钢丝剥壳机的总体设计本科毕业设计Word文档下载推荐.docx
《钢丝剥壳机的总体设计本科毕业设计Word文档下载推荐.docx》由会员分享,可在线阅读,更多相关《钢丝剥壳机的总体设计本科毕业设计Word文档下载推荐.docx(31页珍藏版)》请在冰豆网上搜索。
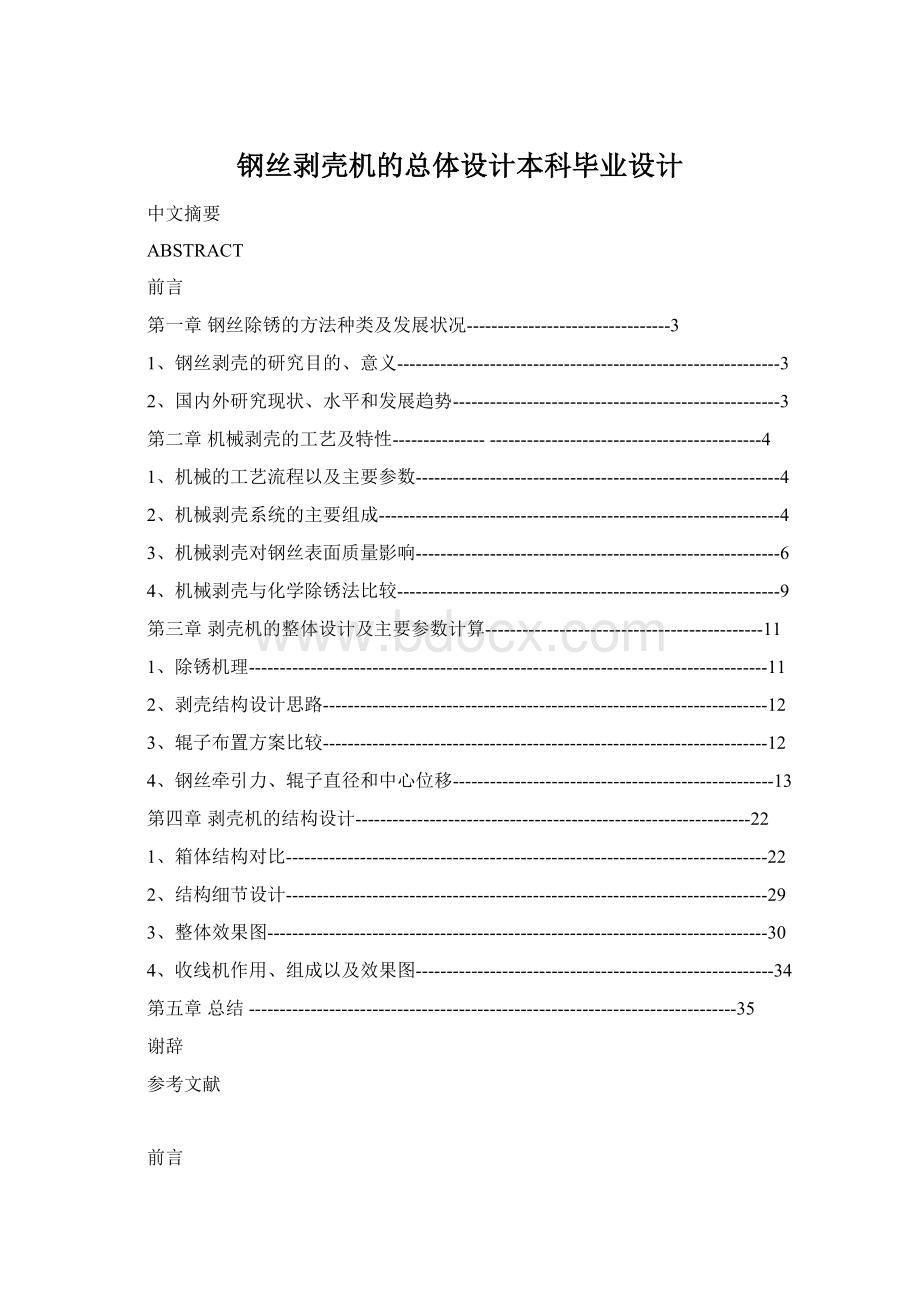
然后把重点放在的机械剥壳机的设计上,对剥壳机整个结构进行了详尽的说明。
第一章钢丝除锈的方法种类及发展状况
1、钢丝剥壳的研究目的、意义:
钢丝在工业生产中是一个不可或缺的部分,垂钓、捆绑、牵引等等工作都需要钢丝来连接。
钢丝的表面质量、性能以及寿命也就成了十分关键的问题。
钢丝表面的氧化层对于钢丝的表面质量、性能和寿命有着举足轻重的关系,不仅影响了其强度而且容易对使用者产生危险。
所以钢丝剥壳技术是一个值得研究的课题。
对于这个问题如果能够研究透彻并能制造出更合理、更稳定、更高效的钢丝剥壳机,那将会对工业生产中的生产效率、生产的安全性等问题有着间接的影响。
因此出于这一系列目的,我们将对钢丝剥壳机进行研究、设计、改造,使它能够满足更高的要求。
2、国内外研究现状、水平和发展趋势:
我们通过对现今国内外的剥壳技术做了一定的研究分析,发现目前主要剥壳手段有以下两种:
一是采用大池子进行酸洗、磷化工艺通过化学反应将钢丝表面的氧化皮分解。
但是由于其工序繁多复杂,而且酸洗磷化后的排污和水处理成本较高。
因此运用这种手段的企业较少。
在满足产品性能要求的同时,保护环境,节能减耗才是生产企业所追求的。
正是由于这种追求才产生了第二种手段:
机械剥壳。
相对与第一种手段,机械剥壳有着工艺简单、产品稳定性好身长效率高、操作简单、生产成本低、低排污少排放等优点。
并且目前对于机械剥壳技术研究有着一定的基础,其发展水平也有相当的高度。
基于成本、效率、环境保护等问题出发,相信机械剥壳是未来钢丝剥壳的主要手段。
所以我们对机械剥壳和它的系统控制进行更深入的探讨、研究和改造。
第二章机械剥壳的工艺及特性
1、机械剥壳的工艺流程以及主要参数:
开卷放线→机械剥壳→矫直→牵引→高压水清洗→电解酸洗→水洗→表面调节→热水洗→磷化→水洗→热水洗→涂硼→蒸汽烘干→LZ9/1000拉丝机拉拔→工字轮收线。
该生产线优点是工艺连续性好,大盘重放线、在线磷化和涂硼,工艺简洁,产品稳定性好,生产效率高,操作简单,生产成本低,低污染少排放;
缺点为生产线较长,一次投资较大。
通常设计成一线双头。
盘条表面处理生产线工艺与性能参数:
预处理线走线根数:
1或2根;
处理线材直径:
8~12mm;
线材材质:
70,72A,77B,82B;
成品拉拔速度:
约200m/min;
年处理量:
单线约1.5万t,双线约3万;
走线高度:
1~1.2m(与拉丝机匹配);
表面预处理线长度:
70m;
生产线长度约90m(放线至收线机);
蒸汽用量:
0.2~0.5t/h;
清洗水用量:
0.8~1.5t/h;
功率:
20kW。
2、机械剥壳系统的主要组成:
2.1 放线架
放线架为自开卷式放线架,无需动力,可承重2~3t盘条。
使用时由汽车、叉车将盘条装到放线架上,通过开卷轮将盘条引至剥壳机组。
放线架结构简单、实用,使用时无噪音。
2.2剥壳机与矫直
机械剥壳主要根据盘条在合适的剥壳轮上反复弯曲、延伸变形的原理,去除盘条表面的热轧氧化皮,通常采用3向3组互为120°
的剥壳轮变形弯曲,将脆性氧化皮剥离盘条表面,通过该道工序,基本上可去除85%~90%的氧化皮,但不能去除水锈氧化膜。
剥壳轮材质选用合金钢制作,辊槽深度为18~20mm;
辊轮通过气缸压力调节其弯曲量,并保持张力恒定。
生产时氧化皮自动掉落到氧化皮收集盒内的收集袋中。
为避免氧化皮的粉尘污染,整套装置通过安全盖进行封闭,安全盖在穿线时可以自动开启。
盘条经变形弯曲后须进行矫直处理,使其顺利进入后道工序,对以后工序的槽体不磨损,在生产连续线上稳定运行。
2.3牵引
牵引轮起到辅助拉丝的作用,给盘条一定的前进动力。
因为预应力钢绞线用盘条直径在9~14mm,比较粗,在经过3向弯曲轮后,阻力较大,为避免拉丝机第一卷筒负荷过大,必须通过牵引给其辅助动力,以满足生产需求。
2.4电解酸洗与气吹系统
电解酸洗主要利用氧气、氢气的剥离作用,将残余的氧化皮清除掉。
电解酸洗是一个发热过程,通过电解反应,热的稀硫酸对盘条表面进行化学酸洗,
整个工作槽体通过盖密封,生产线周围很少有刺激性气味。
电解酸洗需配套500A/16V整流电源一套。
电极为弧形铅极板,电极接线方式为“+---++---+”,循环泵的作用是将酸液在储液槽与工作槽之间进行循环。
气吹系统采用国外先进工艺,气嘴设计独特,对运行的钢丝逆向吹气,将钢丝表面的95%残留液体吹回到原储液槽内,既避免了有效溶液(如电解液、涂层液)的浪费,又减少了清洗水的用量。
该气嘴耐磨,气密性好,更换方便,操作简单。
可采用低压涡流风机或无油压缩空气作为气源供气。
另外,在表面调节、磷化与涂层工序也均配置了气吹系统。
气吹系统功率为2.2kW,风量210m3/h。
2.5磷化槽
磷化涂层为机械剥壳连续线的关键工序,磷化质量的好坏,直接影响拉拔质量,因此,在设计中为保证在线磷化时间,充分满足磷化涂层要求,该段较长。
采用中温磷化工艺,在满足生产要求的前提下,避免产生过多的磷化渣。
磷化储液槽
的作用为:
(1)收集储存工作槽的回流液体;
(2)给磷化液加热,并循环给工作槽,为盘条进行磷化处理提供保证。
储液槽自动控温,且保温效果良好。
磷化液加热采用不锈钢蒸汽管加热,以利清除磷化渣。
3、机械剥壳对钢丝表面质量影响:
采用机械剥壳法去除盘条表面氧化铁皮,其原理通常是利用水平和垂直的矫直辊对盘条进行反复弯折并经过适当的擦拭处理,使盘条表面的氧化铁皮剥离。
其特点是投资少、生产成本低,不需要传统的化学酸洗、表面涂层工序,也减少了废酸处理所带来的环保投资问题,因此,这种工艺方法在钢丝的半成品拉拔生产中普遍采用。
然而,采用机械剥壳法去除氧化铁皮与化学酸洗、表面涂层处理比较,对钢丝拉拔后的表面质量和机械性能有较大影响,在钢丝绳的生产中影响更严重。
(1)机械剥壳法生产制绳钢丝的断裂现象及分析
为国内某港口原料码头生产6×
36SW+IWR-42.5,48mm钢丝绳。
试制的初期(第1~5批),钢丝半成品拉拔前采用机械剥壳法去除氧化铁皮。
原料选用上海宝钢ª
6.5mm77A钢盘条,执行标准为Q/BQB512SWRH77A,A级精度。
实测7个试样,化学成分见表1。
表2-1:
77A钢各元素的质量分数%
钢丝生产工艺流程:
盘条原料→拉拔前表面处理→半成品拉拔→铅淬火处理→酸洗磷化涂层→成品拉拔。
以钢丝绳中主股外层钢丝(2.4mm,2.7mm)为例,均经过2次拉拔:
6.5→5.4→2.4mm;
6.5→6.0→2.7mm。
对钢丝绳在原料码头的使用情况进行追踪调查,发现钢丝绳的破坏形式主要以钢丝脆断为主,而且在钢丝生产的拉拔过程中和钢丝绳捻股、捻绳过程中就出现了较多的断丝现象,这与采用的机械剥壳法对钢丝表面质量的影响有关[1]。
对采用无酸洗拉拔工艺产生的钢丝脆断样品进行分析,其外观为脆性断口,在断口附近存在宏观肉眼可见的横裂纹。
金相照片如图1、图2。
图1为远离裂纹源的正常纤维断口,图2为断裂源处的组织,有撕裂层出现,可以认为是从块状铁素体处产生的。
在断口处还发现夹杂物存在,对夹杂物进行了金相检验,如图3,能谱分析见表2及图4。
图2-1:
正常金相组织
图2-2:
断口金相组织
图2-3:
夹杂物金相组织
表2-2:
夹杂物各元素质量分数%
图2-4:
夹杂物能谱分析
对裂纹源处的能谱分析结果可以看出,夹杂物类型为高磷氧化钙夹杂。
由于钢的组织中不可避免地存在着脆性夹杂物等缺陷,如果在冷加工过程(拉拔)中采用机械剥壳去除盘条氧化铁皮的方法,由于矫直辊对盘条进行反复弯折,容易造成盘条的表面损伤或微裂纹,采用无酸洗拉拔,钢丝未进行表面涂层,拉拔润滑条件差,加剧了表面裂纹的形成,进而造成钢丝拉拔过程中和钢丝绳捻股、捻绳过程中钢丝的断裂。
而且盘条表面一旦有未清理尽的氧化铁皮,在随后的拉拔加工中,轻者会划伤钢丝的表面,重者会提高钢丝和拉丝模之间的摩擦系数,造成断丝。
港口卸船机用钢丝绳在使用过程中,要承受拉应力,同时在抓料和卸料时,或卷筒在起动和停止运转时,钢丝绳上的负荷突然增加和减小,使钢丝绳产生张紧和松弛,产生抖动,使这种拉应力具有交变应力的性质,但周期不是固定的。
同时在运行时要用卷筒卷取和导轮、绳轮,钢丝绳会受到弯曲应力。
港口卸船机用钢丝绳在使用时钢丝的断口各有差别,但其疲劳断裂的特征基本相同,即分为裂纹萌生的疲劳源区、疲劳裂纹扩展区和瞬时断裂区。
钢丝绳受到交变负荷时,钢丝绳表面应力较中心为大,裂纹一般萌生于其边缘处,在其表面最大切应力处的薄弱环节或钢丝本身存在表面缺陷处,将是裂纹源,特别是表面微裂纹,这大大加快了裂纹萌生和钢丝疲劳断裂的速度。
4、机械剥壳与化学除锈法比较:
针对钢丝绳在生产和使用中存在的断丝问题,在随后的生产中取消了半成品机械剥壳无酸洗拉拔工艺,改用酸洗、薄磷化涂层处理后进行半成品拉拔,其它工艺基本保持不变。
结果发现在钢丝半成品、成品拉拔及钢丝绳捻股、捻绳过程中断丝现象大幅度减少。
表3、表4是ª
42.5mm和ª
48mm钢丝绳股中外层钢丝(2.4mm,2.7mm)在不同前处理工艺后生产中断丝情况统计(每批次的生产总量基本相同)。
表2-3:
Ø
25mm钢丝绳生产中断丝次数统计
表2-4:
48mm钢丝绳生产中断丝次数统计
由表3、表4可以看出,第6批改用酸洗、薄磷化涂层处理进行半成品拉拔工艺后,生产过程中发生的钢丝脆断现象大幅度减少,ª
42.5mm由16次、13次降低到3次,ª
48mm由11次、14次降低到3次。
采用机械剥壳法去除盘条表面氧化铁皮进行钢丝拉拔前的预处理,具有投资省、生产成本低的特点,也减少了废酸处理带来的环保投资问题。
但通过对比实验,将钢丝半成品拉拔前由盘条机械剥壳无酸洗拉拔改为酸洗薄磷化涂层拉拔工艺,改善了成品钢丝的表面质量,减少了钢丝脆断倾向。
对高档次钢丝、钢丝绳产品,在钢丝半成品拉拔前,盘条的表面处理不宜采用机械剥壳法。
若采用机械剥壳法,应增加在线酸洗及涂硼工序。
第三章剥壳机的整体设计及主要参数计算
1、除锈机理:
先考虑一个假象模型,母体材料阿A由左右两部分组成,中间以拉伸弹簧相联。
铁鳞B同时粘附在A的两部分(图5a)。
若在A的两端施加拉力P,则中间弹簧将变形伸长,A的两部分之间的距离也随之拉长。
此时铁鳞B上所受的外力与A粘联处的剪力Q(图5b),此时Q力的出现将造成两种后果:
1)当Q力大于B和A之间的粘着力时,B和A之间将发生相对位移,使B从A脱落(图5c);
2)当Q力在B内造成的应力超过B的强度极限时候,B将断裂(图5d)。
图3-1钢丝除锈假想模型
断裂后的铁鳞仍将分别粘附在左右两部分母体材料上,此时由于母体材料A继续受到拉伸,B将可能再次被拉断,每拉断一次,B在A上的粘附长度减少一次,粘着力也随之减少,一直到粘着力小于接触面之间的剪力Q时,铁鳞B即从母体材料上脱落下来。
由于所研究的母体材料为一个连续弹性体,可以假象地把它沿纵向分割成无数个象上面所述的弹簧系统,则随着母体材料拉伸变形的增大,附着在表面上的铁鳞将随之逐渐脱落。
对于粘着力较大的铁鳞,需要母体材料由较大的变形才能使之脱落。
此时要求P力继续增大,但P力增大到一定程度时,假象的连接母体材料A的中间弹簧讲失效,即相当于材料达到屈服。
此时外加拉力P直接作用在铁鳞与母体材料之间的粘附层上,从而破坏粘附层而使铁鳞脱落。
由此可以得到以下结论:
1)塑性材料受到拉伸变形时可使其表面的附着物剥落。
2)只有当材料的拉什变形达到并超过其曲阜极限时候,表面的附着物才可能大量甚至全部脱落。
这一点已由以下实验作了初步验证:
将一根直径为15,表面布满了铁鳞的圆柱形低碳棒放在拉力试验机上作拉伸试验,在材料屈服以前,表面铁鳞仅脱落1/4左右,当材料达到并超过屈服极限时候,铁鳞开始大量剥落,而当应变量达到12%左后时,表面铁鳞全部脱落。
由此推论,盘条在绕过辊子发生弯曲变形时,其表层金属受到反复拉压作用,如果辊子设计合理,则盘条在辊子上每弯曲一次,就会屈服一次,亦即被拉长一次,表面铁鳞随之脱落一部分,当盘条经过一些列辊子弯曲,其变形总量达到一定程度时,表面铁鳞就应完全除尽。
由此可以得出,辊子弯曲除锈的关键是盘条的总伸长量。
2、剥壳结构设计思路:
本设计采用机械剥壳去锈法将盘条的氧化皮用施加外力的方法使之疏松、破裂、剥落。
该方法让钢丝通过相互垂直的两组辊子或滚轮受到弯曲,外表面延伸,内表面压缩,使延伸性较低的氧化皮弯曲脆裂脱落。
滚轮或辊子布置图6如下:
图3-22组辊子布置图
滚轮或辊子通常采用两组垂直布置的三滚轮或辊子,如图7所示。
钢丝在机械除锈机中的除锈洁净程度主要决定于中间辊的中心位置,因此,可以用改变中间辊中心线的位移深度的办法来进行调节,本设计采用液压装置进行调节。
图3-3:
三辊子布置图
上述剥壳机设计成一个独立模块,在机体上预留扩充通道,根据需要可以增加钢丝刷除锈装置,磷化设备或增加酸洗设备。
3、辊子布置方案比较:
基于以上思路,本人设想出2套结构用来参考和比较(见图8和图9),从整体尺寸、牵引所需的力、结构的复杂程度以及剥壳的质量来下手,选择出一套更好的方案来作为最终方案。
结构一:
图3-4:
此结构简单、性能良好
结构二:
图3-5:
此结构相对较复杂,但性能可能较结构一好
4、牵引力、辊子直径和中心位移:
确定了2套方案之后下面进行各套结构所需要的牵引力,以确定后续的收线机所需要的力矩电机型号以及辊子的直径和3个辊子之间的距离。
要研究3辊式机械除锈,先要研究2个辊子间的相互除锈的数学表达式。
钢丝通过相互垂直的两个辊子受到弯曲,外表面延伸,内表面压缩,使延伸性较低的氧化皮弯曲脆裂脱落。
国外的资料表明,当钢丝拉伸至延伸率为3%~5%时,氧化皮开始破裂并与钢丝分离;
延伸率为8%时,钢丝表面的氧化皮基本脱落;
延伸率为12%时,钢丝表面的氧化皮完全脱落。
对延伸率达到12%的试样研究表明,其组织未发生显著变化,但表面粗糙度有所增加,所以过分增大伸长量并无必要。
我们以δ为钢丝的延伸率,所以当δ=3%-5%未达到要求,当δ=8%时为达到要求,而当δ=12%时,钢丝表面质量受影响,所以当5%<
δ<
8%,只有满足这一个要求算是剥丝成功。
钢丝直径为8-12MM。
辊子半径:
我们对钢丝在辊子轮上的状态进行受力分析:
图3-6:
钢丝在辊子上的状态
两辊式机械除锈机的主要参数为工作辊直径D和除锈机的牵引力F。
为了保证清除氧化皮的洁净程度为δ(用达到线材表面氧化皮90%清除时的延伸率来表示),选择工作辊直径时,必须使钢丝通过辊子后表面任意点的延伸率都不得小于δ。
在线材绕辊子弯曲时,线材在中心线弯曲,弯曲半径为(D+d)/2,其中D,d分别为辊子直径和线材直径。
钢丝在辊子上弯曲能保证在A,B,C,D各点的延伸率为δ,假设线材在辊子上包角为180°
A,B点的延伸率:
δ=dcos45°
/(D+d)=1.4142d/[2(D+d)]
所以根据以上理论例出2个如下不等式:
---------------------------------------------3-
(1)
--------------------------------------------3-
(2)
求解以上2个不等式,得出结果:
106mm<
D<
126mm
所以我们取D为中间值:
D=116mm
钢丝所需要牵引力:
首先对辊子分布压力进行研究分析,若要精确计算钢丝截面的弯矩,应由实验测定分布压力。
假设钢丝通过辊子时已经完全贴附于辊子,近似的计算分布压力,由图11根据平衡条件
--------------------------3-(3)
整理上式,得:
---------------------------------------------3-(4)
图3-7:
钢丝所受分布压力示意图
令
为截面弯矩。
我取一段钢丝研究,如图12所示。
图3-8:
钢丝所受截面弯矩示意图
我们假定计算钢丝截面弯矩时候,忽略摩擦力的影响。
那么根据平衡方程
----------------------------------3-5
令M(P)是分布压力对所取截面的弯矩,则:
------3-6
对上式进行积分,将(4)式代入,得出:
----------------------------------3-7
将(7)带入(5)式,有
---------------------------------3-8
假设钢丝为无强化的理想塑料材料,考虑钢丝轴向应变较小,弯曲应变较大,钢丝截面(位于辊子上的一段)已经弯曲变形完全屈服。
-------------------------------------------3-9
式中
-----------------------------------------------------3-10
其中d是钢丝直径。
,并整理,得
-------------------------------3-11
利用上式,对于入口拉力为
,具有n个辊子的除锈机,出口拉力为:
-------------------------------3-12
其中T0为钢丝绳出口的拉力,由于剥壳机为第一道工序,钢丝直接通过剥壳机,所以T0=0,可以省去。
根据前面提到的
,其中W=
,σ为钢丝的屈服应力:
σ=270MPa,n为辊子数,次剥壳机为2组辊子,一组3个辊子,所以n=6。
所以:
=4773N
=16110N
所以T取16110N。
辊子间距、辊子偏距:
辊子直径D、间距P和偏距H(如图13)都对延伸率由直接影响,根据国外的实验资料,在H=D以前,延伸率的增加与辊子偏距几乎是成线性关系为:
但当偏距超过H=D后,延伸率即接近于恒定值,此时盘条的曲率半径接近等于辊子半径D,如图14所示。
图3-9:
辊子间距和偏距示意图
图3-10:
辊子间距和钢丝延伸率关系图
如上图,对于分组型三辊式机械除锈机,我们可以改变中间辊子的偏距H来提高钢丝在辊子上除锈的洁净程度。
对于偏距H给出公式:
----------------------------3-13
其中h必须要满足h>
=d,
得出不等式:
=>
L<
132mm
又因为L>
D+d,所以124mm<
132mm.
所以L取128mm。
将L=128反带回去求出h=98
所以L=128H=98
结构二:
由于结构二不同于结构一的辊子布置,在钢丝截面画内接正方形,如图1所示,使正方形的一边平行于工作辊的平面。
由图15可知,钢丝通过辊子1和辊子2时的位置变化。
图3-11:
钢丝通过1组辊子和2组辊子时,A、B、C、D的位置变化
在线材绕辊子1弯曲时,线材在中心线弯曲,弯曲半径为(D+d)/2,其中D,d分别为辊子直径和线材直径。
线材在辊子1上弯曲能保证在A,B,C,D各点的延伸率为δ1,如图16所示:
假设线材在辊子上包角为180°
δ1=dcos45°
/(D+d)=1.4