模具数控加工课程设计样稿Word格式.docx
《模具数控加工课程设计样稿Word格式.docx》由会员分享,可在线阅读,更多相关《模具数控加工课程设计样稿Word格式.docx(9页珍藏版)》请在冰豆网上搜索。
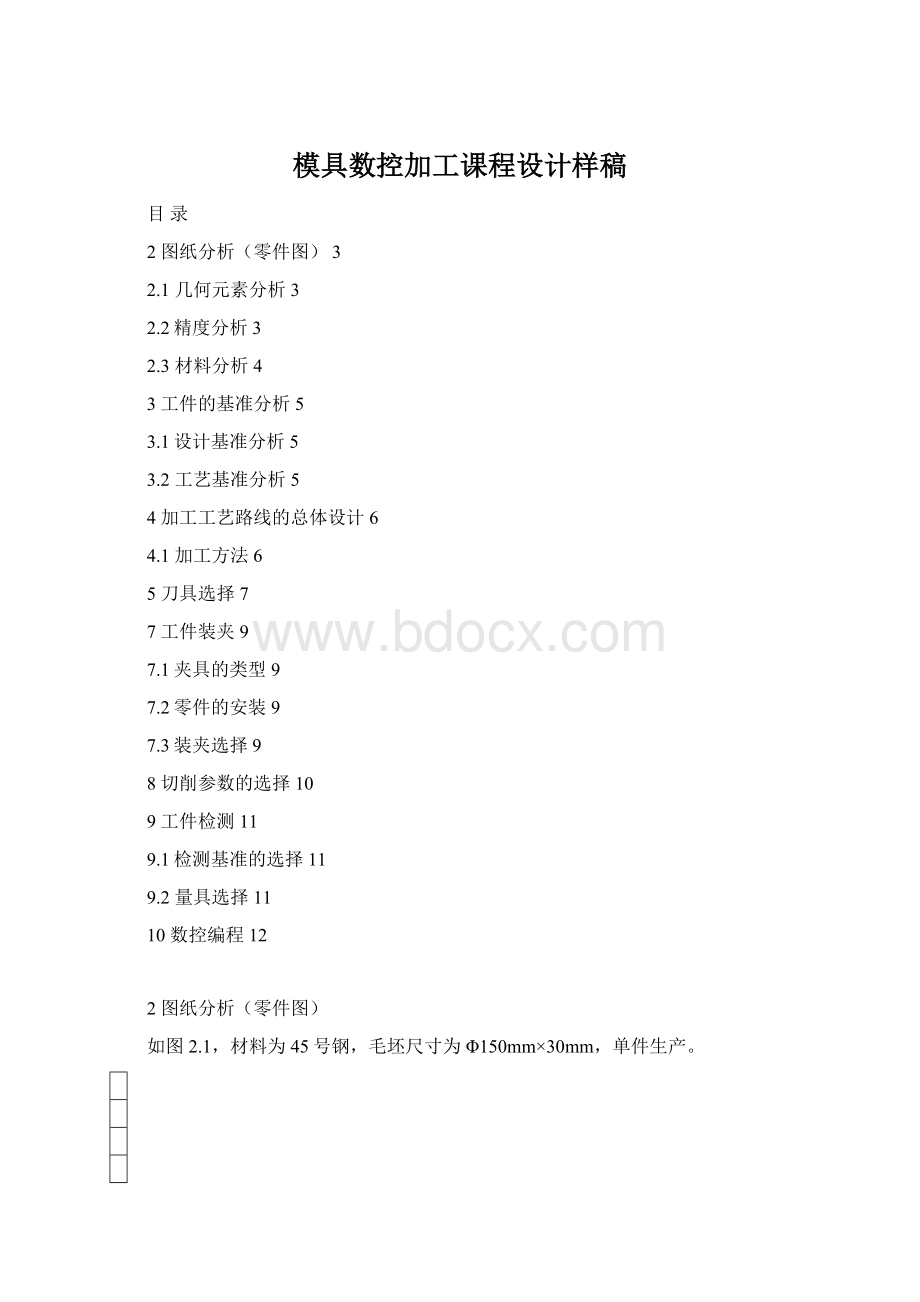
2.2精度分析
加工精度是指零件加工后的实际几何参数(尺寸、形状和位置)与理想几何参数的符合程度。
在加工过程中有很多因素影响加工精度:
1.机床的几何误差包括主轴回转误差和导轨误差,2.刀具的几何误差
,3.夹具的几何误差,4.定位误差,5.工艺系统受力变形引起的误差,6.工艺系统受热变形引起的误差,7.内应力重新分布引起的误差。
卸料板在精密模具中是一套模具的精度中心,有卸料之作用并在冲裁压料以防止料带变形,所以要求精确定位,被加工部分的各尺寸和形位公差、表面粗糙度要求较高,部分尺寸达IT8~IT7级精度。
2.3材料分析
材料对外力作用所具有的抵抗能力,称为材料的机械性能。
板料的性质不同,机械性能也不一样,表现在冲压件工艺过程的冲压性能也不一样。
材料的主要机械性能有:
塑性、弹性、屈服极限、强度极限等,这些性能也是影响冲压性能的主要因素。
卸料板与凹模间的材料接触面,长时间冲压产生压痕,当压痕严重时,会影响材料的压制精度,造成产品尺寸异常、不稳定等,需对料板镶块和卸料板进行维修或重新研磨,因此对卸料板的材料要求也是很严格的。
应采用45钢制造,调质热处理,淬火硬度为40~45HRC,适合数控车床加工。
3工件的基准分析
3.1设计基准分析
在制定零件的加工方案时,首先要选择最佳的精基准来进行加工中心加工。
这就要求在粗加工时,考虑以怎样的粗基准把精基准的各面加工出来,即加工中心上使用的各个定位基准应在前面普通机床或加工中心工序中加工完成,这样容易保证各个工位加工表面相互之间的精度关系,该工件为轴类零件,为加工方便尽量选择零件上的设计基准作为定位基准,因此设计基准为工件的中心线最为合适。
3.2工艺基准分析
工艺基准是在工艺过程中所使用的基准。
工艺基准是在加工,测量和装配时所使用的,必须是实在的。
然而作为基准的点、线、面有时并不一定具体存在(如孔和外圆的中心线,两平面的对称中心面),往往通过具体的表面来体现,用以体现基准的表面称为基面。
因此根据工件的外形特征和加工方法,因选择外圆表面作为基面A面。
如图3.1所示。
图3.1卸料板的基准
4加工工艺路线的总体设计
4.1加工方法
根据工件的几何元素要求,本工件的加工方法包括车端面、车外圆、内孔加工、攻螺纹加工。
4.2加工工序
按照铣削加工的工艺原则,工件的加工工艺路线如图4.1所示:
4.2.1基准面(A面)加工
4.2.2车Φ140外圆
4.2.3加工Φ24.2孔
4.2.4以A面为基准面切断长度为12
4.2.5钻Φ5的孔
4.2.6攻螺纹M6
外轮廓加工路线参见图1-4
3
图4.1凹模的加工工序
5刀具选择
刀具的选择是在数控编程的人机交互状态下进行的。
应根据机床的加工能力、工件材料的性能、加工工序、切削用量以及其它相关因素正确选用刀具及刀柄。
刀具选择总的原则是:
安装调整方便、刚性好、耐用度和精度高。
在满足加工要求的前提下,尽量选择较短的刀柄,以提高刀具加工的刚性。
刀具的选用与工件几何特征、加工方法、加工精度、材料等因素相关。
上下表面用端面车刀,外轮廓车削用外圆车刀,内孔用内孔车刀车削,用线切割加工内齿轮。
从外轮廓几何元素看,所选车刀为600外圆车刀,加工内孔时,内孔刀伸出3~4cm。
工件材料为45号钢,刀具材料用高速钢即可。
表5.1卸料板的刀具选用表
零件名称
卸料板
零件材料
45钢
零件图号
机床名称
数控车
序号
刀具号
刀具名称
刀具规格
刀补地址
刀具材料
长度
半径
1
T0101
端面刀
高速钢
2
T0202
内孔刀
T0303
外圆刀
4
麻花钻
φ15
5
T0404
切断刀
宽4mm
6
钻头
φ5
7
攻丝
M6
6刀路设计
6.1刀路的选择
CNC加工的刀具路径是指:
加工过程中,刀具刀位点相对于工件运动轨迹和方向。
刀具路径一般包括:
从起始点快速接近工件加工部位,然后以工进速度加工工件结构,完成加工任务后,快速离开工件,回到某一设定的终点。
可归纳为两种典型的运动:
点到点的快速定位运动——空行程;
工作进给速度的切削加工运动——切削行程。
确定加工路线的原则主要有以下几点:
1、规划安全的刀具路径,保证刀具切削加工的正常进行。
2、规划适当的刀具路径,保证加工零件满足加工质量要求。
3、规划最短的刀具路径,减少走刀的时间,提高加工效益。
因此车削外圆零件时,一般采用外圆车刀刀尖进行切削。
由于要控制左右两个外圆表面精度,防止出现接刀痕,采用一次完成外圆表面,再切断。
7工件装夹
7.1夹具的类型
数控车床上夹具主要有两类:
一类用于盘类或短轴零件,工件毛坯装夹在可调卡爪的卡盘(三爪、四爪)中,由卡盘传动旋转;
另一类用于轴类零件,毛坯装在主轴顶尖和尾座顶尖间,工件由主轴上的拨动卡盘转动传动旋转。
7.2零件的安装
数控车床上零件的安装方法与普通车床一样,要合理选择定位基准和夹紧方案,主要注意以下两点:
(1)力求设计、工艺与编程计算的基准统一,这样有利于提高编程时数值计算的简便性和精确性。
(2)尽量减少装夹次数,尽可能在一次装夹后,加工出全部待加工面。
7.3装夹选择
根据工件的外形特征加工方法,工件采用三爪卡盘装夹,试切法对刀。
8切削参数的选择
合理选择切削用量,可以充分发挥机床的功率、机床的运动参数、冷却润滑系统、操作系统的功能,可以充分发挥刀具的硬度、耐磨性、耐热性、强度及刀具的几何参数等切削性能可以提高产品的加工质量、效率,降低加工成本,确保生产操作安全。
刀具材料的性能包括:
硬度、耐磨性、耐热性、抗弯强度和抗粘结性等。
不同的刀具材料,其硬度、耐热性、抗弯强度也不同,所允许的切削速度也不同。
详见下表。
该工件材料为45号钢,硬度较高,切削力大,粗车厚度除留精加工余量外,分刀切完。
根据刀具材料和工具材料,选择切削速度为280mm/min,则转速n=1000v/πD。
经计算,粗加工转速取1350r/min,F0.25;
精加工转速取1850r/min,F0.1。
被吃刀量2.5mm。
9工件检测
9.1检测基准的选择
检测基准是测量工件的形状、位置和尺寸误差时采用的基准。
如图2-1,零件是以中心轴线为测量基准。
9.2量具选择
轮廓尺寸用千分尺和游标卡尺测量,深度尺寸用游标卡尺测量,表面质量用表面粗糙度样板检测,用百分表校正平口钳及工件上表面垂直度和平面度。
表9.1量具选用表
量具名称
规格
说明
游标卡尺
0~150mm
精度0.02mm
10数控编程
表10.1卸料板加工参考程序
刀具
外圆车刀(加工左面程序)
程序段号
数控程序
程序注释
o0003
程序号
N10
G99M03S800T0101F0·
主轴正转
N20
G00X157Z2
找定位点
N30
X155Z-10
加工外圆
N40
X157
N50
G00X200Z100
退刀
N60
M30
结束
N70
立铣刀
o0004
G91G28GOZO
G90G40G54M03S800
G00X0Y0
定位
G43Z50H01
刀具补偿
Z10
下刀
G01Z-2F80
G41X12·
1D01
加刀补
N80
G03I12·
加工圆
N90
X0Y-12·
1R12·
N100
X40G01YO
取消刀补
N110
G0Z100
抬刀
N120
附录
附录A卸料板工序卡
卸料板工序卡
共1页
设备名称
数控车,钻床,
数控系统
FANUC0i
第1页
材料
硬度
毛坯种类
工序内容
切削用量
量具
45
HRC20
棒料
N(r/min)
f(mm/min)
αp
(mm)
编号
车基准端面A
1350
200
车Φ140外圆
280
2.5
60度
加工Φ24.2孔
1850
140
切断长度12
500
手动
厚4mm
钻孔
攻螺纹
丝攻
签字
陈磊
日期
2010.04