关于数控轴类加工工艺设计Word格式.docx
《关于数控轴类加工工艺设计Word格式.docx》由会员分享,可在线阅读,更多相关《关于数控轴类加工工艺设计Word格式.docx(12页珍藏版)》请在冰豆网上搜索。
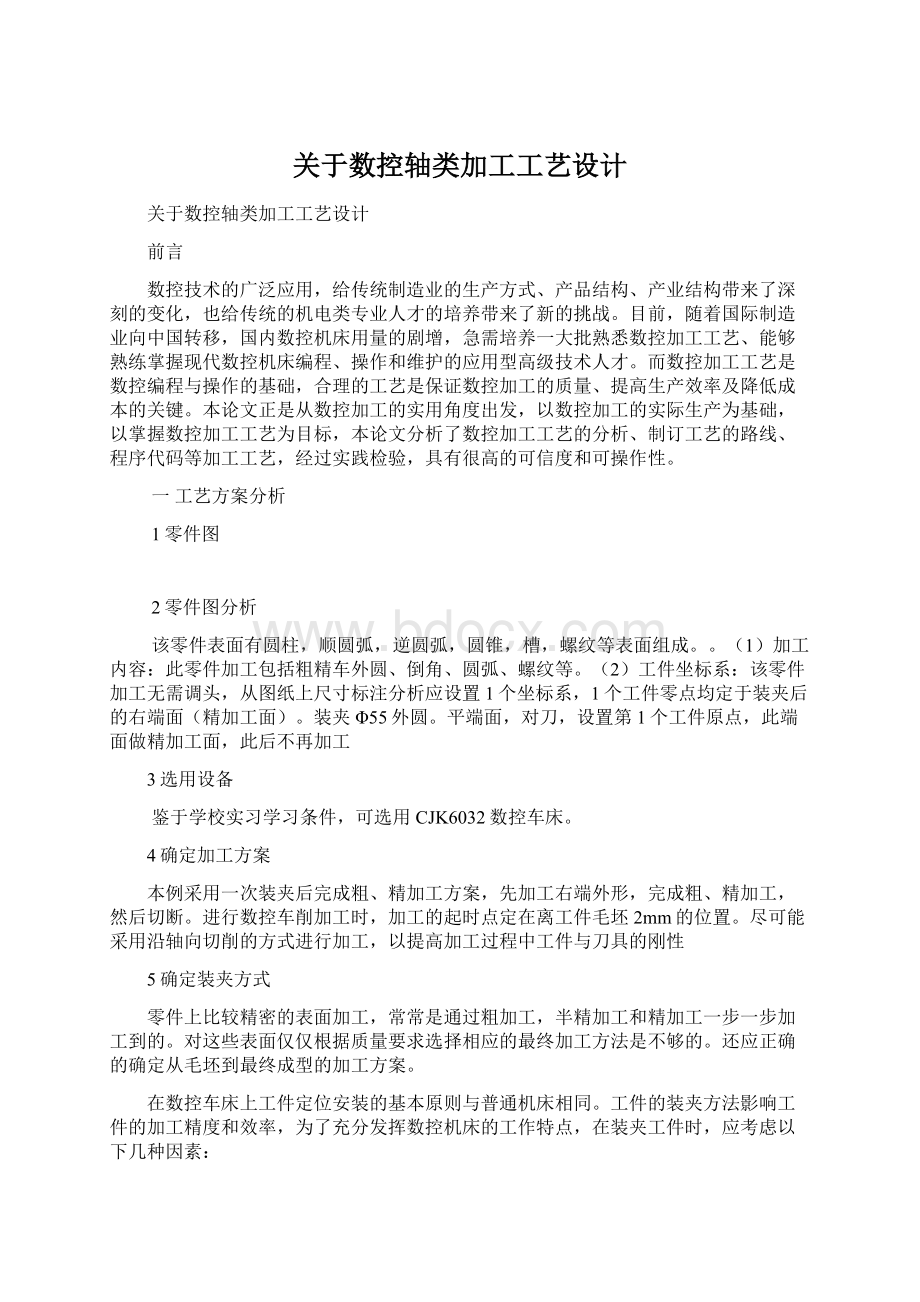
进给路线泛指刀具从对刀点(或机床固定原点)开始运动起,直至返回该点并结束加工程序所经过的路径,包括切削加工的路径及刀具切入、切出等非切削空行程。
在保证加工质量的前提下,使加工顺序具有最短的进给路线,不仅可以节省整个加工过程的执行时间,还能减少一些不必要的刀具消耗及机床进给机构滑动部件的磨损等。
实现最短的进给路线,除了依靠大量的实践经验外,还应善于分析,必要时可辅以一些简单计算。
7刀具的选择
数控刀具的选择和切削用量的确定是数控加工工艺中的重要内容,它不仅影响数控机床的加工效率,而且直接影响加工质量。
刀具的选择是在数控编程的人机交互状态下进行的。
应根据机床的加工能力、工件材料的性能、加工工序、切削用量以及其它相关因素正确选用刀具及刀柄。
刀具选择总的原则是:
安装调整方便、刚性好、耐用度和精度高。
在满足加工要求的前提下,尽量选择较短的刀柄,以提高刀具加工的刚性。
在经济型数控机床的加工过程中,由于刀具的刃磨、测量和更换多为人工手动进行,占用辅助时间较长,因此,必须合理安排刀具的排列顺序。
一般应遵循以下原则:
①尽量减少刀具数量;
②一把刀具装夹后,应完成其所能进行的所有加工步骤;
③粗精加工的刀具应分开使用,即使是相同尺寸规格的刀具;
④先铣后钻;
⑤先进行曲面精加工,后进行二维轮廓精加工;
⑥在可能的情况下,应尽可能利用数控机床的自动换刀功能,以提高生产效率等。
本例选用图3所示的几种刀具可选择。
图3刀具的选用
A切断刀B90度外圆车刀C螺纹车刀D端面车刀
根据实习的条件,可选用整体式或机夹式车刀,4种刀具的刀片材料均选用硬质合金。
本例选用的刀具及参数列于表1中。
表1数控加工刀具卡片
产品名称或代号
零件名称
零件图号
序号
刀具号
刀具规格名称
数量
加工表面
刀尖半径/mm
备注
1
T01
硬质合金端面车刀
车端面
0.4
左偏刀
2
T02
硬质合金90°
外圆粗车刀
粗外车圆
3
外圆精车刀
精外车圆
0.2
4
T03
硬质合金切断刀
切断
0.1
5*12
5
T04
硬质合金60°
外螺纹车刀
粗精车螺纹
编制
审核
批准
年月日
共页
第页
8确定切削用量
合理的切削用量应满足以下要求:
在保证安全生产,不发生人身、设备事故,保证工件加工质量的前提下,能充分发挥机床的潜力和刀具的切削性能,在不超过数控车床的有效功率和工艺系统刚性所允许的额定负荷的情况下,尽量选择较大的切削用量。
(1)粗车时切削用量的选择
粗车时,加工余量较大,主要应考虑尽可能提高生产效率和保证必要的刀具寿命,由于切削速度对切削温度影响最大,切削速度增大,导致切削温度升高,刀具磨损加快,刀具使用寿命明显下降。
所以应首先选择尽可能大的进给量,然后在选取合适的背吃刀量,最后在保证刀具经济耐用度的条件下,尽可能选用较大的切削速度。
(1)背吃刀量。
背吃刀量应根据工件的加工余量和工艺系统的刚性来选择。
①在保留半精加工余量(1~3mm)和精加工余量(0.1~0.5mm)后,应尽量将剩下余量一次切除。
以减小走刀次数。
②若总加工余量太大,一次切除所有余量将引起明显振动,或者刀具强度不允许,机床功率不够。
这时就应分两次或多次进刀,但第一次进刀深度必须选取得大一些。
特别是当切削表面层有硬皮的铸件、锻件毛坯或切削不锈钢等冷硬现象较严重的材料时,应尽量使背吃刀量超过硬皮或冷硬层厚度,以避免刀尖过早磨损或破损。
(2)进给量f(mm/r)与进给速度F(mm/min)。
一般制约进给量的主要因素是切削阻力和表面粗糙度。
粗车时,对工件表面粗糙度要求不高,只要工艺系统的刚性和刀具强度允许,可以选较大的进给量,否则应适当减小进给量。
而进给速度在粗加工时,为提高生产效率,在保证工件质量的前提下,可选择较高的进给速度,一般取100~200mm/min。
当进行切槽、切断、车孔加工或采用高速钢力刀具进行加工时,应选用较低的进给速度,一般在50~100mm/min内来选取。
精加工的进给速度一般取粗加工进给速度的1/2。
(3)切削速度。
粗车时切削速度的选择,主要考虑切削的经济性,既要保证刀具的经济耐用度,又要保证切削负荷不超过机床的额定功率。
具体如下:
①刀具材料耐热性好,则切削速度可选高些。
用硬质合金刀比用高速钢车刀切削时的切削速度高。
②工件材料的强度、硬度高,切削速度应选取低些。
③断续切削,应取较低的切削速度。
④工艺系统刚性差时,切削速度应适当减小。
(2)半精车和精车时切削用量的选择
半精车和精车时切削用量,应以保证加工质量为主,并兼顾生产率和必要的刀具寿命。
(1)切削速度:
为了抑制积屑瘤的生产,降低表面粗糙度,用硬质合金车刀切削时可用较高的切削速度(80~120r/min)。
(2)进给量:
半精车和精车时,制约增大进给量的主要因素是表面粗糙度,通常选择较小的进给量。
(3)背吃刀量:
半精车和精车的背吃刀量是根据加工精度和表面粗糙度要求,由粗车留下的余量确定的。
原则上取一次切削的余量数,一般为0.2~0.5mm。
(3)车螺纹时主轴转速
数控车床加工螺纹时,因其传动链的改变,原则上其转速只要能保证主轴每转一周时,刀具沿主进给轴(多为Z轴)方向位移一个螺距即可,不受到限制。
但数控车床车螺纹时,会受到以下几个方面的影响。
(1)螺纹加工程序段中指令的螺距值,相当于以进给量f(mm/r)表示的进给速度f,如果将机床的主轴转速选择过高,其换算后的进给速度(mm/min)则必定大大超过正常值。
(2)刀具在其位移过程的始终,都将受到伺服驱动系统升/降频率和数控装置插补运算速度的约束,由于升/降频特性满足不了加工需要等原因,则可能因主进给运动产生出的“超前”和“滞后”而导致部分螺牙的螺距不符合要求。
(3)车削螺纹必须通过主轴的同步运行功能而实现,即车削螺纹需要有主轴脉冲发生器(编码器)。
当其主轴转速选择过高时,通过编码器发出的定位脉冲(即主轴每转一周时所发出的一个基准脉冲信号)将可能因“过冲”(特别是当编码器质量不稳定时)而导致工件螺纹产生乱纹(俗称“烂牙”)。
鉴于上述原因,不同的数控系统车螺纹时推荐使用不同的主轴转速范围。
大多数经济数控车床的数控车床的数控系统推荐车螺纹时主轴转速n为
n≤(1200/P)-K
式中P---被加工螺纹螺纹距,mm;
K---保险系统,一般为80。
9工艺卡的制订
将前面分析的各项内容综合成表2所示的数控加工工艺卡片,此表是编制加工程序的主要依据和操作人员配合数控程序进行数控加工的指导文件,主要内容包括:
加工工序,工步内容、各工步所用的刀具及切削用量等。
表2数控加工工艺卡
单位名称
数控加工艺卡片
产品代号
轴类零件
工艺序号
程序编号
夹具名称
夹具编号
使用设备
车间
O001
三爪卡盘
CKJ6032
数控车间
工步号
工步内容(加工面)
刀具规格
主轴转速r/min
进给速度mm/r
背吃刀量mm
端面车刀
460
粗加工外圆轮廓
0.3
1.5
精加工外圆轮廓
1000
0.08
0.15
切断7*2
切断刀
0.05
螺纹车刀
150
6
共_页第_页
10加工工艺路线的确定
在对加工工艺进行认真和仔细的分析后,制定加工方案的一般原则为先粗后精、先近后远、先内后外、程序段最少、走刀路线最短,由于生产规模的差异,对于同一零件的加工方案是有所不同的,应根据具体条件选择经济,合理的工艺方案
(1)加工工序的划分
在数控机床上加工零件,工序可以比较集中,一次装夹应尽可能完成全部工序,与普通机床加工相比,加工工序划分有其自己的特点,常用的工序划分原则有以下两种:
(2)保证精度的原则
数控加工要求工序尽可能集中,常常粗加工在一次装夹下完成,为减少热变形和
切削力变形对工件的形状、位置精度、尺寸精度和表面粗糙度的影响,应将粗、精加工分开进行。
对轴类或盘类零件,将各处先粗加工,留少量余量精加工,来保证表面质量要求。
(3)提高生产效率的原则
数控加工中,为减少换刀次数,节省换刀时间,应将需用同一把刀加上加工部位
全部完成后,再换另一把来加工其它部位。
同时应尽量减少空行程,用同一把刀加工工件的多个部位时,应以最短的路线到达各个加工部位。
实际中,数控加工工序要根据具体零件的结构特点,技术要求等情况综合考虑。
(4)加工顺序的安排
加工顺序的安排应根据工件的结构和毛坯状况,选择工件定位和安装方式,重点保证工件的刚度不被破坏,尽量减少变形,因此加工顺序的安排应遵循以下原则:
(1)上道工序的加工不影响下道工序的定位与夹紧;
(2)先加工工件的端面后进行半精加与精加工;
(3)尽量减少重复定位与换刀次数;
(4)在一次安装加工多道工序中,先安排对工件刚性破坏较小的工序
11.编辑程序
11.1车程序的分类
按照数控程序的分类可将程序分为三种,分别是:
程序开始、程序内容、程序结束三部分内容。
(1)程序开始
主轴定义程序号,调出零件加工坐标系,加工刀具,启动主轴,打开冷却液等方面内容。
主轴最高转速限制定义S2000,设置主轴的最高转速为2000RPM,对于数控车床
来说,这是一个非常重要的指令。
坐标字:
用来设定机床各坐标的位移量由坐标地址符及数安组成,一般以X、Y、Z、U、V、W等字母开头,后面紧跟“-”或“-”及一串数字。
刀具功能字:
用以选择替换的刀具以地址符T为首,其后一般跟二位数字,该数
代表刀具的编号。
如T0808,自动调8号左偏刀8号刀补,开启冷却液。
主轴速度功能字:
指定主轴旋转速度以地址符S为首,后跟一串数字。
单位:
r/min,它与进给功能字的指定方法一样。
(2)程序内容
程序内容是整个程序的主要部分,由多个程序段组成,每个程序段由若干个字组成,每个字又由若干个数字组成。
常见的为G指令和M指令以及各个轴的坐标点组成的程序段,并增加了进给量的功能定义。
F功能是指进给速度的功能,数控车床进给速度有两种表达方式,一种是每转进给量,即用mm/r单位表示,主要用于车加工的进给。
另一种和数控铣床相同采用每分钟进给量,即用mm/min单位表示。
主要用于车铣加工中心铣加工中工的进给。
(3)程序结束
在程序结尾,需用刀架返回参考点或机床参考点,为下一次换刀的安全位置,同时进行主轴停止,关掉冷却液,程序选择停止或结束程序等动作。
停止指令M01为选择停止指令,只有当设备的选择停止开关打开时才有效;
M02
为程序结束指令,执行时,冷却液、进给主轴全部停止。
数控程序和数控设备复位并回到加工前原始状态,为一次程序运行和数控加工重新开始做准备。
11.2编辑程序
根据轴类加工零件图1的图样要求,我们进行了参数选择和设置,经过数值计算、后置处理,编写出零件加工程序单,如表3所示:
表3程序清单及说明
程序名:
程序编号:
O0001
零件图号;
时间:
程序
程序说明
G00X60Z0;
点定位
M03S460;
主轴以460r/min正转
M06T0101;
换一号端面刀,确定其坐标系
G00X100Z80;
到程序起点或换刀位置
G00X60Z5;
到简单端面循环起点位置
G81X0Z0;
简单端面循环加工,加工过长毛坯
到程序起点或换刀点位置
M06T0202;
换二号刀,进行外圆粗加工
G00X60Z3;
到简单外圆循环起点位置
G80X52.6Z-133F100;
简单外圆循环,加大过大毛坯直径
G01X52;
到复合循环起点位置
粗加工后,到换刀点位置
换二号刀,进行外圆精加工
G71U0.5R1P1Q2E0.3F100;
进行复合加工
N1
G00X0Z0;
G01X10F100;
精加工轮廓开始,到倒角延长线处
X19.5Z-2;
精加工倒2*45°
角
Z-33;
精加工螺纹外径
G01X30;
精加工Z33处端面
Z-43;
精加工Φ33外圆
G03X42Z-49R6;
精加工R6圆弧
G01Z-53;
精加工Φ42外圆
X36Z-65;
精加工下切锥面
Z-73;
精加工Φ36槽径
G02X40Z-75R2;
精加工R2过渡圆弧
G01X44;
精加工Z75处端面
X46Z-76;
精加工倒1*45°
Z-84;
精加工Φ46槽径
G02Z-122R70;
精加工R70圆弧凹槽
N2
G01Z-133;
精加工Φ52外圆
返回换刀点位置
M06T0303;
换三号刀切断刀
G01X20Z-26;
定位切断加工点
G01X19Z-33;
切第一刀,吃刀深1mm
返回切断处
G01X18Z-33;
切第二刀,吃刀深1mm
M05;
主轴停
M03S150;
主轴以150r/min正转
M06T0404;
换四号刀螺纹刀
G00X30Z5;
到简单螺纹循环起点位置
G82X19.3Z-26f2;
加工两头螺纹,吃刀深0.7mm
G82X18.7Z-26f2;
加工两头螺纹,吃刀深0.6mm
G82X18.3Z-26f2;
加工两头螺纹,吃刀深0.4mm
G82X18.1Z-26f2;
加工两头螺纹,吃刀深0.2mm
G82X18.0Z-26f2;
加工两头螺纹,吃刀深0.1mm
光整加工螺纹
返回程序起点位置
M02;
程序结束
5程序检验
编制好的程序,在正式用于生产加工前,必须进行运行检查。
在某些情况下,还需做零件试加工检查。
根据检查结果,对程序进行修改和调整,检查—修改—再修改—这往往要经过多次反复,直至获得完全满足加工要求的程序为止。
结论
通过这次的毕业设计,我从设计的过程中学到了很多在书本上没有的内容,加深了对数控机床的了解,巩固了书本的知识。
结论总结如下:
1.对于某个零件来说,并非全部加工工艺过程都适合在数控机床完成。
而往往只是其中的一部分适合于数控加工。
这就需要对零件图样进行仔细的工艺分析,选择那些最适合、最需要进行数控加工的内容和工序。
2.在确定走刀路线时,最好画一张工序简图,将已经拟定出的走刀路线画上去,这样可为编程带来不少方便。
3.有些零件虽然能在一次安装中加工出很多待加工面,但考虑到程序太长,会受到某些限制,如:
控制系统的限制(主要是内存容量),机床连续工作时间的限制等。
此外,程序太长会增加出错与检索困难。
因此程序不能太长,一道工序的内容不能太多。
致谢
本次的毕业设计,虽然时间不是太长,但却让我在作论文的这个过程中学到了很多的知识。
通过此次设计使我感悟到了毕业设计的重要性和必要性,为我们能够更好地迈入工作岗位做了充分的准备,是我从学生到技术人员转变的重要过渡,因此我十分重视学校给我提供的这次学习和锻炼的机会。
在毕业设计规定的时间内,我做了大量的咨询和总结,收集了较大的技术资料。
阅读了大量的专业文献,并将它们应用到了毕业设计当中,并在设计中进行了分析,研究。
同时在整个设计过程中,得到了指导教师的专业知识及其它知识的讲授,这将使我在以后的工作中有很大。
感谢所有老师的帮助,让我们的设计更加完美。
在此,也非常感谢
参考文献
(1)数控加工工艺基础,主编:
潭岭,重庆大学出版社;
(2)数空机床编程,主编:
杜国成,北京机械工业出版社;
(3)现代机械制造工艺,主编:
陈锡渠,北京清华大学出版社;
(4)数控机床加工工艺,主编:
华茂发,北京机械工业出版社;
(5)公差配合与测量技术,主编:
姚云英,北京机械工业出版社;
(6)机械设计基础,主编:
胡家秀,北京机械工业出版社;
(7)金属工艺学,主编:
万德金,北京机械工业出版社;