硫磺回收装置操作规程文档格式.docx
《硫磺回收装置操作规程文档格式.docx》由会员分享,可在线阅读,更多相关《硫磺回收装置操作规程文档格式.docx(98页珍藏版)》请在冰豆网上搜索。
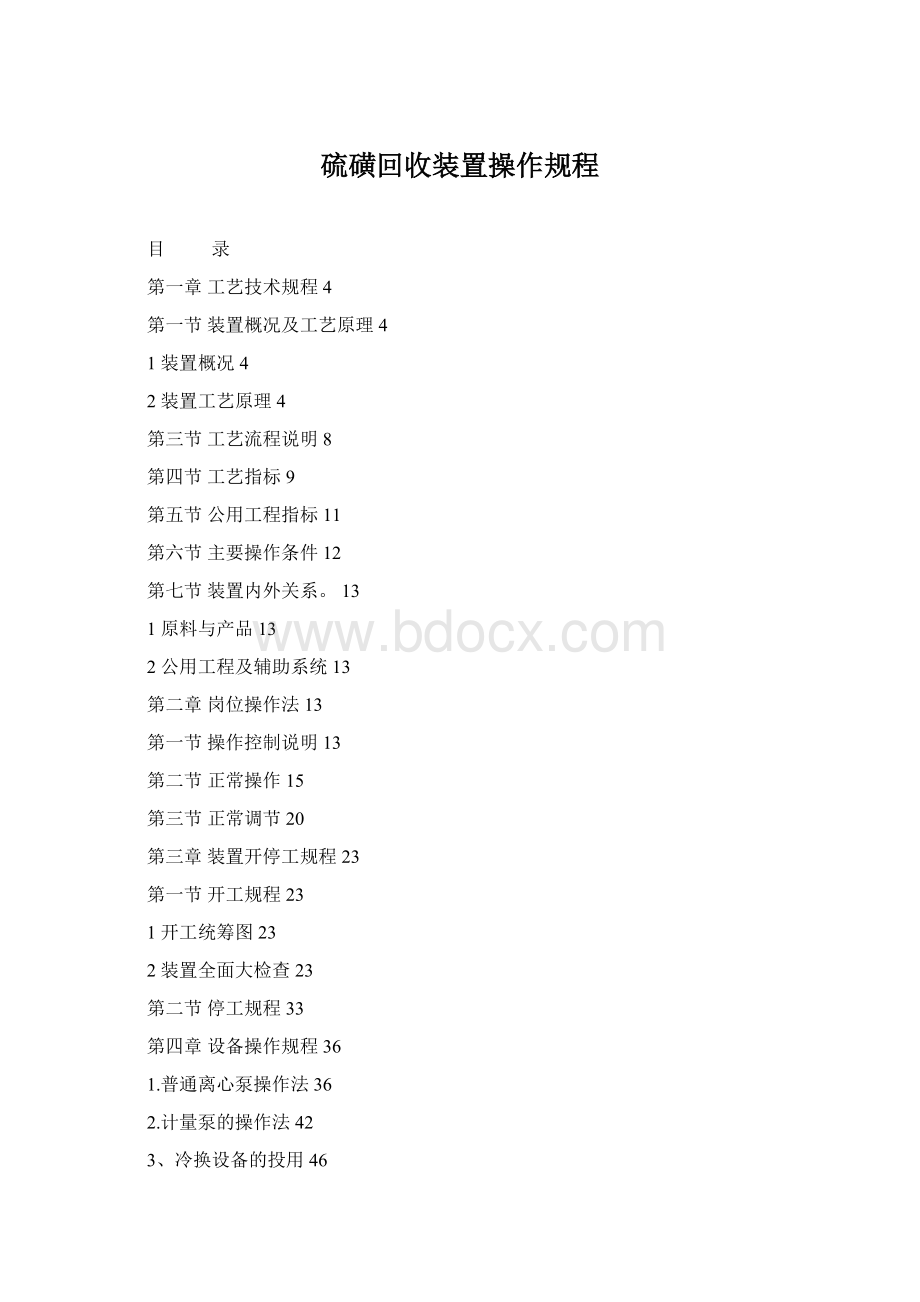
5.防静电安全知识67
6.防毒安全知识67
7.危险化学品安全知识68
8.消防安全知识69
9.本装置个人防护用品及使用方法71
10.现场急救知识74
第二节行业安全禁令75
1.五想五不干75
2.人身安全十大禁令75
3.防火防爆十大禁令76
4.车辆安全十大禁令76
5.防止储罐跑油(料)十条规定76
6.防止中毒窒息十条规定77
7.防止硫化氢中毒十条规定77
8.防止静电危害十条规定78
第三节安全规程79
1.装置检修后开车的安全规程79
2.装置停车的安全规程79
3.检修阶段的安全要求81
4.取样作业安全管理规定82
5.成型造粒机安全管理规定82
第四节防台风、防洪涝措施83
1.适用范围83
2.目的83
3.潜在威胁/风险分析83
4.台风前——准备83
第五节本装置易燃易爆物的安全性质88
第六节本装置主要有毒有害物质性质88
1.硫化氢88
2.二氧化硫88
3.三氧化硫89
4.硫磺89
第七节开工、停工环保管理规定………………………………………………90
附录一:
工艺流程图………………………………………………………………93
附录二:
安全阀一览表……………………………………………………………93
附录三:
设备一览表………………………………………………………………94
附录四:
装置开停工流程图………………………………………………………94
第一章工艺技术规程
1万吨/年硫磺回收装置为连续生产,按年运行8400小时设计。
装置分一、二期两部实施,一期工程包括制硫、液硫脱气、成型及尾气焚烧部分,尾气处理部分(含胺液再生)在二期工程时实施,装置预留二期工程位置。
第一节装置概况及工艺原理
1装置概况
本套硫磺回收装置由制硫、尾气处理和液硫成型三个部分组成。
装置年产硫磺约10000吨。
装置的设计操作弹性为50%-110%。
2装置工艺原理
2.1硫磺回收部分的工艺原理
该部分包括在制硫燃烧炉内发生的Claus热转化反应和在催化转化器内发生的Claus催化转化反应以及在余热锅炉和硫冷凝器内发生的硫磺的气态、液态转化反应。
1)Claus热转化反应
酸气中H2S含量不同,燃烧时所放出的热量也不同。
根据酸气中H2S的含量,对不同浓度的酸气分别采用部分燃烧法、直接氧化法、分流法来回收硫磺。
本装置酸气进料中H2S含量大于50%,故采用部分燃烧法回收硫磺。
即在制硫燃烧炉内通过控制一定量的配风,H2S部分燃烧转化成Sx(以S2表示)和SO2。
涉及到H2S的主要反应有:
H2SH2+1/2S2-905Kcal/Nm3H2S
(1)
H2S+1.5O2H2O+SO2+5531Kcal/Nm3H2S
(2)
H2S+0.5O2H2O+1/2S2+1674Kcal/Nm3H2S(3)
酸气进料中有大约6%的H2S发生分解反应
(1)。
热转化反应(3)主要取决于火焰温度,火焰温度由原料气体中H2S的浓度决定。
热转化反应(3)还受燃烧室内火焰停留时间的影响。
酸气中含有的氨发生如下所示的分解反应:
2NH3+1.5O2N2+3H2O+3380Kcal/Nm3NH3(4)
通过在火嘴内将酸气与燃烧空气适当混合,达到最低的火焰温度1250℃(设计操作温度1390℃),并使被烧掉的气体在反应炉内停留适当时间,可使氨全部被分解。
在酸气燃烧的过程中,其中所含的碳氢化合物按下列放热反应燃烧:
CH4+1.5O2CO+2H2O+5538Kcal/Nm3CH4
C2H6+2.5O22CO+3H2O+9190Kcal/Nm3C2H6
C3H8+3.5O23CO+4H2O+12743Kcal/Nm3C3H8
上述化学反应几乎是完全向右侧进行的反应。
少量碳氢化合物也按以下反应完全燃烧生成H2O和CO2:
CH4+2O2CO2+2H2O+8560Kcal/Nm3CH4
C2H6+3.5O22CO2+3H2O+15225Kcal/Nm3C2H6
C3H8+5O23CO2+4H2O+21800Kcal/Nm3C3H8
C4H10+6.5O24CO2+5H2O+28350Kcal/Nm3C4H10
C5H12+8O25CO2+6H2O+37700Kcal/Nm3C5H12
酸气中所含H2燃烧总是生成水,反应如下:
H2+0.5O2H2O+2578Kcal/Nm3H2
还应考虑到生成COS和CS2的副反应。
这些副反应与酸气中的CO2的含量和酸气中碳氢化合物燃烧过程中生成的CO2有关。
预计发生以下反应:
CO2+H2SCOS+H2O-321Kcal/Nm3H2S
CO2+2H2SCS2+2H2O-359Kcal/Nm3H2S
COS和CS2的生成主要取决于酸气中CO2和碳氢化合物的浓度。
以上所列出的化学反应只用于让操作员熟悉过程气中所含的化学物质种类,给出简单的理论。
这些并不代表在燃烧室内部发生的全部化学反应。
2)Claus催化转化反应
Claus催化转化反应将在最佳的转化器入口温度下,在转化器催化剂床层上进行。
主要反应有:
2H2S+SO22H2O+3/8S8+557Kcal/Nm3H2S(5)
反应(5)是可逆放热反应,低温促进反应向右进行。
COS和CS2水解生成H2S的副反应是重要反应,特别对一级Claus转化器。
由于一级转化器出口有适度的高温,并有改进的氧化铝催化剂,水解反应几乎已完成。
反应如下:
COS+H2OCO2+H2S+321Kcal/Nm3H2S
CS2+H2OCO2+2H2S+359Kcal/Nm3H2S
3)余热锅炉和硫冷凝器中的反应
下列是在燃烧阶段、催化转化阶段和过程气冷凝阶段发生的气态硫的平衡转化反应。
S8(气体)4S2(气体)-4327Kcal/Nm3S8
3S8(气体)4S6(气体)-444Kcal/Nm3S8
在热转化和催化转化阶段生成的气态硫在过程气冷却的过程中,在硫冷凝器中进行冷凝。
化学反应如下:
S8(气体)8S1(液体)+1117Kcal/Nm3S8
S6(气体)6S1(液体)+1171Kcal/Nm3S6
S2(气体)2S1(液体)+1372Kcal/Nm3S2
4)燃料气操作工艺原理
燃料气操作用于装置从冷态开车时将装置升温,或者在酸气操作之后将装置中的硫清理干净,使装置降温,以便进行检修或长期停车。
在这种操作中,绝热火焰必须保持低于反应炉耐火衬里材料的最高操作温度。
用冷却蒸汽来调节火焰温度,使其不超过1400℃,冷却蒸汽由酸气接口注入火嘴。
当装置中有硫存在时(在装置正常操作过程中,硫通常存在于Claus转化器的催化剂床层),燃料气的燃烧必须按化学计量条件进行。
实际上,当燃料气与过量O2进行燃烧时,O2会与装置中的硫反应,无法控制局部高温及SO2和SO3的生成。
如果存在过量O2,过量O2会与装置中的硫反应,特别是催化剂上的硫,化学反应如下:
S+O2SO2+3165Kcal/Nm3S
该反应必须小心避免。
因此在燃烧烟气中几乎应不含O2,换句话说,燃料气燃烧应该按化学计量条件进行。
相反,如果燃料气的燃烧缺少O2,则燃料气中的碳氢化合物不能完全燃烧,会生成一些炭。
炭容易被催化剂床吸收或过滤截留,催化剂因此被污染,生产出的硫的质量变差。
实际上,用低于0.1-0.2%(体积)的O2含量操作,燃料气中的一部分甲烷将按以下方程式发生反应:
CH4+1.5O2CO+2H2O+5540Kcal/Nm3CH4
CH4+2O2CO2+2H2O+8560Kcal/Nm3CH4
C2H6+3.5O22CO2+3H2O+15225Kcal/Nm3C2H6
C3H8+5O23CO2+4H2O+21800Kcal/Nm3C3H8
C4H10+6.5O24CO2+5H2O+28350Kcal/Nm3C4H10
C5H12+8O25CO2+6H2O+37700Kcal/Nm3C5H12
当O2缺少过多时,甲烷燃烧会按以下反应进行:
CH4+O2C+2H2O+4360Kcal/Nm3CH4
比CH4更重的碳氢化合物也按相同方式反应。
在此,化学计量燃烧条件被定义为燃料气中的全部碳氢化合物燃烧生成CO2和H2O,燃烧烟气中有少量过量O2(最高含量O2=0.4%;
CO=0.4%)。
5)液硫脱气部分的工艺原理
Claus硫磺回收部分中生成的单质硫含有溶解的H2S和以H2Sx形式化学结合的H2S。
H2SxH2S+(x-1)S
在液硫脱气部分H2Sx分解为H2S和S,分解出的H2S和液硫中溶解的H2S被气提出液硫。
其反应原理如下:
H2Sx溶胶H2S溶胶+(x-1)SH2S气体+(x-1)S
随着H2S从系统中的脱除,上述平衡反应向右侧进行,H2Sx进一步分解,可脱除更多的H2S。
2.2尾气焚烧工艺原理
尾气的点火温度比尾气的实际温度高很多,因为尾气中含有的可燃组分浓度非常低,因此尾气的燃烧必须有燃料气的支持。
尾气焚烧炉温度保持在750°
C,燃烧废气中O2含量为2%,该含量足够稀释释放到大气中的废气的H2S浓度到10ppm(vol.)。
尾气焚烧炉中的反应如下:
H2S+1.5O2SO2+H2O+5531Kcal/Nm3H2S
COS+1.5O2CO2+SO2+5880Kcal/Nm3COS
CS2+3O2CO2+2SO2+11780Kcal/Nm3CO2
H2+0.5O2H2O+2578Kcal/Nm3H2
CO+0.5O2CO2+3018Kcal/Nm3CO
SO2+0.5O2SO3+1046Kcal/Nm3SO2
前面四个反应基本是定量反应。
涉及H2和CO的反应是非定量反应,取决于下述反应平衡。
CO+H2OCO2+H2.
在750°
C时,大约有85%的H2,50%的CO被氧化。
第三节工艺流程说明
1、克劳斯硫回收部分
从装置外来的二路酸性气经分液罐D—8101脱液,然后进入反应炉(F—8101)燃烧。
从分液罐来的酸性水用泵送至酸性水装置。
从空气鼓风机K—8101来的空气进入反应炉F—8101,反应炉供给充足的空气,使酸性气中的烃和氨完全燃烧,同时使酸性气中65%的H2S直接燃烧生成单质硫,剩余三分之一H2S燃烧成SO2。
为了使氨燃烧得更完全,必须使反应炉温度控制在1250℃以上,反应炉的配风量是通过测量酸性气流量经计算得到的,大部分配风量是通过主动空气调节阀来实现,大约负荷的7.5%空气流量是由微调空气调节阀来控制,其设定值由安装在尾气管线上H2S/SO2在线分析仪给定,确保了反应炉空气与酸性气的最佳配比,从而提高装置硫转化率。
燃烧气经废热锅炉ER—8101热量交换产生高压饱和蒸汽,过程气进入第一硫冷凝器E—8101冷却后,硫蒸汽被冷凝下来并与过程气分离,经高温掺合阀TV-0501来的过程气进入第一反应器R—8101,过程气中H2S和SO2在催化剂作用下发生反应,直到平衡,同时也使部分COS和CS2发生水解反应,反应后的气体先进入过程气换热器E-8104换热后再进入第二硫冷凝器E—8102进行冷却并分离出液硫,然后过程气再进入过程气换热器E-8104,最后进入第二反应器R—8102继续反应,反应后的气体进入第三硫冷凝器E—8103冷却,进一步回收硫磺。
从第一、二、三硫冷凝器、尾气分液罐和过程气换热器得到的液硫,各自经硫封罐D—8105A/B/C/D/E后进入液硫池T—8101,从第三硫冷凝器E—8103出来的尾气进入尾气分液罐。
2、尾气焚烧部分
焚烧炉F—8201焚烧克劳斯尾气、液硫池废气及开工排放尾气中的的S组
分。
焚烧要求在450-550℃的高温和过空气情况下进行。
至焚烧炉烧嘴的第一空气为瓦斯燃烧化学计量的110%,以确保烧咀燃烧的组分在空气10%过量情况下得以完全燃烧。
尾气与烧咀来的高温气体以及第二空气在焚烧炉内混合,把烟道气降温至300℃左右,第二空气具有二个作用,其一确保尾气在过氧量情况下完全燃烧,使烟道气中氧含量大于1.8%(V),其二对焚烧炉起到冷却作用,使其温度接近450-550℃,其流量由焚烧炉炉膛温度控制。
焚烧炉产生的高温气体必须冷却至一定温度才能进入管道和烟囱,冷却分为二个过程,用过热器E—8201取走部分热量,冷却至300℃左右的烟气至烟囱ST—8201放空。
从反应炉废热锅炉产生的高压蒸汽与装置外来的中压蒸汽混合进入蒸汽过热器,过热后的高压蒸汽经减温器S—8201减温至300℃左右送出装置。
3、液硫脱气部分
各硫封罐D—8105A/B/C/D/E的液硫大约含有300ppm的硫化氢,其进入液硫池的脱气部分,氨气进入用液硫脱气泵进行循环,使大部分液硫中的硫化氢生成硫氢化氨。
液硫越过液硫池的液硫堰进入贮存部分,贮存部分液硫停留时间为48小时,当液硫超过一定高度后,通过液硫泵P-8103A/B把液硫输送至成型系统。
为了防止贮存部分和分离部分的液硫冷却凝固,在液硫池底部安装加热管,保持液硫温度在130~150℃之间,蒸汽伴热不必长期投用。
为了防止液硫在过氧情况下的燃烧,液硫池气相部分设置温度检测仪,一旦温度过高操作人员需用蒸汽降温。
离开气泡柱后的空气带有液硫释放出来的硫化氢,其在蒸汽抽射器EJ-8101驱动下通过除雾器抽至焚烧炉焚烧,抽射器的吸入量由液硫池顶部放空管吸入空气来补充。
为了防止液硫池气相达到爆炸极限,脱气部分启用时需有足量的空气吹扫一定时间,投用后的废气流量也必须达到设计要求。
第四节工艺指标
名称
项目
单位
指标
原料质量指标
原料气
胺酸气H2S浓度
%(v/v)
≥60
胺酸气烃含量
≤3
胺酸气氨含量
≤15
汽提酸气H2S浓度
汽提酸气烃含量
汽提酸气氨含量
≤4
中压除氧水
中压除氧水pH
8.8~9.2
中压除氧水硬度
μmol/l
≤2.0
中压除氧水溶解氧
μg/l
中压除氧水二氧化硅
μg/kg
≤20
产品质量指标
硫磺
纯度
%(m/m)
≥99.6
主要操作指标
反应炉F-810炉膛温度
℃
1100~1300
酸性气入炉压力
MPa
0.05
制硫余热锅炉ER-8101液位
%
40~70
一级反应器R-8101入口温度
225~250
一级反应器R-8101床层温度
≤350
硫磺冷凝器E-8101/8102/8103液位
二级反应器R-8102入口温度
205~220
二级反应器R-8102床层温度
尾气浓度:
H2S-2S02
-1~1
液硫池T-8101液硫温度
130~155
液硫池T-8101气相温度
≤170
低压蒸汽压力
0.33~0.42
低压蒸汽温度
152~165
焚烧炉F-8102炉膛温度
450~550
烟道气氧含量
1~5
动力工艺指标
脱氧水压力
1.6~2.0
脱氧水温度
≥105
冷却水温度
≤32
冷却水压力
0.35~0.45
仪表气压力
0.4
仪表气温度
常温
新鲜水压力
0.35
燃料气压力
0.45~0.55
氮气压力
0.8
氮气温度
环境保护指标
烟道气SO2含量
mg/m3
<850
烟道气NOx含量
≤120
烟道气H2S排放量
kg/h
≤9.3
第五节公用工程指标
(1)电源
6KV,3相,3线,50HzAC
380V,3相和中性,50HzAC
220V,1相和中性,50HzDC
电机功率范围:
<
160kw380V
≥160kw6KV
(2)锅炉给水
1)低压锅炉给水
温度:
104°
C压力:
2.0MPa
2)中压锅炉给水
5.5MPa
(3)N2
环境温度
压力(界区):
0.8MPa
纯度:
99.9%
露点:
-60℃
(4)冷却水
给水温度:
33℃
给水压力:
0.4MPa
回水温度:
42℃
回水压力:
0.25MPa
典型结垢传热系数:
3.0×
10-4~3.5×
10-4m2·
K/W
(5)净化风
0.7MPa
含尘量:
3μm颗粒≤1mg/m3
含油量:
≤10mg/m3
-20℃
(6)非净化风
压力(界区)0.55~0.75MPa
(7)蒸汽
1)高压(MP)蒸汽
压力(MPa)温度(℃)
最高3.8425
正常3.5390
最低3.3370
2)中压(LP)蒸汽
最高1.2320
正常1.1250
最低1.0220
3)低压(LLP)蒸汽
最高0.6饱和,高达220℃绝压
正常0.45
最低0.4
(8)凝结水
100℃压力:
0.3MPa
(9)除盐水
30℃压力:
第六节主要操作条件
1.主要操作条件
1、反应炉F-8101炉膛温度:
1100~1300℃。
2、酸性气入炉压力:
0.05MPa
3、制硫余热锅炉ER-8101液位:
40~70%。
4、一级反应器R-8101入口温度:
225~250℃,床层温度:
不大于350℃。
5、硫磺冷凝器E-8101/8102/8103液位:
6、二级反应器R-8102入口温度205~220℃,床层温度:
7、尾气浓度:
H2S-2S02:
-1~1%(V)。
8、液硫池T-8101液硫温度130~155℃,气相温度:
不大于170℃。
9、低压蒸汽压力:
0.33~0.42MPa,低压蒸汽温度:
152-165℃。
10、焚烧炉F-8102炉膛温度450~550℃,烟道气氧含量:
1%~5%(v)。
1原料与产品
1)装置所需原料由全厂生产装置和酸性水汽提装置通过管道送入。
2)装置所产生的固体硫磺由汽车运出。
副产的3.5MPa水蒸汽经本装置过热后由管线送往系统管网。
3)装置设酸性气事故放空管线接系统酸性气火炬。
2公用工程及辅助系统
1)本装置所需的蒸汽、新鲜水、净化水、非净化风、N2等公用工程管线自系统引进本装置。
2)装置所需的燃料气、锅炉给水、除盐水由系统管线引入。
3)装置所需的催化剂(固体、桶装)、化学药剂(液体、桶装)车运至本装置。
4)装置所产生的含盐污水及含油污水管线送至污水处理厂。
含酸污水管线送至污水汽提装置。
第二章岗位操作法
第一节操作控制说明
1.硫酸盐还原
氧化铝催化剂表面的氧化铝会与二氧化硫发生反应生成硫酸盐,使催化剂活性中心失去活性,二氧化硫、氧气和氧化铝相互作用的条件是高的温度和高的氧分压,相反的,硫酸盐在H2S作用下的还原反应也需较高的温度,在250~340℃的温度下,还原反应和硫酸盐化反应的速度都很快,硫酸盐还原后生成了硫和水。
催化剂硫酸盐化后保持表面积大于150㎡/g不变,但由于硫酸盐的存在其活性下降,因此必须对催化剂复活。
催化剂复活一般安排在装置停工之前进行,复活时间为24小时。
由于第一反应器催化剂活性对硫酸盐不太敏感,但不管怎样,催化剂活性会有所下降,因此催化剂也必须复活。
在大多数情况由于第一反应器入口过程气中H2S浓度足够高,这样还原反应只要提高反应温度300~350℃即可。
而第二反应器催化剂还原时,需减少反应炉的空气与酸性气的配比,控制入第二反应器过程气中H2S含量为2~3%,反应温度提高至300~350℃。
2、热浸泡
在开工期间,硫被吸附在催化剂的细孔中,这对装置的操作没有影响。
在正常操作期间,若催化剂床层温度低于露点温度,硫被冷凝在催化剂表面,使催化剂活性下降,当催化剂积累硫太多时,从日常的操作数据可以看出。
从催化剂床层去掉硫操作方法为:
提高反应器入口温度大约15~30℃,操作时间不少于24小时。
3、氨的燃烧
反应炉内必须把酸性气所带的氨全部燃烧掉,使过程气中的氨含量为几个PPm,氨不完全燃烧就会在温度较低部位引起氨盐堵塞(如硫冷凝器出口)。
要使氨得到完全的燃烧,要求的反应炉有足够高的燃烧温度,因此当装置的处理污水汽提装置酸性气时,反应炉燃烧温度至少1250℃,在装置酸性气组成达到设计点时,反应炉火焰温度大约1278℃,燃烧空