断裂韧性KIC测试试验Word格式文档下载.docx
《断裂韧性KIC测试试验Word格式文档下载.docx》由会员分享,可在线阅读,更多相关《断裂韧性KIC测试试验Word格式文档下载.docx(13页珍藏版)》请在冰豆网上搜索。
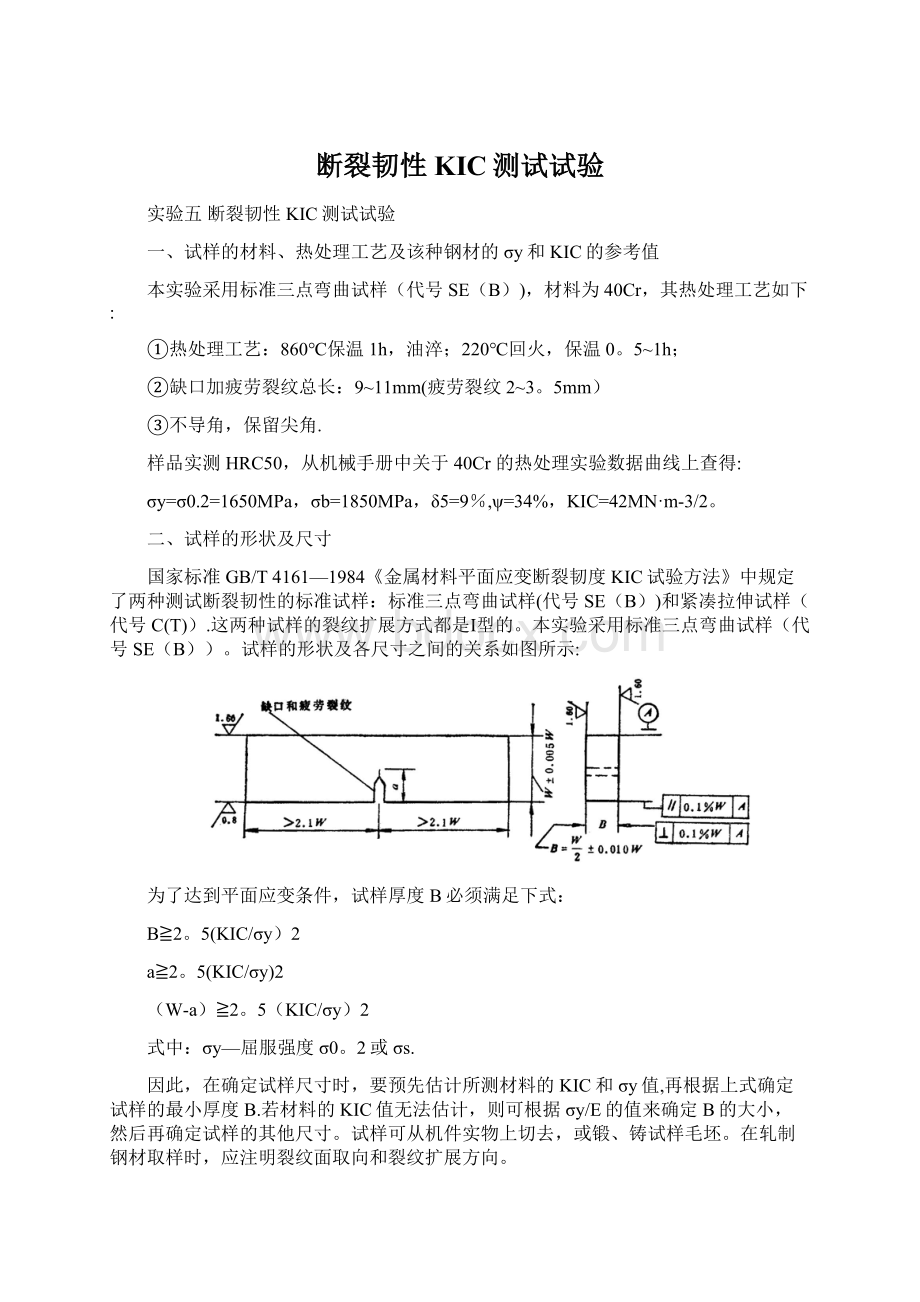
2或σs.
因此,在确定试样尺寸时,要预先估计所测材料的KⅠC和σy值,再根据上式确定试样的最小厚度B.若材料的KⅠC值无法估计,则可根据σy/E的值来确定B的大小,然后再确定试样的其他尺寸。
试样可从机件实物上切去,或锻、铸试样毛坯。
在轧制钢材取样时,应注明裂纹面取向和裂纹扩展方向。
试样毛坯粗加工后,进行热处理和磨削,随后开缺口和预制裂纹。
试样上的缺口一般在钼丝电切割机床上进行切割。
为了使引发的裂纹平直,缺口应尽可能地尖锐。
开好缺口的试样,在高频疲劳试验机上预制裂纹。
疲劳裂纹长度应不小于2.5%W,且不小于1。
5mm.a/W值应控制在0。
45~0.55范围内。
本试样采用标准三点弯曲试样(代号SE(B)),其尺寸:
宽W=19。
92mm,厚B=10.20mm总长100。
03mm。
三、实验装置
制备好的试样,在MTS810材料力学试验机上进行断裂试验。
对于三点弯曲试样,其试验装置如图5-2所示。
可将采集的试验数据以文件形式(数据采集间隔0.1s)存储在计算机中,同时利用3086—11型X—Y系列实验记录仪绘制P—V曲线。
本实验跨距S为80mm,弯曲压头速率0。
01mm/s。
用15J型工具显微镜测量试样的临界裂纹(半)长度a.
图5—2三点弯曲试验装置示意图
1—试验机上横梁;
2-支座;
3—试样;
4-载荷传感器;
5-夹式引伸计;
6—动态应变仪;
7—X—Y函数记录仪。
如图5—2所示,在试验机的横梁1上,换上专用支座2,用辊子支承试样3,两者保持滚动接触。
两支承辊的两端头用软弹簧或橡皮筋拉紧,使之紧靠在支座凹槽的边缘上,以保证两辊的距离等于试样的跨距S。
载荷传感器4为一钢制圆筒弹性元件,壁上贴有电阻应变片,全桥连接。
受载时,圆筒变形,由应变片输出载荷讯号P。
夹式引伸计5的构造及其在试样上的安装方法见图5-3。
引伸计为两弹簧片悬臂梁,中间用垫块隔开,螺钉连紧。
弹簧片上贴有电阻应变片(T1、T2及C1、C2)。
试验前先在试样上缺口两侧用“502”胶水对称贴上刀口(本实验引伸计两臂末端初始间距为12mm,刀口初始间距应略大于12mm),引伸计的两臂末端就卡在刀口上.试验过程中,裂纹嘴受载荷张开,刀口距离增大,弹簧片松弛,由应变片将裂纹嘴两侧刀口张开量V变成电讯号传送出去。
图5—3夹式引伸计构造及安装
1-试样2-刀口3-引伸计
载荷讯号P及裂纹嘴两侧刀口张开位移讯号V,均需输入试验机控制器中,所采集的试验数据以文件形式(数据采集间隔0。
1s)存储在计算机中,同时模拟信号传送到3086-11型X—Y系列实验记录仪7中,可在坐标纸上实时自动绘出P-V曲线。
四、实验步骤
1.参观试样切割缺口及预制疲劳裂纹的设备及过程.
2。
测量试样尺寸:
在疲劳裂纹前缘韧带部分测量试样厚度B,在切口附近测量试样宽度W,测量3次取平均值。
测量精度要求0.02mm或0.1%B(或W)。
3。
安装三点弯曲试验底座,使加载线通过跨距S的中点,偏差在1%S以内。
放置试样时应使缺口中心线正好落在跨距的中点,偏差也不得超过1%S,而且试样与支承辊的轴线应成直角,偏差在±
2°
以内。
4。
将载荷传感器和位移传感器的接线,分别按“全桥法”接入动态应变仪,并进行平衡调节。
用动态输出档,将载荷和位移输出讯号分别接到函数记录仪的“Y"
和“X”接线柱上。
调整好函数记录仪的放大比,使记录曲线的初始斜率在0。
7~1。
5之间,最好为1,并使画出的图形大小适中。
5.开动试验机,对试样缓慢而均匀地加载(本实验弯曲压头速率0。
01mm/s),选择加载速度应使应力场强度因子的增加速率在0.55~2。
75MN·
m-3/2/s范围内.当采用S/W=4,a/W=0.5的三点弯曲试样时,对钢件也可按0.04B~0.2Bmm/分钟的横梁移动速度进行加载。
对于某些老式试验机系统,加载时必须在P—V曲线上记录任一初载荷(由试验机测力度盘读出)和断裂载荷的数值,以便于对P-V曲线上的载荷进行标定,本实验所用测试系统不需要进行此过程。
6.加载结束后,压断试样,从3086-11型X-Y系列实验记录仪上取下记录的P—V曲线。
7。
由于裂纹前沿不平直,取断裂后的试样在断面上划线,如图所示,规定测量
、
和
三处的裂纹长度a2、a3、a4及a1和a5,然后取其平均值
=1/3(a2+a3+a4)得临界裂纹(半)长度a。
五、实验数据及处理
(1)计算机数据
1、确定条件裂纹失稳扩展载荷PQ
图1—1P-VLinearFitofSlopedata
截取图1—2P—V曲线上截取直线段部分,用LinearFit进行直线拟合,求出直线斜率Slope=77。
27653
图1—2P-V曲线
在图1-2P—V曲线上从原点O作一相对于直线OA部分斜率减少5%的割线来确定裂纹扩展2%时相对应的载荷P5,P5是割线与P—V曲线的交点纵坐标值:
即取x=0。
2mm,y=0.2×
77.27653×
0。
95=14.6825KN,过(0,0)和(0.2,14.6825)做直线与P-V曲线相交,用“屏幕上取点"
读出其纵坐标值P5为6。
09188,由于在P5以前没有比P5大的高峰载荷,则PQ=P5=6。
09188KN。
2、测定临界裂纹(半)长度a
将压断的试样在15J型工具显微镜上或其它精密测量工具下测定临界裂纹(半)长度a,测量精度0。
01mm。
由于裂纹前沿不平直,规定测量
三处的裂纹长度a2、a3、a4,然后取其平均值
=1/3(a2+a3+a4).
由测量得:
11号试样宽W=19.92mm,厚B=10。
02mm,总长100。
03mm,
a1=9。
21mm,a2=9.48mm,a3=9。
37mm,a4=9。
37mm,a5=9.02mm。
所以,
=1/3(a2+a3+a4)=1/3(9.48+9.37+9。
37)=9。
41mm。
a2,a3和a4中的最大值与最小值之差=a2—a3=9。
48mm-9。
37mm=0.11mm,
而2.5%W=0。
025×
19.92=0.498mm,
所以a2,a3和a4中的最大值与最小值之差不超过2.5%W
且同时任一a值均大于2.5%W,同时不小于1。
5mm。
此外,表面临界裂纹(半)长度a1和a5均大于
的90%,即8.469mm,
所以,试验有效.
3、计算条件断裂韧性KQ
将PQ和a值代入KⅠ表达式计算KQ。
对于标准三点弯曲试样按下式计算:
PQ=6.09188KN,S=80mm,B=10。
02mm,W=19。
92mm,a/W=9.41/19.92=0.472
由表5—2可以查得YⅠ(
)=2.44
4、判定KQ的有效性
Pmax=9.326KN,PQ=6。
09188KN,Pmax/PQ=9.326/6。
09188=1。
531>
1.1
5(KQ/σy)2=2。
5×
(41.466/1650)2=1.579mm,所以B>
2.5(KQ/σy)2
KQ不满足条件①,但满足条件②,所以KQ≠KⅠc,KQ无效.
(2)坐标纸数据:
由3086-11型系列实验记录仪上取下记录的P-V曲线,用取点法将坐标纸上的数据抄录在Origin的数据表格上,然后乘以各自系数作出P~V曲线。
图1-3P—VLinearFitofSlopedata
截取P-V曲线上截取直线段部分OA,用LinearFit进行直线拟合,求出直线斜率Slope=85.34483
图1-4P—V曲线
在图1-4P—V曲线上从原点O作一相对于直线OA部分斜率减少5%的割线来确定裂纹扩展2%时相对应的载荷P5,P5是割线与P-V曲线的交点纵坐标值:
即取x=0.1mm,y=0。
1×
85。
34483×
0.95=8.1078KN,所以在坐标纸上取点为(0。
1,8.1078),过(0,0)和(0.1,8.1078)做割线与P-V曲线相交,读出其纵坐标值4.5,由于在P5以前没有比P5大的高峰载荷,则PQ=P5=4.5KN。
在计算机数据处理过程中已经得到
=1/3(a2+a3+a4)=1/3(9.48+9。
37+9.37)=9。
41mm,且试验有效。
5、计算条件断裂韧性KQ
对于标准三点弯曲试样按下式计算:
PQ=4。
5KN,S=80mm,B=10。
02mm,W=19.92mm,a/W=9.41/19.92=0.472
由《材料性能》书中表5—2可以查得YⅠ(
6、判定KQ的有效性
Pmax=9.3359KN,PQ=4.5KN,Pmax/PQ=9。
3359/4.5=2。
07>
1。
1
2.5(KQ/σy)2=2.5×
(29.80/1650)2=0。
8154mm,所以B〉2。
5(KQ/σy)2
KQ不满足条件①,但满足条件②,所以KQ≠KⅠc,KQ无效。
图1—5P~V曲线图
六、思考题
1、本实验的重点是什么?
答:
本实验的重点是了解金属材料平面应变断裂韧性KⅠc测试的基本原理、实验装置及试样的形状和尺寸,着重掌握KⅠc的测试过程,根据绘出的P—V曲线确定裂纹失稳扩展载荷PQ;
测定临界裂纹(半)长度a;
计算条件断裂韧性KQ并判断KQ的有效性。
2、为什么载荷传感器和应变引伸计需要经常校验?
答:
因为载荷传感器为一钢制圆筒弹性元件,壁上贴有电阻应变片,全桥连接。
受载时,圆筒变形,由应变片输出载荷讯号P。
夹式引伸计为两弹簧片悬臂梁,中间用垫块隔开,螺钉连紧。
引伸计的两臂末端就卡在刀口上。
试验过程中,裂纹嘴受载荷张开,刀口距离增大,弹簧片松弛,由应变片将裂纹嘴两侧刀口张开量V变成电讯号传送出去,载荷讯号P及裂纹嘴两侧刀口张开位移讯号V,均需输入试验机控制器中,因此载荷传感器和应变引伸计所测得信号的准确性直接影响到试验的数据处理、测量结果和试验结论,并且应变片在使用一段时间时会产生微量变形而影响试验结果;
载荷传感器和应变引伸计属于较高精度的仪器,灵敏度较高,对湿度、温度、压力等外界环境比较敏感;
另外,传感器有重复性、滞后性和蠕变等特点,所以需要经常校验。
3、为何所测定的裂纹长度a被称为裂纹“半”长度?
试验中所测定的裂纹半长度a为原始线切割长度+疲劳裂纹长度。
材料中最危险的缺陷,其作用在于导致材料内部的局部应力集中,是断裂的动力因素。
对于理论强度,其微裂纹半长度可以理解为是原子间距。
在实验中所测得的裂纹长度a=0。
5W,通常为其试样宽度W的一半,所以测定的裂纹长度a被称为裂纹“半”长度。
七、感想与体会
在断裂韧性kⅠc测试试验中,通过观看同组同学安装三点弯曲试验底座及自己亲手安装坐标纸于3086—11型X—Y系列实验记录仪上,我熟悉了MTS810材料力学试验机的操作、试验机各部分配合的关系及断裂韧性KⅠc的测试方法,这锻炼了我在材料性能实验中的实际操作能力,在此同时也体会到了同组同学相互配合、团队意识的重要性.在试验后期,我看到了其宏观断面的形貌.在测量裂纹长度a时,我又了解到一个测量长度的精密测量工具即15J工具显微镜。
在数据处理过程中,通过确定裂纹失稳扩展载荷PQ、测定临界裂纹长度a、计算条件断裂韧性Kq及判断其有效性,我对Origin5.0有了进一步的了解,并学会了如何利用数据及P~V曲线图来计算Kq,并判定Kq是否等于KⅠc。
通过这次实验,我进一步加深了断裂韧性的定义及KⅠ和KⅠc的异同等相关理论知识.
实验六金属磨损试验
一、实验目的
掌握金属材料在滚动摩擦、滑动摩擦和滚动—滑动复合摩擦条件下磨损量及摩擦系数的测定方法。
(本实验参照国家标准GB/T12444.1-1990《金属磨损试验方法MM型磨损试验》和GB/T12444。
2—1990《金属磨损试验方法环块型磨损试验》)
二、实验内容
在一定试验力及转速下对规定形状和尺寸的试样进行干摩擦或在液体介质中润滑摩擦,经规定转数或时间后,测定其磨损量及摩擦系数,观察磨损表面形貌,并加以比较。
三、实验要求
试样的制备不应改变原始材料的组织及力学性能.不应带有磁性,经磨床精磨后,要求退磁。
试样的形状及尺寸如图(6—1、6-2)所示。
四、实验装置及试样
MM200型磨损试验机及MRH-3型高速环块磨损试验机。
200℃烘干箱一个;
TG—328A型光电分析天平1台;
干燥器1个,低倍显微镜、放大镜等.
试样材料:
碳钢或合金钢。
五、实验步骤
本试验应在10~35℃室温范围内进行,对温度有较高要求的试验,应控制在23±
5℃之内。
一般应在无振动、无腐蚀性气体和无粉尘的环境中进行。
摩擦状态与实际工作状态相接近。
滚动、滑动及其复合摩擦磨损试验的上、下试样均采用圆环形试样。
滑动摩擦磨损试验的上试样可为蝶形试样,下试样为圆环形试样.安装上、下试样时,应使试样转动方向与加工方向一致。
两试样之间应均匀接触,试验前应对试样进行磨合。
建议采用粘度较低的润滑剂。
试样在润滑介质中试验时,如果磨损量较小,应在试样不过热的条件下施加较大的试验力。
试验前后均应使用适当的清洗液清洗试样,并应保证前后两次操作方法相同.应对清洗后的试样进行烘干,烘干温度一般为60℃,保温2小时左右。
在烘箱内冷却至室温后,放入干燥器中,2小时后立即进行称量。
六、实验数据及处理
一般取三对试样试验结果的平均值作为一个试验数据。
用TG—328A型光电分析天平(最小刻度0。
1mg)称量试验前后试样的质量,由公式
(1)求得质量磨损值.
m=m0-m1
(1)
m——质量磨损,mg;
m0-—磨前质量,mg;
m1-—磨后质量,mg。
(a)圆环形试样
(b)蝶形试样
图6—1MM200型磨损验机磨损试样
(a)环形试样
(b)块形试样
图6—2MRH—3型高速环块磨损试验机磨损试样
七、思考题
1、简述试验过程.
请见试验步骤。
2、影响磨损试验数据精确度的因素有哪些,如何解决?
质量磨损值取决于磨前质量和磨后质量,首先它们都需要称量,所以称量天平的精确度会影响实验数据,因此要选用精确度较高的天平,其次试验前后均要使用适当的清洗液清洗试样,所以清洗的方法会影响试样数据精确度,所以应保证前后两次操作方法相同.由于清洗后试样附着水分,同样影响磨损试样数据精确度,所以应对清洗后的试样进行充分地烘干,烘干温度一般为60℃,保温2小时左右。
在烘箱内冷却至室温后,放入干燥器中,2小时后立即进行称量。
另外,在试验过程中,如果使用高粘度润滑剂,则可能会使磨损碎屑黏在试样表面,在进行试验时,在摩擦状态下,磨损碎屑有可能镶嵌在试样表面,不易清洗掉,影响磨后质量,造成实验数据的精确度降低,所以要使用粘度低的润滑剂。
八、感想与体会
金属磨损试验,我们并没有进行实际操作,但是通过老师的讲解及相关操作,我们对MM200型磨损试验机及MRH-3型高速环块磨损试验机的运转状况及操作步骤有了一定的了解,并观察到了实际试样的外观及在试验机中的测试位置,我学习到了金属材料在滚动摩擦、滑动摩擦和滚动-滑动复合摩擦条件下磨损量及摩擦系数的测定方法。
通过这个试验,我充分体会到了设备的发展给试验数据采集带来的巨大便利,尤其是先进设备的数字化及自动化过程中减少了不必要的麻烦,既提高了试验的效率也提高了数据的准确性。