合成氨生产工艺58Word文档格式.docx
《合成氨生产工艺58Word文档格式.docx》由会员分享,可在线阅读,更多相关《合成氨生产工艺58Word文档格式.docx(16页珍藏版)》请在冰豆网上搜索。
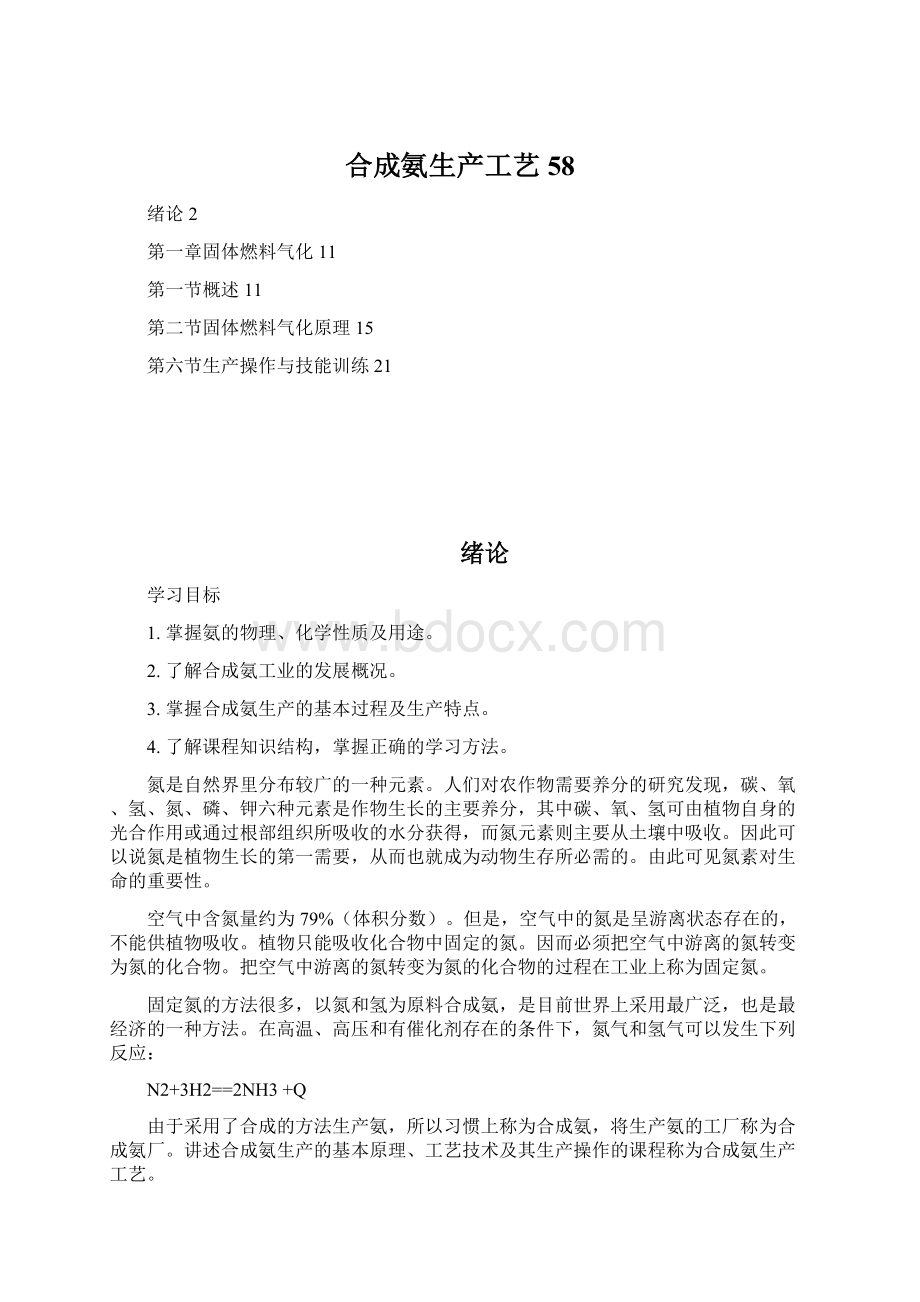
(2)化学性质氨的化学性质较活泼,能与酸反应生成盐。
如与磷酸反应生成磷酸铵;
与硝酸反应生成硝酸铵;
与二氧化碳反应生成氨基甲酸铵,脱水后成为尿素;
与二氧化碳和水反应生成碳酸氢铵等。
在有水的条件下,氨对铜、银、锌等金属有腐蚀作用。
氨自然点为630℃。
氨与空气或氧按一定比例混合后,遇火能爆炸。
常温常压下,氨在空气中的爆炸范围为15.5%~28%,在氧气中为13.5%~82%。
2.氨的用途
(1)制造化学肥料的原料除液氨本身可作为化学肥料外,农业上使用的所有氮肥、含氮混合肥和复合肥,都以氨为原料。
(2)生产其他化工产品的原料基本化学工业中的硝酸、纯碱、含氮无机盐,有机化学工业中的含氮中间体,制药工业中的磺胺类药物、维生素、氨基酸,化纤和塑料工业中的己内酰胺、己二胺、甲苯二异氰酸酯、人造丝、丙烯腈、酚醛树脂等都需要直接或间接的以氨为原料。
(3)应用于国防工业和尖端技术中作为制造三硝基甲苯、三硝基苯酚、硝化甘油、硝化纤维等多种炸药的原料;
作为生产导弹、火箭的推进剂和氧化剂。
(4)应用于医疗、食品行业中作为医疗食品行业中冷冻、冷藏系统的制冷剂。
二、合成氨工业的发展概况
1.合成氨工业化及其产量
自从1913年在德国奥堡巴登苯胺纯碱公司建成了第一个日产30t的合成氨工厂至今已有100多年的历史。
100多年来,随着世界人口的增长,合成氨产量也在迅速增长,如图0-1所示。
从图中可以看出,合成氨工业开始以后30年,产量增长缓慢。
到二次世界大战结束以后,开始大幅提高,这是由于20世纪50年代天然气、石油资源大量开采,氨的需求急剧增长,尤其是60年代以后开发了多种活性好的催化剂,反应热的回收与利用更加合理,大型化工程技术等方面的发展,促使合成氨工业高速发展,其产量在化工产品中仅次于硫酸。
2.我国合成氨工业的发展
我国合成氨工业于20世纪30年代起步,1941年,最高年产量不过50kt。
新中国成立后,经过数十年的努力,已形成了遍布全国、大中小型氨厂并存的氮肥工业布局,1999年合成氨产量为34310kt,排名世界第一。
20世纪50年代初,在恢复与扩建老厂的同时,从前苏联引进并建成一批以煤为原料,年产50kt的合成氨装置。
60年代,随着石油、天然气资源的开采,分别从英国引进以天然气为原料,年产100kt的加压蒸汽转化法合成氨装置;
从意大利引进以渣油为原料年产50kt的部分氧化法合成氨装置。
从而形成了煤、油、气原料并举的中型氨厂的生产体系。
为了适应农业发展的迫切需要,发挥中央和地方办化肥厂的积极性,从20世纪60年代开始在全国各地建设了一大批以碳化法合成氨流程制取碳铵为主的小型氨厂,1979年发展到1539座氨厂。
目前对这些小型厂的改造重点是抓好规模、品种、技术、产业等方面的结构调整工作。
随着石油、天然气工业的迅速发展,20世纪80年代后期和90年代初,我国引进了具有世界先进水平日产1000t的节能型合成氨装置。
与此同时,我国自行设计的以轻油为原料年产30万吨的合成氨装置于1990年建成投产。
由于我国人口众多,粮食产量不断提高,化肥需求逐年增长,在九五期间又相继建成投产了以天然气、渣油、轻油、煤为原料的大型合成氨装置,分布在海南东方县、乌鲁木齐、呼和浩特、九江、兰州、南京、吉林和渭南等地。
三、合成氨生产的基本过程
生产合成氨,必须制备含有氢和氮的原料气。
氢气来源于水蒸气和含有碳氢化合物的各种燃料。
目前工业上普遍采用焦炭、煤、天然气、轻油、重油等燃料,在高温下与水蒸汽反应的方法制氢。
氮气来源于空气,可以在低温下将空气液化分离而得,也可在制氢的过程中加入空气,将空气中的氧与可燃性物质反应而除去,剩下的氮与氢混合,获得氢氮混合气。
除电解水(此法因电能消耗大而受到限制)以外,不论用什么原料制取氢、氮原料气,都含有硫化物、一氧化碳、二氧化碳等杂质。
这些杂质不但能腐蚀设备,而且能使氨合成催化剂中毒。
因此,把氢、氮原料气送入合成塔之前,必须进行净化处理,除去各种杂质,获得纯净的氢、氮混合合成气。
因此,合成氨的生产过程包括以下三个主要步骤。
第一步,原料气的制取。
制备含有氢气、一氧化碳、氮气的粗原料气。
一般由造气、空分工序组成。
第二步,原料气的净化。
除去粗原料气中的氢气、氮气以外的杂质。
一般由原料气的脱硫、一氧化碳的变换、二氧化碳的脱除、原料气的精制工序组成。
第三步,原料气的压缩与合成。
将符合要求的氢氮混合气压缩到一定的压力后,在高湿、高压和有催化剂的条件下,将氢氮气合成为氨。
一般由压缩、合成工序组成。
生产合成氨的基本过程可用方框图0-2表示:
原料造气工序CO变换工序脱碳工序精制工序压缩工序合成工序产品氨
图0-2生产合成氨基本过程
由于所用原料不同,原料气的制备和净化方法也不相同,因而生产合成氨的过程也有差异。
例如,以天然气或轻油为原料制备合成氨原料气时需要先除去硫化物;
以重油为原料制备原料气时,一般先经过变换后进行脱硫。
四、合成氨生产原料的种类及技术特点
合成氨生产的原料,按物质状态可分为固体原料、气体原料和液体原料三种。
固体原料主要有焦炭、煤及其加工品碳化煤球、水煤浆;
气体原料有焦炉气、天然气;
液体原料有石脑油、重质油。
1.固体原料合成氨
合成氨的固体原料主要是焦炭、煤。
焦炭是由原料煤干馏而得到的产品,不含挥发分。
利用焦炭制取合成氨原料气,主要以空气与水蒸气为气化剂通过间歇式交替吹入气化炉中的固定炭层进行气化反应,而获得合成氨生产用的原料气。
煤的品种很多,按其在地下的生成时间的长短,大体分为泥煤、褐煤、烟煤、无烟煤等。
除烟煤外,其他煤种因含挥发分较多,不适于常压固定炭层间歇气化方法。
所选择的造气设备(气化炉)多为流化床(沸腾床)和各类气流床。
沸腾床或气流床都必须连续作业且都需要使用氧气或富氧空气,这是与固定床间歇造气最大不同点。
煤的连续化法唯一使用固定层(移动床)的是德国的鲁奇炉,固定层加压连续气化主要使用无烟煤,或其粉煤加工处理后的碳化煤球。
无烟煤的挥发分含量很低,性能较为接近焦炭,生产能力却高于焦炭。
该工艺一开始就使用加压技术,前后经历了三代自我改造,迄今仍有其生命力。
用粉煤和水配制成可泵送的水煤浆,在外热式的蒸发器内,水煤浆经预热、蒸发和过热三阶段,最终形成蒸汽-粉煤悬浮物。
以高浓度水煤浆进料,液体排渣的加压纯氧气流化床气化是由美国德士古发展公司开发,取名德士古煤气化工艺。
该气化工艺由于煤种适应范围宽,工艺灵活,合成气质量高,生产能力强(引进技术的单台炉日处理煤量达1800t,相当于日产合成氨1200t),不污染环境而成为当今具有代表性的第二代煤气化技术。
2.气体原料合成氨
适合于合成氨生产的气体来源很多,有天然产生的,也有其他工业副产的。
气体原料生产氨的技术很多,如以焦炉气为原料的深冷氢分法,部分氧化法;
以天然气或石油加工气为原料的无催化热裂解法、部分氧化法等。
其中以天然气为原料的蒸汽转化技术被广泛使用。
由于该技术的建设费用少、生产成本低,目前在全世界已成为合成氨厂的主流,在20世纪70年代已达总氨产量的60%,80年代达80%,进入90年代还在继续扩大。
3.液体原料合成氨
石脑油来自石油溜出的较轻馏分。
利用石脑油制取合成氨原料气最先由英国的帝国化学公司(ICI)开发应用,在20世纪50~60年代,一度被一些没有天然气资源的国家所推广。
这种原料的使用技术与天然气蒸汽转化本质上没有太大的不同,主要区别之一是在转化反应中需采用耐烯烃的专用催化剂。
由于石脑油价格上扬等因素,以石脑油制取合成氨原料气的合成氨厂正在逐渐地改用以天然气为原料的制氨技术。
重质油包括减压渣油、常压重油甚至原油。
作为合成氨原料,要根据各地的原油加工深度而定。
制取高热值煤气的工艺技术由热裂解法、加氢裂解法和催化裂解法,适合于氨生产用的工艺技术主要是部分氧化法。
五、学习《合成氨生产工艺》的方法与要求
1.课程知识结构
《合成氨生产工艺》是一门理论与实践紧密结合的综合性化工课程。
不仅需要基础化学理论、化工过程与设备等学科的理论建立本课程完整的理论体系,而且还需要应用计算机、化工自动化与仪表、工程与技术经济等知识建立本课程的操作控制体系。
因此,它不像基础科学学科那样有明显的学科体系。
对初学者应明确这一课程的知识结构,从而运用正确的学习方法取得良好的学习效果。
2.学习方法
本课程的理论与技能是以合成氨生产为序排列的,各工序虽然有独立的生产目标、生产技术,但从宏观上都包含有基本原理、工艺条件选择、工艺流程、主要设备结构、生产操作与技能训练这六个主要部分。
在学习基本原理、工艺条件选择时,要注意运用化学热力学、反应动力学理论以及催化剂理论等去演绎推理;
在学习工艺流程、主要设备及产生操作时,要结合产生认识性实习、下厂参观及仿真模拟训练,将理论与实践相结合。
3.学习要求
就课程体系而言,在学习中要将原料的选择与产生原理,生产方法的选择与设备的作用,催化剂的选择与使用,影响操作的因素与工艺条件的选择等有机的结合起来。
对于典型过程,要求理解并掌握生产原理、工艺条件的选择依据、工艺流程的组织原则、不同反应设备的结构特点等;
对于不同原料的不同工艺路线应从技术特点、能量回收利用等方面分析其各自的优缺点;
对于典型设备或生产过程的物料与能量衡算,要求通过课堂讲解与练习,掌握其基本的计算方法与步骤;
对于生产实习或仿真模拟操作,要求理论与实践相结合,通过实际操作训练培养分析问题和解决问题的能力。
第一章固体燃料气化
第一节概述
固体燃料气化过程是以焦炭、煤为原料,在一定的高温条件下,通入空气、水蒸气或富氧空气-蒸汽混合气(统称为气化剂),经过一系列反应生成一氧化碳、二氧化碳、氢气、氮气及甲烷等的混合气体(统称为煤气)的过程。
合成氨生产中将这一过程称为造气,即制造合成氨生产的粗原料气。
用于实现气化过程的设备称为煤气发生炉。
气化过程中产生的煤气的组成,随气化时所用的固体燃料的性质、气化剂的类别、气化过程的条件和煤气发生炉的结构而有所不同。
对同一品种的固体燃料,采用不同的气化剂,可制出不同组成的煤气;
采用相同的气化剂,在不同气化条件下,所得到的煤气的组成亦截然不同。
因此,必须针对煤气所需的组成来选择气化剂的类别和气化条件。
根据所用气化剂的不同,工业煤气可分为下列四种。
空气煤气:
以空气为气化剂制取的煤气。
水煤气:
以水蒸气为气化剂制取的煤气。
混合煤气:
以空气和适量的水蒸气为气化剂制取的煤气。
半水煤气:
以适量的空气(或富氧空气)与水蒸气为气化剂制取的煤气。
以上四种工业煤气的组成如表1-1所示。
表1-1四种工业煤气组成(体积分数)单位:
%
组分
H2
CO
CO2
N2
CH4
O2
H2S
空气煤气
0.5~0.9
32~33
0.5~1.5
64~66
—
混合煤气
12~15
25~30
5~9
52~56
1.5~3
0.1~0.3
水煤气
47~52
35~40
5~7
2~6
0.3~0.6
0.1~0.2
0.2
半水煤气
37~39
28~30
6~12
20~23
0.3~0.5
煤气中氢气和氮气是合成氨的原料,一氧化碳通过变换反应可生成氢气,从表中煤气的组成可看出,半水煤气是适宜合成氨生产的粗原料气。
水煤气经过净化后得到纯净的氢气,再配入适量的氮气,也可称为合成氨的原料气。
一、固体燃料的种类及对气化反应的影响
1.煤
(1)煤的组成及对气化反应的影响煤是由古代植物转变而来的大分子有机化合物。
煤中除含有碳、氢、氧、氮、硫五种元素之外,还含有水分、灰分及焦油等挥发性物质,如图1-2所示。
表1-2各种煤的成分(质量分数)单位:
成分
木材
泥煤
褐煤
低烟煤
烟煤
半烟煤
半无烟煤
无烟煤
水分
56.70
34.55
24.28
3.24
2.03
3.38
2.80
挥发分
26.14
35.34
27.63
27.13
14.47
8.47
1.16
固定碳
11.17
22.91
44.84
62.52
75.31
76.65
88.21
灰分
5.99
7.20
3.25
7.11
8.19
11.50
7.83
硫
0.64
1.10
0.36
0.95
2.26
0.63
0.89
氢
6.25
6.33
6.60
6.14
5.24
4.14
3.58
1.89
碳
49.50
21.03
42.40
55.29
78.00
79.97
78.43
84.36
氮
0.57
1.07
1.28
1.26
1.00
氧
43.15
62.91
42.13
33.90
7.47
4.18
4.85
4.40
①水分。
煤中的水分是指煤所含有的游离水(开采过程中、运输途中、堆放过程中所沾的水)、吸附水(凝胶水、表面吸附水、毛细孔吸附水和矿物质结晶水)和化合水(通过化学键结合的水),它关系煤的热值和煤的实用价值。
原料煤的水分高,有效成分低,气体产率降低。
气化过程水蒸气带出热量增加,煤的消耗定额增加。
②挥发分。
挥发分与煤的质变程度有关,它的含量依下列次序递减:
泥煤褐煤烟煤无烟煤。
挥发分高,制得煤气的甲烷等碳氢化合物的含量高,挥发分中的焦油等物凝结后,易堵塞管道,使一些阀门关不严。
不利于合成氨生产。
因此常压固定层煤气炉生产合成氨原料气时,必须使用无烟煤或焦炭,为了降低生产成本也可用加工煤球代替。
③硫分。
硫在煤中主要以有机硫、单质硫、硫化物和硫酸盐四种形态存在。
在气化时硫变成硫化氢和有机硫存在于煤气中,会对设备产生腐蚀,并会引起合成氨催化剂中毒,故要求原料中硫含量越低越好。
④灰分。
煤的灰分是指煤中所有可以燃烧以及煤中矿物质在高温下产生分解、化合等复杂反应后剩下来的残渣。
其成分主要是金属和非金属的氧化物和盐类。
固定床和流化床(沸腾床)煤气炉一般以煤灰的软化温度作为衡量其熔融的主要指标,而气流床煤气炉则以煤灰完全熔化,开始流动并形成薄层的流动温度为主要指标。
(2)煤的性质及对气化反应的影响
①化学活性。
指煤与气化剂反应的活性,与煤的炭化程度和成煤条件有关,同时也与反应温度、煤的物理性质(孔隙度和比表面积)有关。
化学活性高,有利于气体质量和制气能力的提高。
②机械强度。
机械强度差的原料,在运输、破碎过程中甚至在进入固定层煤气炉后,易于破裂而生成不能用于气化的碎屑,不仅增大原料的消耗和造气成本,而且还会影响气化过程的正常运行。
因此固定层气化要求煤具有一定的脆度、抗碎或抗压强度。
③热稳定性。
指燃料在高温下保持其原来粒度大小的性质。
热稳定性差的燃料,在气化过程中易于破碎、产生大量碎末及小颗粒,使燃料层阻力增大,影响制气,煤的热稳定性按焦炭烟烟煤无烟煤褐煤依次减弱。
④粘结性。
煤的黏结性是指煤粉在隔绝空气条件下加热,产生胶质体,最后粘结成块状焦炭,并能使无粘结性的惰性物料粘结的性能。
煤的粘结性会破坏气化层中气体的分布,生成拱焦,使气化操作无法进行。
⑤粒度。
要求煤的粒度均匀、大小适当。
固定层入炉煤的粒度按25~100mm、15~25mm、8~15mm分别划分为块煤、小块煤和碎块煤。
综上所述,固定层气化应选择低水、低灰、高活性、高灰熔点、热稳定性好、机械强度高、不粘结的煤类原料。
2.加工煤球
随着机械化采煤的发展及煤在贮运中的自身破碎,煤的成块率一般只在40%~70%左右。
将煤中加入适量的黏结剂加工成粒度为35~55mm的煤球以代替块煤进行气化是将低成本的一项重要措施。
(1)煤球的种类煤球的种类习惯上以所用的黏结剂命名。
用熟石灰作粘结剂,经过碳酸化处理的煤球叫石灰碳化化煤球;
用纸浆黑液和粘土作粘结剂制成的煤球称为纸浆-粘土煤球。
此外还有沥青煤球、粘土煤球、水泥煤球、腐殖酸煤球等。
其中应用最广的煤球是石灰碳化煤球。
(2)煤球的气化特性将石灰碳化煤球加入煤气炉后,煤球中的碳酸钙受热分解,逸出的二氧化碳可增加内部的微孔结构。
煤球的空隙率大,反应表面积大,从而提高了煤球的化学活性,加快了气化反应速率。
与块状固体燃料相比,煤球的大小适宜,粒度一致,炉内燃料层透气性好,流体阻力小。
煤球灰渣的软化温度一般高于1250℃,且具有较高的热稳定性和机械强度,因此石灰碳化煤球可作为固定层间歇气化法的原料。
3.水煤浆
水煤浆的粉煤分散于水中所形成的固液悬浮体。
水煤浆浓度、煤的变质程度、煤的内在水分含量等对气化效率、煤气质量、原料消耗均有很大影响。
在水煤浆制备过程中,通过加入木质素磺酸钠、腐殖酸钠、硅酸钠或造纸废液等添加剂来调节水煤浆的黏度、流动性和稳定性。
第二节固体燃料气化原理
一、气化反应的化学平衡及影响因素
1.以空气为气化剂
以空气为气化剂时,碳与氧之间的反应
C+O2==CO2+393.7kJ(1-1)
2C+O2==2CO+220.9kJ(1-2)
2CO+O2==2CO2+566.1kJ(1-3)
CO2+C2CO-172.4kj(1-4)
(1)温度的影响依据化学平衡移动的理论,降低温度有利于式(1-1)、式(1-2)、式(1-3)反应向右进行,减小压力,有利于式(1-2)、式(1-4)反应向右进行。
在制取半水煤气的生产过程中,我们希望碳与氧的反应式(1-1)和式(1-3)进行,尽量避免发生式(1-2)和式(1-4)的反应。
其目的是提高燃料层的温度,并尽量减少碳的消耗。
实践证明,在高温燃料层中,当空气不断鼓入时,式(1-1)、式(1-2)、式(1-3)的正反应速率占绝对优势,反应主要向右进行,而且反应达到平衡时,平衡组成中几乎全是生成物,因此这三个反应可看成是不可逆反应。
将式(1-1)与式(1-4)两个反应的平衡常数随温度的变化值列于表1-3中。
表1-3反应式(1-1)与式(1-4)的平衡常数
从表1-3中可以看出,在平衡状态下,式(1-4)的平衡常数随温度的变化有很大差异,反应具有可逆性。
研究表明式(1-4)决定着整个系统的平衡,因此必须着重予以分析。
由图1-2所示,随着温度的升高,一氧化碳平衡含量增加,二氧化碳平衡含量下降。
当温度高于900℃时,气体中二氧化碳平衡含量甚少。
因此降低温度可增加二氧化碳平衡含量。
减少热量损耗。
(2)压力的影响式(1-4)是一个体积增大的反应。
压力对CO和CO2平衡组成的影响见图1-3
有图可见,总压增高,不利于CO2还原为CO的反应。
以上指气相中只有CO和CO2,实际上以空气为气化剂时有氮和氩的存在,由于氮和氩的存在降低了它们的分压,而使平衡向生成一氧化碳的方向移动。
比较表1-4和表1-5,同样在800℃,总压0.1MPa时,无惰气稀释的一氧化碳转化率为93.0%,而有惰气稀释的为95.2%。
以上从理论的角度分析了温度与压力对化学反应平衡的影响,在实际生产中,以空气为气化剂进行气化时,除了制取空气煤气外,还有一个重要的目的,就是提高固体燃料层的温度、维持燃料层各类反应的自热平衡。
为了解决理论(降低温度、减小压力)与实际(提高温度、增加压力)的矛盾,工业上采取的措施是增大空气的压力,增大氧的加入量,提高空气的流速,减少气体与碳量的接触时间,使碳与氧反应生成的二氧化碳来不及进行还原反应就离开燃料层;
同时要控制燃料层的高度和燃料层的温度不能过高。
2.以水蒸气为气化剂
C+H2O(汽)CO+H2—131.4kJ(1-5)
C+2H2O(汽)=CO2+2H2—90.20kJ(1-6)
生成的产物还可发生如下反应:
CO2+C2CO-172.4kj(1-7)
当温度较低时,还会发生副反应:
生成甲烷的和一氧化碳转化为氢的反应:
C+2H2=CH4+74.9kJ(1-8)
CO+H2O=CO2+H2+41.2kJ(1-9)
(1)温度的影响依据化学平衡移动的理论,提高反应温度可使反应式(1-5)、式(1-6)、式(1-7)向右移动,使反应式(1-8)、式(1-9)向左移动,这说明提高反应的温度,可以提高煤气中一氧化碳和氢的含量,减少二氧化碳和甲烷的含量,这正是工业生产所希望的。
由图1-4可知,压力一定时,随着温度的升高一氧化碳、氢气的含量增加。
温度高于900℃时,其他组分的含量接近于零,所以在高温下进行水蒸气与碳的反应,平衡时残余水蒸气气量减少,水煤气中氢气及一氧化碳的含量高。
(2)压力的影响式(1-4)、式(1-5)、式(1-6)都是体积增大的反应。
因此,降低蒸汽压力,可以使反应的平衡向右移动,有利于增加煤气中氢和一氧化碳的含量,减少甲烷和二氧化碳的含量。
比较图1-4及图1-5可见,在相同温度下,随着压力的提高,气体中水蒸气、二氧化碳及甲烷含量增加,而氢气及一氧化碳的含量减少。
所以,在制取煤气时,可根据所需组成,选择蒸汽分解(灼热的碳将氢从水蒸气中还原出来的过程称为蒸汽分解)的压力。
3.以空气和蒸汽同时为气化剂
以蒸汽与空气同时为气化剂,燃料层中气体组成的变化如下:
在灰渣层,气化剂只被预热,不发生化学反应;
在氧化层,主要发生碳的氧化反应,氧的含量急剧下降,二氧化碳的含量急剧上升,并有一定的一氧化碳开始生成,蒸汽的含量变化不大;
在还原层,主要进行水蒸气的分解及二氧化碳的还原反应,因此蒸汽和二氧化碳含