第五章机床主运动部件设计Word格式.docx
《第五章机床主运动部件设计Word格式.docx》由会员分享,可在线阅读,更多相关《第五章机床主运动部件设计Word格式.docx(16页珍藏版)》请在冰豆网上搜索。
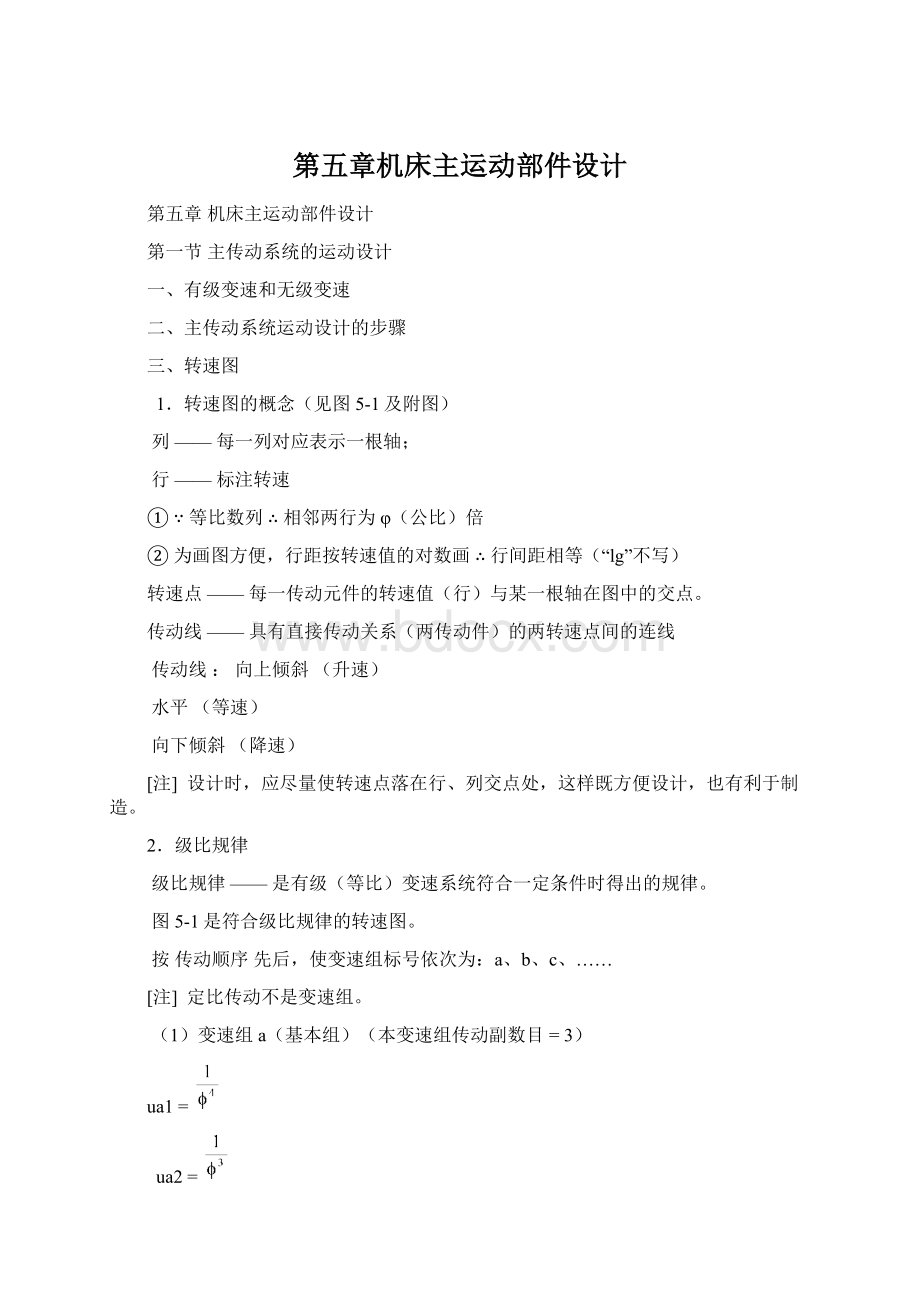
扩大顺序与传动顺序并不是一定一致);
若:
各变速组的传动副数目用pj表示,并根据扩大顺序分别定为p0、p1、p2、…。
注意:
基本组X0=1
第一扩大组X1=3=p0;
第二扩大组X2=9=p0·
p1(=3×
3)
以此类推可得:
∶
∶
第j扩大组Xj=p0p1p2……pj-1
依据此例分析,可得出具有普遍意义的“级比规律”(见书P.92)
基本组级比φX0=φ
第一扩大组级比φX1=φp0;
第二扩大组级比φX2=φp0p1
第三扩大组级比φX3=φp0p1p2
∶
第j扩大组级比φXj=φp0p1p2……pj-1
设计中,只要遵守“级比规律”,就可使主轴获得连续而不重复的、公比为φ的等比数列转速。
符合“级比规律”(单一公比φ)的传动系统称为“正常传动系统”。
“非正常转速图”举例(附图)
上图中若符合级比规律,则应该是X1=3,而
a)X1=4,大了!
出现转速空挡;
b)X1=2,小了!
出现转速重复;
(实际应用举例,见图5-14)
c)X1=1.5,非整数!
转速错开。
(实际应用举例,见图5-17)
3.变速组的变速范围
4.总变速范围(即主轴的变速范围)
四、结构网及结构式
(一)转速图对称画即结构网
图5-1(转速图)图5-2(结构网)
1.转速图包括定比传动,而结构网仅反映变速组;
2.一个转速图对应一个结构网,而一个结构网可画出很多不同的转速图;
3.转速图反映系统各部分真实的转速变化,而结构网仅反映变速组的相对关系;
4.各变速组的r以及传动比相互关系,转速图与结构网是相同的。
(二)结构网的数学表达式即结构式
1.结构式可表达如下(按传动顺序):
Z=pa·
pb·
pc
2.传动副数目选取原则:
每个变速组的传动副数目“P”一般取2或3。
以18级为例,可以有:
18=9×
2(两个变速组;
三根轴;
11对传动副)
18=6×
3(两个变速组;
9对传动副)
18=3×
3×
2(三个变速组;
四根轴;
8对传动副)
实际中取第三种。
(前两种主要问题是“9”、“6”设计困难、使用不便;
另外,两个变速组通常不能满足总变速范围要求)
3.结构网或结构式的选择
按传动顺序不同排列:
(仍以18级系统为例)
2
2×
3
18=2×
如对应图5-2的结构式为:
18=31×
33×
29
注脚为各组对应的级比指数。
(利用级比规律很容易写出)
[注]在结构式中,始终以传动顺序先后(自左向右)写变速组。
但按扩大顺序则有很多种不同排法。
再考虑扩大顺序不同,则有18种方案可选:
2918=31×
23×
3618=21×
32×
36
36×
2318=31×
29×
3318=21×
32
18=33×
31×
2918=32×
21×
3618=23×
18=36×
2318=36×
3218=29×
33
18=32×
2118=36×
3118=23×
31
2118=33×
3118=29×
每一种结构式对应一个结构网。
下面以12级为例观察结构网变化(仅画出12=3×
2六种变化)。
[注]结构网和结构式供方案讨论所用;
而转速图则是具体结构设计的依据。
五、主传动运动设计要点(一般原则)
1.各变速组的极限传动比和变速范围限制
主传动:
降速不要过急
umin≥1/4(避免齿轮太大)
升速不要太快umax≤2(斜齿可2.5)(避免振动和噪声)
∴组变速范围
≤8~10
进给传动:
≤
=14
2.减小传动件尺寸的原则
转矩T、功率P和计算转速nj之间有如下关系:
可见:
若功率不变,转速愈高,则转矩愈小。
这样就可使传动件的尺寸设计得小一些。
以下原则均出自此目的。
([注]目的若变,则原则也要变)
(1)“前多后少”原则
按传动顺序排列,使传动副较多的变速组尽量放在前面。
如:
18=3×
2(两对齿轮副的变速组放在最后)
[注]CA6140例外(24=2×
2)(这里的主要矛盾是“方便结构设计”)。
(2)“前密后疏”(或“前紧后松”)原则(图5-3)
按扩大顺序考虑,尽量先“基本组”、其次“第一扩大组”、再“第二~”……依次排列为好。
“扩大顺序”尽可能与“传动顺序”一致为优先考虑。
(3)“前慢后快”(或“前缓后急”)原则
即降速时,前面变速组降得慢些,最后变速组降得最多。
[注]以上原则主要是针对“中型机床”。
若“小型或精密机床”,则应主要考虑振动和噪声问题。
六、改善传动性能的其它注意事项
1.传动链要短
2.转速和要小
3.齿轮线速度要小
4.空转件要少
综上所述,变速传动系统运动设计要点可归纳为①②③④,即:
①一个规律②两个限制③三条原则④四项注意
七、转速图的拟订
以铣床主传动系统为例。
30~1500r/min——工艺范围要求(已定)
18级转速(公比φ=1.26)——工艺范围要求(已定)
电机转速:
1440r/min(选定)
可以看出:
电机主轴,总的趋势是降速,最大降速比为1/48
∴设计考虑的主要问题是:
怎样降速?
(1)首先考虑极限降速比(图5-4)
a)确定结构式
18级。
根据前述,显然是:
b)定比传动(降速)
一是考虑减少变速组的总降速比;
二是考虑变型方便。
c)合理分配降速比(图5-4为各组间最小传动比的连线)
以“前慢后快”为原则。
(2)画出各变速组其它传动线(图5-5)
根据已确定的结构式,即可画出各组其它传动线。
(3)画出全部传动线(图5-6)
对应画平行线,即可画出全部传动线。
[注]在实际中,转速图是需要经过反复修改才能完成的。
八、齿轮齿数的确定
首先确定定比传动。
定比传动:
①为了某种结构设计需要;
②为了传动比分配;
③为了使电机远离主轴箱(见图2-13、图4-2)。
[注]一个传动比,可以由许多种齿轮形成不同的搭配形式。
若传动比
,
则可以是:
u=
齿数和SZ:
SZ=Z1+Z2(一对啮合齿轮)
1.确定齿轮齿数应注意的问题
(1)齿数和不应过大(否则大齿轮会太大)
一般SZ≤100~120
(2)齿数和不应过小
①根切问题;
∴Zmin≥18~20
②最小壁厚;
(图5-7)a≥2m
③装配空间;
(若有在装配好以后需要操作或调整的环节,两轴间距不宜太小)
④操纵机构等的空间;
⑤轴承(支承空间)。
(3)主轴转速误差≤10(φ-1)%
[注]转速图中主轴的18级转速是根据标准数列写出来的。
(4)三联滑移齿轮中,相邻两齿轮齿数差>4(P.103,图5-9)
m(Z2+2)+
m(Z3'+2)<A
因为:
A=
m(Z3+Z3')
则有:
Z3-Z2>4
若Z3-Z2=4,(可修磨齿顶圆);
若Z3-Z2<4,(可考虑变位)。
[注]将图5-9中Z2'与Z3'的字母位置对调。
2.同变速组单一模数时齿数的确定
[注]同组同模数必然有(见图5-9):
(1)计算法
∴可得到以下公式(5-14):
uj——在拟订转速图时确定;
SZ——由设计者根据实际情况自定。
设计方法:
(先对具有最小齿数的一对齿轮求解)
①先确定最小齿数(任意、但合理地确定);
别忘了:
Zmin≥18~20
②根据
,计算出与之啮合的另一齿数;
③求出SZ(=zj+zj');
(确认SZ是否合适,若不合适,重选Zmin)
④确定了SZ,则可根据公式(5-14)计算出其它几对齿轮的齿数。
(2)查表法(表5-1)
3.变速组内模数不同时齿轮齿数的确定
同一变速组内两对啮合齿轮的中心距分别计算如下:
∵同一变速组内各处的中心距必然相等,即A1=A2=…
∴m1SZ1=m2SZ2=…
[注]e1、e2的引入是考虑计算方便(因为模数可能有小数)。
公式(5-17)计算出齿数和后,再根据公式(5-14)就可算出各个齿轮的齿数。
[注]书上例子中,
、
是基于工艺需要的考虑。
[注]关于齿数和选择的分析:
首先,根据“前慢后快”原则,最后变速组降速最急,因此,最后变速组的齿数和应选得较大,另外,输出轴通常直接承受负载,轴较粗,这也需要最后变速组的齿数和选得大些。
一般地,最后变速组的齿数和SZ≥100~120
其余变速组的齿数和一般<100,且越往前的齿数和一般越小。
八、齿轮的布置与排列
1.滑移齿轮的结构
滑移齿轮总是将几个齿轮固定在一起(或直接做成一体),并一起移动(具体结构后面将详述)。
①窄式和宽式
②齿轮的宽度
齿轮的宽度与模数有关,但在机床传动系统中,若模数差别不大,一般将齿轮的宽度全部做成一致(用“b”表示)。
③整体式和拼装固定式
拼装固定式的总宽即几个齿轮加起来的宽度;
而整体多联式则要在两齿轮中间留出退刀槽(见图3-7)。
整体式可做成窄式或宽式。
2.固定齿轮的轴向布置
固定齿轮必须根据滑移齿轮的尺寸及移动来确定位置。
①若固定齿轮轴向拉得较开,则浪费空间和材料;
②反之,则会铸成大错。
(见图5-10)请牢记一句话:
“一对齿轮完全脱离啮合以后,另一对齿轮才能进入啮合”。
一般取:
△=1~3mm
3.变速组内齿轮的轴向排列
(1)窄式结构轴向尺寸较小(见图5-11、图5-12)
(2)多变速组宽窄结合可减小轴向尺寸(见图5-13)
[注]此处轴向尺寸的减小,可能意味着径向尺寸的变大。
(3)采用公用齿轮可减小轴向尺寸(见图5-13)
[注]这里也有径向尺寸的变大问题。
4.径向尺寸
(1)一对啮合齿轮的齿数差越大,则径向尺寸越大(假设小齿轮大小相同)。
下面两图总传动比均为1/4,但径向结构差别很大。
(2)轴线重合可减小径向尺寸
如CA6140的ⅢⅤ(背轮机构)(见图5-16)
5.采用多速电机
一台多速电机就相当于一个变速组,等于使整体结构的轴向和径向尺寸均缩小了。
综合:
一般地,轴向和径向尺寸的增大和减小经常呈反比,是一对矛盾。
所以,设计者必须根据实际情况,清楚关键是什么,然后予以取舍。
第二节主传动的几种特殊变速方式
一、扩大变速范围的传动系统
1.增加变速组的传动系统
由Rn=r0r1r2……rj
可知:
增加变速组可以扩大总的变速范围。
但根据
最后扩大组的rj最大;
所以,增加变速组就可能使rj>8,
∴当增加变速组时,若最后扩大组的rj>8,则采取:
减小xj,以使rj减小,但Rn还是增大了。
(见图5-14)
2.采用背轮机构的传动系统
[注]修改图5-15。
书中文字是对的,但图中应将Z1改为固定齿轮,将Z4改为滑移齿轮(参考图2-9(c))。
此机构可使组内的rj由≤8增大到≤16。
3.采用分支传动的传动系统
(见图5-16)
[注]分支传动是与主要传动路线并联的,它对原系统的限制不产生影响;
但分支部分增加了一些高的转速级数,即增大了Rn。
二、采用混合公比的传动系统
公比的选用:
①公比φ取小一些——能较好地满足工艺要求;
能减少相对速度损失。
但是,转速级数z的增多,会使机床结构复杂化。
例如:
1)用于大批量生产的自动化机床,要求高生产率,相对转速损失要小,因此φ要取小(1.12或1.26)。
2)大型机床,机动时间长,φ应小些(1.12或1.26)。
3)中型机床,加工范围大,因此希望转速级数z要多一些,但结构又不希望太复杂(常取1.26或1.41)。
②公比φ取大一些——
例如:
小型机床切削加工时间常比辅助时间少,箱体小所以结构要求简单一些,且级数z也不多(常取1.58或1.78)。
③公比φ的混合选取——常用转速段,φ取小一些;
不常用转速段,φ取大一些。
例如书中所述(见图5-17):
在25~63(r/min)以及800~2000(r/min)这两段中,实际用得很少,但有时必需要使用(取φ=1.58);
中间段用得多(取φ=1.26)。
本例主轴16级转速,符合级比规律的结构式为(称为“基型”):
16=21×
22×
24×
28(取公比φ=1.26)
∵1.58=1.26²
∴转速图格线按1.26公比画,只要在需要1.58公比的位置空一格,即可达到要求。
方法:
基型的基本组级比指数x0=1,将x0变大,x0每增加1,即会使主轴转速数列多出一个空格。
增加部分用“x0'”表示。
即:
使x0变为xb,xb=1+x0'
一般地,使变型后上下产生的空格相等,这样就必须使x0'取偶数,本例x0'可取2、4、6。
(若x0'=8,则xb=9,超出了rj允许的范围)。
另外,x0变为xb后,可能比第一扩大组、甚至比第二扩大组的级比指数都大。
所以,应该根据“前密后疏”原则将基本组向后调整。
具体设计步骤参照书上(P.109)举例进行。
三、交换齿轮传动系统(图5-19、图5-20)
特点:
1.可以使结构简化,传动刚性比滑移齿轮好;
2.更换齿轮麻烦。
(通用机床最好别用)([注]Y3150E型滚齿机)
3.设计考虑:
①悬臂设计(所以要特别注意刚性问题)。
②在箱体内应安排在上部;
或轴向伸出箱体安排。
③因为悬臂,传递转矩较小时刚性可较好。
四、多速电动机传动系统(图5-21、图5-22)
特点:
1.可以使结构简化,可在运转中变速;
(方便)
2.功率总是按大的选;
(高速时功率浪费)
3.1.58和1.78公比不适用;
4.除非公比φ=2,否则不符合“前密后疏”原则。
五、采用公用齿轮的传动系统(图5-23)
采用公用齿轮可减少齿轮数,并可缩短轴向尺寸。
但公用齿轮的受力比较复杂;
磨损较为严重(比其它齿轮的寿命短);
齿数计算比较复杂。
六、无级变速传动系统(图5-24)
特点在第二章已有叙述。
(图5-24)是一个无级变速器和机械有级变速组合的结构网。
图中主要想说明机械传动比应选取得小一些,以造成一定的重复(否则在结合部有可能出现空挡)。
第三节主传动的结构设计
(图5-26)是传动部件设计步骤框图。
[注]课程设计要做的事情。
一、箱体内各轴线的布置
1.展开图(图5-27、图5-28)
转速图画好,齿数、模数确定后,展开图中的总径向尺寸即已确定(当然,怎样展开还是需要认真考虑的)。
轴向尺寸则是需要在展开图中具体设计确定的。
[注]展开图上不是顶,下不是底。
画图时一般用箱壁将上下封闭,但若图中放不下时,也可如图5-27下端用波浪线断开。
展开图中要求标出各轴的轴号,要求标出各种配合尺寸。
2.剖面图(图5-29、图5-31)
剖面图主要是确定各轴线在空间的相对位置。
[注]实际设计中,展开图和剖面图设计是应该同时进行的,是需要互为参考、对照修改的。
(如图5-29中,Ⅰ、Ⅳ、Ⅵ轴在装配好以后均需要调整,所以其上部至箱盖不能有东西挡住)
剖面图各向均反映实际尺寸。
图中应标出总体尺寸、配合尺寸、中心距以及一些重要的参数。
二、片式摩擦离合器的选择和计算(略)
三、(车床)Ⅰ轴(输入轴)的设计
[注]①轴号基本按传动顺序排列标注;
②箱体内的第一轴为Ⅰ轴!
表5-5皮带轮与轴的装配结构
四、传动轴设计
除“主轴”以外的轴均称为“传动轴”
1.特点
传动轴一般不承受(或仅承受很小的)外部轴向载荷。
主要目的是传递转矩和运动,应有足够的强度和刚度,以确保传动平稳。
2.轴的结构
轴,一般设计成阶梯轴;
装轴承处需要磨削;
传递运动和动力依靠键。
图5-33解释花键的加工。
3.轴承的选择
[注释]①关于花键和平键的选择;
②关于“在没有轴向力时,采用圆锥滚子轴承”的问题;
③关于镗孔,(见图5-34);
④关于“两孔间的最小壁厚,不得小于5~10mm”;
⑤关于“花键轴两端装轴承的轴颈尺寸至少有一个应小于花键的内径”。
4.轴的轴向定位
表5-6回转轴的常用轴向定位结构
表5-7非回转轴的常用轴向定位结构
表5-8固定齿轮常用轴向定位结构
五、主传动部件中常用装置的设计要点简述
1.主传动的变速装置
(1)交换齿轮变速机构
主要用于自动或半自动机床、专用机床及组合机床等生产率要求较高、加工范围较窄的设备中。
(2)滑移齿轮变速机构
由于其操作方便、并较容易得到较大的变速范围,因而在通用机床中得到了广泛的应用。
(3)离合器变速机构
采用离合器后,齿轮被轴向固定,传动刚性好;
除齿式离合器外,其它离合器均传递转矩较小;
摩擦离合器可在运转中变速,但其传动效率较低,且结构较大。
关于“超速”。
“超速”可有两种理解:
一是不参与传递运动和动力的齿轮高速空转;
二是不参与传递运动和动力的齿轮在超过极限传动比的情况下高速空转。
(本书定义为后一种)
见图5-35。
(a)M1合上时,(b)D合上时,(c)A或D合上时,(d)C合则B高速空转;
C超高速空转;
B高速空转;
D或A均为低速空转;
B合则C超高速空转。
2.主传动的开停装置
3.主传动的制动装置
4.主传动的换向装置
六、计算转速的确定
传动链中的基本构成是轴和齿轮,轴和齿轮主要是根据所传递转矩的大小来进行设计计算的。
(N·
m)
(对于专用机床,其加工范围很窄,所以传动件的设计针对性很强,较好设计。
在此不做讨论)
对于通用机床,其加工范围很宽。
功率大、调速范围宽。
对传动件一般是根据其所传递的最大转矩进行设计计算(转矩越大,传动件尺寸越大),此时应为最低转速下全功率运转。
但经常是,低转速段所用功率并不大。
所以可以考虑用比最低转速高一些的某一转速来设计计算传动件,该转速称为“计算转速”,用“nc”表示。
(一)主轴计算转速的确定
图5-37是通用机床主传动的功率和转矩特性曲线。
图5-37表明:
当主轴转速为nc时,主轴能够以全功率工作,并可传递最大转矩;
当主轴转速高于nc时,主轴均能够以全功率工作,所传递转矩随转速的升高而减小;
(为“恒功率”区)
当主轴转速低于nc时,主轴均能够传递最大转矩,所消耗功率随转速的降低而减少。
(为“恒转矩”区)
计算转速nc是人为的、根据实际情况而确定的转速。
表5-9是研究人员根据实际情况而给出的、确定一些机床主轴计算转速的经验公式。
(二)其它传动件计算转速的确定
某一传动件的计算转速是:
经过该传动件、并传递到主轴,能够实现主轴全功率运转的、该传动件的最低转速。