完整反应器初步设计说明书docxWord下载.docx
《完整反应器初步设计说明书docxWord下载.docx》由会员分享,可在线阅读,更多相关《完整反应器初步设计说明书docxWord下载.docx(52页珍藏版)》请在冰豆网上搜索。
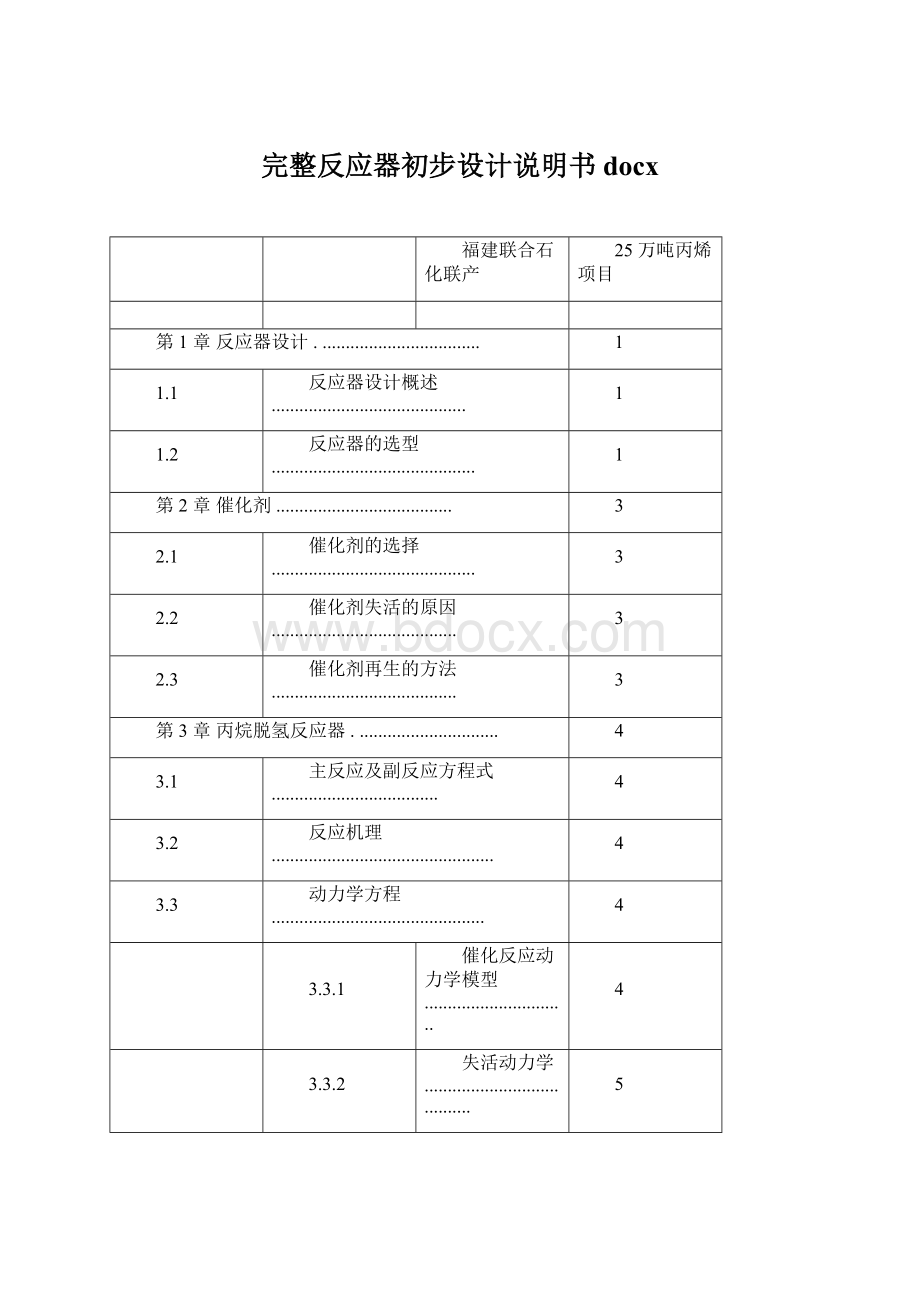
催化剂设计.............................................
11
3.5.1
催化剂用量......................................
3.5.2
催化剂来源......................................
3.5.3
催化剂的装填....................................
3.6
反应器内部结构设计.....................................
3.6.1
催化剂床层开孔..................................
3.6.2
催化剂分布器....................................
12
3.6.3
气体分布器......................................
2
3.7
反应器管口计算.........................................
3.7.1
进料管(以第一台反应器为例)......................
3.7.2
出料管..........................................
13
3.7.3
吹扫空气入口....................................
3.7.4
催化剂进料口....................................
3.7.5
催化剂出口......................................
3.7.6
排净口..........................................
3.7.7
人孔............................................
14
3.7.8
催化剂床层固定钢................................
3.8
加热炉
.................................................
3.9
机械强度的计算和校核...................................
3.9.1
反应器材料的选择................................
3.9.2
反应器筒体厚度的选择............................
3.9.3
反应器封头厚度的计算............................
15
3.9.4
液压试验校核....................................
16
3.9.5
反应器强度校核..................................
3.9.6
反应器封头的选择................................
25
3.10设计结果总结(以第一台反应器为例)......................
26
第4章乙炔选择性加氢反应器........................
4.1
概述...................................................
4.2
反应方程式.............................................
27
4.3
催化剂的选用...........................................
4.4
设计简述...............................................
4.5
在Polymath中的模拟与优化..............................
29
4.6
选择性加氢反应器总结...................................
30
第5章参考文献...................................
福建联合石化联产25万吨丙烯项目
第1章反应器设计
1.1反应器设计概述
化学反应器是将反应物通过化学反应转化为产物的装置,是化工生产流程中的中心环节。
由于化学反应种类繁多,机理各异,因此,为了适应不同反应的需
要,化学反应器的类型和结构也必然差异很大。
反应器的性能优良与否,不仅直接影响化学反应本身,而且影响原料的预处理和产物的分离,因而,反应器设计过程中需要考虑的工艺和工程因素应该是多方面的。
反应器的设计主要包括:
1)反应器选型;
2)确定合适的工艺条件;
3)确定实现这些工艺条件所需的技术措施;
4)确定反应器的结构尺寸;
5)确定必要的控制手段。
在反应器设计时,除了通常说的要符合“合理、先进、安全、经济”的原则,在落实到具体问题时,要考虑到下列的设计要点:
1)保证物料转化率和反应时间;
2)满足物料和反应的热传递要求;
3)设计适当的搅拌器和类似作用的机构;
4)注意材质选用和机械加工要求。
1.2反应器的选型
反应器按结构大致可以分为釜式、管式、固定床、流化床、移动床等类型。
它们的主要适用范围和特性见下表1-1:
表1-1反应器类型
反应器类型适用范围特性
结构简单、加工方便,传质、传热效率
高,温度浓度分布均匀,操作灵活性大,便于
液液,气
控制和改变反应条件,适合于多品种、小批
釜式反应器液,液固,气液
量生产,但返混程度大,间歇操作时辅助
固
时间所占比例大。
返混小,所需反应器体积较小,比传
管式反应器气相,液相热面大;
但对慢速反应,管很长,压降很
大
返混小,高转化率时催化剂用量少,
固定床反应器气固相催催化剂不易磨损;
但传热控温不易,催化
化反应剂装卸麻烦
气固相,尤传热好,温度均匀,易控制,催化剂
流化床反应器其是催化剂失有效系数大;
但床内返混大,不适于高转
活很快的反应化率反应
气固相,尤床层返混小,固气比可操作性大;
但
移动床反应器其是催化剂失床内温差大,调节不易
活很快的反应
本反应器主要针对的是丙烷脱氢生成丙烯的反应,该反应的高效反应温度在
550-650℃,反应压力为0.1MPa。
反应两个最大的特点是:
(1)反应为强吸热,分子数增加的可逆反应,平衡常数随温度的升高而增
加。
若要获得较高的脱氢转化率,则该反应需在高温和负压下进行,然而,高温
又会使烷烃容易发生裂解和深度脱氢反应,导致反应的选择性降低。
(2)催化剂容易结焦失活:
高温对C—C键断裂的裂解反应比对C—H键断
裂的脱氢反应更为有利,从而容易导致催化剂表面积碳,进而使催化剂失活加速。
而连续工业化不允许频繁停车来更换催化剂,否则会导致产品质量的不稳定以及额外的能量与原料消耗。
本项目包括4台脱氢反应器和1台选择性加氢反应器。
综合反应以及催化剂特点,我们分别选择移动床反应器和固定床反应器。
第2章催化剂
2.1催化剂的选择
本反应综合生产实际以及环境友好的要求,丙烷脱氢(PDH)反应器选用Sn
为助剂、Pt为活性中心,Al2O3为载体的Pt-Sn/Al2O3催化剂。
催化剂为颗粒直径2mm的球形颗粒,密度为3800kg/m3,床层孔隙率ε取0.4。
乙炔选择性加氢(SHP)
反应器选用最常用的钯系催化剂。
2.2催化剂失活的原因
丙烷脱氢反应在热力学上是一个分子数增加、强吸热(116KJ/mol)的可逆
反应。
为了使反应向脱氢反向进行,需要提高反应温度和降低反应器中的压力。
但是在高温下,丙烯容易发生深度脱氢,导致选择性降低,而且在高温下C-C
键裂解反应在热力学上比C-H键裂解更有利,从而加剧了碳在催化剂表面沉积导
致Pt-Sn/Al2O3催化剂失活。
2.3催化剂再生的方法
TM
利用CCR再生装置,对结焦的Pt-Sn/Al2O3催化剂进行烧炭再生。
其有4项主要功能:
烧去催化剂的焦炭,铂催化剂的重新分配,移去额外的水分及将催化剂返回到还原状态(催化剂再生)。
缓慢移动的催化剂床在通过反应器和再生器的环路中循环,常用的循环时间为5~10天。
反应部分和再生部分相互独立设计,因此即使再生器停车,也不用中断反应器内催化脱氢反应过程。
第3章丙烷脱氢反应器
3.1主反应及副反应方程式
主反应:
C3
8
36
△
Hr=116.0754KJ/mol
H
→CH
+H
副反应:
24
△r
+CH
H=75.8671KJ/mol
CH
△Hr
=-136.98KJ/mol
C3H8+H2
→C2H2+C+4H2
△Hr=330.595KJ/mol
3.2反应机理
图3-1丙烷脱氢反应机理
3.3动力学方程
3.3.1催化反应动力学模型
-r1=k1*(P(C3H8)-P(C3H8)*P(H2)/Keq)/(1+P(C3H6)/K1);
-r2=k2*P(C3H8);
-r3=k3*P(C2H4)*P(H2);
单位:
mol/(min*g).
其中:
Keq=exp(16.858-15394/t+148728/t2)atm
R=8.314J/(mol*K);
P(C3H8)是C3H8在反应器中的分压;
P(C2H4)是C2H4在反应器中的分压;
P(H2)是H2在反应器中的分压;
t为反应器中的温度.
3.3.2失活动力学
dC
k1c*(Cmax
Cm)2
k2c
dt
C=Cm+CM
Cm
Cmax2*[
k1c*t
]
Cmax*k1c*t
CM=k2c*t
kic
k0ic*exp(
Eaic*(1
1))
R
t
tm
a
(1a1*Cm)
a2*Cm*exp[a3*CM]
a1
a01*exp(
Eaa1(1
动力学方程中各参数如下图3-2:
图3-2动力学参数
3.4反应器设计思路说明
3.4.1反应条件
反应温度:
866K
反应压力:
1atm
稀释剂的选择:
为了提高转化率,可以在反应气中添加稀释剂。
水蒸汽是最早作为稀释气体引入丙烷脱氢过程的,它能有效促进丙烷脱氢反应,提高反应转化率,而且水蒸汽还是一种很好的载热剂,但是水蒸气会对催化剂结构产生影响,
给产物分离造成困扰,并且催化剂价格昂贵,因此我们选择廉价的H2作为稀释剂,并且H2作为反应产物,也可以做到循环利用,提高原子利用率。
本设计选用的氢烃比为1:
1。
反应器:
径向绝热式移动床反应器,四台串联
催化剂:
球形,规格dp=2mm,空隙率0.4
反应进口流量:
G=64869.711mol/min
3.4.2反应器类型的选择
由于该反应体系的原料是以混合气体进料,且进料量比较大,考虑到环保因
素以及所采用的催化剂易失活问题,如若采用流化床反应器,则床层返混比较大,
不适于做高转化率反应,而该反应要求丙烷最终转化率为88%,因此我们考虑选
用床层返混较小且利于催化剂再生的移动床反应器。
绝热式反应器相较于列管反
应器具有造价低,反应器空间利用率高,操作简单的优点,故考虑选用。
3.4.3反应器数学模拟
本次反应器设计利用设计软件POLYMATH进行优化和模拟。
首先根据经验值
确定反应器床层高度,然后利用软件语言写出反应程序,进而运行得到反应器物
料的摩尔分率和温度沿反应器径向的变化情况及个点的反应状态。
最后通过改变
工艺参数,如管长、管径、进口温度等,对反应器结果进行优化,得到最优转化
率和产量。
3.4.4反应器体积的计算
(一)基本衡算方程
研究对象选丙烯,甲烷,乙烷,体系选反应器的一个小微元,(考虑结焦对
反应的影响)对这个微元体系做物料衡算,如下:
dm1
3.14
r
l
((1
m
mr
(2
3)/
Nt
dr
3800000
1)
dm2
(-
(1
2)
dm3
3.14r
l(-m3
r1
m3r2
m3)
r3)/Nt
对这个微元体系做热量衡算,如下:
3.14*(Hr1
Hr2
r2
Hr3
r3)
Cp
其中a
是结焦浓度和催化剂活性的关联系数,
Nt是不同床层位置的进料流
量,Cp为进料物流的平均热容,Hr1,Hr2,Hr3分别是主副反应的反应热,r1,r2,r3分别是主副反应的反应本征动力学。
(二)Polymath模拟过程
有了基本的化学反应动力学,用平推流(PFR)通过polymath来模拟,进口
总的物料流量是Aspen模拟整个流程达到稳态时的数据。
得到模拟程序如下:
图3-3Polymath模拟程序
得到以下反应器中产物丙烯的摩尔分率沿径向的变化(以第一台反应器为例):
图3-4丙烯摩尔分率沿径向的变化
反应器温度沿径向的变化如下:
图3-5反应器温度沿径向的变化
从表格中查得转化率最大时对应的催化剂厚度为△D1=26cm。
同理可得其他反应器催化剂床层厚度如下:
△D2=22cm,△D3=22cm,△D4=27cm。
床层空隙率ε=0.4,所以可得各反应器床层厚度分别为40cm,34cm,34cm,42cm。
9
(三)反应器结构参数
表3-1反应器的结构参数
反应器
气体出口
反应器内
催化剂床层
催化剂床层长
材料
位号
内径/mm
径/mm
厚度/mm
度/m
R201
1200
2400
400
0Cr18Ni9
R202
340
R203
R204
420
(四)反应器塔压降校核
pfm
fu2
(
)H
dp
150
1.75
fm
Re
dpuρ1
μ1-ε
f——流体黏度,kg/(m.s)
f——流体密度,kg/m3
ε——空隙率
dp——催化剂直径
H——反应器高度工艺数据如下:
f
110-6
kg
/(
.)
ms
dp=0.002m
f0.317kg/m3
0.4
H=6m
10
u1.49m/s
由计算公式得到反应器床层压降为△P=5843.93Pa<
10%P=15198.75Pa,可见
床层压降很小,可以看做恒压反应,这是符合设计要求的。
3.5催化剂设计
3.5.1催化剂用量
选用密度为3800kg/m3的Pt-Sn/Al2O3催化剂,各催化剂床层的体积分别是:
3333
V1=7.16m,V2=5.89m,V3=5.89m,V4=7.48m。
对应一次催化剂的装填量为m=m1+m2+m3+m4=∑ρV=100.4吨
3.5.2催化剂来源
由于催化剂的制备比较繁琐,我们采取从UOP公司购买。
3.5.3催化剂的装填
对反应器进行喷砂处理,以清除反应管壁上的铁锈。
将催化剂从反应器顶部入口注入,然后利用自重辅以压缩空气作用使催化剂填入床层。
测量床层压降,使其符合正常压降的25%即可。
3.6反应器内部结构设计
3.6.1催化剂床层开孔
为了使反应气体进入催化剂床层与其充分接触反应,我们需要在催化剂床层
器壁上开孔。
床层的开孔率是开孔面积与总的有效传质面积的比值,其大小开孔
方式的影响。
所开孔直径要小于催化剂颗粒直径,以保证催化剂不泄漏,我们选
择催化剂床层两侧对称交叉开孔,开孔率的计算公式如下:
开孔区的面积
φ
总面积
因为丙烷脱氢是一个分子数增加的反应,所以在催化剂床层两侧开孔大小是
不一样的,所设计反应布气器的开孔率为4%,集气开孔率为6%。
催化剂床层外
侧的总面积为S=2x3.14X1.04x6=39.207m2,所以布气开孔区的面积为
S1=Sxφ1=1.568m2,开孔直径为1.5mm,由此可算得开孔个数为
开孔区面积
1.568
个
n
887756.54
孔面积
0.7850.00150.0015
,圆整后的开孔个数为
887757个。
同理可得催化剂床层内侧的总面积为S=2x3.14X0.6x6=22.608m2,集气开孔区面
积为S2=Sxφ2=1.356m2,开孔直径为1.5mm,由此可算得开孔个数为
1.356
767728.24