稀硝酸装置四合一机组施工方案Word格式.docx
《稀硝酸装置四合一机组施工方案Word格式.docx》由会员分享,可在线阅读,更多相关《稀硝酸装置四合一机组施工方案Word格式.docx(32页珍藏版)》请在冰豆网上搜索。
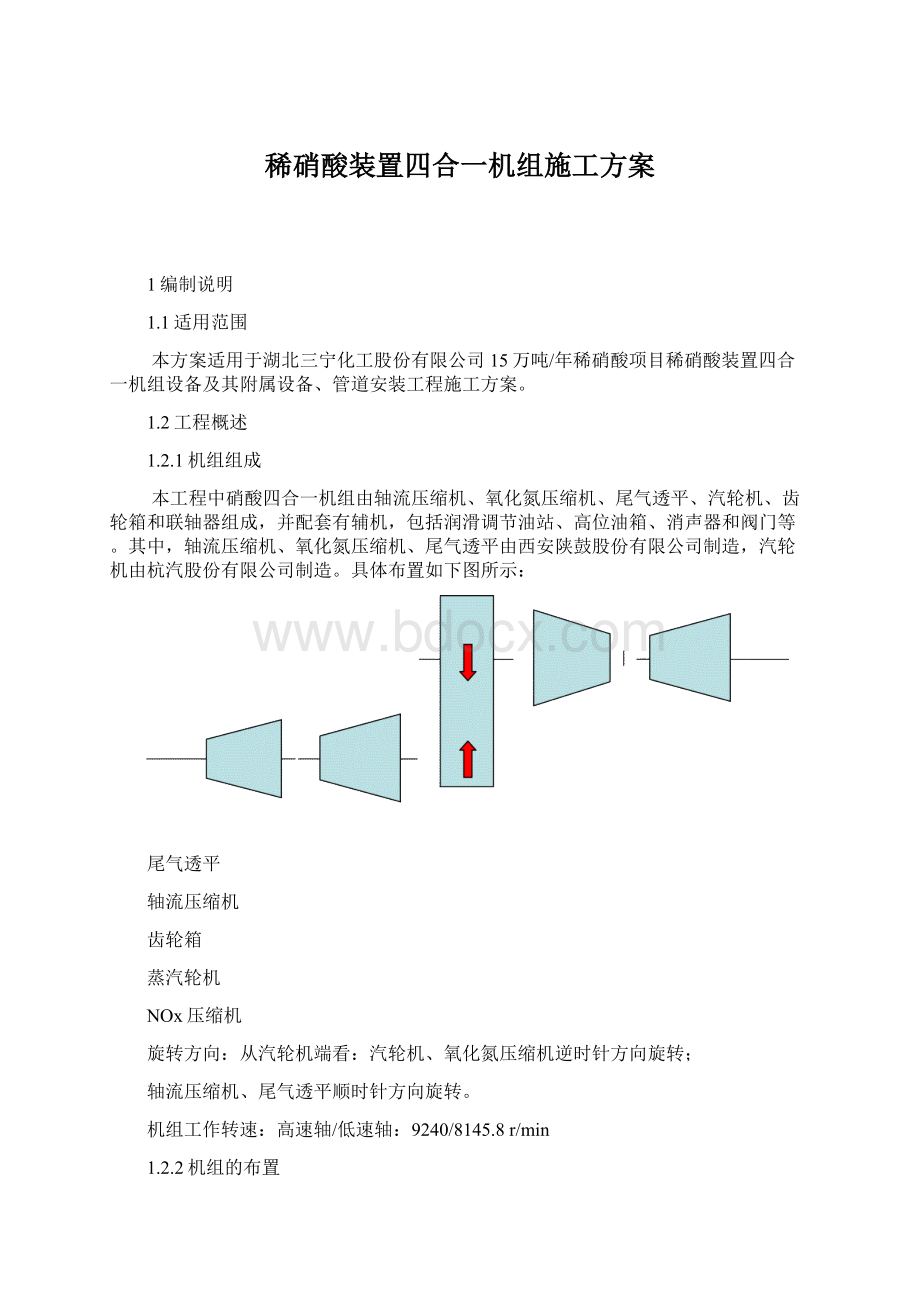
b汽轮机与NOx压缩机、NOx压缩机与齿轮箱、齿轮箱与轴流压缩机之间采用膜片联轴器,轴流压缩机与尾气透平之间使用刚性联轴器。
c齿轮箱高速轴的非联接端配置有电动盘车装置。
d汽轮机配套液压冲击式盘车。
2编制依据
2.1《机械设备安装工程施工及验收通用规范》GB50231-2009
2.2《风机、压缩机、泵安装工程施工及验收规范》GB50275-2010
2.3《化工机器安装工程施工及验收通用规范》HG20203-2000
2.4《化工机器安装工程施工及验收规范》离心式压缩机HGJ205-92
2.5《电力建设施工及验收技术规范》汽轮机机组篇DL/T5047-1995
2.6《起重设备安装工程施工及验收规范》GB50287-1998
2.7招标技术文件
3主要施工流程
4施工准备
4.1制造厂提供的以下技术文件及质量证明文件应齐全:
4.1.1设备供货清单及装箱清单。
4.1.2机器安装、运行、维护说明书和技术文件。
4.1.3设备合格证、组装、试验记录及重大缺陷记录。
主要包括以下内容:
4.1.3.1零部件的材质合格证。
4.1.3.2随机管件、管材、阀门等质量证明文件。
4.1.3.3机壳(汽缸)及附属设备水压试验记录。
4.1.3.4转子制造质量检验证书。
4.1.3.5转子动平衡及叶轮超速试验记录。
4.1.3.6机器装配记录。
4.1.3.7机器试运转记录。
4.1.3.8重大缺陷记录。
4.2施工现场具备的条件
4.2.1土建施工基本结束,厂房已封闭。
4.2.2现场施工用水、电、气及照明齐备。
4.2.3现场消防、保卫措施已落实。
4.2.4安装前应对周围环境进行清理,保持安装环境清洁干燥,应避免有害尘埃及腐蚀气体的影响。
4.2.5土建单位将基础移交给安装单位时,应有质量合格证明书及测量记录。
基础上应明显标出标高基准线及基础的纵横中心线。
基础复查合格并由土建单位与安装单位办理工序交接手续后方准进行安装。
4.2.6机组厂房内桥式起重机安装试车合格,具备使用条件。
4.2.7必要的施工机具、校验完好的量具、必要的消耗材料齐备。
4.3所有施工人员必须熟悉施工图纸(包括机组出厂技术文件、安装指导书、装箱单及合格证等)、技术人员编制施工方案、进行图纸会审等。
4.4每一步工序施工前都要经有关管理人员(技术、质量、安全)对全体作业人员进行技术和HSE交底,使作业人员对工程的情况、施工的程序和要求有全面深入的了解,同时也了解本工程的质量、HSE方面的要求。
5开箱检验
5.1机器到货后,由建设单位、、监理单位、设备制造商和施工单位共同进行开箱检验,应检查设备型号和箱号,谨防开错,核对设备的名称、规格和数量,并对完好情况进行外观检查,并做好验收记录。
5.2开箱使用合适的工具,谨慎开启,以防损坏设备,对装有精密设备的箱体,更应注意保护。
设备上的防护物和包装应按施工工序适时拆除,不得过早拆除或乱拆,包装有损坏时,应及时采取补救措施修补,以免设备损坏。
开箱后,凡经切削加工的零部件不得直接放置在地面上并对设备的出入口法兰均应合理封闭,以防异物进入。
5.3设备的转动和滑动部件,在锈油未清除前,不得转动和滑动,检查合格后涂以机械油或汽轮机油保护。
5.4凡与机器配套的电气、仪表设备及部件,应同电仪专业人员一起验收后交电仪专业保管。
5.5对随机供货的备品、备件认真清点、检查,妥善保管使用。
5.6检查零部件及专用工具是否齐全,零部件有无明显缺陷。
5.7对设备的主体进行外观检查,其外漏部分不得有裂纹、锈蚀、碰伤等缺陷。
5.8对主机及零部件的防水、防潮层包装(若有),检验完成后要进行恢复,安装时再拆除。
5.9设备开箱检验期间或安装过程中发现有设备损坏或质量缺陷,要及时与建设单位、监理单位和制造厂商共同检查协商处理。
6设备基础验收、处理
6.1基础使用前必须办理中间交接证书,并移交下列资料:
6.1.1施工质量合格证书及中心、标高、外形尺寸实测记录。
6.1.2提供基础的沉降观测点位置及其记录。
6.2对基础进行外观检查,应满足下列要求:
6.2.1基础中心线、标高、沉降观测点等标记齐全、清晰。
6.2.2基础不得有裂纹、蜂窝、空洞、露筋等缺陷。
6.2.3按土建基础图和技术文件,对基础外形尺寸,坐标位置进行复测检查,其允许偏差应符合下表的规定。
基础尺寸及位置允许偏差
项次
项目名称
允许偏差mm
1
坐标位置(纵横轴线)
±
20
2
不同平面的标高
一20
3
平面外形尺寸
凸台上平面外形尺寸
凹穴尺寸
士20
+20
4
平面水平度(包括地坪上需安装设备部分)
(1)每米
(2)全长
5
垂直度
(1)每米
10
6
预埋地脚螺栓
(1)标高(顶端)
(2)中心距(在根部和顶部两处测量)
+2
7
预留地脚螺栓孔
(1)中心位置
(2)深度
(3)孔壁铅垂度
8
预埋活动地脚螺栓锚板
(1)标高
(2)中心位置
(3)水平度(带槽的锚板)
(4)水平度(带螺纹孔的锚板)
6.2.4预留地脚螺孔内的木桩、杂物应清理干净;
基础与砼楼板之间应有一定间隙,当直接接触时,应用凿子凿出缝隙。
6.3对基础应进行沉降观测,观测工作至少配合下列工序进行:
6.3.1基础养护期满后(此次测定值作为原始数据)。
6.3.2压缩机组安装前。
6.3.3压缩机组安装完毕二次灌浆前。
6.3.4试运行后。
6.4基础处理
6.4.1机组安装前将需灌浆的基础表面浮浆层铲除,深度约10-15mm。
然后根据机组底座调整螺栓的位置将基础上放置支撑块的位置铲平,铲平部位应比支撑块每边大20mm,并保证支撑块上表面至机座底面至少有20mm的余量,支撑块表面水平度允许偏差为2mm/m。
之后在基础表面其它位置铲出麻点,每平方分米3~5个麻点为宜,深度宜14-20mm。
基础表面不得有油污。
6.4.2基础放线,应放出机组纵向中心线,横向有轴承中心线。
6.4.3以机组纵横中心线为基准,各埋置垫铁位置对螺孔中心的偏差应不大于3mm。
7机组安装
机组的安装应根据厂家的随机文件提供的数据,在厂家的指导下进行,并逐步做好安装记录,由施工单位、厂家现场指导人员、监理单位、建设单位共同签字确认。
由于空气压缩机、氧化氮压缩机、尾气透平膨胀机、变速箱共用一个联合底座,汽轮机单独使用一个底座,为确保机组的安装质量和便于机组施工,汽轮机安装应在压缩机找正后进行。
7.1机组就位前的准备
7.1.1吊装前,安装在机器下部且机器就位后无法安装的设备、管道等,应预先安装好。
7.1.2用压缩空气对基础表面进行吹扫,清除地脚螺栓预留孔中的杂物。
7.1.3吊起底座,去除底座面上的油污、油漆及铁锈等赃物。
7.1.4清理地脚螺栓和顶丝,光杆部分应无油污,螺纹部分应涂抹油脂,地脚螺栓螺的光杆部分涂刷防锈漆。
7.1.5机组吊装前,应将安装基准线及纵、横中心线位置在机器底座侧面且标识清楚,以便于就位后与基础上的划线对中找正。
7.1.6机组吊装前,将地脚螺栓位置的底脚板、固定螺钉和顶丝安装到底座上,并将地脚螺栓穿入底座,把螺栓上部垫片及双螺母临时装好,使其随机器一同起吊就位。
7.1.7吊装前,在基础上设置临时垫铁组,以便机器在X、Y方向移动找正。
每个地脚螺栓旁至少一组垫铁,用水平仪调整垫铁组高度,使垫铁组上平面标高达到设计标高。
并且要求所有垫铁的横向、纵向水平不大于0.1mm/m。
7.1.8吊装前,根据放线位置,用座浆法预埋垫板,再用水平仪找正,要求所有垫板的横向、纵向水平不大于0.1mm/m,并且各垫板的高度差小于1mm,调好后养护3-5天。
7.1.9机组安装区域设为专区,无关人员不得进入机组施工现场,以便做好产品保护。
7.2机组就位、找正、找平
7.2.1机组就位后,找平找正时先用千斤顶调整底座在X、Y方向的位置,使设备底座上的安装基准线和纵、横中心线标记与基础上相应的划线重合,允许偏差为+1mm。
找正时分两步,首先进行安装基准线的对中,之后进行纵、横中心线的对中,两个步骤应交替进行,直至各个基准线全部重合为止。
7.2.2找正后,调整临时垫铁高度,使机器达到设计的安装标高,偏差不得超过1mm。
之后复查机器的基准线及轴线的对中情况,如又产生偏差应按7.2.1的方法再次调整,然后复查机器标高,反复进行,直至机器基准线、轴线和标高完全达到设计允许的范围内。
拧紧顶丝使其全部和垫板顶紧,然后撤去临时垫铁,复查之前找正、找平情况,如有偏差通过顶丝来调整。
7.2.3旋转顶丝,调整机器的水平度,水平度的测量应在机器本体制造厂指定的机加工面上进行。
调整顶丝找平时,底座上所有同类顶丝应均匀调节,使机组载荷均匀分布。
压缩机机组水平度允许偏差为0.04mm/m。
变速箱轴向水平不大于0.02mm/m,径向水平不大于0.04mm/m。
7.2.4压缩机找正要兼顾同类压缩机的轴线进行定位。
7.2.5机组找平、找正以变速箱为基础进行找正的具体数据要符合设备厂家的有关规定。
7.2.6找正时应保证室内环境温度一致,否则误差较大。
7.2.7机组全部找正合格后,预紧地脚螺栓,并将顶丝与垫板点焊固定。
7.2.8压缩机组找平找正的同时,应以压缩机为基准对汽轮机进行找平找正。
7.3.地脚螺栓灌浆
7.3.1压缩机找平找正的同时,以压缩机为基准对汽轮机进行找平找正,待机组找平、找正后,对压缩机底座的地脚螺栓孔进行灌浆,当强度达到后把紧地脚螺栓,压缩机进行精找平找正后,对汽轮机进行初对中。
7.3.2初对中完毕后,对汽轮机地脚螺栓孔进行灌浆,当强度达到后把紧地脚螺栓,进行机组精对中。
7.3.3灌浆料要符合设计或规范要求,灌浆前将螺栓孔壁充分湿润。
7.3.4当灌浆层达到设计强度时,就要对称的把紧地脚螺栓。
7.4机组轴对中
7.4.1机组对中应先确定好对中基准,并根据厂家提供的冷态对中图采用三表对中法进行对中。
7.4.2在对中期间,要经常测量轴端距,偏差不得超过±
0.5mm。
测量轴端距时,每次轴都要先进行轴向移动调整,使止推轴承处于操作位置。
轴头间距、联轴器两法兰间隙符合压缩机厂家技术文件要求。
7.4.3对中调整完毕,在对中图上记录对中数值、轴端距、支腿下垫片厚度。
7.4.4冷态对中允许偏差为:
径向±
0.04mm,轴向±
0.02mm。
冷态对中曲线和冷态对中值须符合技术文件要求。
7.4.5对中步骤:
用一个装有三块百分表的仪表架进行找正,见下图位于径向位置的百分表,测量轴的径向偏差,位于轴向位置的两块百分表,测量轴的轴向偏差。
百分表应经检合格,精度符合测量要求;
仪表架应结构坚固,重量轻、刚度大,安装牢固无晃动,使用时应测量表架挠度,以校正测量结果。
联轴节对中示意图
7.4.5.1联轴节对中应避免在阳光照射或冷风偏吹的情况下进行。
7.4.5.2调整垫片应清洁、平整,无折边、毛刺。
7.4.6汽轮机与NOx压缩机、NOx压缩机与齿轮箱、齿轮箱与轴流压缩机之间采用膜片联轴器,轴流压缩机与尾气透平之间使用刚性联轴器。
膜片式联轴器连接时必须使用专用定位环定位,即必须将定位环装于压缩机轴头再安装联轴器,以保证安装尺寸。
安装联轴器时,必须要保证两个轮毂和隔离套端面的间隙。
7.5机组的二次灌浆
7.5.1机组精对中完毕后,工艺配管之前,对机组进行二次灌浆。
灌浆料要符合设计文件或规范要求。
7.5.2基础二次灌浆前,应检查复测下列项目,并做好记录:
a联轴器的对中偏差和轴向间距应符合要求。
b复测机组各部滑销、立销、连接螺栓等部位的间隙值,使其符合技术要求。
c检查地脚螺栓是否全部按要求紧固。
d机组检查复测合格后,必须在24h内进行灌浆,否则应再次进行复测。
7.5.3在机器底座四周支好模板,地脚螺栓露出螺纹部分用塑料薄膜包扎好。
7.5.4二次灌浆前,基础表面必须清除灰砂、杂物、油污等。
基础表面应用清水湿润24小时,灌浆时应清除表面积水。
7.5.5准备好试块模子,在二次灌浆的同时制备试块。
7.5.6二次灌浆必须在安装人员配合下,连续进行一次灌完。
灌浆时应不断捣固,使灌浆料紧密地充满各部位,灌浆后要精心养护。
7.5.7当灌浆层强度达到设计强度时,拆除机器底座四周支的模板,用小手锤敲击检查灌浆的密实度,对于检查处的空洞进行无收缩水泥填补,必要时可采用环氧树脂灌浆料。
7.5.8二次灌浆层养护期满后,在机组底座地脚螺栓附近放置百分表,将百分表的测量头与底座接触。
然后,松开底座上的调整螺钉,将地脚螺栓再次拧紧,仔细观测底座的沉降量,在调整螺钉附近底座的沉降量不得超过0.05mm。
8设备的拆检、组装
8.1.压缩机揭盖清洗、检测
8.1.1轴承清洗、检测、装配
8.1.1.1轴衬装配前应进行外观检查,轴瓦合金表面不得有裂纹、孔洞、重皮、夹渣、斑痕等缺陷。
合金层与瓦壳应牢固紧密地结合,经涂色检查不得有分层、脱壳现象。
8.1.1.2可倾瓦、薄壁瓦轴承间隙及接触面积是由机械加工保证的,不应进行刮研。
8.1.2径向轴承的清洗、检测、装配应该符合下列要求:
8.1.2.1用涂色法检查瓦背与轴承座孔应紧密均匀贴合,厚壁瓦的接触面积,不应少于50%;
可倾瓦、薄壁瓦、球面瓦的接触面积不应少于75%。
8.1.2.2轴瓦与轴承座和轴承盖之间的过盈量应该符合技术文件的规定。
8.1.2.3用涂色法检查轴颈与轴瓦的接触情况,轴瓦与轴颈接触应均匀,轴向接触长度不应少于80%。
8.1.2.4用压铅法或千分表抬轴法测量径向轴承间隙,应符合设计规定。
8.1.2.5可倾瓦的瓦块厚度应均匀,各瓦块间厚度差不应大于0.01mm。
装配后瓦块能自由摆动,不得有卡涩现象。
8.1.2.6厚壁、可倾瓦口接触应严密。
自由状态时,用塞尺检查,间隙不得大于0.05mm。
8.1.3推力轴承的装配应符合下列要求:
8.1.3.1推力瓦块的外观检查,应符合本方案8.1.1.1的规定,表面粗糙度Ra不应大于0.4μm。
8.1.3.2推力瓦块的厚度应均匀一致,同组瓦块的厚度差不应大于0.01mm。
8.1.3.3推力轴承调整垫应平整,各处厚度差应小于0.01mm,数量不应超过2块。
8.1.3.4用涂色法检查,推力轴承与推力盘应均匀接触,接触面积不应小于75%。
8.1.3.5测量推力轴承间隙,应在上下两半推力瓦、定位环和上下两半瓦套紧固后进行,推力轴承的间隙应为0.25~0.60mm。
8.1.4机壳与隔板清洗、检测、安装
8.1.4.1检查机壳的外观,不得有裂纹、夹渣、气孔、铸砂和损伤等缺陷。
8.1.4.2壳体的水平或垂直剖分面应完好无损,接合面自由结合时,间隙不应大于0.08mm,或每隔一个螺栓拧紧后,间隙不应大于0.03mm。
8.1.4.3轴承箱内的铸砂、杂物等应清理干净。
8.1.4.4底座支撑面和机壳支座底面应紧密结合,自由状态下,宜用0.03mm的塞尺检查,不得塞入为合格。
8.1.4.5底座支撑面与轴承座底面应严密接触,应用0.05mm的塞尺检查,不得塞入为合格。
8.1.4.6支撑滑销系统联系螺栓、滑动键的间隙及膨胀方向,应符合技术文件规定。
8.1.4.7隔板外观检查,铸件不得有裂纹、气孔、未浇满和夹层等缺陷,扩压器和回流器的导流叶片应完整无损。
8.1.4.8隔壁装进机壳时,应自由地落入槽中,无卡涩现象;
隔板装配后,隔板与隔板及隔板与机壳中心的偏差应小于0.05mm。
8.1.4.9两半隔板结合面应接触良好,结合面的局部间隙应小于0.08mm。
8.1.4.10固定上下隔板的销子、定位键和对应孔槽的配合应符合技术文件的规定。
8.1.4.11隔板最终装配时,应在各结合面处涂干石墨粉或其它防咬合剂。
8.1.4.12隔板的吊装应使用专用工具。
8.1.5转子清洗、检测、安装
8.1.5.1检查并清洗转子,应无锈蚀、损伤、变形、裂纹等缺陷。
8.1.5.2测量转子主轴颈及浮环密封配合处轴径的圆度、圆柱度,其各部允许偏差值应符合技术文件的规定。
8.1.5.3检查主轴颈、浮环密封或机械密封配合处及径向探头监测区轴的表面粗糙度Ra不应大于0.4~0.8μm。
8.1.5.4推力盘表面粗糙度Ra不应大于0.4μm。
8.1.5.5测量转子各部位的径向跳动值、端面跳动值,并应符合技术文件的规定。
8.1.5.6转子吊装应使用专用工具,吊装时转子应保持水平状态。
8.1.5.7转子就位后,应测定转子总窜量,并按技术文件要求,调整轴向位置,装推力轴承,使叶轮工作通道对称于扩压器通道,允许偏差宜为±
1mm。
8.1.6密封装置的清洗、检测、安装
8.1.6.1迷宫密封的检查与安装应符合下列要求:
8.1.6.1.1迷宫密封的各密封片应无裂纹、卷曲等缺陷,镶装牢固,安装方向应正确。
8.1.6.1.2以转子为准,检查各部迷宫密封间隙,其值应符合技术文件的规定。
8.1.6.1.3迷宫式软密封的装配间隙,应符合技术文件的规定。
8.1.6.2浮环油膜密封的检查与安装,应符合下列要求:
a浮环油膜密封内外浮环的金属表面不应有气孔、夹渣、重皮、裂纹等缺陷。
b测量内外浮环的直径及各部位尺寸并记录。
c浮环与密封体的接触面应光滑,无碰伤、划痕等缺陷,且接触应良好。
d浮环密封的“O”形环应完好无损。
e浮环密封组的装配间隙,应符合技术文件规定。
f浮环密封组装后,应活动自如,不得有卡涩现象。
8.1.6.3机械密封的检查与安装,应符合下列要求:
a机械密封各零件不应有损伤、变形,密封面不应有裂纹、擦痕等缺陷。
b检查密封环的平行度,其偏差不应大于0.01mm,端面垂直度偏差不应大于0.05mm。
c装配过程中,零件必须保持清洁,动环及静环的密封面应无灰尘和异物。
d静环安装后应能沿轴向灵活移动。
e安装后盘动转子应转动灵活。
f机械密封的冲洗系统及密封系统必须保证清洁无异物。
8.1.7机壳闭合
8.1.7.1机壳闭合前,检查下列各项,均应符合技术文件要求,并应有相应的安装记录:
a径向轴承、推力轴承各部间隙。
b机壳、隔板、密封装置组装状况。
c转子中心位置、水平度、转子的主要部位跳动值。
d机壳水平度、剖分面接触状况。
e支撑滑销系统组装状况。
8.1.7.2机壳闭合时,应符合下列要求:
a检查确认机壳内部清洁无异物。
b检查确认机壳内的紧固或定位螺栓应拧紧、锁牢。
c在机壳剖分面上均匀地涂抹密封剂,密封剂应符合技术文件规定。
d装上导向杆,将机壳平稳地闭合,安装定位销,检查轴封部位不得有错口现象。
e按规定顺序和紧固力矩拧紧机壳剖分面的联接螺栓。
f机壳闭合后,盘动转子应转动灵活无异常声响。
8.1.7.3机壳螺栓的紧固,应符合下列要求:
a机壳螺栓应无毛刺、损伤,螺栓的螺纹部位应涂防咬合剂。
拧螺母时不得有卡涩现象。
b螺栓的紧固顺序:
应从机壳中部开始,按左右对称分两步进行,先用50—60%的额定力矩拧紧,再用100%的额定力矩紧固。
c螺栓的紧固力矩,应符合技术文件规定。
8.2变速箱揭盖清洗、检测
8.2.1箱体外观检查,铸件不得有裂纹、气孔、未浇满、夹层等缺陷;
焊件不得有变形、裂纹等缺陷。
8.2.2检查轴颈的圆度、圆柱度、径向跳动,其允许偏差应符合技术文件规定。
8.2.3检查推力盘的表面粗糙度Ra,不应大于0.8μm,端面跳动值应小于0.015mm。
8.2.4检查齿轮工作面不得有剥落、裂纹、磨损、锈蚀、补焊等缺陷。
8.2.5变速机轴承安装,应符合本方案13.1的有关规定。
8.2.6用涂色法检查齿轮副应啮合良好,接触均匀。
8.2.7两啮合齿轮的中心距的偏差应符合技术文件的规定。
8.2.8检查啮合齿轮轴线的平行度,其偏差应符合技术文件的规定。
8.2.9两啮合齿轮的啮合间隙应用压铅法进行检查,啮合间隙值应符合技术文件的规定。
8.2.10变速机机壳中分面应光滑,无沟槽、划纹、锈蚀等缺陷。
接触应严密,自由状态时,局部间隙不应大于0.05mm。
8.2.11变速机合盖时,在中分面内侧必须涂抹密封剂,并应对称均匀地紧固机壳结合面的螺栓。
8.3汽轮机揭盖清洗、检测、安装
8.3.1汽缸安装前应将座架和猫爪支撑平面清洗干净,接触面积应均匀分布且达75%以上,自由状态下两面之间,用0.04mm塞尺检查不得塞入。
间隙螺栓与螺栓孔的相对位置、座架与螺帽间的自由间隙,都应符合技术文件规定。
8.3.2检查与调整各部位的滑销位置及间隙应符合设计规定。
8.3.3底座的纵、横向水平度应在基准面上进行检测,允许偏差为0.10mm/m。
汽缸的纵向水平度以汽轮机后端轴承座孔或轴颈为准,允许偏差为0.04mm/m。
横向水平应以前、后轴承水平剖面为基准,允许偏差为0.05mm/m。
8.3.4汽缸剖分面接触应严密,在自由状态下的间隙不应大于0.05mm/m,或每隔一个螺栓拧紧后不应有间隙。
8.3.5轴承的检查和安装应符合本方案8.1.1的规定。
8.3.6汽缸内的部件,如隔板、静叶片、汽封等,组装前应清洗检查无缺陷,与汽缸体组合时,其中心位置和相应间隙,应符合技术文件规定。
8.3.7轴承座孔与汽缸中心偏差,不得大于0.03mm。
8.3.8转子安装应符合下列要求:
8.3.8.1转子表面应清洗干净,检查各部件的装配应符合技术文件规定,并无损伤和缺陷。
8.3.8.2转子装入汽缸前,必须对隔板、静叶片、通道、汽封等,用压缩空气吹扫干净,疏水口必须畅通,径向轴承应注入合格润滑油。
8.3.8.3转子起吊及放置必须保持水平状态,严禁碰压汽封等部件。
8.3.8.4转子就位后,调整转子与缸内部件的相对位置及间隙,使其符合技术文件的规定,方可正式装配推力轴承。
8.3.8.5转子有关部位的跳动值,应符合技术文件规定。
8.3.8.6转子与汽缸的中心线应重合,允许偏差应为0.03mm。
8.3.8.7转子安装水平度,应以汽轮机排汽侧轴颈为基准,偏差不应大于0.02mm/m。
进汽