危险固体废弃物管理制度Word下载.docx
《危险固体废弃物管理制度Word下载.docx》由会员分享,可在线阅读,更多相关《危险固体废弃物管理制度Word下载.docx(15页珍藏版)》请在冰豆网上搜索。
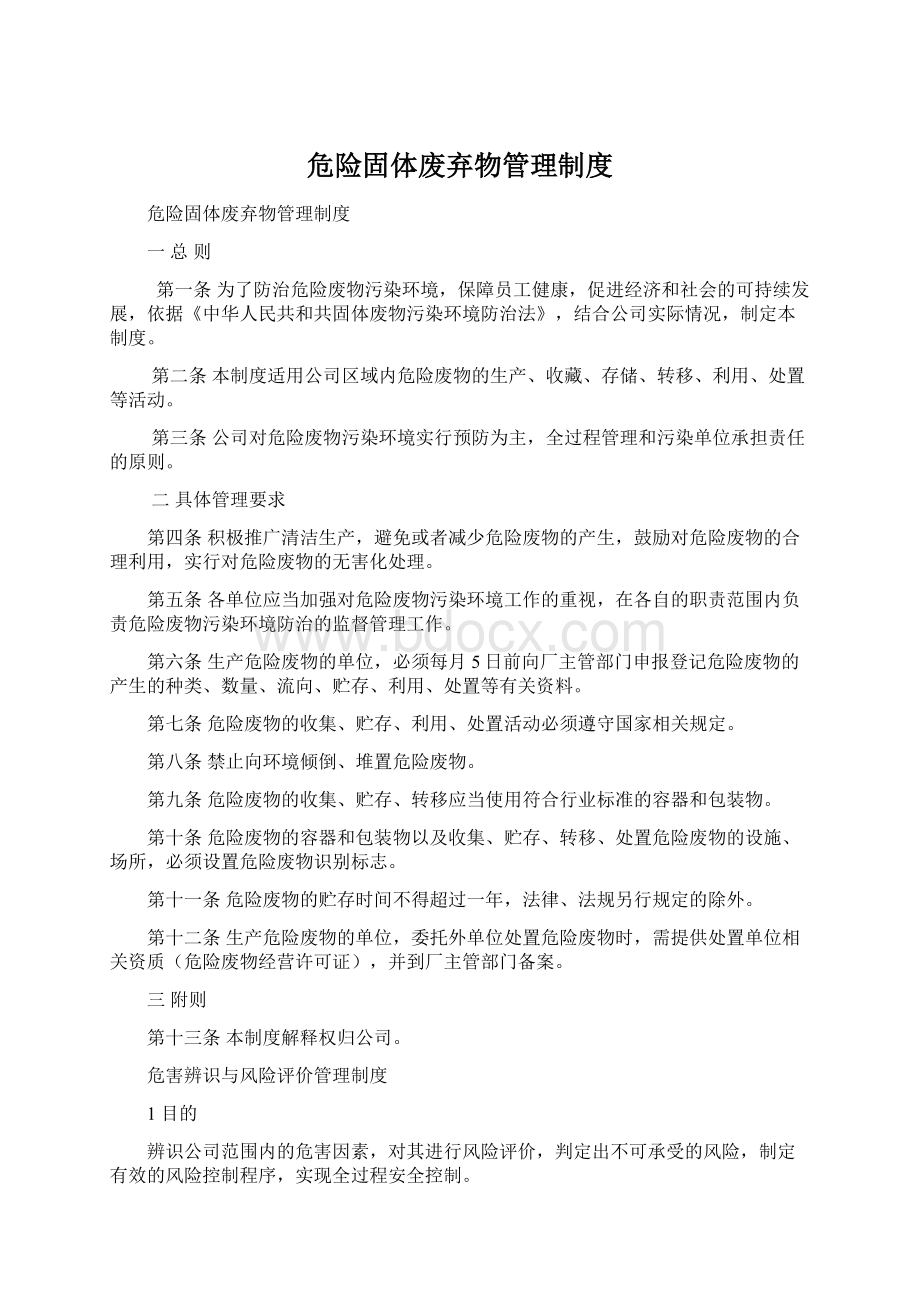
4.2.1负责危害辨识、风险评价及重大风险因素控制计划的制定。
4.2.2对不可承受风险控制计划的落实情况进行监督管理。
4.2.3负责环境污染危害辨识与风险评价。
4.2.4负责环境污染不可承受风险的治理和控制计划。
4.3生产技术部
4.3.1负责组织生产工艺、工程项目的危害辨识与风险评价。
4.3.2负责生产工艺、工程项目方面的不可承受风险治理项目的立项管理。
4.3.3按照“三同时”的要求,保证防止工伤事故和职业病的职业安全健康设施与主体工程同时设计﹑同时施工﹑同时投入生产和使用。
4.3.4负责组织电气、机械设备设施的危害辨识与风险评价。
4.3.5负责电气、机械设备设施不可承受风险治理项目的立项管理。
4.4财务部
负责不可承受风险治理所需费用的支付,确保专款专用。
4.5车间
4.7.1负责本单位作业范围内的危险辨识与风险评价。
4.7.2负责作业范围内的不可承受风险治理项目的立项管理。
4.7.3实施本单位评价出的风险因素的控制计划。
5工作程序
5.1危害辨识与风险评价组织机构
5.1.1公司危害辨识与风险评价领导小组
组长:
主管安全副总经理
副组长:
安全环保部部长
成员:
各部室负责人各车间厂长
5.1.2危害辨识与风险评价专业小组
危害辨识与风险评价专业小组分安全专业小组;
生产技术专业小组、机动能源专业小组:
a)安全专业危害辨识与风险评价小组组长由安全环保部部长兼任,副组长由安全环保部主管人员兼任;
b)生产工艺、工程项目专业危害辨识与风险评价小组组长由生产技术部部长兼任,副组长由生产技术部副部长兼任;
c)电气、机械设备设施专业危害辨识与风险评价小组组长由生产技术部部长兼任,副组长由生产技术部主管电气、机械设备人员兼任;
d)专业小组成员:
安全技术管理人员、生产技术管理人员、电气、机械设备技术管理人员、环境保护技术管理人员。
5.1.3车间危害辨识与风险评价专业小组
车间厂长
车间主管安全副厂长
安全员、设备技术员、生产技术员及班组长。
5.1.4危害辨识与风险评价人员要求:
a)具有安全管理经验或具有相关专业职称的人员;
b)具有丰富的现场施工经验和分析、表达能力;
c)主要人员应接受过专业培训。
5.2划分作业活动
5.2.1一般情况下,可按如下方法划分作业活动:
a)按生产(工作)流程的阶段划分;
b)按地理区域划分;
c)按生产设备划分;
d)按作业任务划分;
e)上述几种方法的结合。
5.2.2收集相关信息,作业活动信息包括:
a)任务:
实施的地点,持续时间,人员,实施频率等;
b)设备:
可能用到的机械、设备、工具及其使用说明;
c)物资:
用到或遇到的物质及其物理形态(烟气、蒸汽、液体、粉末、固体)和化学性质等有关资料;
d)现场控制方法:
操作规程、安全规程、作业程序和作业指导书,员工的能力及已接受的相关培训,现场安全控制设施;
e)手工操作:
可能要手工搬运的物料的尺寸、形状、重量、表面特征,要用手移动物料的距离和高度;
f)数据:
作业活动及作业环境监测数据;
g)事故:
与该工作活动有关的事故经历;
h)现场工作环境(条件):
空间、高度、温度、湿度、安全防护设施等情况。
5.3危害因素识别
5.3.1危害分级依据:
a)法律、法规(《职业性接触毒物危害程度分级》(GB5044—85)和《有毒作业分级》(GB12331—90)等);
b)危害和事故伤亡的程度、规模;
c)事故发生的频率;
d)相关方关注程度;
e)财产损失额度;
f)降低风险的难度。
5.3.2危害因素分类
按导致事故发生的直接原因划分危害类型。
分为人的不安全行为、物的不安全状态、环境缺陷以及管理缺陷等四个方面。
5.3.2.1人的不安全行为:
a)操作错误、忽视安全、忽视警告;
b)造成安全装置失效;
c)使用不安全设备;
d)手代替工具工作;
e)物品(指成品、半成品、材料、工具、切屑和生产用品等)存放不当;
f)冒险进入危险场所;
g)攀坐不安全位置(如平台护栏、汽车挡板、吊车吊钩);
h)在起吊物下作业、停留;
i)机器运转时加油、修理、检查、调整、焊接、清扫等工作;
j)有分散注意力行为;
k)在必须使用个人防护用品、用具的作业或场合中,忽视其使用;
l)不安全装束;
m)对易燃、易爆等危险物品处理错误;
n)误动作;
o)其他不安全行为。
5.3.2.2物的不安全状态:
a)设备、设施、工具、附件有缺陷;
b)防护、保险、信号装置缺乏或有缺陷。
5.3.2.3环境的缺陷:
a)作业场所的缺陷;
b)作业环境不良。
5.3.2.4管理缺陷:
10.1制度缺乏;
10.2机构设置和人员配置有缺陷;
10.3安全培训教育和考核有缺陷;
10.4安全投入不足;
10.5监督与日常检查;
10.6应急救援有缺陷。
5.3.3事故分类
参照《公司职工伤亡事故分类》(GB6441-86),主要分为20类,包括物体打击、车辆伤害、机械伤害、起重伤害、触电、淹溺、灼烫、火灾、高处坠落、坍塌、冒顶片帮、透水、放炮、火药爆炸、瓦斯爆炸、锅炉爆炸、容器爆炸、其它爆炸、中毒和窒息、其它伤害。
5.3.4危害辨识的对象
5.3.4.1作业现场方面
a)作业现场方面主要包括作业的全过程、作业环境、劳保用品以及职业卫生方面,将以上方面融合于每一岗位或作业工种中,以“工种”为载体,贯穿作业的全过程;
b)主要体现于每一作业工种的人在工余、工前、作业前、作业中、作业后的每一步骤中可能受到的伤害。
5.3.4.2生产工艺流程方面:
a)设计方面:
安全预评价、三同时、设计文件和图纸;
b)生产工艺方面:
生产工艺适合生产条件;
考虑特殊灾害的影响;
设备、设施之间相互匹配,并满足工序要求;
各工序之间相互匹配,并满足生产要求;
生产作业顺序和方式适应生产现状;
生产作业范围在作业许可证划定的范围内。
c)生产保障系统:
运输线路、供配电、防排水、防灭火、维修等;
d)变化管理方面:
工艺改造、设备设施改造等的变化管理制度、变化的系统文件、人员的变化等。
5.3.4.3设备设施方面:
a)全过程控制:
规划、采购、安装(建设)、调试、验收、使用、维护和报废;
b)原始技术资料和图纸;
c)维修维护;
d)检测检验:
特种设备、安全标志产品、特殊设施。
5.3.5危害辨识的方法
根据公司的生产特点与管理形式,危害辨识主要采用以下方法:
a)询问与交流法;
b)专家分析法;
c)现场观察法;
d)查阅记录法;
e)工作任务分析法;
f)安全检查表法;
g)作业条件危险性评价法。
主要以访谈法为主,通过召开班组会的形式,由工作小组成员对员工进行询问,与员工进行交流,从而找出员工在作业过程中可能会受到的所有伤害类型及其原因。
5.3.6辨识与评价程序
危害辨识与风险评价应包括如下过程:
a)准备;
b)危害辨识;
c)危险源转化为风险的条件;
d)量化风险结果;
e)划分风险等级。
5.3.7辨识与评价应考虑下列因素:
5.3.7.1在中毒窒息风险评价时,应考虑可能的致因因素,包括:
有害气体积聚区域、通风不良、火灾影响。
5.3.7.2在水灾风险评价时,应考虑可能的不同的突水来源,包括:
地下水;
地表水;
降雨及融雪。
5.3.7.3在火灾风险评价时,应否考虑可能的不同的火灾类型,包括:
固体材料火灾、液体或液化固体火灾、气体或液化气泄漏火灾、粉尘燃爆火灾。
5.3.7.4在机械伤害风险评价时,应考虑可能的不同的致因因素,包括:
穿孔机械;
铲装机械;
运输机械;
排土机械;
破碎机械;
排水机械;
压风机械;
支护机械。
5.3.7.5在意外爆炸风险评价时,应考虑:
燃料油;
锅炉。
5.3.7.6机动设备与交通风险评价时,应考虑采购、维护、检查、自然环境、运输物料特性、路线、时间性等因素。
5.3.7.7在对关键设备进行风险评价时,应考虑其可靠性、安全性、经济性。
5.3.7.8对人机工效进行调查时,应包括:
重复运动、使用电动工具、作业姿势、座位舒适度、环境条件、易接近程度。
5.3.7.9在对心理性危害进行识别时是否考虑了下列因素:
工作因素、人为因素、个人生活环境因素。
5.3.7.10照明测量过程应考虑应急时的照明设备、照明时间、能见度、照明源布置情况。
5.3.7.11对识别的暴露于物理、化学、生物和人机工效,可能造成严重健康风险的危害,应完成定量监测的比例。
5.3.7.12应考虑职业危害的监测是否符合法律法规与其他要求及比例。
5.3.7.13应考虑职业危害监测设备定期校正的比例。
5.3.7.14应考虑风险概述的一致性、可审核性、持续性。
5.4风险评价方法
5.4.1LEC评价法:
LEC法是利用与系统风险率有关的3种指标值之积来评价系统人员伤亡风险大小,这3种因素是:
L——发生事故的可能性大小;
E——人体暴露在危险环境中的频繁程度;
C——一旦发生事故会造成的损失后果。
风险值D=后果L×
暴露E×
可能性C
5.4.2初始风险评价
5.4.3.1凡新工艺流程、新工程项目必须进行初始风险评价。
5.4.3.2初始风险评价过程应综合考虑:
a)生产工艺流程风险;
b)危险物质风险;
c)设备、设施风险;
d)环境风险;
e)职业卫生风险;
f)管理风险;
g)法律、法规、标准需求;
h)相关方的观点。
5.4.3.3初始风险评价结果应包括各种风险可能发生过程的描述和风险的级别,并按危险性排序。
5.4.3.4初始风险评价结果文件化,各单位应依据初始风险评价结果进行风险分级管理。
5.4.3持续风险评价
5.4.4.1各车间应持续地进行风险评价,及时处理重大风险。
5.4.4.2持续风险评价常用方法包括:
a)使用前检查;
b)计划任务观察;
c)设备检查;
d)工前危险预知;
e)交接班检查;
f)定期安全检查
g)定期检修;
h)安全标准化系统评价。
5.4.4风险评价计划
5.4.5.1根据生产特点,应制定风险评价计划如下:
a)冶炼作业风险评价;
b)工程地质风险评价;
c)设备设施风险评价;
d)职业卫生风险评价;
e)交通、运输风险评价;
f)危险物料风险评价;
g)火灾风险评价;
h)水灾风险评价;
i)紧急情况风险评价。
5.4.5.2风险评价计划必须配备相应的资源。
5.4.5风险评审
安全环保部根据所完成的初始风险评价工作的结果,对各个车间汇总的风险评价结果进行核实,并进一步完成其他的评审工作。
5.4.6.1核实已完成的风险评价工作:
a)核实每个车间列出的工种是否全面,核实主要的设备设施是否全部包括在内,核实工艺流程是否符合实际情况,核实各职能部室的评价是否准确;
b)核实作业过程评价表中的各工种的作业过程是否有条理,是否有缺漏;
c)核实其采用的LEC法评价的是否符合实际情况,是否准确,核实所确定的风险等级是否准确;
d)核实所确定的不可承受风险是否准确;
e)核实所提出的风险控制措施是否实际、合理。
5.4.6.2评审以下三个方面:
a)获取和识别适用的法规和其他要求,搜集各个部室、车间的法规、制度、安全操作规程等资料,评审其是否健全、是否有效、是否执行落实到位,即符合性、实施性和有效性;
b)对既往事故进行分析总结,搜集以往的事故事件资料,进行分类汇总、统计、分析和总结;
c)对现有的规章制度、文件、机构和职责进行评审,评审其是否健全、是否有效、是否执行,安全职责是否明确。
5.4.6.3新建、改建、扩建项目的危害辨识、风险评价工作,按照实施指南的要求执行时,可参考政府单位认可的有资质的机构提出的劳动安全卫生预评价报告。
5.4.7风险等级判定,使用LEC评价法评价出以下风险等级。
五级:
超过320,为非常高的风险,极其危险,不能继续作业,考虑放弃、停止本项作业。
四级:
160至320,为高风险,高度危险,需要立即整改纠正。
三级:
70至160,为中风险,显着危险,需要整改纠正。
二级:
20至70,为可能的风险,一般危险,需要关注。
一级:
20以下,为可接受的风险,稍有危险,可以接受容忍。
5.5风险控制措施
5.5.1风险分级管理
a)风险程度在四级及以上的,定为公司关键任务、关键设备或关键工艺,由生产技术部、安全环保部组织有管单位现场制定安全措施;
b)风险程度达到三级的,定为车间关键任务、关键设备或关键工艺,由车间主管领导组织车间生产、安全等有关部室现场制定安全措施;
c)作业风险程度达到二级的,定为工段或班组的关键任务,由工段或班组组织本单位安全、技术管理人员制定安全措施。
5.5.2风险控制计划
对风险控制主要采取以下一项或多项措施的组合:
A——制定目标、指标及管理方案;
(例:
技术改造、上硬件设施)
B——制定安全规章制度;
C——制定应急预案与响应;
D——制定关键任务作业指导书;
E——执行工作票制度;
F——执行危险作业审批制度;
G——编制安全操作规程;
H——制定安全检查表(日常、专项);
I——加强培训教育;
J——保持现有措施。
5.5.3安全环保部监督、协调各部室、车间对重大风险进行有效控制;
对各部室、车间的风险控制的有效性实施监督、评价。
5.5.4车间每年依据当年内、外部条件,对单位管理、生产活动进行一次危害辨识、危险评价工作,并将辨识和危险评价结果报安全环保部。
5.5.5各单位依据风险评价结果,汇总本单位的风险等级、关键任务、关键设备、关键工艺以及各类风险控制措施。
5.5.6生产车间、安全环保部应根据危害辨识与风险评价结果,制定相应的风险控制措施,以达到有效控制。
5.5.7风险控制措施的确定,应遵循下列原则:
a)消除;
b)替代;
c)工程控制、隔离;
d)管理措施;
e)个体防护。
5.5.8当员工安全健康与财产保护发生矛盾时,应优先考虑确保员工安全健康的措施。
5.5.9重大风险控制措施按《重大危险源监控和重大隐患整改制度》执行。
5.5.10作业过程方面的重大风险控制按安全标准化系统的作业管理制度执行。
5.5.11设备设施方面的风险控制按《设备设施管理制度》执行。
5.5.12工艺方面的风险控制按《工艺管理制度》及有关的生产保障系统管理制度执行。
5.5.13职业危害风险控制措施按《职业危害控制制度》执行。
5.5.14对危险作业或进入危险区域作业的按《许可作业管理制度》执行。
认真执行《危险作业审批制度》和《工作票制度》。
5.5.15供应商与承包商方面的风险控制按《供应商管理制度》和《承包商管理制度》执行。
5.5.16管理过程中的风险控制按安全标准化系统的有关制度执行。
5.6危害辨识与危险评价工作的更新
5.6.1安全环保部每年三月应组织有关单位对公司的危险源、风险评价结果、风险控制措施进行重新确认,如有变化予以更新。
5.6.2安全环保部应定期进行危害辨识与风险评价的回顾。
并根据危害辨识、风险评价结果及更新情况,并采取相应的控制措施。
5.6.3新施工项目由施工单位负责人组织对新施工项目进行危害辨识,填写《危害辨识与风险评价表》。
上报安全环保部,由安全环保部进行风险评价,对新产生的重大风险制定控制措施予以实施。
5.6.4当发生下列情况之一时,应重新进行危害辩识与危险评价工作:
a)当法律、法规更新时;
b)当生产活动内容或工艺发生重大变化时;
c)当危害辨识与危险评价知识或方法有所进步认为必要时;
d)当安全检查中发现重大事故隐患时;
e)当有新设备、新工艺、新材料时;
f)其他情况需要时。
5.7员工教育和培训
5.7.1劳动工资培训部应按照《安全教育与培训管理制度》,组织对危险源监控管理人员、作业人员进行安全教育和技术培训,并建立教育培训档案。
5.7.2教育和培训内容如下:
a)危害的辨识;
b)危害安全管理制度和安全操作规程;
c)危害可能发生事故时的危害后果;
d)事故案例和预案事故的措施;
e)自我防护方法的方法;
f)发生事故的报告方法。
6相关文件
6.1GB5044-85《职业性接触毒物危害程度分级》
6.2GB12331-90《有毒作业分级》
6.3GB6441-86《公司职工伤亡事故分类》
6.4《变化管理制度》
6.5《重大危险源监控和重大隐患整改制度》
6.6《设备设施管理制度》
6.7《工艺管理制度》
6.8《职业危害控制制度》
6.9《许可作业管理制度》
6.10《危险作业审批制度》
6.11《工作票制度》
6.12《供应商管理制度》
6.13《承包商管理制度》
6.14《安全教育与培训管理制度》
7相关记录
7.1风险评价计划
风险评价计划表
序号
评价
时间
评价项目名称
依据
方法
控制
措施
责任
单位
风险评价结论
评价审核单位
7.2《危害辨识与风险评价表》
危险源辨识、风险评价及控制措施一览表
单位:
时间:
年月
作业活动
危险
因素
危害
方式
可能导致的
事故
评价方式:
D=LEC
危险级别
L
E
C
D
7.3《重大危险源清单》
重要危险源清单
年度:
危险因素
可能导致的事故
风险级别
责任单位
控制措施
单位责任人:
制表人: