粉末冶金复习Word文档下载推荐.docx
《粉末冶金复习Word文档下载推荐.docx》由会员分享,可在线阅读,更多相关《粉末冶金复习Word文档下载推荐.docx(16页珍藏版)》请在冰豆网上搜索。
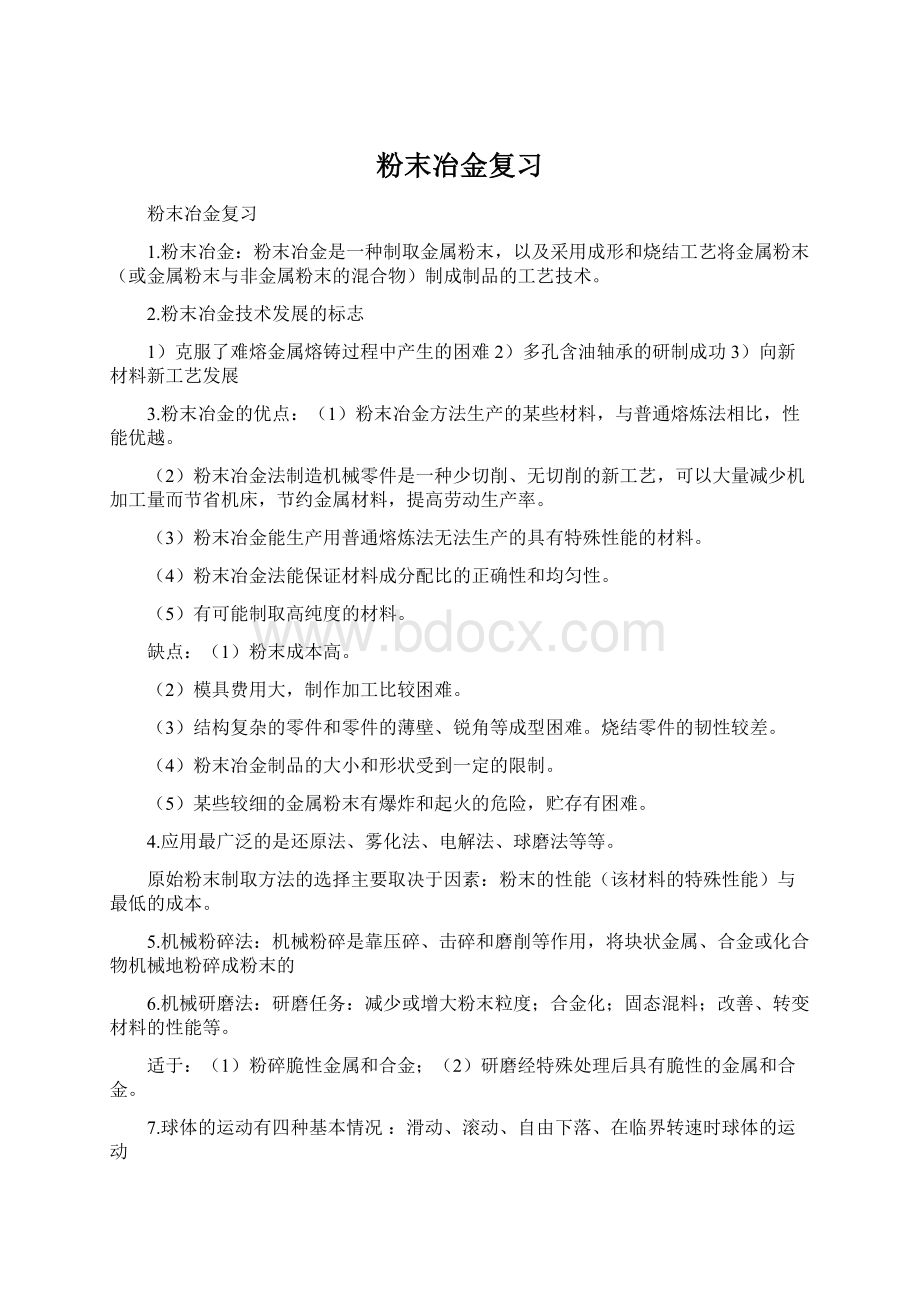
β临界称为自然坡度角
8.影响球磨的因素
(1)球磨筒
A、球磨筒的转速:
n=(0.7~0.75)n临界,球体发生抛落;
适于较粗、性脆,需要冲击作用的物料;
n=0.6n临界时,球体滚动;
用来研磨较细物料;
n<
0.6n临界时,球以滑动为主;
研磨作用很小。
B、球磨筒尺寸:
可选用D/L>
3的球磨机可保证球体发生冲击作用,研磨硬而脆的材质,;
当D/L<
3时,只发生摩擦作用,此时适于研磨塑性的材质。
(2)装球量
装球量过少,球在倾斜面上主要是发生滑动,使研磨效率降低;
装球量过多,球层之间干扰大,破坏球的正常循环,也会研磨效率降低。
一般球磨机的装填系数为0.4~0.5为宜;
随着转速增大,装填系数可略有增加。
(3)球料比
料太少:
则球与球之间碰撞加多,磨损太大;
料过多:
则磨削面积不够,不能很好的磨细粉末,需要延长研磨时间,能量消耗增大。
一般在球体的装填系数为0.4~0.5时,装料量以填满球间的空隙,稍掩盖住球体表面为原则。
(4)球的大小和材质:
球太小,质量轻,对物料的冲击力弱;
球太大,则装球的个数太少,因而撞击次数减少,磨削面积减小,也使球磨效率降低。
一般大小不同的球配合使用,球的直径d按球筒直径D的(1/18~1/24)范围选择:
另外,物料的原始粒度愈大,材料愈硬,则选用的球也应愈大;
球磨铁粉,选用10~20mm的钢球;
球磨硬质合金,选用5~10mm的硬质合金球。
(5)研磨介质
干磨、湿磨,应根据物料要求选择。
湿磨,在硬质合金、金属陶瓷及特殊材料的研磨工艺中常被采用。
(6)被研磨物料的性质:
脆性的物料虽然硬度大,但可很快被粉碎;
较塑性的物料虽然硬度小,但却难粉碎;
有些塑性物料要先进行人工脆化,再粉碎。
7)研磨时间:
若要求物料最终粒度愈细时,则需要的研磨时间愈长;
存在着极限研磨的颗粒大小。
研磨时间一般是几小时到几十小时,很少超过100小时。
9.冷气流粉碎的基本工艺:
利用高速高压的气流带着较粗的颗粒通过喷嘴轰击于靶子上,压力立即从高压(高达7MPa)降到0.1MPa,发生绝热膨胀,使金属靶和击碎室温度降到室温以下甚至零度以下,冷却了的颗粒就被粉碎。
10.冷气流粉碎适于:
粉碎硬质的以及比较昂贵的材料,对粉碎塑性金属和合金,如不锈钢、合金钢、超合金等效果都很好。
冷气流粉碎特点:
随气流压力增加,粉末粒度愈细;
粉末通常颗粒细(微米级)而均匀、形状不规则,几乎无氧化;
简单,生产费用低;
作业温度低(防止氧化),能保持高纯度以及能控制被粉碎材料的粒度)。
11.二流雾化:
借助高压水流或气流冲击破碎液流获得粉末
1)雾化过程原理:
克服液体金属原子间的结合力而成粉末的。
2)喷射流的主要作用是:
a.把熔融液流击碎成小颗粒(动力源)
b.通过急冷使颗粒凝固(冷却剂)
12.金属液流在气流作用四个区域
(1)负压紊流区
(2)原始液滴形成区
(3)有效雾化区
(4)冷却凝固区
13.喷嘴结构的设计要求:
a、使雾化介质获得尽可能大的出口速度和所需要的能量;
b、保证雾化介质与金属液流之间形成最合理的喷嘴角度;
c、使金属液流产生最大的能量;
d、工作稳定性好,喷嘴不易堵塞;
e、加工制造简单。
14.影响二流雾化性能的因素
A雾化介质
(1)雾化介质类别
气体:
1)氧化不严重或雾化后经还原处理可脱氧的金属,可采用空气作雾化介质;
2)易于氧化金属或合金粉末可采用惰性气体
水:
冷却能力强,粉末多为不规则形状;
不适于活性很大的合金或金属。
适于易被还原的金属或合金
(2)气体或水的压力:
气压愈高,所得粉末愈细,
B金属液流
(1)金属液的表面张力和粘度
表面张力越小,粘度越低,所得粉末颗粒越细;
表面张力愈大,粉末成球形越多,粉末粒度也越粗;
表面张力、粘度受加热温度和化学成分影响,金属强烈氧化时,粘度大大提高。
(2)金属液过热温度
金属液过热温度愈高,越易得细、球形粉末
(3)金属液流直径
越细,细粉末越多;
但太小,会降低雾化粉末生产率,堵塞漏嘴,使金属液过冷,不易得细粉末。
有时还要考虑金属熔点的高低。
通常熔点小于1000℃,金属液流直径5-6mm;
通常熔点小于1300℃,金属液流直径6-8mm;
通常熔点大于1300℃,金属液流直径8-10mm;
C其它工艺因素
(1)喷射参数:
金属液长度短,喷射角适当。
(2)聚粉装置参数:
液滴飞行路长,利于形成球形,粉末也较粗
15.还原法:
用还原剂还原金属氧化物和盐类来制取粉末的方法。
16.还原法中,反应速度与时间的关系具有吸附自动催化的特点。
其曲线的三个阶段:
第一阶段(诱导期):
反应速度很慢,还原仅在固体氧化表面的某些活化质点上开始,新相形成有很大困难。
第二阶段(反映发展期):
当新相一旦形成,由于新旧界面上力场不对称,较易吸附气体还原剂和晶格重新排列,因此反应就沿着新旧相的界面逐渐扩展,反应面逐渐扩大,反应速度也不断增加。
第三阶段(减速区):
由于反应沿着以新相晶核为中心而逐渐扩大到相邻反应面,然后反应面随着过程的进行不断减小,引起反应速度的降低。
17.影响还原过程和铁粉质量的因素
(1)原料a.原料中杂质的影响 Si02的含量超过一定限度后,不仅还原时间延长,并且使还原不完全,铁粉中含铁量降低。
矿石作原料都要磁选,一般要求铁鳞中Fe总>70%~73%,SiO2<0.25%~0.30%
b.原料粒度的影响 原料粒度愈细,促进反应的进行。
原料在准备中一般都要粉碎。
(2)固体碳还原剂a.固体碳还原剂类型的影响 常用的固体碳还原剂有木炭、焦炭和无烟煤。
木炭的还原能力最强,其次是焦炭,而无烟煤则较差。
使用焦炭和无烟煤时,要加入适量的脱硫剂,如石灰石、石灰以除去其中的硫。
b.固体碳还原剂用量的影响 主要根据氧化铁的含氧量而定。
木炭加入量为86%~90%,
用无烟煤还原时,配碳比取铁鳞:
无烟煤:
石灰石=60%:
33%:
7%
(3)还原工艺条件a.还原温度和还原时间的影响 在一定范围内随着还原温度的提高,还原时间可以缩短。
随着温度的升高,海绵铁高温烧结趋向增大,这使CO难以通过还原产物扩散,减低还原速度,同时,海绵铁高温烧结使得海绵铁块变硬,,将造成下一步粉碎困难,使铁粉加工硬化更大。
b.料层厚度的影响 随着料层厚度的增加,还原时间亦随之增长。
c.还原罐密封程度的影响 密封不好,往往还原不透,或者使海绵铁在冷却过程中容易氧化。
(4)添加剂a.加入一定的固体碳的影响生产上常采用分层相间的加入法,同时再在原料中加入一定的固体碳,起疏松剂和辅助还原剂的作用。
b.返回料的影响 往原料中预先加入一定的废铁粉,缩短还原过程的诱导期,增加反应活性。
c.引入气体还原剂的影响 使还原过程加速,同时所得海绵铁比较疏松,质量也比较高。
d.碱金属盐的影响 能加速还原过程
(5)海绵铁的处理 退火软化作用、补充还原作用、脱碳作用
18.氢铁还原法的特点
a.采用较低的还原温度和较高的压力。
b.可利用粉矿。
c.所得铁粉很纯,很适于生产粉末冶金铁基零件。
d.所用的氢是将转化天然气中CO转化为CO2除去后的转化氢。
e.可吸收部分固体颗粒和氢气
19.金属热还原剂满足条件
(1)还原反应所产生的热效应较大,希望还原反应能依靠反应热自发地进行。
(2)还原过程中形成的渣以及残余的还原剂应该容易与所得的金属分离开来。
(3)还原剂与被还原金属不能形成合金或其他化合物。
20.其他制取粉末方法
气相沉积法包括:
金属蒸气冷凝、羰基物热离解、气相还原、化学气相沉积。
气相还原包括气相氢还原和气相金属热还原。
羰基物热离解法就是离解金属羰基化合物而制取金属粉末的方法。
化学气相沉积(CVD)是从气态金属卤化物还原化合沉寂制取难熔化合物粉末和各种涂层的方法。
液相沉淀法包括:
金属置换法;
溶液气体还原法;
从熔盐中沉淀法;
辅助金属浴法。
金属置换法原理:
用负电位交大的金属去置换溶液中真点位较大的金属,置换次序取决于电位差。
溶液氢还原法:
用气体从溶液中还原金属盐溶液制取金属粉末的方法。
液相共沉淀法制取粉末方案:
1)使基体金属和弥散相金属验或氢氧化物在某种溶液中同时析出达到均匀分布,然后经过干燥、分解、还原过程以得到基体金属和弥散相化合物。
2)将弥散相制成最终粒度,然后悬浮在含基体金属的水溶液中作为沉淀结晶的核心。
电解法主要采用水溶液电解和熔盐电解。
熔盐电解:
由于难熔金属与氧的亲和力大,不能从水溶液中析出,使用熔盐做电解质,在低于熔点下电解。
21.粉末体:
粉末体是由大量颗粒及颗粒之间的空隙所构成的集合体。
单颗粒:
粉末中能分开并独立存在的最小实体成为单颗粒
22.粉末的性能
(1)单颗粒的性质
a.由粉末材料所决定的性质,如点阵构造、固体密度、熔点、塑性、弹性、电磁性质、
化学成分等。
b.由粉末生产方法所决定的性质,如粒度、颗粒形状、有效密度、表面状态、晶粒结构、点阵缺陷、颗粒内气体含量、表面吸附的气体与氧化物、活性等。
(2)粉末体的性质 除了单颗粒的性质以外,还包括:
平均粒度、粒度组成、比表面、
松装密度、摇实密度、流动性、颗粒间的摩擦状态。
(3)粉末的孔隙性质 总孔隙体积、颗粒间的孔隙数量和体积、平均孔隙大小、孔隙大小的分布及孔隙形状。
23.粉末的化学成分、物理性能和工艺性能
金属粉末的化学成分应包括主要金属的含量和杂质的含量。
物理性能
粉末的物理性能包括:
颗粒形状与结构,颗粒大小和粒度组成,比表面积,颗粒的密
度、显微硬度,光学和电学性质,熔点、比热容、蒸气压等热学性质,由颗粒内部结构决
定的射线、电子射线的反射和衍射性质,磁学与半导体性质等。
工艺性能
粉末的工艺性能包括松装密度、振实密度、流动性、压缩性与成形性。
工艺性能也主
要取决于粉末的生产方法和粉末的处理工艺(球磨、退火、加润滑剂、制粒等)。
24.粉末中杂志包括:
1)与主要金属结合,形成和固溶体或化合物的金属或非金属成分;
2)从原料和从粉末生产过程中带入的机械夹杂;
3)粉末表面吸附的氧、水蒸气和其他气体;
4)制粉工艺引进的杂质
菲水滴定法是将含有金属氧化物的金属粉末试样置于纯净、干燥的氢气流中加热,金属氧化物与氢反应生成的水用试剂滴定,从而确定氧的含量。
25.粉末的比表面:
粉末的比表面定义为1g质量粉末所具有的总表面积。
松装密度:
松装密度是粉末试样自然地充满规定的容器时,单位容积的粉末质量。
振实密度:
指将粉末装入容器中,在规定的条件下经过振实后所测得的粉末密度。
拱桥效应:
粉末在松裝位移时,由于表面不规则,彼此之间有摩擦颗粒互相搭架而形成搭桥孔洞的现象。
粉末的流动性是指50g粉末从标准的流速漏斗流出所需的时间
压缩性:
压缩性就是金属粉末在规定的压制条件下被压紧的能力。
成形性:
成形性是指粉末压制后,压坯保持既定形状的能力。
26.影响松装密度和振实密度的因素
a.粉末颗粒形状越规则,其松装密度越大;
颗粒表面越光滑,松装密度也越大。
b.粉末颗粒越粗大,其松装密度越大。
c.粉末颗粒越致密,松装密度越大
d.粉末粒度范围窄的粗细粉末,松装密度都较低
27.粉末冶金成形是将松散的粉末体加工成具有一定尺寸、形状、以及一定密度和强度的坯块工艺过程。
成形分普通成形和特殊成形两大类。
28.成形前原料准备的目的是要制备具有一定化学成分和一定粒度,以及适合的其它物理化学性能的混合料。
预处理包括:
粉末退火、筛分、混合、制粒、加润滑剂等。
29.退火的目的
a.软化作用,消除粉末的加工硬化,稳定粉末的晶体结构,提高塑性,改善压缩性;
b.补充还原作用,使氧化物还原,提高粉末的纯度;
c.降低碳和其它杂质的含量;
d.为了防止某些超细金属粉末的自燃,需要将其表面钝化
30.A混合
混合一般是指将两种或两种以上不同成分的粉末混合均匀的过程。
混合有机械法和化学法两种
B筛分
筛分的目的在于把不同颗粒大小的原始粉末进行分级,而使粉末能够按照粒度分成大小范围更窄的若干等级。
C制粒是将小颗粒的粉末制成大颗粒或团粒的工序,常用来改善粉末的流动性。
31.选择成形剂、润滑剂的基本条件是:
1)有较好的粘结性和润滑性能,在混合粉末中容易均匀分散,且不发生化学变化。
2)软化点较高,混合时不易因温度升高而熔化。
3)混合粉末中不致于因添加这些物质而使其松装密度和流动性明显变差,对烧结体
特性也不能产生不利影响。
4)加热时,从压坯中容易呈气态排出,并且这种气体不影响发热元件、耐火材料的
寿命。
32.压坯强度是指压坯反抗外力作用保持其几何形状和尺寸不变的能力。
弹性后效:
在压制过程中,当除去压制压力并把压坯压出压模之后,由于内应力的作用,压坯发生弹性膨胀,这种现象称为弹性后效。
侧压力:
粉末体在压模内受压时,压坯会向周围膨胀,模壁就会给压坯一个大小相等方向相反的反作用力,模壁施加于压坯的侧面压力称为侧压力。
33.压制压力作用在粉末体上之后分为两部分,一部分是用来使粉末产生位移、变形和克
服粉末的内摩擦,这部分力称为净压力;
另一部分,是用来克服粉末颗粒与模壁之间外摩擦的力,这部分力称为压力损失。
34.弹性膨胀现象的原因是:
粉末体在压制过程中受到压力作用后,粉末颗粒发生弹塑性变形,从而在压坯内部聚集很大的内应力——弹性内应力,其方向与颗粒所受的外力方向相反,力图阻止颗粒变形。
当压制压力消除后,弹性内应力便要松弛,改变颗粒的外形和颗粒间的接触状态,这就使粉末压坯发生了膨胀。
35.金属粉末压制时压坯密度的变化规律
第一阶段:
滑动阶段,在这阶段内,由于粉末颗粒发生位移,填充孔隙,因此当压力稍有增加时,压坯的密度增加很快;
第二阶段:
第一阶段压缩后其密度已达到一定值,粉末体出现了一定的压缩阻力。
在此阶段内,压力虽然继续增加,但压坯密度增加很少;
第三阶段:
当压力超过一定值后,压坯密度又随压力增加而继续增大,然后又平缓下来。
36.影响压坯密度分布的因素
压力损失是在普通钢模压制过程中造成压坯密度分布不均匀的主要原因。
1)增加压坯的高度会使压坯各部分的密度差增加;
而加大直径则会使密度的分布更加均匀。
高径比越大,密度差越大。
2)采用模壁光洁度很高的压模并在模壁上涂润滑油,能够减少外摩擦系数,改善压坯的密度分布。
3)压坯中密度分布的不均匀性,在很大程度上可以用双向压制法来改善。
4)为了使压坯密度分布得更加均匀,除了采用润滑剂和双向压制外,还采用利用摩擦力的压制方法。
37.为了使压坯密度分布尽可能均匀,生产上可以采取下列行之有效的措施:
1)压制前对粉末进行还原退火等预处理,消除粉末的加工硬化,减少杂质含量,提高粉末体的压制性能。
2)加入适当的润滑剂或成形剂,如铁基零件的混合料中加硬脂酸锌、机油、硫等。
3)改进加压方式,当H/D≤1而H/δ≤3时,可采用单向压制;
当H/D>1而H/δ>3时,则需采用双向压制;
当H/D>4~10时,要采用带摩擦芯杆的压模或双向浮动压模、引下式压模等。
4)改进模具构造或者适当变更压坯形状,使不同横截面的连接部位不出现急剧的转折;
5)降低粉末与模壁的摩擦系数,减少压力损失,提高压坯的密度均匀性。
38.A外摩擦力对压制过程的影响
1)由于外摩擦力的方向与压制压力的方向相反,所以它的存在实际上是无益地损耗一部分压力;
2)由于外摩擦力的存在,将引起压制压力的不均匀分布;
3)由于摩擦力的存在,将阻碍粉末体在压制过程中的运动
B减少因摩擦引起的压力损失,可采用添加润滑剂、提高模具光洁度和硬度、改进成型方式等措施。
39.脱模压力使压坯由模中脱出所需的压力称为脱模压力。
它与压制压力、粉末性能、压坯密度和尺寸、压模和润滑剂等有关。
硬质合金物料在大多数情况下:
脱模压力随着压坯高度而增加,在中小压制压力(小于300~400MPa)的情况下,脱模压力一般不超过0.3P。
40.压坯密度分布规律
在任何垂直面上,上层密度都比下层密度要大些。
在水平面上,接近上模冲的断面的密度分布是两边打中间小。
而远离上模冲的截面的密度分布则是中间大两边小。
但是,在靠近模壁的层中,由于外摩擦的作用,轴向压力的降低比压坯中心大得多,以致在压坯底部的边缘密度比中心的密度低。
因此,压坯下层的密度和硬度之分布状况和上层相反。
41.A压制过程中减少摩擦的方法大致有两种:
一种是采用高光洁度的模具或用硬质合金模
代替钢模;
另一种就是使用成形剂或润滑剂。
B使用成形剂的目的
a促进颗粒变形,改善压制过程,降低单位压制力;
b提高压坯强度,减少粉尘飞扬,改善劳动条件;
c提高压坯密度的均匀性,改善压坯表面质量;
d可明显提高压模寿命等等。
C成形剂的选择原则
(1)成形剂的加入不会改变混合料的化学成分;
成形剂在随后的预烧或烧结过程中能全部排除,不残留有害物质;
所放出的气体对人体无害。
(2)成形剂应具有很好的分散性能;
具有较好的粘性和良好的润滑性;
并且易于和粉末料混合均匀。
(3)对混合后的粉末松装密度和流动性影响不大;
除特殊情况外其软化点应当高,以防止混合过程中的温升而熔化。
(4)烧结后对产品性能和外观等没有不良影响。
(5)成本低,来源广
42.成形剂的不足
1)降低了粉末本身的流动性2)成形剂本身需占一定的体积,实际上使得压坯密度减小,不利于制取高密度的制品3)压制过程中因成形剂的阻隔,金属粉末之间的相互接触程度降低,从而降低了某些压坯的强度4)成形剂在烧结前或烧结中排除,因而可能损伤烧结体的外观。
排除出的气体可能影响炉子的寿命,有时甚至污染空气。
5)某些成形剂容易和金属粉末起作用,降低产品的力学性能。
43.A粉末性能对压制过程的影响
a.粉末物理性能的影响
(1)金属粉末的硬度和可塑性对压制过程的影响很大。
软金属粉末在压缩时变形大,粉末颗粒之间的接触面积增大,压坯密度容易提高。
但是,塑性差的硬金属粉末在压制时必须利用成形剂,否则很容易产生裂纹等压制缺陷。
(2)金属粉末的摩擦性能对压模的磨损影响很大。
一般来说,压制硬金属粉末压模的寿命短。
b.粉末纯度的影响粉末纯度越高,压制越容易进行
c.粉末粒度及粒度组成的影响粉末越细,流动性越差,在填充狭窄而深长的模腔时就越困难,越容易形成拱桥效应,压力损失随之增大,影响了压坯密度的均匀分布
d.粉末颗粒形状的影响表面平滑规则的、接近球形粉末的流动性好,易于充填模腔,使压坯密度分布均匀
e.粉末松装密度的影响松装密度大时,模具的高度及模冲的长度可以缩短
B成形剂对压制过程及压坯质量的影响
为了改善粉末的成形性、塑性、增加压坯强度等,均需加入成形剂。
润滑剂的加入可降低粉末颗粒与模壁和模冲间的摩擦,能有效地改善密度分布,降低脱模压力等。
C压制方式对压制过程和压制质量的影响
a.加压方式的影响
为了减少由于有压力损失,压坯密度出现不均匀的现象,可采用双向压制(如浮动阴模压制)及多向压制(等静压制),或者改变压模结构等。
对于形状复杂的零件,压制时为了使各处的密度分布均匀,可采用组合模冲。
某些难熔金属化合物的压制,有时为了保证密度要求,还可采用换向压制的方法
b.加压速度的影响
压制过程中的加压速度不仅影响到粉末颗粒间的摩擦状态和加工硬化程度,而且影响到空气从粉末颗粒的孔隙中的逸出情况。
如果加压速度快,空气逸出就困难。
因此,通常的压制过程均是以静压(缓慢加压)状态进行的。
c.加压保持时间的影响
粉末压制过程中,如果在某一特定压力下保持一定的时间,往往等到非常好的效果。
这对于形状复杂或体积较大的制品来说更为重要。
保压的理由
(1)是压力传递的充分,进而用利于压坯中各部分的密度均匀。
(2)使粉末孔隙中的空气有足够的时间通过模壁和模冲和芯棒之间的缝隙逸出。
(3)给粉末之间的机械啮合和变形以时间,有利于应变弛豫的进行。
d.振动压制的影响
e.磁场影响
44.压坯废品分析
1)分层,因压制力过大,压坯密度就过高,其弹性后效也就明显增大所致。
凡是弹性后效的因素都影响分层。
2)裂纹,当压坯脱模时中间停顿,压坯脱出部分产生弹性膨胀;
而未脱出部分仍受到压缩,产生压应力,致使压坯产生裂纹。
凡是引起弹性后效不均匀的因素,都会引起裂纹。
3)掉边掉角,主要由于压坯强度和密度不够,或者操作不慎所造成的。
4)压坯密度严重不均和其他废品,密度不均主要原因是操作不慎,装料不均造成。
划伤大多为阴模软或光洁度差的缘故。
毛刺过大和同轴度超差大多数是模具尺寸精度低、配合间隙过大等原因引起。
特殊成形:
等静压成型、三轴压制、粉浆浇注、金属粉末轧制、楔形压制、挤压、高能成形
45.等静压成形优点:
(1)能够压制具有凹形、空心等复杂形状的压件。
(2)粉末体与弹性模具的相对移动很小,摩擦损耗小。
单位压制压力较钢模压制法低。
(3)能够压制各种金属粉末及非金属粉末。
压制坯件密度分布均匀,对难熔金属粉末及其化合物尤为有效。
(4)压坯强度较高,便于加工和运输。
(5)模具材料是橡胶和塑料,成本较低廉。
(6)能在较低的温度下制得接近完全致密的材料。
等静压成形缺点:
(1)对压坯尺寸精度的控制和压坯表面光洁度都比钢模压制法低。
(2)一般地说,生产率低于自动钢模压制法。
(3)所用橡胶塑料具有使用寿命比金属模具要短得多。
46.与熔铸轧制法比较,粉末轧制法的优点是:
1)能够生产一般轧制法难于或无法生产的板带材;
2)能够轧制出成分比较均匀的带材,且成分易于控制,组分分布均匀;
3)粉末轧制的板带材料具有各向同性特点;
4)粉末轧制工艺过程短,节约能源;
5)粉末轧制法成材率高
粉末轧制法生产的带材厚度受轧辊直径限制,受到轧辊宽度的限制;
其次,粉末轧制法只能制取形状较简单的板、带材及直径与厚度比值很大的衬套等。
47.烧结是粉末或粉末压坯,在适当的温度和气氛条件下