模具设计与制造冲裁模文档格式.docx
《模具设计与制造冲裁模文档格式.docx》由会员分享,可在线阅读,更多相关《模具设计与制造冲裁模文档格式.docx(87页珍藏版)》请在冰豆网上搜索。
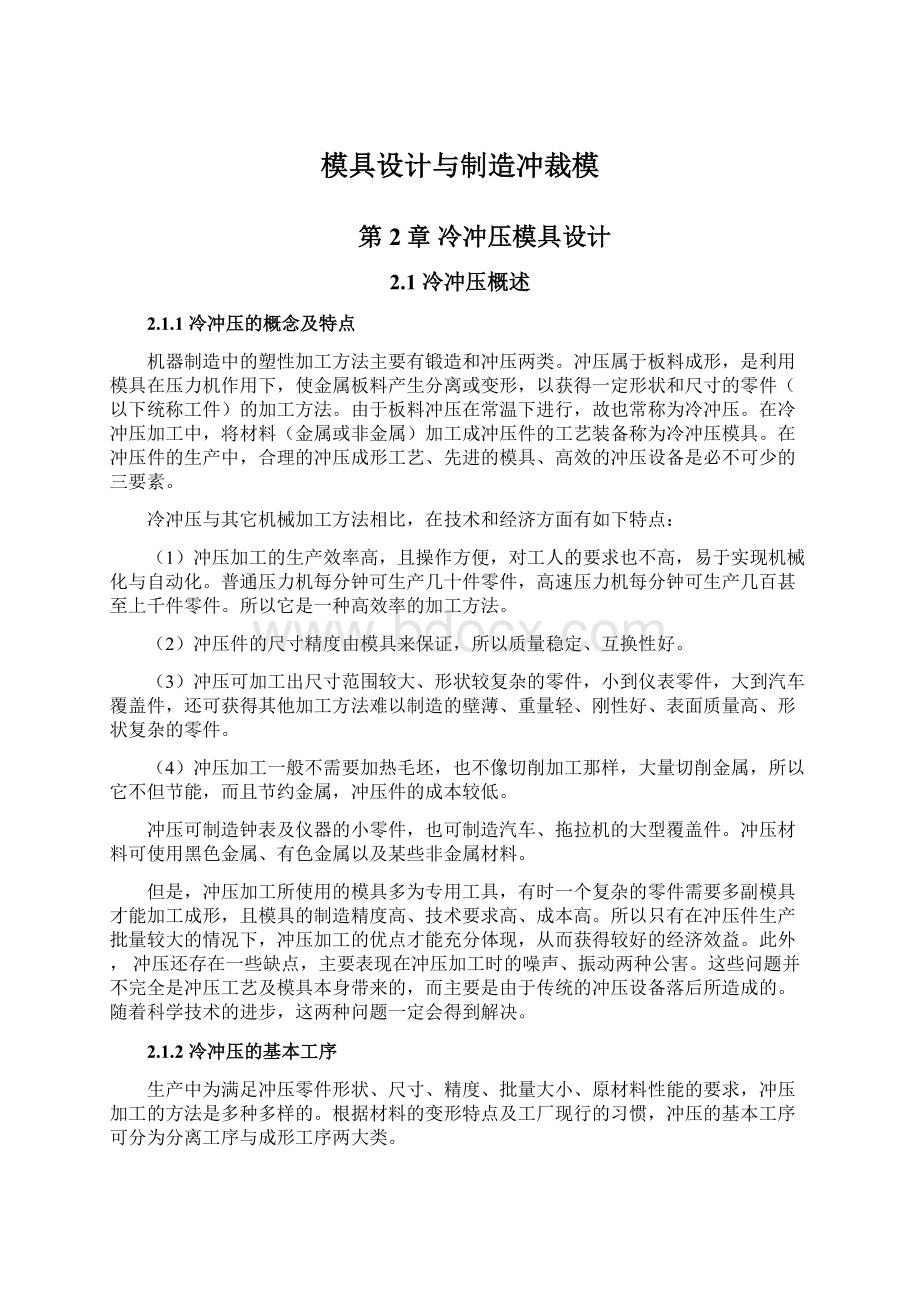
成形工序
拉深
用模具将板料制成开口空心件
成成形
起伏(压筋)
用模具将板料局部拉深成凸起和凹进形状
翻
边
用模具将板料上的孔或外缘翻成直壁
缩口
用模具对空心件口部施加由外向内的径向压力,使局部直径缩小
胀形
用模具对空心件施加向外的径向力,使局部直径扩张
整形
将工件不平的表面压平;
将原先弯曲或拉深件压成正确形状
同拉深模具
2.1.3常用冲压材料
1.材料的种类
常用冲压材料一般可分为三大类:
黑色金属板料、有色金属板料和非金属板料。
(1)黑色金属
主要有普通碳素结构钢、优质碳素结构钢、合金结构钢、碳素工具钢、不锈钢、电工硅钢等。
优质碳素结构钢钢板主要用于成形复杂的弯曲件和拉深件。
对冷轧钢板,根据国家标准GB708-88规定,按轧制精度(钢板厚度精度)可分为A级和B级:
A级较高精度;
B级普通精度。
对厚度4mm以下的冷轧薄钢板,根据GB/T13237一1991规定:
表面质量可分为I、Ⅱ、Ⅲ三组。
按拉深级别又分为Z、S、P三级:
I高级的精整表面;
Ⅱ较高级的精整表面;
Ⅲ普通的精整表面;
Z最深拉深级;
S深拉深级;
P普通拉深级。
(2)有色金属
包括有纯铜、黄铜、青铜、铝等。
常用的有色金属主要有黄铜板(带)和铝板等.
(3)非金属材料
主要有纸板、胶木板、橡胶板、塑料板、纤维板和云母等。
2.材料的规格
冲压用材料大部分都是各种规格的板料、带料、条料和块料。
板料的尺寸较大,用于大型零件的冲压。
主要规格有500mm×
1500mm、900mm×
1800mm、1000mm×
2000mm等。
条料是根据冲压件的需要,由板料剪裁而成,用于中、小型零件的冲压。
带料(又称卷料)有各种不同的宽度和长度。
成卷状供应的主要是薄料。
适用于大批量生产的自动送料。
块料一般用于单件小批生产和价值昂贵的有色金属的冲压,并广泛用于冷挤压。
关于材料的牌号、规格和性能,可查阅有关设计资料和标准。
表2-2给出了常用冷冲压材料的机械性能,从表中数据,可以近似判断材料的冲压性能。
表2-2冷冲压常用材料的机械性能
材料名称
牌号
材料状态及代号
力学性能
抗剪强度
τ/Mpa
抗拉强度
σb/Mpa
屈服点
σS/Mpa
伸长率
δ(%)
普通碳素钢
Q195
Q235
Q275
未经退火
255~314
315~390
195
28~33
303~372
375~460
235
26~31
392~490
490~610
275
15~20
碳
素
结
构
钢
08F
08
10F
10
15
20
35
45
50
已退火
230~310
275~380
180
27~30
260~360
215~410
200
27
220~340
275~410
190
260~340
295~430
210
26
270~380
335~470
230
25
280~400
355~500
250
24
400~520
490~635
320
19
440~560
530~685
360
440~580
540~715
380
13
不锈钢
1Cr13
320~380
440~470
120
1Cr18Ni9Ti
经热处理
460~520
560~640
40
铝
1060、1050A、
1200
80
70~110
50~80
20~28
冷作硬化
100
130~140
——
3~4
硬铝
2A12
105~125
150~220
12~14
淬硬并经自然时效
280~310
400~435
368
10~13
淬硬后冷作硬化
280~320
400~465
340
8~10
纯铜
T1、T2、T3
软
160
70
29~48
硬
240
300
25~40
黄铜
H62
260
294~300
3
半硬
343~460
420
≥12
H68
280
340~441
400
392~400
2.1.4冷冲压模具与冷冲压设备的关系
1.冷冲压设备的类型
冲压设备属锻压机械。
常见冷冲压设备有机械压力机(以Jxx表示其型号)和液压机(以Yxx表示其型号)。
机械压力机按驱动滑块机构的种类可分为曲柄式和摩擦式;
按滑块个数可分为单动和双动;
按床身结构形式可分为开式(C型床身)和闭式(Ⅱ型床身);
按自动化程度可分为普通压力机和高速压力机等。
而液压机按工作介质可分为油压机和水压机。
常用冷冲压设备的工作原理和特点如表2-3所示。
表2-3常用冷冲压设备的工作原理和特点
类型
设备名称
工作原理
特点
机械压力机
摩擦压力机
利用摩擦盘与飞轮之间相互接触并传递动力,借助螺杆与螺母相对运动原理而工作
结构简单,当超负荷时只会引起飞轮和摩擦盘之间的滑动,而不致损坏机件,但飞轮磨损太大,生产率低,适用于中小型件的加工,用于校正、压印和成形等冲压工序较为适宜
曲柄压力机
利用曲柄连杆机构进行工作,电机通过皮带轮和齿轮带动曲轴转动,经连杆带动滑块作直线往复运动
生产率高,适用于各类冲压加工
高速压力机
工作原理与曲柄压力机相同,但其刚度、精度和行程次数较高,一般带有自动送料和安全检测装置
生产率高,适用于大批量生产,模具一般采用多工位级进模
液压机
油压机
水压机
利用帕斯卡原理,以水和油为工作介质,采用静压力传递进行工作,使滑块作上下往复运动
压力大,而且是静压力。
但生产率低,适用于拉深、挤压等成形工序等
2.冷冲压设备的选用
(1)类型选择
冲压设备类型较多,其刚度、精度、用途各不相同,应根据冲压工艺的性质、生产批量、模具大小、工件精度等正确选用。
一般生产批量较大的中小工件多选用操作方便、生产效率高的开式曲柄压力机。
如生产洗衣桶这样的深拉深件,最好选用有拉深垫的拉深油压机。
而生产汽车覆盖件则最好选用工作台面宽大的闭式双动压力机。
(2)规格选用
确定压力机的规格时应遵循如下原则:
1)压力机的公称压力必须大于冲压工序所需压力,当冲压工作行程较长时,还应注意
在全部工作行程上,压力机许可压力曲线应高于冲压变形力曲线。
2)压力机滑块行程应满足工件在高度上能获得所需尺寸,并在冲压工序完成后能顺利地从模具上取出来。
对于拉深件,则行程应大于工件高度两倍以上。
3)压力机的行程次数应符合生产率和材料变形速度的要求。
4)压力机的闭合高度、工作台面尺寸、滑块尺寸、模柄孔尺寸等都应能满足模具的正确安装要求。
对于曲柄压力机,如图2-1所示,模具的闭合高度与压力机的闭合高度之间要符合以下关系
Hmax-5mm≥H模+H1≥Hmin+10mm(2-1)
式中H模模具的闭合高度(mm);
Hmax压力机的最大闭合高度(mm);
Hmin压力机的最小闭合高度(mm);
H1压力机的垫板厚度(mm)。
图2-1模具的闭合高度与压力机闭合高度关系
2.2冲裁模设计
冲裁是利用模具使板料沿着一定的轮廓形状产生分离的一种冲压工序。
冲裁工序的种类很多,常用的有切断、落料、冲孔、切口、剖切、修边等。
但一般来说冲裁主要是指落料和冲孔。
若使材料沿封闭曲线相互分离,封闭曲线以内的部分作为冲裁件时,称为落料;
而封闭曲线以外的作为冲裁件时,称为冲孔。
例如冲制平面垫圈,冲其外形的工序称落料,冲其内孔的工序称冲孔。
冲裁是冲压工序中最基本的工序之一,其应用非常广泛,它既可直接冲制成品零件,又可为其它成形工序制备坯料。
根据变形机理不同,冲裁可分为普通冲裁和精密冲裁。
这里主要介绍普通冲裁。
冲裁所使用的模具称为冲裁模,如落料模、冲孔模、切边模、冲切模等。
2.2.1冲裁工艺及设计计算
1.冲裁过程分析
图2-2所示为普通冲裁示意图,凸模1与凹模2具有与冲裁件轮廓相同的锋利刃口且相互之间保持均匀合适的间隙。
冲裁时,板料3置于凹模上方,当凸模随压力机滑块向下运动时,冲穿板料进入凹模,使冲裁件与板料分离,从而完成冲裁工作。
从凸模接触板料到板料相互分离是在瞬间完成的。
冲裁变形过程大致可分为三个变形阶段。
(1)弹性变形阶段
如图2-3a所示,当凸模接触板料并下压时,在凸、凹模压力作用下,板料开始产生弹性压缩、拉伸、弯曲等复杂变形。
这时,凸模略微挤入板料上部,板料下部也略微挤入凹模洞口,并在凸、凹模刃口接触处形成很小的圆角。
同时板料稍有穹弯,材料越硬,凸、凹模刃口间隙越大,穹弯越严重。
随着凸模的下压刃口附近板料所受的应力逐渐增大,直至到达弹性极限,弹性变形阶段结束。
(a)(b)(c)(d)
图2-3冲裁变形过程
(2)塑性变形阶段
当凸模继续下压,使板料变形区的应力达到塑性变形条件时,开始进入塑性变形阶段,如图2-3b所示。
这时,凸模挤入板料和板料挤入凹模的深度逐渐增大,产生塑性剪切变形,形成光亮的剪切断面。
随着凸模的下降,塑性变形程度增加,变形区材料硬化程度加剧,变形抗力不断上升,冲裁力也相应增大,直到刃口附近的应力达到抗拉强度时,塑性变形阶段结束。
由于凸、凹模间隙的存在,此阶段中冲裁变形区还伴随着弯曲和拉伸变形,且间隙越大,弯曲和拉伸变形也越大。
(3)断裂分离阶段
当板料内的应力达到抗拉强度后,凸模再向下压时,则在板料上与凸模、凹模刃口接触的部位先后形成裂纹,如图2-3c所示。
裂纹的起点一般在距刃口很近的侧面,且一般先在凹模刃口附近的侧面产生,然后才在凸模刃口附近的侧面产生。
随着凸模的继续下行,已产生的上、下裂纹将沿最大剪应力方向不断向板料内部扩展,当上、下裂纹重合时,板料被剪断分离,如图2-3d所示。
随后,凸模将分离的材料推入凹模洞口,至此,冲裁变形过程结束。
2.冲裁件的工艺性
冲裁件的工艺性是指冲裁件对冲裁工艺的适应性,即冲裁加工的难易程度。
良好的冲裁工艺性是指在满足冲裁件使用要求的前提下,能以最简单、最经济的冲裁方式加工出来。
因此,在编制冲压工艺规程和设计模具之前,应对冲裁件的形状、尺寸和精度等方面进行分析。
从工艺角度分析冲裁件设计得是否合理,是否符合冲裁的工艺要求。
(1)冲裁件的结构工艺性
1)冲裁件的形状应力求简单、规则,有利于材料的合理利用,以便节约材料,减少工序数目,提高模具寿命,降低冲裁件成本。
2)冲裁件的内、外形转角处要尽量避免尖角,应以圆弧过渡,以便于模具加工,减少热处理开裂,减少冲裁时尖角处的崩刃和过快磨损。
冲裁件的最小圆角半径可参照表2-4选取。
表2-4冲裁件最小圆角半径
工序
圆弧角度
α
最小圆角半径
黄铜、铝
低碳钢
合金钢
备注
α≥90°
α<90°
0.18t
0.35t
0.25t
0.50t
0.70t
≥0.25
≥0.50
α≤90°
0.20t
0.40t
0.30t
0.60t
0.45t
0.90t
≥0.30
≥0.60
注:
t为料厚。
3)尽量避免冲裁件上过于窄长的凸出悬臂和凹槽,否则会降低模具寿命和冲裁件质量,如图2-4所示。
一般情况下,悬臂和凹槽的宽度B≥1.5t(t为料厚,当料厚t<lmm时,按t=lmm时计算);
当冲裁件材料为黄铜、铝、低碳钢时,B≥1.5t;
当冲裁件材料为高碳钢时,B≥2t。
悬臂和凹槽的深度L≤5B。
图2-4冲裁件的悬臂与凹槽
4)冲孔时,因受凸模强度的限制,孔的尺寸不应太小。
冲孔的最小尺寸取决于材料凸模强度和模具结构等。
5)冲裁件的孔与孔之间、孔与边缘之间的距离,受模具强度和冲裁件质量的制约,其值不应过小,一般要求c≥(1~1.5)t,c′≥(1.5~2)t,如图2-5a所示。
在弯曲件或拉深件上冲孔时,为避免冲孔时凸模受水平推力而折断,孔边与直壁之间应保持一定的距离,一般要求L≥R十0.5t,如图2-5b所示。
(a)(b)
图2-5冲裁件上的孔距以及孔边距
(2)冲裁件的精度和断面质量
1)冲裁件的精度
冲裁件的经济公差等级不高于ITl1级,一般要求落料件公差等级最好低于ITl0级,冲孔件最好低于IT9级。
此外,冲裁件的尺寸公差标注及基准的选择应尽可能与模具设计基准一致,以减小误差。
2)冲裁件的断面质量
冲裁件的断面粗糙度及毛刺高度与材料塑性、材料厚度、冲裁间隙、刃口锋利程度、冲裁模结构及凸、凹模工作部分表面粗糙度等因素有关。
用普通冲裁方式冲裁厚度为2mm以下的金属板料时,其断面粗糙度Ra一般可达到12.5~3.2μm,毛刺的允许高度见表2-5。
表2-5普通冲裁毛刺的允许高度mm
料厚t
≤0.3
>0.3~0.5
>0.5~1.0
>1.0~1.5
>1.5~2
试模时
≤0.015
≤0.02
≤0.03
≤0.04
≤0.05
生产时
≤0.08
≤0.10
≤0.13
≤0.15
3.冲裁件的质量
(1)冲裁件的质量
图2-6冲裁件的断面质量
冲裁件的质量是指冲裁件的断面质量、尺寸精度和形状误差。
冲裁件的断面应尽可能垂直、光滑、毛刺小;
尺寸精度应保证在图纸规定的公差范围以内;
冲裁件外形应符合图纸要求,表面应尽可能平直。
1)冲裁件的断面质量冲裁件断面呈明显的四个特征区,即塌角带、光亮带、断裂带和毛刺,如图2-6所示。
塌角带a该区域的形成主要是当凸模刃口刚压入板料时,刃口附近的材料产生弯曲和伸长变形,材料被带进模具间隙的结果。
光亮带b该区域发生在塑性变形阶段,当刃口切入金属板料后,板料与模具侧面挤压而形成的光亮垂直的断面。
正常情况约占全断面的1/2~1/3。
断裂带c该区域是在断裂阶段形成的,是由于刃口处产生的微裂纹在拉应力的作用下不断扩展而形成的撕裂面,其断面粗糙,具有金属本色,且带有斜度。
因断裂带都是向材料内倾斜,所以对一般应用的冲裁件并不影响其使用性。
毛刺d毛刺的形成是由于在塑性变形阶段后期,凸模和凹模的刃口切入被加工的板料一定深度时,刃口正面材料被压缩,微裂纹的起点不会在刃尖处发生,而是在刃口侧面距刃尖不远的地方发生。
普通冲裁中毛刺是不可避免的,但间隙合适时,毛刺的高度较小,易去除。
毛刺影响冲裁件的外观和使用性能,因此希望毛刺越小越好。
2)冲裁件的尺寸精度冲裁件的尺寸精度是指冲裁件的实际尺寸与公称尺寸之差。
差值越小,精度就越高。
该差值包括冲裁件相对于凸模或凹模尺寸的偏差和模具本身的制造偏差两方面。
3)冲裁件形状误差冲裁件形状误差是指翘曲、扭曲、变形等缺陷。
(2)冲裁件质量的影响因素
冲裁件质量影响因素主要有以下几个方面:
1)材料的性能对冲裁件质量的影响
对于塑性较好的材料,冲裁时裂纹出现得较迟,因而材料被剪切挤压的深度较大。
所得到的断面光亮带所占比例大,断裂带较小,但圆角和毛刺也较大;
而塑性差的材料,当剪切开始不久.材料便被拉裂,使断面光亮带所占比例小,断裂带较大,但圆角和毛刺都较小。
对于比较软的材料,弹性变形量较小,冲裁后的弹性恢复也较小,因而冲裁件的精度较高;
硬的材料则相反。
2)冲裁间隙对冲裁件质量的影响
冲裁间隙是影响冲裁件断面质量的主要因素。
当间隙合适时,上、下刃口处产生的剪切裂纹基本重合,这时光亮带约占板厚的1/2~1/3左右,圆角、毛刺和断裂带斜角均较小,断面质量较好,如图2-7a所示。
当间隙过小时,上、下裂纹延伸后互不重合。
两裂纹之间的材料,随着冲裁的进行将被第二次剪切,在断面上形成第二光亮带,该光亮带中部有残留的断裂带。
小间隙会使应力状态中的拉应力成分减小,挤压作用增大,使材料塑性得到充分发挥,裂纹的产生受到抑制而推迟。
所以,断面光亮带宽度增加,圆角、毛刺、斜度、翘曲、穹弯等弊病都有所减小,断面质量较好,但断面的质量也有缺陷,如中部的夹层等。
毛刺比合理间隙时高一些,但易去除,如图2-7b所示。
当间隙过大时,上、下裂纹也不重合。
因变形材料应力状态中的拉应力成分增大,材料的弯曲和拉伸也增大,材料容易产生微裂纹,使塑性变形较早结束。
所以,断面光亮带减小,毛面、圆角带增大,毛刺和斜度较大,穹弯、翘曲现象显著,冲裁件质量下降。
并且拉裂产生的斜度增大,断面质量不理想,如图2-7c所示。
另外,当模具间隙不均匀时,在凸、凹模之间可能同时存在着间隙合适、间隙过小和间隙过大几种情况,因此会出现在冲裁件断面上同时分布着上述各种情况的断面。
(a)(b)(c)
图2-7间隙大小对冲裁件断面质量的影响
冲裁间隙对冲裁件尺寸精度有很大影响。
图2-8a、b分别表示冲孔模和落料模的凸、凹模间隙Z对冲裁件尺寸精度(δ为冲裁件相对于模具的尺寸偏差)影响的一般规律。
(a)(b)
图2-8间隙对冲裁件尺寸精度的影响
3)模具刃口状态、结构及制造精度对冲裁件质量的影响
模具刃口状态对冲裁件的断面质量也有较大影响。
当模具刃口磨钝后,挤压作用增大,则冲裁件圆角和光亮带增大。
对于钝的刃口,即使间隙选择合理,在冲裁件上将产生较大的毛刺。
实践表明:
凹模磨钝时,冲孔件的孔口下端产生明显毛刺如图2-9a所示;
凸模磨钝时,在落料件上端产生明显毛刺,如图2-9b所示;
当凸、凹模刃口均磨钝时,则会在冲裁件上端和孔口下端都产生毛刺如图2-9c所示。
(a)(b)(c)
图2-9凸、凹模刃口磨钝后毛刺的形成
4)冲裁模的制造精度(主要是凸、凹模的制造精度)对冲裁件尺寸精度有直接的影响,冲裁模的制造精度越高,冲裁件的精度越高。
此外,采用压料板和顶板等结构形式的模具,合理选择搭边,注意润滑等也可提高冲裁件质量。
4.冲裁间隙
冲裁间隙是指冲裁模的凸、凹模刃口横向尺寸之差。
双面间隙用Z表示,单面间隙用Z/2表示。
其值可为正,也可为负。
如无特殊说明,冲裁间隙都是指双面间隙。
如图2-10所示,即
Z=D凹—d凸(2-2)
图2-10冲裁间隙
式中D凹凹模刃口尺寸;
d凸凸模刃口尺寸。
(1)冲裁间隙的影响
冲裁间隙对冲裁过程有着很大的影响。
在前述中已经分析了间隙对冲裁件质量起着决定性作用。
除此以外,间隙对冲压力和模具寿命也有着较大的影响。
1)间隙对冲压力的影响
间隙很小时,因材料的挤压和摩擦作用增强,冲裁力必然较大。
随着间隙的增大,材料所受的拉应力增大,容易断裂分离,因此冲裁力减小。
但试验表明,当单面间隙介于材料厚度的5%~20%范围内时,冲裁力降低不多,不超过5%~10%。
因此,在正常情况下,间隙对冲裁力的影响不很大。
间隙对卸料力、顶件力、推件力的影响比较显著。
由于间隙的增大,使冲裁件的光亮带变窄,材料弹性回复使落料件尺寸小于凹模尺寸,冲孔件尺寸大于凸模尺寸,因而使卸料力、推件力或顶件力随之减小。
一般当单面间隙增大到材料厚度的15%~25%左右时,卸料力几乎降为零。
2)间隙对模具寿命的影响
模具寿命通常是用模具失效前所冲得的合格冲裁件数量来表示。
冲裁模的失效形式一般有磨损、变形、崩刃和凹模胀裂。
间隙大小主要对模具的磨损及凹模的胀裂产生较大影响。
在冲裁过程中,由于材料的弯曲变形,材料对模具的反作用力主要集中在凸、凹模刃口部分。
如果间隙小,垂直冲裁力和侧向挤压力将增大,摩擦力也增大,且间隙小时,光亮带变宽,摩擦距离增长,摩擦发热严重,所以小间隙将使凸、凹模刃口磨损加剧,甚至使模具与材料之间产生动结现象,严重的还会产生崩刃。
另外,小间隙因落料件堵塞在凹模洞口的胀力也大,容易产生凹模胀裂。
小间隙还易产生小凸模折断,凸、凹模相互啃刃等异常现象。
凸、凹模磨损后,其刃口处形成圆角,冲裁件上就会出现不正常的毛刺,且因刃口尺寸发生变化,冲裁件的尺寸精度也降低,模具寿命减小。
因此,为了减少模具的磨损,延长模具使用寿命,在保证冲裁件质量的前提下,应适当选用较大