车身结构与工艺Word格式.docx
《车身结构与工艺Word格式.docx》由会员分享,可在线阅读,更多相关《车身结构与工艺Word格式.docx(28页珍藏版)》请在冰豆网上搜索。
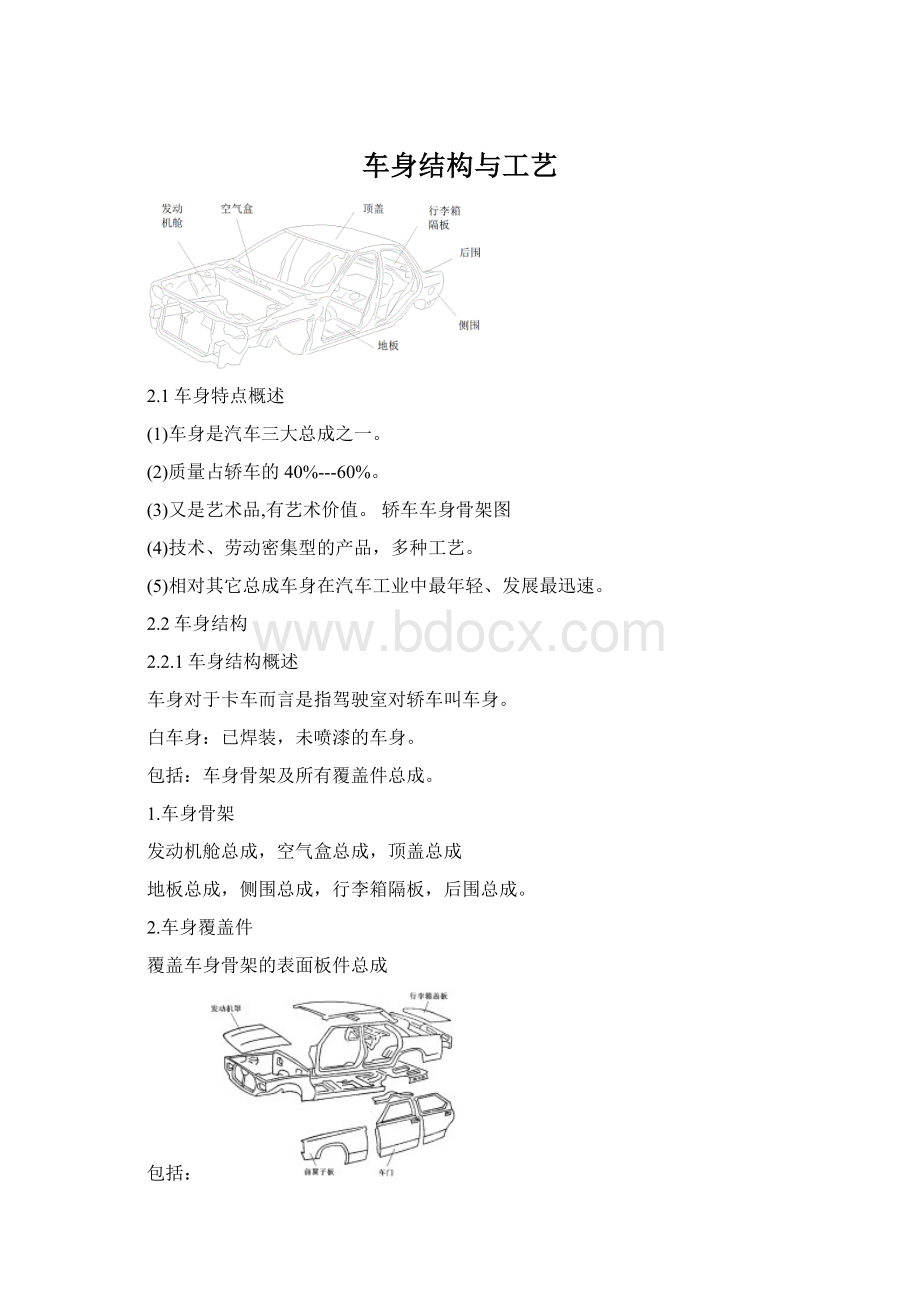
④车架质量较大。
⑤车架增加了整车高度。
⑥车架加工成本高。
2.承载式车身结构
(1)底座承载式
格珊式结构:
①由尺寸相近型钢组成,易于建立较符合实际的有限元模型,提高计算精度。
②变动杆件的数量和位置调整杆件中的应力,达到等强度设计。
③较大的抗扭刚性。
④节省材料,成本低。
(2)整体承载式
车身的上部与下部形成整体封闭环。
优点
可以设计出等强度的空间结构,使车身质量小刚度大,易于保持低重心、可用空间大,易于实现自动化生产、安全性高。
(3)承载式车身特点
1)薄钢板材料,质量明显减少。
2)没有车架降低整车高度,风阻系数减少。
3)适应现代流线型车身的制造。
4)增加成本和质量。
5)改型较困难。
6)抗扭性较差、不适宜作小批量生产。
2.2.3车身覆盖件结构类型
1.骨架外蒙皮式
2.内外板组合式
现代轿车基本都采用内外板组合式结构
2.2.4车身刚性结构与安全
纵向撞车:
在车身前部和后部均为弹性结构而中部位刚性结构的情况下,能确保乘员的安全。
弹性结构刚性结构
2.2.5车身结构分析
1.轿车结构特点
(1)车身底部边纵梁与侧围融为一体,既提高刚度又不占用车内使用空间。
(2)为保护乘员安全,重要部位设置柱状结构,如:
三环樑、六立柱结构,提高整车强度和刚度。
(2)焊缝特点
1)具有隐蔽性,焊点避开视线。
覆盖件搭接利用门框、窗框、雨水槽、车底附近、密封条、装饰条。
2)双边搭接处形成空心柱,又提高刚度,一举两得。
如地板与侧围。
3)容易焊接操作,尽量边缘搭接、必要处开工艺孔。
4)搭接宽度适中,15-20mm.
2.3车身材料发展趋势
2.3.1车身用薄钢板发展趋势
1.力学性能及工艺性能
屈服强度要低。
屈服强度(124-140)MPa钢板的废品率为0.3%,
屈服强度(130-165)MPa钢板的废品率为5%,
2.镀层钢板
双面镀锌板白车身,使用寿命可达12年。
汽车造型发展的趋势
1)减少发动机所占空间,驾驶室前移;
2)加长轴距,减少前后悬的长度;
3)行李厢向车尾部后移或向车顶部上移;
4)从三厢式向单厢式发展;
5)车门由转轴式设计向旋翼式、推拉式及整体顶盖翻转式结构发展。
3.拼焊钢板
外表部位用涂镀层钢板,耐蚀性。
承力、易磨损部位用较厚高强度钢板。
如:
车门内板、车身底板、侧面横档、档风玻璃窗框、中立柱等。
拼焊钢板,生产工艺简单、降低了模具和焊装夹具制造成本,改善了零件性能的稳定性。
4.表面质量
冲压过程中,材料表面缺陷因应力集中而引起破裂。
表面质量差会增加焊接电阻影响电焊质量。
表面粗糙度时涂漆效果较好
钢板表面粗糙度和清洁度影响锌层附着力。
机器人点焊,板厚误差增加焊接电阻导致虚焊,影响质量。
要求对宽1.5米长3000米的厚0.8毫米钢板,厚度公差不能超出20微米。
5.化学成分
含碳量:
0.05%-0.15%,含硅量:
在0.37%以下,钢板具有良好的塑性。
先进工艺,钢板的化学成分稳定性↑,有害元素含量明显↓。
钢厂可根据零件的用途、形状的复杂程度来调整同钢的化学成分。
2.3.2车身用非金属有色金属材料比例增加
1.车身塑料化、复合材料化
提高汽车造型的美观度与设计的灵活性,降低汽车的能耗。
塑料有抗腐蚀、耐磨、隔热、消声、减振等优点。
由内外装饰件向车身覆盖件和结构件方面发展。
近来塑料在轿车上的使用量约占车身重的10-30%。
保险杠采用复合材料。
蓝鸟轿车车门下部采用塑料贴片,保险杠实现了整车周边化。
图4-7宝马M3轿车的前翼子板为塑料减量1.5kg
2.铝、镁合金材料使用比例增加
每使用lkg的铝,可降低汽车重量2.25kg
汽车每减轻1kg重量,1L汽油汽车多行驶1.1m。
用泡沫铝材制造汽车零件的质量,只有原钢件质量的1/2,而刚度却为钢件的10倍。
其保温绝热性能比铝高95%;
对频率大于800Hz的噪声有很强的消声能力。
实验表明,两辆各质量为2000kg,速度为20km/h轿车相碰撞,只需3块15cm*15cm*l0cm的泡沫铝材就能将碰撞能量吸收掉。
2.4车身冲压用材料
冲压性能:
便于加工、容易得到高质量的冲压件,生产效率高,一次冲压工序的极限变形程度和总极限变形程度大,模具磨损小的等。
2.4.1冲压加工对表面质量和厚度公差的要求
1.良好的表面质量
(1)良好的表面质量
覆盖件外表面不应有气泡、缩孔、划痕、麻点、裂纹、结疤、分层等缺陷。
因在冲压中,缺陷因应力集中而引起破裂。
(2)表面平整
板料表面翘曲不平,剪切或冲压因定位不稳而出现废品;
在冲裁中会因板料变形展开而损坏模具。
拉深时使压料不均而影响材料的流向而引起开裂或起皱。
(3)表面无锈
有锈,对冲压不利,损伤模具,影响后续焊装涂装工序的正常进行及质量。
2.严格的厚度尺寸公差
板料过薄则回弹难以控制,或出现“压不实”现象;
板料过厚会拉伤制件表面,缩短模具寿命,甚至损坏模具或设备。
2.4.2材料冲压工艺对板料力学性能的要求
1.极限
屈服极限材料易屈服,变形抗力↓,产生相同变形所需变形力↓。
压缩不起皱。
弯曲变形回弹↓即贴模性和定形性好。
2.屈强比
容易产生塑性变形而不易破裂,而传力区的材料有较高强度而不易拉裂。
3.厚向异性系数R
R>
1时,宽度方向的变形比厚度方向的变形容易.
R愈大,在拉深过程中越不容易产生变薄和发生破裂
4.延伸率
拉深力大于或等于屈服极限而小于或等于强度极限。
对于冲压成形性能有更直接、实际的意义。
越高,板料的冲压成形性能愈好。
2.4.3冲压性能对化学成分和金相组织的要求
1.化学成分
碳量不超过0.05%-0.15%的低碳钢板具有良好的塑性。
含硅量在0.37%以下的钢,硅对塑性影响不大。
2.金相组织
晶粒大小不均最引起裂纹。
粗大的晶粒在冲压成形时,会在制件表面留下粗糙的“桔皮”,影响制件表面质量。
过小的晶粒会使钢板的塑性降低。
2.4.4冲压用钢板的类型
1.按钢的品质分类
常用:
普通碳素钢、优质碳素钢以及汽车专用的具有较高冲压性能的低合金高强度钢板
优质碳素结构钢板牌号:
沸腾钢----05F、08F、10F、15F、20F;
半镇静钢----08b;
镇静钢08、10、15、20、30等。
汽车专用钢板:
08Al(车身),09Mn、16Mn、06Ti、10Ti等用来制造汽车的受力零件,例如车架。
2.按钢板的拉深级别分类
表2-2热轧钢板的拉深级别代号
表2-3冷轧钢板的拉深级别代号
3.按钢板的表面质量分类
表2-4钢板的表面质量分类
4.按钢板轧制尺寸精度(厚度公差)分类
钢板的尺寸精度或厚度公差为:
A---高级精度;
B---较高级精度C---一般精度
深冲压用冷轧钢板分A、B两级;
优质钢板分A、B、C三级,普通钢板分为B、C两级。
钢板标注示例:
第3章冲压设备
3.1冲压设备的类型
1.按驱动力分
机械压力机(摩擦压力机曲柄压力机)
液压机
2.按床身型式分
开式压力机
闭式压力机
3.按曲柄压力机曲轴支承形式分
单柱式压力机
曲柄悬臂式结构
双柱式压力机(两轴承座)
单面传动
双面传动
4.按曲柄压力机连杆数目分
单点压力机
双点压力机
5.按压力机公称压力分
小型压力机100t以下
中型压力机100t~300t
大型压力机300t以上
6.按滑块数目分
单动压力机
双动压力机
其一滑块作拉深时压料用
3.2压力机类型的选择
选择依据:
冲压工艺的性质、生产批量、制件几何形状、尺寸及精度,安全操作等因素。
1.制件的几何形状、尺寸
1)复杂的大型拉深件:
双动拉深压力机,以保证压边的可靠性。
2)大、中型冲压件:
闭式曲柄压力机。
这类压力机刚度好、精度高,但只能两个方向操作
3)中、小型件:
选用开式曲柄压力机。
压力机刚度差,降低了模具寿命和制件质量。
但成本低、三个方向都可操作,容易安装机械化装置。
2.制件的工艺性质
校平、整形、弯曲、成形和温、热挤压工序:
可选用摩擦压力机。
结构简单、造价低,不易发生超负荷损坏。
3.3压力机的主参数
1.公称压力(吨位)
公称压力p是指滑块离下死点前某一特定距离S1时,滑块上所容许承受最大作用力。
S1称压力行程,
开式压力机=3-5mm,
闭式压力机=13mm;
2.电机功率
大型件冲裁、深度很大拉深,会出现压力不足而功率不足的现象,此时对电机功率进行校核,额定功率大于冲压总功率。
3.滑块行程s和行程次数n
滑块从上死点运动到下死点所经过的距离称为滑块行程S。
行程次数n是滑块在空载时每分钟往复行程的次数。
4.装模高度
5.工作台面和滑块底面尺寸导轨间距A、滑块底面前后尺寸B1、工作台面左右尺寸L、工作台前后尺寸B2。
6.压力机的精度和刚度
精度指压力机在静态情况下,所测得的压力机应达到的各种精度指标。
包括:
工作台面的平面度。
滑块下平面的平面角。
工作台面同滑块下平面的平行度。
滑块行程同工作台面的垂直度。
滑块中心孔同滑块行程的平行度。
第4章车身冲压工艺与材料变形理论
4.1冲压工艺特点及冲压工序分类
4.1.1冲压工艺特点
常温,压力机模具施压板料,在塑性变形极限内,板料分离或变形。
1.优点:
(1)操作简便,生产率高,易于实现机械化与自动化。
(2)在大批量生产中显著降低成本。
(3)冲压可以获得其它加工方法所不能制造或难以制造的,形状复杂的零件。
(4)模具多为单件生产、精度要求高,制造周期长,模具制造费用高,不宜用于单件小批量的零件生产。
2.冲压生产的三大要素
板料、模具和冲压设备
4.1.2冲压工序分类
1.按是否分离分
板料在冲压过程中沿设计分界线分离。
(1)分离工序
(2)成形工序
板料在不分离前提下发生塑性变形
2.按工件成形特点分
(1)弯曲将板料弯成一定的角度或弧面的工序。
(2)拉深
将平面板料变成各种开口空心零件,或把空心件的形状,尺寸作进一步改变。
(3)局部成形
用各种不同性质的局部变形来改变冲压件形状。
包括翻边、胀形、校平和整形等。
4.1.3冲压件类型
2冲压件基本类型
(1)伸长型:
工件某处拉应变的绝对值最大,板料伸长和厚度减薄。
(2)压缩型:
压应变的绝对值最大,板料压缩和厚度增厚。
4.冲压件的成形工序分析
多工序作用结果:
车身翼子板:
周边→翻边,腹板→拉深、冲孔。
4.2金属塑性变形的力学规律
4.2.1金属塑性变形的基本概念
外力作用下,金属形状和尺寸变化→变形。
分为弹性变形、塑性变形。
1.塑性变形
外力破坏原子间原有的平衡状态→排列畸变→金属形状、尺寸变化。
2.塑性及塑性指标
(1)塑性:
金属在外力作用下,能稳定的发挥塑性变形而不破坏其完整性的能力。
(2)塑性指标
3.影响金属的塑性与变形抗力的因素
(1)影响塑性的因素
内因:
化学成分的影响;
组织结构的影响
外因:
温度,变形速度,应力应变状态。
(2)影响金属变形抗力的主要因素
化学成分及组织
变形温度
4.金属塑性变形对组织和性能的影响
晶粒形状、方位变化→应力加工硬化
(1)硬化现象表现形式
材料的强度指标随变形程度增加而增加,塑性随之降低.
(2)加工硬化结果
引起材料力学性能指标的变化。
(3)加工硬化有利及不利方面
有利方面:
板料硬化减小过大的局部变形,使变形趋于均匀,增大成形极限,同时提高材料强度.
不利方面:
使进一步变形困难.
4.2.2材料塑性变形的应力应变状态
1点的应力状态
以点的应力状态为切入点。
九个应力分量
互相垂直平面上的剪应力互等
已知三个正应力和三剪应力,该点的应力状态就确定。
2主应力与主应变
存在这样一组坐标系,使得单元体各表面上只有正应力而无剪应力.
三个坐标轴的方向就称为主方向,而三个正应力就叫主应力.
4.2.4塑性变形条件
1.屈服准则:
物体中某点在三向应力状态下,当各应力分量之间符合一定关系时,该点才开始屈服。
(1)屈斯加屈服准则(最大剪应力理论
2.密席斯屈服准则(工程常用)
等效应力达到某一临界值,材料开始屈服:
β—与σ2有关系数,平均值1.1。
4.2.4真实应力、真实应变概念
1.真实应力
(1)不考虑横截面积的变化
(2)考虑横截面积的变化
(实际横截面积)
4.2金属塑性变形的力学规律
1.增量理论
2全增量理论
4.全增量理论的应用
(1)ε2=0时,为平面应变
如宽板弯曲
(2)σ1=σ2=σs时
材料三向等拉或等压时,材料不产生塑性变形,仅有弹性变形.
(4)σ1>
0且σ2=σ3=0时,材料受单向拉伸
材料受单向拉伸时产生拉伸变形其余两方向为压缩变形。
(5)σ1=σ2>
0时,σ4=0
材料受双向等拉时,拉应力方向为拉伸变形。
厚度方向为压缩变形,其值为拉伸变形的两倍。
从上式可知,判断某个方向的应变是伸长还是缩短,并不是看这个方向受拉还是受压,而是看该方向的偏应力是正还是负值;
或者说看该方向的应力值是大于还是小于平均应力值。
4.3板料的冲压成形性能
1.板料成形极限
两种失稳现象
拉伸失稳:
拉伸时缩颈和断裂
压缩失稳:
压缩时起皱
成形极限:
最大变形程度
总体成形极限、局部成形极限
2.板料的冲压成形性能
板料对冲压成形工艺的适应能力
抗破裂性、贴模性、定形性
冲压生产中,主要是用抗破裂性作为评价冲压成形的指标。
4.4成形极限图
1.概念
半平面内的两个主应变的任意组合,只要落在成形极限图中的成形极限曲线之上,薄板料变形时就会发生破裂;
反之则是安全的
方法:
调整压料力、改变润滑条件、改变毛坯尺寸、调整凹模圆角半径以及是否采用拉深筋,调整拉深材料流入凹模的变形阻力,以减少应变。
(2)提高复杂冲压件的成形质量
起皱和拉裂
在防皱的情况下,如何保证零件不破裂。
图示A点,用减小长轴方向应变的办法,使A点应变移至B点,从而进入安全区,这一措施也有利于解决起皱问题。