临沂图书馆钢结构采光顶棚液压提升施工方案Word格式.docx
《临沂图书馆钢结构采光顶棚液压提升施工方案Word格式.docx》由会员分享,可在线阅读,更多相关《临沂图书馆钢结构采光顶棚液压提升施工方案Word格式.docx(18页珍藏版)》请在冰豆网上搜索。
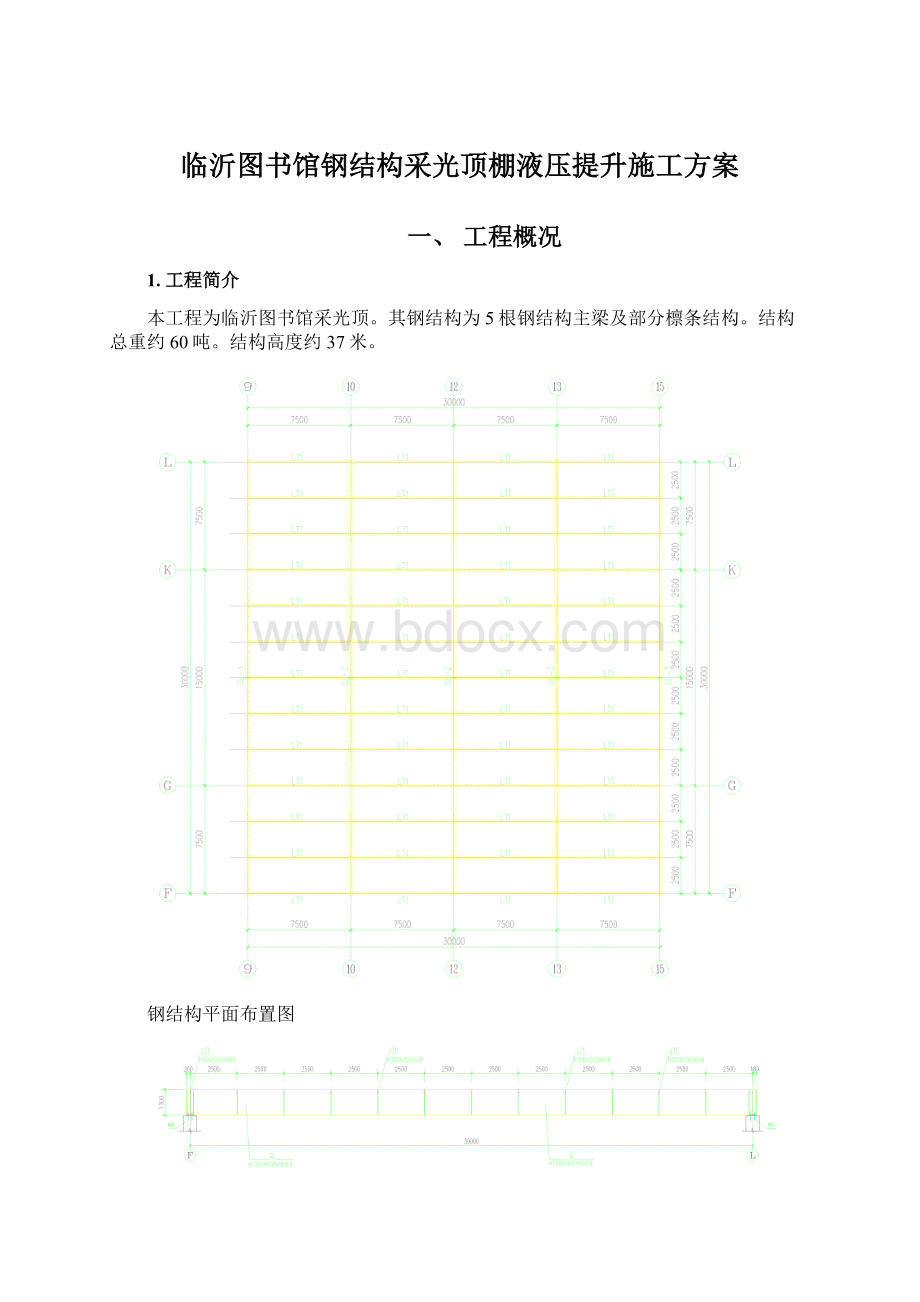
液压提升器液压泵源系统
4.液压同步提升技术
(1)超大型构件液压同步提升施工技术特点
✧通过提升设备扩展组合,提升重量、跨度、面积不受限制;
✧采用柔性索具承重。
只要有合理的承重吊点,提升高度不受限制;
✧液压提升器锚具具有逆向运动自锁性,使提升过程十分安全,并且构件可以在提升过程中的任意位置长期可靠锁定;
✧液压提升器通过液压回路驱动,动作过程中加速度极小,对被提升构件及提升框架结构几乎无附加动荷载;
✧液压提升设备体积小、自重轻、承载能力大,特别适宜于在狭小空间或室内进行大吨位构件牵引安装;
✧设备自动化程度高,操作方便灵活,安全性好,可靠性高,使用面广,通用性强。
(2)液压同步提升技术原理
“液压同步提升技术”采用液压提升器作为提升机具,柔性钢绞线作为承重索具。
液压提升器为穿芯式结构,以钢绞线作为提升索具,有着安全、可靠、承重件自身重量轻、运输安装方便、中间不必镶接等一系列独特优点。
液压提升器两端的楔型锚具具有单向自锁作用。
当锚具工作(紧)时,会自动锁紧钢绞线;
锚具不工作(松)时,放开钢绞线,钢绞线可上下活动。
液压提升过程如图所示,一个流程为液压提升器一个行程。
当液压提升器周期重复动作时,被提升重物则一步步向前移动。
第1步:
上锚紧,夹紧钢绞线;
第2步:
提升器提升重物;
第3步:
下锚紧,夹紧钢绞线;
第4步:
主油缸微缩,上锚片脱开;
第5步:
上锚缸上升,上锚全松;
第6步:
主油缸缩回原位。
(3)计算机同步控制技术
液压同步提升施工技术采用行程及位移传感监测和计算机控制,通过数据反馈和控制指令传递,可全自动实现同步动作、负载均衡、姿态矫正、应力控制、操作闭锁、过程显示和故障报警等多种功能。
操作人员可在中央控制室通过液压同步计算机控制系统人机界面进行液压提升过程及相关数据的观察和(或)控制指令的发布。
液压同步提升控制系统人机界面
二、整体提升施工方案
1.采光顶安装思路
(1)吊装条件分析
结构自重较大,且杆件众多。
根据以往类似工程的成功经验,若将采光顶钢结构在地面拼装成整体后,利用“超大型液压同步提升施工技术”将其一次提升到位,再进行柱顶支座处及部分预留后装结构的安装,将大大降低安装施工难度,并于质量、安全和工期等均有利。
(2)液压提升方案简述
根据本工程的结构特点,将采光顶钢结构在端部断开,即将钢梁(GL-1,GL-2,GL-3)在端部断开,将框架顶部分预先安装就位,在预先就位的钢梁端部上设置临时设施,形成上吊点。
剩余部分钢结构在地面拼装成整体,在钢梁端部设置临时设施,形成下吊点。
上下吊点间使用钢绞线连接,同步整体提升钢结构至安装位置,对口焊接,达到设计标准。
2.施工流程
采光顶钢结构整体提升流程如下:
采光顶钢结构整体提升流程图
采光顶钢结构整体提升流程详述:
✧STEP1:
在地面拼装胎架上散拼采光顶钢结构,设置提升上吊点;
✧STEP2:
采光顶钢结构钢梁及檩条整体拼装好后,在对应提升上吊点的钢梁下方安装好提升下吊点(地锚),上下吊点间通过钢绞线连接好;
✧STEP3:
提升设备调试完毕,分级加载,预提升采光顶钢结构,使采光顶钢结构提升离开胎架约200mm,暂停。
全面检查提升设备、采光顶钢结构结构、提升支架等设备及设施,悬空停留约4小时以上,以便进一步观察结构件及提升设备等情况;
✧STEP4:
检查一切正常后,正式同步提升采光顶钢结构。
提升过程中随时监测各提升设备并观察采光顶钢结构的变形情况;
✧STEP5:
连续同步提升采光顶钢结构,各吊点保持同步,直至采光顶钢结构提升至设计安装位置,暂停,开始对口焊接;
✧STEP6:
采光顶钢结构对口焊接完毕,提升器卸载,设备拆除。
3.提升上下吊点
在预装端部钢梁上方搭设支架,布置上吊点。
根据结构重量及结构形式特点。
共布置10个吊点。
吊点平面布置图(●代表吊点)
在采光顶钢结构上设置临时吊点结构,用于安装提升地锚座,并通过钢绞线与提升平台上的液压提升器连接。
提升平台及下吊点锚具详图见附图。
三、施工技术措施
一切准备工作做完,且经过系统的、全面的检查确认无误后,经现场吊装总指挥下达吊装命令后,可进行结构的液压整体提升。
1.分级加载(试提升)
先进行分级加载试提升。
通过试提升过程中对采光顶钢结构、框架柱、上下吊点以及提升设备系统的观察和监测,确认符合模拟工况计算和设计条件,保证提升过程的安全。
初始提升时,各吊点提升器伸缸压力应缓慢分级增加,最初加压为所需压力的40%,60%,80%,90%,在一切都稳定的情况下,可加到100%,即采光顶钢结构试提升离开拼装胎架。
在分级加载过程中,每一步分级加载完毕,均应暂停并检查如:
上吊点、下吊点等加载前后的变形情况,以及框架柱、采光顶钢结构整体的稳定性等情况。
一切正常情况下,继续下一步分级加载。
当分级加载至采光顶钢结构即将离开拼装胎架时,可能存在各点不同时离地,此时应降低提升速度,并密切观查各点离地情况,必要时做“单点动”或微动提升。
确保采光顶钢结构离地平稳,各点同步。
分级加载完毕,采光顶钢结构提升离开拼装胎架约200cm后暂停,停留约4小时作全面检查各设备运行及其它构件体系的正常情况:
如上吊点、下吊点等加载前后的变形情况,每一吊点的提升器受载均匀情况(压力表读数),以及框架柱、采光顶钢结构整体的稳定性等情况。
一切正常情况下,开始采光顶钢结构的正式提升。
2.正式提升
试提升阶段一切正常情况下开始正式提升。
在整个同步提升过程中应随时检查:
1每一吊点提升器受载均匀情况;
2每吊点框架柱的稳定情况;
3采光顶钢结构提升过程的整体稳定性;
4计算机控制各吊点的同步性;
5激光测距仪配合测量采光顶钢结构提升过程中的同步性;
6提升承重系统监视:
提升承重系统是提升工程的关键部件,务必做到认真检查,仔细观察。
重点检查:
●锚具(脱锚情况,锚片及其松锚螺钉)
●导向架中钢绞线穿出顺畅
●主油缸及上、下锚具油缸(是否有泄漏及其它异常情况)
●液压锁(液控单向阀)、软管及管接头
●各类传感器(行程、锚具、位移传感器等)及其导线
7液压动力系统监视:
●系统压力变化情况
●油路泄漏情况
●油温变化情况
●油泵、电机、各电磁阀线圈温度变化情况
●系统噪音情况
3.提升就位
采光顶钢结构提升至设计位置后,暂停,各吊点微调使采光顶钢结构精确提升到达设计位置,与预装部分对口焊接,最终使采光顶钢结构整体达到设计标准。
液压提升系统设备卸载、拆除,完成采光顶钢结构的提升安装。
采光顶钢结构提升到位后,高空对口焊接时,采光顶钢结构需要在空中停留一段时间。
液压同步提升器独有的机械和液压自锁装置,可使采光顶钢结构在空中(或提升过程中)的任意位置长期可靠锁定。
4.设备卸载、拆除
采光顶钢结构空中各弦杆对口焊接、补杆完毕后,采光顶钢结构与框架柱成为一整体受力体系,即采光顶钢结构提升安装就位。
此时启动液压提升系统,相同于采光顶钢结构各吊点分级加载时状况,各吊点载荷卸载时也为分级卸载,依次为40%,60%,80%,在确认各部分无异常的情况下,可继续卸载至100%,使提升器钢绞线不再不受力。
四、类似工程
圆形屋架整体提升
矩形屋架整体提升
提升上吊点
提升下吊点
五、施工现场要求
1)施工用设备安装
1.施工现场甲方应保证提升设备运输。
2.液压设备安装需甲方吊机、人员配合。
2)施工用电
1.提升时需甲方提供动力电缆,每台泵站60KW。
2.夜间工作时,安装场地周边需提供夜间施工照明。
3)设备安全及现场协调
1.设备进场后需甲方提供必要的现场保护。
2.现场交叉作业需甲方协调。
六、施工组织体系
分工
人数
总工程师
1
项目经理
液压系统工程师
电器系统工程师
后勤保障
合计
5
七、主要施工设备
序号
名称
规格
型号
设备单重
数量
液压泵源系统
60KW
1.2吨
台
2
液压提升器
600KN
TJJ-600
1.0吨
3
标准油管
标准油管箱
箱
4
计算机控制系统
32通道
YT-2
套
传感器
行程
八、应急预案
1.现场设备故障应急预案
(1)油缸故障
滑移过程中如主油缸发生严重泄漏等故障,应停止滑移更换主油缸。
(2)液压泵站故障
液压泵站可能出现管路漏油、阀门动作不灵、油泵或电机损坏等故障。
对于漏油故障,只需在几分钟内更换垫圈即可;
对于阀门动作不灵、油泵或电机故障,先确认故障性质。
对于可以在线修理的问题,可以在系统停止工作的情况下进行维修,若情况较为严重或确实硬件损坏,应立即进行备件更换。
(3)液压油管(软管)损坏
滑移过程中,如发生油管爆裂,应立即停止滑移作业,并用备用有关更换即可。
(4)计算机控制系统故障
本工程中所采用的计算机同步控制系统稳定性高、故障率低。
对于一般故障,可通过现场调试解决;
为不影响现场滑移连续作业,确保配合屋面钢结构安装工作,考虑备用一套计算机同步控制系统。
2.自然环境影响应急预案
1雨天停止高空作业,大雨停止现场作业;
2整个钢结构及电气控制系统应有可靠的避雷措施;
如遇大风天气(六级以上),停止吊装及滑移作。
一、工程概况1
1.工程简介1
2.工作内容2
3.关键技术和设备2
4.液压同步提升技术3
二、整体提升施工方案6
1.采光顶安装思路6
2.施工流程7
3.提升上下吊点11
三、施工技术措施12
1.分级加载(试提升)12
2.正式提升13
3.提升就位14
4.设备卸载、拆除15
四、类似工程15
五、施工现场要求17
六、施工组织体系18
七、主要施工设备19
八、应急预案19
1.现场设备故障应急预案19
2.自然环境影响应急预案20