热处理工艺复习题docx.docx
《热处理工艺复习题docx.docx》由会员分享,可在线阅读,更多相关《热处理工艺复习题docx.docx(18页珍藏版)》请在冰豆网上搜索。
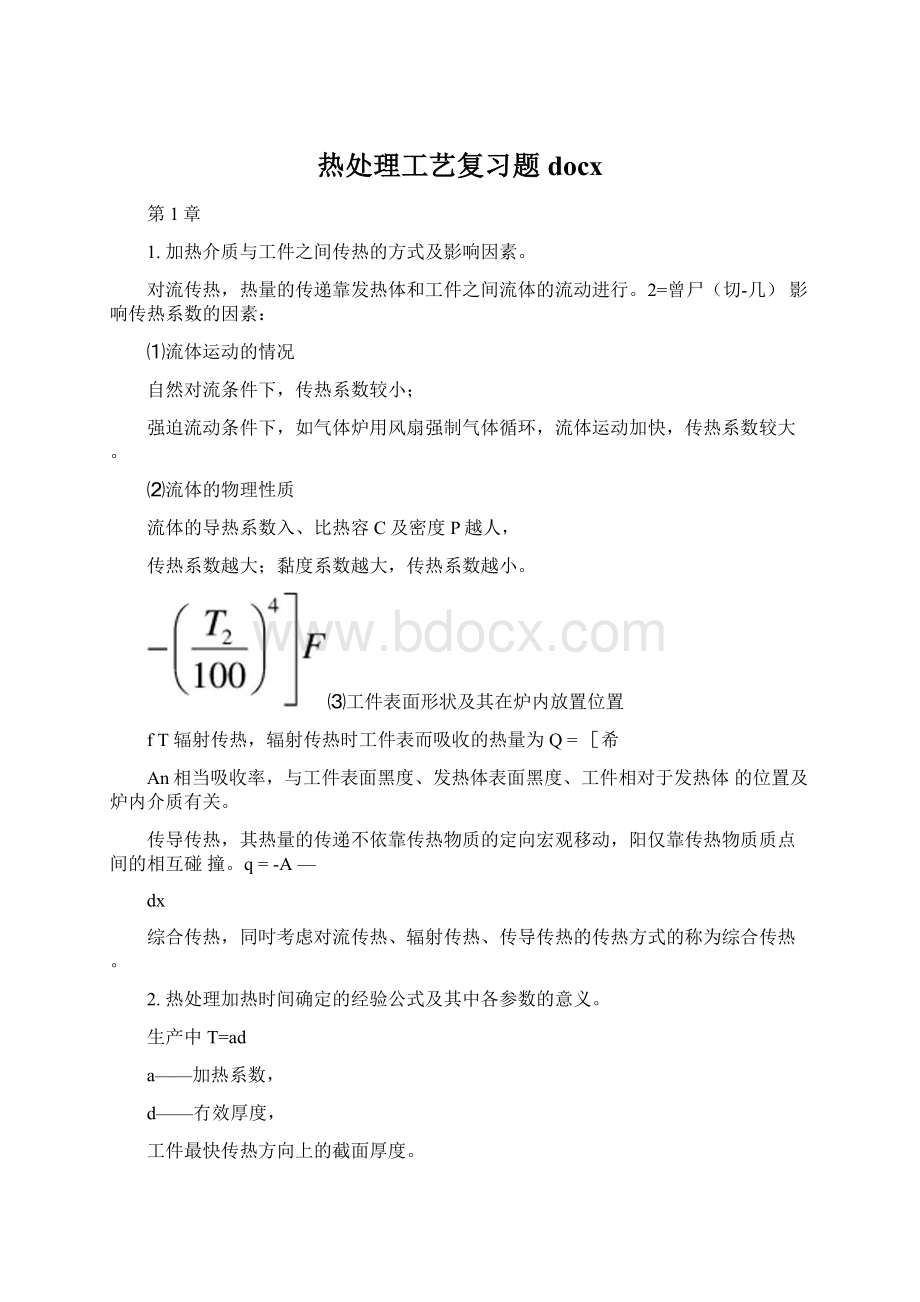
热处理工艺复习题docx
第1章
1.加热介质与工件之间传热的方式及影响因素。
对流传热,热量的传递靠发热体和工件之间流体的流动进行。
2=曾尸(切-几)影响传热系数的因素:
⑴流体运动的情况
自然对流条件下,传热系数较小;
强迫流动条件下,如气体炉用风扇强制气体循环,流体运动加快,传热系数较大。
⑵流体的物理性质
流体的导热系数入、比热容C及密度P越人,
传热系数越大;黏度系数越大,传热系数越小。
⑶工件表面形状及其在炉内放置位置
fT辐射传热,辐射传热时工件表而吸收的热量为Q=[希
An相当吸收率,与工件表面黑度、发热体表面黑度、工件相对于发热体的位置及炉内介质有关。
传导传热,其热量的传递不依靠传热物质的定向宏观移动,阳仅靠传热物质质点间的相互碰撞。
q=-A—
dx
综合传热,同吋考虑对流传热、辐射传热、传导传热的传热方式的称为综合传热。
2.热处理加热时间确定的经验公式及其中各参数的意义。
生产中T=ad
a——加热系数,
d——冇效厚度,
工件最快传热方向上的截面厚度。
3.影响热处理加热速度的因素。
1加热方式的影响
随炉加热(冷装炉)
特点:
装炉虽大,加热速度缓慢,表面与心部的温差AT小。
应用:
人型铸锻件、高合金钢、形状复杂,工件如大型轧辘等,生产率低。
到温装炉(热装炉)
特点:
加热速度t,温差f,生产率t
应用:
如化学热处理、淬火、正火、回火等。
预热加热
特点:
加热速度较冷装炉t,AT小。
应用:
大型铸锻件、较大截血的高合金,工貝钢模具钢淬火加热。
高温装炉
特点:
炉温比正常加热温度高100^200°C,强化加热,加热速度ft,表面与心部温差f
t,生产率t
应用:
锻件退火、正火、碳钢、低合金钢淬火等。
2加热介质及工件放置方式的影响(影响a的因索)
⑴加热介质的影响
1固体介质木炭、石墨、氧化铝、石英砂等
流态化炉加热特点:
以対流为主的综合传热,传热系数t,加热效率ttO
2液态介质熔盐、金属、油等。
热传导为主,兼有辐射和对流,加热速度快,温度均匀,表面氧化、脱碳倾向小,变形较小。
3气体介质小加热。
综合传热高温区以辐射为主,低于600°C以对流为主,屮温区混合作用。
4真空加热,为辐射传热,加热速度慢,工件变形小,无氧化脱碳,保持表面原始状态,
清洁光亮
⑵工件在炉内排布方式的影响。
工件在炉内排布方式肯接影响热量传递的通道,例如辐射传热中的挡热现象及对流传热中影响气流运动的情况等。
⑶工件本身的影响。
工件本身的几何形状、工件表面积与体积Z比已经工件材料的物理性质(C,2,卩等)直接影响工件内部的热量传递及温度场。
4.钢在氧化性介质中加热时的氧化反应及无氧化加热条件。
(P13)
5.何谓碳势?
如何根据实际碳势曲线确定炉气碳势
碳势:
即纯铁在一定温度卜•于加热炉气屮加热时达到既不增碳也不脱碳,并与炉气保持平衡时表而的含碳量。
获得了实际碳势曲线以后,即可通过测定炉气成分来确定炉气碳势。
吸热式气氛中,影响碳势的主要气体成分是CO、H2、C02、H20和CH4,在C0和H2成分恒定情况下,只要测定C02、H20和CH4之一的含量,气体成分即可确定,从而碳势也随之确定。
(1)温度一定时,炉气中C02含量越高,碳势越低。
炉气一定时,随温度升高,碳势降低。
(2)气M+H20含量越高,露点越高,碳势越低。
6.如何根据炉气碳势、加热温度及钢的含碳量确定钢脱碳层的组织。
(P18)
脱碳过程:
表面的碳与炉气反应,表面碳浓度降低;表面打内部形成碳浓度梯度,内部的碳向表面扩散。
第2章
1•各种退火工艺(扩散退火、完全退火、球化退火、等温退火、再结晶退火、低温退火)的目的、工艺特点、适用材料及组织。
退火——将钢加热到>Ac3(Accm)或Ac广Ac3(Accm)或温度,保温一定时间,缓冷,以得到接近平衡组织的热处理工艺。
目的:
1)改善组织缺陷,消除粗人品粒、魏氏组织铁素体、网状渗碳体、带状组织,细化品粒、均匀成分、消除冷热加工内应力等;
2)为切削加工、淬火作纽织准备;
3)某些零件的最后热处理
(1)扩散退火(或均匀化退火)
目的:
消除或者减少化学成分偏析及显微组织(枝品)的不均匀性,以达到均匀化的目的。
温度:
Ac3(或Accm)+(150-300)°C,一般为碳钢1100-1200°C,合金钢1200-1300°C保温时间:
一般以每25mm截面厚度30-60min算。
特点:
温度高、时间长,成木和能耗高,效率低,对于钢屮宏观偏析和夹杂物分布基木上不起作用。
应用:
优质合金钢铸锻件及偏析较严重的合金钢
示续工艺:
正火或退火消除晶粒粗人
(2)完全退火
目的:
细化品粒、降低硬度、改善切削性能、消除内应力等。
温度:
Ac3+(20-30)°C,适用于0.3-0.6C%中碳钢铸锻件。
低碳钢:
(960-1100)°C,高温退火,获得4—6级晶粒度,提高切削性能
过共析钢〉Accm加热后缓冷一P+网状Fe3C——不采用完全退火工艺
常用结构钢、弹簧钢和热作模具钢钢锭:
加热速度:
100-200°C/h,保温时间:
t=8.5+》4h亚共析钢锻轧钢材:
主要消除锻后组织及更度的不均匀性,改善切削加工性能和为后续热处理做准备。
保温时间:
t=(3-4)+(0.4-0.5)Qh
(3)不完全退火
目的:
消除热加工的内应力,降低硬度,改善切削加T•性
加热温度:
AcPAc3(Accm)
特点:
由于加热温度在Acl"Ac3(Acm)之间,不完全奥氏体化——部分重结晶,第二相形态、分布仍保留。
因此不能消除热加工组织缺陷、细化晶粒等。
应用:
终轧(锻)温度不高,原始组织细小的亚过共析钢(合金钢)锻件和热轧件,代替完全退火,降低成本。
(4)球化退火(过共析钢的不完全退火)
冃的:
降低硕度,改善切削加丄性;获得均匀组织,改善热处理丄艺性能,为淬火做好准备;经淬火、回火后获得良好的综合机械性能。
由奥氏体转变为球化体的退火工艺有以下三种:
1一次球化退火法:
加热到Acl以上20°C左右,然后以10-20°C/h的速度控制冷却到Ari以下一定温度;
特点:
退火时间长,炉冷速度不易控制
2等温球化退火:
加热Acl以上20°C左右,然后在略低于A1的温度下等温;
特点:
奥氏体在较高温度下分解,碳化物质点的聚集和球化的过程加快。
3往复球化退火:
在A1上、下20°C左右交替保温。
特点:
球化较充分,周期较短,但在操作和控制上比较繁琐。
(5)等温退火
目的:
对完全退火、球化退火的改造,缩短工艺时间,提高生产率,防止白点等。
等温退火适用于合金钢、高合金钢、高碳钢等需要退火降低硬度的工件。
(6)再结晶退火
再结晶退火:
经过冷变形后的金属加热到再结晶温度之上,保持适当时间,使形变晶粒重新转变为均匀的等轴晶粒,以消除加工皎化和残余应力的热处理工艺。
冃的:
消除加工硬化,提高延展性(塑性),改善切削性能及压延成型性能。
(7)消除应力退火(或低温退火)
冃的:
消除铸锻零件、悍接件、机加工件的内应力
加热温度随材料选择500^700°C。
加热时间:
2~8h。
加热、冷却速度:
50〜150°C/h
2•正火的工艺、目的。
正火工艺:
正火是将钢加热到Ac3或Accm以上30〜50°C保温,然示空冷的热处理工艺。
正火口的:
可以细化晶粒,使组织均匀化,获得一定的硬度,改善铸件的组织和低碳钢的切削加工性;可以作为预备热处理,为随后的热处理作准备;也可作为最终热处理。
1低碳钢正火的目的之一是为了提高切削性能。
2中碳钢正火应该根据钢的成分和工件尺寸来确定冷却方式。
3组织中冇网状碳化物的高碳钢,止火是为了消除网状碳化物,加热时必须保证碳化物全部溶入奥氏体中,冷却时须采用较大冷速,可抑制碳化物的析出,获得伪共析组织。
4双垂」I•:
火。
冇些锻件的过热组织或铸件粗大铸造组织,一次止火不能达到细化组织的冃的。
为此采川二次正火,可获得良好的结果。
表4.5退火和正火的热处理工艺
3
理掠蜒艺諛工
理的处目
相应
组织
的七
0变
*13
・退火扩散(均匀化)
泯子晶化髙原枝匀
5鬻間树大砂快+F析粗锂玖P+共
完全退火等温退火
•至保以加50处钢~至碳30m冷箱上期空砂以随炉
C3UU
P」
共钢等並金件一——j丨‘—「L
制証性瑟率控岀和短产确度织缩生准冷组大髙
同5火
i
\7
完連
同化
M*4.5
理的处目
应织相组
■
球化退火
基分状
F旳粒
焉着>
PM体布G
1————」
低闷擀热
度但好过
apt性易
■T
很温〉退火去勞
至炉炉热随出"■眦砒保20
5500眄常
才的同
再结聶退火
fJ
「■4・■■经热g温将加200室
为W
著显显明度性强降提
形B
正火(常化)
ta上在钢以后
钵A温纯处gT冷(«a50中亚至~气将熔30空
瞅析析V如J共stx亚F+聘杯
L询!
;曲酣啲低金3零理中
3.退火、正火缺陷的种类、形成原因、消除方法。
(P31)
1.过烧:
由于加热温度过高,出现晶界严重氧化,英至局部熔化,造成工件报废。
2.黑脆:
碳素工具钢或低合金工具钢在退火后,有时发现硬度虽然很低,但脆性却很大,一折即断,断口呈灰黑色,所以叫'‘黑脆”。
3.粗大魏氏组织
4.反常组织
5.网状组织
6.球化不均匀
7.硬度过高第3章
1.理想的淬火冷却介质的冷却特性o
在过冷奥氏体最不稳定区域,即珠光体转变区,具有较快的冷却速度,而在MS点附近的温度区域冷却速度比较慢,它可以减少淬火过程中所产生的内应力,避免淬火变形、开裂的产生。
2.有物态变化的淬火介质的冷却过程大致可分为哪几个阶段?
r汽膜阶段
冷却过程大致可分为*沸腾阶段
I对流阶段
(1)气膜阶段:
当工件进入介质的一瞬间,周围介质立即被加热而汽化,在工件表面形成-层蒸汽膜,将工件少液体介质隔绝。
由于蒸汽膜的导热性较差,故便工件的冷却速度较慢。
(2)沸腾阶段:
当蒸汽膜破裂后,工件即与介质直接接触,介质在工件表血激烈沸腾,通过
介质的汽化并不断逸出气泡而带走了大量热量,使冷却速度变快.
(3)对流阶段:
当工件冷至低于介质的沸点时,则主要依靠对流传热方式进行冷却,这时工
件的冷速甚至比蒸汽膜阶段还要缓慢。
3.淬火烈度及淬火烈度H的测量.
淬火介质冷却能力最常用的表示方法是所谓的淬火烈度规定18°C静止水的淬火烈度11=
1,其它淬火介质的淬火烈度由与静止水的冷却能力比较而得。
淬火介质冷却特性的测量银球探头法(P37)
淬火特性温度是指蒸汽膜破裂即沸腾阶段开始的温度
4.几种常用的淬火介质(水、盐水与碱水、淬火油)各有何特点?
(1)水在静止与流动状态下的冷却特性,静止水的蒸汽膜阶段温度较高,在800〜380°C温度范围,此阶段的冷速缓慢,约180°C/s.温度低于380°C以下才进入沸腾阶段,使冷却速度急剧上升,280°C左右冷速达最大值,约770°C/s.
水作为淬火介质的主要缺点:
1冷却能力对水温的变化很敏感水温升高,冷却能力便急剧卜-降,并使对应于最大冷速的温度移向低温;
2在马氏体转变区的冷速太大,易使工件严重变形甚至开裂;
3不溶或微溶杂质(如汕、