完整版船体建造原则工艺规范汇总Word文档格式.docx
《完整版船体建造原则工艺规范汇总Word文档格式.docx》由会员分享,可在线阅读,更多相关《完整版船体建造原则工艺规范汇总Word文档格式.docx(29页珍藏版)》请在冰豆网上搜索。
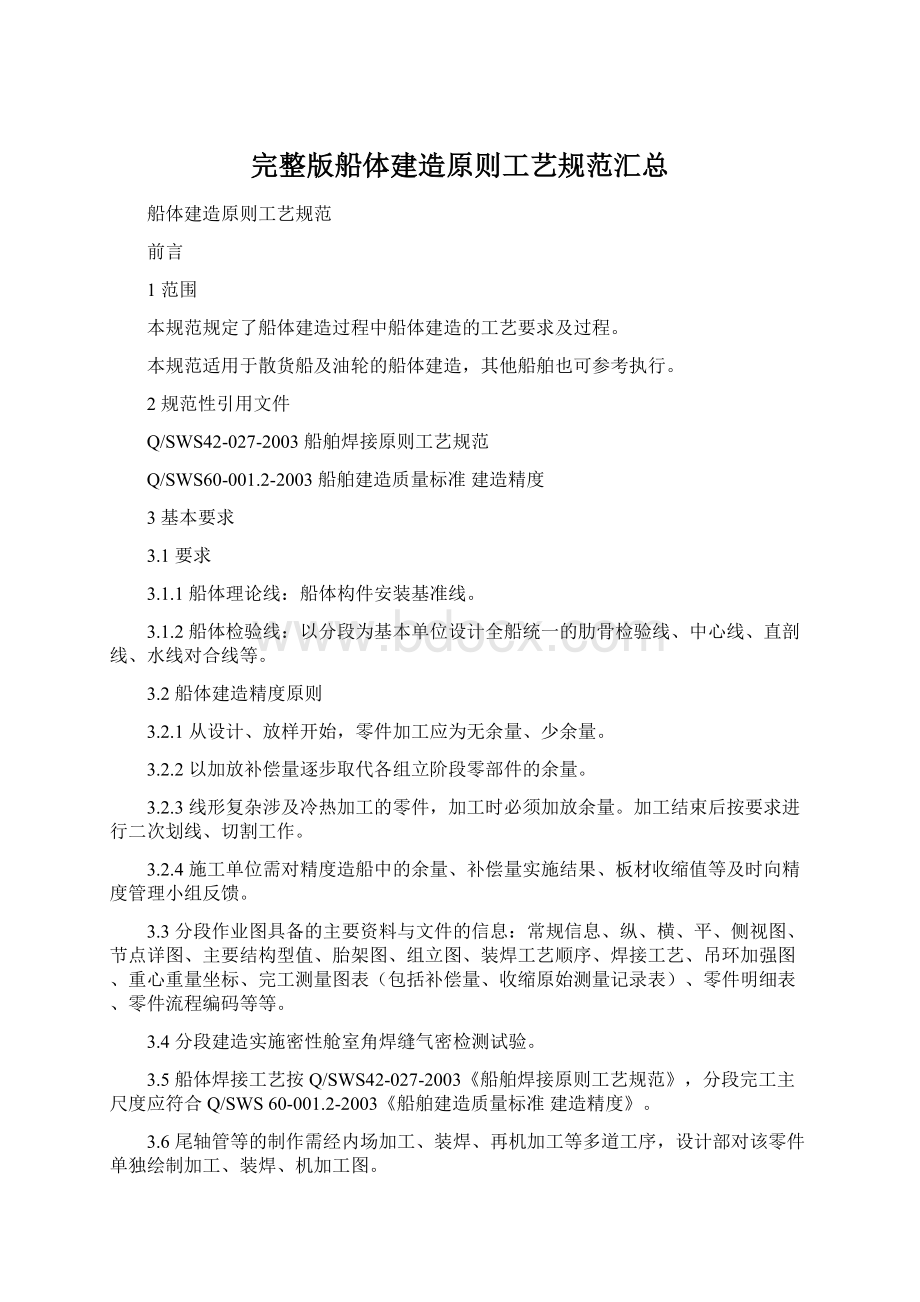
3.8.3.1零件流程编码必须齐全,对合线、矫正线、构架线数控划线必须清晰,零件的坡口形式、企口上下、首尾、正反、左右等零件加工符号、尺寸、标注必须正确无误。
3.8.3.2下料后零件的减轻孔、人孔、透气孔、漏水孔、切口、面板的自由边都必须打磨。
3.8.3.3切割下料零件,严格按分段小组立、中组立、大组立、散装件、标准件等,分阶段配套、堆放,确保分段零件配套完整及零件分流正确。
3.8.3.4切割材料严格按下料工艺单要求,材料规格材质不准擅自替代。
3.8.4型材加工必须控制其直线度、水平度、角尺度及焊接质量。
3.8.5拼板切割零件其直线度精度、对角线精度达到质量标准。
3.8.6数控切割、门式切割、光电跟踪切割等设备的操作人员须每天上下班做好起始点检测保养,从而确保零件切割精度。
3.8.7板材的吊装严禁直接用钢丝绳捆扎。
3.8.8操作人员应根据设计要求做好切割下料实动工时的原始记录。
3.8.9加工单元配套完工后,需将分段切割加工资料、草图、盘片、板图等资料文件保管好,以防散失。
3.8.10切割中心应认真落实处理好切割残余边材及割渣,应预先采取切实有效的措施,定时、定期清除残渣,确保切割平台的平整度。
4船体分段结构建造
4.1双层底分段(双壳油船舷侧分段建造相同)
4.1.1工艺要求
4.1.1.1拼板时以肋骨检验线、板端部对合线为准,误差≤1mm。
4.1.1.2纵骨、纵桁以对合线为准安装,误差≤1mm。
4.1.1.3中组立时分段主尺度、构件垂直度符合Q/SWS60-001.2-2003《船舶建造质量标准建造精度》。
4.1.1.4大组立时分段四周内外底板垂直度和内、外纵骨垂直度,误差≤4mm。
4.1.2工艺过程
4.1.2.1建造方法:
以内底为基面反造,外场翻身,与外板正态合拢;
对艏艉部有曲面外板的分段,采用以内底为基面反造,待外底纵骨定位后,外板反贴,装焊定位,外场翻身,然后内部构架焊接。
4.1.2.2胎架形式:
内场由平直中心流水线生产或采用支柱式胎架,外场采用水平搁墩或水平胎架。
4.1.2.3工艺操作程序(以典型平行舯体双层底分段为例):
4.2单底分段(甲板分段相同)
4.2.1工艺要求
4.2.1.1拼板时以肋骨检验线、板端部对合线为准,误差≤1mm。
4.2.1.2纵骨、纵桁以对合线为准安装,误差≤1mm。
4.2.1.3分段主尺度符合Q/SWS60-001.2-2003《船舶建造质量标准建造精度》。
4.2.2工艺过程
4.2.2.1制造方法:
正造。
4.2.2.2胎架形式:
由平直中心流水线生产或采用支柱式胎架。
4.2.3工艺操作程序:
4.3货舱下边水舱分段(油船下边水舱分段建造相同)
4.3.1工艺要求
4.3.1.1拼板时肋骨检验线、板端部对合线为准,误差≤1mm。
4.3.1.2纵骨、纵桁以对合线为准安装,误差≤1mm。
4.3.1.3构件安装位置正确,垂直度≤3mm。
4.3.1.4分段端面平面度≤4mm。
4.3.2工艺过程
4.3.2.1建造方法:
平行舯体部分下边水舱分段分别制成斜底、外底、外傍片状组立,然后以外底片状组立为基面,吊装斜底片状组立,最后以外傍片状组立为基面吊装斜底、外底合拢后的组合体,制成完整的下边水舱分段。
对艏、艉外板有线型的下边水舱分段以斜底为基面进行建造,采用外板反贴进行装焊定位,然后吊出胎架,翻身,回转焊接。
4.3.2.2胎架形式:
片状由平直中心流水线生产,大组立采用支柱式胎架或有型值的搁墩。
4.3.3工艺操作程序(以典型平行舯体下边水舱分段为例):
4.4货舱上边水舱分段
4.4.1工艺要求
4.4.1.1拼板时肋骨检验线直线度良好,板端部误差≤1mm。
4.4.1.2构件安装位置正确,垂直度≤3mm。
4.4.1.3分段端面平面度≤4mm。
4.4.2工艺过程
4.4.2.1建造方法:
平行舯体部分上边水舱分段分别制成外傍、甲板、斜顶板片状组立,然后以甲板片状组立为基面,装焊斜板片状组立,最后以外傍片状组立为基面,装焊由甲板、斜板合拢后的组合分段,形成完整的上边水舱分段。
艏、艉有线型的上边水舱分段建成外板片状分段与甲板、斜板合拢的组合分段,分别涂装后在平台上总组成完整的上边水舱分段。
4.4.2.2胎架形式:
4.4.3工艺操作程序(以典型平行舯体上边水舱分段为例):
曲面中心或平台
4.5上层建筑分段(包括甲板桅屋、烟囱、机舱棚分段)
4.5.1工艺要求
4.5.1.1分段主尺度、构件垂直度、甲板平整度、围壁平整度等应符合Q/WSW60-001.2-2003船舶建造质量标准。
a.a.
窗的开孔高度尺寸,应以上口为基准线;
b.b.
设计部在技术协议书中明确,厂商应提供窗框外形尺寸的开孔样板;
c.c.
施工人员对门、窗划线、开孔应按厂商提供的样板。
门窗开孔切割形式由设计定,可以数切亦可手工切割。
4.5.1.2控制焊接变形,减少火工矫正。
装配点焊,在有条件情况下应采用CO2焊接;
严格控制焊脚高度,以控制焊接变形;
注意部件的焊接方法及焊接顺序,湿房间的具体位置。
4.5.1.3加强及吊环
上层建筑外围壁光面应少设马脚、吊环。
加强拆除后的马脚,应批磨光;
加强及吊环应尽量考虑设置在构架上。
4.5.1.4对外提交报验前,做好自检工作。
4.5.2工艺过程
4.5.2.1建造方法:
除烟囱外的上层建筑分段均以甲板为基面反造;
烟囱卧造。
4.5.2.2胎架形式:
支柱式胎架
4.5.3工艺操作程序:
4.6机舱区双层底分段制造
4.6.1工艺要求
4.6.1.1机舱区双层内底、机座面板与胎架吻合,间隙误差≤2mm。
4.6.1.2分段内外底端缝处垂直度误差≤4mm。
4.6.1.3分段主尺度及机座面板、内底水平要求符合Q/SWS60-001.2-2003《船舶建造质量标准建造精度》。
4.6.1.4凡通过主焊缝的管子开孔时,焊缝必须先焊透后方可开孔,覆板施焊。
4.6.1.5海底门根据开孔样板划线、开孔。
4.6.2工艺过程
4.6.2.1建造方式:
以机舱内底板为基面反造,外板反贴。
4.6.2.2胎架形式:
支柱式胎架和主机座附近设计桁架式胎架。
4.6.3工艺操作程序:
4.7机舱舷侧分段
机舱舷侧的制造与机舱平台(主甲板)分段的舷侧分段相似,其制造工艺参照机舱平
台(主甲板)分段的舷侧分段。
4.8机舱平台分段和机舱主甲板分段
4.8.1工艺要求
4.8.1.1外板组立制造工艺要点
应大力推广支柱式胎架。
按结构特点,由设计确定少量桁架式胎架;
胎架底脚线应有四角定位点及板缝线;
拼板以肋骨检验线为准,误差≤1mm;
d.d.
曲面分段必须二次划线;
e.e.
外板与胎架吻合;
f.f.
肋骨冲势正确,误差≤3mm。
4.8.1.2分段施工工艺要点
平台胎架应平整,主甲板胎架梁拱正确,线形光顺。
大组时应测量分段下口半宽,焊前应放8mm反变形。
分段两端面平面度误差≤4mm,极限≤8mm。
纵向构件以对合线为准,误差≤1mm。
4.8.2工艺过程
4.8.2.1建造方法:
机舱平台(主甲板)分段的舷侧以外板为基面侧造,整个分段以平台(主甲板)为基面反造。
4.8.2.2胎架形式:
4.8.3工艺操作程序:
4.9艉尖舱分段制造
4.9.1工艺要求
4.9.1.1艉尖舱壁定位时必须与地面预埋件刚性固定。
4.9.1.2各肋板中心线对准艉尖舱壁中心线,误差≤1mm。
4.9.1.3尾轴管小组立时,前后中心线垂直度误差≤2mm。
4.9.1.4尾轴管安装时必须保证尾轴毂尾端加工余量。
4.9.1.5尾轴管焊接时(包括尾轴管小组时与尾轴毂焊接及中组时与艉尖舱壁铸钢件焊接)必须预热,并派人专职监视轴孔中心线情况,发现偏差,随即调整焊接顺序,确保轴孔中线精度。
焊后保温冷却。
4.9.1.6外板端面平面度误差≤4mm,极限≤8mm。
4.9.1.7分段主尺度误差符合Q/SWS60-001.2-2003《船舶建造质量标准建造精度》。
4.9.2工艺过程
4.9.2.1建造方式:
以艉尖舱壁为基面侧造,外板外贴。
4.9.2.2胎架形式:
桁架式(支柱式)胎架。
4.9.3工艺操作程序:
4.10舵机平台分段建造
4.10.1工艺要求
4.10.1.1舵机平台定位时,其四周及挂舵臂处必须用[20槽钢]与地面预埋件刚性固定。
4.10.1.2挂舵臂安装时,其下舵钮中心线向艉倾斜10mm作反变形,并用[20槽钢]斜撑与地面拉紧。
4.10.1.3在挂舵臂焊接时,挂舵臂必须预热,焊后保温冷却,焊接过程中派人专职监控,一旦发现舵钮中心线偏离监控点,随即调整焊接顺序,确保精度。
4.10.1.4外板端面平面度误差≤4mm,极限≤8mm。
4.10.1.5分段主尺度符合Q/SWS60-001.2-2003《船舶建造质量标准建造精度》。
4.10.2工艺过程
4.10.2.1建造方法:
以舵机平台为基面反造,外板反贴。
4.10.2.2胎架形式:
支柱式胎架。
4.10.3工艺操作程序:
4.11其余艉部分段制造
艉部除艉尖舱分段及舵机平台分段外的其余分段,与机舱平台(甲板)分段相似,其建造参照机舱平台(甲板)分段制造工艺施工。
4.12艏底部分段
4.12.1工艺要求
4.12.1.1分段尾端大接缝平面度≤4mm,极限误差≤8mm。
4.12.1.2企口尺寸确保。
4.12.1.3分段主尺度等符合Q/SWS60-001.2-2003《船舶建造质量标准建造精度》。
4.12.2工艺过程
4.12.2.1建造方式:
以平台为基面反造,外板反贴。
4.12.2.2胎架形式:
4.12.3工艺操作程序:
4.13球鼻艏分段(艏部鼻梁分段)
4.13.1工艺要求
4.13.1.1艏柱中心线误差≤4mm。
4.13.1.2胎架底脚线应有四角定位点及板缝线。
4.13.1.3拼板以肋骨检验线为准,误差≤2mm。
4.13.1.4装焊结束后切割外板加工余量。
4.13.1.5尾端大接缝平面度≤4mm,极限误差≤8mm。
4.13.1.6舱壁垂直误差≤0.1h%,(h为舱壁高度)且极限误差<12mm,二者取小值。
4.13.1.7分段主尺度等符合Q/SWS60-001.2-2003《船舶建造质量标准建造精度》。
4.13.2工艺过程
4.13.2.1建造方法:
以舱壁为基面侧造,外板反贴。
4.13.2.2胎架形式:
4.13.3工艺操作程序:
4.14艏部主甲板分段
4.14.1工艺要求
4.14.1.1胎架底脚线应有四角定位点及板缝线。
4.14.1.2拼板以肋骨检验线为准,误差≤1mm。
4.14.1.3尾端大接缝平面度≤4mm,极限误差≤8mm。
4.14.1.4舱壁垂直误差≤0.1h%,(h为舱壁高度),极限误差<12mm,二者取小值。
4.14.1.5分段主尺度等符合Q/SWS60-001.2-2003《船舶建造质量标准建造精度》。
4.14.2工艺过程
4.14.2.1建造方法:
以主甲板为基面反造。
4.14.2.2胎架形式:
4.14.3工艺操作程序:
4.15艏部其余分段
艏部其余分段的制造与机舱平台分段相似,其制造工艺参照机舱平台分段。
4.16槽形舱壁制造
4.16.1工艺要求
4.16.1.1按设计要求安装加强排。
4.16.1.2分段主尺度等符合Q/SWS60-001.2-2003《船舶建造质量标准建造精度》。
4.16.2工艺过程
4.16.2.1制造方法:
以槽形舱壁平直面为基面制造。
4.16.2.2胎架形式:
用[20槽钢支撑落地支撑式,下墩采用支柱式胎架。
4.16.3工艺操作程序:
5船体分段总组(根据公司实际生产需要,亦可不进行总组,直接进坞搭载)
5.1双层底分段总组
5.1.1工艺要求
5.1.1.1总组时以肋骨检验线为准,误差≤4mm。
5.1.1.2总组后总段主尺度等符合Q/SWS60-001.2-2003《船舶建造质量标准建造精度》。
5.1.2工艺过程
5.1.2.1胎架形式:
采用搁墩为总组胎架。
5.1.2.2总组方法:
正态总组。
5.1.3总组工艺操作程序:
5.2舷侧分段总组
5.2.1“P”型分段总组
5.2.1.1工艺要求
首尾端面平面度≤4㎜;
总组后总段主尺度等符合Q/SWS60-001.2-2003《船舶建造质量标准建造精度》。
5.2.1.2工艺过程
a.总组方法:
以舷侧外板为基面侧造;
b.胎架形式:
采用搁墩或支柱式胎架;
5.2.1.3总组工艺操作程序:
5.2.2“C”型分段总组
5.2.2.1工艺要求
总组时以肋骨检验线为准,误差≤4mm;
总组时型深放5mm补偿量;
首尾端面平面度≤4mm;
5.2.2.2工艺过程
5.2.2.2.1总组方法:
以舷侧外板为基面侧造。
5.2.2.2.2胎架形式:
搁墩。
5.2.2.3总组工艺操作程序:
5.2.3“D”型分段总组
5.2.3.1工艺要求
5.2.3.2工艺过程
5.2.3.2.1总组方法:
5.2.3.2.2胎架形式:
5.2.3.3总组工艺操作程序:
5.2.4机舱分段总组
5.2.4.1工艺要求
总组时甲板宽度加放3mm~5mm补偿量;
首尾端面平面度误差≤4mm;
定位后,总段下口设置加强排;
5.2.4.2工艺过程
5.2.4.2.1总组方法:
正态总组
5.2.4.2.2胎架形式:
搁墩和加排固定。
5.2.4.3总组工艺操作程序:
5.2.5艏部单底分段总组
艏部单底分段总组与机舱分段总组相似,其总组参照机舱分段总组工艺施工。
5.2.6艏部多层分段总组
艏部多层分段总组与上层建筑分段总组相似,其总组参照上层建筑分段总组工艺施工。
艏部多层分段总组时应保证鼻梁(艏柱中心线)的正直。
5.2.7艏部主甲板分段总组
5.2.7.1工艺要求
a.总组时以肋骨检验线为准,误差≤4mm;
b.总组时甲板宽度加放3mm~5mm补偿量;
c.甲板梁拱、艏舷弧要注意;
d.尾端端面平面度误差≤4mm,极限≤8mm;
e.总组后总段主尺度等符合Q/SWS60-001.2-2003《船舶建造质量标准建造精度》。
5.2.7.2工艺过程
5.2.7.2.1总组方法:
5.2.7.2.2胎架形式:
5.2.7.3总组工艺操作程序:
5.2.8艉部其余分段总组
艉部其余分段总组与机舱分段总组相似,参照机舱分段总组工艺施工。
5.2.9甲板分段总组(油船)
5.2.9.1工艺要求
c.首尾端端面平面度误差≤4mm,极限≤8mm;
d.总组搁墩要牢固,不能用槽钢或板材简单支撑,以防失稳;
5.2.9.2工艺过程
正态总组;
搁墩;
5.2.9.3总组工艺操作程序:
5.2.10上层建筑分段单层总组与机舱分段总组相似,参照机舱分段总组工艺施工。
5.2.11上层建筑分段多层总组
5.2.11.1工艺要求
a.总组时以肋骨检验线、中心线为准,误差≤4mm;
b.总组时每层层高加放3mm~5mm补偿量;
d.甲板水平误差≤10mm,极限≤15mm;
e.总段主尺度等符合Q/SWS60-001.2-2003《船舶建造质量标准建造精度》;
f.火工矫正原则:
——单层矫正时顺序:
构架甲板围壁;
——变形状态时顺序:
先矫正变形大的地方,其次为中度变形处,最后矫正小变形处,直至完工;
——层次顺序:
由上至下矫正,并需反复循环矫正。
5.2.11.2工艺过程
按居住甲板内围壁分布位置,用[20槽钢制作落地支撑式胎架;
5.2.11.3总组工艺操作程序:
6船坞搭载
船坞搭载为船体建造的最后一道工序,其质量优劣对航海性能十分重要,必须严格控制。
6.1船坞格子线
6.1.1工艺要求
6.1.1.1船坞中心线:
中心线直线度误差≤2mm。
6.1.1.2船坞角尺线。
6.1.1.3肋骨检验线:
各肋骨检验线误差≤3mm。
6.1.1.4半宽线:
误差≤3mm。
6.1.1.5船长线:
6.1.1.6假设基线高度:
误差≤2mm。
6.2底部定位总段搭载
6.2.1工艺要求
6.2.1.1中心线误差≤3mm,极限≤5mm。
6.2.1.2肋骨检验线误差≤4mm,极限≤11mm。
6.2.1.3基线高度误差≤5mm,极限≤8mm。
6.2.1.4底部分段水平误差≤8mm,极限≤12mm。
6.2.2底部定位总段搭载工艺操作程序:
6.3后续底部总段搭载
6.3.1工艺要求
6.3.1.1后续双层底总段在欲对接缝的内底板上设置4~6块搁排。
6.3.1.2搭载时其长度还应检测前后总段的肋骨检验线的间距。
6.3.1.3搭载主尺度等符合Q/SWS60-001.2-2003《船舶建造质量标准建造精度》。
6.3.1.4大接缝的坡口、间隙、焊接方法符合Q/SWS42-027-2003《船舶焊接原则工艺规范》。
6.3.2后续底部总段搭载工艺操作程序:
6.4横舱壁(槽形舱壁)分段搭载
6.4.1工艺要求
6.4.1.1在内底上按装靠马。
6.4.1.2定位时舱壁高度加放3mm~5mm补偿量。
6.4.1.3分段吊到位后,槽形舱壁固定。
6.4.1.4搭载焊缝的坡口、间隙、焊接方法符合Q/SWS42-027-2003《船舶焊接原则工艺规范》。
6.4.1.5搭载主尺度等符合Q/SWS60-001.2-2003《船舶建造质量标准建造精度》。
6.4.2横舱壁(槽型舱壁)分段搭载工艺操作程序:
6.5纵舱壁定位分段搭载
6.5.1工艺要求
6.5.1.1肋骨检验线与双层底肋骨检验线一致。
6.5.1.2搭载主尺度等符合Q/SWS60-001.2-2003《船舶建造质量标准建造精度》。
6.5.1.3大接缝的坡口、间隙、焊接方法符合Q/SWS42-027-2003《船舶焊接原则工艺规范》。
6.5.2纵舱壁定位分段搭载工艺操作程序:
6.6后续纵舱壁定位分段搭载
6.6.1工艺要求
6.6.1.1肋骨检验线与双层底肋骨检验线一