烃类蒸汽转化催化剂讲义文档格式.docx
《烃类蒸汽转化催化剂讲义文档格式.docx》由会员分享,可在线阅读,更多相关《烃类蒸汽转化催化剂讲义文档格式.docx(67页珍藏版)》请在冰豆网上搜索。
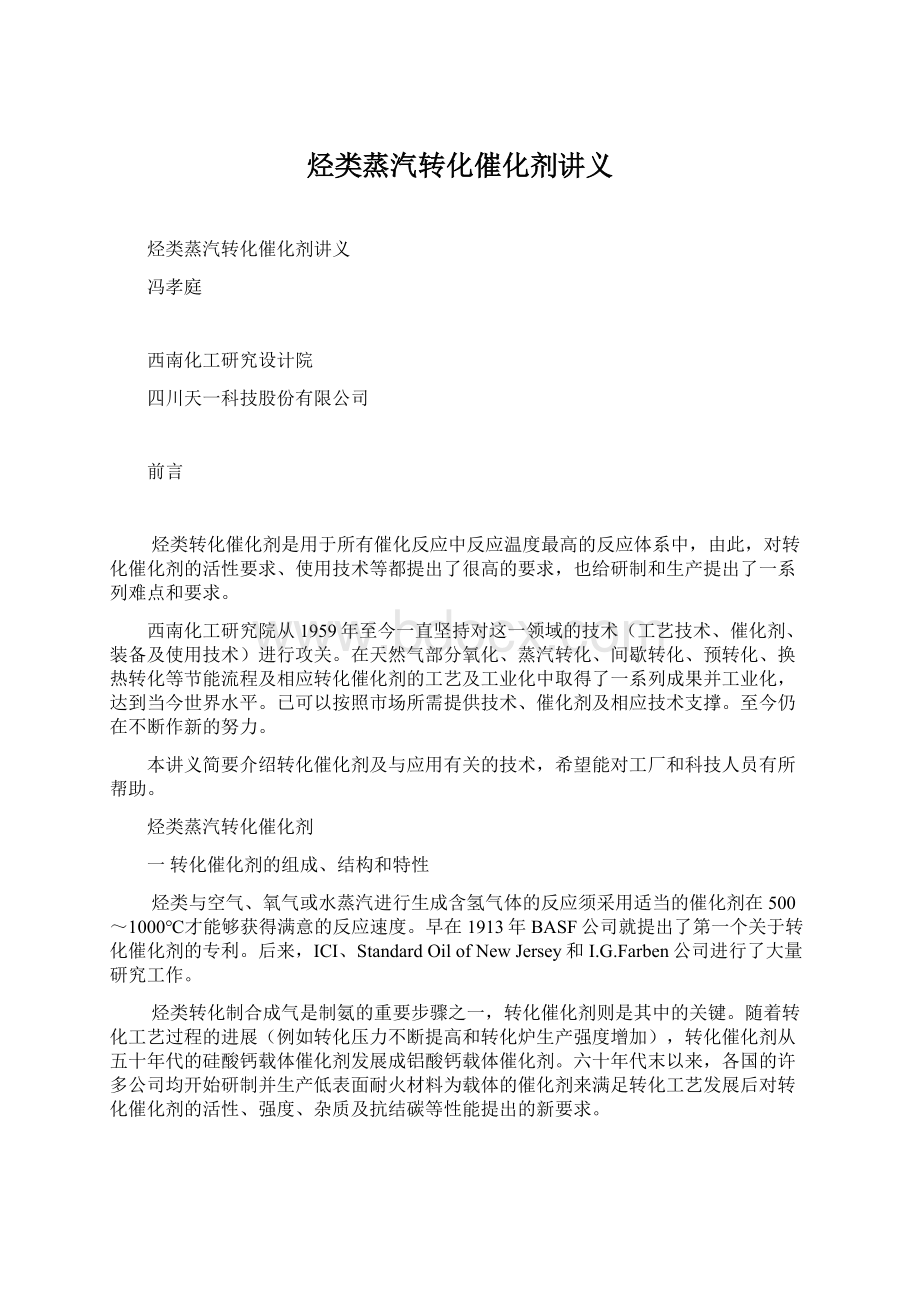
由于转化催化剂使用温度高,所以通常采用难还原、难挥发的金属氧化物作助催化剂,例如Cr203、Al203、MgO,TiO等。
有许多添加剂对提高转化催化剂的催化活性有明显的效果。
例如,
表1-1常用工业烃类转化催化剂的化学组成
国别及公司
名称
型号
形状及尺寸
外径×
内径
毫米
堆密度
公斤/升
化学组成重量%
说明
NiO
Al2O3
CaO
MgO
SiO2
Fe2O3
K2O
中国
Z102
φ19×
19×
9环
9
1.00~1.10
12-15
58
15
0.7
~2
~1.00
≤20公斤/厘米2天然气转化用
Z204
φ16×
16×
6环
1.10~1.20
≤14.0
~55.0
~10.0
—
<0.20
30公斤/厘米2天然气转化、二段炉用
Z205
φ25×
17×
10环
1.10~1.15
~6.0
~90.0
~3.5
~0.10
K+Na<0.20
即Z204R,二段炉热保护剂
Z(T)203
8×
1.00~1.05
9.0
67
<0.2
23
<0.10
即RKS-2,二段炉用
Z107
6
1.20~1.25
14~16
84
30公斤/厘米2天然气转化、一段炉用
Z402
6×
~17
30
7
11.85
12.88
0.53
6.00
轻油转化,管上半部用
Z404
~15
50
14
0.16
轻油转化,下半部用
Z405
~11
76
13
0.47
0.24
轻油转化,管下半部用
Z(T)403H
0.95~1.00
Ni25
11
~65
轻油转化用,即RKNR
英国
(ICI公司)
ICI57-1
φ17×
5环
27
46
12
0.10
一段转化
ICI57-3
10×
7环
1.00
~75
10
ICI54-2
~55
二段转化
ICI54-4
~80
ICI54-3
25柱
1.30
5
~95
二段炉热保护剂
ICI46-1
1.00~1.15
~20
~12
12.64
15.41
5~6
~6
轻油转化,管半部
ICI46-2
~14
~16
0.55
轻油转化,管下半部
ICI46-4
~10
75
13.0
0.42
0.2
ICI46-9
73
美国
(UCI公司)
C11-2S-04
~0.95
~25
0.20
用于比甲烷重的烃
C11-2S-06
~30
48
0.34
天然气,一段炉管下半部
C11-9-02
1.12~1.28
Ni12±
1
80~86
天然气转化,一段炉管下半部
C11-4-03
0.72~0.88
天然气转化,一段炉
C15-1-02
Cr2O36±
2
<0.05
C15-1-04
φ28×
18×
~0.85
Cr2O36~2
78
0.15
二段炉热保护剂,分析值
法国
RG5C
φ15×
15带槽柱状
1.20~1.30
14.0
85.0
<0.30
<0.1
部分氧化
表1-2添加剂对转化活性的影响
转化条件:
温度1720~1740°
F;
空速3000时-1仅用载体时转化率为28%;
添加5%镍后转化率为49%。
在镍含量为5%的Ni-Al2O3催化剂中添加1%的不同的添加剂的效果见表1-2。
助催化剂
转化率,%
88~99
B2O3
ZrO2
89~99
MnO2
65
54
Cr2O3
85
ZnO
TiO3
82
Cu
63
ThO2
V2O5
62
Sn
40
Ce2O3
71
BaO
61
不同的添加量对活性的影响也较大,从表1-3可知不同的添加剂有不同的最佳添加量。
MgO、TiO2及镧、铈的氧化物等对维持转化催化剂的活性稳定性方面有明显的作用。
除此之外,转化催化剂中还常常添加提高机械强度及耐热性能的添加剂,例如钙的化合物、钡的氧化物及钛的氧化物等。
为提高转化催化剂的抗结碳性能,常常添加能够改变催化剂表面酸性的碱金属或碱土金属,最常用的有钾、CaO、TiO2、稀土元素氧化物、铀和钍的氧化物等。
添加助催化剂的效果随添加数量、添加方式,催化剂的组成及制备条件不同而变化。
有些添加剂同时具有几方面的效果,例如添加稀土氧化物不但可以提高转化催化剂的抗结碳性能,而且可以减慢其活性下降的速度。
1.1.3载体
与转化催化剂使用温度相适应,其载体通常都是难熔的耐火氧化物,如Al2O3、MgO、CaO、ZrO2、TiO2或其化合物。
常用的有三类:
硅铝酸钙载体主要用波特兰水泥形式加入,同时起粘结剂及载体的作用。
在运转过程中由于脱水及相变使催化剂强度下降50%以上,而且催化剂中有害杂质含量也较高,所以目前已很少用这类载体。
表1-3助催化剂添加量对活性的影响
添加量重%
49
0.5
94
87
0.1
1.0
97
80
51
1.5
99
102
0.3
92
88
2.0
93
铝酸钙载体这类载体是用含多种铝酸钙的铝酸钙水泥组成。
在转化过程中由于脱水、相变及高浓度的碳的氧化物的作用,其机械强度也发生较大幅度下降(见图1-1)[10],为改善这类载体的性能可以添加Al2O3、ZrO2、TiO2等耐火氧化物或采用特殊的养护方法。
图1-1不同载体的催化剂强度在运转中的变化
低表面积耐火材料载体这类载体经高温煅烧而成,其比表面小,结构稳定、耐热性好,在使用中机械强度下降少(见图1-1),所以得到愈来愈广泛的应用。
常采用的载体有а-Al2O3、MgO-Al2O3、ZrO2-Al2O3、CaO-Al2O3等。
1.1.4杂质
在转化催化剂中常含有一些有害的杂质,它们常常是由原料和制备过程中带入。
毒物将在后面叙述,这里仅论述SiO2、Na2O和Fe2O3等。
SiO2在天然气转化催化剂中对提高强度及抗硫中毒等方面是有积极作用的。
但是,SiO2不但会降低催化剂的抗结碳性能,而且随着转化压力逐渐提高,SiO2在水蒸汽中的挥发带来了严重的问题—SiO2挥发出来,沉积在废热锅炉及高变催化剂层顶部温度较低的部位,对换热效率、变换效率及阻力均产生不利影响。
所以,SiO2成为重要的有害杂质之一。
从图1-2和1-3可看出,SiO2在水蒸汽相中的浓度与压力在正比;
温度升高汽相中SiO2的浓度也升高。
国内外均有一些氨厂曾由于耐火材料或转化催化剂中SiO2的挥发迁移而影响了氨厂的正常运转,表1-4中列出了二段炉后废热锅炉内生成垢层的化学组成。
由此可知,对转化装置中采用的耐火材料和催化剂中SiO2含量均应严格要求。
通常前者中SiO2<0.5%;
催化剂中含SiO2<0.20%。
K2O和Na2O在蒸汽转化过程中转化催化剂内所含的碱性物质能够促进碳的气化反应。
例如K2O能够使碳的气化反应速度提高数十倍以上,所以它们能够提高催化剂的抗结碳性能。
英国ICI公司开发成功并广泛使用至今的ICI46-1型轻油转化催化剂就是以添加钾著称,并获得了良好的效果。
表1-4从废热锅炉内取出锅垢的典型分析
组分
含量,重量%
工厂A
工厂B
工厂C
工厂D
67.6
47.9
34.15
30.22
5.2
9.3
35.75
12.19
12.5
24.2
4.30
7.60
0.9
5.02
2.19
0.0
1.10
0.40
4.2
3.0
0.81
3.1
0.67
1.4
1.7
1.67
0.88
Na2O
5.6
9.1
14.50
8.98
2.4
26.00
P2O5
SO3
0.6
总计
102.1
99.5
97.31*
93.57
但是,钾、钠会使转化催化剂的活性显著下降,低熔点的钾和钠的氧化物存在会降低催化剂的耐热性。
除此之外,在高温和水蒸汽存在的条件下K2O和Na2O均会发生挥发迁移,当有二氧化碳存在时其挥发速度大大加速。
可知一、二段炉的运转条件是有利于K2O和Na2O挥发的。
许多学者认为,K2O在水蒸汽中是以KOH形态挥发的;
这将加速钾的挥发。
当有二氧化碳存在时,钾以K2CO3形式存在,这将加速钾的挥发。
据报道,含K2O和Na2O为0.15~0.20%的催化剂在二段转化炉内运转中其K2O和Na2O可挥发迁移68~87%。
所以,通常要求天然气转化催化剂中钾和钠的总含量应当小于0.20%。
1.2物理结构及其影响
1.2.1转化催化剂的物理结构
合适的转化催化剂的物理结构是综合各方面因素的影响而确定的。
(1)催化剂的比表面和镍的分散状况不同型号的转化催化剂的比表面大不相同(从~3米2/克到100米2/克以上),但是它们的活性大体相同,可知其比表面的大小不是决定活性高低的主要因素,它们之间没有明显的对应关系。
不过,比表面的大小会影响镍的分散度,而在工业使用中催化剂比表面下降时又会促使镍表面降低,许多研究结果均显示出转化催化剂的活性变化与其镍表面变化趋势相似。
因此,为了保证活性镍有足够的分散度重要的是转化催化剂应当具有较稳定的比表面。
(2)催化剂的孔率和孔径分布由于在工业装置中转化反应的速度通常由内扩散速度控制,为了提高转化催化剂的有效利用率,它除了应当具有数目较多的细孔以提供反应所需的足够的表面以外,还应当拥有一定量的大孔作为反应物进入催化剂内部的大通道。
尽管对于转化催化剂应有的最佳孔径分布尚无统一见解,不过,绝大部分转化催化剂的孔径选择在100埃到2000埃之间。
当然,由于不同转化过程的反应条件差异较大,显然所用催化剂最佳孔径分布也会不同。
Β.Β.Βеселов指出,对甲烷转化反应在400℃时最佳孔径为100埃左右;
在900℃时则为1000埃左右。
Д.В.Гернег则提出,在常压、当反应温度为800~1000℃时,转化催化剂内通道孔径应为20000埃左右。
不过小于500埃的孔,催化剂的热稳定性通常是不好的,在选择孔径分布时还应当考虑其热稳定性。
为了兼顾转化催化剂的活性和强度,其孔率一般不超过50%,大于50%时转化催化剂通常难以具有足够的强度。
1.2.2转化催化剂的外形及尺寸
转化催化剂的外形及尺寸不但与制备方法、转化工艺条件及转化设备的结构有关,而且与其使用性能也是密切相关的。
(1)对活性的影响烃类蒸汽转化反应的总速度是受催化剂内扩散速度控制,所以转化催化剂的表观活性随着其几何表面的增加而明显提高。
表1-5和图1-4给出了催化剂外形尺寸改变(即几何表面改变),对催化剂性能的影响。
表1-5转化催化剂颗粒大小及几何表面的影响
催化剂形状
尺寸,毫米
高×
相对传热
相对活性
相对压力降
环状
100
8
106
103
117
118
126
129
143
车轮状(RC401)
17
130
当颗粒减小后其表观活性增加,一方面是由于其几何表面增加而提高了催化剂的利用率;
另一方面是由于粒度变化后显著改善了反应管内的热传递效果。
图1-4转化催化剂颗粒大小
对活性的影响
(2)对压力降的影响使转化系统中工艺气体通过催化剂层所产生的压力降维持在允许的范围内,是保证过程正常进行和节约能耗的重要条件。
从表1-5可知,为改进活性而采用小颗粒催化剂必然导致催化剂层压力降迅速上升。
但是,当改变催化剂的外形时其压力降则明显下降。
(3)对气流分布的影响不合适的催化剂的形状及尺寸会导致催化剂层中气流分配不均匀,甚至形成沟流并破坏转化过程的正常进行。
在采用圆柱状或环状催化剂时,其高度与外径的比应接近1∶1,否则在装填催化剂时,颗粒间有互相平行排列的倾向,不但会影响气流分布、导致压力降增加,而且也会减少转化催化剂的有效表面。
催化剂的外形、尺寸应当与反应管的尺寸相适应。
例如,对于小管径的一段炉,为减少管壁效应影响则应采用较小尺寸的催化剂;
为防止在一段炉反应管内催化剂架桥,其外表应当光滑且不应设计成凸凹不平的复杂外形。
对于圆形大直径转化炉,则可以采用尺寸较大或外表面不光滑的转化催化剂。
(4)对机械强度的影响转化催化剂的形状和尺寸对其机械强度有明显的影响。
例如,同种催化剂的大环比小环侧压强度差;
壁薄的比壁厚的强度差;
空心的又比内有支承筋的(或实心)强度差。
图1-5转化催化剂受力示意图
由上可知,转化催化剂的形状和尺寸对其活性、阻力、强度等均有明显影响,而且对各种性能的改善往往是有矛盾的。
所以,正确选择其外形和尺寸必须兼顾上述各方面。
例如,在一段转化炉中为兼顾活性与阻力的矛盾,有些工厂在反应管上部装入小尺寸的环,管下部则仍装尺寸稍大的环,既提高了催化剂的低温活性又未使气温阻力增加太多。
近些年新开发的带沟槽的柱状催化剂(RG5C、CN-8及RC401、Z110Y、C11-9-09型车轮状转化催化剂)就是兼顾了各方面的性能要求,具有较大的几何表面(表观活性高)、空隙率大(气流阻力小),拥有优良的机械强度等特点。
所以,转化催化剂外形的改时已受到越来越多的注意。
但是,特殊外形的催化剂制造较困难,加工费用较高。
1.2.3转化催化剂应具备的机械强度
在工业运转中,无论转化催化剂的活性多么好,如果其机械强度差,由于粉化、碎裂导致催化剂层产生过大的压力降,会迫使装置停车。
据报道,在过去使用粘结型催化剂时,约有75%的一段炉更换催化剂的原因是其机械强度已降到不得不更换的水平。
从图1-1可以看到,不同制备方法的转化催化剂在使用过程中强度的下降是不相同的。
显然,催化剂在使用过程中具有的机械强度比新催化剂的强度更为重要。
了解工业转化装置中允许的催化剂机械强度的最低值是重要的,因为它不但使我们知道转化催化剂应具有的机械强度指标,而且也提供了判断催化剂是否需要更换的强度依据。
不同的转化方法、不同的转化设备中转化催化剂应具备的机械强度的最低值不同。
我们通过催化剂在运转中的受力分析可计算出所需最低强度要求。
图1-5是运转时催化剂受力简图。
显然、底部的催化剂受力最大。
假设转化催化剂层最底部的催化剂颗粒在运转时承受的总力为W
W=h·
F·
d堆+(Pl—P2)·
104(1-1)
式中W——最底层催化剂承受的总力,公斤,
h——催化剂层高度,米,
F——催化剂层截面积,米2,
d堆——催化剂堆密度,公斤/米3,
P:
——催化剂层进口压力,公斤/厘米2,
P2——催化剂层出口压力,公斤/厘米2。
设催化剂颗粒在水平面投影面积为F1米2/颗,则每一截面应有的催化剂颗数为:
n=F/F1(1-2)
由上两式可求出每颗催化剂受力为:
f=h·
Fl·
d堆+ΔP·
104,(1-3)
式中f——每颗催化剂受的力,公斤/颗,
ΔP——催化剂层压力降,公斤/厘米2。
每颗催化剂应具有的强度应当从其强度最差的方向考虑,环状催化剂应选其侧压(径向)强度。
不同的转化方法中催化剂层高度h及压力降AP不同,因此对强度要求不同。
由于运转过程中催化剂层压力降会变化,在开、停车和升、降温过程中转化管径向和轴向均会产生热胀冷缩,系统升降压速度增加会使催化剂层产生更大的压力降,这些都会使转化催化剂承受附加应力。
考虑到上面各种因素,对于催化剂床层最高。
压力降最大的加压蒸汽转化过程的一段转化催化剂应具有的最低侧向机械强度为10~13公斤/颗。
二转化催化剂的装填
正确装填转化催化剂对充分发挥其催化效能和延长转化催化剂寿命有重要作用。
一种性能较好的转化催化剂如果装填不当,转化炉的运转很快就会达不到工艺要求而迫使更换催化剂。
所以,对催化剂的装填决不能掉以轻心。
2.1一段转化催化剂的装填
一段转化催化剂被装填在数百根垂直悬挂的转化管中,管底部设有托盘或筛板。
装填时应以保证工艺气体能够均匀地分配到各转化管去为根本目的。
理想的装填状况是在每根管内装入相同体积、相同重量的催化剂,而且催化剂装填高度也相同。
但是,相同数量的转化催化剂在管内疏松装填或紧密装填时,其相应堆密度可相差10%左右,即其装填高度及空隙率相差较大。
这会影响运转中的气体分布。
在装填时应尽力做到装填均匀。
2,1.1装填时应注意的要点
(1)过筛新催化剂在贮存和搬运中总会产生少量碎颗粒及粉尘,在装填时,它们将进入空隙中,从而使压力降增加、破坏气体均匀分布。
所以在装填前过筛步骤不可少。
(2)检查管内状况管内干净与否会影响装填的松紧程度,管底托盘或筛板上的孔通畅与否将对运转中气流阻力大小有明显影响。
所以装填前应当仔细检查并测定空管阻力。
(3)分层装填、分层检查转化管通常约有10米高,所以,