电脱盐工作原理Word文件下载.docx
《电脱盐工作原理Word文件下载.docx》由会员分享,可在线阅读,更多相关《电脱盐工作原理Word文件下载.docx(8页珍藏版)》请在冰豆网上搜索。
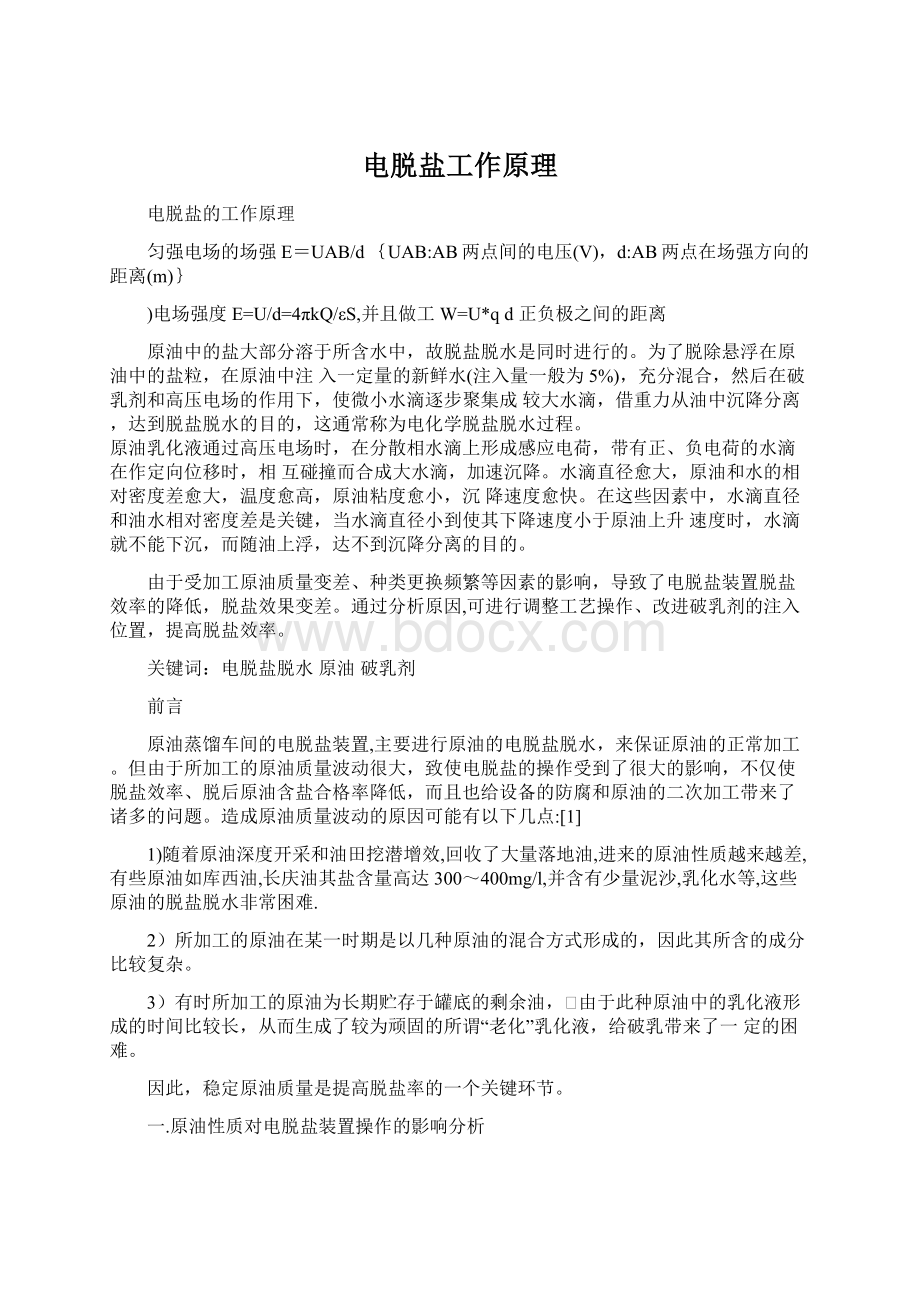
但由于所加工的原油质量波动很大,致使电脱盐的操作受到了很大的影响,不仅使脱盐效率、脱后原油含盐合格率降低,而且也给设备的防腐和原油的二次加工带来了诸多的问题。
造成原油质量波动的原因可能有以下几点:
[1]
1)随着原油深度开采和油田挖潜增效,回收了大量落地油,进来的原油性质越来越差,有些原油如库西油,长庆油其盐含量高达300~400mg/l,并含有少量泥沙,乳化水等,这些原油的脱盐脱水非常困难.
2)所加工的原油在某一时期是以几种原油的混合方式形成的,因此其所含的成分比较复杂。
3)有时所加工的原油为长期贮存于罐底的剩余油,由于此种原油中的乳化液形成的时间比较长,从而生成了较为顽固的所谓“老化”乳化液,给破乳带来了一定的困难。
因此,稳定原油质量是提高脱盐率的一个关键环节。
一.原油性质对电脱盐装置操作的影响分析
由于原油来源紧张,原油质量与以往相比波动很大,从而直接影响了电脱盐装置的平稳操作。
通过对兰州石化炼油厂的调查进行分析,分析结果如下图表。
表1原油盐含量的变化对脱盐效率及脱后合格率的影响
项目库西原油含盐量脱盐率%脱后合格率%
180.094.264.0
256.793.667.2
358.392.057.4
491.390.050.5
5409.985.012.2
注:
数据取自岗位记录,采用库仑仪法
表2某一时期原油盐含量的变化情况
调查对象库西原油
调查项目123456
原油盐含量(mg/l)224.8121.0125.0345.0122.093.5
脱后盐含量(mg/l)11.86.46.515.95.62.3
通过对表1,2,及图1及2的分析可以看出:
原油质量不断在变,同时脱盐后的原油的含盐量和合格率也在不断变化,特别是盐含量很高时,平均高达300~400毫克/升,脱盐率和脱后合格率也相应的下降了10%和40%。
这对生产操作是非常有害的,这是因为:
盐易结垢从而影响传热效率,而且,MgCl2、CaCl2等盐还容易造成腐蚀,同时,在馏分油中的盐类还会影响最终产品的品质等。
二.改善电脱盐装置脱盐效果的途径
基于分析的基础上,结合生产实际,不妨通过以下的途径来改善电脱盐装置的操作,以此来缓解由于原油质量的不稳定所带来的诸多影响。
1.调整工艺参数
电脱盐装置的主要工艺参数为:
操作压力、操作温度、电场强度、原油在电场中的停留时间、注水量等[2]。
从实际生产过程来看,原有的操作参数在适应原油性质变化大,种类更换频繁这一生产实际的过程中充分的暴露出不足。
因此可以通过调整工艺参数来提高电脱盐装置的操作水平。
(1)温度的调整
如果常减压装置加工负荷还未达到工艺设计水平导致了原油经换热管网后进入电脱盐装置的温度就会低于正常温度(110°
C左右),此进装置的温度是比较低的。
较高的温度,可以使原油的粘度降低,减少水滴的运动阻力。
同时,较高的温度还有利于油水界面张力的降低,从而使水滴受热膨胀,乳化膜减弱,有利于破乳和聚结。
另外,温度还可以通过影响油水密度差、原油粘度而影响水滴的沉降速度,从而影响脱盐效率。
因此,提高原油进电脱盐装置的温度是很有利的。
(2)电场强度的调整
电场强度是影响电脱盐效率的一个主要的工艺参数。
每一种原油都有与其相适应的脱盐电场强度,过高或过低都会使脱盐率降低。
在原油质量稳定的情况下,19KV的电场强度是可以满足生产的需要,但是,当原油质量波动很大时,它的不足就表现的很明显。
北京石化设计院通过分析研究总结出脱盐率、停留时间及电场强度三者间的相互关系(见图3).
脱盐率(%)
94T1T:
表示停留时间
T1:
2.25小时
92T2
T2:
1.00小时
90
15002000电场强度(V/cm)
图3脱盐率、停留时间、电场强度关系
通过对上图的分析可以看出:
在停留时间一定的条件下,提高电场强度有利于脱盐率的提高。
因此在实际的生产中可根据原油盐含量高这一实际情况,适当的调节电压使电场强度增强以此来满足生产的需要。
(3)注水量的调整
在原油脱盐的过程中,注入一定量的新鲜洗涤水的目的主要是与原油混合,增加水滴的密度使之更易聚结,同时注水还可以破坏原油乳化液的稳定性,对脱盐有利[3]。
下面通过表3具体的说明一下注水量及注水含盐对脱盐率的影响。
表3注水量及注水含盐对脱盐率的影响
原油含水(w%)0.20.20.20.20.20.20.20.20.20.20.20.2
脱前原油含盐(m/L)202020202020202020202020
注水量(占原油量%)456456456456
注水含盐(mg/L)000150150150250250250350350350
脱水含水0.6(mg/L)2.862.311.943.903.162.804.273.743.384.844.313.95
脱盐率(%)85.788.590.381.584.286.078.681.383.175.778.480.2
脱水含水0.4(mg/L)1.911.511.282.472.111.872.852.502.263.232.882.64
脱盐率(%)90.592.393.687.789.590.785.887.588.783.985.986.5
脱水含水0.2(mg/L)0.960.770.651.241.060.941.431.251.131.621.441.32
脱盐率(%)95.296.296.893.894.795.392.993.894.491.292.893.4
通过表3可以发现:
1.在原油含水及脱前原油含盐量一定的条件下,注水量由4%提高到6%,其脱后含盐量降低,脱盐率提高。
2.在原油含水、脱前原油含盐量及注水量一定的条件下,注水含盐量增加(由0毫克/升增至350毫克/升),导致脱盐率降低(由90.3%降至80.1%)
因此,在实际的操作中,可以根据生产的需要将新鲜脱盐水的注入量适当提高,于此同时还应考虑注水的盐含量,后者往往在生产中容易被忽视。
表4调整前后原油性质、脱盐率及脱后合格率的情况调查
原油种类项目原油盐毫克/升脱盐率%合格率%
库西原油1409.985.0调整前:
12
2332.493.9
吐哈原油3158.589.0
493.092.1调整后:
33
长庆原油5137.086.4
6126.195.0
备注:
盐含量采用库仑仪法测定
由表4看出,经对工艺参数的调整,三种原油在原油质量好转不大的情况下,其脱盐率和脱后合格率均有所上升,从而缓解了因原油质量变差给电脱盐装置带来的诸多问题但是,值得说明的是:
脱后合格率虽有所提高(上升了21%),但仍显过低,待今后进一步完善提高。
2.破乳效果的调整
在装置正常运行的情况下,电脱盐的效果好坏除受工艺参数的影响外,还直接受破乳效果的影响.破乳效果不够理想主要表现为原油二级脱后含水量高导致盐含量偏高。
这主要是因为一级脱盐罐主要脱除了悬浮于原油中的盐(大部分)及部分存在于油包水型乳化液中的原油盐。
二级脱盐罐主要脱除的存在于乳化液中的原油盐,由于破乳效果不好,二级脱后水份含量高,从而导致了原油盐脱不下来。
造成破乳效果不理想的原因主要有两方面:
(1)破乳剂的影响
破乳剂的影响关键在于使用的破乳剂的型号与所加工的原油不匹配。
同时破乳剂的影响还表现在其很难适应原油种类更换频繁、质量差的生产实际[4]。
因此,针对上述情况,不妨考虑采取以下的方法:
(1)重新对原油进行破乳剂的评价。
(2)不妨将两种或两种以上的破乳剂或采用几种破乳剂以一定的比例混合构成一种新的破乳剂(混合型破乳剂),其破乳脱水效果可能高于任何一种单独使用时的效果,此种现象称为破乳剂的协同效应。
(2)破乳剂注入流程的影响
破乳剂注入流程对脱盐效果的好坏也有一定的影响。
目前电脱盐装置的破乳剂注入流程如图4所示:
图4破乳剂注入流程
通过上图所示可以看出:
由于破乳剂注入流程比较短、注入点少,因此不利于破乳剂与原油的充分混合,更无法使破乳剂均匀的分散到原油中,不能到达水滴表面,很难起到很好的破乳效果。
因此,不妨将目前的破乳剂的注入流程进行一下改进使之趋于合理。
办法为:
将以往的破乳剂与水一同注入原油中的方式改为破乳剂在注水前注入原油中,注入点由原来的B-116和B-1211的入口处改在B-211/1,2,3,4的入口处。
这样的改动可以使原油与破乳剂能通过原油泵和换热管网这一路途进行充分的混合,可以达到比目前要好的破乳效果。
另外一种提高破乳效果的方法是:
将目前一个注入点增加为两个或三个,中石化辽阳石油化纤公司炼油厂将其电脱盐装置的注入点由一个增加为三个,脱盐率由35%上升至78%,取得了较好的效果。
结论
1)提高原油进电脱盐装置的温度是很有利的.
2)适当的调节电压使电场强度增强可满足生产的需要。
3)在原油含水、脱前原油含盐量及注水量一定的条件下,注水含盐量增加(由0毫克/升增至350毫克/升),导致脱盐率降低(由90.3%降至80.1%)
4)破乳剂位置的改变可以提高脱盐效率。
3.电脱盐工艺、设备的优化调整与升级改造
为应对原油劣质化的总体趋势,电脱盐系统自身工艺流程也需要作出必要的优化调整,比如原油换热工艺网络的优化、注水工艺的调整、脱盐罐内电场结构布局的优化、反冲洗位置和排水流程的调整、混合阀的升级等等。
为从根本上解决问题,要求今后新增的电脱盐装置在设计阶段就充分考虑原油重质化趋势的实情,在电脱盐工艺的设计上作出必要的优化调整。
3.1工艺流程的改造
根据上文的论述,原油电脱盐工艺需要进行以下几方面的优化调整:
一是电脱盐工艺流程上要能实现根据装置加工负荷、原油性质变化而在“并联工艺”与“串联工艺”之间进行自由调整。
比如,在负荷较低的情况下,根据本装置实际情况在局部改并联操作为串联操作(如一级两脱盐罐由并联改串联等等),如此可相应改善脱盐效果,并提高装置的操作弹性。
二是常减压装置工艺换热网络要进行整体上的优化调整,目标是确保原油各级电脱盐温度能够达到加工重质原油的要求,这其中还包括换热工艺需要对各级注水的水温有所保证。
三是注水位置、注破乳剂位置、反冲洗位置的优化调整。
实践证明,注水、注破乳剂位置的不同对整个电脱盐装置的脱盐效果、操作稳定性有微妙的影响,电脱盐注水最好采用逐级回注的模式,同时注意根据原油性质的变化,以及所选用的油溶性或水溶性等不同的破乳剂类型对破乳剂注入位置进行必要的优化调整。
另外为了确保电脱盐罐的反冲洗效果,防止因反冲洗引起油水界面的波动,最好是增加独立的反冲洗系统,并实现用脱盐切水进行反冲洗操作。
四是在原油进电脱盐罐前增设热沉降罐,这样可以有效地将原油中的部分杂质甚至泥沙有效地沉降下来,相当于增加原油的沉降时间,从而减轻了原油性质变化对一级电脱盐罐的直接冲击。
另外,还可考虑根据实际情况增设一台脱盐污水沉降罐,增加油水沉降时间以确保水质环保指标,严格控制脱盐污水含油指标不大于150PPM。
可积极采用新技术,例如中原炼厂应用石油大学旋流除油技术来控制污水含油指标,产生了很好的工艺效果。
3.2脱盐罐内电场结构的调整
现在的电脱盐装置一般采用交直流电脱盐技术,建议直流电极板可由水平分布改为垂直分布,这样可以获得更大的电场容量以及更加合理的电场梯度,还能使原油在强电场中的停留时间得到适当延长,对破乳与油水分离很有利。
部分原油电脱盐装置还可根据自身的脱盐罐结构,对原油分配器、收集器等做出相应改动,适当增加圆弧电极板面积,以增强本装置对重质原油的适应性。
3.3
关键设备及其控制技术的升级
根据加工重质原油时出现的各类问题,电脱盐装置在设备上应做好以下几个方面的工作:
一是对混合阀进行升级,应选用混合效果更好,控制水平更高的混合阀(比如最好由手动控制改为自动控制,以提高控制效率),要在混合器产品的性价比上做足文章。
二是做好电脱盐装置的防腐工作,以应对加工劣质原油的需要。
由于原油硫含量、酸值指标的变化,尤其目前开发的脱钙脱金属剂大多为酸性化合物,电脱盐装置应用脱金属剂,出现酸腐蚀与盐腐蚀共存并且相互叠加的危害,因此电脱盐防腐工作必须引起我们足够的重视,这也是确保电脱盐装置“安稳优”运行的前提。
目前一种新型的电脱盐装置缓蚀防腐技术已经得到开发和成功应用,比如以NC-6高温有机缓蚀剂为主合成的高效缓蚀剂,就是针对电脱盐装置防腐的一种有效的缓蚀剂技术,尤其对解决加工高钙稠油时的腐蚀问题具有现实意义。
三是在电脱盐主体设备许可的条件下,对变压器等电气设施进行必要的更新换型,确保电气部分在加工劣质原油时性能的可靠性,以提高整个电脱盐装置运行的平稳性。
四是对仪表控制系统进行升级改造。
比如用射频导纳界位仪代替内浮筒界面变送器,可以显著改善电脱盐罐界位的控制效率。
为适应原油重质化的趋势,杜绝油水乳化严重界位不清的影响,也可以考虑采用微差压式界面变送器,从而更好地控制油水界位参数,以确保电脱盐工艺的优质平稳运行。
4.新型电脱盐技术及其应对原油重质化趋势的优势
由于影响原油电脱盐效果的影响因素很多,目前所进行的电脱盐技术研究也呈现出一种多元化的局面,主要可以总结为以下三个方面的研发:
一是研究开发新型的电极板结构,如三层极板、鼠笼极板等;
二是研究开发不同的电场方式和破乳方式,如交直流电场、脉冲电场、微波破乳、超声波破乳等;
三是研究开发高效广谱的破乳剂技术,包括在脱盐助剂方面的研发。
可以说,新型电脱盐技术的研发进展为应对原油劣质化趋势,解决电脱盐实际生产问题具有重大影响。
以下分别介绍相对比较成熟的脉冲电脱盐技术和超声波电脱盐技术。
4.1脉冲电脱盐技术及其应用
脉冲电脱盐技术是新一代的原油电脱盐技术,它采用脉冲方波电压,形成高压、脉冲式电场,这完全不同于以往的交流或交直流电脱盐电场。
脉冲电脱盐的基本原理是:
脉冲电场下,原油中的油水乳化颗粒在瞬间形成的高压电场下被极化,水滴之间的聚结力大大增加,从而电脱盐效果得到显著改善。
脉冲供电系统的特点是:
采用微电脑控制的脉冲变压器,可以直接通过电脑操作屏设置电脱盐系统的工作电压、频率等指标,实现恒压控制以及对电场击穿保护的跟踪控制,与传统的全阻抗变压器相比,脉冲式电脱盐技术对原油重质化趋势具有更强的适应性,也解决了电流过载和短路的技术难题。
该技术在中石化洛阳分公司和胜利石油化工总厂电脱盐装置上的应用表明,能够显著提高电脱盐效率,并起到了节省电耗和降低破乳剂消耗的作用,具有很好的应用前景。
4.2
超声波电脱盐技术及其应用
在应对原油劣质化的问题上,现有的原油电脱盐装置不仅破乳剂消耗量大,而且脱盐效果也并不是很理想,这将给后续炼油生产与加工过程造成相当大的负面影响。
超声波—电脱盐组合工艺具有无污染、能耗低、投资少、效果好等技术优点,对原油性质变化也具有更强的适应能力。
其理论基础是,通过超声波作用使原油中的水滴粒子产生位移效应,破坏原油油水乳化结构,使微小的水粒高速聚合下沉,达到高效分离油水的工业目的。
国内首个达到工业应用技术条件的超声波—电脱盐组合技术是由中石化齐鲁分公司研究院研发的,并首次在齐鲁石化第一套常减压装置的进行了成功的工业应用。
近年来的工业应用结果表明,该技术不仅能显著改善脱盐效果,也能有效节省了破乳剂消耗和电费,大大降低了操作费用与运行成本。
应用超声波-电脱盐组合技术对于大多数厂家而言都是一个可行的工艺技术路线,因为它可以在保持电脱盐装置原流程基本不变的情况下,通过在原油出混合器之后进脱盐罐之前的增设一条同径付线,并在此付线上安装数台超声波发生器就可实现对注水原油发射出顺逆流超声波,使乳化液受到超声波的物理激发效应而强化了破乳效果。