基于虚拟仪器滚动轴承故障分析系统开发学位论文Word文件下载.docx
《基于虚拟仪器滚动轴承故障分析系统开发学位论文Word文件下载.docx》由会员分享,可在线阅读,更多相关《基于虚拟仪器滚动轴承故障分析系统开发学位论文Word文件下载.docx(38页珍藏版)》请在冰豆网上搜索。
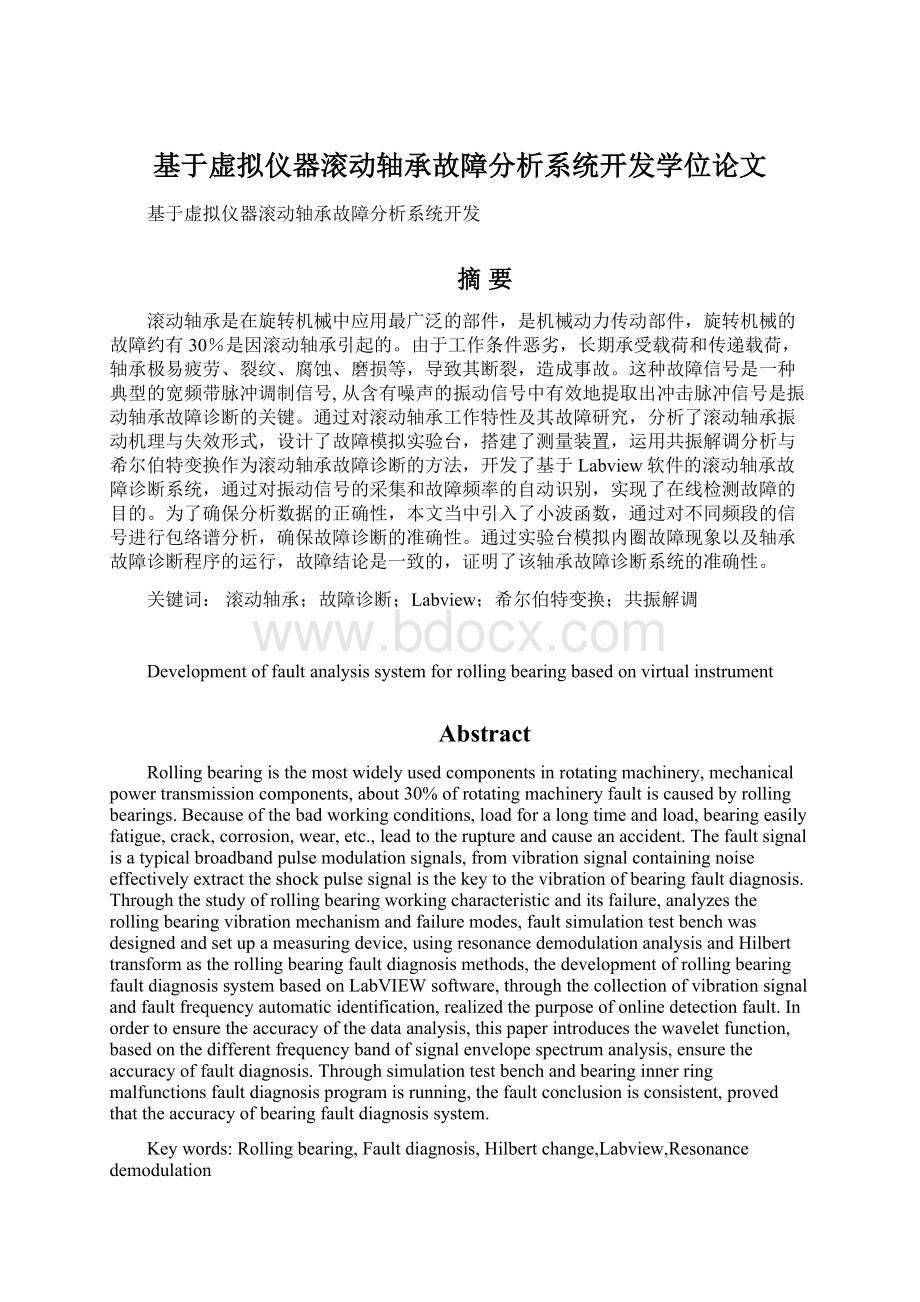
AbstractII
第1章绪论1
1.1课题研究的目的与意义1
1.2国内外研究现状2
1.3研究的主要内容4
第2章滚动轴承及故障的基本理论5
2.1轴承的分类和基本结构5
2.2滚动轴承的损伤分析6
2.3.1滚动轴承故障类型9
2.3.2滚动轴承的固有振动频率9
2.3.3滚动轴承特征频率10
2.4轴承振动信号处理11
2.4.1低通滤波包络解调法12
2.4.2希尔伯特变换及包络谱算法12
2.5本章小结14
第3章滚动轴承故障模拟试验台15
3.1滚动轴承故障模拟试验台方案15
3.2滚动轴承试验台结构设计15
3.3控制系统和数据采集系统设计17
3.3.1控制系统17
3.3.2数据采集系统18
3.4本章小结20
第4章轴承故障诊断软件设计21
4.1虚拟仪器概述21
4.2Labview的含义22
4.3基于虚拟仪器轴承故障诊断程序开发22
4.4本章小结28
第5章轴承故障诊断实验29
5.1轴承实验台参数设置29
5.2轴承故障模拟与分析29
5.2本章小结32
结论33
致谢34
参考文献35
附录A36
第1章绪论
1.1课题研究的目的与意义
轴承一直是各种机械中应用最广泛的通用部件,其运行状态直接影响整台机器的性能、寿命、功能和效率,机械设备诊断中的重点是旋转机械的故障检测,而滚动轴承是旋转机械的重要组成部件,许多的故障都是滚动轴承的故障引起的。
滚动轴承比较容易受损,并且由于滚动轴承的使用环境不同导致使用寿命也有很大的差别。
据统计旋转机械的故障有30%是由轴承引起的,由于工作条件恶劣,长期承受载荷和传递载荷,轴承极易疲劳、裂纹、腐蚀、磨损等,导致其断裂,造成事故。
滚动轴承的寿命离散性很大,对其进行定期维修是不可取的,因此,滚动轴承故障诊断工作十分重要。
滚动轴承能否正常工作对机器的工作状况有很大的影响。
在精密机械中对轴承的要求更高,轴承滚道上极微小的故障都是不能容忍的,在故障发生之前通过一些方法对其监控,把故障在初期消除做到预知维护,不仅提高了生产效率而且大大的节省了维修费用,所以滚动轴承的故障检测有着非常重要的意义。
一旦由于轴承的疲劳损伤、磨损、腐蚀及操作不当而产生的故障,就会导致轻则影响机械设备的正常运行,重则带来人民生命和财产的巨大损失。
因此随着工业社会的高速发展和进步,及时的发现并排除轴承故障责任重大。
在过去,轴承作为关键部件往往需要定时维修以免发生严重事故,但实际使用过程中,一些超过使用寿命但完好的轴承被报废,而有些未达到设计寿命的轴承却已经出现故障,这样势必造成浪费或严重的机械故障。
因此,对于具有重要用途的轴承仅是定时维修时是十分不科学的,开展轴承的状态监测和故障诊断,改变传统的定期为预知维修,不但可以防止机械系统的性能下降,减少事故发生,而且还能避免浪费可用部件,对于最大限度地发挥轴承的工作能力,具有重要的意义。
开展轴承故障诊断研究除了具有实际意义之外,还具有深刻的理论意义。
通过实施故障诊断技术,带动与故障诊断有关的一系列相关理论,如信号采集、信号分析、模式识别等相关科学的发展,在实际中检验理论,寻找最佳故障诊断方法,进一步完善机械设备故障诊断学,同时也为下一代产品的优化设计、正确制造提供反馈信息及理论依据。
在经济方面,正确地对各类轴承的异常或故障进行分析以便确定最佳维修决策,发挥大型机械系统最大的运行能力和使用效率,可明显提高运营经济效益。
机械设备诊断在工业高度自动化方面具有重要意义,由于机械设备越来越精密,各个部分之间关系越来越紧密,工作强度不断增大,任何一处危险的故障就会产生一系列的连锁反应,导致设备损坏,与此同时影响其他设备的工作进度,整个系统处于瘫痪中,造成巨大的经济损失,甚至危及人身安全,后果非常严重。
综上所述,旋转机械的安全、正常运转可以避免重大的经济损失、严重事故和人员伤亡。
滚动轴承是选装机械的重要组成部分。
本文主要针对滚动轴承机械故障进行试验台模拟实验及理论分析,获取相关故障的振动信号的产生机理及故障特征提取和诊断方法,探讨滚动轴承故障的分析方法和识别方法,这对于轴承制造行业和其他机械行业非常重要,在经济和社会方面都有一定的意义。
滚动轴承最大的特点就是寿命离散性很大,因此对其进行定时维修是不可取的,要进行工况监控和故障诊断。
随着计算机和相关技术的发展,笔者利用虚拟仪器技术开发滚动轴承的测试诊断系统,以实现快速可靠检测。
成虚拟仪器的实质是,利用计算机显示器的显示功能来模拟传统仪器的控制面板,以多种形式表达输出检测结果;
利用计算机强大的软件功能实现信号数据的运算、分析和处理;
利用I/O接口设备完成信号的采集测量与调理,从而完成各种测试功能的一种计算机测试系统。
使用者用鼠标或键盘操作虚拟面板,就如同使仪器一样。
1.2国内外研究现状
目前,轴承故障诊断技术仍以时频分析为主,如时频分析中常用的均方根值(RMS)、峰值和峭度值等、频域基于周期信号的倒谱分析及高频响应技术(HFRT)等,这些轴承诊断都受到多方面的限制,如诊断面不能大于6.25mm²
,这边造成了很多状态检测的漏检从而导致发生严重的事故。
在诊断与生产的协调方面,当监测到一个致命故障时,往往被迫停机,也带来了许多不方便和生成效率低下的问题,因此,轴承故障诊断更重要的是要着眼于预测寿命和故障发展状况,以便提前做好生产维修安排和计划。
只有具备可靠的预兆检测功能,轴承维修和更换才能做到有的放矢。
滚动轴承的状态检测与故障诊断开始于20世纪60年代。
在其后20多年的时间里,随着科学技术的不断发展,各种方法和技巧不断产生、发展和完善,使应用领域不断扩大。
一般认为,轴承工况检测与故障诊断技术的发展可分为四个阶段。
第一阶段:
利用通过的频谱分析仪诊断轴承故障。
20世纪60年代中期,由于快速傅里叶变换技术的出现和发展,使振动信号的频谱分析技术得到了很大的发展。
人们根据故障的滚动轴承元件所产生的振动信号特征频率的计算和采用频谱分析仪实际分析得到的结果来判断轴承的故障。
第二阶段:
利用冲击脉冲技术诊断轴承故障。
20世纪60年代末,瑞典仪器公司根据各个钢制轴承元件表面损伤后在受载情况下接触时要产生冲击引起高频压缩波的现象开发了一种称为冲击脉冲的仪器来检测轴承故障,并且不需要进行频谱分析,所以他一经发明便很快被美国、英国等工业发达国家所采用的。
早期的脉冲冲击只用来检测轴承的局部损伤类故障,后来,随着这一技术的不断发展和完善,世界上其他一些国家的公司和厂家相继开发出各种更新代换产品,这些仪器不但用于检测轴承局部损伤类故障,而且用来检测轴承的润滑情况甚至油膜的厚度等。
第三个阶段:
利用共振解调技术诊断轴承故障,1974年,美国波音公司的DR.Harting发明了一项叫做“共振解调分析系统”的专利技术,这就是中国现在统称的“共振解调技术”的雏形。
采用共振解调技术由于放大(谐振)和分离(带通滤波)了故障特征信号,极大地提高了信噪比,所以比较容易地诊断出故障来。
第四阶段:
开发以微机为中心的滚动轴承工况监视与故障诊断系统。
20世纪80年代以后,随着微机技术同飞猛进的发展,开发以微机为中心的波动轴承工况监视与故障诊断系统引起了国外研究者的重视。
由于设备故障诊断理论的发展和新的信号测试与处理方法的出现,人们还使用了多种其他有效的方法和技巧来诊断滚动轴承的故障。
从20世纪60年代开始,经过世界各国研究人员近40年的努力,滚动轴承的诊断技术已走向了实际的应用阶段。
目前,美、英、日、俄等工业发达的国家相继开发了以微机为主的滚动轴承状态监测与诊断系统、如Bently公司的REBAM系统、俄罗斯的VAST公司开发的滚动轴承自动诊断系统DREAM。
国内的起步尽管较晚,但是在轴承诊断技术的研究和开发上也取得了令人瞩目的成绩,如航空航天部608研究所唐德尧等人开发的JK8342齿轮轴承故障分析仪和铁路货车的JK86411滚动轴承自动试验诊断系统,以及南京航空航天大学诊断所的赵淳生等人开发的MDS系列轴承故障诊断系统等。
小波变换是一种有利的工具,在轴承诊断领域中应用最多的还是其降噪功能,Martin已证明了使用傅里叶变换诊断轴承故障会受限制,Hitherto时频分析是最普遍的非静态振动信号的分析方法。
小波变换(WT)可以弥补傅里叶变换的不足。
国内多数研究侧重于对故障信息提取算法的研究,包括基于小波变换、遗传算法与神经网络算法的故障信息识别方法等,这些研究虽能够提高故障诊断的准确性,但是分析过程复杂,计算量较大,难以实现在线诊断[1]。
而国外因起步较早,无论从硬件还是软件上,故障诊断技术都发展较快。
但是基于Labview软件的故障诊断研究,无论国内还是国外只是处于起步阶段,目前还只是用Labview软件实现简单的数据采集、显示、滤波和频谱分析等。
因此,研究基于虚拟仪器滚动轴承故障分析技术与方法是非常有意义的。
1.3研究的主要内容
该课题主要是开发基于虚拟仪器的轴承故障检测分析系统。
所以对于轴承的故障特征对于我们完成该系统是非常重要的,因为使轴承失效的原因很多,比如点蚀、化学腐蚀、干摩擦等等,都会引起轴承的产生故障,所以很难确认是什么原因导致轴承产生故障。
本文根据轴承的故障特征,主要要完成的任务有下面几个方面
1.搭建滚动轴承故障模拟实验台,组建振动信号测量硬件系统;
2.研究多故障信息提取技术。
用Labview8.5应用程序开发多故障信息提取程序模块,该模块能够同时对振动信号的时域特征参数、幅值域特征参数、频域特征参数等进行计算,并将计算结果实时显示出来;
3.开发时频分析系统。
该系统能将轴承振动信号的数据进行保存和回放,也可将振动信号波形、相关曲线、幅频谱、功率谱等曲线实时显示出来,便于用户分析、观测,和诊断;
4.开发滚动轴承故障信号仿真与分析程序。
该程序能够实现Labview与Matlab软件交互式访问功能,充分利用二者各自的编程优势,实现故障信号的仿真与分析。
第2章滚动轴承及故障的基本理论
2.1轴承的分类和基本结构
1.滑动轴承的分类和基本结构
滑动轴承根据摩擦状态和润滑方式可以分为:
(1)下摩擦轴承,又分为无润滑轴承和固体润滑轴承,采用固体润滑,为固体摩擦方式。
(2)含油轴承,浸渍润滑方式,固体、边界、流体混合摩擦。
(3)不完全油膜轴承,摩擦方式同
(2),但润滑采用了滴油、油绳、油垫方式。
(4)动压轴承,为流体摩擦,备有循环润滑系统。
(5)静压轴承,同(4)。
滑动轴承一般由轴承座、轴瓦和润滑系统组成,工作时轴颈在轴承中旋转带动润滑油形成动压油膜,考油膜压力与外载荷相抵来实现支撑并保证轴颈灵活转动。
动压油膜不仅是载荷的传递体,而且也是避免轴颈有轴承直接接触的中介物质。
油压模的性质和工作状态将严重影响润滑轴承的工作品质。
由于油压模的形成和性质不仅与轴承结构本身有关,还与工作条件、供油系统及环境因素等相关,这一点决定了滑动轴承故障的特殊性和复杂性[1]。
2.滚动轴承的分类
(1)按承受载荷的方向分
向心轴承:
主要承受径向载荷,公称接触角0°
<α<45°
;
推力轴承:
主要承受轴向载荷,公称接触角45°
<α<90°
。
(2)按滚动体的形状分
按滚动题的形状可分为球轴承和滚子轴承,滚子轴承又分为圆柱滚子轴承、针滚子轴承、圆锥滚子轴承和调心滚子轴承
(3)按是否具有调心性分
调心轴承:
滚道为球面,能适应两滚道轴心线间的角位移;
非调心轴承:
能阻抗两滚道轴心线间的角位移。
(4)按滚动体的列数分
按滚动体的列数可分为单列、双列、多列轴承。
(5)按滚动体是否分离分
按滚动体是否分离可分为可分离轴承和不可分离轴承。
(6)按轴承公称外径D的大小分
微型轴承:
D≤26mm;
小型轴承:
28mm≤D≤55mm;
中、小型轴承:
60mm≤D≤115mm;
中、大型轴承:
120mm≤D≤190mm;
大型轴承:
220≤D≤430mm;
特大型轴承:
D≥440mm。
3.滚动轴承的基本结构
滚动轴承,在支承负荷和彼此相对运动的零件间做滚动运动的轴承,一般是有内圈、外圈、滚动体和保持架四部分组成,如下图2-1所示
图2-1深沟球轴承
(1)内圈。
通常装配在轴上,在多数情况下,内圈是与轴一起旋转的。
内圈外表面上有供钢球和滚子的沟槽,称内沟或内滚道。
(2)外圈。
通常装配在轴承座或壳体上,起支承钢球和滚子的作用。
有些轴承是外圈旋转,内圈固定起支承作用。
外圈内表面上也有供钢球或滚子滚动的和沟槽,称为外沟或外滚道。
(3)滚动体。
在内圈和外圈的滚道之间滚动,他的大小和数量决定着轴承的承载能力。
(4)保持架。
把轴承中的一组滚动体均等地相互隔开,以免互相碰撞,并使每个滚动体均匀地并且轮流地承受相等的负荷。
在推力轴承中与轴紧配的套圈叫紧圈,与轴承座或机械壳体相配的叫活圈。
此外,根据机械部件对轴承性能要求的不同,轴承的结构有所差异。
有的轴承无内圈或无外圈或内、外圈都没有,有的轴承中海油铆钉、防尘盖、密封盖以及安装调整时用的止动垫圈、紧定套和螺母等零件。
2.2滚动轴承的损伤分析
滚动轴承虽然不如滑动轴承在一般机械中的广泛应用,但是由于本身具备的一些独特的优点,使得它在高速、高精度、重载、结构上要求剖分、径向尺寸受限等场合下忍占有重要的地位。
再实际工作中,由于各方面的的原因,滑动轴承却不能达到其应有的寿命,过早地出现了损伤,从而影响了正常生产,人们所说的的轴承失效是指在负荷超标或工作条件恶劣的情况下,轴承未能达到设计的寿命的提前失效,滑动轴承的失效形式机理错综复杂,下面就对其主要失效形式和机理进行简要的分析。
1.擦伤
如果缺油,轴承与轴颈表面的金属就会直接接触,导致工作表面产生擦痕而出现损伤。
如果不添加润滑油,残油可能被完全挤出,轴与轴承的干摩擦是温度剧增,使轴承材料变软、熔化、产生黏连迁移,导致滑动轴承严重损坏。
产生擦伤的主要原因是过度超负荷使用、局部才和集中、油道不畅或堵塞、过滤器失效,以及由于油温过高、间隙配合过大、油稀释等原因造成油膜难以形成;
或者是润焕油中的杂质嵌入减摩层中形成应质点,经过一定时间后,其高度打与轴承间隙时,也会在工作表面磨出沟来。
此外,还有一种微振磨损。
当轴承不旋转而仅受到振动时,由于滚动体和滚道接触面有微小的反复的滑动而产生了磨损,在滚道表面上形成振纹状的磨痕,轴承运行时将增加磨损。
2.磨损
磨损是一种表面损伤等现象,也是滑动轴承工作时不可避免的一种损伤,按照磨损的机理的不同,磨损失效主要包括黏附磨损和磨粒磨损。
黏附磨损产生于边界润滑条件下,油膜破坏或是异物嵌入轴承金属表面,导致轴和轴承的金属表面在局部直接接触,摩擦发热使油温升高,黏度降低,有时发热导致表面金属流动产生黏连,严重时使机械顷刻间无法运转。
如果周与轴承出现瞬间干摩擦,或润滑油中的杂质进入轴与轴承之间,常常会发生魔粒磨损,润滑不良及磨屑得不到有效的滤清,滑动轴承磨损及加剧,影响正常的工作,导致提前失效。
3.疲劳
滑动轴承往往工作在交变载荷下,若应力超过了材料的疲劳强度,经过一的应力循环,轴承的表面便会产生裂纹,且裂纹会沿着最大应力方向由表面、向内部扩展。
除此之外,油膜层的破裂使轴承发生咬黏,由此造成的伤痕亦可产生新的疲劳。
一般情况下,疲劳裂纹由表面向里扩展至结合面附近,当这些裂纹沿结合面彼此相遇时,就会引起轴承合金材料和镀层的脱落,轴承表面出现不规则的伤痕,即出现疲劳损伤,最后导致轴承失效。
4.腐蚀
使用没有防腐涂层的金属表面往往会发生腐蚀,这是因为润滑油中残留有少量的水或者是其他酸性物质,经长期高温工作后,氧化生成了有机酸,从而轴承合金造成了腐蚀,产生凹坑和溃烂,减少了轴承的支撑面积,并妨碍油膜的形成。
5.汽蚀
重载、高速运转的情况下,滑动轴承工作表面与轴颈表面间的油膜压力低于润滑油在该温度的饱和蒸汽压力以下时,会形成小的气泡,若随后润滑油压力升高或气泡跑到压力较高的区域使气泡消失,气泡周围的润滑油迅速地补充到原气泡出,使轴承表面受到强烈冲击,该压力波的作用面积很小但量值很高,会引起表面塑性变形而是工作应力升高,最后导致轴承表面局部剥落,这种现象称为汽蚀。
6.油膜涡动
利用动压油膜工作的滑动轴承虽有许多优点,但同时也带来了由于动力失效而产生的油膜涡动和油膜振筋问题,它是造成回转机械亚同步振动的重要因素之一。
亚同步振动又称自激振动,其振动频率低于转子的回转频率,由于这种差异而在转子和定子中产生交变应力,并且这种振动常常在某个转速下突然发生,因而对回转机械具有极大的危害性。
7.烧瓦
当轴承长时间缺乏润滑、装配间隙过大或过小、局部偏大或偏小、超载运转,以及轴承间存在着杂质或异物,使轴承间压力油膜不易形成,破坏了油膜的承载能力,这些都将使轴承产生“过热”,引起轴瓦材料软化,甚至发生局部熔化黏结在一起,最后导致烧瓦。
这是最为严重的损伤之一,往往会立即造成事故。
8.过热
对于一个正常的滑动轴承来说,其油温或轴表面温度应该有一定的分布规律,而当轴承的任何环节发生变化时,都可能引起油温或轴承温度的变化,如承载能力不足、供油不充分、油脂劣化、涡动剧烈、超载运行等,因此油温不仅滑动轴承工作状态的综合指标,也是滑动轴承故障消息的一个重要载体。
2.3滚动轴承的故障特征
滚动轴承的损伤失效形式很多,其基本形式主要介绍如下
1.磨损失效。
磨损失效是轴承滚道、滚动体、保持架、孔座或安装轴承的轴颈,由于机械原因引起的表面磨损。
磨料的存在是产生轴承磨损的基本原因。
2.疲劳失效。
表现为滚动体或滚道表面剥落或脱落,主要是由于疲劳应力造成的。
3.腐蚀失效。
轴承零件表面的腐蚀是有下面三种原因造成的:
润滑油、水分或湿气的化学腐蚀;
轴承表面间有较大的电流通过造成的电腐蚀;
轴承套圈在座孔中或轴颈上产生微小相对运动而造成的微振动。
4.断裂失效。
轴承零件的破断或裂纹主要由磨削、热处理、运行载荷过大、转速过高、润滑不良、装配不善、产生过大的热应力而引起的。
5.压痕失效。
压痕是在滚道或滚动体表面上产生局部变形而出现的凹坑,他既可能是由于过载、撞击,也可能是由于装配敲击或异物落入滚道而形成。
6.胶合失效。
胶合指滚道和滚动体表面由于受热而局部融合在一起的现象。
常见出现在高速、高温、重载、润滑不良、启动加速度过大等情况。
在工作的过程中,滚动轴承造成的振动通常分为两类:
其一为与轴承的弹性有关的振动;
其二是与轴承滚动表面的状况(波纹、伤痕)有关的振动。
前者不论