年产60万吨煤制甲醇定稿稿Word文件下载.docx
《年产60万吨煤制甲醇定稿稿Word文件下载.docx》由会员分享,可在线阅读,更多相关《年产60万吨煤制甲醇定稿稿Word文件下载.docx(47页珍藏版)》请在冰豆网上搜索。
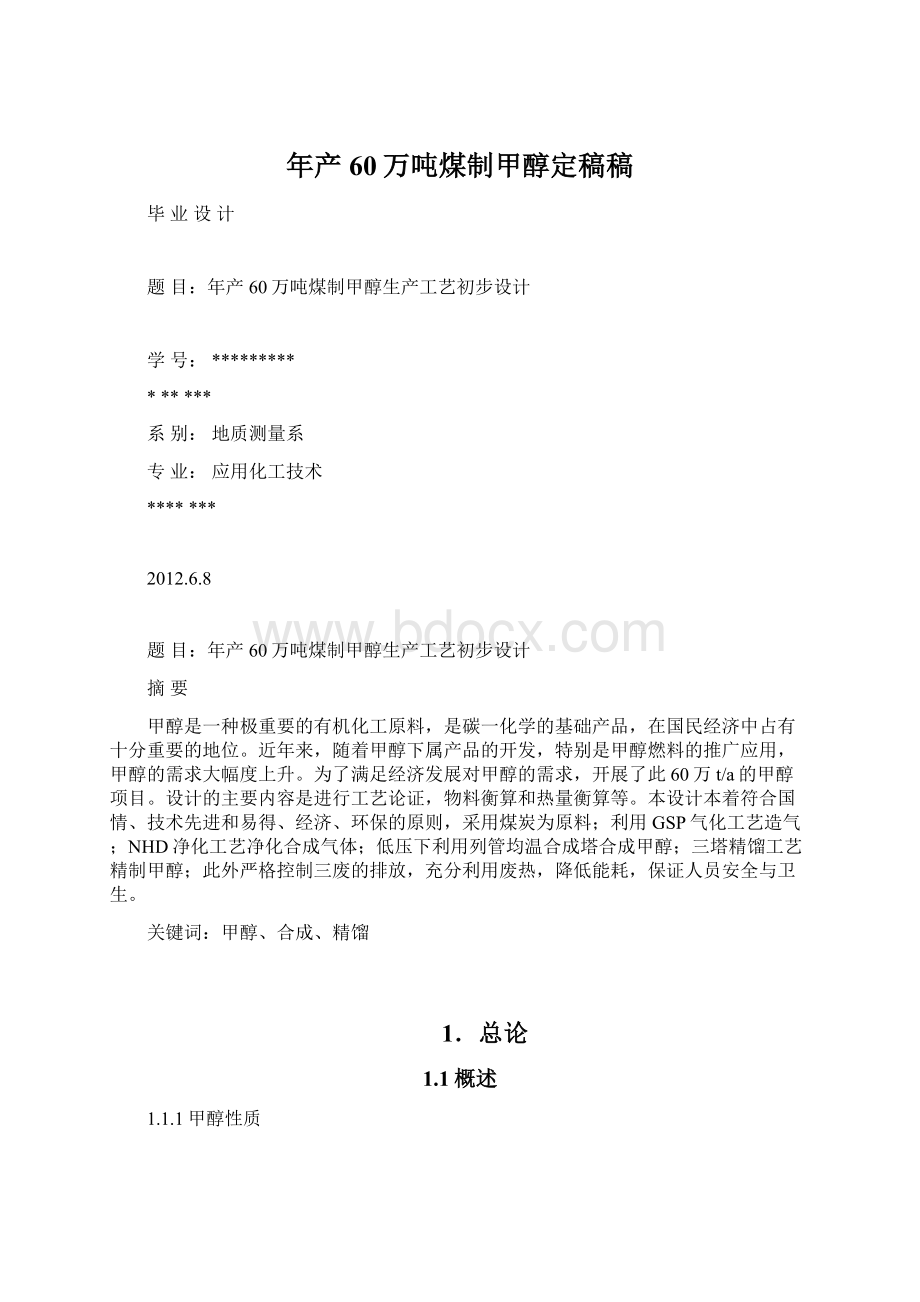
能与水、乙醇、乙醚、苯、酮类和大多数其他有机溶剂混溶。
蒸气与空气形成爆炸性混合物,爆炸极限6.0%~36.5﹪(体积比)。
化学性质较活泼,能发生氧化、酯化、羰基化等化学反应。
1.1.2甲醇用途
甲醇是重要有机化工原料和优质燃料,广泛应用于精细化工,塑料,医药,林产品加工等领域。
甲醇主要用于生产甲醛,消耗量要占到甲醇总产量的一半,甲醛则是生产各种合成树脂不可少的原料。
用甲醇作甲基化试剂可生产丙烯酸甲酯、对苯二甲酸二甲酯、甲胺、甲基苯胺、甲烷氯化物等;
甲醇羰基化可生产醋酸、醋酐、甲酸甲酯等重要有机合成中间体,它们是制造各种染料、药品、农药、炸药、香料、喷漆的原料,目前用甲醇合成乙二醇、乙醛、乙醇也日益受到重视。
甲醇也是一种重要的有机溶剂,其溶解性能优于乙醇,可用于调制油漆。
作为一种良好的萃取剂,甲醇在分析化学中可用于一些物质的分离。
甲醇还是一种很有前景的清洁能源,甲醇燃料以其安全、廉价、燃烧充分,利用率高、环保的众多优点,替代汽油已经成为车用燃料的发展方向之一;
另外燃料级甲醇用于供热和发电,也可达到环保要求。
甲醇还可经生物发酵生成甲醇蛋白,富含维生素和蛋白质,具有营养价值高而成本低的优点,用作饲料添加剂,有着广阔的应用前景。
1.1.4甲醇生产原料
合成甲醇的工业生产是以固体(如煤、焦炭)、液体(如原油、重油、轻油)或气体(如天然气及其它可燃性气体)为原料,经造气、净化(脱硫)变换,除二氧化碳,配制成一定配比的合成气。
在不同的催化剂存在下,选用不同的工艺条件可单产甲醇(分高、中、低压法),或与合成氨联产甲醇(联醇法)。
将合成后的粗甲醇经预精镏脱除甲醚,再精镏而得成品甲醇。
2.工艺流程设计
甲醇合成
合成气净化
煤制合成气
甲醇精馏
图1煤制甲醇的简单工艺流程
首先是采用GSP气化工艺将原料煤气化为合成气;
然后通过变换和NHD脱硫脱碳工艺将合成气转化为满足甲醇合成条件的原料气;
第三步就是甲醇的合成,将原料气加压到5.14Mpa,加温到225℃后输入列管式等温反应器,在XNC-98型催化剂的作用下合成甲醇,生成的粗甲醇送入精馏塔精馏,得到精甲醇。
然后利用三塔精馏工艺将粗甲醇精制得到精甲醇。
2.1煤气化技术路线的选择
煤气化技术按气化反应器的形式,气化工艺可分为移动床(固定床)、流化床、气流床三种。
2.1.1移动床气化
采用一定粒度范围的碎煤(5mm~50mm)为原料,与气化剂逆流接触,炉内温度分布曲线出现最高点,反应残渣从炉底排出,生成气中含有可观量的挥发气。
典型的气化炉为鲁奇(Lurgi)炉。
移动床气化,是目前世界上用于生产合成气的主要方法之一。
在大型煤制甲醇的装置中,固定床的优点是投资低,可是它有很多不足:
(1)对原料煤的黏结性有一定有一定要求:
(2)气化强度低:
(3)环境污染负荷大,治理较麻烦。
2.1.1流化床气化
采用一定粒度分布的细粒煤(<10mm)为原料,吹入炉内的气化剂使煤粒呈连续随机运动的流化状态,床层中的混合和传热都很快。
所以气体组成和温度均匀,解决了固定床气化需用煤的限制。
生成的煤气基本不含焦油,但飞灰量很大。
发展较早且比较成熟的是常压温克(Winkler)炉。
它的缺点是:
(1)在常压或接近于常压下生产,生产强度低、能耗高、碳转化率只有88%~90%。
(2)对煤的气化活性要求高,仅适合于气化褐煤和高活性的烟煤。
(3)缺少大型使用经验;
要在大型甲醇装置中推广,受一定限制。
2.1.3气流床气化
气流床采用粉煤为原料,反应温度高,灰分是熔融状态。
典型代表为GSP,Shell,Texaco气流床气化工艺。
气流床气化优点很多,它是针对流化床的不足开发的。
气流床气化具有以下特点:
(1)采用<
0.2mm的粉煤。
(2)气化温度达1400~1600℃,对环保很有利,没有酚、焦油,有机硫很少,且硫形态单一。
(3)气化压力可达3.5~6.5MPa,可大大节省合成气的压缩功。
(4)碳转化率高,均大于90%,能耗低。
(5)气化强度大。
(6)但投资相对较高,尤其是Shell粉煤气化。
从技术先进性、能耗、环保等方面考虑,对于大型甲醇煤气化应选用气流床气化为宜.从流程分,可分为冷激式流程和废热锅炉流程。
前者在煤气离开气化炉后用激冷水直接冷却,它适合于制造氨气或氢气。
因为这种流程易于和变换反应器配套,激冷中产生的蒸汽可满足变换反应的需要。
后者热煤气是经辐射锅炉,再送往对流锅炉,产生高压蒸汽可用于发电或作热源。
2.1.4GSP工艺技术简介
GSP工艺技术是20世纪70年代末由GDR(原民主德国)开发并投入商业化运行的大中型煤气化技术。
与其他同类气化技术相比,该技术因采用了气化炉顶干粉加料与反应室周围水冷壁结构,因而在气化炉结构以及工艺流程上有其先进之处。
GSP气化技术的主要特点如下:
(1)采用干粉煤(水份含量<
2%)作为气化原料,根据后续化工产品的要求,煤粉可用氮气或一氧化碳输送,故操作十分安全。
由于气化温度高,故对煤种的适应性更为广泛,从较差的褐煤、次烟煤、烟煤到石油焦均可使用,也可以两种煤掺混使用。
对煤的灰熔点的适用范围比其他气化工艺更宽,即使是高水份、高灰分、高硫含量和高灰熔点的煤种也能使用。
(2)气化温度高,一般在1450~1600℃,煤气中甲烷体积分数小于0.1%,(CO+H2)体积分数高达90%以上。
(3)氧耗较低,与水煤浆加压气化工艺相比,氧耗低约15%~20%,可降低配套空分装置投资和运行费用。
(4)气化炉采用水冷壁结构,无耐火材料衬里。
水冷壁设计寿命按25年考虑。
正常使用时维护量很少,运行周期长。
(5)只有一个联合喷嘴(开工喷嘴与生产喷嘴合二为一),喷嘴使用寿命长,为气化装置长周期运行提供了可靠保障。
(6)碳转化率高达99%以上,冷煤气效率高达80%以上。
(7)对环境影响小,气化过程无废气排放。
(8)投资省,粗煤气成本较低。
2.2净化工艺方案的选择
净化工艺包括;
变换、脱硫脱碳、硫回收三个部分。
2.2.1变换工序
以煤为原料制得的粗甲醇原料气必须经过一氧化碳变换工序。
变换工序主要有两个方面的作用:
通过变换调整氢碳比和使有机硫转化为无机硫。
变换工艺主要有:
鲁奇低压甲醇生产中的变换工艺,Tops¢e法甲醇生产中的变换工艺,以及国内的以重油为原料的全气量部分变换工艺。
设计中的变换工艺是一种全新的设计,该工艺采用的是部分气变换。
该工艺的简单流程为:
气化工段来的水煤气首先进入预变换炉,出炉后分为两部分:
一部分进入另一变换炉,变换后经过多次换热和气液分离后去了脱硫系统;
另一部分先进入有机硫水解槽脱硫,出来后气体又分为两部分,部分去调节变换炉出口CO含量,部分去发电系统发电。
2.2.2NHD脱硫脱碳
NHD溶剂的物理性质和应用性能
NHD溶剂主要组分是聚乙二醇二甲醚的同系物,分子式为CH3O(C2H4O)nCH3,
式中n=2~8,平均分子量为250~280。
物理性质(25℃):
密度1.027kg/m3
蒸汽压0.093Pa
表面张力0.034N/m
粘度4.3mPa.s
比热2100J/(kg/K)
导热系数0.18W/(m/K)
冰点-22℃~-29℃
闪点151℃
燃点157℃
综上所述,NHD法脱硫脱碳净化工艺是一种高效节能的物理吸收方法。
且在国内某些装置上己成功应用,有一定的生产和管理经验,本着节约投资、采用国内先进成熟的净化技术这一原则,设计采用了NHD脱硫脱碳净化工艺。
2.3合成甲醇工艺的选择
甲醇合成的典型工艺主要是:
低压工艺(ICI低压工艺、Lurgi低压工艺)、中压工艺、高压工艺。
甲醇合成工艺中最重要的工序是甲醇的合成,其关键技术是合成甲醇催化剂的和反应器,设计采用的是低压合成工艺。
2.3.1甲醇合成塔的选择
甲醇合成反应器实际是甲醇合成系统中最重要的设备。
从操作结构,材料及维修等方面考虑,甲醇合成反应器应具有以下要求:
(1)催化剂床层温度易于控制,调节灵活,能有效移走反应热,并能以较高位能回收反应热;
(2)反应器内部结构合理,能保证气体均匀通过催化剂床层,阻力小,气体处理量大,合成转化率高,催化剂生产强度大;
(3)结构紧凑,尽可能多填装催化剂,提高高压空间利用率;
高压容器及内件间无渗漏;
催化剂装御方便;
制造安装及维修容易。
甲醇合成塔主要由外筒、内件和电加热器三部分组成。
内件事由催化剂筐和换热器两部分组成。
根据内件的催化剂筐和换热器的结构形式不同,甲醇内件份为若干类型。
按气体在催化剂床的流向可分为:
轴向式、径向式和轴径复合型。
按催化剂筐内反应惹得移出方式可分为冷管型连续换热式和冷激型多段换热式两大类。
按换热器的形式分为列管式、螺旋板式、波纹板式等多种形式。
本设计采用了固定管板列管合成塔。
这种合成塔就是一台列管换热器,催化剂在管内,管间(壳程)是沸腾水,将反应热用于副产3.0MPa~4.0MPa的中压蒸汽。
代表塔型有Lurgi公司的合成塔和三菱公司套管超级合成塔,该塔是在列管内再增加一小管,小管内走进塔的冷气。
进一步强化传热,即反应热通过列管传给壳程沸腾水,而同时又通过列管中心的冷气管传给进塔的冷气。
这样就大大提高转化率,降低循环量和能耗,然而使合成塔的结构更复杂。
固定管板列管合成塔虽然可用于大型化,但受管长、设备直径、管板制造所限。
在日产超过2000t时,往往需要并联两个。
这种塔型是造价最高的一种,也是装卸催化剂较难的一种。
随着合成压力增高,塔径加大,管板的厚度也增加。
管板处的催化剂属于绝热段;
管板下面还有一段逆传热段,也就是进塔气225℃,管外的沸腾水却是248℃,不是将反应热移走而是水给反应气加热。
这种合成塔由于列管需用特种不锈钢,因而是造价非常高的一种。
合成塔的选用原则一般为:
反应能在接近最佳温度曲线条件下进行,床层阻力小,需要消耗的动力低,合成反应的反应热利用率高,操作控制方便,技术易得,装置投资要底等。
综上所述和借鉴大型甲醇合成企业的经验,(大型装置不宜选用激冷式和冷管式),设计选用固定管板列管合成塔。
这种塔内甲醇合成反应接近最佳温度操作线,反应热利用率高,虽然设备复杂、投资高,但是由于这种塔在国内外使用较多,具有丰富的管理和维修经验,技术也较容易得到;
外加考虑到设计的是年产60万吨的甲醇合成塔(日产量为1950吨左右),塔的塔径和管板的厚度不会很大,费用也不会很高,所以本设计采用了固定管板列管合成塔。
2.3.2催化剂的选用
XNC-98甲醇合成催化剂简介:
XNC-98型催化剂是四川天一科技股份有限公司研制和开发的新产品。
目前已在国内20多套大、中、小型工业甲醇装置上使用,运行情况良好。
它是一种高活性、高选择性的新催化剂。
用于低温、低压下由碳氧化物与氢合成甲醇,具有低温活性高、热稳定性好的特点。
常用操作温度200~290℃,操作压力5.0~10.0MPa。
催化剂主要物化性质:
催化剂由铜、锌和铝等含氧化合物组成。
外 观:
有色金属光泽的圆柱体
堆积密度:
1.3~1.5kg/L
外型尺寸:
5×
(4.5~5)mm
径向抗压强度:
≥200N/cm
催化剂活性和寿命:
在该催化剂质量检验规定的活性检测条件下,其活性为:
230℃时:
催化剂的时空收率≥1.20kg/(L.h)
250℃时:
催化剂的时空收率≥1.55kg/(L.h)
在正常情况下,使用寿命为2年以上。
表4XNC-98型与C型催化剂的性能对比
催化剂型号
合成塔进口温度
加入量/
(kg.h-1)
甲烷单耗/(t.t-1)
甲纯收率/%
甲纯产率/
(t.m-3.h-1)
甲纯产量/
(t.h-1)
初期
末期
C
210
224
670
0.48
0.45
90.72
XCN-98
200
230
900
0.43
229
0.49
98.93
通过对比,并结合生产实际可见,XCN-98型催化剂具有以下性能优点:
(1)易还原。
(2)低温活性好,日产量高。
75%负荷下的甲醇产量(4.1t/h)接近装置满负荷设计甲醇量(4.17t/h)。
(3)适用温区宽,使用寿命长。
合成塔进口温度可调温C型催化剂为14℃,而XCN-98型则为30℃。
随着可调温区的增加,催化剂的使用寿命也相应延长。
(4)选择性好。
75%负荷下合成系统未发现结蜡,粗甲醇质量符合设计要求。
(5)可适用于含高浓度CO2的合成气。
50%负荷下,C型催化剂CO2加入量最高不超过670kg/h,而XCN-98型催化剂则最高可达900kg/h。
75%负荷时,使用XCN-98型催化剂,当入塔气中CO2组分体积分数高达5%时,生产运行情况仍良好,收率和物耗都较低,催化剂仍能保持较高的活性,产品质量符合质量标准的要求。
综上所述,催化剂的活性、选择性和使用寿命等主要技术经济指标均优于进口催化剂及国产C型催化剂,所以本设计选用四川天一科技股份有限公司研制的XNC-98型催化剂。
2.3.3合成工序工艺操作条件的确定与论证
(1)操作温度
甲醇合成催化床层的操作温度主要是由催化剂的活性温度区决定的。
操作温度的控制同样是一个操作费用的控制问题,在设计中,需要延长催化剂的使用寿命,防止催化剂的迅速老化和活性衰减速度加快。
一般而言,在催化剂的使用初期,反应温度维持较底的数值,随着使用时间的增加,逐步提高反应温度。
例如副产蒸汽型等温甲醇合成塔采用国产铜系催化剂,使用前期,可控制床层零点温度230~240℃,热点温度260℃左右;
后期,可控制床层零点温度260~270℃,热点温度290℃。
设计采用的甲醇合成塔为列管式等温反应器,管间走的是沸腾水,可以副产蒸汽,床层内温差很小,接近最佳温度操作曲线。
设计中采用的甲醇合成催化剂为国产的铜系XCN-98,由它的性质可知:
适合使用的温度范围为200~290℃。
(2)操作压力
压力是甲醇合成反应过程的重要工艺条件之一。
甲醇合成反应时分子数变少,因此增加压力对反应有利,由于压力高,组分的分压提高,因而催化剂的生产强度也提高。
操作压力的选用与催化剂的活性有关。
早期的高压法合成甲醇工艺采用的是锌基催化剂,由于活性差,需要在高温高压下操作,其操作压力为25~35Mpa,操作温度350~420℃。
至较高的压力和温度下,一氧化碳和氢生成甲烷、异丁醇等副产物,这些副反应的反应热高于甲醇合成反应,使床层温度提高,副反应加速,如果不及时控制,回造成温度猛升而损坏催化剂。
近年来普遍使用的铜基甲醇合成催化剂,其活性温度范围在200~300℃,有较高的活性,对于规模小于30万吨/a的工厂,操作压力一般可降为5Mpa左右;
对于超大型的甲醇装置,为了减少设备尺寸,合成系统的操作压力可以升至10Mpa左右。
设采用的是低压法(入塔压强为5.14MPa)合成甲醇。
(3)气体组成
对于甲醇合成原料气,即合成工序的新鲜气,应维持f=(H2-CO2)/(CO+CO2)=2.10~2.15,并保持一定的CO2。
由于新鲜气中(H2-CO2)/(CO+CO2)略大于2,而反应过程中氢与一氧化碳、二氧化碳的化学计量比分别为2:
1和3:
1,因此循环气中(H2-CO2)/(CO+CO2)远大于2。
合成塔中氢气过量,对减少副反应是有利的。
甲醇合成过程中,需要一定的二氧化碳存在以保持催化剂的高活性。
二氧化碳的存在可以降低反应系统的热效应,这对维持床层温度也是有利的。
但是过高的二氧化碳含量会降低合成系统的生产能力,粗甲醇含水增加,增加精馏系统的负荷和能耗。
所以二氧化碳的含量应该尽可能低一些,一般不超过5%。
(4)空速
空速不仅是一个和合成回路气体循环量相关联的工艺控制参数,也是一个影响综合经济效益的变量。
甲醇合成过程中,首先甲醇合成塔内的气体空速必须满足催化剂的使用要求,国产铜基催化剂,一般要求气体空速在8000~20000h-1之间。
空速过低,结炭等副反应加剧,空速过高,系统阻力加大或合成系统投资加大,能耗增加,催化剂的更换周期缩短。
空速的选择需要根据每一种催化剂的特性,在一个相对较小的范围内变化。
XCN-98的空速要求为6000~15000h-1,本设计空速定为12000h-1。
2.4粗甲醇的精馏
在甲醇合成时,因合成条件如压力、温度、合成气组成及催化剂性能等因素的影响,在产生甲醇反应的同时,还伴随着一系列的副反应。
所得产品除甲醇为,还有水、醚、醛、酮、酯、烷烃、有机酸等几十种有机杂质。
由于甲醇作为有机化工的基础原料,用它加工的铲平种类很多,因此对甲醇的纯度均有一定的要求。
甲醇的纯度直接影响下游产品的质量、消耗、安全生产及生产过程中所用的催化剂的寿命。
所以粗甲醇必须提纯。
2.4.1精馏原理
精馏是将沸点不同的组分所组成的混合液,在精馏塔中,同时多次部分气化和多次部分冷凝,使其分离成纯态组分的过程。
其分离的原理如下:
对于由沸点不同的组分组成的混合液,加热到一定温度,使其部分气化,并将气相与液相分离。
因低沸点组分易于气化,则所得气相中低沸点组分含量高于液相中的含量,而液相中高沸点组分含量,较气相中高。
若将气相混合蒸汽再部分冷凝下来,将冷凝液再加热到一定温度,使其部分气化,并将气相与液相分离,则所得气相冷凝液中的低沸点组分又高于原气相冷凝液。
如此反复,低沸点组分不断提高。
道最后制得接近纯态的低沸点组分。
2.4.2精馏工艺和精馏塔的选择
1.甲醇精馏按工艺主要分为三种:
双塔精馏工艺技术、带有高锰酸钾反应的精馏工艺技术和三塔精馏工艺技术。
双塔精馏工艺技术由于具有投资少、建设周期短、操作简单等优点,被我国众多中、小甲醇生产企业所采用。
其在联醇装置中得到了迅速推广。
带有高锰酸钾反应的精馏工艺技术仅在单醇生产中用锌铬为催化剂的产品中有应用。
近年来.随着甲醇合成铜基催化剂的广泛应用和气体净化水平的提高。
粗甲醇生产中的副反应减少和杂质的降低,此工艺流程己经很少采用。
三塔精馏工艺技术是为减少甲醇在精馏中的损耗和提高热利用率,而开发的一种先进、高效和能耗较低的工艺流程。
近年来在大、中型企业中得到了推广和应用。
本设计采用三塔精馏工艺
近年来,许多企业原有甲醇双塔精馏装置己不能满足企业的需要。
随着生产的强化,不仅消耗大幅度上升,而且残液中的甲醇含量也大大超过了工艺指标。
对企业的达标排放构成了较大的威胁。
甲醇三塔精馏工艺技术是为了减少甲醇在精馏过程中的损耗,提高甲醇的收率和产品质量而设计的。
预精馏塔后的冷凝器采用一级冷凝,用以脱除二甲醚等低沸点的杂质,控制冷凝器气体出口温度在一定范围内。
在该温度下,几乎所有的低沸点馏分都为气相,不造成冷凝回流。
脱除低沸点组分后,采用加压精馏的方法,提高甲醇气体分压与沸点,减少甲醇的气相挥发,从而提高了甲醇的收率。
作为一般要求的精甲醇经加压精馏塔后就可以达到合格的质量。
如作为特殊需要,则再经过常压精馏塔的进一步提纯。
生产中加压塔和常压塔同时采出精甲醇,常压塔的再沸器热量由加压塔的塔顶气提供,不需要外加热源。
粗甲醇预热器的热量由精甲醇提供,也不需要外供热量。
因此.该工艺技术生产能力大,节能效果显著,特别适合较大规模的精甲醇生产。
图3三塔工艺流程
1预精馏塔2加压精馏塔3常压精馏塔
2.精馏塔的选择
精馏塔市粗甲醇精馏工序的关键设备,它直接制约着生产装置的产品质量、消耗、生产能力及对环境的影响。
所以要根据企业的实际条件选择合适的高效精馏塔。
目前常用的精馏塔主要有四种塔型:
泡罩塔,浮阀塔,填料塔和新型垂直筛板塔。
四种塔,可以知道填料塔和新型垂直筛板性质更加优越,同时考虑到新型垂直筛板是一种新型塔,目前使用很少,技术难得,而填料塔使用较普遍,技术非常成熟,所以设计选用了填料塔。
其自结构及特点如下:
填料塔是在塔内装填新型高效填料,如不锈钢网波纹填料,每米填料相当5块以上的理论板。
塔总高一般为浮阀塔的一半。
该塔生产能力大,压降小,分离效果好,结果简单,维修量极小,相对投资较小,是目前使用较多的塔型之一。
3.工艺流程
3.1GSP气化工艺流程
GSP气化工艺过程也主要是由给料系统、气化炉、粗煤气洗涤系统组成.即备煤、气化、除渣三部分组成。
固体气化原料被碾磨为不大于0.5㎜的粒度后,经过干燥,通过浓相气流输入系统送至烧嘴。
气化原料与气化剂氧气经烧嘴同时喷入气化炉(R1001)内的反应室,然后在高温(1400一1600℃)、高压(4.0MPa)下发生快速气化反应,产生以CO和H2为主要成分的热粗煤气。
气化原料中的矿物部分形成熔渣。
热粗煤气和熔渣一起通过反应室底部的排渣口进入下部的激冷室。
冷却后的粗煤气进入分离器(V1002),从分离器出来的气体分为两部分:
一部分进入变换炉(R1002),气体出来后进入换热器(E1003),出来的气体和另外一部分气体混合后进入水解器,气体出来后入分离器(V1004),从V1004出来后去净化工段;
而从分离器(V1002)下分离出的液体进入分离器(V1003),从V1003出来的气体经过冷却器(E1002)后,主要为H2S去硫回收系统;
从V1003下分离的液体去污水处理系统,处理后的水和从E1002,E1003,V1004出来的冷液一起返回气化炉冷激室。
气化炉冷激室里的渣粒固化成玻璃状,通过锁斗系统排出。
污水的处理过程是先送入减压闪蒸槽,闪蒸后的液体进入沉淀池,沉淀后去浓缩,再去过滤。
图4GSP气化工艺流程
3.2净化装置工艺流程
3.2.1变换
由气化工段送来的3.8MPa(A),216℃左右,汽气比为1.43的水煤气经煤气水分离器(V2003)和中温换热器(E2002)温度升高至240℃进入预变换炉(R2001)后分成两部分:
一部分进入变换炉(R2002),变换炉内装两段耐硫变换触媒,二段间配有煤气激冷管线,出变换炉变换气的CO含量约6.0%(干),温度为393℃左右进入中温换热器(E2002),温度降为332℃,与旁路调节的水解气混合进入变换气第一废热锅炉(E2003),生产1.4MPa(A)饱和蒸汽,使变换气温度降至为208℃进入变换气第二废热锅炉(E2004),产生0.5MPa(A)低压蒸汽,出口变换气温