有关硅钼球铁的一些问题李传拭Word格式.docx
《有关硅钼球铁的一些问题李传拭Word格式.docx》由会员分享,可在线阅读,更多相关《有关硅钼球铁的一些问题李传拭Word格式.docx(11页珍藏版)》请在冰豆网上搜索。
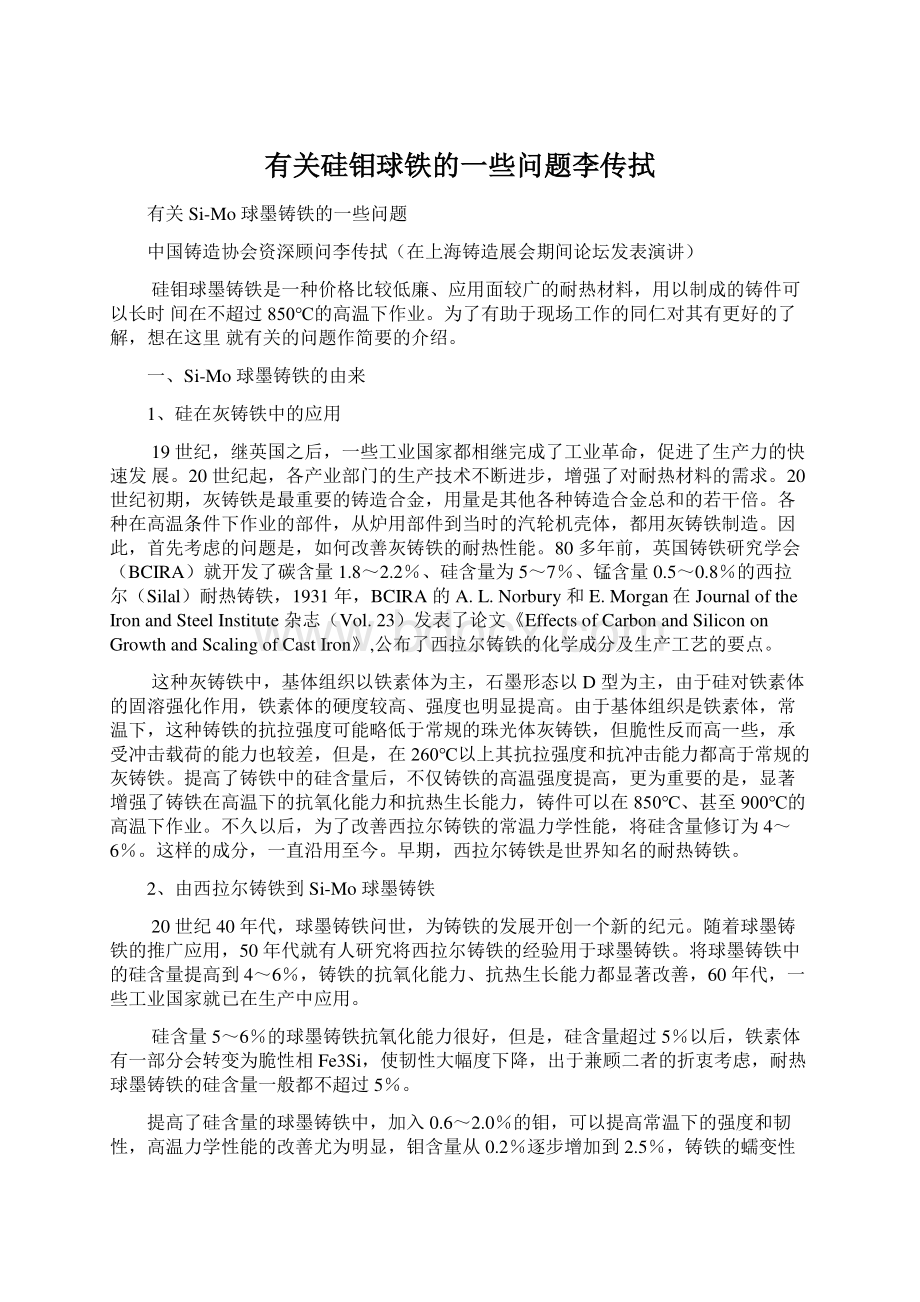
随着技术的进步,内燃机排气温度逐渐提高,排气歧管的材质也随之不断改进。
80年代以后,档次较高的内燃机排气温度超过了800,所用的排气歧管和涡轮增压器,灰铸铁、蠕墨铸铁、硅铸铁等材质都不能适应要求。
于是,Si-Mo球墨铸铁大行其道,广泛用于世界各国的汽车行业,其需求量猛增。
90年代以后,一些汽车发动机的排气温度超过了900,Si-Mo球墨铸铁不能胜任了,开始用高镍奥氏体球墨铸铁。
2000年代早期,高档汽车发动机的排气温度又越过了950,排气歧管和涡轮增压器不得不改用铁素体耐热钢。
2005年以后,为了进一步提高燃油的燃烧效率,排气温度超过了1000,又要改用高镍奥氏体不锈钢。
在内燃机燃烧效率不断提高的条件下,Si-Mo球墨铸铁在汽车行业的应用是有所减少了,而且还有继续减少的趋向。
但是,在柴油机方面的应用仍然很多,而且,其他方面对耐热铸件的需求量也非常可观,Si-Mo球墨铸铁仍然是一种重要的铸造合金。
二、Si-Mo球墨铸铁的化学成分及其对力学性能的影响Si-Mo球墨铸铁中的主要合金元素是硅,钼是为改善铸铁而加入的辅助合金元素,在硅、钼含量确定之后,对碳、锰、磷、硫等元素的含量也应该予以严格的控制。
1、硅在Si-Mo球墨铸铁中,硅是重要的组分,其在球墨铸铁中的作用是多方面的,主要是提高抗氧化能力和降低热生长率,同时还可以使铁素体固溶强化。
其负面作用是,硅含量太高时导致铸铁脆化。
(1)促进石墨化、抑制渗碳体的析出在铸铁中,硅固溶于奥氏体中的溶解度约为2,在铁素体中的溶解度可高达18.5。
铸铁中,硅是促进石墨化作用最强的合金元素,其促进石墨化的能力大致是镍的3倍、铜的5倍。
无论在液态铸铁或固态铸铁中,铁与硅结合的能力比与碳结合的能力强。
增加铸铁中的硅含量,可以使铁-碳平衡图中铁-石墨系的共晶转变温度略有提高,铁-渗碳体系的共晶转变温度明显降低,从而使二者之间的间隔显著扩大。
对二者的共析转变温度也有类似的影响。
液态铸铁中含有硅,就会使碳的溶解度降低。
铁液中硅的含量愈高,能溶解的碳量相应地愈低,就会有更多的碳脱溶析出。
铁液为过共晶成分时,硅含量高,凝固过程中,有更多的碳以初生石墨的形态析出,直到剩余的铁液达到共晶成分后发生共晶转变。
铁液为亚共晶成分时,凝固过程中,硅富集于初生奥氏体中。
共晶转变时,硅富集于早期结晶的共晶奥氏体中,抑制碳与铁化合成渗碳体,增强碳在奥氏体中的扩散速度,促使碳以共晶石墨的形态析出。
共析转变时,固溶于奥氏体中的硅,仍然抑制碳与铁形成渗碳体,增强碳在奥氏体中的扩散速度,促使碳以共析石墨的形态析出,硅含量为4左右的铸铁,基体组织大体上全是铁素体。
在加入了钼,而且用于制造薄壁铸件的条件下,组织中就可能含有少量的珠光体和碳化物。
Si-Mo球墨铸铁中,硅含量较高,因而,薄壁铸件中形成碳化物的倾向较低,这对于制造排气歧管之类的薄壁铸件是很适宜的。
(2)提高铸铁的抗氧化能力一般说来,耐热铸件的作业条件是,在高温下、长时间与氧化性气体(主要是O2、H2O、CO2)接触。
在这种条件下,铁基铸件的表面层会被氧化。
高温气体介质中有时还含有硫化物,硫对铁的作用也属于氧化反应。
耐热铸件应具有在高温下抗氧化的能力,也就是高温下的化学稳定性。
铁在高温下的氧化从表面开始,先形成一层薄氧化膜,然后逐渐增厚。
由于铸铁件的基本成分是铁,其氧化过程实际上是铁被氧化的过程。
在570以上的高温下,铁基铸件表面的氧化膜为三层结构。
内层(贴近金属本体)为FeO,中间层为Fe3O4,外层为Fe2O3。
氧化过程中,氧原子以扩散的方式通过氧化膜进入铁中,使铁氧化,铸铁中的铁原子则向氧化膜方面扩散。
铁逐层被氧化成FeO,FeO逐层被氧化成Fe3O4,Fe3O4又逐层被氧化成Fe2O3。
结果是各氧化层不断增厚,金属本体逐渐减薄(见图1)。
铸铁的氧化过程中,在金属本体逐渐减薄的同时,由于氧化膜的密度小于铁,铸件的体积却反而会增加。
铸件外表面产生的氧化皮,是可能剥落的。
如果铸件的内部氧化,则产生的氧化皮不可能剥落,结果是导致铸件的体积增大,这就是因氧化而致的热生长。
图1铁基铸件表面氧化的示意图要提高铸铁的抗氧化能力,必须使其中含有能形成致密氧化膜的合金元素,而且这种氧化膜还应与金属本体结合紧密,从而抑制外界的氧原子通过氧化膜向铸件内部扩散、以及铁原子向氧化膜扩散。
如果铸铁中含有加入铝、硅、铬等元素,形成的氧化膜的成分和结构都有变化,可以增强铸铁的抗氧化能力。
铬、铝含量高时,铸件的表面上形成致密的Cr2O3或Al2O3氧化膜,有良好的保护作用。
铬、铝含量不很高时,铸件的表面上形成FeOCr2O3、FeOAl2O3等尖晶石型氧化物,能与铁结合牢固,也有一定的保护作用。
硅含量较高的铸铁中,氧化膜的主要组成成分是铁橄榄石(Fe2SiO4),致密程度大为改善,能抑制外界的氧原子通过表面进入铸铁内部。
就提高铸铁的抗氧化能力而言,硅是很强的抗氧化元素,其作用能力大约是铬的3倍。
几种常用合金元素对铁氧化速率的影响见图2。
图2常用合金元素对铁氧化速度的影响(3)减少铸件的热生长铸铁件热生长的定义是:
铸件长时间暴露于高温下,或在反复加热、冷却作用下所产生的永久性体积增大。
热生长不仅使铸铁的强度降低,还可能损坏与之接触的其他部件。
铸铁发生热生长的原因,可以简要地归纳为以下三个方面。
1)高温下珠光体中的渗碳体分解、析出石墨所致的体积膨胀球墨铸铁中的珠光体在540以下比较稳定。
超过540以后,其中的渗碳体就会逐渐分解,碳以石墨的形态析出,通过扩散方式沉积在石墨球上。
650以上,石墨化的速度提高。
在700以上,石墨化在短时间内就可以完成。
石墨化的结果就导致铸铁的体积膨胀。
基体组织全部为珠光体的球墨铸铁件,因石墨化而致的体积生长,按计算,大约是1。
由于铸件内部存在疏松和其他细小的孔隙,实际铸件因石墨化而致的生长低于此值。
有研究报告称:
珠光体组织的球墨铸铁件,在高温下长时间保持,因石墨化而致的体积生长约在0.250.5之间。
完全铁素体基体的球墨铸铁件,在820以下保持,实际上不可能因石墨化而产生体积增长。
Si-Mo球墨铸铁中,硅含量提高到4左右,不仅基体组织基本上是铁素体,珠光体很少,而且可以使铁-石墨系的共析转变温度Ac1提高到870以上。
因此,在作业温度不超过850的条件下,不必担心铸件因石墨化而产生热生长的问题。
2)相变所致的体积膨胀铸件作业过程中,即使是铁素体基体的球墨铸铁,如果所处的温度不断通过铸铁共析转变温度范围,铸铁周期性地发生铁素体奥氏体、奥氏体铁素体的相变。
加热到基体组织为奥氏体时,少量石墨溶入奥氏体,留下一些微小的孔隙。
冷却时,奥氏体中的碳又以石墨的形态析出,但不会析出在原来留下的孔隙中,从而造成石墨化膨胀。
长时间反复经历这种转变,铁就会有可观的体积膨胀,导致很坏的后果。
因此,常规的铁素体球墨铸铁的作业温度,一般都不能高于共析转变温度(约在760左右)。
提高铸铁中的硅含量,可以使其共析转变温度提高,铸铁作业的温度也可相应地提高,参见表1。
表1硅含量对共析转变温度的影响3)铸铁内部氧化所致的体积膨胀前面已经提到,铸铁件的内部氧化是导致热生长的主要原因之一,而铸铁组织中石墨的形态和数量又是影响铸件内部氧化的重要因素。
灰铸铁的显微组织中,石墨呈分散的片状,实际上是相互连接的团簇体,而且还有触及铸件表面的石墨片。
石墨是碳质材料,在高温、氧化性气氛下易于氧化,这样,就逐渐形成了氧进入铸件内部的通道。
因此,灰铸铁是易于发生内部氧化,所导致的热生长率也高。
石墨片越粗大、数量越多、连续性越好,内部的氧化就越严重。
球墨铸铁中的石墨球是互不相连的,也没有联通外界的通道,可以有效地抑制内部的氧化。
提高铸铁的硅含量后,铸铁本身抗氧化能力又大为增强,这方面就更不成问题了。
Si-Mo球墨铸铁件中,可能导致内部氧化的因素是:
在反复加热、冷却的条件下,可能产生延伸到铸件表面的细微裂纹。
4)硅对铁素体的固溶强化作用在球墨铸铁中,硅固溶于铁素体,有抑制渗碳体析出、促进铁素体形成、提高铸铁抗氧化能力等作用,此外,固溶于铁素体的硅能使铁素体强化、改善球墨铸铁的力学性能。
将球墨铸铁中的硅含量提高到3.84.5,可以得到全铁素体组织。
由于硅对铁素体的固溶强化作用,抗拉强度可以略高于600MPa,而且屈服强度、伸长率都有较大幅度的提高。
但是,硅含量超过4.5以后,铸铁即显现脆性,伸长率随硅含量的增高而急剧下降。
由于铸铁组织全部为铁素体,铸件的硬度均匀,加工性能明显改善。
硅固溶强化的球墨铸铁,疲劳极限优于常规球墨铸铁。
硅固溶强化的球墨铸铁,脆性转变温度很高:
用V-形缺口试样和U-形缺口试样测定时,脆性转变温度都高于室温,在60以上;
用无缺口试样测定时,也在10以上。
因此,硅固溶强化的球墨铸铁不宜用于制造结构上有应力集中部位的铸件,尤其不宜用于在低温条件下承受冲击载荷的铸件。
在脆性转变温度以上,硅固溶强化的球墨铸铁的冲击韧性优于常规球墨铸铁。
无论是铸铁或铸钢中,硅含量太高都会使铸铁(或铸钢)的脆性增大。
因此,硅作为提高抗氧化性能的元素,其应用受到了很大的制约,不像铬那样,加入量可高达2030。
灰铸铁是脆性材料,硅含量可略高一点,一般宜在6以下;
球墨铸铁中,硅含量不宜超过5;
铸钢中的硅,一般都用作改善抗氧化性的辅助元素,其含量应限制在3以下。
2、钼钼是促进碳化物形成能力很强的元素之一。
钼在奥氏体中的固溶度可达3,随着奥氏体中碳含量的增高,固溶度还可提高。
钼在铁素体中的固溶度更高,可达37左右,有使铁素体固溶强化的作用。
硅含量较高的铁素体球墨铸铁加入钼,可以提高其常温强度、高温强度和蠕变性能,其正面作用是非常明显的。
但是,加入钼不可避免地也会有一些负面作用,随着钼含量的增加,铸铁组织中可能出现少量碳化物。
凝固终了后,珠光体分解时,还可能在晶界附近析出富钼的次生相。
次生相的组成挺复杂,其中含有Fe-Mo-Si金属间化合物、钼的碳化物、固溶有钼和硅的铁素体和珠光体,有时简化用分子式Fe2MoCM6C表示。
含有少量珠光体和这种次生相,铸铁的伸长率和断面收缩率当然会相应地有所下降。
关于钼含量对Si-Mo球墨铸铁性能的影响,美国ClimaxMolybdenum公司曾经进行过大量的试验研究工作。
以下,引用该公司的一些实验数据,大致说明钼在Si-Mo球墨铸铁中的作用。
1)钼对Si4球墨铸铁拉伸性能的影响采用碳、硅、锰含量基本一致的铸铁(碳含量为3.163.23;
硅含量为3.974.04;
锰含量均为0.31),球化处理和孕育处理的工艺相同,只改变钼的含量,制成拉伸试样后,在不同温度下的拉伸性能见表1.1(说明:
屈服强度均为残留变形为0.2的屈服强度)。
表1.1在不同温度下钼含量对Si4球墨铸铁拉伸性能的影响2)钼对Si4球墨铸铁蠕变性能的影响在硅含量为4左右的球墨铸铁中,增加少量的钼,还可以降低铸铁在高温下的蠕变速度、提高蠕变断裂的强度。
钼含量对Si4球墨铸铁在705保持后的断裂强度的影响见图3。
图3钼含量对Si4球墨铸铁在705保持100h和1000h后的断裂强度的影响(试样经790退火)钼含量对Si4球墨铸铁在815下产生1蠕变的应力和时间的影响见图4。
图4钼含量对Si4球墨铸铁在815下产生1蠕变的应力和时间的影响3、Si-Mo铸铁中的其他组分1)碳和碳当量常规的球墨铸铁,随着硅含量的提高,碳含量要相应降低,以调整碳当量,但是,碳含量降低的程度,不能按保持碳当量相同考虑。
在降低碳含量的同时,往往要使碳当量略高一些。
Si-Mo球墨铸铁中的硅含量较高,应该相应地调低碳含量,而碳当量的值则应略高于常规球墨铸铁。
确定碳含量,还应考虑铸件结构特点及壁厚等要求。
对于排气歧管之类的薄壁铸件,没有石墨漂浮的问题,碳当量宜保持在4.8%左右,或者再略高一点。
壁厚50左右的铸件,碳当量则以控制在4.54.7为好。
2)锰锰是大家熟知的碳化物形成元素,常规的铁素体球墨铸铁中,通常都要求锰含量不超过0.2,为此,炉料中往往不得不配用高纯生铁。
但是,球墨铸铁中可以容许的锰含量,与铸铁中的硅含量和铸件的壁厚有关。
提高铸铁中的硅含量,可以有效地削弱锰促进碳化物形成的作用,而且铸件的壁厚愈薄,这种作用就愈明显。
大约每增加1的硅,可容许锰含量增加0.1。
铸件凝固过程中,硅偏析于石墨球附近,锰则偏析于最后凝固的液相中。
因此,厚壁铸件凝固过程中,最后凝固部位的锰含量很高,例如,平均锰含量为0.35的中厚铸件,最后凝固部位的锰含量可能高达2.5。
铸铁中的硅,则在铸件凝固的早期偏析于石墨球附近的铁素体中,最后凝固部位的硅含量很低。
因此,对于中、厚型铸件,不可能通过提高硅含量来解决锰在晶界处形成碳化物的问题。
Si-Mo球墨铸铁中的硅含量相当高,对于铸造排气歧管之类的薄壁铸件,锰的负面作用不像常规铁素体铸件那样严重,一般说来,锰含量的上限值可以是0.4,美国SAE标准规定的上限值为0.5。
3)磷磷在球墨铸铁中是导致脆性的有害元素,其在铁素体中的固溶度随铁素体中碳含量的提高而降低。
铸铁中的磷含量如果在0.07以下,可固溶在铁素体中,对铸铁的性能影响不大;
超过固溶度以后,就可能析出分散的新相Fe3P(熔点1166);
含量更高一些,就可能出现二元磷共晶(铁素体Fe3P,熔点约1050)或三元磷共晶(铁素体Fe3PFe3C,熔点约953),析出于共晶团的边界,使铸铁脆化。
磷还可能使铁素体球墨铸铁的脆性转变温度提高。
此外,有报道说,提高铸铁中的硅含量,还可能增强磷的脆化作用。
Si-Mo球墨铸铁中的磷含量,一般都要求低于0.05,也有将上限值规定为0.07的。
4)硫总体而言,球墨铸铁中,硫是有害元素。
硫与稀土、镁、钙、锰等元素结合的能力很强,球化处理时,原铁液含有的硫首先与球化剂中的活性元素反应,耗用球化剂。
因此,通常都认为硫是反球化的元素,其在原铁液中的含量愈高,铸铁球化需用的球化剂量愈多。
高硫原铁液还会导致铸件产生浮渣缺陷。
球墨铸铁件表面出现的浮渣,主要是由硫化镁、氧化镁和硅酸镁组成的。
如浮渣中硫化镁含量高,在铸件与砂型的界面处,可能与大气中的氧反应(2MgSO22MgO2S),硫返回界面处的铁液,使铸件表面的球化衰退,出现片状石墨。
硫化镁还可能与型砂中的水分反应(MgSH2OMgOH2S),使铸件产生皮下气孔。
但是,硫又是球墨铸铁中不可或缺的元素。
球墨铸铁凝固过程中,最先结晶析出的是石墨,而石墨析出所依托的是异质晶核。
经球化处理的铁液,纯净度高,其中的硫、氧含量显著降低。
从热力学能位的角度看来,一些元素的硫化物比氧化物稳定,因而先形成MgS、CaS和MnS等硫化物,作为晶核的核心。
然后,在微细的硫化物上形成多种氧化物,这些氧化物又与SiO2作用,形成复合的硅酸盐外层,其与石墨晶格的匹配度较好,这就是析出球状石墨所依托的异质晶核。
因此,从石墨化生核方面考虑,原铁液中不能没有硫,其含量还不宜太低,尤其不宜时高、时低,最好保持在0.0100.015之间,生产薄壁铸件时尤应如此。
当然,原铁液还应该保留有一定的氧含量。
基于这样的认识,就会想到:
如果原铁液经球化处理后用含硫、氧的孕育剂进行孕育处理,应该有很好的效果。
这种设想,已在十多年前由欧洲同行的研究工作确认,采用含硫、氧的孕育剂,可以使球化率提高、石墨球数量增多、石墨球尺寸减小,因而可以从多方面提高球墨铸铁件的质量。
4、Si-Mo球墨铸铁的规格和标准迄今为止,国际标准化组织、欧洲标准化组织、美国的ASTM和日本标准化组织,都未发布有关Si-Mo球墨铸铁的标准。
我国标准GB/T94372009耐热铸铁件中,列有两种Si-Mo球墨铸铁(QTRSi4Mo和QTRSi4Mo1),化学成分要求见表2,力学性能要求见表3。
表2Si-Mo球墨铸铁的化学成分()表3Si-Mo球墨铸铁的力学性能要求美国汽车工程师学会标准SAEJ2582DEC2001用于高温条件的汽车球墨铸铁件也列有两种Si-Mo球墨铸铁,标准中规定硅含量、钼含量和布氏硬度必须符合要求,见表4。
表4对Si、Mo含量和硬度的要求碳、锰、磷、硫等元素的含量和残留镁量,标准中只提出适用于两种牌号的大致范围,供参考:
C3.303.80;
Mn0.100.50;
P0.050;
S0.035;
Mg0.0250.060。
实际生产中,铸造厂应该根据客户的要求和对铸件的具体条件,规定更为严格的成分控制范围。
至于对力学性能的要求,铸造ASTMA536标准规定的单铸试块,截取试样,预期的测定值见表5。
表5Si-Mo球墨铸铁力学性能的预期值(SAEJ2582DEC2001)实际生产中,由于铸件的几何形状和截面的冷却速率不同,自铸件本体截取试样测定的值可能与表5中的数值有所不同。
应该符合客户根据铸件用途提出的具体要求。
三、有关生产工艺的几个问题由于Si-Mo球墨铸铁化学成分和性能要求方面的特点,生产工艺方面不宜完全沿用常规球墨铸铁的方式,以下简单地提及以下几点,供参考。
1、熔炼理论上,熔炼Si-Mo球墨铸铁所需的原铁液,既可以用冲天炉,也可以用感应电炉。
实际上,当前应用的Si-Mo球墨铸铁件的大多是小型、薄壁铸件,单位时间需求的原铁液为量不多,而且要求控制的成分范围很窄,不宜用大型冲天炉熔炼。
小型冲天炉,在能耗、环保等方面又难以适应当前的要求。
因此,熔炼设备宜优先选用感应电炉。
炉前最好配备有光谱分析仪。
由于铸铁的硅含量比常规铸铁高,应该按要求的硅含量范围,用专用的标样校定光谱仪。
对钼含量的测定,也要经常校核。
碳含量,应以燃烧法的测定值为依据。
2、炉前的处理Si-Mo球墨铸铁的碳当量较高,生产壁厚20的铸件时,宜采用稀土含量低、或不含稀土的球化剂,以避免出现碎块状石墨。
由于铸铁中的硅含量高,有利于石墨化,尤其是对于薄壁铸件,球化剂的用量可以略低于常规球墨铸铁。
这样,既可以节省球化剂,又有利于控制铸态组织中的珠光体含量和碳化物。
国外一些铸造厂,将残留镁量控制在0.0200.025之间,效果很好。
当然,提出这一数值只是供参考而已,各铸造厂的最佳控制范围,要根据厂家的具体生产条件,如所用的球化剂、孕育剂、孕育方法、孕育剂加入量等,经实际试验后确定。
孕育处理方法一般都应该采用瞬时孕育方式,使孕育的衰退减至最小。
最好在出炉前,用碳化硅对原铁液进行预处理,以获得更好的显微组织。
3、防止铸件出现收缩缺陷Si-Mo球墨铸铁是过共晶成分,碳当量较高,而硅含量又较高,碳大都在铁液中脱溶、以初生石墨析出。
凝固过程的早期,奥氏体析出,又促使石墨球长大,而凝固后期析出的石墨相当少,石墨化膨胀的补缩作用降低。
因而,铸件产生缩孔、缩松之类收缩缺陷的倾向较大。
工艺设计时,要注意设置较大的冒口,而且补缩的距离不可太长。
4、冷隔缺陷及其对策生产Si-Mo球墨铸铁件、尤其是薄壁铸件时,易出现冷隔缺陷。
如何应对这样的问题?
不少人马上会想到提高浇注温度。
实际上,这种考虑是不够全面的,也是不很妥当的。
Si-Mo球墨铸铁中的硅含量较高,充型时,液流表面、紊流产生的液滴表面上,很快就会形成氧化膜,阻隔液流的对接。
这种情况,往往是铸件出现冷隔缺陷的主要原因。
不必要地提高浇注温度,只会使氧化膜的形成更快、更多、更厚,反而更易于造成冷隔缺陷。
为防止冷隔缺陷,浇注系统的设计应力求液流充型平稳,不宜采用阻流式浇注系统。
浇注系统中采用过滤片,不仅可以吸附氧化物,而且,如系统设计适当,紊流的铁液可以转换为平流,防止冷隔的效果很好。
5、铸件的热处理Si-Mo球墨铸铁中的钼含量较高,生产薄壁铸件时,组织中会出现一些珠光体、碳化物和次生相。
如果组织现珠光体含量不超过15、碳化物不超过5,铸件可不必经热处理。
虽然这种铸铁常温下的脆性较大,如果在铸件后处理过程中充分注意到这一特点,尽量做到轻取、轻放,一般都没有什么问题。
如果组织中珠光体、碳化物的含量较高,铸件就应该进行热处理。
在组织中不存在游离渗碳体的条件下,没有必要采用高温下的全退火,最适当的热处理工艺是在亚临界温度下退火。
硅含量为45的球墨铸铁件,应用非常广泛的亚临界退火温度是790。
在此温度下,珠光体和碳化物分解的方式不是通过相变,而是逐渐扩散。
将铸件加热到790,铸件厚度在20以下,保温1h。
厚度在20以上,每增加20,保温时间增加1h。
保温后,随炉缓慢冷却。
缓慢冷却的过程中,组织中的珠光体、碳化物会逐步分解为石墨和铁素体。
经亚临界退火后,既可以提高