完整word版甲醇合成催化剂分析解析Word文档格式.docx
《完整word版甲醇合成催化剂分析解析Word文档格式.docx》由会员分享,可在线阅读,更多相关《完整word版甲醇合成催化剂分析解析Word文档格式.docx(12页珍藏版)》请在冰豆网上搜索。
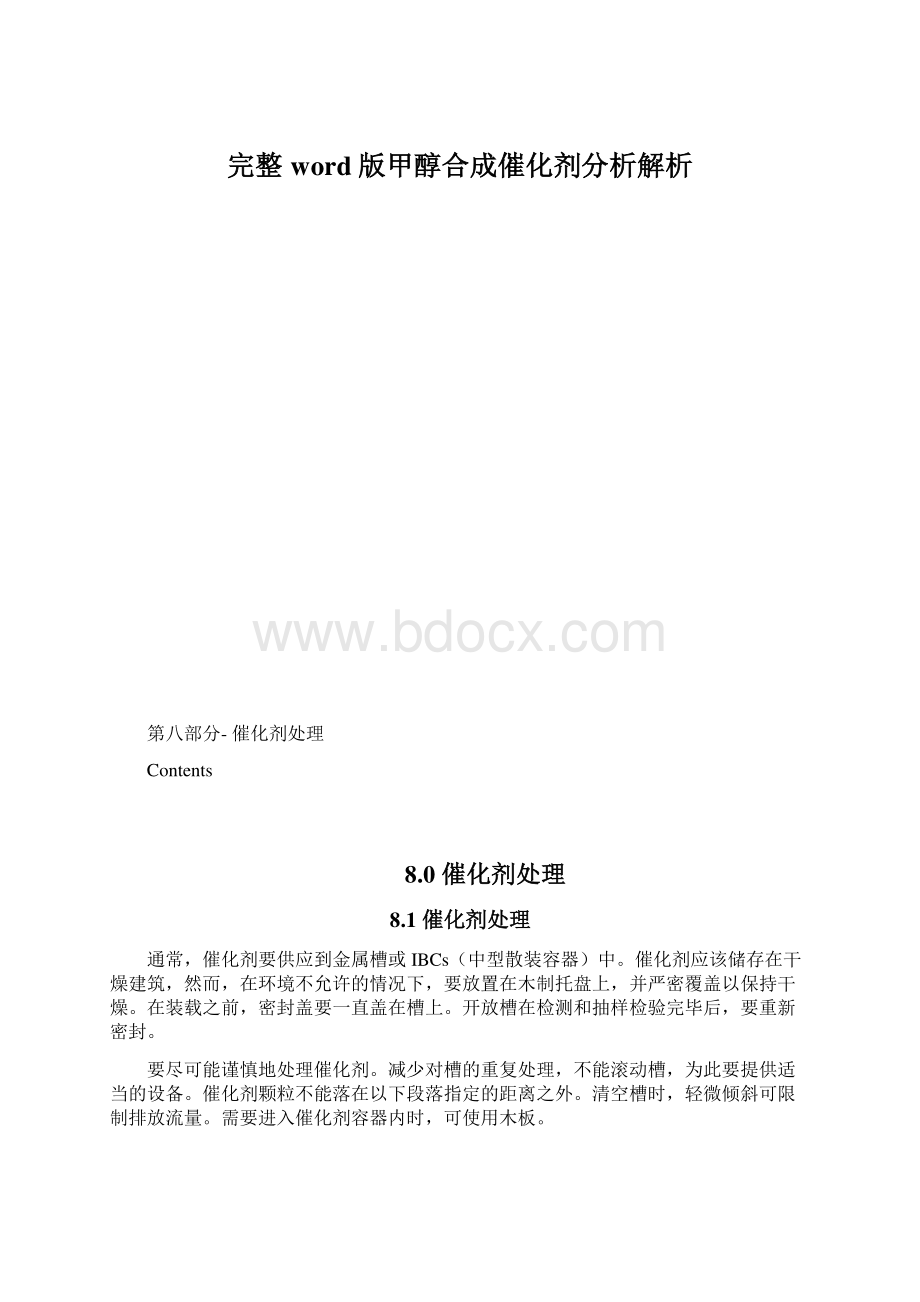
软管内要一直保持充分的催化剂,这样,催化剂通过软管开口到催化剂表面,最终落进漏斗里。
操作人员长期留驻在容器内时非常有必要的。
在这种情况下,要表明注意安全的标牌。
人工装载:
由容器外的一组工作人员将催化剂倒入10到15公升的吊桶。
吊桶通过绳索升至人行通道,随后在降至容器内的操作人员处。
朝不同的方向清空吊桶,以保证催化剂均匀铺开。
操作人员会使用厚木板分散自身的重量,以避免挤压催化剂。
这个方法很简单,还可以为催化剂提供一个低“落差”。
毛刷装载:
毛刷装载转化炉管的方法,已经被成功的采用了很多年。
这个技术可以用于甲醇1号转化炉管程的装载。
要求每500到1000米处,都有嵌入转化炉管程的半刚性柱子(带半刚性毛刷)。
当柱子逐步收缩时,添加一定剂量的催化剂。
8.2.1筛选筛选通常不建议对催化剂进行筛选,因为这样会产生更多的粉尘。
倾倒催化剂后,通常在每个槽的底部都会留有50mm的催化剂(绝大部分灰尘会积聚在槽底),所以很有必要对材料进行遮蔽。
尽管如此,在催化剂的运送过程中,有时也会不可避免的发生过度磨损的状况,因此,最好在装料之前遮蔽材料。
在操作过程中有可能会损害催化剂小球和DPT的质量,所以要特别注意。
或者可以在着手工作前请教催化剂供应商。
适当的筛选方法是将催化剂通过一个斜槽(由适当尺寸2x2mm的筛绢制成)。
如果使用振动筛的话,筛角和振幅必须具备调节性。
通常采用最小振幅。
持续进行振动调节,直到确定催化剂在筛选过程中未受到损害为止。
仔细观察催化剂和粉煤,确保不会过度覆盖。
在筛选的操作过程中,要对收集到的粉尘要进行检验。
数量应当低于1%。
如果超过这个量,要暂停整个操作过程,重新审核。
要记录粉煤的重量,并从槽排放到筛网的催化剂重量中扣除。
注意筛网过载,否则将会导致无效筛选。
8.2.2取样取样每次装料时,建议对催化剂进行取样,并由操作者保留,这样可以调查造成意外情况出现的原因。
取样的一个方法是在装料程序中,从槽里取样。
样品应该从每个取样桶的中心部位而不是末端提取,这样才能够得到具有代表性的材料。
接着,这些样品会结合在一起,构成催化剂床中500mm处催化剂的代表样品(重1kg)。
在铺平催化剂床,测量完相对深度后,对每一批代表高处和低处的样品进行记录。
另一个方法适用于装料时操作员在容器内的情况-平均铺平到300mm时,从床表面提取代表性样品。
每一层提取5份样品,中心位置一个,每90度方向一个。
这些单独的样品结合起来,构成该层催化剂的代表性样品。
所有的样品都要标注,这样标签就不会脱落,具体信息也不会被抹去。
标签内容包括:
装置,流体和容器取样时间取样槽数催化剂床顶部和底部范围内槽体成分的位置8.2.3合成气净化槽合成气净化槽合成气净化槽内要装载Puraspec2020吸收剂。
吸收剂相对较浓,容器内没有复合内件。
8.2.3.1容器装料容器装料时需要注意的事项:
吸收剂不能自由落在0.51米以外。
吸收剂要均匀分布在整个反应器表面上,避免将粉煤集中在一个区域,直接导致气体分布不均匀。
高局部压力不能直接施加在吸收剂上,这样的负荷由板支撑。
比如:
人体的重量可以平均受力于至少0.3平方米的区域。
8.2.3.2装载惰性支撑球在装载吸收剂前,先将惰性支撑小球填料到容器的底层。
直径为25mm惰性氧化铝瓷球的底层,装载在出口收集器周围和上部到底部正切线200mm以下的部位。
在直径为25mm瓷球上装载100mm厚的一层直径为13mm惰性氧化铝瓷球。
最后,在直径为13mm小球顶部,装载100mm厚的直径为6mm的惰性氧化铝瓷球。
每层在铺平后,才能进行下一层的装载。
容器内底部正切线的位置可能不太明显。
必要的话,可以参考容器图纸,得到焊接线到正切线之间的距离。
8.2.3.3装载吸收剂推荐的装载吸收剂的方法是用漏斗和sock。
将300mm的吸收剂装载喷嘴直接连接到容器入口喷嘴上方的吸入管路上。
这意味着容器的的人行通道仅供容器出入。
漏斗安装在装载喷嘴上方,附加到达容器底部的SOCK。
Sock的长度是可调节的,采用zippedsock,或者移开底部部件进行调节。
SOCK内部为平滑表面,且无磨蚀成分。
从容器开口运送吸收剂的速率,通过信号绳或类似工具控制。
SOCK的直径不能太大,否则它所承载的吸收剂重量会很难操纵。
SOCK内要一直保持填满吸收剂,这样,吸收剂只会落入漏斗,或从SOCK开口落到吸收剂表面。
或者,也可采用简单的吊桶装载吸收剂。
吊桶上安装绳索使其从人行通道降至容器内部。
无论是用漏斗,SOCK,还是用吊桶,都有必要安排一个操作员长期驻留在容器内部。
在这种情况下,必须标明注意安全的标签。
8.2.3.4装载惰性球顶层将150mm厚的直径为13mm的惰性氧化铝瓷球,小心装载到吸收剂床顶部,并均匀铺平。
8.2.4甲醇转化炉甲醇转化炉甲醇反应器装载了Katalco51-9S甲醇合成催化剂。
因为两个转化炉内都有复合内件,所以必须制定特殊的装载程序。
装载前检查转化炉,确保转化炉干净清洁,所有内件和附件都安装正确。
必要的情况下,转化炉程序面要进行化学清洗,如4.2.5.3.所示。
以下程序为装载催化剂一种方式,实现终点目标:
轻柔地处理催化剂,减少粉煤和灰尘均匀装载催化剂尽快装载催化剂通过达到均匀的密度,减少灰尘和粉煤,优化催化剂性能。
甲醇转化炉的准备1.打开顶部和底部人行道2.通过对转化炉目视检查:
a.底部人行道b.顶部人行道3.如果转化炉内部出现大量铁锈,需要进行化学清洗(清洗程序的详细说明没包含在这个记录中)8.2.4.1一号甲醇转化炉催化剂装载程序设备要求下列设备要求装载到甲醇转化炉上。
用于装载惰性球的合适尺寸的吊桶半刚性管(4”to6”),最好用在1.5到2.0m长的部位。
注意:
半刚性管在装载的时候,可以轻松地保持原形。
但时间久了,会有所磨损磨短。
尽管帆布软管也很容易被磨损磨短,但折叠在内件上后,会呈封闭状态。
建议两种软管都采用,通过实验可以证明哪种软管效果更好。
软管顶部采用漏斗长8米的软质杆装载惰性球1.经过底部人行道手工装载直径为50mm的惰性氧化铝瓷球。
可能需要一个人进入转化炉,一个人在底部人行道旁配合工作。
直径为50mm的球层不需要很平坦。
将球装载到转化炉底层的可及区域,与人行通道底部齐平。
条件允许的情况下,尽可能多的装载直径为25mm的惰性球,确保人行通道可以完全关闭。
关闭人行通道底部,包括任何催化剂阻滞塞。
将剩下的直径为25mm的惰性球倒入转化炉管程。
要求用柔质杆检验转化炉底部球层的高度。
由于转化炉管程内件直径的尺寸,要特别注意筛选25mm的惰性球,避免尺寸过大的球阻塞管道。
直径为25mm的惰性球层大致平坦后,将管板下一层厚150mm,直径为25mm的惰性球倒入转化炉管程。
通过检验,直径为13mm的惰性球形成到达管板底部的均匀球层后(通过柔质杆测定),可以增添直径为6mm的惰性球,与底部管板厚度齐平。
2.将直径为6mm的惰性球装载至要求的高度,最简单的方法是把定量的球倒入每跟转化炉管道。
催化剂装载甲醇合成气催化剂可以通过漏斗和斜槽或吊桶直接装载。
如果采用漏斗和斜槽,这个临时的漏斗要支撑在甲醇转化炉的顶部。
漏斗由低碳钢制成,这样可以清除表面的所有灰尘。
漏斗要大到可以容纳3个催化剂槽和斜槽(连接到漏斗基座,通过催化剂装载喷嘴,最后进入反应器)的成分。
斜槽由消防水带(粗布)或柔质塑料管(直径大致为4”)制成,在斜槽末端附近绑一根质量好的绳子,定位负荷区以上的部位。
1.将催化剂简单倒在管板上,可以用吊桶或软管,随后将其刷入转化炉管道。
2.将催化剂装载到管板的顶部边缘3.关闭顶部人行通道。
8.2.4.2二号甲醇转化炉催化剂装载程序设备要求要求采用以下设备装载甲醇转化炉用于装载惰性球的从中间切割的半钢性管半刚性软管,最好用在1.5到2.0米长的部位。
软管顶部采用漏斗需要一个靶子控制容器内部的氧化铝珠装载惰性球由于转化炉“D”型集管的分散性,惰性氧化铝珠要通过7个手孔装载。
1.通过底部人行通道尽量装载直径为50mm的惰性球,然后用支撑在“D”型集管上的檐槽,软管和漏斗,将剩下的直径为50mm的惰性球。
这些球要装载至内部分流管的底部。
2.直径为50mm的球层不需要很平坦。
将球装载到转化炉底层的可及区域,用靶子将其摊开。
3.依照同样的方式,将直径为25mm的氧化铝珠装载至”D”型集管底部,用靶子将其尽量铺平。
4.将直径为13mm的氧化铝珠装载到”D”型集管一半的高度,约为200mm,用靶子铺平。
5.最后,将直径为6mm的氧化铝珠(厚约160mm)装载至“D”型集管的顶部,用靶子铺平。
大多数氧化铝珠要用檐槽装载至中心集管,然后用靶子通过手孔将转化炉底部的氧化铝珠铺开。
催化剂装载甲醇合成气催化剂可以通过漏斗和斜槽直接装载。
这个临时的漏斗要支撑在气体入口喷嘴N2上甲醇转化炉的顶部。
漏斗由低碳钢制成,这样可以清除内表面的所有灰尘。
斜槽由消防水带(粗布)或柔质塑料管(直径大致为4”)制成,在斜槽末端附近绑一根质量好的绳子,定位负荷区以上的部位。
1.为避免催化剂阻塞管道,在装载过程中用合适的帽或塞关闭每一个管道。
帽与转化炉一同提供。
2.在反应器内安装循环木质平台,覆盖甲醇转化炉的直径。
3.平台平均分为30块,每块都可以从完整的覆盖面上移除。
每一块分都要有通过顶部手孔的合适尺寸。
编号后,小心放置在筒颈顶部。
按照以下程序,直接从槽里装料筛选好的催化剂。
1.移除一块木质筒颈,将催化剂斜槽架在管道开口部位上。
2.缓慢清空3个槽内的催化剂至漏斗,每个槽装有大概200kg的催化剂。
漏斗内的成分分流到开口区域,这样,通过斜槽绳索控制流量,可以均匀地铺开排放物。
3.Afterthe3drumsareloadedintothefirstsection,replacethewoodencoverandremovethenextsectionreadyforloading.Recordthedrumnumbersandweightofcatalystloadedagainstthereactorcovernumber.3个槽内的成分装载到第一部分后,替换木盖,移除下一部分准备装载。
对照反应器盖的编号,记录装载催化剂的槽编号和重量。
4.同样地,清空另外3个槽内的催化剂至漏斗,装载至反应器的第二部分。
旋转装料会避免催化剂全部流到中心,然后滑向转化炉壁。
利用这样的装料技术可以减少催化剂粉煤的产生(这样会导致流量分布不均及其他问题)。
5.催化剂落在管道之间,管道支架会降低催化剂的下落速度。
通过移动斜槽平稳装载催化剂。
6.在随后的每一部分填料过程中,该部分的管道会振动一段时间。
7.反应器装载到大约一半,即所有部分都完成第一次装载后(每部分3槽催化剂含量),暂停进料,将30个部分分别降低到一定程度,确定催化剂表面的高度。
8.确定催化剂进料量,填充空余区域,同时,计算装载物的容积密度,并与参考值进行对比。
这样可以对要求装料高度所需的最后重量有正确的估量,也可以显示装料的不均匀分布。
9.重复每部分3槽催化剂的装载,再次检验装载物的容积密度。
10.检验催化剂的最终重量,完成所有装料。
填料时,将要求高度(混合器高位箱底部500米以下)处的顶部表面摊平。
11.装载到一定量,并达到要求的催化剂高度后,安装气体分流器。
12.完成最终的内部检验后,移除转化炉上的所有负荷齿轮。
做详细的检查,确保所有进入反应器的设备都被移除,包括所有端盖和附件。
13.最后,关闭顶部手孔。
8.3催化剂卸载催化剂卸载羰基风险:
吸收剂或催化剂会受到进料器内镍和铁羰基化合物中镍和铁的污染。
如果催化剂冷却到含一氧化碳气体以下的温度,会形成挥发性羰基化合物。
因此,所有催化剂在高温情况下,都要用氮气清洗。
操作者要意识到尽管经过清洗,羰基化合物仍有可能存在。
需做适当的警告。
细节详见3.18.3.1合成气净化槽合成气净化槽吸收剂按照以下程序,依靠来自底部的重力流从容器内排出。
或者,也可以使用大型机动真空抽提成套设备。
任何推荐程序都要经过吸收剂卖方的审核。
移除吸收剂时要特别注意,因为硫化物吸收剂可能自燃。
1.在每分钟最大比率为0.1-0.2MPa的条件下,降低反应器内的压力,如设备机械设计所规定的。
火炬管线上容器的下游设备球心阀,用于容器到火炬的减压。
2.用低压氮气清洗容器和所有上游设备和管线。
在气流作用下,将反应器冷却到40C度以下。
3.在未使用过的催化剂排放喷嘴上,用氮气对喷嘴N6A/B进行清洗,为容器内供应适当压力的氮气,确保排放过程中无气体进入容器。
4.喷水要能够达到冷却的效果,用于移除吸收剂的排放喷嘴上的喷嘴N6A/B可发挥这样的作用。
如果有必要进行喷水的话,注意不要分散废弃的吸收剂,也不能包含液体溢流物。
5.用适当的排气方式,将催化剂排放到合适的容器中。
可以是盛放氮气或二氧化碳等惰性气体的槽或催化剂箱。
装满排放的吸收剂后,进行密封,防止气体进入。
只有卸料口可以开放,以避免气体通过烟囱效应进入容器。
铰接盖或闸床的外形可用于控制吸收剂流量,减少气体进入容器的几率。
6.密封惰性气体容器内的吸收剂另作处理。
8.3.2甲醇反应器甲醇反应器在还原状态下的甲醇合成催化剂具备自燃性。
因此在催化剂能够安全卸载前,要进行轻度氧化。
这个程序描述如下。
一旦进行氧化程序,催化剂应该被完全氧化。
但是,由于催化剂床层分布不均匀,不能够保证被完全氧化。
氧化了的催化剂可以通过反应器底部的催化剂卸载喷嘴抽出或卸载。
未被氧化的催化剂应该在氮气环境下,通过催化剂排放喷嘴排出。
在催化剂卸载期间,需供应水以防催化剂发热。
催化剂不能和任何可燃材料接触,如,木材,橡胶等。
在卸载程序期间,应该检测转化炉内催化剂的温度。
8.3.3甲醇转化炉催化剂氧化甲醇转化炉催化剂氧化8.3.3.1概要在催化剂氧化过程中的任何时候,如果发生引起操作员注意的意外或原因不明的升温或其它情况,应立即停止添加氧气(仪表空气)。
由于在循环器吸入口只有一个可以确保混合物形成的空气附加点,所以甲醇转化炉要依次进行氧化。
这样,氧化曲线会首先穿过甲醇2#转化炉R2001,其次会穿过R2002。
重要的是,两个甲醇转化炉在完成每个阶段的程序之后,才能进入下一步程序。
另外,如果气流暂停,必须慢慢地再次输入,且增加量不能超过氧浓度的0.25vol%。
催化剂床的温度在每次递增后,要恢复稳定。
循环氮气的质量流与回路压力有直接的关系。
因此空气流量必须与压力成正比,以达到要求的氧气浓度,保持峰值温度在允许范围内。
因为在升汽转化炉内没有测定的温度,所以空气流速和回路压力之间的关系是至关重要的。
气流和回路压力的比率(通过低倍测距仪PIC-20016测定)显示在有上限信号器的FFI-20008上。
协助进行氧化反应的FFI-20008所给出的值以t/h/MPa(a)为单位,象征着甲醇回路的氧气浓度。
如果需要精确数据,可以利用S-5A-20009进行采样。
对氧化程序的进展进行评估,添加的空气总量由FQI-20005监测,并与催化剂完全氧化计算的总量相比较。
两个转化炉中催化剂的完全氧化消耗氧气约10,200kg,这相当于44,000kg的空气(34,000Nm)。
两个甲醇转化炉(R2001和R2002)必须同时进行氧化。
完成氧化程序花费的时间取决于氧气摄入速度和能够达到的循环速度。
但是,我们期望完成氧化(包括氧气渗透)花费的时间范围是在24-48小时之间。
8.3.3.2详细程序1.按照正常停车程序进行降压,从回路排出液体。
氮气清洗系统直到氢气浓度降低到或低于2vol%的安全极限。
如果方便,利用排泄器ZM-20002和甲醇回路开车加热器E2007的小量高压蒸汽,将甲醇一号转化炉蒸汽侧温度保持在150C。
用氮气将回路压力减至0.39MPa(a)。
2.打开增压阀HV-20002和HV-20010,关闭阀门HV-20003和HV20008,使循环气流经甲醇回路开车加热器,进入甲醇二号转化炉顶部,采用与还原反应时同样的回路气路结构。
3.氧化反应开始前,确保回路与分离界区的合成气进料,在主要进料管路和还原反应管路上采用双阻塞泄放布局将其分离。
合成气净化槽V2001和合成气压缩机C1901,通过在合成气净化槽下游安装双隔断分离阀将其分离。
粗甲醇过滤装置S2001A/B,通过关闭过滤器上游管线的断流阀和眼圈盲板将其分离。
回路清洗洗涤柱T2001和氢气回收工艺包Y2201,通过关闭回路清洗管线上的分离阀将其分离。
到合成气进料器的除盐水管,通过关闭XV-20001将其分离。
氮气管道,通过关闭管线LN-20002和LN-19004上的眼圈盲板将其分离。
火炬系统,通过关闭到火炬管道RG-20014和RG-20016的回路降压器上的眼圈盲板;
隔离清洗管线和所有净化和回路取样点;
隔离所有的净化和回路在线分析仪将其分离。
放空到火炬的压缩机密封气要转移到大气。
4.打开放空管线(VG-20006)和仪表空气管线(IA-20003)上的眼圈盲板。
5.通过HS-20005挑选氧化模式,这样PIC-20016就会受到PV-20017的控制。
6.开启合成气压缩机/循环机(C1901/C1902)。
7.氮气回流条件下运行的合成气压缩机可供应低压氮气。
将循环机入口的回路压力增至0.70MPa(a)。
8.利用到排泄器ZM-20002和甲醇回路开车加热器E2007的高压蒸汽,将转化炉加热(或冷却)至150C。
9.在添加空气到回路前,确定氢气浓度在安全范围内。
即使在降低回路压力后,氢气仍会从催化剂中缓慢释放。
如果在程序上有所耽搁,就有可能将氢气积聚在系统中。
所以,在程序的任意暂停后,都要对氢气进行分析。
检验氢气是否在2vol%以下和添加气体之间的间隔时间越短越好。
因为在催化剂的作用下,氢气会与氧气发生反应。
所以一旦开始添加气体,循环气体中的氢气浓度最好能立即下降至0。
10.第一阶段经由FV-20005缓慢添加仪表空气,为甲醇1号转化炉提供入口浓度为0.25vol%的氧气(在取样点S-6-20005测定)。
11.一旦开始添加空气,经由PV-20017和管道VG-20006将气体吹扫至大气来控制回路压力,保持气流量。
12.通过把槽压控制在0.389MPa(g),将氧化过程中1号转化炉闪蒸槽(D2001)的温度保持在150C。
有必要继续将高压蒸汽通过转化炉壳体注入主要蒸汽/水循环机。
13.逐步添加空气,使甲醇1号转化炉(R2001)入口氧气含量达到0.84vol%,为转化炉提供大约270C的峰值温度。
在甲醇转化炉中,任何位置的温度值都要低于275C。
在高温或合成气压缩机/循环机跳闸的情况下,必须立即停止供应空气,冷却甲醇转化炉。
在二号甲醇转化炉中,由于热电偶间隔相对较大,测量的峰值温度不一定能反应床层的实际峰值温度。
在氧化反应过程中,预期一号甲醇转化炉R2001中的峰值温度约为200C,二号甲醇转化炉R2002为275C。
例如,二号甲醇转化炉进入氧化反应约4小时时,测量的最高温度是275C。
因此必须保持最大允许入口氧气浓度为0.84vol%,不能增加。
14.严密监测来自甲醇转化炉出口气体的氧气分析值(在取样点S-620006和S-6A20008处测定),因为反应前沿到达催化剂床边缘时,会发生氧气突破。
15.当反应前沿到达甲醇2号转化炉R2002催化剂床边缘时,氧气的工作速率会降低。
为将入口甲醇转化炉的氧气含量保持在0.84vol%,需逐步减少空气供应量。
16.监测热回路交换机E2003,合成气净化加热器E2001和锅炉给水加热器E2004下游低点防护罩内的高度,必要的情况下将其清空。
17.第二阶段氧气不发生反应时,应停止供应空气,在可控方式下将甲醇转化炉温度升高到200C。
转化炉温度在200C的情况下,重复以上的第8步到第10步,因为氧气会被再次消耗。
为将预期峰值温度保持在275C,这个阶段的最大允许氧气浓度限制在0.5vol%。
18.第三阶段观察完温升的最终迹象后,留一段时间用于氧气渗透。
增加甲醇1号转化炉R2001入口的氧含量,随后保持在10vol%,将两个甲醇转化炉温度增至240C。
继续观察第12步中所指示的温度范围。
这样的状态要保持几个小时,直到发现新的升温状况。
19.排放催化剂前,将甲醇转化炉冷却到周围温度。
缓慢减少闪蒸槽的压力,以25-50C/h的速率持续注入高压蒸汽,将甲醇1号转化炉温度降至100C,随后停止高压蒸汽的流动。
20.此程序会产生完全氧化的催化剂。
但是,由于催化剂床分布不均,很难保证彻底的氧化反应。
对于在催化剂排放、运送及进入容器的过程中,可能会出现的空气中氧气耗尽,或催化剂中气体耗尽的情况,需采取适当的预防措施。
在甲醇转化炉催化剂氧化过程中温度和氧气浓度极限Stage阶段SteamTemp(C)蒸汽温度MaxO2Conc.(vol%)最大氧气浓度11500.8422000.53220108.4催化剂保护催化剂保护为保证环保地处理废弃催化剂,