年产1000吨参苓健脾颗粒生产车间工艺设计论文Word文档下载推荐.docx
《年产1000吨参苓健脾颗粒生产车间工艺设计论文Word文档下载推荐.docx》由会员分享,可在线阅读,更多相关《年产1000吨参苓健脾颗粒生产车间工艺设计论文Word文档下载推荐.docx(21页珍藏版)》请在冰豆网上搜索。
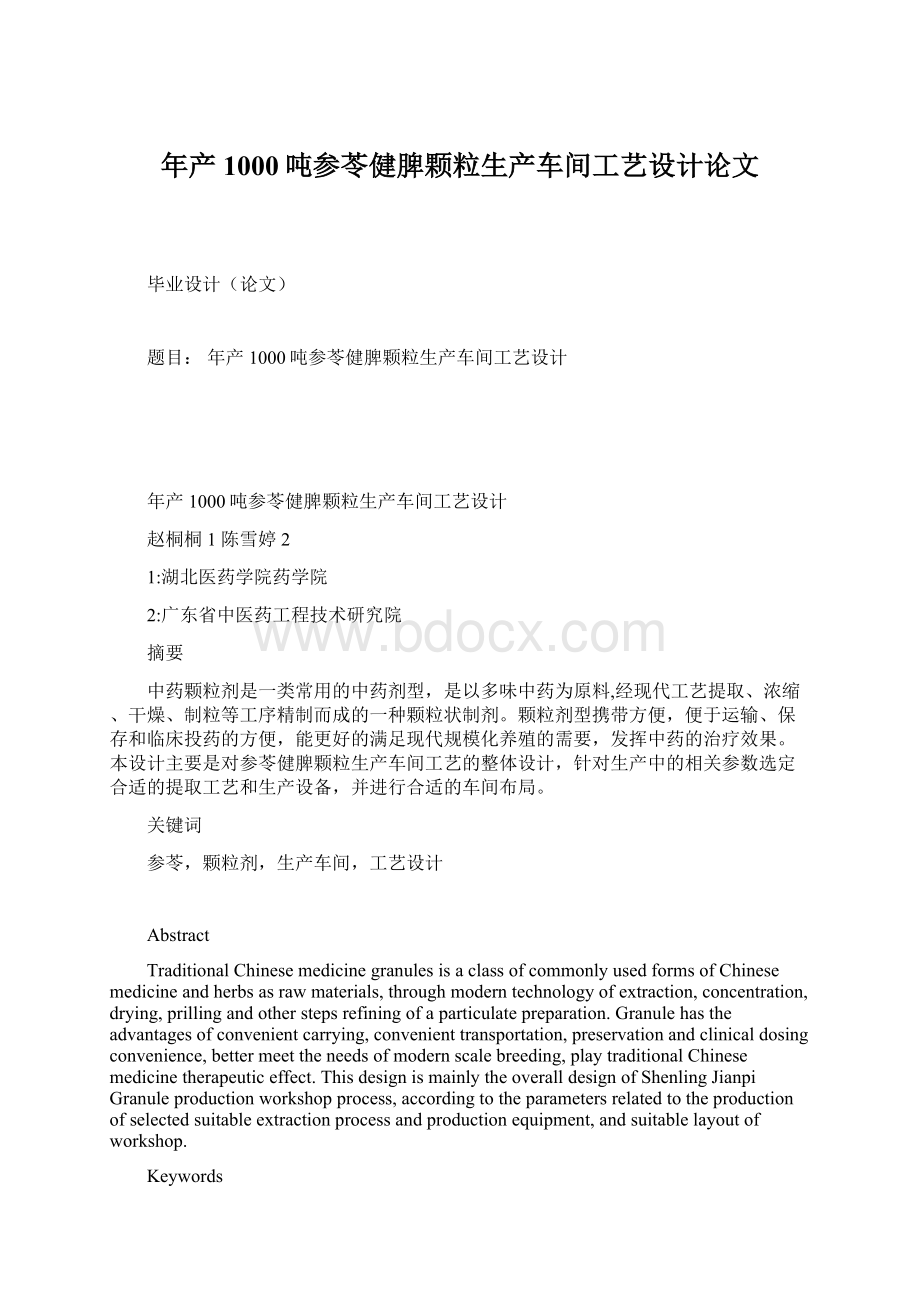
颗粒剂,取供试品,照水分测定法测定。
除另有规定外,不得超过5.0%。
1.1.3.4溶化性
取供试品(颗粒剂10g),加热水20倍,搅拌5分钟,可溶性颗粒剂应全部溶化,可以有轻微浑浊;
混悬性颗粒剂应能混悬均匀,不能有焦屑等异物;
泡腾性颗粒剂遇水时应立即产生二氧化碳气体,并呈泡腾状。
1.1.3.5硬度
取供试品5块,从lm高处平坠于厚度2cm松木板上,不得有一块破碎。
1.1.3.6装量差异
表1.1颗粒剂装量差异
颗料剂装置差异限度
标示装量
装置差异限度
1.0g或1.0g以下
±
10%
1.0g以上至1.5g
8%
1.5g以上至6.0g
7%
6g以上
5%
检查法:
取供试品10袋,分别称量每袋内容物的重量,每袋的重量与标示量相比较,超出限度的不能多于2袋,并不能有1袋超出限度1倍。
1.1.3.7重量差异
表1.2块形冲剂重量差异限度
块形冲剂重量差异限度
取供试品10块,分别称量每块内容物的重量,每块的重量与标示重量相比较,超出限度的不能多于2块,并不能有1块超出限度1倍。
1.1.3.8卫生标准
颗粒剂不得检出大肠杆菌、致病菌、活螨和螨卵;
不含药材原粉颗粒剂细菌不可多于1000个/g,霉菌不可多于100个/g;
含药材原粉的颗粒剂细菌数不可多于1000O个/g,霉菌数不可多于500O个/g。
其检查方法按卫生部《药品卫生检验方法》检查[2]。
1.1.4颗粒剂在制备与贮藏过程中易出现的问题
当直接制粒时,浸膏与辅料混合不均匀,这时会出现色泽不一现象,如果要二次制粒,要将浸膏、辅料搅拌干燥粉碎并进行制粒,制出的湿颗粒由于加乙醇浓度的不同,有时会出现较大颗粒,烘干后颗粒较大,整粒后颗粒不均匀[3]。
1.2参苓健脾颗粒剂简介
成分:
麸炒白术、茯苓、鸡内金、太子参、焦山楂、莱菔子、砂仁、山药、炒麦芽、焦神曲
性状:
棕黄色颗粒;
气芳香,味甜
功能主治:
补脾健胃,利湿止泻。
用于脾胃虚弱,消化不良,泄泻呕吐,精神萎靡,全身乏力。
第二章处方设计及工艺
2.1参苓健脾颗粒剂处方设计
2.1.1处方
麸炒白术10g茯苓10g鸡内金10g太子参10g
焦山楂10g莱菔子7g砂仁3g山药10g
炒麦芽10g焦神曲10g
2.1.2辅料的选择原则
选择辅料一般有以下原则:
1.加入的辅料应增加药物的物理和化学稳定性。
2.辅料与药粉混合后得到的混合物应具有适当的流动性和分散性。
3.选用辅料应可提高或者不妨碍制剂药效的功能。
4.辅料的加入不会增加制剂的毒副作用,最好能改善制剂功效[4]。
第三章工艺流程
3.1设计概述
3.1.1课题名称
3.1.2设计依据
本设计以中国2015年药典和相关材料作为依据,同时参考《制药工程工艺设计》、《药品注册管理办法》、《医药工业洁净厂房设计规范》、《药品生产质量管理规范》、《药品生产质量管理规范指南》等多种设计规范。
3.1.3设计原则
(1)本设计为颗粒剂车间,在设计中严格遵照《药品生产质量管理规范》和《医药工业洁净厂房设计规范》等标准进行设计。
(2)对设备的选择,应考虑其是否能够完成生产任务,且具有节能高效,经济方便,实用可行,符合药品生产质量管理规范生产等优点。
(3)为保证控制区的洁净度要求,采用全封闭的空调系统。
(4)遵守防火,安全,卫生,环保,劳动保护等相关规范制度。
(5)严格质量管理制度,推行质量责任制,严格工艺设计质量。
3.2工艺流程介绍
制剂工艺流程是以保证处方的功能主治为目的,围绕功能主治的要求,对药物的处理原则、方法和程序所作的最基本的规定。
它决定着制剂质量的好坏,也决定着制剂大生产的可行性和经济效益。
工艺流程的选择需根据药物的性质、制剂剂型以及药物的类别要求、生产可行性、生产成本等因素来决定[5]。
颗粒剂的制法:
湿法制粒、干法制粒、喷雾制粒。
(1)湿法制粒是指将药物细粉或稠膏与辅料放于合适的容器内混合均匀,加入润湿剂制成“手捏成团,轻压即散”的软材,再用挤压方式通过14~22目筛网,制成均匀的颗粒。
小剂量制备可以用手工制粒筛,大生产用摇摆式颗粒机或者旋转式制粒机。
(2)干法制粒可以通过滚筒平压制粒机完成[6]。
具有一定的相对密度的中药提取液,经过喷雾干燥得到干浸膏粉,添加辅料后,用干挤制粒机压成薄片,再粉碎成颗粒。
该法所用辅料少,有利于提高颗粒的稳定性、崩解性和溶散性。
(3)喷雾干燥制粒先将适当处理后的药材浸提液,经过喷雾干燥制成干浸膏粉,然后加入辅料,用干挤制粒机制粒。
工艺流程图:
图3.1
3.2.1提取
中药的提取方法有水煎煮法、浸渍法、渗漉法、回流法、溶剂提取法、水蒸气蒸馏法和升华法等。
溶剂提取法是应用最广泛的方法,它是根据中草药中各种有效成分溶解度的性质,选择对所需成分溶解度大而对其他成分溶解度小的溶剂,将所需的活性成分从药材中溶解出来的一种提取方法。
常见的提取溶剂可分为以下三类:
(1)水:
水是一种强的极性溶剂。
中草药中亲水性的成分,如无机盐、糖类、分子不太大的多糖类、鞣质、氨基酸、蛋白质、有机酸盐、生物碱盐及甙类等都能被水溶出。
为了增加某些成分的溶解度,也常采用酸水及碱水作为提取溶剂。
(2)亲水性的有机溶剂:
就是一般与水能混溶的有机溶剂,如乙醇、甲醇、丙酮等,乙醇最常用。
乙醇的溶解性能比较好,对中草药细胞的穿透能力较强。
亲水性的成分除蛋白质、粘液质、果胶、淀粉和部分多糖等外,大多能在乙醇中溶解。
难溶于水的亲脂性成分,在乙醇中的溶解度也较大。
用乙醇提取比用水量较少,提取时间短,溶解出的水溶性杂质也少。
乙醇为有机溶剂,虽易燃,但毒性小,价格便宜,来源方便,有一定设备即可回收反复使用,而且乙醇的提取液不易发霉变质。
由于这些原因,用乙醇提取的方法是最常用的方法之一。
(3)亲脂性的有机溶剂:
就是一般与水不能混溶的有机溶剂,如石油醚、苯、氯仿、乙醚、乙酸乙酯、二氯乙烷等。
这些溶剂的选择性能强,不容易提出亲水性杂质。
如果药材中含有较多的水分,这类溶剂就很难浸出其有效成分,因此,大量提取中草药原料时,直接应用这类溶剂有一定的局限性。
通过对文献资料的研究,有效的总结出本处方药材同功能主治及现代药理作用相关的主要有效成分主要存在于水提取液中,结合本处方在临床运用中一直以汤剂入药有效的现状以及生产设备条件,确定提取工艺是鸡内金打粉入药,其余药味采用水煎煮提取[7]。
3.2.2筛分
筛分是将不同粒度的混合物料按粒度大小进行分离的操作。
筛分法是借助筛网将物料进行分离的方法。
筛分法操作简单,经济且分级精度较高,是医药工业中应用最广泛的分级操作之一。
3.2.3混合
混合就是把两种以上物质均匀混合的操作。
混合过程是以细微粉体为主要对象,具有粒度小,密度小、附着性、凝聚性、飞散性强等。
合理的混合操作是保证制剂质量的重要措施之一。
混合的机理有三种:
对流混合在机械转动下固体粒子群体产生大幅度位移时进行的总体混合。
剪切混合由于粒子群内部力的作用结果,在不同组分的区域间发生剪切作用而产生滑动面,破坏粒子群的凝聚状态而进行的局部混合。
扩散混合相邻粒子间产生无规则运动时相互交换位置而进行的局部混合。
混合的影响因素有:
a)物料的粉体性质的影响。
b)设备类型的影响。
c)操作条件的影响。
3.2.4制粒
制粒是把粉末、水溶液等状态下的物料经加工制成具有一定形状与大小粒状物的操作,是颗粒剂生产中最终的流程,制粒作为颗粒的加工过程,几乎与所有的固体制剂有关。
3.2.5干燥
干燥是利用热能使物料中的湿分汽化,并利用气流或真空带走汽化湿分而获得干燥产品的操作。
干燥除去的湿分多数为水,一般用空气作为带走湿分的气流。
物料干燥的加热方式一般有:
热传导、对流、热辐射、介电等,而对流加热干燥是制药过程中应用最广泛的一种方式,简称对流干燥。
3.2.6整粒
制粒过程中制成的湿颗粒由于含有水分和粘性成分,在干燥过程中容易发生粘结成团,造成颗粒的粒径过大,影响颗粒的流动性,所以要通过整粒设备使干颗粒形成粗细均匀且流动性强的药物颗粒。
第四章物料衡算
4.1物料衡算的基础
物质的质量守恒定律是物料衡算的基础,即进入一个系统的全部物料必等于离开系统的全部物料,再加上过程中的损失量和在系统中的积累量。
∑G1=∑G2+∑G3+∑G4
式中:
∑G1—输入物料量总和;
∑G2—输出物料量总和;
∑G3—物料损失量总和;
∑G4—物料积累量总和。
当系统内部积累量为零时,上式可以写为:
∑G1=∑G2+∑G3
4.2物料衡算的基准
(1)对于间歇式操作过程,常采用一批原料进行计算。
(2)对于连续式操作过程,可以采用单位时间产品数量或原料量为基准进行计算。
物料消耗的结果应列成原材料消耗定额和消耗量表,在计算时应把原料、辅料及主要包装材料一起算入。
4.3物料衡算的条件
年产量:
1000吨
一年按300个工作日计算,每天两个班次,每班实际工作时间8小时。
处方:
制成干膏
干膏粉:
麦芽糊精=3:
1
甜菊素的加入量为成品量的2%
参苓健脾颗粒的年产量:
日产量:
3.33吨
班产量:
1.67吨
损耗:
原辅料5%其他均不计
每年原辅料需求量:
735+735*5%=771.75吨干膏粉得率为30%
麦芽糊精:
245+245*5%=257.25吨
甜菊素:
20吨+20*5%=21吨
原药材:
共2572.5吨
麸炒白术,茯苓,鸡内金,太子参,焦山楂,山药,炒麦芽,焦神曲各285.8吨,莱菔子200吨,砂仁85.8吨
第五章设备的选型
5.1工艺设备的设计与选型
5.1.1生产设备选型的说明
设备选型是工艺设计的主要内容,在设备选型问题上应坚持GMP的要求。
1、从设计角度看GMP对制剂设备的要求[8]
GMP认证达标中一个重要内容是设备验证,它包括设备的安装确认(IQ)、运行确认(OQ)、性能确认(PQ)和投产后的产品验证(PV)四个阶段,制剂设备要达标,关键在于制剂设备在设计、选型、制造和安装上要符合GMP标准。
要达到GMP标准,制剂设备在具体设计中应体现符合产品生产及工艺要求、安全、稳定、可靠以及易于清洗、消毒或灭菌,便于生产操作和维修保养,并能防止差错和交叉污染的总体思想。
在设计中凡与药品直接接触的设备内表面及工作零件表面,尽可能不设计有台、沟及外露的螺栓连接。
设备内外表应平整、光洁、无棱角、无死角、无凹槽、易清洗与消毒。
同时,为不对装置之外构成污染,设备应采用防尘、防漏、隔热、防噪声及防爆等措施。
设备的选材应严格控制,凡与药品直接接触的零部件均应选用五毒/耐腐蚀/不与药品发生化学反应/不释出微粒或吸附药品的材质。
无菌设备的清洗,尤其是直接接触的部件必须灭菌,除采用一般方法外,最好配备就地清洗(GIP),就地灭菌(SIP)的洁净、灭菌系统等。
同时设备设计还应满足GMP对制剂设备在安装、维修、保养、管理和验证等方面的一系列要求。
5.1.2工艺设备设计与选型的步骤
工艺设备设计与选型分两个阶段,第一阶段有以下内容:
①定型机械设备和制药机械设备的选型;
②计量贮存容器的计算;
③确定非定型设备的形式、工艺要求、台数、主要规格。
设备选型的步骤:
首先了解所需设备的大致情况.国产或者引进,使用厂家的使用情况,生产厂家的技术水平等;
其次是搜集所需资料,目前国内外生产制剂设备的厂家很多,技术水平和先进程度也各不一样;
然后,核查与本设计所要求的是否一致;
最后到设备制造厂家了解其生产条件和技术水平及售后服务等。
优良的产品必须要有精良的设备作保证,GMP要求使用符合其标准的设备。
设备是根据生产要求和设备的生产能力的对比而选定的。
通常情况下,所选设备的生产能力应大于生产任务。
但是不能过大,否则就会造成浪费9]。
5.2主要设备选型
5.2.1提取设备
中药所含成份十分复杂,既含有多种有效成份,又有无效成份,也包含有毒成份。
提取有效成分并进一步加以分离、纯化,得到有效单体是中药研究领域中的一项重要内容[10]。
中药提取就是利用一些技术尽可能提取其中的有效成份,使中药制剂的质量和临床治疗效果提高,使中药的效果得以最大限度的发挥[11]。
图5.1TQ-8提取罐
表5.1TQ-8提取罐
规格/型号
TQ-8
有效容积
8000
罐内设计压力(MPa)
常压
夹层工作压力(MPa)
0.1-0.4
夹套工作压力(MPa)
0.6-0.8
加料口直径(mm)
500
加热面积(㎡)
14.5
冷凝面积(㎡)
14
冷却面积(㎡)
2
过滤面积(㎡)
5
排渣门直径(mm)
1400
搅拌转速
25-120R/min
电动机功率kw
7.5
设备质量kg
4030
根据物料衡算,日需处理原料药为8.575吨,两班次,一班4.2875吨,提取工艺为提取两次,加十倍水,提取1.5小时,所以一班可以提取两次,每次需要提取2.14吨,所以该工艺选择4个8吨提取罐,每个提取罐按75%的装量,也就是可装6吨,4个就是24吨,大于2.14+2.14*10=23.54吨,满足工艺要求。
提取罐性能指标详见图5.1,表5.1
5.2.2筛分设备
筛分是将不同粒度的颗粒按粒度大小进行分离的操作。
筛分法是借助筛网将颗粒进行分离的方法。
筛分法操作简单,经济而且分级精度较高,是医药工业中应用最广泛的分级操作之一。
筛分的目的是为了得到均匀粒度的颗粒。
这对药品质量以及制剂生产都有重要的意义。
筛分的药筛按制作方法分冲眼筛、编织筛两种,因为本设计所涉及的原辅料硬度不大,设计中选择编织筛。
(1)筛孔
药筛的径孔大小用筛号表示,筛子的孔径规格有药典标准和工业标准。
药典选用国家标准的R40/3系列。
见表5.2:
表5.2我国药典标准筛规格表
筛号
1
3
4
6
7
8
9
平均筛孔内径(μm)
2000
70
850
29
355
13
250
9.9
180
7.6
150
6.6
125
5.8
90
4.6
75
4.1
我国工业用标准筛常用“目”数表示筛号,即以每一英寸(25.4mm)长度上的筛孔数目表示,表5.3列出了部分工业筛的规格。
根据颗粒剂的生产要求,规定原辅料通过80目钢丝筛。
表5.3工业筛规格
目数
锦纶纳纶
(μm)
镀金铁丝
铜丝
钢丝
1300
1430
1375
16
1170
1211
1270
18
1060
1096
20
920
954
955
960
40
380
441
462
80
210
100
172
170
(2)筛分设备
筛分设备有许多种,如:
摇动筛、振动筛、旋动筛、滚动筛、多用振动筛等。
振动筛是利用机械或电磁作用使筛产生振动将物料进行分离的设备。
本设计选用JH系列三次元旋振筛,见图,相关参数见图5.2,表5.4
图5.2JH三次元旋振筛
表5.4JH三次元旋振筛
型号
公称直径(mm)
筛面直径
有效筛面直径
最大入料粒度
筛面规格(目/英寸)
层数
振次(Rpm)
功率(Kw)
JH-400
400
340
0.09
<10
2-325
1-3
1500
0.18
JH-600
600
530
0.22
0.25
JH-800
800
720
0.4
<20
0.55
JH-1000
1000
900
0.63
0.75
JH-1200
1200
1100
0.95
1.1
JH-1500
1.5
2.2
JH-1800
1800
1710
2.3
<30
JH-2000
1910
2.86
5.2.3混合设备
用机械的或流体动力的方法,使两种或多种物料相互分散而达到一定均匀程度的单元操作。
混合在化工生产中的应用十分普遍,其目的主要是:
①制备均匀的混合物;
②为某些单元操作或化学反应过程提供良好的条件。
在制备均匀混合物时,混合效果以混合物的混合程度来衡量。
所谓混合,就是在外力的作用下,各种物料组分互相掺合,使之在容积里各种组分的微粒均匀分布。
它是确保物料质量和提高物料效果的重要环节。
混合的方法有多种,如机械式混合、气动式混合、冲动式混合等,其中机械式混合较为常见。
以机械式搅拌混合为例,其混合过程可分为3个阶段:
首先以散状物料小块运动形成的对流混合为主,混合均匀度迅速提高;
其次,粒子问的相互滑动与冲击,或桨叶与壁面之间的压缩与伸延的剪切作用,混合速度平稳;
第三,粒子位置交换的扩散作用与分离作用达到平衡状态,即混合均匀性保持稳定或稍有波动。
完成上述过程一般只需2-6分钟,但不同的混合机有不同的均匀混合的时间要求。
本设计采用HD多向运动混合机HD-1000,见图5.3,参数见表5.5
图5.3HD多向运动混合机HD-1000
表5.5HD多向运动混合机HD-1000
规格
HD-1000
料筒容积(L)
最大装料容积(kg)
主轴转速(r/min)
8-15
电机功率(kw)
外形尺寸(宽*深*高)
2250*2600*2300
整机重量(kg)
2500
5.2.4制粒设备
制粒的原理:
制粒操作使颗粒具有某种相应的目的性,以保证产品质量和生产的顺利进行。
制粒方法有多种,制粒方法不同,即使是同样的处方不仅所得制粒物的形状、大小、强度不同,而且崩解性、溶解性也不同,从而产生不同的药效。
因此,应根据所需颗粒的特性选择适宜的制粒方法[12]。
制粒的目的:
①改善流动性。
一般颗粒状比粉末状粒径大,每个粒子周围可接触的粒子数目少,因而黏附性、凝集性大为减弱,从而大大改善物料的流动性。
②防止各成分的离析。
混合物各成分的粒度、密度存在差异时容易出现离析现象,混合后制粒或制粒后混合可有效防止离析。
③防止粉尘飞扬及器壁上的黏附。
粉末的粉尘飞扬及黏附性严重,制粒后可防止环境污染与原料的损失,有利于GMP的管理。
④调整堆积密度,改善溶解性能。
⑤改善片剂生产中压力的均匀传递。
⑥便于服用,携带方便,提高商品价值等。
在医药生产中广泛应用的制粒方法可以分为三大类:
湿法制粒、干法制粒、喷雾制粒,其中