数控支承板毕业设计Word格式.docx
《数控支承板毕业设计Word格式.docx》由会员分享,可在线阅读,更多相关《数控支承板毕业设计Word格式.docx(17页珍藏版)》请在冰豆网上搜索。
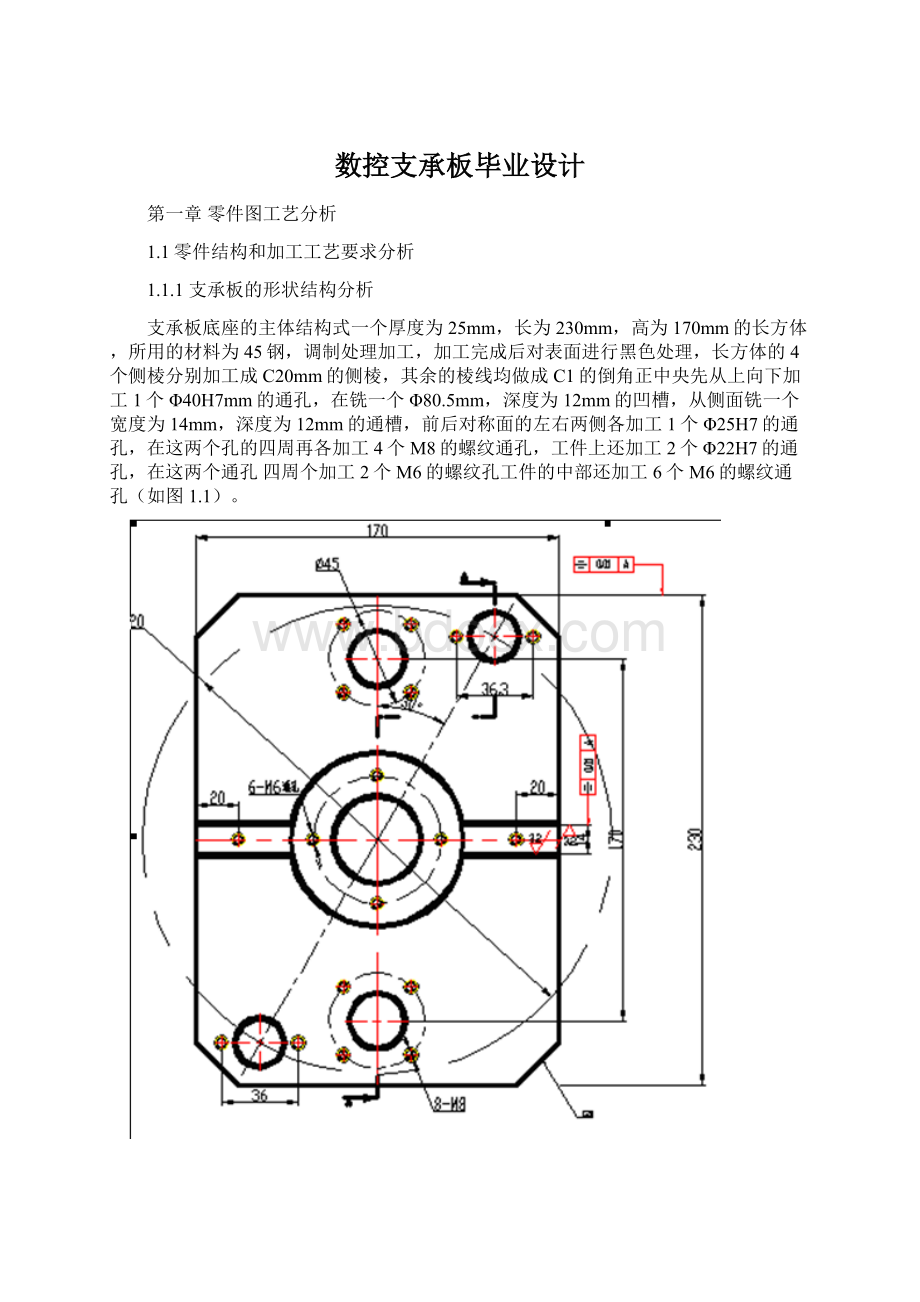
(3)自为基准原则,某些要求加工余量小而均匀的精加工或光整加工工序,选择加工表面本身作为定位基准。
(4)互为基准反复加工原则,使各加工表面之间具有较高的位置精度,或为使加工表面具有均匀的加工余量,可采取两个加工表面互为基准反复加工的方法。
(5)便于装夹原则。
图1.3粗基准面
本零件基准的选择粗基准面为C面,粗铣定位基准面后粗精铣B面,后铣4个侧棱→以B面为精基准面精铣C面至高度到25mm(如图1.3)。
1.5刀具的选择
刀具的选择是数控加工中重要的工艺内容之一,它不仅影响机床的加工效率,而且直接影响加工质量。
编程时,选择刀具通常要考虑机床的加工能力、工序内容、工件材料等因素。
与传统的加工方法相比,数控加工对刀具的要求更高,不仅要求精度高、刚度高、耐用度高,而且要求尺寸稳定、安装调整方便。
这就要求采用新型优质材料制造数控加工刀具,并优选刀具参数。
选择Φ30mm的硬质合金立铣刀铣4个侧棱的C25mm倒棱和Φ80.5mm的凹坑;
选择Φ12mm的高速钢键槽铣刀铣前后通槽;
分别选择Φ39.6mm、Φ24.6mm、Φ21.6mm、Φ5.15mm、Φ6.91mm高速钢钻头加工孔和螺纹底孔;
分别选择Φ40mm、Φ25mm、Φ22mm硬质合金铰刀加工Φ40H7、Φ25H7、Φ22H7光孔;
选择M6、M12高速钢丝锥加工螺纹孔;
选择倒角铣刀加工所有的C1mm的倒角(如表1.2)。
产品名称或代号
零件名称
零件图号
序号
刀具号
刀具名称
数量
加工表面
刀具半径
刀尖角
1
T01
Φ30mm硬质合金立铣刀
倒棱、铣Φ80.5mm凹坑
0.2
2
T02
Φ12mm高速钢键槽铣刀
铣前后通槽
3
T03
Φ39.6mm高速钢钻头
钻Φ39.6mm孔
4
T04
Φ40mm硬质合金铰刀
加工Φ40H7光孔
5
T05
Φ24.6mm高速钢钻头
钻Φ24.6mm孔
6
T06
Φ25mm硬质合金铰刀
加工Φ25.7mm光孔
7
T07
Φ21.6mm高速钢钻头
钻Φ21.6mm孔
8
T08
Φ22mm硬质合金铰刀
9
T09
Φ5.15mm高速钻头钢
钻M6螺纹底孔
10
T10
M6的高速钢丝锥
加工M6螺纹
11
T11
Φ6.91mm高速钢钻头
钻M8螺纹底孔
12
T12
M8的高速钢丝锥
加工M8螺纹
13
T13
倒角铣刀
倒所有的C1mm倒角
14
T14
中心钻
Φ3mm加工各孔的中心孔
表1.2
1.6切削用量选择
1.6.1切削用量选择原则
合理选择切削用量的原则是:
粗加工时,一般以提高生产率为主,但也考虑经济性和加工成本;
半精加工或精加工时,应在保证加工质量的前提下,兼顾切削效率、经济性和加工成本。
具体数值应根据机床说明书、切削用量手册,并结合经验而定。
1.6.2选择背吃刀量和侧吃刀量
表1.3
查表后倒棱面的加工,侧吃刀量取af=5吗,分5次走刀加工完成;
dw-dm
切削深度ap的计算公式:
ap=2
式中:
dw—待加工表面外圆直径,单位mm
dm—已加工表面外圆直径,单位mm.
粗铣Φ80.5mm凹坑,采用环形走刀,背吃刀量af=2.2mm,侧吃刀量af=15mm,加工后背吃刀量留ap=0.4mm的余量,侧吃刀量留af=0.5mm的余量;
粗铣前后通槽,背吃刀量ap=11.5mm,侧吃刀量af=6mm,底面留0.5mm加工余量,侧面各留1mm的加工余量;
精铣前后通槽,分左右两次走刀,每次走刀被吃刀量ap=0.5mm,侧吃刀量af=1mm。
1.6.3主轴转速
主轴转速n的公式:
n=1000Vc/∏D
D—工件或刀尖的回转直径,单位mm
Vc—切削速度,单位m/min
(1)Φ30mm硬质合金立铣刀,
D=30mm,根据表1.3切削速度取vc=60m/min,
n=1000Vc/∏D=1000×
60/3.14×
30=636r/min,n可取680r/min;
(2)Φ12mm高速钢键槽铣刀,
D=12mm,根据表1.3切削速度取vc=25m/min,
25/3.14×
12=663r/min,n可取700r/min;
Φ39.6mm高速钢钻头,根据表1.3切削速度取vc=25m/min,
39.6=187r/min,n可取200r/min;
Φ40mm硬质合金铰刀,根据表1.3切削速度取vc=60m/min,
40=465r/min,n可取480r/min;
Φ24.6mm高速钢钻头,根据表1.3切削速度取vc=22m/min,
22/3.14×
24.6=263r/min,n可取280r/min;
Φ25mm硬质合金铰刀,根据表1.3切削速度取vc=60m/min,
25=745r/min,n可取760r/min;
Φ21.6mm高速钢钻头,根据表1.3切削速度取vc=20m/min,
20/3.14×
21.6=288r/min,n可取300r/min;
Φ22mm硬质合金铣刀,根据表1.3切削速度取vc=60m/min,
22=855r/min,n可取870r/min;
Φ5.15mm高速钢钻头,根据表1.3切削速度取vc=15m/min,
15/3.14×
5.15=874r/min,n可取900r/min;
M6的高速钢钻头,根据表1.3切削速度取vc=2.5m/min,
2.5/3.14×
6=172r/min,n可取180r/min;
Φ6.91mm高速钢钻头,根据表1.3切削速度取vc=16m/min,
16/3.14×
6.91=776r/min,n可取700r/min;
M8的高速钢丝锥,根据表1.3切削速度取vc=2.5m/min,
8=138r/min,n可取150r/min;
倒角铣刀,切削速度取vc=25m/min,n可取500r/min;
中心钻,切削速度取vc=20m/min,n可取800r/min。
1.6.4进给速度
常用硬质合金或图层硬质合金切削不同材料时的切削用量推荐值见表1.4。
表1.4硬质合金刀具切削用量推荐表
刀具
材料
工件
粗加工
精加工
切削速度(m/min)
进给量(mm/r)
背吃刀量(mm)
硬质合金或涂层硬质合金
碳钢
220
260
0.1
0.4
低合
金钢
180
高合
120
160
铸铁
80
140
不锈钢
钛合金
40
0.3
1.5
60
灰铸铁
150
0.15
0.5
球墨
100
铝合金
1600
参考表1.4
倒棱角的加工,选取进给量fz=0.15mm/z;
粗铣Φ80.5mm凹坑,选取进给量fz=0.20mm/z;
精铣Φ80.5mm凹坑,选取进给量fz=0.10mm/z;
粗铣前后通槽,选取进给量fz=0.20mm/z;
精铣前后通槽,选取进给量fz=0.10mm/z;
钻Φ39.6mm孔,选取进给量f=0.20mm/r;
铰Φ40H7孔,选取进给量f=0.10mm/r;
钻Φ24.6mm孔,选取进给量f=0.20mm/r;
铰Φ25H7孔,选取进给量f=0.10mm/r;
钻Φ21.6mm孔。
选取进给量f=0.20mm/r;
铰Φ22H7孔,选取进给量f=0.10mm/r;
钻Φ6.91mm孔,选取进给量f=0.10mm/r;
钻Φ5.15mm孔,选取进给量f=0.08mm/r;
钻中心孔,选取进给量f=0.20mm/。
1.7
切削加工顺序
1.7.1
加工顺序的安排原则
(1)基面先行原则。
加工一开始,总是先把精基面加工出来,因为定位基准的表面越精确,装夹误差就越小。
(2)先粗后精原则。
各个表面的加工顺序按照粗加工→半精加工→精加工→光整加工的顺序依次进行,这样才能逐步提高加工表面的精度和减少表面粗糙度。
(3)先主后次原则。
零件上的工作表面及装配面精度要求较高,属于主要表面,应先加工,从而能及早发现毛坯中主要表面可能出现的缺陷。
(4)先面后孔原则。
对于箱体、支架和机体类零件,平面轮廓尺寸较大,一般先加工平面,后加工孔和其他尺寸。
(5)上道工序的加工不能影响下道工序的定位与夹紧。
根据以上原则,将零件加工顺序、所采用的刀具和切削用量等参数编入表1.5所示的加工工序卡中以指导编程和加工操作。
数控加工工序卡片
支承板
工序号
程序编号
夹具名称
夹具编号
使用设备
车间
1
通用夹具
数控加工车间
工步号
工步内容
刀具规格
(mm)
主轴转速
(r/min)
进给量(mm/z)
背吃刀量
铣4个侧棱的C25mm倒棱
Φ30
680
粗铣Φ80.5mm凹坑
0.20
2.2
精铣Φ80.5mm凹坑
0.10
粗铣前后通槽
Φ12
700
11.5
精铣前后通槽
钻中心孔
800
钻一个Φ39.6mm的通孔
Φ39.6
200
19.8
用铰刀加工Φ40H7光孔
Φ40
480
钻2个Φ24.6mm的通孔
Φ24.6
280
12.3
用铰刀加工2个Φ25H7光孔
Φ25
760
钻2个Φ21.6mm的通孔
Φ21.6
300
10.8
用铰刀加工2个Φ22H7光孔
Φ22
870
钻10个M6的螺纹底孔,4个深度为15mm,6个为通孔
Φ5.15
900
2.6
用丝锥加工M6螺纹,4个深度为15mm,6个为通孔
M6
15
钻8个M8的螺纹底孔,为通孔
Φ6.91
0.08
3.5
16
用丝锥加工M8螺纹
M8
17
加工所有C1mm的倒角
表1.5
3.8工艺路线设计
方案一:
(1)锯床据毛坯240x180x30。
(2)基准以4面分中粗铣底板毛坯6面,各面给磨床留余量0.5mm。
(3)基准以4面分中,精磨底板6面。
使底板加工尺寸为230x170x25
(4)粗铣侧棱C20
(5)粗,精铣凹槽部位及倒角
(6)钻,扩,铰孔Φ40通孔
(7)钻,扩,铰孔2-Φ22通孔
(8)钻,扩,铰孔2-Φ25通孔
(9)钻螺纹孔8-M8通孔
(10)钻螺纹孔6-M6通孔
(11)钻螺纹孔4-M6
(12)去毛刺,倒角,攻丝
(13)入库
方案一的特点是装夹次数少避免了多次装夹产生的误差。
方案二:
(1)锻造毛坯240x180x30。
(2)选择粗基准面为C面,粗铣定位基准面后粗精铣B面,后铣4个侧棱;
以B面为精基准面精铣C
(3)铣,铣4个侧棱的C25mm倒棱
(4)铣,粗、精铣Φ80.5mm凹坑
(5)钻,钻中心孔
(6)钻,钻一个Φ39.6mm的通孔
(7)铰,用铰刀加工Φ40H7光孔
(8)钻,钻2个Φ24.6mm的通孔
(9)铰,用铰刀加工2个Φ25H7光孔
(10)钻,钻2个Φ21.6mm的通孔
(11)铰,用铰刀加工2个Φ22H7光孔
(12)钻,钻10个M6的螺纹底孔,4个深度为15mm,6个为通孔
(13)攻丝,用丝锥加工M6螺纹,4个深度为15mm,6个为通孔
(14)钻,钻8个M8的螺纹底孔,为通孔
(15)攻丝,用丝锥加工M8螺纹
(16)去倒角,加工所有C1mm的倒角
(17)检验,入库
方案二的特点是:
装夹时保证底面平整,确保加工精度。
比较上述两套方案后不难看出,方案一的装夹次数比较少,看上去貌似更加的简便,节省工时,但细细分析一下,可以发现,方案一在保证零件精度上有所欠缺,毛坯的材料分布欠均匀,即使夹具的自定心能力再好也不能保其起精度。
虽然方案二装夹次数比较多,但是保证了底面平整,保证了零件的精度。
综合上述,方案二优于方案一,因此本设计的工艺路线选择方案一。
第二章零件加工程序的编制
2.1数控程序编制的一般方法
数控程序编制的一般方法主要有手动编程和自动编程。
手动编程,即整个编程过程由人工完成,对编程人员的要求高,要熟悉数控代码功能、编程规则,具备机械加工工艺知识和数值计算能力。
适用于几何形状不太复杂的零件;
三坐标联动以下加工程序。
自动编程,即编程人员根据零件图纸的要求,按照某个自动编程系统的规定,将零件的加工信息用叫简便的方式送入计算机,编程系统将能根据数控系统的类型输出数控加工程序。
自动编程适用于形状复杂的零件;
虽不复杂但编程人员工作量很大的零件(如有数千个孔的零件);
虽不复杂但计算工作量大的零件(如非圆曲线轮廓的计算等)。
2.1.1数控程序编制的内容及步骤
(一)分析零件图样和工艺处理
1.选择合适的对刀点
对刀点—刀具相对零件运动的起点,又称起刀点。
2.选择对刀点的原则:
(1)为了提高零件的加工精度,刀具的起点应尽量选在零件的设计基准或工艺基准上。
(2)对刀点应选在对到方便的位置,便于观察和检测。
(3)对刀点的选择应便于坐标值的计算。
3.确定加工路线
加工路线—加工过程中刀具相对于工件运动的轨迹。
加工路线的确定应考虑以下几个方面的问题:
(1)应使加工路线最短,这样既可减少程序段,又可减少空刀时间,大余量切除的走刀次数要少,每一次走刀应切除尽可能多的加工内容,尽量减少或缩短空行程。
(2)在车削与铣削零件时,应尽量避免径向切入和切出,而应沿零件的切向切入和切出。
(3)要选择工件在加工后变形较小的路线。
例如对细长零件或薄板零件,应采用分几次走刀加工到最后尺寸。
此外,确定加工路线时,还要考虑工件的加工余量和机床、刀具的刚度等情况,确定是一次走刀还是多次走刀完成加工,以及在铣削加工中是采用顺铣还是逆铣等。
(二)数学处理
先建立一个工件坐标系,根据图纸的要求,计算出刀具的运动轨迹。
(三)编写零件程序清单
加工路线和工艺参数确定后,编写程序清单。
(四)程序输入
现代数控机床,多次用键盘把程序输入到计算机中。
在通信控制的机床中,程序可以由计算机接口传送。
(五)程序校验和试切削
校验通常的方法是将控制的内容输入到数控装置中进行机床的空运转检查。
对于平面轮廓的工件,可在机床上用笔代替刀具。
坐标纸代替工件进行空运行进行绘图。
对于空间曲面零件,可用木料或塑料工件进行试切,以此检查机床运动轨迹与动作的正确性。
在具有图形显示的机床上,用模拟刀具进行试切削过程的方法进行校验。
2.2零件加工程序的编制
在完成了上述准备工作后便可以进行零件加工程序的编制,我们学习了日本的FANUC系统和德国的SIEMENS系统,本设计选择FANUC系统编程,
N10G90G54绝对坐标编程,设定工作坐标系
N20G00X0.0Y0.0
N30M03S800M08主轴正转
N40G43Z5.0H14调用刀具
N50G99G81Z-3.0R5.0F0.2
N60X-85.0Y0.0钻孔
N70X100.91
N80G80G49G00Z100.0
N90M05M09主轴停止
N100M00
N110G54G00X0.0Y0.0
N120M03S200M08主轴正转
N130G43Z5.0H03
N140G99G83Z-26.0R5.0Q3F100调用孔加工循环
N150G80G49G00Z100.0
N160M05主轴停止
N170M00
N180G54G90G00X0.0Y0.0M0.S680
N190G43H01Z3.0M08
N200G01Z-6.0F80
N210X-20.0
N220G03X-20Y0.0I2.0J0.0
N230G01G41X-40.0Y0.0D01建立刀补
N240G03-40.0Y0.0I40.0J0.0
N250G01G40X-20Y0.0F80取消刀补
N260G01Z-12.0
N270G03X-20.0Y0.0I20.0J0.0
N280G41X-40.0Y0.0D01
N290G03X-40.0Y0.0I4.0J0.0
N300M00
N310G54G90G00X0.0Y0.0M03S700
N320M00主轴暂停
N330G54G00X-30.0Y0.0
N340M03S900M08主轴正转
N350G43Z-7.0H09
N360G99G83Z-14.0R5.0Q3F60
N370Y-73.0
N380G80G00Z100.0
N390M00
N400G54G00X-30.0Y0.0
N410M03S180M08
N420G43Z-7.0H10
N430G99G84Z-14.0R5.0F180
N440Y-73.0
N450G80G00Z100.0
N460M00程序暂停
N470G54G0