ABS规范04Word文件下载.docx
《ABS规范04Word文件下载.docx》由会员分享,可在线阅读,更多相关《ABS规范04Word文件下载.docx(56页珍藏版)》请在冰豆网上搜索。
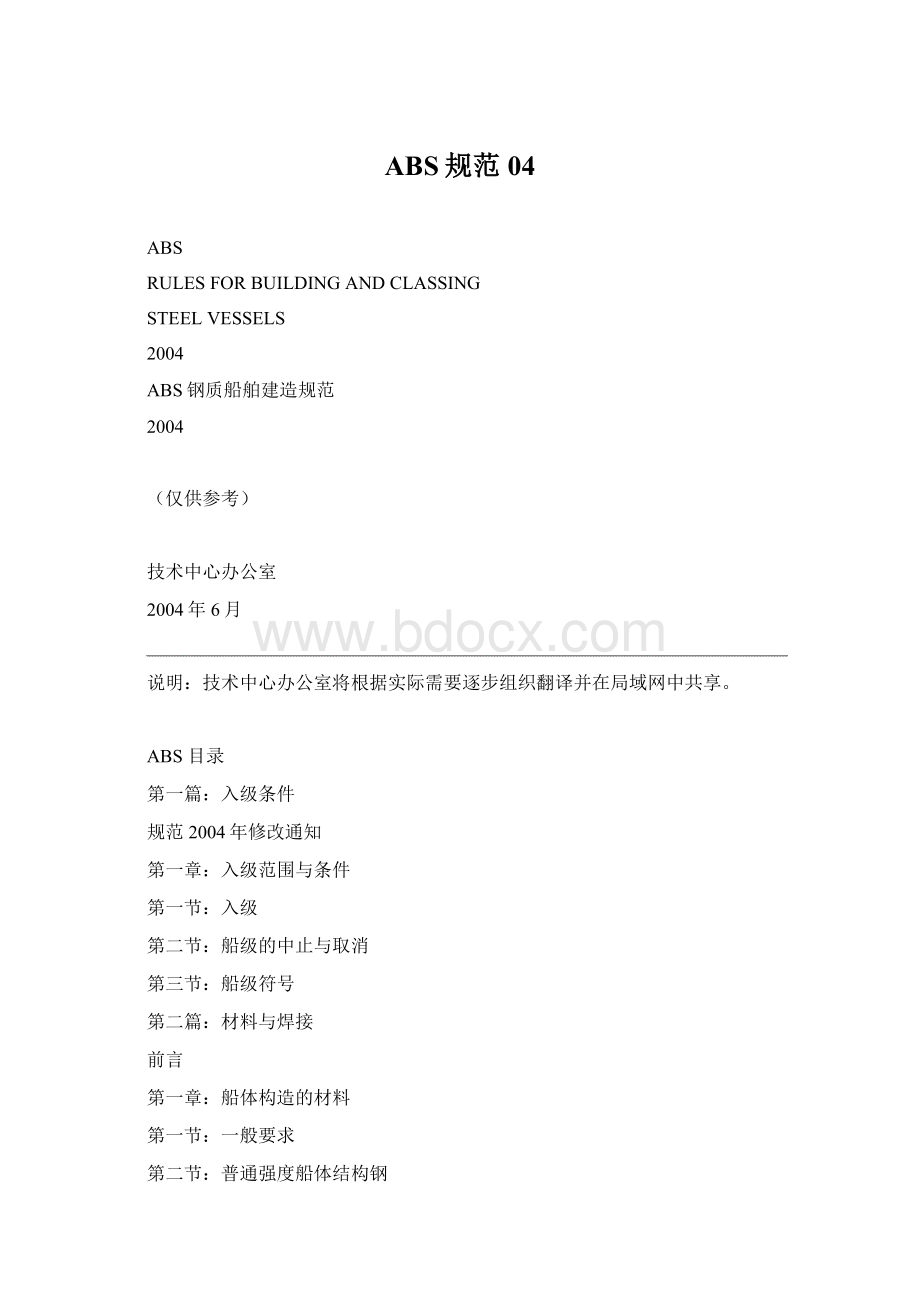
灰铸铁件
第十二节:
钢管
第十三节:
用于低温[-18℃(0℉)以下]的管路、阀及配件
第十四节:
青铜铸件
第十五节:
奥氏体不锈钢螺旋桨铸件
第十六节:
无缝铜管
第十七节:
无缝红铜管
第十八节:
第十九节:
冷凝器及热交换器管
第二十节:
铜镍管路
第二十一节:
蒙乃尔铜镍管路
附录1:
第二部分1~3章要求的有损或无损测试及其验证之责任
附录4:
批准轧制船体结构钢生产商的方案
第四章:
焊接与装配
船体建造
锅炉、非燃式压力容器、管系及工程部件
焊接试验
管路
附录2:
填充金属的认可要求
附录3:
填充金属对ABS钢的适用范围
第三篇:
船体构造与设备
总言
定义
船体结构与布置
总纵强度
船壳板
甲板
船底部结构
肋骨
强肋骨和舷侧纵桁
梁
支柱,甲板纵桁及强横梁
水密舱壁及舱门
深舱
上部建筑、舱面室及起重机甲板
机械处所和轴隧
船首、船首框架及舵角
舵
甲板开口的防护
船壳开口的防护
舷墙、栏杆、舷门、舷门灯、通风筒、液舱排气及溢流口
舱内衬板、舱壁护条及钢结构的防护
焊接设计
分舱及稳性
消防措施
结构防火
第五章:
锚泊、系泊及拖缆设备
第六章:
航行
可见度
第七章:
船体建造过程中的试验、测试与检查
液舱、舱壁和舵的密性试验
测试
检查
第四篇:
舰船系统与机械
机械的入级
原动机
柴油机
涡轮增压器
汽轮机
蒸汽轮机
推进及机动机械
齿轮
1总言
1.1应用范围
1.3定义
1.5应送审的图纸及资料
3材料
3.1材料规格及测试要求
3.3可替用材料测试要求
5设计
5.1轮齿精加工
5.3轴承
5.5齿轮箱体
5.7检测途径
5.9齿轮箱轴的计算
5.11圆柱齿轮及斜齿轮的额定值
5.13替用的齿轮额定值标准
5.15多原动机输入的齿轮箱
7齿轮箱的管路系统
9齿轮箱的测试、检测与认证
9.1材料测试
9.3动态平衡
9.5工厂检查
9.7齿轮箱的认证
9.9船上试用
附录1圆柱齿轮和斜齿轮的额定值
附录2配件指南
附录3齿轮参数
推进器轴系
螺旋桨
转向齿轮装置
推力器及动态定位系统
锅炉、压力容器及消防设备
设计规范
甲板及其它机械
起锚机
管路系统
一般规定
金属管
塑料管
船舶管路系统及液舱
内燃机管路系统
蒸汽轮机管路系统
其它管路系统
消防系统
特殊处所的规定
灭火系统及设备
第八章:
电气系统
系统设计
电气设备
船上安装与测试
特殊系统
第九章:
推进远程控制与自动控制
推进远程控制
ACC符号
ACCU符号
装配、测试与试车
计算机控制系统
第十章:
除推进外辅助机械与系统的遥控与监测
水密舱壁门、船壳体门及对外门
第五篇:
特殊船型
运输散装油的船舶(船长在150米(492英尺)以上)
介绍
设计考虑因素及一般要求
负荷标准
初始船材尺度标准
总强度评估
船体结构超过0.4L船腹
装油及关联系统
运输散装油的船舶(船长在150米(492英尺)以内)
船体结构
运输矿石或大宗货物的船舶(船长在150米(492英尺)以上)
货物安全
运输矿石或大宗货物的船舶(船长在150米(492英尺)以内)
运输集装箱的船舶(船长130米(427英尺)至350米(1148英尺))
运输集装箱的船舶(船长130米(427英尺)以内)
安全船体建造监控程序指南
客轮
运输散装液化气的船舶
船舶残存能力及货舱位置
船舶布置
货物密封度
加工压力容器及液体、汽体及压力管路
建造用材料
货物压力温度控制
货舱排气系统
环境控制
电气装配
防火与灭火
货舱区域机械通风
使用仪器(表、气体检测及货物装卸装置)
人身防护
货舱装载极限
货物用作燃料
特殊要求
操作要求
最低要求总结
运输散装化学品的船舶
货物驳运
货物温度控制
货舱通风及除气布置
使用仪器
第十六节A:
保护海洋环境的附加措施
本标准不适用化学品的清单
从事海上液体化学废品焚化工作船舶的要求
液体化学废品的运输
运输车辆的船舶
车辆基座
人车运输
第六篇:
附加项目与系统
冰海航行加强
一般冰级
波罗的海冰级
运输冷冻货物的船舶
应送审的图纸与数据
货物装卸设备
冷冻货物处所
冷冻机械
辅助系统
灭火系统与设备
使用仪器,控制及监控用
氨冷冻系统
受控空气系统
冷冻货物容器基座
冷冻散装食品液体油轮
冷冻鱼容器
第七篇:
建成后检查的规范
建成后检查的条件
一般信息
检查间隔
未限定用途的船舶
大湖区行驶的船舶
河道及近岸内航道的船舶
拖至洋面后检查
船体检查
所有船舶内部检查要求
入干船坞检查
检查要求
艉轴检查
允许轴承磨损
机械检查
锅炉检查
船自动及遥控系统
年度检查
定期特别检查
附加系统与设备的检查要求
货物制冷系统
船体状况监控系统
一人操纵系统
推进冗余系统
快速释放系统
蒸汽喷射控制系统
灭火系统
安全辅助系统
离岸装配支持用途
残油回收用途
自控、遥控及监控系统
驾驶台设计及导航设备或系统
钢质浮式干船坞
第十一章:
水下搬运装置、系统及增压供氧设备
驳运损失检查
观察孔的更换
第十二章:
近海赛艇与帆船
第2篇材料与焊接
第3章机器、锅炉、受压容器及管系用材
第7节机器钢锻件2-3-7
第7节机器钢锻件
1.13检测
经最终的热处理工序后,由检测员检测所有锻件,应无缺陷。
1.13.1尾轴锻件的表面检测
所有尾轴锻件进行一项无损检测如磁粉探伤,着色检查等。
如有不均匀性则不予通过。
(参看4-3-2/2.4.3钢船建造及分级规则,精加工条件下的表面检测要求)。
1.13.2尾轴锻件的超声波探伤
成品直径为455mm(18in)或以上的尾轴锻件应在检测员到场情况下进行超声波探伤。
如符合船级社单独发行的《尾轴碳钢锻件超声波探伤准则》或等同文件的要求,则视为合格。
3.合金钢齿轮组锻件(2000)
3.1生产工序
3.1.1总言
以下要求述及用于推进装置及辅助涡轮的齿轮合金钢锻件。
主要部件包括用于船上齿轮组件中的钢制大小齿轮的锻造轮缘与毛坯。
所用钢应为全脱氧钢并经以下一种或一种以上工序平炉,氧气顶吹转炉、电炉或其它可被批准的工序。
未经机加工、成品锻件主体的横截面积不应超出钢锭面积的三分之一;
锻件上的掌形物、凸缘及类似延展物不应超出钢锭面积的三分之二。
每块钢锭须留有一定废料以备有气泡缝及过度分凝时之需。
锻造时应施以足够大的力而使金属在锻件的最大截面内延展。
3.1.2化学成份
每炉钢水必须加以分析以确定指定元素的百分比。
由此得出的化学成份情况应提交检查员并应符合2-3-7/表3要求。
该分析应在该炉钢水浇铸时取样品进行。
3.1.3ASTM(美国材料试验标准)标识
与ABS等级相对应的ASTM标识如下:
ABS等级
ASTM标识
A1
A2912级
A2
A2913级
A3
A2914级
A4
A2915级
A5
A2916级
A6
A2917级
3.3标识,再试验及报废
3.3.1标识
除了制造商的标志外,由检查员提供的符合规则要求的船级社标志也应打在所有的锻件上,其部位应确保在机加工及安装后仍可辩清。
此外,从A1级到A6级锻件都应分别打上AB/A1、AB/A2、AB/A3、AB/A4、AB/A5及AB/A6。
3.3.2再试验
如任一个或任一批锻件的机械试验结果有不符指定要求的情况,可按照2-3-7/9或2-1-2/11.7进行再试验,或者制造商也可按2-3-7/3.5.7对这些锻件重新试验。
在重新加热后,锻件必须进行所有的机械试验。
3.3.3报废
在制造厂家接收前后发现有任何致伤的不均匀性的锻件可予以报废。
3.5热处理
3.5.1总言
各级锻件所要求热处理如下:
所需热处理及最低回火温度
级别
热处理
温度℃(°
F)
淬硬+回火
620(1150)
580(1075)
565(1050)
充分考虑部件厚度及该锻件用途后,经特别批准可采用其它热处理工艺。
所用炉应大小适当,确保锻件温度一致。
3.5.2热处理前冷却
锻造之后热处理重热之前,为防止损伤并完成变形,允许对锻件进行冷却。
在温度低于315℃(600°
F)前冷却率约为每小时55℃(100°
F)。
3.5.3退火
锻件重热并保持足够时间的正确奥氏体化温度。
然后在炉内缓慢均匀冷却直至温度降到455℃(850℃)以下。
3.5.4正火
锻件重热并保持足够长时间的变形范围以上的温度以取得所需变形。
然后从炉中取出,
在炉外自然冷却。
3.5.5回火
锻件重热并保持在适当温度,即低于变形温度范围但高于2-3-7/3.5.1中所注的最低温度。
然后以不超过每小时100°
F(55℃)的速率冷却直至温度低于315℃(600°
3.5.6解除应力
如在机加工前进行了机械性能的热处理,则该锻件应以低于先前回火温度28℃(50°
F)到55℃(100°
F)但高于540℃(1000°
F)的温度解除应力。
冷却率不得超过每小时100°
F(55℃)直至温度低于315℃(600°
3.5.7再热处理
制造商可重复热处理锻件,但额外次数不得多于3次。
3.7机械性能
3.7.1抗拉性能
锻件的抗拉性能应符合2-3-7/表4要求。
3.7.2硬度
除粗加工后重量低于113kg(250lbs)的锻件外,其余每个锻件所测出的硬度应符合以下要求:
ABS级别
硬度BHN(10mm直径3000kg负载)
201至241
223至262
248至293
285至331
302至352
341至415
3.9试验样品
3.9.1取样位置及方向
机械性能通过抗拉试验确定,其样品取自延长部分且其横截面积不小于锻件本身,如2-3-7/表4延性要求所述,确定一条以该锻件最大延展方向或与之相切方向的轴线,再以与该轴线平行方向取样。
纵向样品的轴心可定于锻件表面以下32mm(1.25in)任意一点,而切向样品的轴心则应尽可能接近表面。
对于减速齿轮圆形锻件、减速大小齿轮锻件及减速齿轮轴锻件,取样方位则按分别按2-3-7/3.9.3(d),2-3-7/3.9.3(e)及2-3-7/3.9.3(f)所述。
3.9.2样品确认
测试样品应在锻件完成最后热处理工序后提取,并应由检验员打上确认标识。
如制造商的材料确认系统受船级社认可并且在船级社首次及各次定期检查都保持此种状态,可以取代检验员在提取前所打标识。
3.9.3抗拉测试
3.9.3(a)大锻件:
对于粗加工后重量达3180kg(7000lb)及以上的大型锻件,应对其各端进行抗拉测试。
如锻件为环形或中空圆柱形,该测试则在锻件末端及与之呈180°
处进行。
3.9.3(b)中型锻件:
对于粗加工后重量轻于3180kg(7000lb)的,除以下段落所指锻件外,每个锻件应至少进行一处抗拉测试。
3.9.3(c)小型锻件:
对于粗加工后重量轻于227kg(500lb)的锻件,可在一批此类锻件取一件进行抗拉测试来代表,只要这批锻件为尺寸相近,同一等级与类别,在同一炉次及在相同炉容量经热处理的。
测试用批次大小最多为25件。
3.9.3(d)减速齿轮圆形锻件:
如是减速箱上的圆形锻件,则在每个锻件的完全延长处及与之180°
处或是在每个复合锻件的两端进行抗拉测试。
取样应在锻件粗加工表面尽可能近的切向方向。
3.9.3(e)减速箱大小齿轮锻件:
如是减速箱上的大小齿轮锻件,测试应在纵向或切向方向进行。
延长主体(带齿部分)轴线长度到一定距离,即是取样的适当位置。
3.9.3(f)减速箱轴锻件:
如是减速箱的轴锻件,该测试应在完全延展处的纵向方向进行。
3.9.4硬度
3.9.4(a)大、中、小型锻件:
除粗加工后轻于113kg(250lbs)的其它各个锻件都应进行硬度测试。
3.9.4(b)减速箱圆形锻件:
对于减速箱圆形锻件,布氏硬度试验在外径减去约
径向厚度处进行,并且应按以下次数及位置要求:
外径cm(in)
硬度试验次数
少于102(40)
每端1次,180°
分开
102到203(40~80)
每端2次,180°
203到305(80~120)
每端3次,120°
305以上(120)
每端4次,90°
3.9.4(c)减速箱大小轮锻件:
如是直径在203mm(80in)及以上的大、小轮锻件,在要切齿的锻件部分的外表面上应进行四次布氏硬度试验,在相隔180°
的螺旋线上进行两次试验,每根线上的两次试验相隔90°
。
对于每个203mm(80in)及以下直径的锻件,应在隔180°
的螺旋线上进行两次布氏硬度试验。
硬度试验在带齿部分直径的
宽处进行。
3.9.4(d)减速箱轴锻件:
对于减速箱的轴锻件,在相隔180°
的各一端进行两次硬度试验。
3.11检测
最后热处理之后,所有锻件应经检查员检测,无任何缺陷。
成品没有破裂、裂缝、皱皮、冷疤、起鳞、收缩及迸裂现象。
第4篇船舶系统与设备
第3章推进及机动机械
第1节齿轮装置4-3-1
第4篇
第1节齿轮装置
1.总述
1.1应用
按照本节条款规定,设计、制造、检验并安装额定功率为100kW(135hp)以上,用于推进器以及推进、机动及安全所必需的附属服务设备的齿轮装置。
额定功率低于100kW(135hp)的齿轮箱装置不要求符合本节规定但应按良好的商业及船上运用实践来设计、制造并安装。
该类齿轮装置的接收将基于制造商的保证书,齿轮铭牌数据的验证,还应有安装完毕后在检查员在场情况下良好的性能测试结果。
额定功率为100kW(135hp)以上,但对于推进、机动及安全并不至关重要的齿轮装置不须按本节要求设计、制造及检验,但其安装及测试须让检查员满意。
齿轮装置的管路系统,尤其是润滑油路及液压油路将分别在4-6-5节及4-6-7节中说明。
1.3定义
本节采用如下定义:
1.3.1齿轮装置
本节所用术语“齿轮装置”包括用于主推进器或辅助设备的有平行轴的内、外啮合渐开线直齿、斜齿圆柱齿轮以及锥齿轮。
1.3.2额定功率
齿轮的“额定功率”是指齿轮保持持续额定速度运转所需的最大传递功率。
1.3.3额定扭矩
额定扭矩由额定功率及速度确定,用于齿轮额定值计算中。
1.3.4齿轮额定值
齿轮额定值是指该齿轮为运载其额定扭矩而设计的额定值。
1.5需提交的设计图及数据
1.5.1齿轮结构
总配置图
剖视图
齿轮箱外壳详图
负载图
主轴、齿轮轴及毂
热套安装计算书及安装说明
小轮
大轮及轮缘
齿轮装置焊接详图
1.5.2传动系统及附件
联轴节
联轴节螺栓
润滑油系统及喷油配置
1.5.3数据
各齿轮的额定传递功率
各齿轮在额定功率下每分钟的转数
轴承长度及直径
螺旋面之间间隙长度(如存在的话)
轴承内端间距离
齿形轮廓(见4-3-1A1图1)或计算得出数据
净、及总齿轮宽
最高应力部位的齿宽
分度圆上及齿节直径上螺旋角
螺旋线偏移
法向压力角
分度圆圆柱上端面压力角
工作节圆柱上端面压力角
齿轮装置的参考锥角
齿轮装置的顶锥角
齿轮锥距
齿轮中锥距
法向模数
端面模数
载荷用于单齿副接触点上的齿根弯曲应力的弯曲力臂
工作节直径
齿轮根圆直径
分度圆直径
齿顶高
齿轮齿顶高修正系数
齿根高
端面径节
法向基节
齿轮齿数
齿轮直齿当量齿数
配对齿轮间的中心距
转动平面的接触长度
在临界部位齿轮的齿根圆弧半径
轴向导程修正或导程失配(如有,供参考)
轮齿切削及精加工方法
齿厚修正系数(中间面)
基准齿条齿形图
根圆半径、基准齿条的齿顶高及齿根高
齿侧光洁度
精确度
轮齿硬度范围,包括芯部硬度,从表面至芯部的总淬硬深度
齿根过渡圆弧的峰谷平均粗糙度
转动件质量
花键参数
轮缘与毂的收缩公差
原动机与减速齿轮间的联接方式
制造商推荐润滑油的种类及粘度
完整的参数表,见附录4-3-1A3
1.5.4材料
应提交以下齿轮材料的主要性能
化学成份
室温下物理性能
抗点蚀性、接触应力与齿根弯曲应力的耐久极限
齿轮、联接元件、轴、主轴及外壳的热处理
1.5.5淬硬过程
表面淬硬齿轮的淬硬过程应提交审核。
提交内容应包括材料,硬化程序细节,质量保证程序及测试程序。
测试程序应包括表面硬度,表面淬硬深度及芯部硬度。
其中表面淬硬深度和芯部硬度(及它们形状)由试样剖面确定。
试样必须达到足够尺寸以确定芯部硬度,并且必须与它们所代表的齿轮一样采用相同材料,经过相同的热处理。
按第2-4-1测试锻件。
1.5.6计算与分析
轴承寿命计算
齿式联轴节与花键连接计算
3.材料
3.1材料规格与测试要求
3.1.1材料证明书
齿轮及齿轮装置所用材料,必须符合各项设计所要求的规格。
材料规格及采购合同的复本应提交给检查员。
3.1.2材料测试
除4-3-1/3.3节中另作说明的外,以下材料必须经过检查员在场并监管的测试。
材料应符合第4章第2部分的要求或该项设计的要求。
齿轮装置、轴、联轴节、联接螺栓的锻件。
允许代替上述锻件