金属工艺学实验指导书Word文件下载.docx
《金属工艺学实验指导书Word文件下载.docx》由会员分享,可在线阅读,更多相关《金属工艺学实验指导书Word文件下载.docx(13页珍藏版)》请在冰豆网上搜索。
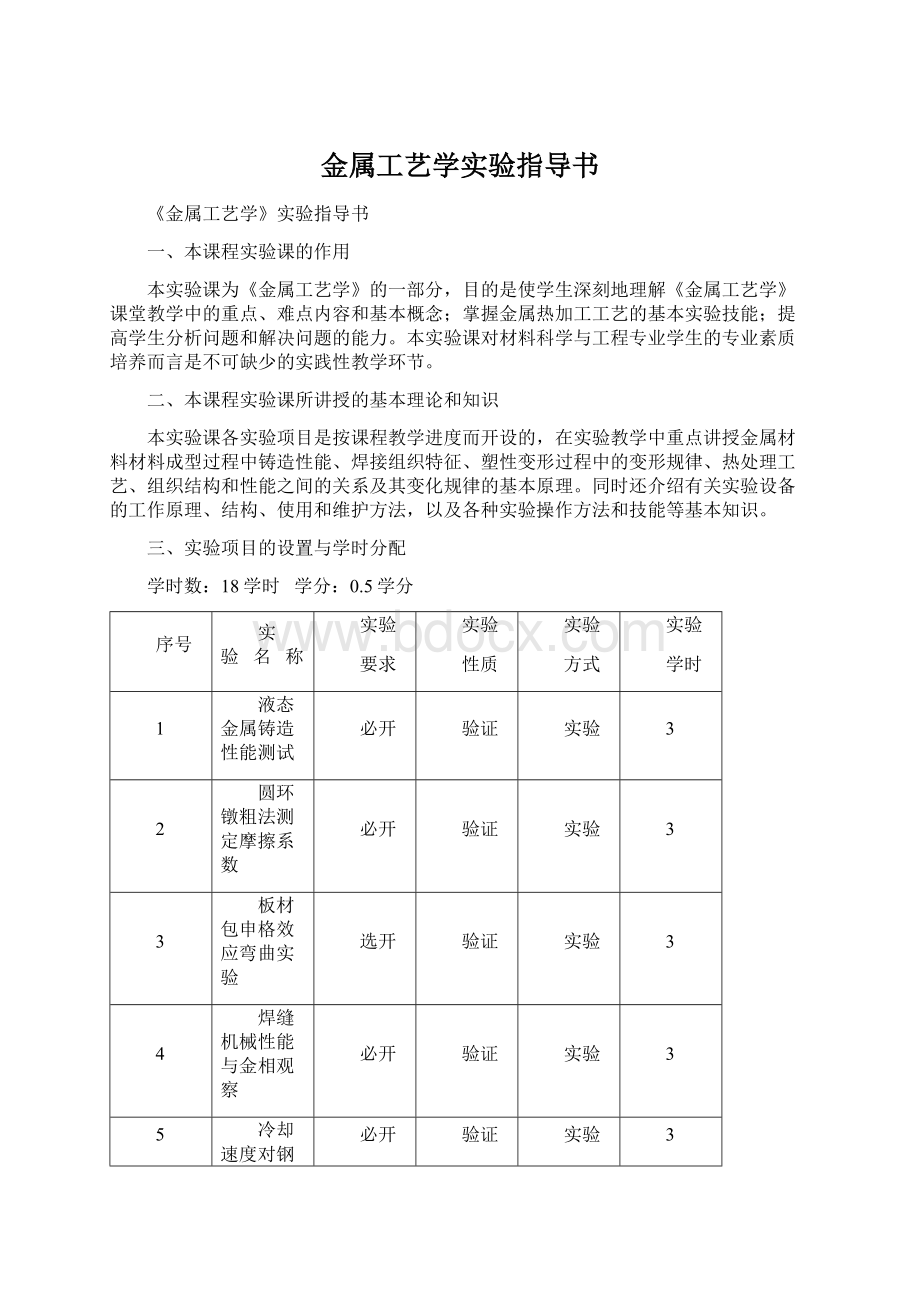
3
2
圆环镦粗法测定摩擦系数
板材包申格效应弯曲实验
选开
4
焊缝机械性能与金相观察
5
冷却速度对钢组织与性能的影响
6
铝合金的时效硬化曲线测定
五、实验考核(试)方式、内容及记分办法
本实验课对学生的实验操作技能、实验报告的质量、分析问题能力和实验结果的正确性,以及学生对实验课的态度进行综合考核评分。
实验课成绩占《金属工艺学》成绩的20%。
实验一:
一、实验目的
1)了解流动性的概念;
2)熟悉液态合金的测温方法,测量合金在不同温度下的流动性;
3)分析影响流动性好坏的因素及流动性对铸件质量的影响。
二、实验原理
采用如图1所示的螺旋型试样,根据浇铸温度不同流动性不一样的原理,在不同温度下浇铸螺旋型试样,测量螺旋型试样的长度,确定流动性并进行分析比较。
ZLL-1500III型螺旋线合金流动性试样如图1所示,采用砂型手工造型。
三、实验步骤及方法
1)手工造型制造流动性试样铸型。
2)在电阻坩锅炉中熔化ZL101合金。
3)分别在750℃、700℃、650℃浇铸流动性试样。
4)清理后,测量螺旋线试样长度,确定流动性。
四、实验报告
1)绘制浇铸温度及流动性曲线;
浇铸温度T(℃)
750
700
650
螺旋试样长度L(mm)
2)简述影响流动性的因素,重点分析浇铸温度对合金流动性的影响原因;
3)分析讨论流动性对铸件质量的影响、提高合金流动性的方法措施。
实验二:
圆环镦粗法摩擦系数的测定
一、
实验目的
1)根据圆环镦粗后的变形,了解摩擦对金属流动的影响;
2)通过实验掌握实际测定摩擦系数的方法;
3)分析镦粗对材料组织的影响,并与铸态情形进行比较。
二、实验内容说明
1.塑性加工过程中摩擦的特点
凡是物体之间有相对运动或有相对运动的趋势就有摩擦存在。
前一种是动摩擦,后一种是静摩擦。
在机械传动过程中,主要是动摩擦。
在塑性加工过程中的摩擦,虽然也是由两物体间相对运动产生的,但与一般机械传动中的摩擦有很大差别。
(1)接触面上压强高
在塑性加工过程中,接触面上的压强一般在100MPa以上。
在冷挤压和冷轧过程中可高达2500-3000MPa。
而一般机械传动过程中,摩擦副接触面上的压强仅20-40MPa。
由于塑性加工过程中接触面上的压强高,隔开两物体的润滑剂容易被挤出,降低了润滑效果。
(2)真实接触面积大
在一般机械传动中,由于接触表面凹凸不平,因而,实际接触面积比名义接触面积小得多。
而在塑性加工过程中,由于发生塑性变形,接触面上凸起部分会被压平,因而实际接触面积接近名义接触面积。
这使得摩擦阻力增大。
(3)不断有新的摩擦面产生
在塑性加工过程中,原来非接触表面在变形过程中会成为新的接触表面。
例如,镦粗时,由于不断形成新的接触表面,工具与材料的接触表面随着变形程度的增加而增加。
此外,原来的接触表面,随着变形程度的进行可能成为非接触表面。
例如,板材轧制时,轧辊与板材的接触表面不断变为非接触表面向前滑出。
因此,要不断给新的接触表面添加润滑剂。
这给润滑带来困难。
(4)常在高温下发生摩擦
在塑性加工过程中,为了减少变形抗力,提高材料的塑性,常进行热加工。
例如,钢材的锻造加热温度可达到800-1200℃。
在这种情况下,会产生氧化皮,模具软化,润滑剂分解,润滑剂性能变坏等一系列问题。
2.摩擦对塑性加工过程的影响
摩擦对塑性加工过程的影响,既有有利的一面,也有不利的一面。
轧制时,若无摩擦力,材料不能连续进入轧辊,轧制过程就不能进行。
在摩擦力起积极作用的挤压过程中,浮动凹模与坯料之间的摩擦力有助于坯料运动,使变形过程容易进行。
又如板料拉深时,有意降低凸模圆角半径处的光洁度,以增加该处的摩擦力,使拉深件不易在凸模圆角处流动,以免引起破裂。
但是,对多数塑性加工过程,摩擦是有害的,主要表现在以下方面:
(1)增加能量消耗
在塑性加工过程中,除了使材料发生形状改变消耗能量外,克服摩擦力也要消耗能量。
这部分能量消耗是无用的,有时这部分能量消耗可占整个外力所做功的50%以上。
(2)改变应力状态,增加变形抗力
单向压缩时,如工具与工件接触面上不存在摩擦,工件内应力状态为单向压应力状态。
当接触面上存在摩擦时,工件内应力状态成为三向压应力状态。
同时摩擦也引起接触面上应力分布状况的改变。
无摩擦均匀压缩时,接触面上的正应力均匀分布;
存在摩擦时,接触面上的正应力呈中间高两边低的状况。
摩擦会使变形抗力提高,从而增加能量消耗和影响零件的质量。
摩擦使金属流动阻力增加,坯料不易充满型腔。
对于轧制过程,由于摩擦使变形抗力提高,轧辊的弹性变形加大,同时使轧辊之间的缝隙中间大、两边小,其结果是轧件中间厚两边薄。
(3)引起变形不均匀
在挤压实心件时,由于外层金属的流动受到摩擦阻力的影响,出现了流动速度中间快边层慢的现象,严重时会在挤压件尾部形成缩孔。
有时,摩擦引起的变形不均匀会产生附加应力,使制件在变形过程中发生破裂。
(4)加剧了模具的磨损,降低模具的寿命
摩擦产生的热使模具软化,摩擦使变形抗力提高,从而导致模具的磨损加剧。
3.影响摩擦系数的主要因素
(1)金属的种类和化学成分
不同种类的金属,其表面硬度、强度、氧化膜的性质以及与工具之间的相互结合力等特性各不相同,所以摩擦系数也不相同。
即使同一种金属,当化学成分不同时,摩擦系数也不相同。
一般来说,材料的强度、硬度愈高,摩擦系数愈小。
(2)工具表面粗糙度
通常情况下,工具表面越粗糙,变形金属的接触表面被刮削的现象愈大,摩擦系数也愈大。
(3)接触面上的单位压力
单位压力较小时,表面分子吸附作用小,摩擦系数保持不变,和正压力无关。
当单位压力达到一定值后,接触表面的氧化膜破坏,润滑剂被挤掉,坯料和工具接触面间分子吸附作用愈益明显,摩擦系数便随单位压力的增大而增大。
但增大到一定程度,便稳定了。
(4)变形温度
一般认为在室温下变形时,金属坯料的强度、硬度较大,氧化膜薄,摩擦系数最小。
随着温度升高,金属坯料的强度硬度降低,氧化膜增厚,表面吸附力、原子扩散能力加强;
同时高温使润滑剂性能变坏,所以,摩擦系数增大。
到某一温度,摩擦系数达到最大值。
此后,温度继续升高,由于氧化皮软化和脱落,氧化皮在接触面间起润滑剂的作用,摩擦系数却下降了。
(5)变形速度
由于变形速度增大,使接触面相对运动速度增大,摩擦系数便降低。
4.圆环镦粗法原理
这种方法适于测定体积成形过程中的摩擦系数或摩擦因子。
采用这种方法时,将几何尺寸(指外径、内径、高度的比值)一定的圆环放在平板之间进行压缩。
压缩后圆环内、外径的变化情况与平板接触面上的摩擦情况关系很大。
理论分析结果与实验结果表明,圆环的内径变化对接触面上摩擦情况的变化比较敏感。
如果接触面上不存在摩擦,则圆环压缩时的变形情况和实心圆柱体一样,其中各质点在径向均向外流动,流动速度与质点到对称轴之间的距离成正比,当接触面上的润滑情况很差时,压缩后圆环的内径将减小;
如果接触面上的润滑情况较好,则压缩后圆环的内径将增大。
因此,采用圆环镦粗法时,是以压缩后圆环的内径变化来确定摩擦系数或摩擦因子的。
假设圆环的几何尺寸为外径:
内径:
高度=6:
3:
2,高度压缩30%后内径变化率为-10%。
根据上述数据,在相应标定曲线上(如图1所示)就可得一点。
从图1可以看出,该点与m=0.10的曲线最为接近,因而可以认为对所考虑的情况,m=0.10。
图1.测定摩擦因子用的标定曲线
三、实验方法和步骤
1.试样
试样为工业纯铝,制成环状,其外圆、内径、高度比值为6:
3:
2,具体尺寸如图2所示。
图2
圆环试样
图2.圆环铝试样示意图
2.实验设备、工具及辅助材料
设备:
600KN和1000KN万能材料试验机;
工具:
150mm游标卡尺、垫板;
辅助材料:
MoS2油膏
3.实验步骤
取圆环铝试样两个,分别在不同摩擦条件下(一个用油膏,一个不用油膏),在两平板间进行压缩,圆环要放在平板中心,保证变形均匀。
每次压缩量为15%左右,然后取出擦净测量变形后的圆环尺寸(外径、内径、高度)。
注意测量时测量圆环内径的上、中、下三个直径尺寸,取其平均值。
重复进行上述步骤三次,控制总压缩量在50%。
根据所获得的内径、高度数据,查图表得出摩擦系数值。
1.列表填写实验数据(分加润滑剂和未加润滑剂);
2.计算、并查对校正曲线,得出实验结果;
3.分析不同摩擦条件对圆环变形分布的影响;
4.对测定摩擦系数的误差因素进行分析。
实验三:
板材包申格效应弯曲实验
—、实验目的
通过对预变形的试件进行反向加压,使学生加深理解包申格效应。
很多金属材料因为有高的强度和韧性而被大量应用于承载结构,例如输送石油或天然气的管道。
结构的尺寸及使用效率跟其材料的强度直接相关,一般都按材料强度进行工程构件设计。
在工程实际中,屈服强度是描述金属材料力学性能的重要参数。
然而,屈服强度会随着加载历史的不同而有所变化。
许多金属材料经过某一个方向加载变形后,卸载,再反向加载,变形与原方向相反,则其屈服强度明显降低,这就是包申格效应。
包申格效应是金属材料所具有的普遍现象,了解包申格效应对于产品的生产工艺和设计有重要指导意义。
三、实验仪器和材料
1)液压式万能试验机
2)X80钢试件
为了容易进行轴向拉伸及压缩实验,把试件加工成如图1所示的形状。
试件长度为200mm,夹持部分较长,便于拉伸加载;
中间标距段较短,仅为10mm,这可使试件受压时避免微弯失稳。
图1.试件形状及尺寸(mm)
四、实验方法和步骤
首先记录试件在轴向拉伸情况下的应力-应变曲线。
为了获得X80钢的包申格效应情况,对试件进行轴向拉伸产生预变形。
控制对各个试件的总预变形量分别为:
0.50%,0.60%,0.95%,1.20%,1.50%,卸载后再反向加载,记录应力-应变曲线。
五、实验报告
1.试件的应力应变-曲线;
2.分析试件在没有预变形和有不同预变形后的屈服强度的变化;
3.讨论减小或消除包申格效应的方法。
实验四:
1)观察低碳钢焊接接头金相组织变化情况;
2)掌握常用硬度计的使用与测量方法,分析焊接接头组织变化对机械性能的影响;
3)初步分析影响焊接接头金相组织的因素和改进措施。
熔化焊是工业生产中应用最广的焊接方法,其中又以手工电弧焊最为普遍,气焊多用于少量焊接3mm以下薄板制件。
熔化焊是将焊件接头处金属加热到熔化状态,靠熔化金属冷却结晶成一体而完成焊接的方法。
由于是局部加热,接头上各点温度分布不均匀,焊缝金属加热到熔点以上,紧邻焊缝的母材加热到接近熔化的高温,有部分熔化,再向外受热温度逐渐降低,愈远离焊缝,温度愈低。
一般将焊缝两侧受焊接热影响发生组织与性能变化的区域,称为热影响区,焊缝和热影响区之间的极小过渡区,称为熔合区。
因此,焊接接头由焊缝区、熔合区和热影响区三部分构成,如图1焊件的质量主要取决于接头的质量,特别是热影响区的大小。
所以,了解焊接接头的金相组织变化情况及其对金属机械性能的影响,对尽量减小热影响区、制定合理工艺方案,提高接头质量极其重要。
图1.焊接接头示意图
1)金相显微镜
2)金相抛光机
3)金相砂纸、浸蚀液
4)小负荷维氏硬度计
5)低碳钢焊接接头试样
四、实验内容及步骤
(一)试件制备
1.对试件表面依次进行粗磨→细磨→抛光研磨;
粗磨,细磨主要采用金相砂纸,从粗砂到细砂依次进行研磨,每次磨痕与前一次垂直,注意用力要均匀且不宜过大。
2.研磨过的试样在镜检前先要进行腐蚀,方法如下:
首先把抛光后的试件在流动的清水中冲洗,然后用纯酒精脱脂棉擦干,吹风机吹干,再立即在4~5%的硝酸酒精溶液中进行腐蚀,腐蚀时间约为30秒~1分钟不等(视具体情况而定);
然后用脱脂棉擦拭干净,再用清水冲洗-无水酒精冲洗-吹风机吹干,至此试样的制备过程结束。
(二)显微镜观察
在显微镜下观察焊接接头试样的组织
(三)硬度试验
通过对母材、焊缝与过热区硬度值的对比,了解焊接接头不同区域的力学性能。
1)绘出低碳钢焊接接头横截面的金相组织变化示意图,并指出各区域组织名称;
2)分析各区组织变化情况和原因;
3)母材、焊缝和熔合线的硬度值及解释各区的性能变化原因;
4)分析和提出保证熔化焊焊接接头质量的措施。
实验五:
1.了解T8钢、45钢各自在相同奥氏体化温度下,以不同的冷却速度(水冷、油冷、炉冷、空冷)进行冷却时对其组织与性能的影响。
2.识别钢中珠光体、索氏体、屈氏体、贝氏体的组织形态特征。
将钢加热奥氏体化后,以不同的冷却速度进行冷却,将会发生不同的转变,得到不同的组织,因而具有不同的性能。
工业生产上采用水淬、油淬、正火等工艺操作实质上是通过水冷、油冷、空冷等冷却方式来获得不同的冷却速度,从而获得所需的组织与性能。
三、实验装置
1.中温电炉、水桶和油桶
2.硬度计
3.金相显微镜
四、实验方法
1.了解使用膨胀仪制作CCT曲线的过程;
2.每人领取样品一只(45钢或T8钢),将试样用铅丝扎好。
将试样同时放入已升温到900℃的电炉中,保温20分钟后,取出进行水冷、油冷、空冷及炉冷。
淬火时注意制钳夹住铅丝,不要夹住样品,以免降低冷却速度;
3.将试样用砂纸磨光,测定硬度并记录下来;
4.制备金相试样,观察其金相组织,再对照观察实验室所做的金相试样,绘出一种钢号的五种金相组织(水冷、油冷、空冷、炉冷、原始组织)。
为了便于观察组织,本实验中采用高于正常的淬火加热温度。
1.实验目的;
2.实验方法与注意事项;
3.实验结果:
T8钢、45钢经不同冷却速度后的硬度值与金相组织示意图;
4.
根据T8钢与45钢的连续冷却转变曲线(CCT曲线)与水冷、油冷、正火、退火相应的大致冷却曲线的相应位置讨论冷却速度对组织与性能的影响。
图1.T8钢CCT曲线
图2.45钢CCT曲线
实验六:
通过测定铝合金经固溶处理后,在不同温度保温不同时间后的硬度变化,绘制时效硬化曲线,了解铝合金的时效硬化规律。
从过饱和固溶体中析出第二相(沉淀相)或形成溶质原子聚集区以及亚稳定过渡相的过程称为脱溶或沉淀,是一种扩散型相变。
具有这种转变的最基本条件是,合金在平衡状态图上有固溶度的变化,并且固溶度随温度降低而减少。
如果将C0成分的合金自单相α固溶体状态缓慢冷却到固溶度线(MN)以下温度(如T3)保温时,β相将从α相固溶体中脱溶析出,α相的成分将沿固溶度线变化为平衡浓度C1,这种转变可表示为:
。
β为平衡相,可以是端际固溶体,也可以是中间相,反应产物为(α+β)双相组织。
将这种双相组织加热到固溶度线以上某一温度(如T1)保温足够时间,将获得均匀的单相固溶体α相,这种处理称为固溶处理。
若将经过固溶处理后的C0成分合金急冷,抑制α相分解,则在室温下获得亚稳的过饱和α相固溶体。
这种过饱和固溶体在室温或较高温度下等温保持时,亦将发生脱溶,但脱溶相往往不是状态图中的平衡相,而是亚稳相或溶质原子聚集区。
这种脱溶可显著提高合金的强度和硬度,称为沉淀强(硬)化或时效强(硬)化,是强化合金材料的重要途径之一。
固溶处理所得的过饱和固溶体在时效过程中,其机械性能、物理性能和化学性能等均随之发生变化,这种现象称为时效。
室温下产生的时效称为自然时效,高于室温的时效称为人工时效。
对于结构材料而言,最重要的是硬度和强度。
按时效硬化曲线的形状不同,可分为冷时效和温时效。
冷时效是指在较低温度下进行的时效,其硬度变化曲线的特点是硬度一开始就迅速上升,达一定值后硬度缓慢上升或者基本上保持不变。
冷时效的温度越高,硬度上升就越快,所能达到的硬度也就越高。
在Al基和Cu基合金中,冷时效过程中主要形成G.P.区。
温时效是指在较高温度下发生的时效,硬度变化规律是:
开始有一个停滞阶段,硬度上升极其缓慢,称为孕育期,一般认为这是脱溶相形核准备阶段,接着硬度迅速上升,达到一极大值后又随时间延长而下降。
温时效过程中将析出过渡相和平衡相。
温时效的温度越高,硬度上升就越快,达最大值的时间就越短,但所能达到的最大硬度反而就越低。
冷时效与温时效的温度界限视合金而异,A1合金一般约在100℃左右。
本实验采用两种铝合金(铸造铝合金和变形铝合金)进行温时效,在不同的时效温度下等温时效不同时间后冷却,然后测试合金的硬度,绘制时效硬化曲线。
1)布氏硬度计
2)A357(铸造铝合金)、6061(变形铝合金)
因为固溶处理和时效处理所需时间很长,实验室已经准备好实验所需的试样,同学只需分组测试不同温度下的一系列不同时效时间的试样的硬度,即可绘制出时效硬化曲线。
A357(铸造铝合金)
6061(变形铝合金)
固溶处理
温度
(℃)
时间(Hr)
冷却方式
时间
(Hr)
535
8
70℃水淬
525
室温水淬
时效处理
温度(℃)
165;
180
空冷
170;
185
一系列不同时效时间(Hr):
0.5、1、2、3、4、6、8、10、12、16、20、24。
1.绘制时效硬化曲线;
2.对时效过程中的组织和性能变化进行分析。