梁板预制QC成果报告Word文件下载.docx
《梁板预制QC成果报告Word文件下载.docx》由会员分享,可在线阅读,更多相关《梁板预制QC成果报告Word文件下载.docx(21页珍藏版)》请在冰豆网上搜索。
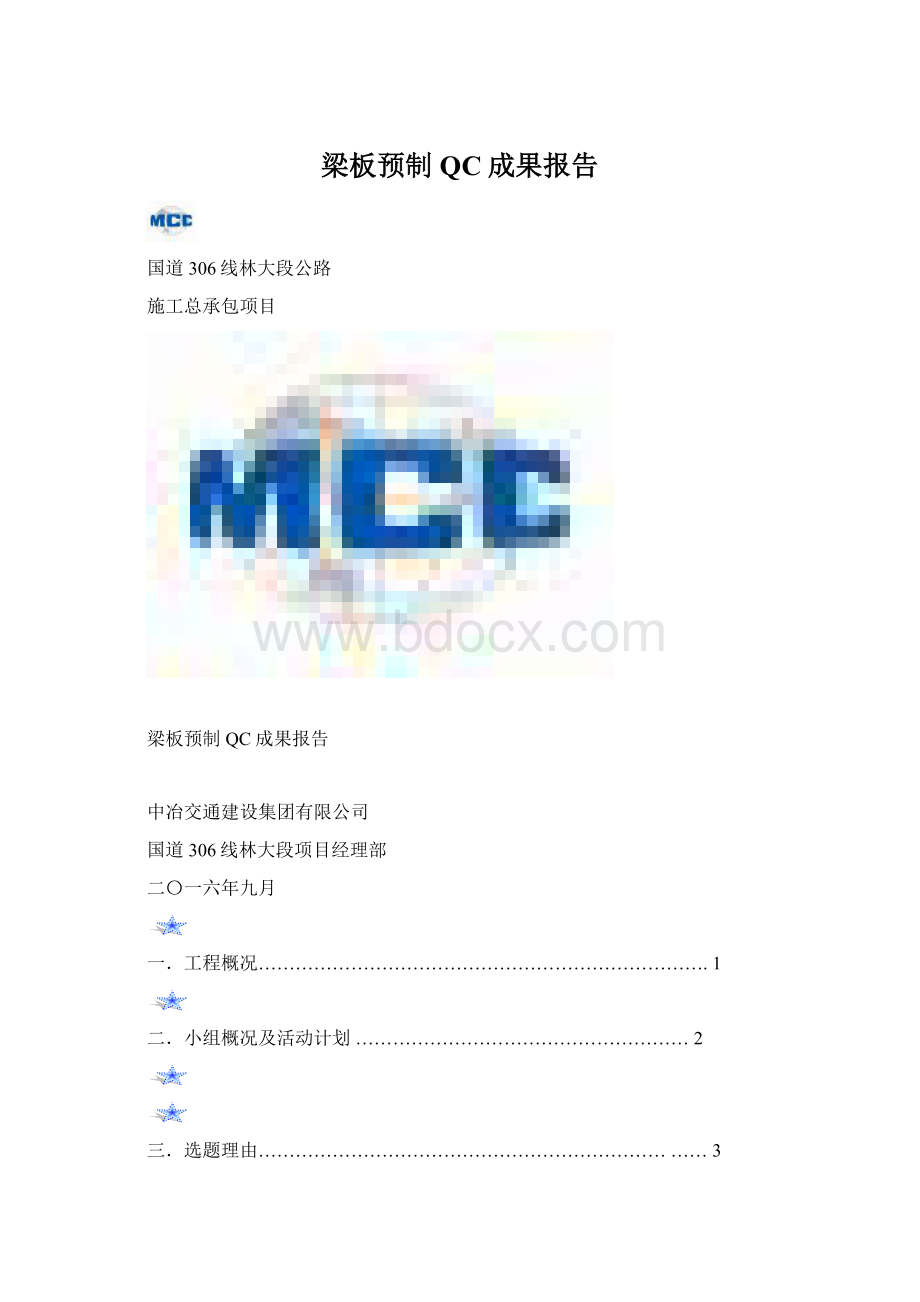
小组名称
梁板预制QC小组
成立时间
2016.8.6
小组类型
现场型
课题名称
梁板预制
小组活动时间
2016.8.6—2016.9.20
活动
次数
6次
小组人数
8人
成
员
序号
姓名
性别
年龄
组内职务
组内
分工
学历
职称
接受教育时间
1
唐峰
男
50
全面负责
组长
本科
教高
30
2
闫治平
55
现场负责
副组长
高工
3
王建平
34
技术负责
研究生
工程师
4
卜国防
38
技术人员
组员
5
李飞
33
试验负责
6
胡华伟
31
7
余宗昌
24
助工
8
蓝天旭
26
(二)小组活动情况
QC小组成立之后,每周活动不少于一次,每次不少于两小时,活动出勤率100%,发言率90%以上。
小组活动计划表
周
阶段
课题选定
现状调查
目标确定
问题分析
要因确定
对策
实施过程
活动总效果
巩固措施
遗留问题及下步打算
三、选题理由
理由一:
国道306线是国家公路网规划中干线主要通道,对于完善国家公路网建设和发挥路网整体效益有着重要的意义,故工程本身就对质量要求特别高,我项目部质量管理目标为“标段工程交工验收的质量评定:
合格;
竣工验收的质量评定:
优良”。
尤其是桥梁工程对于质量控制更为严格。
主要体现在混凝土达到外光内实,表面平整光洁,个别气泡直径小于3mm,无贯穿性裂纹、缺角、掉边、蜂窝、麻面等缺陷,外观尺寸符合设计误差要求。
理由二:
梁板预制生产过程中对梁板的尺寸及钢筋砼保护层精度本身要求特别高,这就要求我们在生产过程中一定要保证制作的梁板符合设计及规范要求的误差内。
梁板外观尺寸允许误差
检查项目
误差范围
检测方法及频率
权值
受力钢筋间距(mm)
±
10
尺量:
每构件检查2个断面
箍筋间距(mm)
每构件检查5~10个间距
钢筋骨架尺寸—长(mm)
按骨架总数30%抽查
钢筋骨架尺寸—宽(mm)
每骨架抽查30%
保护层厚度(mm)
每构件沿模板周边检查8处
理由三:
查看目前本项目生产的梁板普遍存在外表面气泡多、蜂窝麻面、裂缝、飞边、掉角和保护层控制合格率低等质量缺陷,影响了梁板外观质量和梁板耐久性的要求。
四、现状调查
小组对前期预制的20片梁板存在的外观缺陷等问题的梁板数量进行的调查统计数据如下:
梁板预制质量情况调查统计表
序号
存在的问题
片数
发生频率(%)
备注
裂纹
光洁度
25
小气泡
35
蜂窝
20
麻面
模板错台
15
烂根
保护层
根据上表中的数据,绘制如下排列图
由上图可以看出,梁板预制质量存在缺陷的主要方面为光洁度、气泡、麻面等。
麻面蜂窝
裂纹光洁度不好
五、目标确定
(1)梁板预制质量目标
从上面的缺陷统计表可以看出,梁板以光洁度、气泡、蜂窝、麻面和保护层居多,占到问题的78%,小组成员经过对现场调查分析,精心安排,认真研究一致认为:
只要解决了光洁度、气泡、蜂窝、麻面和保护层这五个问题,梁板制作质量就会有很大提高。
确定目标为蜂窝、裂纹、烂根和保护层缺陷率不得高于5%,光洁度、小气泡和麻面等缺陷率不得高于10%。
目前比例与目标比例对比见下图表示。
(2)目标可行性分析
目标可行性分析图
(3)为使活动目标得以实现,我们制定了小组活动保证体系,见下图。
小组活动保证体系图
六、分析原因
小组成员对存在的这些质量缺陷,进行了认真的分析总结,详见下表:
存在缺陷原因分析
七、确定主要原因
原因一:
原材料的质量
我们QC小组认真调查了砼用砂、石、水泥、外加剂,包括拌合用水等原材料,以上材料全部由试验室进行了原材试验,部分试验项目也经外委单位检验,全部合格,同时前期都进行了砼配合比试验,砂石、水泥等后期进场原材料也都经过了原材检测,上报至上级部门经过了审批,所生产的梁板砼强度100%合格。
结论:
原材料质量可靠并可控,基本对砼外观质量没有影响或者是影响可以忽略不计,此项非主要因素。
原因二:
拌合站计量精度
通过查验拌合站计量设备的标定等一切证书全部符合要求,并通过实际放料称量进行拌合站计量设备的自校,均在误差范围之内,符合规范要求。
拌合站计量设备完全正常,精度符合要求,此项非主要因素。
原因三:
作业工人技术水平差,责任心不强,振捣不到位
对混凝土振捣过程中的下料方式,振动功率及振捣时间等参数的多次实验,发现掌握生产工艺参数对管片质量甚为重要。
试验情况
实验项目
预制质量
气泡
坍落度
160
√
140
-
×
120
下料
方式
一次
二次
三次
振捣
时间
5分钟
7分钟
10分钟
注:
上表中√表示较多;
-表示较少;
×
表示没有。
此项为主要原因
原因四:
模板清理不净,未抛光,脱模剂涂刷不到位
经过调查,由于模板清理不干净和漏涂脱模剂会出现光洁度不好、蜂窝、麻面等质量问题,经多次查验砼浇筑前模板抛光打磨程度,确实发现在模板未抛光的部位存在光洁度不好和蜂窝麻面的现象。
此项为主要因素
原因五:
班组自检未落实到位
由于作业人员文化程度低,质量意识不高,责任心不强,存在随意性,所以每道工序的施工必须经过严格的自检程序,自检过程中总能发现一些常忽略的晓得的细节方面的问题,往往就这些问题导致了砼外观方面出现缺陷,比如说麻面,模板错台和保护层的定位等。
此项是形成模板错台和保护层厚度的主要原因之一。
原因六:
洒水养护不及时
混凝土浇捣后,之所以能逐渐凝结硬化,主要是因为水泥水化作用的结果,而水化作用则需要适当的温度和湿度条件,因此为了保证混凝土有适宜的硬化条件,使其强度不断增长,必须对混凝土进行洒水养护。
大量的经验告诉我们,洒水不及时,水化热因水分不够,水化热不充分就会产生裂纹,目前已生产的梁板虽然砼强度都已经达到了设计的强度,但个别梁板由于养护不充分,产生了个别微小的裂纹,通过前期的养护条件发现如下的养护规律:
砼养护时间与裂纹产生的规律情况表
水养护方式
水养护时间
管片裂纹
覆盖喷水
14
21
上表中√表示有裂纹;
-表示较少裂纹;
表示没有裂纹。
从上表可以看出,砼在覆盖洒水养护7天以上,表面无裂纹,少于5天会产生不同程度的微小裂纹,故此项为引起砼表面裂纹的主要原因。
原因七:
砼浇筑间隔时间太长
在砼浇筑过程中应连续浇筑,中途不得进行间断,但由于某些突发情况,如停电、拌和设备故障等,或是由于浇筑过程出现意外情况需要临时暂停浇筑,待排除故障后再继续浇筑,如果间隔时间小于40min,并且能够在砼初凝之前继续浇筑,整体的浇筑质量不会受到太大影响,但会在砼表面隐约出现一条砼施工缝线;
如果时间间隔太长,超过了砼的初凝时间,那这种情况是决不允许的。
我项目部在拌合站配备了发电机,用来应付突然停电状况;
同时配备了备用拌合站,如果一台出现故障,短时间修理不好的话,及时启动备用站。
故此项因素可以忽略,非主要因素。
原因八:
砼拌制及运输
混凝土搅拌时间过短会造成拌合不均匀,减水剂没有完全反应,使混凝土坍落度控制不准,造成混凝土坍落度用水量偏大;
混凝土搅拌运输车运输距离和时间越长,混凝土熟料由于发生化学反应、自由水份减少,造成混凝土坍落度损失,混凝土现场就位、料斗下料还会造成砂浆损失,这也是造成混凝土坍落度损失和混凝土入模质量的重要原因。
拌合站采用自动计量拌和设备进行拌制砼,拌制时间电脑控制,严格按照砼配比试验进行;
预制场和拌合站相邻,运输距离不超300m,采用砼罐车运输,现场直接料斗入模,从出料到入模时间上不超过20分钟。
从砼的拌制和运输施工工艺上来看,对梁板预制的质量问题几乎没什么影响,故此项为非主要因素。
原因九:
作业人员经验不足
在对其他分部的走访和调查中发现,使用技术熟练、经验足的工人及技术人员,对梁板预制质量有很大的保证。
一些业务不熟练的劳务作业人员或是互相之间配合不默契,预制出来的梁板蜂窝麻面等小问题就比较多,整体光洁度不是很好,后对工人进行培训或引入熟练工人,梁板预制的质量有很大的提高。
原因十:
技术交底不到位,监管不到位
施工作业前,必须对作业班组及作业人员进行施工工艺的技术交底,并在施工过程中加强监管督促,严格按照技术交底实施,交底越详细越全面,效果越好,从组模、砼浇筑和拆模、覆盖养护整个施工过程中统一指挥,统一协调,既能加快施工进度,又能保证施工质量。
此项为主要因素。
我们QC小组经对以上分析进行统计后,确定影响梁板预制整体质量的主要因素如下:
1、作业工人水平差,责任心不强,振捣不到位
2、模板清理不净,未抛光,脱模剂涂刷不到位
3、班组自检未落实到位
4、洒水养护不及时
5、作业人员经验不足
6、技术交底不到位,监管不到位
八、根据原因制定解决措施
我们QC小组针对以上六项主要原因,召开会议,集体讨论,制定如下对策、方案:
QC小组制定的对策、方案表
要因
对策
目标
解决措施
更换水平高的作业人员并确定最佳的振捣方式
确定最佳生产工艺参数及振捣方式
更换有经验、水平高的作业人员,现场探讨共同确定振捣方式,同时加强监管督促
将模板清理干净,抛光符合要求,采用洁净的脱模剂进行涂刷
使砼面不出现或少出现麻面现象,整体光洁度符合外观要求
配备足够的抛光机,安排有经验和责任心的作业人员进行操作,抛光完后严格检查;
采用新机油和柴油按照比例掺配,并且涂刷均匀
加强自检,严格自检
每道工序完成后均满足规范及设计要求
配备富有责任心的技术及试验人员,每道工序进行自检,严格监理报验程序,不符合要求的坚决不予转序
洒水养护
不及时
优化场地布置,加大覆盖养生力度
保证充分养护,杜绝表面裂纹
优化场地布置,布设水管,购买足够的覆盖养生土工布,全过程覆盖,设置专人进行洒水养护,保证至少7天的养护时间
进行作业人员的培训
培养一批有经验的作业人员
请相关专业人员现场进行讲解,并在实践中验证,同时去其他分部进行现场观摩,学习别人好的经验,学习他们的优势同时找出存在的问题,对所有作业人员进行技术培训
岗前进行详细的技术交底
现场所有作业人员了解交底内容
制作详细的作业指导书和现场的技术交底及安全交底,组织开展技术交底讨论会
九、存在问题采取的预防措施
(一)光洁度、麻面
1、模板表面清理干净,脱模剂应涂刷均匀;
2、混凝土搅拌时间要适宜,一般应为1~2分钟;
3、浇筑混凝土时,无论那种模型,均需洒水湿润,但不得积水;
4、浇筑前检查模板拼缝,对可能漏浆的缝,设法封堵;
5、振捣遵循快插慢拔原则,振动棒插入到拔出时间控制在20S为佳,插入下层5-10㎝,振捣至混凝土表面平坦泛浆、不冒气泡、不显著下沉为止;
(二)蜂窝
1、浇筑前检查并嵌填模板拼缝以免浇筑过程中跑浆;
2、浇筑前浇水湿润模板以免混凝土的水分被模板吸去;
3、振捣工具的性能必须与混凝土的工作度相适应;
振捣工人必须按振捣要求精心振捣,尤其加强模板边角和结合部位的振捣;
4、混凝土拌制时间应足够、拌合均匀,坍落度适合;
混凝土下料高度超过过2m应设串筒或溜槽:
浇灌应分层下料,分层振捣,防止漏振:
模板缝应堵塞严密,浇灌中,应随时检查模板支撑情况防止漏浆;
(三)烂根
1、接缝处贴橡胶海绵条或土工布止浆,并用钢木压板、橡胶压条止浆;
2、拼缝两侧的振捣器起振时保持同步。
(四)裂纹
1、浇筑完混凝土6小时后开始养护,养护龄期为14天,前24小时内每2小时养护一次,24小时后按每4小时养护一次,用湿土工布覆盖,避免曝晒;
2、振捣密实而不离析,对板面进行二次抹压,以减少收缩量;
(五)气泡
气泡属麻面的范畴,也是常见的缺陷。
除不易排气泡的结构(如倒角等)外,形成气泡缺陷的原因常见的是浇筑分层厚度过大,气泡溢出表面的距离大,此时振捣稍有不足,便容易形成气泡。
同时,脱模剂的影响也不容忽视。
涂刷在模板表面的脱模剂(隔离剂)一般为油性,如脱模剂浓度过稠、涂刷厚度过大时,在表面张力的作用下,包裹混凝土内的气体吸附于模板表面,形成较难溢出仓外的气泡,在混凝土凝固后便成为气泡缺陷。
(六)模板错台
为避免混凝土表面出现错台、挂帘的现象,要求模板首先要有足够的刚度且边缘平整,对已经使用过的模板,安装前一定要进行校正。
其次是模板安装时,须保证模板间拼接紧密、支撑牢固,整体刚度足够。
特别需加强模板与老混凝土之间的紧固,因为这是错台的多发点。
如浇筑高度大,最好在上一仓拆模时保留最上一块模板,与新浇筑仓模板拼接。
同时,须注意混凝土浇筑过程的跟进工作,对模板受力后的变形实时监测,对变形模板及时调整。
当混凝土浇至1/3、1/2高度时,需对模板支撑件各紧固一次,待浇筑完成时再紧固一次,可有效防止错台、倒帘的现象发生。
(七)保护层
控制保护层的总体工作思路在严格控制钢筋及模板平面位置、几何尺寸的基础上控制钢筋与模板的距离,并使钢筋、模板及相应的固定设施(加密垫块、定位筋、模板固定支架及拉索)形成一个整体,在浇筑混凝土过程中避免破坏钢筋、模板的整体性,从而保证钢筋保护层厚度在控制范围内。
1、钢筋加工应严格按设计要求加工,主要钢筋采用数控弯箍机、数控弯曲机等机械设备加工,提高钢筋加工的精度及统一性。
2、钢筋绑扎、安装时应准确定位,采用钢筋定位架施工,确保符合设计要求图纸,无漏筋现象。
3、钢筋的保护层垫块应使用高强度砂浆垫块,梁底、翼板等部位采用梅花形垫块,并绑扎牢固可靠,确保每平方米垫块数量不少于4块;
腹板钢筋采用穿心式圆饼垫块,垫块规格不得私自改变;
翼缘梳形板外露钢筋的保护层控制要特别重视,采用可靠加固措施,确保钢筋位置准确且混凝土浇筑过程中不出现移位现象,必要时每根钢筋要固定牢靠;
横隔板、梁端预留孔位置必须准确,避免因模板预留孔位偏差太大,导致钢筋保护层厚度超标。
十、效果检查
梁板预制鉴于工期紧迫,在QC小组活动期间,预制生产过程也从未停止,自8月20日实施相应措施以来,至9月12日三周共计生产了42片梁,对梁板存在的外观缺陷等问题的梁板数量再次进行了统计数据如下:
2.4
11.9
9.5
4.8
7.1
从上图中可以看出,采取相应的改善措施后,存在缺陷比例的预制梁板的数量百分比明显下降了。
通过QC小组的共同努力,通过开展多次PDCA循环,梁板预制质量改善前和改善后有了明显的提升,除了光洁度上没能达到目标值,其余几项缺陷率都控制在了目标范围之内,QC小组活动取得了阶段性的成绩,对于改善梁板预制质量起了推动性的作用。
十一、总结
在QC小组全体成员的共同努力下,本次活动不但实现了预期目标,提高了生产质量,而且使项目部技术人员的质量意识、改进意识、参与意识都得到了很大提高,也使小组成员的个人能力得到了提高,增强了解决问题的信心,更让人感到了团队的巨大力量。
通过活动,在项目部内部形成了一股技术比武、争做标兵的良好风气。
通过QC活动解决了梁板预制外观缺陷,不但节约了大量了修补费用,同时也为公司在社会上赢的了好的信誉,为以后我公司在类似领域市场奠定了坚实的基础,我部预制的梁板质量多次受到驻地办、总监办及业主的一致好评。
QC小组下一步准备继续对梁板预制中光洁度控制攻关,使外观质量更上一层楼。