施工人员流动,造成漏掉的现象发生,在同一个工序上还组织二次交底。
图8:
技术交底
技术交底不到位,针对性不强,不是主要因素
确认五:
预制轨枕开工后,于2014年4月,组织了一次技术质量培训,并在施工现场张贴质量宣传标语,以提高施工工人的质量意识。
施工过程中,通过与现场施工人员交流,发现参与此项施工的工人质量意识均保持较高的水平。
图9:
质量培训讲座
施工人员质量意识淡薄不是主要因素。
确认六:
通过现场检查,预制场工人均是熟练工,同时我们也进行了现场培训,都明白严格按照设计图纸、钢筋下料单进行加工,唯有2号钢筋弯折角比较多,操作频繁,质量难以控制,加工速度慢,除2号、3号钢筋外,其他型号钢筋制作没有问题,合格率较高。
进行现场培训,并做标准问卷调查,要求合格率≥80%。
同时统一工艺流程,形成操作
规程,提高施工人员操作技能水平和熟练程度。
图10:
现场培训及钢筋加工示范
现场操作不规范不是主要因素。
确认七:
道钉孔预埋钢筒未刷黄油
在施工现场,施工人员清理轨枕模板时,孙忠良负责逐个检查每个预埋钢筒是否涂刷了黄油,基本做到了没有漏刷。
道钉孔预埋钢筒未刷黄油不是主要因素。
确认八:
经检查预制轨枕混凝土存在振捣时间不够、遗漏二次振捣和二次收面时间把握不准的情况,准确掌握砼凝结时间,浇筑砼时,多留置1组现场同步养护条件试块,及时进行收面工作。
振捣不到位,二次收面时间把握不准不是主要因素。
确认九:
海边风大,突风多,刚浇筑完毕的轨枕由于没有及时覆盖养生,表面细裂纹较多,同时遇到道钉孔预埋钢筒难以拔出时,工人存在硬敲硬拔现象,造成孔口破碎,但归根结底是因为工具不好用的原因造成的,是孔口破坏严重的次要原因,但也需要加强教育,以提高施工人员成品保护意识。
养护不到位,成品保护意识不强不是主要因素。
确认十:
每周到砂石料场督促一次材料供应,毛泽英、赵洪亮对轨枕预制所用原材料进行抽检,发现质量不稳定,部分河砂含泥量大,部分碎石中石屑含量高,经与供应商交涉,解决了这个问题,保证了砂石料的质量。
另外采用的水泥品牌也经常更换,理由为河北环保局改善环境拆除大批水泥厂,造成水泥供应不足。
但为了确保轨枕砼外观色差一致,我们要求统一采用鲁北水泥普通硅酸盐P.O42.5水泥,并多次要求山东鲁北化工股份有限公司水泥供货商优先保证我方水泥需要量。
原材料供应不及时,待料时间长不是主要因素。
确认十一:
2014年4月22日,工程部长孙忠良针对采用废机油做脱模剂问题,对现场进行了跟踪调查,发现买回来不少废机油,且刷涂不均,造成混凝土表面污染,为此,孙忠良要求采购员当场退回已买回来的废机油5桶,另购优质机油作脱模剂。
脱模剂不合格,不是主要因素。
确认十二:
一个预制场预制施工,场地受限
预制场地受限,主要是构件存放区紧张,后来我们找监理、业主磋商,划出多用途码头空箱堆场一块场地临时存放轨枕,解决了这一问题。
一个预制场预制施工,场地受限,不是主要因素。
确认十三:
现场主要是完善钢筋棚等设施,提供较好条件的作业环境。
海边突风多,施工环境差,不是主要因素。
经过以上对每条末端因素进行调查分析和确认,小组成员召开小组会议,针对施工中存在的问题进行认真分析、研讨,确定导致预制轨枕施工效率低的主要原因如下:
1.常规钢筋加工设备不适用,钢筋加工效率低,误差大。
2.道钉孔模具取拔器设计不合理,取孔苦难。
八、制定对策
经分析确定的主要原因及对策表如下:
表6:
主要原因采取对策表
要因
对策
目标
措施
实施地点
常规钢筋加工设备不适用,钢筋加工效率低,误差大
对现有钢筋加工机械进行创新改造
提高2号钢筋加工质量和效率,以保证钢筋骨架绑扎的质量和效率。
按照钢筋设计长度、弯折角,制造定型钢筋骨架模具,采用液压系统对称冲压弯折点一次成型;
箍筋组合调直机、切断机、多功能弯曲机为一体,增加数控,进行批量加工。
主筋对称同步弯曲,弯曲角度达到设计要求;
箍筋集调直、切断、弯曲一体,加工一次成型,避免偏差累积。
2014.5.20
秦皇岛钢构件加工厂
道钉孔模具取拔器设计不合理,取孔苦难
改造道钉孔预埋钢筒模具取拔器
取拔器设备使用,效率高,孔口完好率高。
计划在现有的取拔器螺杆上加长丝扣,中部增加活塞锤,螺杆顶部增加挡块。
拆除时依靠活塞锤人工敲击上部挡块,从而产生向上拔的力量,缓慢取出道钉孔预埋钢筒,达到无破损取孔效果。
2014.4.30
施工现场
王力彬制表日期:
2014年4月12日
九、对策实施
2014年4月1日至2014年5月15日针对对策进行现场实施,具体实施如下:
实施一:
针对“常规钢筋加工设备不适用,钢筋加工效率低,误差大”要因
负责人:
毛泽英、孙忠良、张志贵
2014年4月初,我们邀请了秦皇岛机械厂技术人员到现场考察,对常规钢筋加工机械加工轨枕2号钢筋的现状,钢筋工人的熟练程度及单根弯折角加工的繁琐程度进行了解
。
重新制造新型钢筋加工设备势在必行,为此工程部长孙忠良带领机械工程师,对轨枕2号钢筋规格、形状、长度及数量进行了认真分析和研究,在机械工程师的设计、指导下,采用液压系统,定型模具,由秦皇岛钢构件加工厂制造,制造完毕,在厂家反复试验,改进,最后设备制造完成,然后运输到现场,最终于5月1日设备调试完成运至现场。
轨枕2号主筋加工采用该设备加工成型,设备如图所示。
图11:
液压系统,定型模具组的新设备
图12:
正在加工钢筋的新设备
首先根据设计图纸做好轨枕钢筋下料单,并对钢筋工进行详细交底,采用人工下料,严格控制每根钢筋的下料长度,分批送入钢筋加工设备
定位卡槽,启动液压冲压器,即加工成符合设计角度、形状的2号主筋。
在钢筋加工过程中,由技术员对半产品进行抽样检查,特别是钢筋的弯折点、弯折角度进行重点控制,根据检查结果及时修正设备预设参数,保证产品尺寸、角度符合设计图纸要求。
图13:
绑扎轨枕钢筋骨架图
实施二:
针对“红酒启子取拔器设计不合理,取孔困难”要因
王力彬、李帅
2014年4月初,由副经理王力彬牵头,组织技术员李帅、现场工长张志贵一起讨论,对现有“红酒启子”原理的模具取拔器进行改造,原来仅靠丝扣旋入预埋钢筒,敲击上拔,成功率较低。
改进方式如下:
先将螺杆另一端加长丝扣,使拧入预埋钢筒足够长,强度够,防止取拔时脱扣;
然后在螺杆中间增加能够上下敲击的活塞锤,在上下端均焊接定位挡板,上端挡板做成“一字型”,以方便省力的将螺杆旋入预埋钢筒模具。
取拔模具时,先将取拔器与预埋带螺孔的钢筒通过丝扣连接,操作时,用活塞锤向上敲击上部挡板,依靠活塞锤对螺杆的上拔力缓慢取出道钉孔模具。
施工过程中不断摸索改进道钉孔模具取拔器,同时对轨枕道钉孔预埋钢筒的丝扣部分进行了加厚,从而优化了预埋孔取拔工艺,完全改变了原来预埋钢筒难以拔出和拔出时破坏孔口边缘的现象,改进后不仅能够保证全部拔出,而且对预留孔的边角破坏现象明显减少,预留孔口基本无破损。
图14:
升级改进后的取拔器使用过程及效果
14.1将取孔器旋入预埋钢筒
14.2取孔过程中
十、检查效果
1、质量效果
⑴钢筋加工质量效果
2014年8月1日至8月30日,对现场加工的2号钢筋尺寸、起弯点、弯折角度质量进行现场检查,检查结果统计如下:
表7:
钢筋尺寸、起弯点位置、弯折角度质量检查结果
检查部位
测点数
合格点
不合格点
测点合格率(%)
平均合格率(%)
备注
1班组50根
98
2班组50根
96
并对其中发生的质量问题进行统计,如下表:
表8:
钢筋加工质量问题统计表
质量问题
频数(点)
累计频数(点)
频率(%)
累计频率(%)
弯折角度
15.4
起弯点位置偏差
23.1
38.5
骨架外轮廓尺寸
61.4
其它
……
依据统计表绘制出饼分图如下:
图18:
钢筋加工质量问题饼分图
通过饼分图得出,钢筋加工弯折角度、起弯点位置偏差、骨架外轮廓尺寸已经不是主要问题,通过设备改造升级钢筋加工的质量得到了很好的提升和控制。
⑵道钉孔模具取出质量效果
2014年8月1日至8月30日,对已预制完成的轨枕道钉孔质量进