浅谈75th循环流化床锅炉能量系统优化文档格式.docx
《浅谈75th循环流化床锅炉能量系统优化文档格式.docx》由会员分享,可在线阅读,更多相关《浅谈75th循环流化床锅炉能量系统优化文档格式.docx(14页珍藏版)》请在冰豆网上搜索。
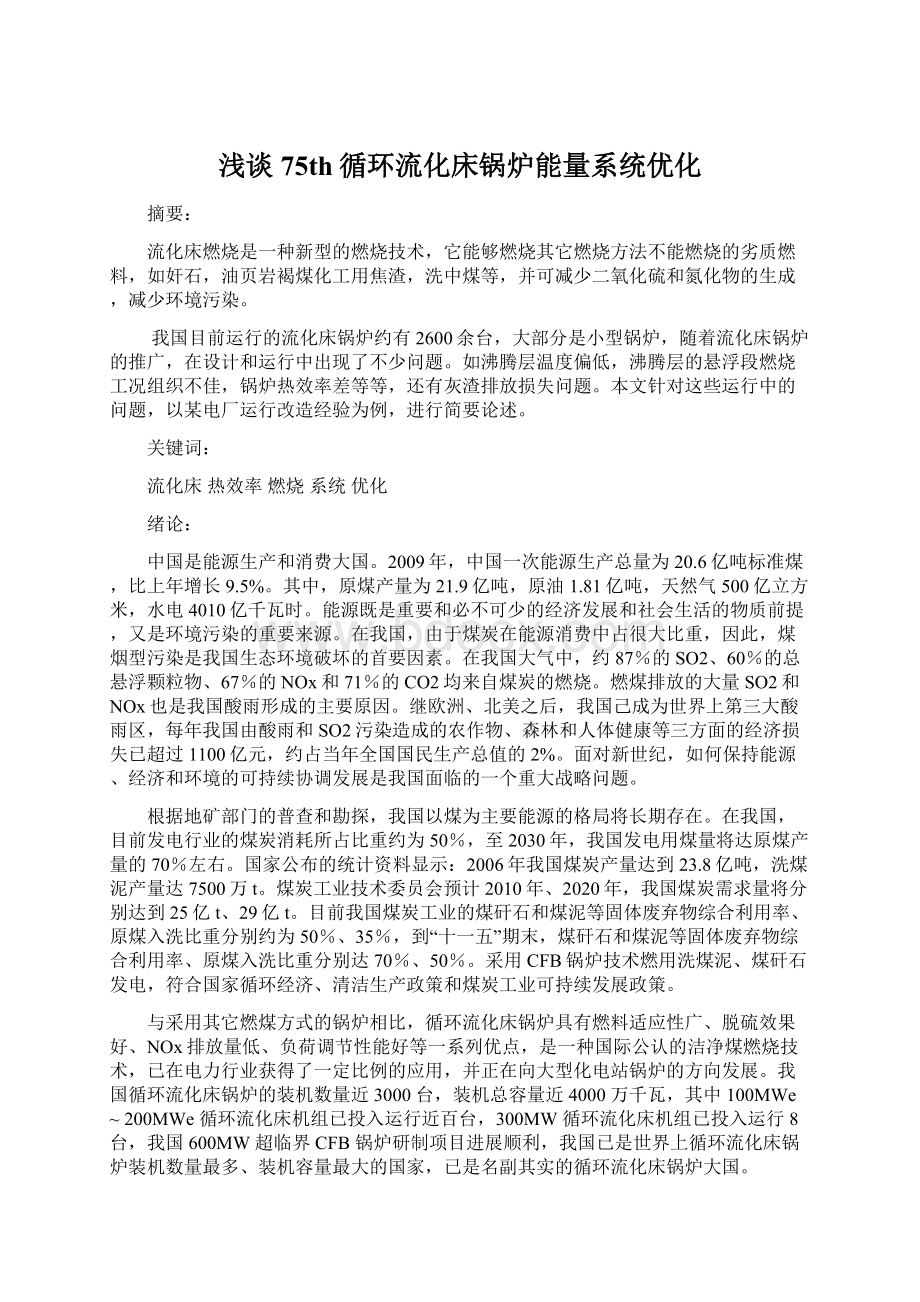
2006年我国煤炭产量达到23.8亿吨,洗煤泥产量达7500万t。
煤炭工业技术委员会预计2010年、2020年,我国煤炭需求量将分别达到25亿t、29亿t。
目前我国煤炭工业的煤矸石和煤泥等固体废弃物综合利用率、原煤入洗比重分别约为50%、35%,到“十一五”期末,煤矸石和煤泥等固体废弃物综合利用率、原煤入洗比重分别达70%、50%。
采用CFB锅炉技术燃用洗煤泥、煤矸石发电,符合国家循环经济、清洁生产政策和煤炭工业可持续发展政策。
与采用其它燃煤方式的锅炉相比,循环流化床锅炉具有燃料适应性广、脱硫效果好、NOx排放量低、负荷调节性能好等一系列优点,是一种国际公认的洁净煤燃烧技术,已在电力行业获得了一定比例的应用,并正在向大型化电站锅炉的方向发展。
我国循环流化床锅炉的装机数量近3000台,装机总容量近4000万千瓦,其中100MWe~200MWe循环流化床机组已投入运行近百台,300MW循环流化床机组已投入运行8台,我国600MW超临界CFB锅炉研制项目进展顺利,我国已是世界上循环流化床锅炉装机数量最多、装机容量最大的国家,已是名副其实的循环流化床锅炉大国。
由于种种原因,目前我国CFB锅炉的使用现状还不很乐观:
在脱硫系统的热效率、脱硫效率等方面还存在不少问题,离国际先进水平有一定差距。
如何针对各种存在的问题加以解决,值得研究和实践。
正文:
循环流化床技术由于其煤种适应性和在低成本污染物排放控制等优点,已成为很有潜力的一种洁净煤技术。
中国早在上个世纪八十年代即已开始发展CFB锅炉,至今CFB锅炉应用技术已逐步成熟。
绝大多数小型CFB锅炉(35~130t/h)采用中国自己的技术,超过220t/h的CFB锅炉则是引进国外技术。
一般认为,CFB锅炉具有很高的燃烧效率,但在中国,许多燃烧硬煤如烟煤和无烟煤以及废弃物等的CFB锅炉的实际飞灰含碳量很高,锅炉热效率远远低于预测和设计值。
高飞灰含碳量使得CFB锅炉的市场竞争力下降。
另外,锅炉飞灰可用作建筑材料,部分替代水泥或用于制造水泥,这是飞灰最具经济价值的应用。
飞灰含碳量过高将限制其在水泥和建筑行业的应用。
含碳量很高的飞灰曾被用作燃料来制砖。
但是这种季节性的砖生产只能部分消化源源不断地从CFB锅炉中排出的高含碳飞灰,并且近年来砖生产迅速减缩并被新建材替代。
另一方面,飞灰填埋成本也在上长。
因此处理CFB锅炉飞灰的最好办法是提高锅炉热效率、减少含碳量,使得建筑和水泥工业能够接受,这一问题俨然成为小电厂亟待解决的一个棘手问题。
本文将针对如何提高锅炉效率,降低锅炉飞灰含碳量提出一些建议。
循环流化床锅炉是在常规流化床锅炉的基础上加上飞灰循环燃烧而发展起来的。
因此要了解什么是循环流化床锅炉必须先了解什么是流化床锅炉,从固体粒子流态化过程来看,从固定床(煤粒在炉蓖上静止不动,即层燃炉)开始,随着风量的增加,即空筒流速(通常叫表观流速或流化速度)的增加→细粒在煤层表面流化,是为细粒流态化→炉蓖上开始产生气包,是称鼓泡流态化(即常规流化床,又名鼓泡流化床或沸腾床,此时的沸腾床有明显的上界面)→湍流流态化(湍流流化床,此时气泡变细狭窄状,波动振幅增大,上界面已不甚清楚)→快速流态化(高速流化床,此时的流化床内已无气泡,也无上界面,颗粒聚合成絮团状粒子束,粒子束不断形成与解体,形成强烈的固体返混,此时煤粒与气流的相对速度达最大,因此大大强化了燃烧与传热)→气力输送(即煤粉燃烧,此时煤粉与气流间的相对速度近于零,即已无相对速度)。
经典的循环流化床锅炉的炉内流态化工况应为高速流化床工况,故严格而言,循环流化床锅炉不仅是在炉膛出口处加一个分离器收集部分飞灰返回炉膛燃烧而已,而是其炉内流态化工况应属于高速流化床工况,但实际存在的循环流化床其下部浓相区为鼓泡流化床或湍流床,上部稀相区为高速流化床。
但国内有相当数目的流化床锅炉仅是在鼓泡流化床炉膛出口加一个分离器收集部分飞灰返回炉膛燃烧(即其上部稀相区未达高速流化床工况),现也称为循环床。
循环流化床锅炉的优缺点:
1、循环流化床锅炉优点:
1.1、燃料适应性广——几乎可燃用各种优、劣质燃料。
如优、劣质烟煤(包括高硫煤),无烟煤,泥煤,煤泥,矸石,炉渣,油焦,焦炭,生活垃圾,生物质废物等等。
1.2、燃烧效率高——对无烟煤可达97%,对其他煤可达98~99.5%,可与煤粉燃烧相竞争。
1.3、环保性能好
1.3.1、炉内可直接加石灰石脱硫,本钱低,脱硫效率高,当Ca/S比为1.5~2.5时,脱硫效率可达85%~90%,石灰石循环利用,其利用率比常规流化床进步近一倍。
1.3.2、分段送风,低温燃烧,NOx排放量低(~120ppm),即为煤粉炉排放量的1/3~1/4。
1.4、燃烧强度高,床面积小,给煤点少,利于大型化。
1.5、负荷调节范围大(110~25%),调节速度可快,利于调峰。
也可压火。
1.6、燃料仅需破碎到10mm以下,无需磨煤制粉系统。
1.7、灰渣可综合利用,减少环境污染。
因其低温燃烧,灰渣可保持活性,可制作水泥,提炼稀有金属(硒、锗)等。
2、循环流化床锅炉缺点:
2.1、高循环倍率流化床锅炉的炉膛高大,初投资大。
2.2、分离循环系统复杂,自身电耗大。
2.3、循环灰浓度大,受热面磨损大等。
我国在上世纪80年代初开始研究开发循环流化床燃烧技术,与西方国家不同,原我国发展循环流化床锅炉的主要目的是解决劣质煤的应用题目。
近年来,我国环保要求日益严格,再加上煤价上涨,煤质变化大,大量中、小型(130t/h以下)层燃炉与煤粉炉要求进行技术改造等原因,大大地促进了循环流化床锅炉技术的发展。
循环流化床锅炉已成为目前产业锅炉、中、小型热电厂及大型电站的优选技术之一。
上世纪80年代以来,我国循环流化床锅炉数目和单台容量逐渐增加,几乎D级以上的锅炉厂无一不在生产循环流化床锅炉。
容量从4、6、8、10、12、15、20、25、30、35、50、65、75、90、130、220、400、410到670吨/时。
据不完全统计,现有2600余台35~670吨/时循环流化床锅炉在运行、安装、制造或订货。
均匀单台炉容量从37.40吨/时上升到106.80吨/时,蒸汽参数从低压、次中压、中压、高压到超高压。
有关研究机关和高校正在研制、开发超临界参数的600~800MW的循环流化床锅炉,来满足我国大型电站的迫切需求。
已投入运行的2600余台循环流化床锅炉,其中大于410吨/时的100余台,无论总容量或台数均已超过了除我国以外的全世界循环流化床锅炉的总和。
但是,目前的循环流化床锅炉派系林立,种类繁多,热效率参差不齐,高的达到88%—90%,低的不到65%,飞灰含碳量高的40%以上,低的不到5%,稳定运行周期不确定,有的能连续运行3000小时以上,有的不到200小时,送风机的电耗,高的达到12kWH/吨汽,低的不足6kWH/吨汽,有的厂家新上或改造为循环流化床锅炉后,给企业带到了巨大的经济效益,有的企业新上或改造循环流化床锅炉后带来了灾难性的损失分析原因,主要有以下几个方面:
1、热效率问题:
进步的循环流化床锅炉热效率必须满足三大基本条件:
一是有足够的有效容积,二是分离效率,三是分离返料温度。
1.1、有效容积:
有效容积是炉膛边界范围以内燃料燃烧及有效辐射传热的空间容积。
布风板小孔中心线至炉膛出口中心线的容积为炉膛容积,炉膛容积与烟气在炉膛内的停留时间有一定的关系,假如1吨蒸汽炉膛容积为1m3,则对应的烟气停留时间约为0.7s。
对于烟煤来说,850℃以上的炉膛容积为有效容积,对于无烟煤来说,930℃以上的容积为有效容积。
要想进步锅炉效率,对于烟煤来说,有效容积要大于5.5m3/吨汽以上,对于无烟煤来说,有效容积要大于6m3/吨汽以上。
各类型的循环流化床锅炉,烟气在炉内的停留时间不一样,有的不到2秒,有的5秒以上,换句话说,炉内的有效容积(即燃用烟煤850℃以上的容积,燃用无烟煤930℃以上的容积)有的不足3m3/吨汽,有的高达5.5m3/吨汽以上,固然有的容积高达5m3/吨汽以上,但炉内温度偏低,有效容积太小,有部分锅炉的过热器为屏式的,占用了大部分容积,且炉膛温度过高,导致过热蒸汽温度超温,为保证过热器温度,不得不牺牲炉膛有效容积。
另外,由于小于0.1mm的煤粒,相当部分分离器无法捕捉下来,只有靠一次性在炉内燃烬,而炉膛有效容积太小,细灰在炉内难以燃烬,导致热效率低,飞灰含碳量高。
炉膛有效容积除设计原因外,燃用煤种也可以导致有效容积的变化,当<
1mm的煤粒增多时,悬浮段温度过高,密相区的温度偏低,当<
1mm的煤粒过少时,悬浮段温度偏低,也导致炉膛有效容积减少。
对于高速床而言,炉内温度主要靠循环量来调节,因此,煤的颗粒变化对高速床影响较小,对低速床影响较大。
1.2、分离器的位置及分离效率:
高温分离器分离下来的飞灰直接进进炉膛,易着火燃烬,但高温分离器材质要求高,中温分离器材质易解决,但对燃烬不利。
分离器的效率也直接影响了热效率。
分离器的效率高,但阻力大,电耗高。
如何平衡考虑,也是循环流化床的一个设计题目。
惯性分离器如平面流、百叶窗、槽型分离器,结构简单阻力小,但一般来说分离效率不到40%,离心分离器如旋风上排气,旋风下排气,旋风多管分离器结构复杂,阻力大,一般为800—1000Pa,但分离效率都在95%以上。
1.3、飞灰燃烬问题:
碳的燃烬必须具备三个条件:
充分的氧进行反应、温度和停留时间。
固然有了足够的有效容积,延长了停留时间,有相应的温度,但在飞灰燃烬过程中,由于碳粒子四周形成了一定的灰壳,外面的氧很难与碳粒子接触发生反应,同样使得难以燃烬,因此,在有效容积的范围内,必须有气流扰动,打破其灰壳,才能使得碳与氧发生良好的反应,如具有旋风高温分离的流化床,由于气流的旋转,切向运动切割,打破了灰壳,碳粒子能很好的与氧接触发生反应,所以飞灰含碳量低。
在有效容积范围内,没有气流扰动的,尽管有足够的温度与时间,飞灰含碳量也难以下降到极限。
2、负荷问题:
锅炉负荷就是指单位时间产生蒸汽的能力.比如用锅炉蒸汽来驱动汽轮机,汽轮机用来对外做功.这样实际上就是锅炉在做功,单位时间做功越多则说明锅炉负荷大,反之则小。
低速床的埋管受热量的吸热量占了整个蒸发吸热量的40%,所以,带埋管的低速床只要各参数如炉膛各截面的温度达到设计要求,负荷一般都能保证,并具有一定的超负荷能力。
对于高速床而言,由于整个蒸发受热面,主要靠炉内辐射,它的传热系数一是靠炉内的温度,二是靠飞灰的浓度,温度高,传热系数大,负荷高。
假如燃用低热值的燃料(发热量在2000大卡/公斤以下)时,为了维持高温,必须覆盖一部分受热面。
这样,固然进步了传热系数,但减少受热面,炉膛必须有相当大的空间,否则难以达到满负荷。
现也有人在炉膛出口增设对流管,来增加受热面,达到满负荷的目的,这也是一个可取的办法。
另一方面,假如煤的灰分在20%以下时,发热量高,但由于灰量少,循环量少,也直接影响了传热系数,使之负荷下降。
3、磨损问题:
高速床固然没有严格的稀相区与密相区之分,但下面颗粒粗、飞灰浓度大、流化速度高、循环倍率高,磨损严重。
低速床有明显的稀相区与密相区之分,密相区的磨损比稀相区严重。
总的来说,高速床磨损比低速床明显严重。
高速床没有埋管,不存在埋管磨损,但水冷壁管磨损严重。
低速床有埋管,但只要控制好穿过埋管的烟气流速,并采取有效的防磨措施,就可以保证其寿命达到4年以上。
过热器、省煤器主要靠公道选择烟气流速,如烟气流速选择适当,过热器寿命可大于10年,省煤器寿命可大于5年。
分离器在过热器之前,过热器磨损较轻,否则,磨损加剧。
另一方面,要特别留意烟气偏流题目,即使烟气流速选择合适,但由于烟气偏流,造成局部流速过高,也同样会影响过热器、省煤器的寿命。
下面就针对循环流化床锅炉的以上问题进行研究,如何有效提高锅炉效率:
1、提高热效率措施:
1.1、提高锅炉有效容积:
将锅炉后墙后移,采用高低混合流速结构,增大炉膛的容积,炉内受热面通过卫燃带调节,使各部位的温差控制在50度以内,整个炉膛温度都在900℃以上,整个容积都是有效容积,总有效容积可以达到435m3,吨气有效容积5.8m3,按900℃计算,烟气停留时间进步到4.1s,使分离器不能分离的粒径小于80μm煤粉颗粒通过炉膛时一次性燃烧完全,有效降低了飞灰的含碳量。
1.2、提高分离器的分离效率和分离返料温度:
1.2.1、旋风分离器工作原理及飞灰分离特性:
图1-1旋风分离器工作原理图1-2旋风分离器飞灰分离特性
图1-1及图1-2示意了常规旋风分离器及其工作原理。
含固体颗粒的气体切向进入分离器,受筒壁结构的影响,含尘气体被迫在排气管和分离器外壁之间的同心环柱体内作旋转运动。
在旋转过程中,离心力将固体颗粒甩向分离器内壁面,在气流和重力共同作用下下落,由分离器下部的排灰管收集。
绝大部分气体则在旋转的同时沿分离器外壁螺旋向下运动,在分离器下部的锥段,气体带着少量颗粒进入内部区域,改为旋转向上的运动,由排气管排出。
旋风分离效率的变化将对炉膛床料粒度、底渣粒度、燃料停留时间、飞灰和底渣排出比例以及对整个锅炉的经济性产生影响。
因煤泥在燃烧过程中产生的飞灰较细,如需要提高循环倍率、降低飞灰含碳量,必须对旋风分离器进行优化,以提高小颗粒飞灰的分离效率,增加燃烧在炉内的停留时间;
同时,因炉内颗粒浓度增加,传热系数增大,提高锅炉的热效率。
以某电厂旋风分离器改造为例,旋风分离器改造目的是,改善该公司3台以煤泥为原料的75t/h循环流化床锅炉,投运以来存在燃烧不充分、锅炉效率偏低、飞灰含碳量高等问题。
1.2.2、优化及提高分离效率有以下几种途径:
1.2.2.1、提高气体进口风速
气体进口风速越高,分离效率越高,但运行阻力也越大。
一般气体进口风速为15-25m/s,最高不超过35m/s。
1.2.2.2、调整气体进口高宽比
气体进口风速一定时,气体进口高宽比增加,分离效率会增加。
一般气体进口高度/气体进口宽度取2-3。
1.2.2.3、进气方式调整为蜗壳式
气体进口形式主要有切向和蜗壳两种。
切向进口简单;
蜗壳进口结构上复杂一些,但有助于提高分离效率和减小阻力损失。
1.2.2.4、调整中心筒的长度、直径
中心筒直径越小,分离效率越高,但运行阻力也越大。
中心筒插入深度过短过长都不利于分离。
中心筒尺寸的选择需要根据飞灰的粒径分布及分离器的设计尺寸进行计算,以优化分离效率。
1.2.2.5、偏置中心筒
根据浓相流场流动特性,将中心筒偏移中心位置,致使烟气中的颗粒浓度降低,提高分离器的分离效率。
1.2.3、某电厂改造后的效果对比:
表1-1锅炉燃烧系统改造前、后能耗指标情况
时间段
项目
项目实施前
2007年
项目实施后
2009年
矸石消耗量(t)
146764.00
162521.00
煤泥消耗量(t)
99760.00
95516.00
脏杂煤消耗量(t)
33178.00
折标总量(t)
109269.22
96706.20
发电量(万kWh)
25718.10
25140.92
发电标煤耗(g/kWh)
424.87
384.66
产汽量(t)
1038228.34
1029690.50
锅炉热效率(%)
81.3
89.8
通过对分离器进行优化改进,分离器阻力降为400Pa—700Pa,分离效率高达99%以上,分离温度高达950℃以上。
旋转烟气的扰动打破了灰包碳结构,烟气与循环灰强烈的混合使分离内燃烧在较低氧浓度的情况下也十分强烈,促进飞灰的燃尽,降低飞灰的含碳量。
又是高温返料,返料温度高达850—950℃,有利于飞灰燃烬。
循环倍率为5-7,热效率高达90%以上,飞灰含碳量可降至5%以下。
2、改善负荷的措施:
2.1、采用高低混合流速循环流化床技术,下部布置埋管,埋管的吸热量是整个蒸发吸热量的40%以上,所以在燃用低热值燃料时,也可使锅炉的出力能够达到满负荷,并有一定的超负荷能力。
在进炉煤低位发热量比设计煤种低位发热量下降500Kcal/kg,上浮1500Kcal/kg的范围内,都可以保证锅炉满负荷经济稳定运行,各参数符合运行要求,并保证有10%以上的超负荷能力。
2.2、采用底饲回燃技术:
2.2.1、底饲回燃技术特点和工作原理:
图1-3底饲回燃工作原理
如图1-3所示,它由1底饲喷嘴、2耐磨弯头、3疏堵装置、4飞灰分离装置、5飞灰给料装置、6输送气源和7喷射装置等组成一套稳定、可靠、易于调节的飞灰气力输送系统。
和通常采用的将分离飞灰在床面送回炉内(即所谓“面饲回燃”)不同,“面饲回燃”将分离器分离灰送回炉内循环多次,虽然表面燃尽情况尚可,但内部仍有未燃的黑芯颗粒物,即使一定的循环倍率,效果也受限。
有的将温度较低的尾部除尘器飞灰,经气力输送从二次风口返回炉内很快进入稀相区。
由于颗粒粒径小,与气流间的相对滑移速度低,气固间传热速率小,颗粒升温慢。
当温度快要升高到固定碳开始燃烧时,颗粒也差不多要飞离炉膛了,因而飞灰循环出现了所谓“走过场”的现象。
在底饲回燃系统中,分离飞灰由飞灰给料装置控制流量,靠喷射器喷射,经气力输送管路、穿过风室和布风板,从位于密相床层底部的底饲喷嘴送入床内,实现循环燃烧。
飞灰分离装置可以是位于炉膛出口的高温分离器,也可以是中温分离器,还可以是锅炉尾部的除尘器(静电式或机械式等),其作用是将含碳量较高的飞灰颗粒高效分离下来。
飞灰给料装置起控制回燃飞灰流量的作用,对高温或中温飞灰采用非机械式的气控阀较好,而对尾部除尘器飞灰则常用电动锁气器或螺旋给料机。
底饲喷嘴是系统中最为关键的部件,它所处的工作环境十分恶劣,外侧受到高温固体床料颗粒的剧烈冲刷和磨蚀,内部则承受着高速含灰气固两相流的冲蚀和磨蚀,而在锅炉启动阶段或飞灰底饲回燃系统不投运时,底饲喷嘴完全处于干烧状态,因此必须选用耐高温、抗氧化和耐磨蚀的优质材料制成。
经过多年的经验积累,已找到满足上述要求、性能优越而价格合理的底饲喷嘴材料,使用寿命可保证在3~5年。
气力输送管道上的弯头既要耐磨,阻力也要尽量小。
设计时除了要选择合适材料外,结构必须合理。
而底饲喷嘴下面耐磨弯头下方的疏堵装置则是在底饲回燃系统停运的条件下,疏通开底饲喷嘴下被炉渣堵塞的垂直输灰管路,实现底饲回燃系统全天候投运的关键设备。
循环流化床锅炉采用底饲/密相区回燃技术正是为流化床燃烧室获得理想的燃烧效果提供了燃烧理论必须遵循的“3T”条件,即Temperature(高的温度)、Time(长的停留时间)和Turbulence(强烈的扰动)。
不管回燃的飞灰温度高低,飞灰通过底饲喷嘴进入密相床层底部后与大量炽热的床料颗粒混合,进行强烈的传热传质,迅速升温而开始燃烧。
这就克服了通过面饲方式回燃的飞灰颗粒入炉后进入稀相区,因气固间滑移速度低、传热速率小、升温缓慢,在还没来得及升到足够的燃烧温度就飞出炉膛(即飞灰回燃出现走过场)的问题。
同时,在密相区燃烧的回燃颗粒进入温度相对较低的稀相区后,仍能保持高温以利于继续燃尽。
图2示出底饲回燃与面饲循环燃烧效率随循环倍率的变化规律,东南大学热能工程研究所的系统性研究结果表明,即使在实验室装置燃烧室高度和密相区高度比实际工业循环流化床低很多、在较低循环倍率下,飞灰底饲回燃方式下飞灰含碳量比面饲回燃方式下有了大幅度降低,底饲循环的燃烧效率比面饲循环高约5%,其优越性非常清晰地体现了出来。
循环流化床密相区内通常处于鼓泡流化床或湍动流化床状态,底饲回燃入炉的飞灰颗粒与床内大量床料颗粒一起剧烈翻滚、摩擦,就可将飞灰颗粒外层的灰壳磨掉,使其露出里面的黑芯,有利于燃尽。
底饲回燃飞灰颗粒从密相层底部入炉,增加了其在密相层为时可观的停留时间,从而延长了在炉内总的停留时间,对飞灰燃尽十分重要。
底饲回燃的飞灰颗粒从风帽区域入炉,正是大量一次风进入床内的地方,氧浓度高,对提高飞灰中残碳的燃烧速率十分有利。
飞灰底饲回燃技术对减轻受热面磨损有其特殊的优越性。
如前所述,CFB锅炉采用飞灰底饲回燃技术后飞灰返回炉内循环一次对提高飞灰残碳燃尽度作用非常显著,因此,要获得同样的燃尽效果底饲回燃所需的循环量、也即循环倍率要比常规面饲循环低得多。
而受热面的磨损与烟气中飞灰浓度成正比,底饲回燃所需的低循环倍率无疑对减轻受热面磨损是十分有利的。
尾部电除尘器飞灰回燃时,对除尘效果影响小。
综上所述,底饲回燃飞灰颗粒被送回密相层底部后与大量炽热的床料混合,进行强烈的传热传质,迅速升温燃烧,表面灰壳被磨掉后露出新鲜的黑芯,在高温和高氧浓度条件下,以高燃烧速率燃烧,在床内较长停留时间内,获得高燃尽度。
正在燃烧着的飞灰颗粒进入稀相区后仍保持高的温度,在稀相区停留期间进一步燃尽,循环一次即可获得很高的燃尽度,这是常规面饲回燃所无法相比的,对于低温或中温飞灰采用两种回燃方式的差别尤其明显。
因此,采用飞灰底饲回燃方式,即使在中低循环倍率下也可获得理想的燃尽效果。
3、锅炉磨损改善:
循环流化床锅炉的受热面和耐火材料受到大量固体物料的不断冲刷。
在表1-2中给出了各种锅炉典型的固体物料浓度和烟速的范围,从表中的数据可以看出,循环流化床锅炉由于其特定的燃烧方式,炉内的固体物料浓度为煤粉炉的几十倍到上百倍。
在实际运行方面美国纽克拉(Nucla)电厂的75t/h循环流化床锅炉,对其服役期内12年(共运行15700h)的事故率汇总(见表1-3)进行分析,可以看出由于磨损(受热面、耐火材料、风帽等)造成的事故接近事故停炉总数的50%。
在国内已投运的一些循环流化床锅炉受热面磨损爆管事故也时有发生。
因此循环流化床锅炉的防磨措施正确与否,直接影响循环流化床锅炉机组的可用率。
根据调研资料,综述了循环流化床锅炉主要磨损部件及相应的防磨措施。
表1-2各种锅炉的典型固体物料浓度及烟速
锅炉区域
固体物料浓度(kg/m