垃圾吊行车维修投标文件Word文档下载推荐.docx
《垃圾吊行车维修投标文件Word文档下载推荐.docx》由会员分享,可在线阅读,更多相关《垃圾吊行车维修投标文件Word文档下载推荐.docx(16页珍藏版)》请在冰豆网上搜索。
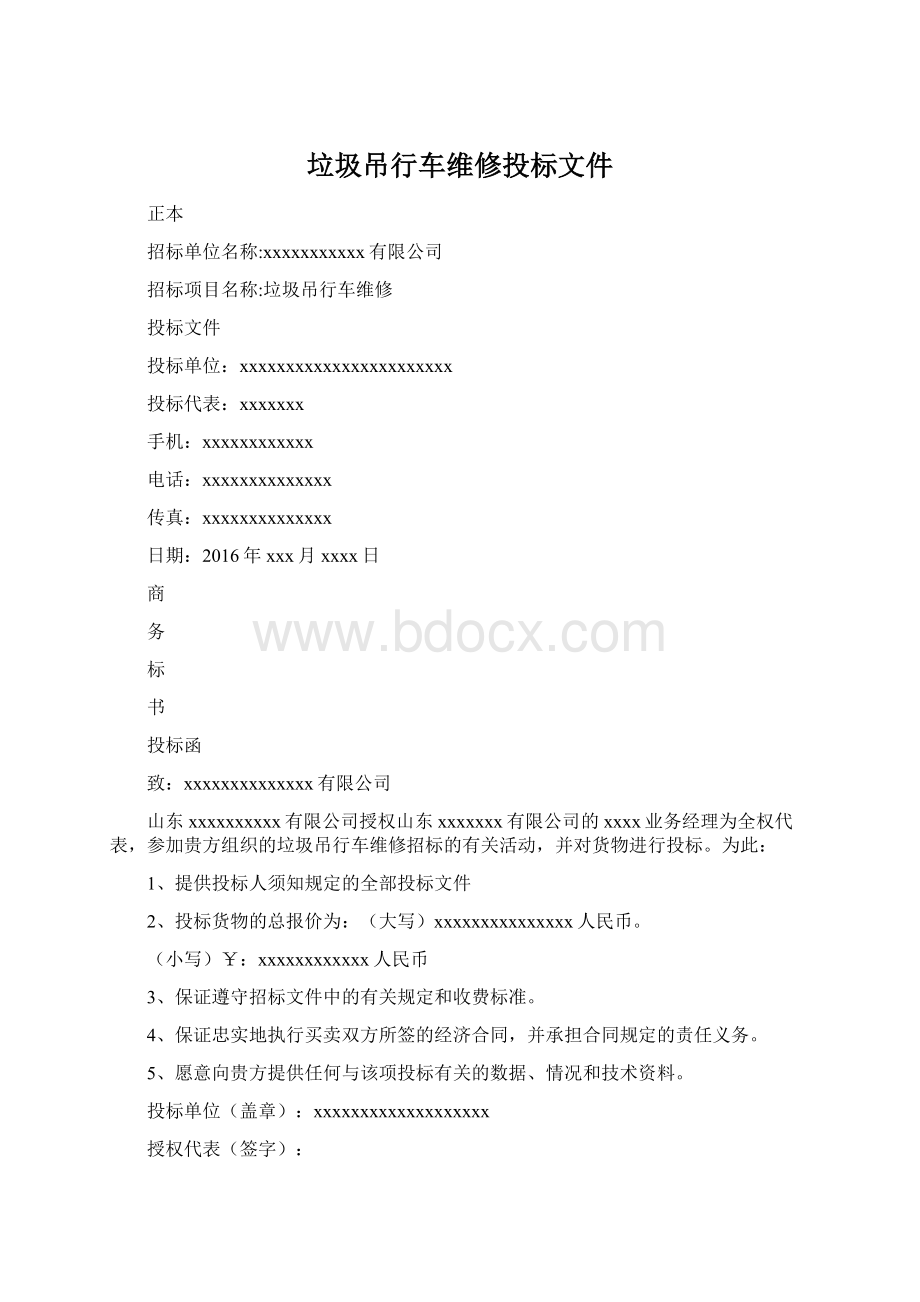
为垃圾吊行车维修项目,签署上述项目的投标文件,进行合同谈判,签署合同和处理与之有关的一切事务。
特此证明!
投标人(盖章):
山东xxxxxxxxxxxx公司
2016年xxxx月xxxx日
授权委托书
本授权委托书声明:
山东xxxxxxx有限公司的法人:
xxxx授权山东xxxxxxxxx有限公司的xxxxxxxxx为我公司代理人,以本公司的名义参加贵公司的投标活动,代理人在招投标、合同谈判过程中所签署的一切文件和处理与之有关的一切事务,我均予以承认。
代理人无转委权。
特此委托。
代理人:
xxxxx性别:
xxx职务:
授权单位(盖章):
山东xxxxxxxx公司
法定代表人(签字):
代理人(签字):
日期:
2016年xxx月xx日
投标价格汇总表
材料名称
规格型号
数量
单价(元)
金额(元)
备注
行车轮
缓冲器
刹车的更换
电缆更换
滑车轨道倒置
小车减速机加固
轨道铰调
道轨附件
山东xxxxxxxx有限公司
投标代表(签字):
技
术
一、工程概况
本方案是针对xxxxxxxxxx有限公司QZL10t液压抓斗起重机机械部分大修所制定,其公司共有2台QZL10t液压抓斗桥式起重机。
现桥抓大车、小车部件损坏现象。
近期桥抓大车行走过程中出现振动、啃轨等现象,严重影响桥抓安全运行。
为保证安全运行,需对其机械系统进行维修,消除设备存在的问题和缺陷,使起重机恢复正常工作状态。
具体项目如下:
设备类型
检查、检修项目
抓斗起重机
大车轨道检修调整附件添加
制动器检查发现不合格的给予更换
大车行车轮更换
电缆滑车轨道倒置
防撞装置更换
减速机加固
大车电缆更换
清理现场、验收
检修目的
规范检修行为,确保生产区域被QZL10t液压抓斗起重机机械系统维修后符合规定要求。
消除设备存在的缺陷,恢复起重机性能,提高设备感官质量和运行的可靠性及安全性。
稳定起重机正常的使用状态。
检修标准及依据
泰安中科环保电力有限公司QZL10t液压抓斗起重机图纸及相关技术文件
GB3811-2008《起重机设计规范》
GB6067-2010《起重机机械安全规程》
GB5905-2011《起重机试验规范和程序》
GB/T14407-93《通用桥式和门式起重机司机室技术条件》
GB50278-2010《起重机设备安装工程施工及验收规范》
工期要求
计划工程总工期天,计划开工时间年月日,计划竣工时间为年月日(根据甲方要求)。
工程质量、环境、职业健康安全目的和指标
分项工程交验合格率100%,争取达到优良。
(对原安装质量无法达到,同时又无法进行彻底改造的项目除外)
a.杜绝人员伤亡和重伤事故;
人身轻伤和轻微受伤事件控制在0次以内;
事故未遂事件控制在0次以内。
b.杜绝火灾、高空坠落、触电和交通事故;
c.不发生中毒事故
d.对员工健康有影响的岗位配备各种劳动防护用品配备率为100%
e.机械设备主要安全防护设施完好率为100%
二、劳动力及施工机具计划表
施工阶段
工种
分解阶段
检修阶段
验收阶段
管理人员
1
安全员
焊工
2
电工
机械检修工
4
合计
10
5
人员安排
序号
人员名单
项目负责人
xxx
3
电气焊工
xxxx
主要机具、测试仪表一览表
名称
规格
单位
电焊机
8-30KW
台
岛链
1t
手电钻
机械专用工具
套
各种测量仪器
6
千斤顶
16-50t
7
兆欧表
8
万用表
个
9
压线钳
端子液压工具
11
常用工具
若干
三、施工准备及计划
施工技术准备
档案管理制度”、“技术交底制度”、“安全操作制度”等一系列制度
施工计划
装复阶段:
在这一阶段有大量的检修、更换处理等工作,要求工作人员必须细心、严谨地完成。
同时,本阶段也是整个工程的关键,关系着整个工程的质量和工期,因此,本阶段必须要求工作人员对项目的分解工作保质、安全、按时完成。
施工作业重点、难点
四、设备存在缺陷
经现场实际勘察,发现起升、开闭以及大小车运行减速机漏油严重,声音异常
起升、开闭及大小车运行传动系统联轴器等磨损严重并违章焊接(此处不允许焊接,容易破坏其强度和刚度增加疲劳强度)
大小车轮啃轨,特别是小车运行啃轨严重及其容易造成脱轨的发生存在安全隐患
制动器闸架间隙超标松动,制动片、制动轮磨损超标、推动器漏油推力不足存在隐患
五、主要设备检修工艺
齿轮联轴器的修理(起升、开闭系统)
外齿套轮齿的磨损、破坏状态。
对于起升机构和运行机构的轮齿磨损量不超过前述报废标准。
声判断或用浸油法观察有无疲劳裂纹,如发现裂纹,应更换新件
卷筒拆装工艺
齿连接盘4分离,在右端卸下轴承座11的地脚螺栓,使卷筒组与小车分离,并将卷筒组向右拉出
掳子拉下轴承3和15,取下通盖16和套筒10
卷筒组的装配则以与拆卸相反的程序进行。
装配安装后进行试运转,将各部传动正常,钢丝绳紧固劳靠后,即可正式投产
起升开闭机构卷筒、钢丝绳、滑轮组检修
升机构卷筒、滑轮组等是否有裂纹或磨损严重的情况,钢丝绳是否有断丝、断股现象,必要时更换或处理
升机构卷筒两端钢丝绳末端压板螺栓紧固情况,卷筒与两端轮廓连接螺栓紧固情况,并逐一打紧
度连接螺栓紧固情况,并对松动的螺栓进行力矩拧紧。
六、轨道修理
施工方案:
根据该起重机大车运行轨道变形损坏情况,我方计划按以下方案进行修理矫正:
承轨梁;
承轨梁已无法移动,我方计划根据实测承轨梁的高度差和直线差,用钢垫板来调整轨道高度符合标准。
。
修理施工工艺及操作方法
利旧使用的压板螺栓,用煤油进行渗泡、清洗,对螺栓丝纹生锈的螺栓进行报废处理。
承轨梁,或是把轨道吊至地面,重新安装轨道。
承轨梁检查
根据业主提供的建筑检测数据,对承轨梁按如下内容进行复查。
承轨梁顶面标高。
承轨梁中心位置及两侧承轨梁中心距。
承轨梁与设计中心线的偏离。
安装轨道
在承轨梁上放线,弹出轨道中心线,再按轨道底宽,弹出轨道底边线,以导电侧的轨道线为基准,根据轨距,用钢卷尺、弹簧秤定出另一侧轨道中心线,同样弹出轨道中心线。
将调直的轨道吊装到承轨梁上,吊放在所需位置,把轨道底面用20mm左右厚度的木板垫起来,以便放置钢垫板。
到承轨梁上,。
钢垫板垫好后,将轨道下的木板抽出,然后用鱼尾板把轨道连成一体,其轨道接头间隙不应大于2mm左右,两侧轨道接头错开,且错开距离不得等于轮距,接头左、右、上三面偏移均应小于1mm,根据中心线大体找成一根直线,用轨道压轨器等把轨道初步固定,最后进行全面找正,符合要求后把螺栓全部紧固。
10m,△S=±
3mm;
s>
10m,△S=[3+(S-10)]mm,且最大值不超过±
15mm。
10mm;
轨道顶面相对于理论高度的极限偏差为±
两根轨道的高度差最大±
轨道中心与承轨梁中心之间的偏差不得超过承轨梁腹板厚度的一半。
轨道安装质量检测工序
采用水准仪检测法,一般只需设二个测站(仪器有盲区)。
如果轨道较长,还需设三个或更多个测站。
但是,只要掌握第一测站和第二测站的计算方法,其它测站的计算均可导出。
推导计算公式时,假定第一测站的第一测点A1(后视点)标高为零,其它各点标高均是相对A1点标高而言的。
1)第一测站计算公式:
h(A1、A2……)=H后1-H前(A1、A2……)
式中h(A1、A2……)——第一测站各点相对于A1点标高值;
H后1——第一测站后视值;
H前(A1、A2……)——第一测站各点前视值。
水准仪置于第二测站后,改变了仪器高程。
这样,第二测站各点的视值与第一测站A1点视值产生一个高程差值。
因此,第二测站的计算过程应采用高程差值修正法,将第二测站各点前视值变成第一测站各点前视值,方可按第一测站公式进行计算。
但是,此种计算方法比较复杂,故在这里不详细介绍。
为了使第二测站各点标高值的计算简单化,这里着重介绍后视点标高加入法。
此种方法,是将第二测站的后视值与第二测站的前视值之差的结果,再与第一测站最后一测点标高值之代数和,即是该点的标高值。
2)第二测站计算公式:
h(An、An-1……)=H后2-H前(An、An-1……)+n重
式中h(An、An-1……)——第二测站各点相对于A1点标高值;
H后2——第二测站后视值;
H前(An、An-1……)——第二测站各点前视值;
n重——第一测站最后一测点标高值(即重合点标高值)。
例1:
有一起重机,轨道长42m,检测其单根轨道标高及两轨道相对标高,并绘制其轨道曲线图。
如图1所示。
1)检测过程
①工具配备
水准仪一架,1m钢板尺一支;
②设置测站
在大车轨道A和B上,每隔
3m设一测点,共15点。
若新安装或要调整的轨道,最好每块压板位置设一侧点,这样精度高,并可根据曲线图选择最佳调整方案。
A轨道分别编号为A1、A2……A15;
B轨道为B1、B2……B15。
③第一测站的检测过程
置水准仪距A轨道第一测点A1最远清晰点处大车前承轨梁顶面上,整平,对中。
另一人置测尺于A1点轨道顶面上。
回转水准仪瞄准A1点测尺,调焦,对光,至看清测尺刻度值,并将A1点视值记录例1表一和表二的后视栏内,作为第一测站A轨和B轨的后视值。
然后,置尺人按顺序分别置于A2、A3……A11点上(A11点以后为仪器盲区),并将上述各视值记录例1表一前视栏内。
例1表一(A轨)表二(B轨)㎜
测站
测点
后视
前视
标高
一
站
A1
715
B1
720
-5
A2
B2
A3
710
B3
725
-10
A4
705
B4
713
A5
708
B5
A6
B6
A7
702
13
B7
A8
700
15
B8
A9
701
14
B9
A10
707
B10
A11
B11
二
A12
827
832
B12
A13
829
-7
B13
-6
A14
836
-14
B14
817
A15
837
-15
B15
再置尺于B轨的B1点上。
回转水准瞄准B1为测尺,调焦,对光,至看清测尺刻度值。
然后,按顺序置尺于B2、B3……B11点上,并将上述各视值记录例1表二的前视栏内。
此时,第一测站测量结束,收起水准仪。
④第二测站的检测过程如图2所示。
将起重机大车开回A1点处停下,再重新置水准仪距A11点(最后一测点)最近清晰点处大车前承轨梁顶面上,整平,对中。
另一人置测尺
于A11点上(A11点是第一测站最后一测点,即重合点)。
回转水准仪瞄准A11点测尺,并将其视值记录例1表一和表二的后视栏内,作为A轨和B轨第二测站的后视值。
然后,远离水准仪移动测尺,按顺序置尺于A12……A15上,并将其视值记录例1表一的前视栏内。
再置测尺于B轨的B12点上(B轨道不做重合点,B12点不再测量),并按顺序再置尺于B11……B15点上,将其视值记录例1表二前视栏内。
至测完全长为止,将水准仪收起。
2)标高值的计算
①第一测站的标高值的计算:
按公式一,将例1A轨各点视值代入
hA1=715-715=0;
hA2=715-720=-5;
hA3=715-710=5;
hA4=715-705=-10;
hA5=715-708=7;
hA6=715-710=5;
hA7=715-702=13;
hA8=715-700=15;
hA9=715-701=14;
hA10=715-707=8;
hA11=715-720=-5;
②第二测站标高值的计算
按公式二,将例1A轨各点视值代入
hA15=827-837+(-5)=-15;
hA14=827-836+(-5)=-14;
hA13=827-829+(-5)=-7;
hA12=827-832+(-5)=-10;
同理,按公式一和二将B轨各点视值代入,计算从略。
将其A轨和B轨各点标高值填入例1表一和表二的标高栏内。
3)轨道标高曲线图的绘制
如图3所示。
绘图时,以纵坐标OY轴表示轨道标高,比例必须选择1:
1;
以横坐标OX轴表示轨道长度,比例应根据测点的多少和轨道长度选取适当的长度。
图3大车轨道标高曲线图
根据计算出的标高值,在直角坐标系中,找出相应各点,将相邻两点依次用直线连接起来,即是被测轨道标高曲线图。
质量要求
检查项目
技术要求
轨道的实际中心线对安装基准线的水平位置偏差
≤5mm
起重机轨道的允许偏差;
当跨度S≤10m,跨度偏差
当跨度S>10m
±
3mm
{3+(S-10)}
但最大不超过15mm
轨道顶面对其设计位置的纵向倾斜度
1/1000
轨道顶面基准点的标高对于设计标高的允许偏差
10mm
同一截面内两平行轨道的标高相对差
≤10mm
两平行轨道的接头位置错开量
>车轮的基距
轨道接头高低差及侧向错位
≤1mm
轨道接头的间隙
≤2mm
方钢和工字钢轨道的横向倾斜度
≤轨道的1/100
各压紧螺栓无松动,同一跨端两条轨道上的车档与起重机缓冲器均应接触
安装验收交验方法
轨道安装完工自检合格后,向起重机使用单位提交检验报告,由起重机使用单位对轨道及滑线安装质量进行必要的审查和复查。
工程验收合格后施工单位向使用单位提交正式验收移交报告和有关资料。
验收后应有双方代表签字,认可验收及移交的全部技术文件。
抓斗拱度
经测量发现抓斗拱度下挠偏移零界值,建议对2台行车主梁进行校调。
七、制动器更换安装、检修要求
制动器拆除
开动起升电机将吊钩放置地面,然后固定,待起重机整体固定稳定后,拆开各部联轴器及传动器,然后分别打开制动器调整螺杆,拆卸固定螺栓将制动器移除。
制动器的安装及调整
制动轮节器9-弹簧座上,10-弹簧架刻度机
在保证闸瓦最小退距的情况下,推动器的工作行程越小越理想,因此需要调节其安装高度H1,其调整方法:
松开螺母6和8(见图),转动螺杆7,使H1安装尺寸符合表1的要求,调好后拧紧螺母6和8。
松开螺母4,夹住螺杆的尾部方头,转动螺母5,使方形弹簧座位于弹簧架刻线以内,调整后将螺母4和5拧紧退即可。
的退距调整
当制动瓦打开时,调整螺栓1,使两边退距基本保持一致。
使用和维修
要定期检查制动器的工作状况
检查时应着重以下各项:
1)制动器的构件无能运动是否正常,调整螺母是否紧固
2)推动器的构件是否正常,液压油是否足量。
有无漏油和渗油现象。
引入电线的地缘是否良好
3)尺寸H1不得小于表1所列之最小尺寸,如超出要求须立即调整,否则失去制动作用
4)制动瓦是否正常的靠在制定轮上,摩擦表面的状态是否完好,有无油腻脏物。
当制动衬垫的厚度达到表2中的数值时,则应更换制动衬垫。
5)制动轮的温度不应超过200℃
八、车轮更换调整方案
大车轮更换
键板原位置和需要移动的位置打上标记
割掉键板和定位板
及键板安好,并拧紧螺栓
轮跨和对角线等,并要求用手灵活转动车轮
有啃轨须调整
无啃轨现象,将键板和定位板点焊上,为了防止焊接变形,采用焊一段试车再焊的方法。
更换后对角线的调整:
根据对角线的测量进行分析,决定调整措施。
为了驱动传动轴的同心性,调整被动轮,不调整主动轮。
大、小车轮的调整:
依据主梁检测数据进行车轮调整解决啃道。
调整解决车轮的水平偏斜、跨度和对角线超差等几个方面问题,所以应检查分析。
特别要注意的是,因为主动车轮与传动机构相连接,所以调整主动轮容易造成传动机构不同心,所以除必须外,以调整被动轮为好。
调整车轮前,首先用千斤顶将端梁顶起,使车轮悬空,然后松开紧固螺栓,再调整。
加垫即可。
键板铲开,在键板与端梁弯板之间加垫调整(见图4)。
调整水平偏斜,应在垂直键板处加垫,调整垂直偏斜,应在水平键板处加垫。
1车轮2端梁弯板3水平键板4角形轴承架5垂直键板6紧固螺栓
四块键板全部铲平,调整好后再把定位键板焊接在端梁弯板上
调整为锥顶向外侧
九、工程质量保证措施
施工准备过程中的质量控制
技术复核制度、样板引路制度、施工挂牌制度、过程三检制度、质量否决制度、成品保护制度
施工过程中质量控制
质量控制程序
定期召开现场碰头会由项目技术负责人对当天质量工作情况,做出分析和总结,找出问题并提出解决问题的方法,以工作质量保证工程质量
度,保证分部分项工程的施工质量
十、安全体系
1.我公司严格贯彻执行党和国家、电力行业及项目所在地各级人民政府关于安全生产的一系列方针、政策、法规、条例和规定,必须采取一切必要措施和手段强化安全管理,提高安全水平,确定严格的安全工作秩序以保证人员在工作中的安全与健康,并确保本项目的顺利实施。
2.我公司必须贯彻执行“安全第一、预防为主”的方针,严格执行中华人民共和国电力行业标准《电业安全工作规程(火力发电厂部分)》和业主有关安全规定及各自行业安全工作规程。
3.项目经理是我公司在该项目的第一安全责任人,必须亲自抓安全;
建立严密的安全监察网络和有效的安全保障体系;
必须配备专职或兼职安检人员。
4.必须服从业主的安全管理,因我方的原因给业主方、己方或第三方造成人身伤害或死亡,均由承包方按国家有关规定承担相应责任;
因我方的原因给业主方、己方或第三方造成设备事故或经济损失,均由我方负责并赔偿造成的一切经济损失。
5.我方必须严格执行业主关于文明工作方面的管理文件、规定,由此而发生的一切费用由承包商自理。
6.我方在现场遵守所有现行的有关安全、文明工作的规章制度。
(a)全面负责在本项目中工作的人员的安全,并使工作现场保持良好的秩序,以避免发生人身事故,保证建构筑物和设备的安全。
(b)为了保护设备或为了公众及其他人员的安全及方便,在业主或任何依法建立的主管机关所要求的时间和地点、我方应以其自己的费用提供并维修所有检修维护工作所需的临时照明、护栏、警告标志等。
(c)采取一切合理措施,保护工作现场周围的环境,避免污染、噪音或由于其工作方法的不当造成的对公共人员和财产等的危害或干扰。
安全网络图
7.针对本项目,由以上专业人员组成安全体系,对各专业安全由专职负责制,安全专工考核建立完整的工作安全档案。
8.投入每项工作前,先由专业安全员对工作危险点分析,针对方案和意外发生情况,做好一切准备,方可工作。
安全总监责任,周安全开会提出本周主要工作,主要项目安全要求,由各专业安全员讨论分析工作中危险点。
排除办法实施策略。
然后由安全总监根据讨论汇总,形成文字安全卡和工作量单一并。
发放各专业人员,各专业人员,各专业人员必须签字执行。
周末由安全总监对于安全卡执行情况进行检察是否和工作中安全实施相符。
再组织各专业人员开总结会,对于专业实行好的垒计褒奖。
反之提出批评,违反安全规定的实行惩罚。
9.安全专工责任,在工作中时检查安全卡和工作环节是否相符,作出第一手资料,对各专业严格考核,对于不正确的工作方式,方法进行纠正,必要时停工讨论,周末总结安全情况,对每专业安全情况仔细剖析。
10.起重专业责任,对起重机各安全机构灵敏灵活度负责,根据各部位运转情况及安全情况建档分析,起重机阻滞实施修理,巡察时为主要安全责任人。
11.电气专业责任:
对电气运行情况,及安全措施必须提前提交各专业,把运行和危险点出现控制在零范围。
电气专业责任,进行工作前,对于用电方面进行检查,先知其它人员,对于刀开关断电后负责挂“有人工作,禁止合闸”醒目标志。
在用电时做好一切安全措施,使各专业人员工作中必须安全,杜绝有触电或漏电现象发生。
12.电气焊专业责任,工作前对周围环境察看分析,工作中严禁有火花引起火灾或烧烤周围设备,对自己工器具检查,防止工器具发生意外。
13.以上各专业工作前和工作时,现场负责人必须严密配合,监督各安全情况,对工作时出现危险点指正处理出现时必须记录在册。
山东xxxxxxxxxxxxxxxxxxxx公司
2016年xx月xx日