红坝金属结构制作施工组织设计Word格式文档下载.docx
《红坝金属结构制作施工组织设计Word格式文档下载.docx》由会员分享,可在线阅读,更多相关《红坝金属结构制作施工组织设计Word格式文档下载.docx(45页珍藏版)》请在冰豆网上搜索。
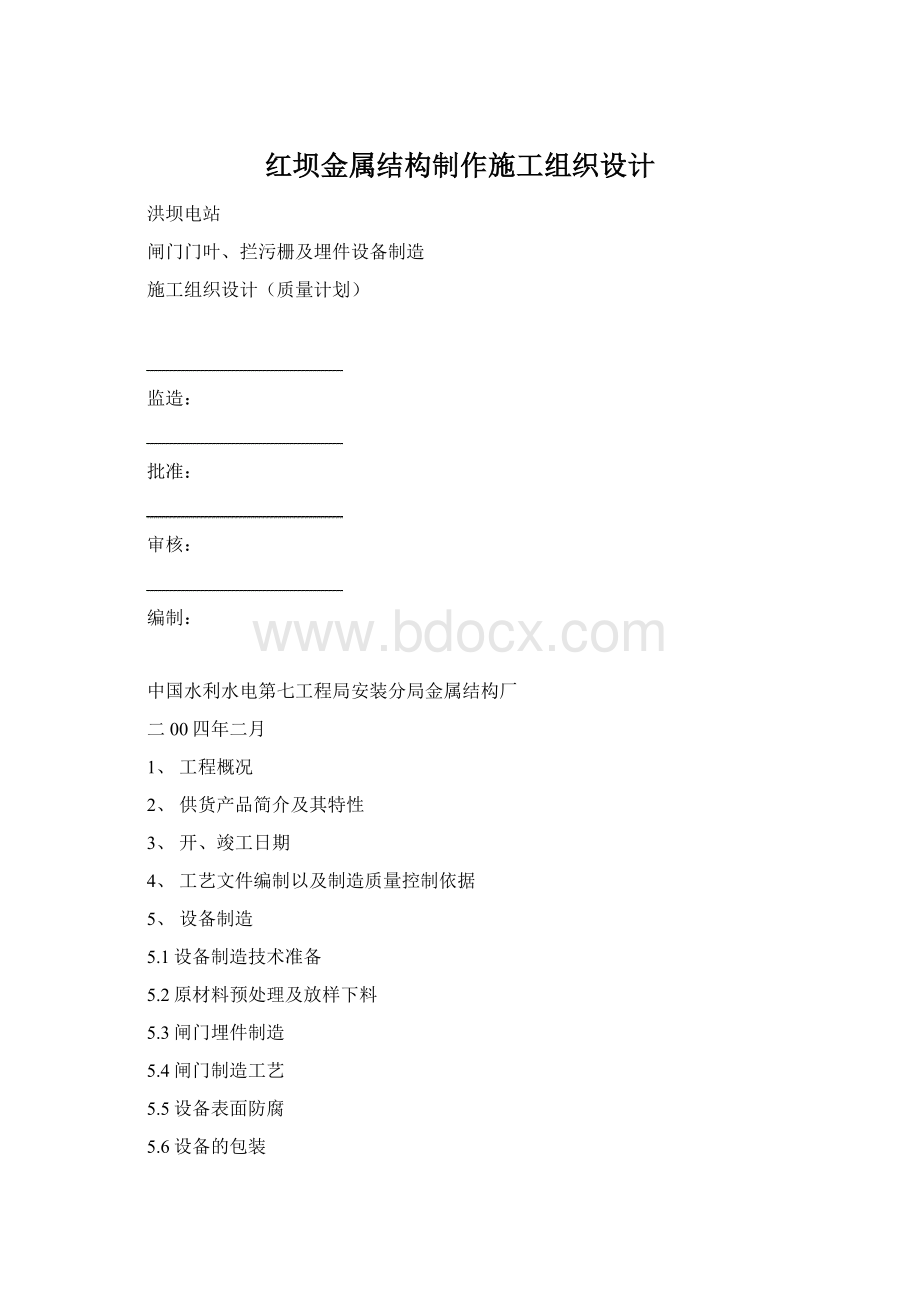
估重(t)
总重(t)
202
泄洪闸工作门槽
6x6.5-6.5
2
3.1
6.2
204
泄洪闸检修门槽
3
6
206
冲砂闸工作门槽
3x6.5-6.5
1
2.4
210
取水口拦污栅槽
5x3.4-2
1.7
3.4
232
尾水检修门槽
3.06x3.08-15
4
8
208
冲砂闸检修门槽
2.8
212
截砂槽工作门槽
1x1-6
214
沉砂池进口拦污栅槽
5x5.5-2
2.1
6.3
216
沉砂池进口工作门槽
5x5.5-5.5
2.5
7.5
218
沉砂池冲砂孔闸门槽
2x2-12.5
1.5
220
沉砂池出口检修门槽
5x8.4-8.4
5
15
222
调节池进口污栅槽
224
调节池进口工作门槽
201
泄洪闸工作门
定轮门
30
205
冲砂闸工作门
213
沉砂池进口拦污栅叶
22.5
226
调节池出口检修门槽
4x6-12.5
228
调节池冲砂孔工作闸门槽
203
泄洪闸检修门
滑块门
12
207
冲砂闸检修门
7
209
取水口拦污栅叶
211
截砂槽工作门叶
潜孔定轮门
215
沉砂池进口工作门叶
36
217
沉砂池冲砂孔闸门叶
219
沉砂池出口检修门叶
45
221
调节池进口污栅叶
223
调节池进口工作门叶
229
施工支洞进人门叶
2.4x1.8-50
9
230
施工支洞进人门槽
231
尾水检修门叶
潜孔滑块门
233
泄洪闸冲砂闸检修门储门槽
225
调节池出口检修门叶
227
调节池冲砂孔工作闸门叶
3、开竣工日期
洪坝电站开工日期为2004年2月28日,竣工日期为2004年7月30日。
合同要求交货期最终日期为2004年7月30日。
计划安排闸门开工日期为2004年2月28日,
4.工艺文件编制以及制造质量控制依据
4.1《合同文件》(合同编号HB/CⅧ-2)及发包方要求等;
4.2施工蓝图及技术要求;
4.3规范与标准
DL/T5018-94水利水电工程钢闸门制造安装及验收规范
GB146.1-83标准轨距铁路机车车辆限界
GB146.2-83标准轨距铁路建筑限界
GB191-85包装储运图示标志
GB247-88钢板和钢带验收、包装、标志及质量证明书的一般规定
GB324-88焊缝符号表示法
GB699-88优质碳素结构钢技术条件
GB700-88碳素结构钢
GB704-88热轧扁钢尺寸、外形、重量及允许偏差
GB706-88热轧工字钢尺寸、外形、重量及允许偏差
GB707-88热轧槽钢尺寸、外形、重量及允许偏差
GB709-88热轧钢板和钢带的尺寸、外形、重量及允许偏差
GB983-85不锈钢焊条
GB984-85堆焊焊条
GB985-88气焊、手工电弧焊及气体保护焊焊缝坡口的基本形式与尺寸
GB986-88埋弧焊焊缝坡口的基本形式和尺寸
GB1031-83表面粗糙度参数及其数值
GBll76-87铸造铜合金技术条件
GBll82~1184-80形状和位置公差
GB1300-77焊接用钢丝
GB/T1591-94低合金高强度结构钢
GB1800~1804-79公差与配合
GB2101-89型钢验收、包装、标志及质量证明书的一般规定
GB3077-88合金结构钢技术条件
GB3274-88普通碳素结构钢和低合金结构钢热轧厚钢板和钢带技术条件
GB3323-87钢熔化焊对接接头射线照相和质量分级
GB4237-84不锈钢热轧钢板
GB5117-85碳钢焊条
GB5118-85低合金钢焊条
GB5293-85碳素钢埋弧焊用焊剂
GB/T7233-87铸钢件超声波探伤及质量评定方法
GB8923-88涂装前钢材表面锈蚀等级和除锈等级
GB9439-88灰铸铁件
GB9444-88铸钢件磁粉探伤及质量评定方法
GB9787-88热轧等边角钢尺寸、外形、重量及允许偏差
GB9788-88热轧不等边角钢尺寸、外形、重量及允许偏差
GB9793-88热喷涂锌及锌合金涂层
GB9794-88热喷涂锌及锌合金涂层试验方法
GB9795—88热喷涂铝及铝合金涂层
GB9796-88热喷涂铝及铝合金涂层试验方法
GB10854-89钢结构焊缝外形尺寸
GBll345-89钢焊缝手工超声波探伤方法和探伤结果分级
GBll352-89一般工程用铸造碳钢件
GBll373-89热喷涂金属件表面预处理通则
JISH9300-77喷涂锌操作标准
JISH9301—77喷涂铝操作标准
JB3092-82火焰切割面质量技术要求
JB3144-82锅炉大口径管角焊缝超声波探伤
JB3223-83焊条质量管理规程
JB/ZQ4297-86合金铸钢
Q/ZB75-73机械加工通用技术条件
Q/ZB76-73装配通用技术条件
SL35-92水工金属结构焊工考试规则
SL36-92水工金属结构焊接通用技术
SL105-95水工金属结构防腐蚀规范
SDZ012-85铸钢件通用技术条件
SDZ016-85锻件通用技术条件
4、设备制造
5.1、设备制造技术准备
5.1.1按照工艺设计程序,组织工艺人员学习合同条款,熟悉设计图纸、技术文件、质量标准、验收规范。
5.1.2组织工艺人员对施工图进行尺寸校对和工艺性审核,并与设计单位联系,及时解决设计图中的工艺问题。
5.1.3本产品制造定轮轴承为新材料,由设计指定供应商提供相应技术资料,满足轴承的主要技术要求。
其它未涉及新结构、新材料、新工艺,不进行工艺试验与评定。
5.1.4依据合同条款、设计图纸、验收规范、工艺试验与评定成果,结合厂内生产条件,设计合理的产品加工工艺方案,制定工艺流程,绘制加工工艺图,编制关键件及重要工序的作业指导书及工艺规程,总工程师批准后执行。
5.1.5依据产品质量验收标准,结合加工工艺方案,编制“产品质量检验计划”(检验大纲),预设质量控制点,作好检测记录、报告等资料准备,报经监理工程师审批。
5.1.6工程开工前和重要工序施工前,对施工人员进行详细的施工技术交底和必要的技术工艺培训。
5.1.7开工前对主要加工机械设备和新购置的设备的可靠性和技术性能进行检查、试验与鉴定,以保证加工精度。
5.1.8开工前对生产环境的适宜性进行检查、调整、处理。
5.2.1原材料预处理
5.2.1.1产品所用原材料进厂时,按质量保证体系控制程序进行验证。
其型号、规格、材质、数量、技术指标应符合合同条款、设计图纸和技术标准要求,并有出厂合格证和材质证明书。
无证材料应作复验,不合格产品不得投料使用。
5.2.1.2用于产品上的板材,在下料前一律用七辊平板机平板,型材用20t或500t压力机或其它机械方法进行调直处理
5.2.1.3焊接材料的型号应符合设计图样规定,焊材到货后应进行外观检查和试焊检验,受潮或性能不稳不能使用。
焊条使用前应严格按其说明书规定作烘干处理,焊丝在使用前要清除其表面的油污及杂质。
5.2.1.4油漆涂料使用前应进行调配、稀释、试板喷涂试验,确认其各项指标达到设计要求后方可使用。
5.2.2放样下料和边缘加工
5.2.2.1放样下料统一在下料车间进行。
人工放样所用测量器具和放样样板应经周期检查合格。
下料切割优先采用数控切割机,也可采用仿形切割机或半自动切割机。
不锈钢板采用等离子切割或机械剪切。
5.2.2.2对尺寸精度要求高的板材和有一、二类焊缝坡口的板材,在火焰切割后全部采用刨边机等机械进行边缘加工。
加工后应用砂轮机将边缘毛刺等修磨平正。
5.2.2.3板料和型材需要拼接时,应将拼接头避开构件应力集中的断面,并避免出现十字焊缝,两平行焊缝间的最小间距应符合规范或设计规定。
受力构件的拼接焊缝应保证焊透,且符合DL/T5018-94中的规定。
5.2.2.4下料时要考虑予放加工余量。
主要有气割余量、刨边余量、机加工余量和特殊情况下的热矫正收缩余量。
5.2.2.56放样下料过程中,应作好不同材质的标识和标识移置,并分类存放,以便于追溯和防止混料、错料。
5.3.1埋件制造工艺流程
5.3.2焊接结构埋件的零件制作
埋件的零件主要为型钢、钢板条、筋板等,其制作主要是下料及矫正。
筋板采用数控切割机切割,保证筋板形位尺寸统一。
型钢一律采用砂轮切割机切割;
并在两端预留5mm余量,待单节埋件端头加工时再将余量加工去除。
5.3.3焊接结构单节埋件的组装、焊接与矫正
5.3.3.1组装
单节埋件在钢板平台上组装。
组装时以埋件的迎水面钢板为基础,划线后组装其它型钢、筋板并点焊固定。
组装后检查其形位尺寸,应符合制造工艺图要求,然后进行焊接。
组装工艺要点为:
组装前应复检各零件尺寸、坡口;
组装时应保证接缝顶紧;
组装用的钢平台应平整,其平面度应不大于2mm。
5.3.3.2焊接
埋件焊接至少由二人实施对称、分段、退步或间跳焊,且力求焊接速度一致,以减小焊接变形。
焊角尺寸以达到设计要求和设计修改为准。
焊接方法以CO2气体保护焊为主,手工焊为辅。
凡不锈钢板的拼接焊和其与基板的焊缝及塞焊缝一律采用E0-19-10Nb-15(GB/T983-1995)焊条焊接。
5.3.3.3矫正
埋件焊后存放一段时间,进行自然时效后,再对残余变形采用500t压力机矫正,局部小范围变形采用火焰热矫正。
特殊情况例外(业主要求水下12米埋件制造后要求即时安装)。
5.3.4焊接结构单节埋件机加工
埋件止水座面的平面度用1.0m的钢直尺靠模检测,每米范围内不大于0.5mm,且不超过2处。
埋件两端头结合面利用滑台式铣削动刀头铣削加工,其粗糙度达到Ra12.5um。
5.3.5焊接结构埋件整体组装与验收
防腐前一律按DL/T5018规范和全同文件技术规范要求,进行分部或全长大组装,并装焊定位板。
在组装状态下检查接头对口间隙、全长范围直线度、工作面平面度等指标应达到规范要求,检验合格后做出接头定位标记和编号,作好检验记录,然后交监理验收。
5.4.1平面定轮闸门制造工艺流程
5.4.2平面滑块闸门制造工艺流程
5.4.3拦污栅制造工艺流程
平面定轮闸门制造工艺流程
平面滑块闸门制造工艺流程
拦污栅制造工艺流程
5.4.4平面闸门制作
5.4.4.1平面闸门主要单件制作
平面闸门的主要构件包括门叶面板、主边梁、纵向T形隔板、吊耳以及滑块、侧轮、定轮等。
其主要制作工艺和要点如下:
5.4.4.2面板制作
(1)制作程序:
钢板平板→拼板设计及下料切割→拼接接头坡口机加工→焊接→焊缝探伤→矫形
⑵加工设备:
七辊平板机、半自动切割机、刨边机、埋弧自动焊机、超声波探伤仪。
⑶制作工艺要点:
a.面板拼接缝应避开梁与面板的连接焊缝。
b.面板拼接避免出现十字焊缝。
c.面板拼接缝为Ⅱ类焊缝,其拼接坡口应刨边机加工。
d.面板拼接缝按Ⅱ类焊缝作探伤检查。
5.4.4.3主、边梁、T形隔梁制作
⑴制作程序:
钢板平板→下料切割→焊接坡口机加工→组装→焊接→焊缝探伤→矫形(尽可能机械矫正)。
七辊平板机、数控切割机、半自动切割机、刨边机、埋弧自动焊机、CO2气保焊机、超声波探伤仪、H梁翼缘矫正机。
⑶制作方法
a.工字形主梁制作
闸门第1~4节的主梁均为工字形主梁。
工字梁的制作在二车间工字梁自动生产流水线上完成。
流水线的程序是:
工字梁组装在H型钢组立机上自动完成钢板对中定位,液压夹紧,定位压紧与焊接、输送同步完成,工作效率高;
工字梁焊接在龙门式H型钢自动焊机上完成;
工字梁矫正在H型钢翼缘液压矫正机上完成。
b、第5节为两根T形梁,T形主梁制作:
在H型钢组立机上自动完成钢板对中定位,在龙门式H型钢自动焊机上完成焊接,在H型钢翼缘液压矫正机上完成矫形。
b.边梁为T形梁,制作要求同第5节T形主梁。
c.T形隔板制作
T形隔板实为闸门纵向梁系,其装配在钢平台上进行,检查合格后,在船形位置用C02气体保护焊焊接。
(4)制作工艺要点:
a、翼缘与腹板装配时应顶紧。
b、点焊用的焊条应与母材配套并经烘干处理,点焊应由合格焊工进行,点焊长度及间隔要均匀一致。
c、主、边梁之翼板与腹板组合缝及角缝属Ⅱ类焊缝,腹、翼板拼接缝属Ⅰ类焊缝,其拼接坡口要刨边机加工,焊缝作探伤检查。
d、主、边梁和T形隔板焊后应采用H梁翼缘矫正机。
形位偏差应达到DL/T5018—94规范中表8.1.7中规定。
e、次梁为型钢,采用型钢切割机切割,调正平直后将端头修磨平正,拼接头应坡口焊,且应焊透。
5.4.4.4吊耳制作
钢板下料切割→焊接坡口机加工→吊耳补强板组焊→吊耳部件装配、焊接、矫正→二类缝探伤→吊耳孔划线→镗孔→参加门体组装焊接。
数控切割机、刨边机、直流焊机、探伤仪、镗铣床。
⑶工艺要点:
a、吊耳先做成п形,矫形镗孔后与门体组焊,吊耳腹板与主梁角接坡口表面及附近打磨平正、清扫干净。
b、吊耳板与门体组装焊接后,对一、二类焊缝作100%超声探伤。
5.4.4.5定轮装置制作
板材下料切割→焊接坡口机加工→对装→焊接→探伤→矫形→铣座板面→划线镗轴孔→轮子、轴承装配(均为外协加工)→定轮装配(高程暂不定位)
(2)加工设备:
数控切割机、龙门刨、直流焊机、探伤仪、镗铣床
5.4.4.6侧轮装置制作
制作程序:
板材下料切割→轮轴加工、镀铬→对装→焊接→矫正→装配。
5.4.5门体组拼
5.4.5.1组拼程序
门叶面板对接组合并用拉板连接固定→整体放样划线及检查验收→依次组装主梁、小梁、隔板→组装边梁→整体检测验收→焊接→检查验收→装焊吊耳→装焊锁锭板
5.4.5.2组拼设备:
两台20t/5t桥机、两台25t/5t龙门吊、标准钢平台、逆式直流电焊机、焊条烘干箱。
5.4.5.3组拼工艺要点:
⑴组装钢平台使用前进行检测其不平度应小于2mm。
⑵组装的门体单件应检验合格,不合格品不得进行组装。
⑶组装时应由中间向两边依次进行,不得强力装配。
⑷组装时应按组装工艺图和尺寸进行。
⑸组装中应保证各单件、零件的平行度、垂直度。
接头应顶紧,不得超出规范允许的间隙。
⑹组装中的定位焊,应由合格焊工使用烘干过的正式焊接使用的焊条进行点焊。
点焊段长度50mm,厚度不超过坡口深度的二分之一,最厚不得超过8mm。
间距100—400mm。
5.4.6门体焊接及焊缝检验
5.4.6.1焊接条件
⑴门体整体组装结束,经厂专职质检员检查合格,必要时报监理工程师批准,下达了开焊令;
⑵门体周围影响焊接的环境因素已排除;
⑶焊缝特别是一、二类焊缝坡口及附近10~20mm区域的污物、铁锈、水迹、油污已清除干净。
⑷焊条已按说明书规定进行了烘焙处理,并存放在100~200°
C保温箱内。
5.4.6.2焊接工艺评定与焊接工艺规程
闸门单个构件和门体组拼焊接前应作焊接工艺评定。
我厂针对Q235B材料已进行过焊接工艺评定并依评定成果编制有焊接工艺规程,不再进行焊接工艺评定和焊接工艺规程编制。
5.4.6.3焊接工艺
1)一般技术艺要求
⑴焊接方法:
手工电弧焊、CO2气体保护、埋弧自动焊。
⑵电力特性:
直流反接
⑶焊接材料:
手工焊焊条:
E5015焊前经400°
C烘焙1~2小时
CO2气保焊焊丝:
H08MnA,使用前清扫干净。
⑷焊接方式:
偶数焊工均布对称焊,每条焊缝均采用分段倒退或间跳焊。
分段长度300~400mm。
⑸焊接顺序:
先立焊,后平焊,再仰焊;
2)根据闸门及部件结构特点编制专用“焊接工艺”,详细规定焊接过程中的各种技术和工艺要求。
5.4.6.4焊接检验:
⑴门体焊接后对所有焊接接头进行外观检查,焊缝外观尺寸、外观成形均应达到DL/T5018—94标准和设计图纸要求。
外观缺陷不得超出规范限定。
⑵按DL/T5018—94标准和设计图纸要求,对一、二类组合焊焊缝焊透并按规范作超声波探伤检查,当出现疑难问题时用射线拍片核查。
5.4.6.5焊缝缺陷处理
⑴焊接过程中应加强工艺控制,防止不合格缺陷产生,一般同一部位焊缝返修不宜超过二次,第三次返修前应制定措施并经总工程师批准以后才能执行,在执行过程由工程技术科、质量安全科监督。
⑵返修后的焊缝应按原条件进行扩大探伤复查,即探伤范围适当扩大。
5.4.7门体机加工
5.4.7.1水封座板面加工
闸门水封待闸门成形后,面板朝上大组后以边梁中心线为基准线,五节门叶整体铣销水封座板,再将水封螺孔用水封压板配钻孔。
同时装配底水封小梁,划线配钻面板上底水封螺孔。
5.4.7.2吊耳加工
闸门吊耳孔轴孔,将吊耳装置制作成部件,整体焊接矫正后划线镗孔,镗孔基准为腹板机加工边。
5.4.7.3门叶端铣
用落地镗铣床铣门叶边梁两端面及节间止水座面。
划线时注意面板与边梁腹板的错位值。
端铣后将需要坡口的边梁铣坡口。
5.4.7.4定轮孔加工
闸门制作整体成形大组时划出定轮孔镗孔线,用落地镗铣床进行整体镗孔。
5.4.8门叶整体组装与验收
门体组装,按照设计要求进行整体组装,检查验收。
组装范围包括:
门体、定轮(或滑道)(装配时将所有定轮或滑块高程调一致)、侧轮、反向滑块等全部附件。
组装后经自检合格,做出各项指标检测记录,呈报监理工程师(如果监理工程师驻厂),由其组织验收。
验收合格后,在分节(段)处做出组装记号和编号。
5.5拦污栅制作
5.5.1拦污栅制作的工艺要点
(1)栅体框架纵、横梁系的制作。
纵、横梁系一般为工字梁,其制作程序、工艺方案与闸门主梁制作工艺相同,H型钢自动对装机上对装成形后自动焊焊接,翼缘矫直机矫直。
(2)栅片与栅体焊接。
栅片中栅条间隔密集,焊量较大,采用CO2焊焊接,分片对称跳焊,每片间栅条又分隔间对称跳焊,保证焊缝在整个栅体上均匀受热,让焊接变形有规律,栅体焊后不发生扭曲,易于矫正。
(3)节间连接孔的加工。
为保证栅体两侧连接孔的同心度,栅体在大组状态下整体划线,再在T6126镗床镗制连接轴孔。
最后再大组栅体试装连接装置,确保连接装置的配合。
(4)验收合格后,在分节(段)处做出组装记号和编号。
5.6设备表面防腐
5.6.1门叶及埋件表面预处理
闸门门叶及埋件未埋入混凝土表面预处理用喷砂法,按GB11373和GB9793实施。
经处理的钢材表面应达到GB8923规定的除锈等级Sa
级,粗糙度Ry应在60100m范围内,且应干燥、无灰尘。
闸门埋件其埋入混凝土一侧除锈等级按GB8923中规定的Sa1级。
5.6.2门槽涂漆技术条件
门槽涂料配套表
埋件表面
涂层
系统
涂装材料
道数
涂层干膜厚度(μm)
涂料干膜总厚度(μm)
外露表面
底层
环氧富锌漆(底漆)
70-80
100-120
面层
氯化橡胶铝漆(面漆)
30-40
埋入表面
(与砼结合面)
苛性钠水泥沙浆(或无苛性钠特种水泥沙浆)
500
注:
1、对材料为不锈钢的埋件外露表面(机械加工面)不进行上述涂装,因此涂装时应采取保护措施。
2、埋入混凝土的表面使用的水泥沙浆优先选用TN-922#强力胶作为添加剂。
b.油漆的质量和调制应符合SL105和涂料产品说明书的规定;
c.涂装的技术要求遵照SL105和涂料产品说明书的规定执行;
d.漆膜的外观检查:
湿膜不得有拽尾、缩孔缩边、起泡、喷丝、发白失光、浮色、流挂、渗色、咬底、皱皮桔皮等弊病;
干膜不得有白化、针孔、细裂龟裂、回粘、片落剥落脱皮等弊病;
e.薄膜性能的检验:
漆膜的干透性、粘手性、硬度、粘附力及弹性按SL105检验,并应符合该标准的规定;
f.漆膜的厚度用测厚仪测量,每10m2不少于3处。
厚度误差不得超过±
20%。
5.6.3闸门喷锌及涂漆技术条件
a.涂层金属为Ce铝丝,其铝+添加元素含量≥99.6%,符合GB9795-88《热喷涂铝及铝合金涂层》之规定,分多次进行喷涂,每次涂层分别为30~60μm。
每层厚度和Ce铝层最小局部厚度以及封闭层的涂料牌号、涂层道数、每道漆