PLC的煤矿空压机控制系统设计 精品Word文档格式.docx
《PLC的煤矿空压机控制系统设计 精品Word文档格式.docx》由会员分享,可在线阅读,更多相关《PLC的煤矿空压机控制系统设计 精品Word文档格式.docx(29页珍藏版)》请在冰豆网上搜索。
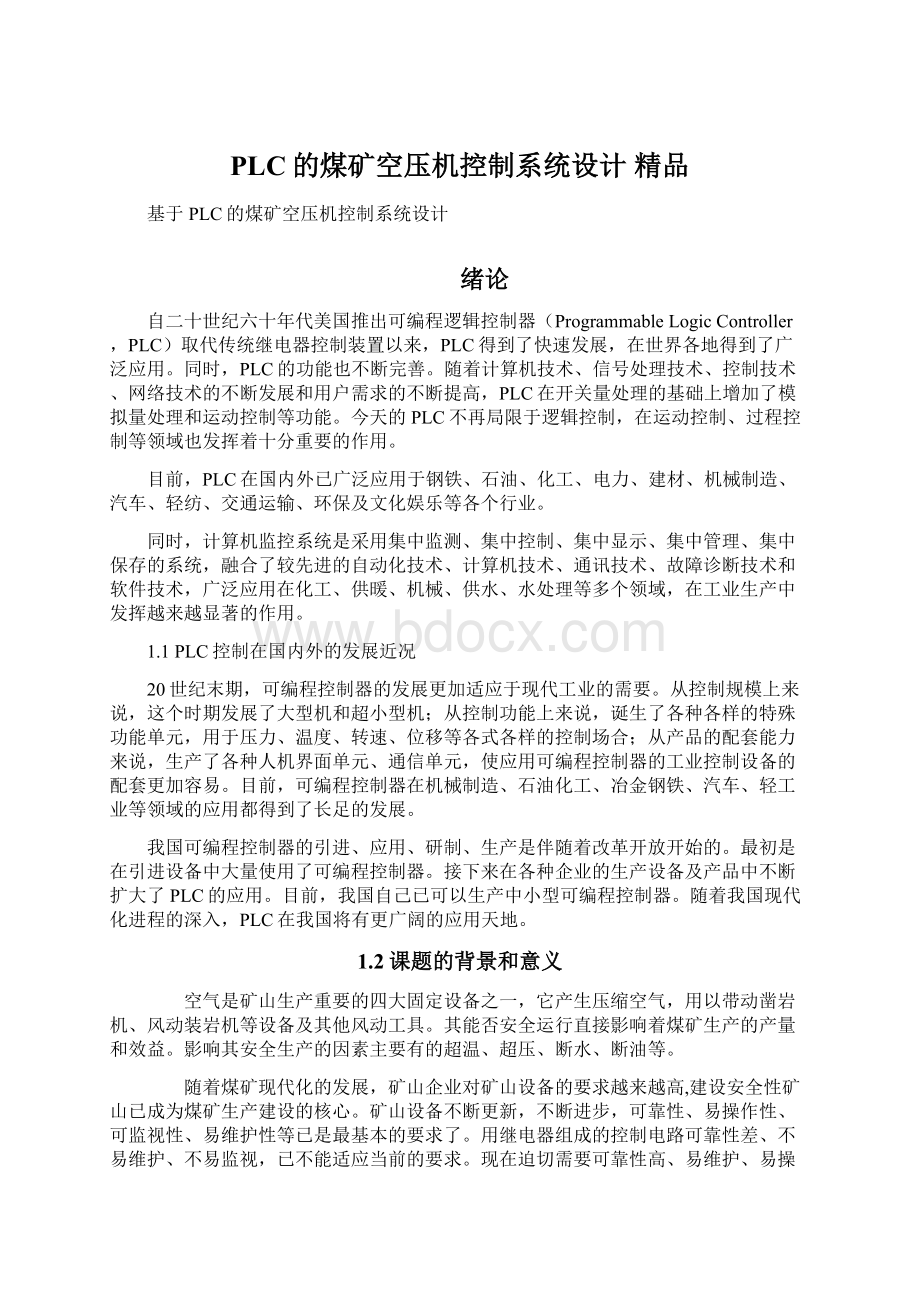
随着电子技术、软件技术、控制技术的飞速发展,可编程控制器(PLC)发展迅猛,性能很高,价格较为合理,与继电器组的控制电路比具有非常大的优势。
许多矿山设备已选用了PLC来代替比较重要的控制设备。
传统的保护设备主要采用分离仪表,其可靠性差、集程度低、费用高,不能有效的满足矿山设备投入的经济性和安全性的要求。
空压机控制系统中PLC的引入极大地简化了空压机系统的操作,节省了人力并且提高了系统的安全性和稳定性。
基于PLC和变频器的空压机控制系统使工作人员可以在计算机集控下完成各项工作,大大减轻了工人的劳动强度,极大地节省了生产中所需的人力资源,也保障了生产和系统的安全。
2空气压缩机
2.1空气压缩机及分类
空气压缩机(空压机)是一种利用电动机将气体在压缩腔内进行压缩并使压缩的气体具有一定压力的设备。
作为基础工业设备,空压机在冶金、机械制造、矿山、电力、纺织、石化、轻纺等几乎所有的工业行业都有广泛的应用。
空压机分为螺杆式空压机(螺杆式空压机又分为单螺杆式空压机及双螺杆式空压机)、离心式空压机、活塞式空压机、滑片式空压机、涡旋式空压机和旋叶式空压机等(如图2-1所示)
图2-1空气压缩机分类
2.2螺杆式空压机
2.2.1螺杆式空压机基本结构
在压缩机机体中,平行的配置着一对互相咧合的螺旋形转子通常把节圆外具有凸齿的转子,称为阳转子或阳螺杆。
把节圆内具有凹齿的转子,称为阴转子或阴螺杆。
一般阳转子与原动机连接,由阳转子带动阴转子转动。
转子上的最后一对轴承实现轴向定位,并承受压缩机中的轴向力。
转子两端的圆柱滚子轴承使转子实现径向定位,并承受压缩机中的径向力。
在压缩机机体的两端,分别开设一定形状和大小的孔口。
一个供吸气用,称为进气口;
另一个供排气用,称作排气口。
2.2.2螺杆压缩机的工作原理
螺杆压缩机的工作循环过程可分为进气,压缩和排气三个过程。
随着转子旋转,每对相互啮合的齿相继完成相同的工作循环。
(1)进气过程:
转子转动时,阴阳转子的齿沟空间在转至进气端壁开口时其
空间最大,此时转子齿沟空间与进气口的相通,因在排气时齿沟的气体被完全排出,排气完成时,齿沟处于真空状态,当转至进气口时,外界气体即被吸入,沿轴向进入阴阳转子的齿沟内。
当气体充满了整个齿沟时,转子进气侧端面转离机壳进气口,在齿沟的气体即被封闭。
(2)压缩过程:
阴阳转子在吸气结束时,其阴阳转子齿尖会与机壳封闭,此时气体在齿沟内不再外流。
其啮合面逐渐向排气端移动。
啮合面与排气口之间的齿沟空间渐渐减小,齿沟内的气体被压缩,压力提高。
(3)排气过程:
当转子的啮合端面转到与机壳排气口相通时,被压缩的气体开始排出,直至齿尖与齿沟的啮合面移至排气端面,此时阴阳转子的啮合面与机壳排气口的齿沟空间为0,即完成排气过程,于此同时转子的啮合面与机壳进气口之间的齿沟长度又达到最长,进气过程又再进行。
从上述工作原理可以看出,螺杆压缩机是一种工作容积作回转运动的容积式气体压缩机械。
气体的压缩依靠容积的变化来实现,而容积的变化又是借助压缩机的一对转子在机壳内作回转运动来达到。
2.2.3螺杆压缩机的特点
就气体压力提高的原理而言,螺杆压缩机与活塞压缩机相同,都属容积式压缩机。
就主要部件的运动形式而言,又与离心压缩机相似。
所以,螺杆压缩机同时具有上述两类压缩机的特点。
(1)螺杆压缩机的优点
1)可靠性高:
螺杆压缩机零部件少,没有易损件,因而它运转可靠,寿命长,大修间隔期可达4~8万小时。
2)操作维护方便:
操作人员不必经过专业培训,可实现无人值守运转。
3)动力平衡性好:
螺杆压缩机没有不平衡惯性力,机器可平稳地高速工作,可实现无基础运转。
4)适应性强:
螺杆压缩机具有强制输气的特点,排气量几乎不受排气压力的影响,在宽广范围内能保证较高的效率。
5)多相混输:
螺杆压缩机的转子齿面实际上留有间隙,因而能耐液体冲击,可压送含液气体,含粉尘气体,易聚合气体等。
(2)螺杆压缩机的缺点
1)造价高:
螺杆压缩机的转子齿面是一空间曲面,需利用特制的刀具,在价格昂贵的专用设备上进行加工。
另外,对螺杆压缩机气缸的加工精度也有较高的要求。
2)不适合高压场合:
由于受到转子刚度和轴承寿命等方面的限制,螺杆压缩机只能适用于中,低压范围,排气压力一般不能超过3.0MPa。
3)不能制成微型:
螺杆压缩机依靠间隙密封气体,目前一般只有容积流量大于0.2m3/min,螺杆压缩机才具有优越的性能。
2.3活塞式空压机
活塞式空压机主要由三部分组成:
运动机(曲轴、轴承、连杆、十字头、皮带轮或联轴器等)、工作机构(气缸、活塞、气阀等)与机身。
此外还有3个辅助系统,即润滑系统、冷却系统及调节系统。
活塞式空压机是一种最常见的容积式压缩机。
它由曲柄连杆机构将驱动机的旋转运动变为活塞的往复运动。
活塞与气缸共同组成压缩机工作腔,依靠活塞在气缸内的往复运动,并借助进、排气阀的自动开闭,使气体周期性的进入工作腔,进行压缩和排出。
活塞在气缸内一次往复的全过程分为吸气、压缩和排气三个过程,合称一个工作过程,如图2-2所示。
图2-2单级活塞式空压机原理简图
一个工作循环周期如下:
(1)吸气过程。
当活塞2向右边移动时,汽缸左边的容积增大,压力下降,当压力降到稍低于进气管中空气压力时,管内空气便顶开进气阀3进入气缸,并随着活塞的向右移动继续进入气缸,直到活塞移至右边的末端为止。
(2)压缩过程。
当活塞向左移动时,气缸左边容积开始缩小,空气被压缩,压力随之上升。
由于进气阀的止气作用,缸内空气不能倒流回进气管中。
同时,因排气管内的空气压力又高于气缸内空气压力,空气无法从排气阀4流出缸外,排气管中的空气也因排气阀的止逆作用而不能流回缸内,所以这时气缸形成一个密闭的容积。
当活塞继续向左移动,气缸容积缩小,空气体积也随之缩小,压力不断提高。
(3)排气过程。
随着活塞不断左移压缩缸内空气,使压力继续升高。
当压力稍高于排气管中的压力时,缸内空气便顶开排气阀排入排气管中,并继续排出到活塞移至左边的末端为止。
然后,活塞又向右移动,重复上述吸气、压缩和排气工作过程。
活塞式的传动机构是曲轴连杆往复运动结构,其主要特点有:
流量较小,气流速度低,损失小,效率高;
压力范围广,适用于从低压到超高压;
适应性强,排气压力变动较大时,排气量不变;
机组零件多用普通金属材料,制造精度要求不太高;
外形尺寸及重量较大,结构复杂,易损失件多。
活塞式空压机与螺杆式空压机的比较:
(1)零部件的数量多,零部件的损坏的机率大,产品的可靠性低。
这样必然增加用户的维修费用。
(2)曲轴连杆往复运动结构,由于其往复运动的特性,限制了其转速的提高,致使机器笨重,同时,该运动结构所产生的惯性力能以平衡,剩余的惯性力,会使机器产生振动、噪声以及零部件的不正常的损坏。
所以活塞式振动大,机械性噪音大、可靠性低。
鉴于以上原因,本系统选用螺杆式空压机。
3可编程控制器(plc)控制系统
3.1PLC的产生和发展
(1)PLC概念
PLC是在继电器控制和计算机技术的基础上开发出来的,并逐渐发展成以微处理器为核心,集计算机技术、自动控制技术及通讯技术于一体的一种新型工业控制装置。
(2)PLC发展必然性
传统的继电接触器控制系统(硬件布线)
优点:
结构简单,因而长期广泛应用。
缺点:
采用固定的接线方式。
一旦生产要求及生产过程发生变化,必须重新设计线路,重新接线安装。
不利于产品的更新换代。
还有灵活性、通用性差;
体积大;
速度慢等缺点。
60年代末期,美国汽车制造工业相当发达,要求不断更换汽车的型号。
传统的继电接触器控制系统被淘汰。
1968年,美国最大的汽车制造商GM公司公开招标。
研制新的控制系统。
提出以下要求:
设计周期短,更改容易,接线简单,成本低;
把继电器控制和计算机技术结合起来;
但编程要比计算机简单易学,操作方便,系统通用性强。
1969年,美国数字设备公司研制出世界上第一台PLC,并在GM公司的汽车生产线上首次应用成功。
其后,日本、德国相继引入。
中国1974年研制,1977年成功。
(3)功能发展史:
(名字的由来)
早期:
顺序控制。
包括逻辑运算功能。
称PLC(ProgrammableLogicController)
70年代:
微处理器用于PLC。
功能增强、数值运算、数据处理、闭环调节等,称PC。
3.2PLC基本结构
PLC主要是由CPU、电源、存储器和专门设计的输入输出接口电路等组成。
其基本结构框图如图3-1所示。
图3-1PLC结构简图
3.3PLC基本工作原理
PLC的CPU采用顺序逻辑扫描用户程序的运行方式,即如果一个输出线圈或逻辑线圈被接通或断开,该线圈的所有触点(包括其常开或常闭触点)不会立即动作,必须等扫描到该触点时才会动作。
PLC扫描用户程序的时间一般均小于100ms,因此,PLC采用了一种不同于一般微型计算机的运行方式---扫描技术如图3-2所示。
3.3.1扫描技术
当PLC投入运行后,其工作过程一般分为三个阶段,即输入采样、用户程序执行和输出刷新三个阶段。
完成上述三个阶段称作一个扫描周期。
在整个运行期间,PLC的CPU以一定的扫描速度重复执行上述三个阶段。
图3-2 扫描过程
(1)输入采样阶段
在输入采样阶段,PLC以扫描方式依次地读入所有输入状态和数据,并将它们存入I/O映象区中的相应的单元内。
输入采样结束后,转入用户程序执行和输出刷新阶段。
在这两个阶段中,即使输入状态和数据发生变化,I/O映象区中的相应单元的状态和数据也不会改变。
因此,如果输入是脉冲信号,则该脉冲信号的宽度必须大于一个扫描周期,才能保证在任何情况下,该输入均能被读入。
(2)用户程序执行阶段
在用户程序执行阶段,PLC总是按由上而下的顺序依次地扫描用户程序(梯形图)。
在扫描每一组梯形图时,又总是先扫描梯形图左边的由各触点构成的控制线路,并按先左后右、先上后下的顺序对由触点构成的控制线路进行逻辑运算,然后根据逻辑运算的结果,刷新该逻辑线圈在系统RAM存储区中对应位的状态;
或者刷新该输出线圈在I/O映象区中对应位的状态;
或者确定是否要执行该梯形图所规定的特殊功能指令。
即,在用户程序执行过程中,只有输入点在I/O映像区内的状态和数据不会发生变化,而其他输出点和软设备在I/O映象区或系统RAM存储区内的状态和数据都有可能发生变化,而且排在上面的梯形图,其程序执行结果会对排在下面的凡是用到这些线圈或数据的梯形图起作用;
相反,排在下面的梯形图,其被刷新的逻辑线圈的状态或数据只能到下一个扫描周期才能对排在其上面的程序起作用。
(3)输出刷新阶段
当扫描用户程序结束后,PLC就进入输出刷新阶段。
在此期间,CPU按照I/O映像区内对应的状态和数据刷新所有的输出锁存电路,再经输出电路驱动相应的外设。
这时,才是PLC的真正输出。
3.3.2PLC的I/O响应时间
为了增强PLC的抗干扰能力,提高其可靠性,PLC的每个开关量输入端都采用光电隔离等技术。
为了能实现继电器控制线路的硬逻辑并行控制,PLC采用了不同于一般微型计算机的运行方式(扫描技术)。
以上两个主要原因,使得PLC的I/O响应比一般微型计算机构成的工业控制系统慢得多,其响应时间至少等于一个扫描周期,一般均大于一个扫描周期甚至更长。
所谓I/O响应时间指从PLC的某一输入信号变化开始到系统有关输出端信号的改变所需的时间。
3.4PLC的主要特点
(1)高可靠性
1)所有的I/O接口电路均采用光电隔离,使工业现场的外电路与PLC内部电路之间电气上隔离。
2)各输入端均采用RC滤波器,其滤波时间常数一般为10~20ms。
3)各模块均采用屏蔽措施,以防止辐射干扰。
4)采用性能优良的开关电源。
5)对采用的器件进行严格的筛选。
6)良好的自诊断功能,一旦电源或其他软,硬件发生异常情况,CPU立即采用有效措施,以防止故障扩大。
7)大型PLC还可以采用由双CPU构成冗余系统或有三CPU构成表决系统,使可靠性更进一步提高。
(2)丰富的I/O接口模块
PLC针对不同的工业现场信号,如:
交流或直流、开关量或模拟量、电压或电流、脉冲或电位、强电或弱电等。
有相应的I/O模块与工业现场的器件或设备,如:
按钮、行程开关、接近开关、传感器及变送器、电磁线圈、控制阀等直接连接。
另外为了提高操作性能,它还有多种人-机对话的接口模块;
为了组成工业局部,它还有多种通讯联网的接口模块等等。
(3)采用模块化结构
为了适应各种工业控制需要,除了单元式的小型PLC以外,绝大多数PLC均采用模块化结构。
PLC的各个部件,包括CPU、电源、I/O等均采用模块化设计,由机架及电缆将各模块连接起来,系统的规模和功能可根据用户的需要自行组合。
(4)编程简单易学
PLC的编程大多采用类似于继电器控制线路的梯形图形式,对使用者来说,不需要具备计算机的专门知识,因此很容易被一般工程技术人员所理解和掌握。
(5)安装简单,维修方便
PLC不需要专门的机房,可以在各种工业环境下直接运行。
使用时只需将现场的各种设备与PLC相应的I/O端相连接,即可投入运行。
各种模块上均有运行和故障指示装置,便于用户了解运行情况和查找故障。
由于采用模块化结构,因此一旦某模块发生故障,用户可以通过更换模块的方法,使系统迅速恢复运行。
4基于plc的煤矿空压机控制系统设计方案
4.1控制系统组成
控制系统由以下部分组成:
变频器、可编程控制器、电抗器、压力变送器、接触器、空气开关、电流表、电压表、按钮、互感器等。
基于PLC的控制系统原理图如图4-1所示。
图4-1控制系统简图
PLC由电源、CPU、模拟量输入、输出模块、开关量输入、输出模块等组成。
其用来实现电气部分的控制。
包括五部分:
起动、运行、停止、切换、报警及故障自诊断。
起动:
三台电机M1,M2,M3如图4-1所示,可以通过转换开关选择变频/工频启动。
运行:
正常情况,电机M1处于变频调速状态,电动机M2、M3处于停机状态。
现场压力变送器检测管网出口压力,并与给定值比较,经PID指令运算,得到频率信号,调节变频器的输出频率,以调节电动机的转速,达到所需压力的目的。
停止:
按下停止按钮,PLC控制所有的接触器断开,变频器停止工作。
切换:
实现M1,M2,M3工频、变频相互切换。
报警及故障自诊断:
空压机内部一般有四个需要监测的量:
冷却水压力监测、润滑油监测、机体温度监测、储气罐压力监测。
4.2控制系统的工作原理
启动前,将变频器的机组开关置于欲工作的机组,工作方式选择置于变频位置,将PLC的控制开关置于运行状态,按下启动按钮,机组运行。
1#空压机变频启动,转速从零开始上升,若达到预设的频率上限值50Hz时,延时一段时间后风包出口处的压力仍不能达到预设的压力值(0.55~0.65MPa),则由PLC通过控制中间继电器的通断将1#空压机切换到工频运行,同时将2#空气压缩机切换到变频状态,变频启动2#空压机。
若2#空压机达到频率上限时,延时一段时间后仍不能满足要求,再自动将2#空压机切换到工频运行,变频启动3#空压机。
当用风量减小,若3台空压机同时运行时,3#空压机变频运行而此时变频器的频率降到频率的下限值20Hz时,则自动停止1#空压机,若还不能满足要求,则自动停止2#空压机的运行。
当空压机在运行的过程中出现机体温度过高,润滑油温度过高,风包温度过高,分包压力过高及润滑油压力过高,断水等故障时,系统会发出声光报警信号,提示有关的工作人员及时地排除故障。
控制系统工作流程如图4-2所示。
图4-2控制系统流程图
该系统具有手动和自动两种运行方式:
(1)手动运行方式
选择此方式时,按启动按钮空压机或停止按钮,可根据需要而分别启停各空压机。
这种方式仅供检修或控制系统出现故障时使用。
(2)自动运行方式
在自动运行方式下开始启动运行时,首先打开冷却水阀,关闭供气阀,1#空压机变频交流接触器吸合,电机与变频器连通(启动过程如图4-3)变频器输出频率从0Hz开始上升,此时压力变送器检测压力信号反馈PLC,由PLC经PID运算后控制变频器的频率输出;
如压力不够,则频率上升至50Hz,延时一定时间后,将1#空压机切换为工频,2#空压机变频交流接触器吸合,变频启动2#空压机,频率逐渐上升,直至供气压力达到设定压力,依次类推增加空压机。
变频调速系统将管网压力作为控制对象,装在储气管出气口的压力变送器将储气罐的压力转变为电信号送给PLC内部PID调节器,与压力给定值进行比较,并根据差值的大小按既定的PID控制模式进行运算,产生控制信号去控制变频器的输出电压和逆变频率。
当压力小于设定值时,频率升为50HZ,延时30s后,若测量值仍小于设定值,则变频器切换为工频运行,同时变频器启动下一台空压机,依次启动各台空压机。
当压力大于设定值时,通过PID调节降低频率,当频率降为20HZ,延时30s后,若测量值仍大于设定值,则变频器切换到下一正在运行的空压机进行调速,同时关闭当前机。
依次关闭各台空压机。
从而使实际压力始终维持在给定压力。
另外,采用该方案后,空气压缩机电动机从静止到稳定转速可由变频器实现软启动,避免了启动时的大电流和启动给空气压缩机带来的机械冲击。
正常情况下,空气压缩机在变频器调速控制方式下工作。
变频器一旦出现故障,煤炭生产不允许空气压缩机停机,因此,系统设置了工频与变频切换功能,这样当变频器出现故障时,可由工频电源通过接触器直接供电,使空气压缩机照常工作。
整个控制过程如下:
用气需求↑——管路气压↓——压力设定值与反馈值的差值↑——PID输出↑——变频器输出频率↑——空压机电机转速↑——供气流量↑——管路气压趋于稳定
特别注意:
为防止电机频繁起制动和变速,在压力容差范围内,变频器的输出频率不变。
图4-3启动过程
空压机变频调速系统原理如图4-4所示。
图4-4空压机变频调速原理图
空压机变频调速的要求:
(1)空压机是大转动惯量负载,这种启动特点很容易引起变频器在启动时出现跳过流保护的情况,故采用具有高启动转矩的无速度矢量变频器,保证既能实现恒压供气的连续性,又可保证设备可靠稳定的运行;
(2)空压机不允许长时间在低频下运行,空压机转速过低,一方面使空压机稳定性变差,另一方面也使缸体润滑度变差,会加快磨损。
所以工作下限应不低于20Hz;
(3)功率选用比空压机功率大一等级的变频器,以免空压机启动出现频繁跳闸的情况;
(4)为了有效的滤除变频器输出电流中的高次谐波分量,减少因高次谐波引起的电磁干扰,选用输出交流电抗器,还可以减少电机运行的噪音,提高电机的稳定性;
(5)设计的系统应具备变频和工频两套控制回路,确保变频出现异常跳保护时,不影响生产。
4.2.1空压机切换工作过程
开始时,若1#空压机变频启动,转速从0开始随频率上升,如变频器频率达到50Hz而此时空气压力还在下限值,延时一段时间(避免由于干扰而引起的误动作)后,1#空压机切换为工频运行,同时变频器频率由50Hz下降至0Hz,2#号空压机变频起动,如气压仍不满足,则会启动3#空压机,切换过程同上;
同样,若3台空压机(假设1#、2#、3#)都在运行,3#空压机变频运行降到0HZ,此时气压仍处于上限值,则延时一段时间后使1#空压机停止,变频器频率从0HZ迅速上升,若此时供气压力仍处于上限值,则延时一段时间后使2#空压机机停止。
这样的切换过程,有效的减少空压机的频繁启停,同时在实际管网对供气压力波动做出反应之前,由于变频器迅速调节,使气压平稳过渡,从而有效的避免了井下风动工具供气不足的情况发生。
切换过程流程图如图4-5所示。
图4-5空压机切换流程图
在自动状态下系统启动时,首先KM2吸合,1#空压机在变频器控制下起动,延时5s(延时是为了让压力稳定下来)PLC对变频器的输出频率进行检测。
当检测到变频器下限频率信号则关闭1#空压机;
反之当检测到变频器上限频率信号则PLC执行增加空压机动作:
KM2断开、KM1吸合,1#空压机改为工频运行并延时1s(延时一是为了让开关充分熄弧,另一方面是为了让变频器减速为0,KM4吸合变频启动2#空压机。
为了保护空压机及变频器,1#空压机的KM1与KM2之间进行了电气互锁。
当2#空压机投入变频运行后,延时5sPLC继续对变频器输出频率进行检测,当检测到变频器下限频率信号则关闭1#空压机,剩下2#空压机在变频状态下运行,延时5s如果PLC再次检测到变频器下限频率信号则把2#空压机也关闭;
反之当检测到变频器上限频率信号则PLC再执行增泵动作:
KM3断开、KM4吸合,2#空压机改为工频运行并延时1s,KM6吸合变频启动3#空压机。
依此类推,当3#空压机投入变频运行后,延时5s,PLC继续对变频器输出频率进行检测以决定执行增加或减少空压机动作来满足恒压供气目的。
另外为了方便故障检查维修。
在设计中增加了故障指示和故障报警输出,变频器本身具有短路保护、过载保护等功能,只需把变频器的故障输出点、接触器、热继电器等辅助触点接到PLC即可。
PLC通过程序扫描这些输入点,如果发生故障