汽车保险杠零件高分子材料选择与加工本科毕业论文Word下载.docx
《汽车保险杠零件高分子材料选择与加工本科毕业论文Word下载.docx》由会员分享,可在线阅读,更多相关《汽车保险杠零件高分子材料选择与加工本科毕业论文Word下载.docx(10页珍藏版)》请在冰豆网上搜索。
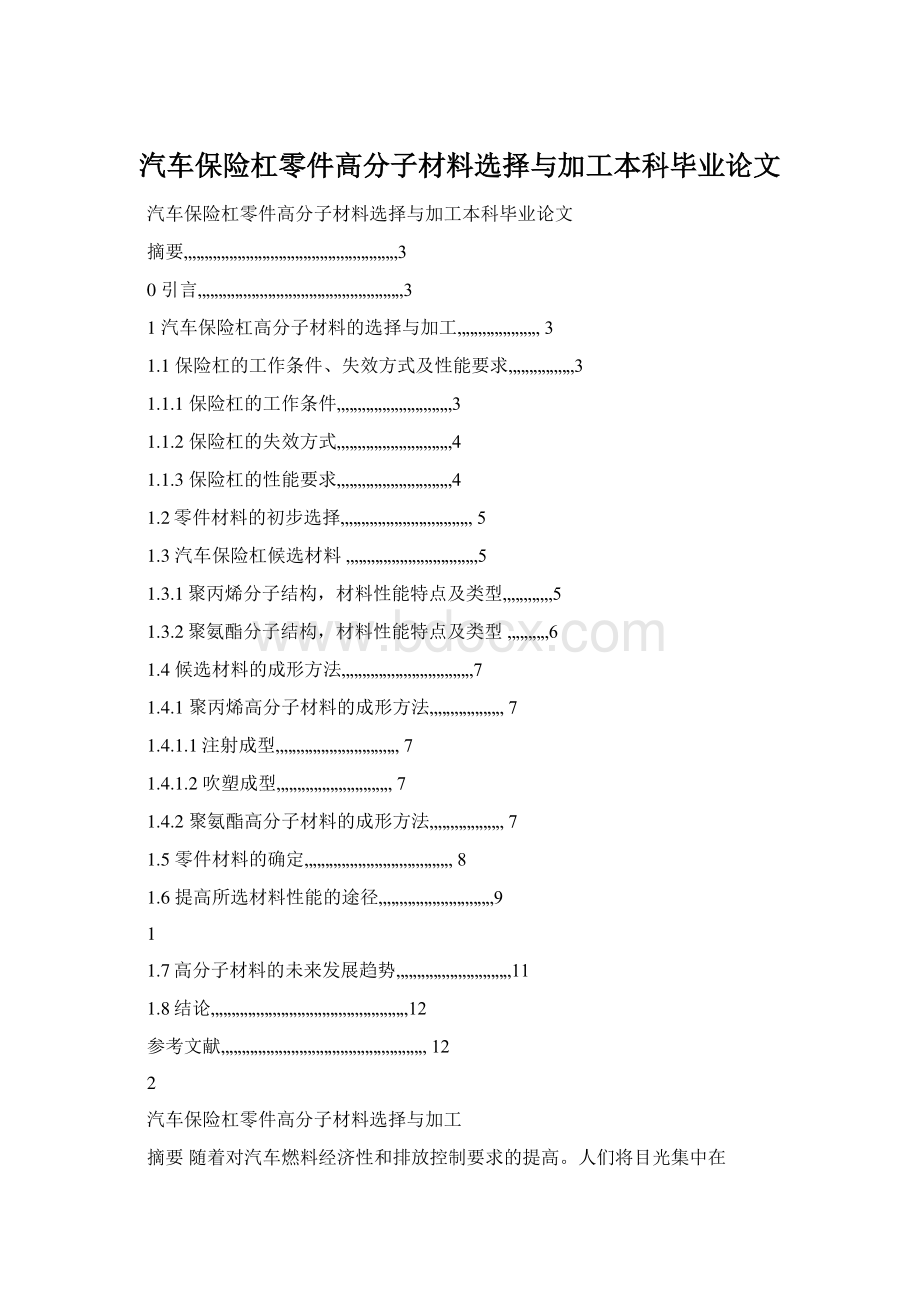
但是往往在外观发生变化时,保险杠作为防护装置性能本身就很有可能发生了改变,所以,两者可以一起来看,则可以得出保险杠失效的形式有以下几点:
1、破裂、裂痕2、外观变形、软化3、表面龟裂、粉化、褪色4、产品装配松动5、装配后与周边配合件之间的间隙和断差不理想6、产品产生缩痕7、前保险杠再有两侧支架断裂,强度不够8、漆面附着力差1.1.3保险杠的性能要求保险杠性能的要求随其失效形式和工作条件决定。
其性能要求有:
1、具有良好的冲击韧性,在其断裂破坏时能吸收足够多的能量2、抗老化性能好43、温度变化时,材料的延伸率较小4、在雨水、暴晒下不易发生化学、物理上的变化5、强度与刚度高,不易发生变形1.2零件材料的初步选择热塑性聚氨酯弹性体由于减震、柔韧和耐磨性能好,可制备轴衬、轴瓦和轴套类配件;
由于弹性好,耐屈挠、耐疲劳和耐油性能优,可制备护套类配件;
由于气密性能和抗切割性能好,可制备垫圈、垫板和垫片等密封配件;
由于尺寸稳定性好和冲击强度高,可制备气囊、保险杠等配件。
聚丙烯材料密度轻、易回收,通过改性的手段,特别是LFT-PP,聚丙烯已经进入汽车工程塑料的领域,聚丙烯因其优异的性价比,在汽车内外饰件中得到广泛应用,特别是应用在汽车的前后保险杠上。
所以我的候选材料为聚氨酯和聚丙烯。
1.3汽车保险杠候选材料1.3.1聚丙烯分子结构,材料性能特点及类型聚丙烯(简称PP)是由丙烯聚合而制得的一种热塑性树脂,分子式为C3H6n。
由于分子结构中有甲基的存在,在聚丙烯分子链节上存在不对称碳原子,按甲基排列位置分为等规聚丙烯,间规聚丙烯和无规聚丙烯。
甲基排列在分子主链的同一侧称等规聚丙烯;
若甲基无秩序地分布在分子主链的两侧称无规聚丙烯;
当甲基交替排列在主链的两侧称间规聚丙烯。
通常生产的聚丙烯树脂中,等规结构的含量约为95%,其余为无规或间规聚丙烯。
工业产品以等规聚丙烯为主要成分,由于甲基在空间的规则排列,聚丙烯结晶度较高,力学性能及软化点也高。
此外,通常聚丙烯类塑料也包括丙烯与另一种烯烃单体(或多种烯烃单体)共聚而成的无规共聚物。
聚丙烯通常为半透明无色固体,无臭无毒。
它的结晶度一般在70%以上,结33330.935,Kg/0.85,Kg/晶体密度为,非结晶体密度为,通常聚丙烯10m10m330.9,Kg/:
C的密度为,是最轻的通用塑料。
聚丙烯熔点在170,热变形10m:
C:
C温度为150;
制品可长期在110以下使用,即使使用温度达90,其强度:
C也无明显下降;
100也保持常温强度的一半以上。
聚丙烯的拉伸强度比聚乙烯,聚苯乙烯和ABS等都高,但韧性较低。
经过牵伸的聚丙烯带具有很高的韧性和极58好的弯曲疲劳寿命,经反复折叠次也不断裂。
但由于聚丙烯含有叔碳H原子,10较活泼,易与大气中的氧反应生成过氧化物,然后分解成羟基而引起主链断裂,所以不加稳定剂的聚丙烯制品耐光、热、氧等性能很差。
聚丙烯树脂的基本性能项目数值项目数值吸水率0.03,洛氏硬度R80,(24h)/%0.041002拉伸强度/MPa30,392,3冲击强度/(kJ/)m16,cm断裂伸长率/%100,300体积电阻率/,10拉伸模量/GPa1.1,1.6电压击穿强度/(kV/mm)206弯曲强度/MPa42,562.0Hz介电常数/10,2.6压缩强度/MPa39,56耐电弧性/s136,185热膨胀系数1.1热变形温度/(负荷110,1,4:
C,116(0.46MPa),/:
C10成型线收缩率1.0,2.0/%1.3.2聚氨酯分子结构,材料性能特点及类型聚氨酯热塑性弹性体又称热塑性聚氨酯橡胶,简称TPU,是一种(AB)n型嵌段线性聚合物,A为高分子量(1000-6000)的聚酯或聚醚,B为含2-12直链碳原子的二醇,AB链段间化学结构是用二异氰酸酯,通常是二苯甲烷二异氰酸酯(MDI)连接。
热塑性聚氨酯橡胶靠分子间氢键交联或大分子链间轻度交联,随着温度的升高或降低,这两种交联结构具有可逆性。
在熔融状态或溶液状态分子间力减弱,而冷却或溶剂挥发之后又有强的分子间力连接在一起,恢复原有固体的性能。
氨酯弹性体是聚氨酯合成材料中的一个品种,由于其结构具有软、硬两个链段,可以对其进行分子设计而赋予材料高强度、韧性好、耐磨、耐油等优异性能,6它既具有橡胶的高弹性又具有塑料的刚性,被称之为“耐磨橡胶”。
聚氨酯弹性体具有很好的抗拉强度、抗撕裂强度、耐冲击性、耐磨性、耐候性、耐水解性、耐油性等优点。
1.4候选材料的成形方法1.4.1聚丙烯高分子材料的成形方法1.4.1.1注射成型聚丙烯保险杠普遍采用注射成型工艺,其主要优点是,可成型形状比较复杂的产品、生产效率较高、能赋予制品必要的刚性等优点。
其缺点是,必须采用流动性较佳的原料,制品的坚固性较差,受冲撞时易断裂、成本高,小批量生产成本高。
我国聚丙烯保险杠成型均采用注射成型。
如上海桑塔纳轿车保险杠由江苏省江阴塑料有限公司用北京化工研究院的保险杠专用料注射成型。
一汽奥迪车保险杠由铁岭市橡胶制品厂以国产的PP/EPDM共混料为原料,引进日本模具和宇部兴产公司ST2500机,采用注射成型,机械手自动取件生产保险杠,产品性能超过德国同类产品。
1.4.1.2吹塑成型高分子PP共聚物聚合技术的开发,随着吹塑成型装备和操作技术的不断改进,以及模具设计和制作技术的进步,目前国外已经能够采用吹塑成型技术来生产聚丙烯保险杠。
吹塑成型与注射成型相比具有以下优点:
可成型高分子量PP共聚物,极大地提高产品的低温韧性;
产品具有很高的刚性和弯曲强度;
外观质量大幅度改善;
相对注射模具而言,吹塑模具不仅结构简单、制作容易、价格低廉,且易于更改产品的外形设计。
其缺点是:
成型周期较长;
表面光洁度略差。
德国Hoechst公司已生产出PPH8018吹塑级PP专用料,吹塑模塑技术成功地用于制取保险杠。
美国GE公司生产的PC/PBT合金材料吹塑保险杠已用于Ford汽车上;
Himont公司的TPO树脂已吹塑成卡车保险杠;
Borg-Warner公司采用CycolacLXB吹塑级ABS已成功吹塑外观漂亮、冲击性能良好的汽车保险杠。
1.4.2聚氨酯高分子材料的成形方法反应注射成形注射成型是将塑料在注射成型机料筒内加热熔化,当呈流动状态时,在柱塞7或者螺杆加压下,熔融塑料被压缩并向前移动,进而通过料筒前端的喷嘴以很快的速度注入温度较低的闭合模具内,经过一段时间冷却成型后,开启模具,顶出制品。
但随着注塑尺寸和长泾比的增大,在注塑期间要保证聚合物熔体受热的均匀性和足够的和模力就变得相当困难了,而反应性注塑成型可克服这一困难,其实质是在模具中完成大部分聚合反应,是注射物料黏度可降低两个数量级一以上。
此方法操作简单,镀层均匀,外观良好,具有有机物保护层。
1.5零件材料的确定聚氨酯具有良好的耐热,耐油,耐溶剂性能,韧性强,粘接性和弹性优良,但加工性能,耐寒性,耐水解性差,加工和在回收利用成本高。
聚丙烯具有许多优良特性:
1、相对密度小,仅为0.89-0.91,是塑料中最轻的品种之一。
2、良好的力学性能,除耐冲击性外,其他力学性能均比聚乙烯好,成型加工性能好。
3、具有较高的耐热性,连续使用温度可达110-120?
。
4、化学性能好,几乎不吸水,与绝大多数化学药品不反应。
5、质地纯净,无毒性。
6、电绝缘性好。
7、聚丙烯制品的透明性比高密度聚乙烯制品的透明性好。
8、价格便宜。
聚丙烯的成形方法相对成熟。
具体表现在:
以小本体聚丙烯(PP)为基料通过与共聚聚丙烯(CPP)、聚烯烃弹性体(POE)、滑石粉以及其他助剂共混改性制备汽车专用料。
当PP:
CPP:
POE:
滑石粉30:
35:
15:
20时,再配以适量的偶联剂、氧合抗氧剂、降温母粒等,制得的共混料完全可以满足汽车保险杠性能要求。
性能参数见表2。
产品性能数值,16g,()熔体流动速率/10min拉伸屈服强度/MPa19断裂伸缩率/%350,147kJ,悬臂梁缺口冲击强度/m:
C负载下热变形温度(0.45MPa)/95收缩率/%0.96以PP、EPDM、CaCO3等为原料研制的保险杠专用材料的拉伸强度、弯曲模量值均较高,材料成型流动性能良好的成型模缩率稳定,符合汽车保险杠材料8及总成性能指标规定、要求。
向聚丙烯中加入0.11%的晶型成核剂,经过双螺杆挤出机造粒,制得晶型聚丙烯。
结果表明,晶型聚丙烯的悬臂梁缺口冲击强度可达38kJ/m,力学性能指标达到汽车保险杠的要求。
并通过注射时加入碳酸钙刚性粒子增韧母粒的方法,解决了晶型PP模塑收缩率大和表面漆膜附着性差的缺点。
综上所述,作者本人选择聚丙烯就为汽车保险杆的最终材料。
1.6提高所选材料性能的途径聚丙烯是综合性能优良的一种通用塑料,但聚丙烯本身低温性能及抗冲击性能差、耐老化性及尺寸稳定性差,难以满足汽车保险杠对材料性能的苛刻要求。
因此,在汽车保险杠中使用的聚丙烯材料均为改性聚丙烯。
根据汽车行业对保险杠的要求,以及保险杠材料构成上的差异,PP汽车保险杠专用料可以分成以下几个基本类型。
1)聚丙烯与弹性体共混料聚丙烯共混改性是用增容剂、增强剂、填充剂、偶联剂、交联剂、熔体指数调节剂以及抗老化剂等与聚丙烯基料共混,使聚丙烯改性,大幅度提高其性能。
是生产PP保险杠专用料采用各种合成橡胶和PP进行共混改善PP的低温韧性,的传统工艺。
大部分保险杠专用料采用EPDM增韧。
目前国外还有用SBS、SEBS(苯乙烯-乙烯-丁二烯-苯乙烯共聚物)、氢化SBS等增韧,或EPDM与SEBS、EPDM与PE并用等。
我国保险杠专用料则主要采用PP/EPDM共混改性。
影响共混料性能的主要因素有:
基础树脂的平均分子量、分子量分布、共混料中各组分的比例和特征,以及对橡胶的交联处理等。
随着基础树脂平均分子量的提高,韧性将得以改善,但流动性会明显下降,从而给加工带来困难。
解决途径有两个:
(1)过氧化物热降解技术目前认为比较理想的方法是采用过氧化物热降解技术,由分子量较高的基础树脂来制取所需的高流动性材料。
用此技术生产的树脂,与具有相同熔体指数的直接聚合技术合成的树脂相比,分子量分布窄、加工性能好(不易翘曲)、刚性和低温耐冲击性能均较高。
国外许多厂商均采用这一技术来制造PP保险杠13专用料,如德国Hoechst公司的PPN8018,Huls公司的4402L,美国Himont公司的8623,Exxon公司的9146,日本东燃石油化学公司的EL-08-3和三菱油化公司的BX2D和BX4A等
(2)动态硫化技术动态硫化是对含有橡胶的橡塑共混料硫化的过程,其中橡胶在高剪切条件下硫化,结果橡胶交联,同时以“微粒凝胶”的形式分散在聚烯烃基质中。
动态硫化是在橡胶的硫化温度或高于硫化温度下混合橡胶和塑料组分后实现的。
混合用设备可采用密炼机、双螺杆挤压机等。
经动态硫化后的共混料在橡胶相内部形成交联结构,同时在橡胶相和塑料相之间形成一定程度的共交联结构。
通过此方法制成的EPDM/PP保险杠专用料与传统的共混方法相比,具有更好的耐热性、流动性、均衡的刚性和韧性。
国内有些单位采用动态硫化法生产或研制保险杠专用料。
如扬子石化公司研究院、金陵石化公司等。
中科院长春应用化学研究所以EPDM增韧PP,采用对共混料进行可控降解的方法,使物料的熔体指数在4g/10min16g/10min范围内任意调节,用二异丙苯过氧化物作交联剂,使橡胶相内部形成部分交联结构,同时在橡胶相和塑料相之间形成一定程度的共交联结构,使材料的拉伸强度和断裂伸长率有明显提高;
通过加入适量的滑石粉、碳酸钙等无机填料,材料的弯曲强度、热变形温度和硬度不致有明显的下降。
当共混料中橡胶含量控制在15%35%之间时,所得PP/EPDM共混料的常温和低温冲击强度能提高240倍,其各项性能达到国外同类产品水平,该项研究成果已用于生产“奥迪”汽车的保险杠。
2)PP/EPDM型反应器共混料随着催化剂的不断改进,目前已能采用两步串联气相聚合技术生产橡胶含量高的优质耐冲击PP共混料。
通过提高乙烯含量及控制乙烯单体引入PP大分子链上方式的不同,不仅能获得韧性较好的产品,还能在一定范围内调整聚合物、共聚单体含量相同材料的刚性与韧性之间的相对关系,从而获得所需性能的新材料。
这种材料从微观结构看是PP和乙丙橡胶的混合物,即PP硬相中分散有高弹性EPDM颗粒,故被称为PP/EPDM型“反应型共混料”。
德国巴斯夫公司的Novolen牌“反应器共混料”包括2800jx、2900HX和2900NCX3个牌号。
3)嵌段共聚PP/聚烯烃热塑性弹性体(TPE)共混料某些牌号的聚烯烃热塑性弹性体如同EPR一样,能赋予PP较好的低温韧性,且共混料刚性亦佳。
采用TPE的另一个理由是:
TPE颗粒料无需象EPR那样进行破块开10炼后再与PP树脂共混(有时无需进行硫化处理),而可以将TPE颗粒和PP颗粒在使用过程中按比例掺混后,直接加入到注塑机中进行成型加工,这样可降低成本。
4)非交联发泡保险杠日本StyrenPaper公司生产的非交联发泡保险杠现已被丰田公司采用。
这种保险杠采用JSP公司开发生产的PP发泡珠粒,先将珠粒装入模具中发泡成型,生产的保险杠具有良好的耐热性、尺寸稳定性和缓冲性。
这种泡沫硬度作汽车保险杠非常合适。
此外,以这种可发性PP(EPP)为基础成型的PP保险杠具有吸附冲击能量,质轻及易回收的性能。
法国标志公司已为他的306型车配备了EPP保险杠系统。
北美洲的BASF公司也投巨资生产EPP,并准备在欧洲和德国生产同类产品,以满足市场需要。
1.7高分子材料的未来发展趋势国外对塑料汽车保险杠的研究起步较早,60年代就已形成商品化生产规模,当时主要选材为PU和PC/ABS合金进人80年代后,由于P改性材料具有价格便宜、设计自由度大、可注射成型、废料可回利用等优点,成为制作保险杠的首选材料近年来,随高分子合金、共混、复合、动态硫化、相容剂及共混理论与技术的发展,p改性材料已不断适应各种汽车保险杠用材的要求,PP保险杠正在使用P改性材料生产的保险杠已占70%。
欧洲保险逐步代替其它材料的保险杠,杠材料大部分采用可注射成型的EPDM改性P材料,90年代初,欧洲约有85%保险杠是用弹性PP制作,1995年提高到95%。
西欧1992年保险杠用PP/EPDM量为1kt,1995年用量则增加了1倍。
日本在塑料保险杠的开发方面始终处于世界的前列。
日本90年代大约80%保险杠用改性即制成日本窒素公司开发了一系列用于汽车保险杠的高结晶PP。
日本本田CR一X型汽车是世界上较早采用注射模塑法生产改性汽车保险杠的汽车。
日产汽车公司和三菱油化公司也研制了由P嵌段共聚物、苯乙烯弹性体和聚烯烃系乙丙橡胶3种组分配成的新材料制作的保险杠用该体系生产的保险杠具有高刚性、耐冲击性、抗损伤并具有良好的光泽、弹性和涂装性将保险杠装车后,在8k耐h受冲撞时可不碎裂,并具有复原的弹性。
这种材料还具有装饰美观、可注射成型等特点。
在性能方面与聚氨醋差不多,成本则减少1020%。
日本三井化学也研制了由p嵌段共聚物、弹性体和滑石粉色目料配成的材料制成保险杠,11综合性能良好。
1991年,丰田汽车公司将纳米P复合材料用于汽车前后保险杠,使原保险杠厚度由4mm减至3mm,质量减轻约l/3。
随着汽车产销量的不断增加,汽车废料的回收已经成为影响汽车用塑料增长的大问题。
据估计,1990年仅德国新注册的汽车就有300万辆,如以汽车平均寿命为10年来计算,每辆车平均用100kg塑料,这300万辆车将产生30万吨废塑料。
由此可见,全世界每年产生的汽车废塑料是相当可观的。
从环境保护和资源有效利用的观点出发,回收塑料已成为越来越紧要的问题.所以未来聚丙烯高分子材料的发展方向除了开发满足更高要求的力学性能外,还应注重材料的回收利用。
1.8结论国外聚丙烯汽车保险杠发展迅速,使用弹性体聚丙烯改性生产保险杠已占70%。
以日本为代表的由嵌段共聚PP、苯乙烯弹性体和聚烯烃类乙丙橡胶3组分配制成的新材料,及Himont公司反应器中直接生产的改性PP合金,极大地改善了保险杠的涂装性、耐热性及弹性,使PP在性能方面与聚氨酯接近,可用于生产中高档轿车保险杠。
为此我国应该重点研究开发pp汽车保险杠的材料。
另外随着汽车产为代表的热塑性量的增加,我们还应注重研究开发材料的再回收利用。
以改性PP聚烯烃材料将是今后保险杠材料应用和发展方向。
参考文献:
1李馥梅.聚丙烯汽车保险杠专用料发展概况J.现代塑料加工应用,2000,12(l):
52.2江梅,王清国,聂华汽车塑料及其制品的发展J.汽车工艺与材料,2005,(4):
373王跃.聚丙烯汽车保险杠的应用与开发进展J.塑料.200l.30(3):
11一18.4林铁年.聚丙烯汽车保险杠J.塑料加工应用,1990,
(1):
23-29.5林铁年.聚丙烯汽车保险杠J.塑料加工应用,1990,
(1):
23-29.6丁会利,袁金凤,钟国伦(高分子材料及应用M.北京:
化学工业出版社,2011:
249(7周达飞,吴张永,王婷兰,编.汽车用塑料塑料在汽车中的应用M.12北京:
化学工业出版社,2003:
8.13