火电机组运行优化指导意见Word格式.docx
《火电机组运行优化指导意见Word格式.docx》由会员分享,可在线阅读,更多相关《火电机组运行优化指导意见Word格式.docx(17页珍藏版)》请在冰豆网上搜索。
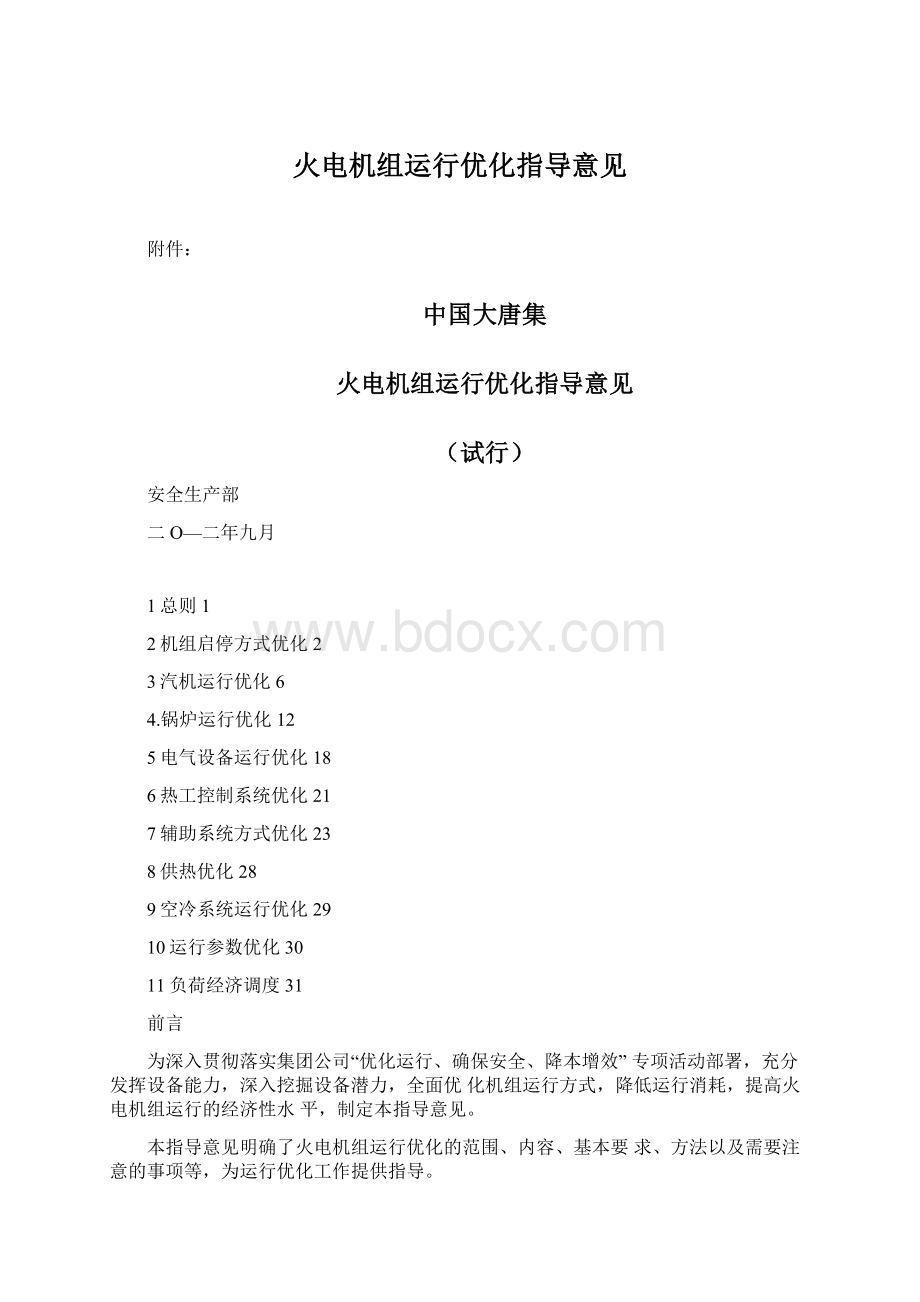
主要起草单位:
大唐国际发电股份有限公司。
主要起草人:
大唐国际祝宪、郑博生、谢德勇、黄俊峰、黄治军、王军、刘彦鹏、刘冬、郝晨亮,河北发电公司姚利平,河南分公司董志勇、艾秋菊、马清贵,贵州发电公司李满辉、杜俊鸿,湖南分公司陆元湖,吉林发电公司李业盛。
本指导意见由中国大唐集团公司安全生产部负责解释。
1总则
1.1运行优化是根据机组主、辅机设备运行状况,在与设计值、行业标准值同类型机组标杆值对标的基础上,通过开展性能试验及综合分析,建立一整套科学、合理的运行调整方法和控制程序,使机组始终保持最安全、最经济的运行方式和最佳的参数控制,降低机组运行消耗。
1.2运行优化必须坚持“保人身、保电网、保设备”基本原则,任何系统、设备、操作的优化方案均不准违反“两措”的要求。
1.3运行优化要以机组设计值和行业标准值为基础,对每台机组及公用系统开展对标分析、性能试验,全面分析查找影响机组节能降耗的问题;
通过加强操作调整、设备治理和改造,实现机组运行指标达到设计值的目标。
1.4运行优化的主要内容包括机组启停过程优化,汽轮机、锅炉、电气、除尘脱硫、燃料输送、热工控制、辅助系统、供热、空冷系统、运行参数、负荷经济调度优化等。
各火电企业要结合设备、系统和运行人员积累的宝贵经济调整经验,不斷完善优化方案,有针对性地开展运行优化工作,杜绝生搬硬套。
1.5运行优化要以机组耗差分析系统为参考依据,以绩效考核为保障,深入开展指标竞赛活动,充分调动全体员工的积极性、主动性和创造性,强化全员的节能降耗意识,实现机组参数压红线运行。
1.6运行优化不是简单的运行方式和参数的调整,而是一个系统的管理模式。
通过动态对标,以运行数据分析、优化运行体系为抓手,理清工作思路、实现闭环管理,使运行优化工作不斷持续改进。
1.7运行优化工作要定期开展统计分析、经验总结工作,通过经验积累,不斷完善运行规程、标准操作票库、定期工作标准等规章制度,实现机组运行优化的系统化、制度化、常态化。
1.8运行优化要以机组主要能耗指标及主要小指标的改善为标准,在同工况、同条件下进行同比(环比)分析,以此检验运行优化的效果。
2机组启停方式优化
2.1基本要求
2.1.1各火电企业应结合厂家说明书和运行经验,对机组启停的每个环节进行认真分析,摸清机组的特性,优化机组经济启停步骤,确定最佳的启动、停机时间和操作方法,完善运行规程和操作票。
2.1.2运行人员必须熟练掌握机组启停的重要操作步骤,熟知各专业间相互配合的关键点,有效控制启停节奏,精准把握启停时机。
2.2机组启动过程优化
2.2.1严格执行机组启动前系统检查标准操作票,及时发现、处理影响机组启动的缺陷,避免延长机组启动时间。
2.2.2机组准备启动前,应对机组设备状态、运行方式进行全面核查(包括工作票、缺陷、报警信息、阀门状态等),为机组顺利启动创造条件。
2.2.3启动过程中,应根据机组实际情况选择采用邻炉加热、邻炉送粉、炉底加热、汽缸预暖、小油枪或等离子点火、汽泵全程运行、单侧风机启动等节能技术,同时根据参数变化,适时投运设备,优化启动过程。
2.2.4汽轮机修后启动试验,有邻机汽源的,应首选邻机汽源暖机和冲动,以节省锅炉启动消耗。
2.2.5机组启动试验应制定运行操作方案,反复论证各项试验的先后次序,复杂操作应提前在仿真机上演练。
2.2.6机组启动时严格执行到岗到位制度,现场留足技术过硬的检修人员,以便快速处理缺陷,缩短启动时间。
2.3机组停机过程优化
2.3.1汽机设备优化
2.3.1.1停机过程中,在不违反运行规程的前提下,应尽早停运循环水泵、凝结水泵、电动给水泵等高耗能设备(对于采用开式循环冷却系统的机组,停机1小时确认循环水系统无用户后,应停运循环水泵)。
2.3.1.2对采用冷却塔的循环冷却系统,根据邻机负荷情况,能够环并循环水系统时,可停止部分循环水泵运行。
2.3.1.3闭式水系统在单元机组之间设计有公用管路能实现互联的,当一台机组停运时,可通过公用管路由邻机向停运机组供水。
若不能满足要求,应对机组系统进行改造,实现邻机供水。
2.3.2锅炉设备优化
2.3.2.1锅炉熄火后,当锅炉相关参数达到本企业规程规定值时,应尽早停运风机运行。
送、引、一次风机停运1小时后,根据风机轴承温度变化,尽早安排停运润滑、液庄油泵。
2.3.2.2滑停烧空煤仓工作应提前布置,正确计算燃煤耗用量,不许采用输煤系统长时间运行连续输煤的方法烧空仓。
2.3.2.3滑停控制好汽温、汽压下降速度,尽量减少使用关小给水调节门提高减温水流量的方法,以降低给水泵能耗。
2.3.2.3锅炉负荷低于稳燃负荷时,应尽快缩短停运时间,减少燃油消耗。
2.4启停机典型优化方案
2.4.1采用全程汽泵给水方式
2.4.1.1机组冷态启动前,使用汽泵前置泵给锅炉上水。
2.4.1.2锅炉点火升庄阶段,应按照庄力变化情况,在凝汽器达到一定真空后,用辅助蒸汽汽源冲转一台汽动给水泵,满足锅炉启动需求。
2.4.1.3优化汽动给水泵各路汽源的使用顺序,优先使用低品质汽源。
2.4.2机组少油或无油启动
2.4.2.1等离子点火方式
采用等离子点火系统启动时,为保证点火初期煤粉能够着火稳定,必须维持一定的煤粉浓度。
在点火初期不宜投入过多燃料,防止造成机组升温升压速度过快;
对于超临界、超超临界直流炉防止出现加剧受热面氧化皮剥落现象。
对于前后对冲燃烧的旋流燃烧器和中速磨煤机,可以通过在点火初期关闭部分等离子燃烧器的进口挡板,来保证运行燃烧器的煤粉浓度。
同时满足最低运行煤量,保证磨煤机能够正常运行而不发生振动。
采用等离子点火方式,要保证煤质良好、稳定,确保第二套制粉系统顺利启动。
2.4.2.2小油枪点火系统微油或少油启动
直吹式制粉系统锅炉冷态启动前,向锅炉下层原煤仓输入高挥发分煤,投入磨煤机进口一次风加热器(如磨煤机进口风道为油枪加热时5在点火时再投入),磨煤机入口风温达160°
C时点燃小油枪,启动磨煤机。
小油枪投入期间,保证合理的煤粉细度,控制锅炉升温升庄速度,投入空预器连续吹灰。
2.4.3邻炉加热技术
2.4.3.1从邻炉引入加热汽源,为保证参数要求,宜采用汽轮机高压缸排汽做为邻炉加热的汽源。
2.4.3.2锅炉在底部加热过程中,为防止水冷壁产生较大振动,应注意控制温升速度。
锅炉点火前停止底部加热系统,防止破坏水循环。
2.4.3.3底部加热投入后,应关闭锅炉烟风挡板,降低散
热损失。
2.4.4单侧风机启动
2.4.4.1采用单侧风机启动且配备回转式空预器的锅炉,必须具备引风机入口烟道和送风机出口均有联络通道的条件。
2.4.4.2在单侧风机启动时,监视空气预热器出入口烟温、预热器电流的变化,防止出现预热器膨胀过快或不均现象。
2.4.4.3应启动与引风机同侧的一次风机,投运与运行引风机对侧的送风机,以控制两侧烟气温度偏差在规定范围内。
3汽机运行优化
3.1基本要求
各火电企业应按照集团公司《以热效率为核心能耗管理指导意见》要求,定期开展热力试验,对照标杆查找分析短板,以提高汽轮机热效率为目标,全面优化汽机系统运行方式。
3.2机组定滑压运行优化
3.2.1各企业应结合现场测试、理论分析和运行调整进行定滑压曲线的测绘,对无法满足测试要求的企业,可委托电科院进行,并严格按照此曲线运行,力求机组在各种负荷下都能够运行在最高循环热效率点上。
3.2.2最佳的定滑压曲线随真空的不同而改变,应通过试验方法确定不同真空下的最优滑庄曲线。
3.2.3投AGC的机组,为满足负荷响应能力,滑压曲线的下拐点偏高。
应通过试验对机组AGC跟踪能力进行测试,在满足机组负荷响应速度要求的情况下,尽可能使滑压下拐点接近最优值°
3.3汽轮机单'
顺阀控制方式优化
3.3.1机组启动过程中应采用单阀控制方式,对汽缸均匀力口热,加快机组的启动速度。
机组启动正常后,应及时将单阀切为顺序阀控制,以减少调门的节流损失。
3.3.2若单阀、顺序阀控制方式切换或投入顺序阀控制时出现轴振大、瓦温高、高调门摆动等异常现象,采用“对角开启顺序阀控制”的配汽方式和优化阀门重叠度的组合方案解决。
3.3.3顺序阀控制方式运行时,部分机组调门重叠度大,节流损失大。
应通过阀序优化试验,测定调门开度与流量对应关系曲线,优化调门管理曲线。
运行时阀门开启重叠度一般不大于10%。
3.3.4对未设计顺序阀控制的机组,进行顺序阀改造时5要对调节级动应力校核。
为防止门杆斷裂,宜将各高调门指令上限调整至95%。
3.4高♦低压加热器运行优化
3.4.1要求高压加热器事故疏水手动门改电动门的机组,电动门逻辑应改为加热器水位高时联开,使高压加热器事故疏水电动门正常处于关闭状态,减少阀门内漏,减少汽轮机的冷源损失,提高机组经济性。
3.4.2高、低压加热器端差大的机组,应及时对高、低庄加热器基准水位进行校正,运行中控制高、低压加热器水位在正常范围内,降低高、低庄加热器端差。
3.4.3对凝结水、给水各级加热器温升进行分析(重点分析给水温度,各加热器上端差和下端差的变化,高加三通阀后的温度,抽汽管道庄损的变化,高、低压加热器及轴封加热器的水位,除氧器的运行温度、压力以及抽汽管路的压降等)发生异常变化及时做好分析调整;
机组检修时加强对阀门解体检查、阀门研磨工作和冷热态阀门行程调整,防止水侧旁路阀发生短路。
3.5轴封系统运行优化
3.5.1正常运行中要保持足够的凝结水通过汽封加热器,使汽封回汽及门杆漏汽完全凝结,确保轴封回汽及门杆漏汽畅通。
3.5.2要维持轴封加热器合适的水位,对轴封溢流应优先考虑将蒸汽导入低加系统。
3.6阀门的运行优化
3.6.1阀门内漏对机组的经济性影响很大,要从设计、安装、采购等方面着手把好质量关。
对介质温度超过150°
C的疏放水门应加装管壁温度测点。
并将阀门管壁温度测点引至DCS系统,监视其温度变化趋势,发现异常要及时处理。
3.6.2机组启动后应对需关闭的阀门进行一次全面检查,对管壁温度测点或红外线测温仪测得的阀体温度进行分析。
3.6.3在机组启停过程中,应严格按照规定对疏水阀门进行开启和关闭操作,严禁早开、晩关疏水阀门,以免蒸汽过度冲刷造成疏水阀门损坏。
3.6.4机组停机检修时,加强对疏水阀门的检查维护,加大阀门密封面研磨治理,对于密封面磨损过大的阀门及时进行更换。
3.6.5运行操作应先开一次门,再开二次门,关闭时应先关二次门,后关一次门,防止一次门磨损无法隔绝系统。
3.7循环水系统运行优化
3.7.1为保证循环水满足机组在最佳真空下运行,提高机组运行的经济性。
火电企业应通过试验确定各机组循环水泵与真空经济工况点,采取改变循环水泵运行台数、循环水泵配置高、低速切换电机或加装变频器的方式改进循环泵的运行方式,有效降低电能损耗。
3.7.2对于有两台及以上机组的电厂,应联通循环水系统,采用扩大单元制供水,使循环水系统的优化方式更加灵活,同时能降低机组在启停时循环水泵的耗电量。
3.8凝结水系统运行优化
3.&
1机组运行中要定期检查凝结水系统处于关闭状态阀门(包括凝结水再循环门、疏扩减温水门、低旁减温水门、排汽缸喷水门、凝结水系统放水门、高排通风阀减温水门等)的严密性,减少因阀门内漏导致凝结水泵耗电率增加。
2凝结水泵变频改造后,凝结水母管庄力明显降低,低负荷时尤为明显。
若轴封减温器减温水压力低,不能满足正常要求,应根据实际情况及时更换喷嘴或对系统进行改造,保持低庄轴封温度在正常范围。
3凝结水泵变频改造时,综合考虑凝结水压力下降对密封水的影响,以及机组启动过程低旁减温水对压力的要求,应通过试验确定凝结水最低压力,尽可能减少因提升凝结水压力而造成的耗电率升高。
凝结水泵改造前后要对整个系统各段阻力进行测试比较,变频和通流改造后凝结水调节站主、副调整门应处于全部开启状态。
3•&
4对于设计采用“两运一备”方式配置的凝结水系统,应通过试验核定单泵最大出力。
以凝结水泵耗电率最低为目标,运行中及时调整运行方式。
3.9冷却水塔的运行优化
3.9.1冷却水塔旁路电动门、防冻管电动门关闭后,应确认其关闭严密,防止冲刷内漏导致冷却塔出水温度升高。
3.9.2冷却水塔热负荷大于90%额定负荷,夏季至少每月测试冷却塔出口水温与大气湿球温度之差不大于7°
C,否则应查明原因。
3.9.3在冬季环境温度较低时,北方寒冷地区冷却塔需要开启防冻管、关闭内环配水门(对于虹吸配水冷却塔采取破坏内环虹吸的方法)并配合装设挡风板防冻。
机组运行中调整真空时优先使用防冻管和调整内环配水,若通过上述方法调整仍无法满足要求时,应通过调整挡风板的数量调整循环水进水温度。
已结冰的冷却水塔应根据结冰情况及时加大淋水密度化冰,严重时要组织人力除冰,防止损坏水塔填料。
3.10真空系统的运行优化
3.10.1工业水温度较高时,应采用其他合适的低温水源,如采用深井水、中央空调制冷水或加装制冷机组等作为真空泵的备用冷却水,降低真空泵冷却水的温度,保证真空泵的抽真空能力。
3.10.2真空泵补水采用温度较低的除盐水,用低温水置换高温水,从而维持或降低真空泵的冷却介质温度。
3.10.3在现有的凝汽器抽空气管道的入口处加装一混合式冷却器,蒸汽空气混合物中的蒸汽在进入水环真空泵之前凝结,提高水环真空泵的工作能力。
3.11双背压凝汽器运行优化
3.11.1在不影响高压侧凝汽器真空的前提下,尽量关小高压侧凝汽器抽真空手动总门,提高真空泵对低压侧凝汽器的抽吸能力,减小低压侧凝汽器传热端差,提高低压侧真空。
3.11.2要保证胶球清洗装置的投入,确保胶球清洗装置收球率,发现问题及时进行分析查找原因,保证胶球装置运行正常。
并根据循环水水质、管束的脏污程度、凝汽器端差变化调整胶球清洗装置的投运周期。
3.11.3对于闭式循环水系统,应定期对循环水一次滤网进行清理。
对于开式循环水系统,应定期对栏污栅进行清理,确保旋转滤网冲洗质量。
3.11.4定期对循环水旋转二次滤网进行排污并就地检查滤网旋转情况,保证循环水二次滤网自动排污装置正常运行,确保循环水旋转二次滤网工作正常,定期检查滤网前后压差及滤网堵塞情况,发现滤网堵塞应积极消除。
机组大小修启动后应加强循环水旋转二次滤网自动排污回收器清理工作。
3.11.5定期组织人员对水塔区域杂物进行清理,防止杂物随风吹入水塔集水池内。
机组大修时进行水塔清理底部淤泥工作,水塔充水前,对塔盆内的清洁及水塔进水槽篦子是否完好进行验收确认。
3.11.6闭式循环水系统,要根据化学监督的数据及时进行循环水浓缩倍率的调整。
4.锅炉运行优化
4.1基本要求
依靠机组在线监视、调整,在对设备运行状态进行诊断分析的基础上,减少锅炉各项损失,不断提高锅炉效率,苦练内功,向调整要效益。
4.2锅炉燃烧运行优化
4.2.1对于高挥发份煤种,应避免燃烧器喷口结焦,或烧损燃烧器喷嘴。
运行中需保持合理的一次风速和风量,保持较高的风煤比。
对挥发份较低的煤种,应在运行中适当降低一次风量,提高磨煤机一次风粉浓度,并尽量提高磨煤机出口温度。
4.2.2保证合适的煤粉细度。
煤粉细度的选择应根据锅炉燃烧情况、受热面是否存在结焦、超温以及飞灰可燃物等情况进行综合判斷。
4.2.3根据锅炉燃烧型式采取合适的燃煤掺烧方式。
在进行掺烧时,需综合考虑锅炉的各项经济、安全以及环保等指标。
煤种掺烧主要采取炉外预混或者炉内混烧(即磨煤机分仓上煤)两种方式。
对于切圆燃烧锅炉,同层各角燃烧器相互支持,燃烧稳定性较强,宜采取炉内混烧的方式;
对冲燃烧方式的锅炉,同层各燃烧器之间相互支持作用较小,低负荷燃烧稳定能力相对较弱,在燃用低挥发分煤种宜采用炉外预混的掺配方式。
4.2.4进行炉外预混,掺烧热值相差较大的煤种时,应控制配煤混合的均匀性,避免混煤不均造成锅炉燃烧波动。
4.2.5根据锅炉负荷、燃料性质以及配风工况等因素通过试验确定合理的氧量控制曲线,运行中严格按照控制曲线进行燃烧调整。
遇到煤质、设备状态有明显变化时,必须通过燃烧调整试验对氧量曲线进行修正。
低负荷时的风量调节应在满足燃烧稳定的前提下尽量控制锅炉风量不至于过大。
4.2.6对于切圆燃烧锅炉,燃用贫煤、无烟煤等着火与燃尽特性不好的煤种,宜采用分级配风,即倒塔型配风方式。
燃用烟煤等燃烧特性一般的煤种,宜采用均匀配风方式。
但在低负荷燃烧不稳或者有轻微结焦情况下,可以采用束腰型的配风方式,以达到加强煤粉着火,提高燃烧的稳定性和经济性的目的。
燃用无结渣性的优质烟煤等燃烧特性较好的煤种,宜采用正塔型配风方式。
燃用易结渣的烟煤等燃烧特性较好的煤种,可采用束腰型配风方式。
4.2.7对于对冲燃烧锅炉,燃用挥发份偏低的煤种,应提高燃烧器旋流强度,并通过调小燃烧器中心风量来提高燃烧器根部温度,保证煤粉燃烧温度。
燃用高挥发份煤种,应降低燃烧器旋流强度,开大燃烧器内二次风挡板,降低通风阻力。
同时加大燃烧器中心风量,降低燃烧器喷口温度,防止燃烧器喷口烧损或结焦。
4.2.8锅炉燃烧调整时一、二次风量应合理分配:
一次风量以能满足挥发份的燃烧为原则。
二次风混入一次风的时间要合适。
在满足锅炉合适氧量前提下,应尽可能降低一次风量(但必须满足送粉需求,防止磨煤机或者输粉管堵塞),增加二次风量,以达到加强煤粉燃烧、降低锅炉排烟温度的目的。
4.2.9减少锅炉的无效配风(炉底漏风、干渣系统冷却风、炉膛与烟道的漏风、磨煤机出口温度控制冷风、备用磨的通风及燃烧器的冷却风、磨煤机密封风、负压制粉系统漏风等,都是锅炉的无效配风),这部分漏风未经过空预器加热,一定程度上造成排烟温度升高、炉膛温度降低,近而影响锅炉效率降低。
因此,在机组运行中要尽量避免或减少这些掺冷风问题的出现。
4.2.10根据制粉系统运行状况,定期进行一次风调平以及煤粉细度的测试工作。
一次风调平时,应保证阻力最大的煤粉管道缩孔全开。
对于带有动态分离器的直吹式制粉系统,应积极摸索磨煤机动态分离器转速与给煤量对应函数关系,保证经济煤粉细度。
4.2.11定期对锅炉省煤器出口氧量、锅炉送风量、磨煤机入口风量进行标定,以提高运行人员对锅炉燃烧调整把握的准确度,防止锅炉实际送风量过大或者过小对锅炉运行经济性造成不利影响,以及磨煤机入口风量过大影响到锅炉排烟温度。
4.2.12对安装在线飞灰可燃物检测装置的锅炉,应定期与手工取样飞灰可燃物进行对比校验,以确保在线飞灰可燃物显示的准确性,指导运行人员进行相应的燃烧调整。
4.2.13定期对石子煤的发热量进行测试,当发现石子煤发热量偏大时应及时对磨煤机出力进行分析,并采取有针对性的调整措施(如改变制粉系统风煤比、煤粉细度以及对磨煤机进行检修等),将石子煤排放控制在合理的范围内。
4.2.14对于中储式制粉系统,应定期进行分离器试验,保证分离器良好工作效果,防止三次风大量带粉引起锅炉燃烧滞后,导致锅炉效率下降。
4.3锅炉吹灰系统优化
4.3.1根据吹灰前后排烟温度和主、再热汽温的变化情况,定期分析吹灰效果,优化吹灰的次数、时间,避免欠吹或过吹°
4.3.2优化吹灰应遵循以下原则:
4.3.2.1再热减温水量最小;
4.3.2.2排烟温度最低;
4.3.2.3受热面壁温不超标。
在锅炉进行吹灰时,应摸索吹灰母管疏水方式(疏水温度或疏水时间)合理性,既要保证充分暖管,避免蒸汽带水对锅炉受热面造成损伤、或空预器换热元件积灰堵塞,也要避免疏水时间过长导致工质浪费。
4.4制粉系统优化
4.4.1合理确定机组一次风压曲线,用运行磨煤机的最大给煤指令作为一次风压设定函数,机组负荷作为一次风压设定的前馈信号。
随着磨煤机给煤量的变化,一次风压的设定值也相应发生变化,保证运行磨煤机一次风调节挡板维持足够大的开度,降低磨煤机通风阻力,降低制粉系统单耗。
4.4.2合理组合磨煤机运行方式,在机组运行工况允许的条件下,应通过及时投、停磨煤机来保证各台磨煤机经济运行,避免磨煤机低出力运行。
此外,在机组运行过程中,为保证燃烧的均匀性和制粉系统的运行经济性,应尽量让各台运行磨煤机保持稳定出力运行。
4.4.3为了维持锅炉经济的风煤比,在磨煤机出力允许的条件下,可通过改变磨煤机入口一次风温度的方法调节磨煤机出口温度。
4.4.4通过试验确定不同型式分离器的特性曲线,根据特性曲线以及飞灰可燃物、炉底渣量、石子煤量、磨煤机火检、制粉单耗等情况调整磨煤机出口分离器挡板开度,并适时测量磨煤机煤粉细度,使磨煤机达到经济煤粉细度。
4.4.5定期校验一次风量,在保证制粉出力、干燥出力及煤粉初期着火需求情况,合理调整一次风量。
4.4.6对于中速磨煤机,应合理的确定磨煤机液压加载曲线,在保证磨煤机出力和煤粉细度的前提下,降低磨煤机加载力,延长磨棍、衬瓦、输粉管及受热面的使用寿命,降低磨煤机单耗。
4.4.7采用二次风小风门(或二次风挡板)控制各燃烧器进风量的均匀性,在保证锅炉燃烧器进风量的情况下,二次风小风门(或二次风挡板)尽可能开大,减少燃烧器阻力。
4.4.8通过试验确定增压风机与引风机串联运行方式下,经济运行点(增压风机和引风机电流之和为最小值)。
在对引风机与增压风机协调控制运行优化不斷摸索的同时,还可以尝试在机组低负荷时停止一台增压风机运行,保持风机维持较高效率,达到进一步提高运行经济性的目的。
4.5燃煤掺配优化
4.5.1入炉煤混配应根据供热负荷、发电调度曲线和锅炉燃烧特性进行燃煤掺配。
掺配白天用煤,热值和挥发分可相对高一些,掺配夜间用煤,热值和挥发分尽可能低一些。
4.5.2掺配高硫煤时,可根据各台炉脱硫特性进行分炉配煤,防止排放超标。
新矿、较长时间未供应煤的矿来煤,严禁立即使用,需取样分析,清楚煤质后方可配用。
4.5.3燃煤如偏离设计煤质较大时,应采取纵堆横取的掺混方法,均匀混配入炉煤。
泥煤必须经干燥处理后方可进行掺烧,洗混煤的掺烧应控制比例。
根据泥煤、洗混煤的存放量,每日有计划地掺烧。
4.5.4特殊情况下的掺配煤,必须先通过全面的燃烧调整试验来确定方案。
5电气设备运行优化
5.1基本要求
整合系统各类运行信息,深度开展电气运行方式分析,结合电气运行方式特点,有针对性的根据年度、季度、月度不同工况,开展电气设备优化工作,不斷提高发电机效率,降低厂用电率。