最新HT200泵盖铸造工艺设计课程设计Word文档下载推荐.docx
《最新HT200泵盖铸造工艺设计课程设计Word文档下载推荐.docx》由会员分享,可在线阅读,更多相关《最新HT200泵盖铸造工艺设计课程设计Word文档下载推荐.docx(18页珍藏版)》请在冰豆网上搜索。
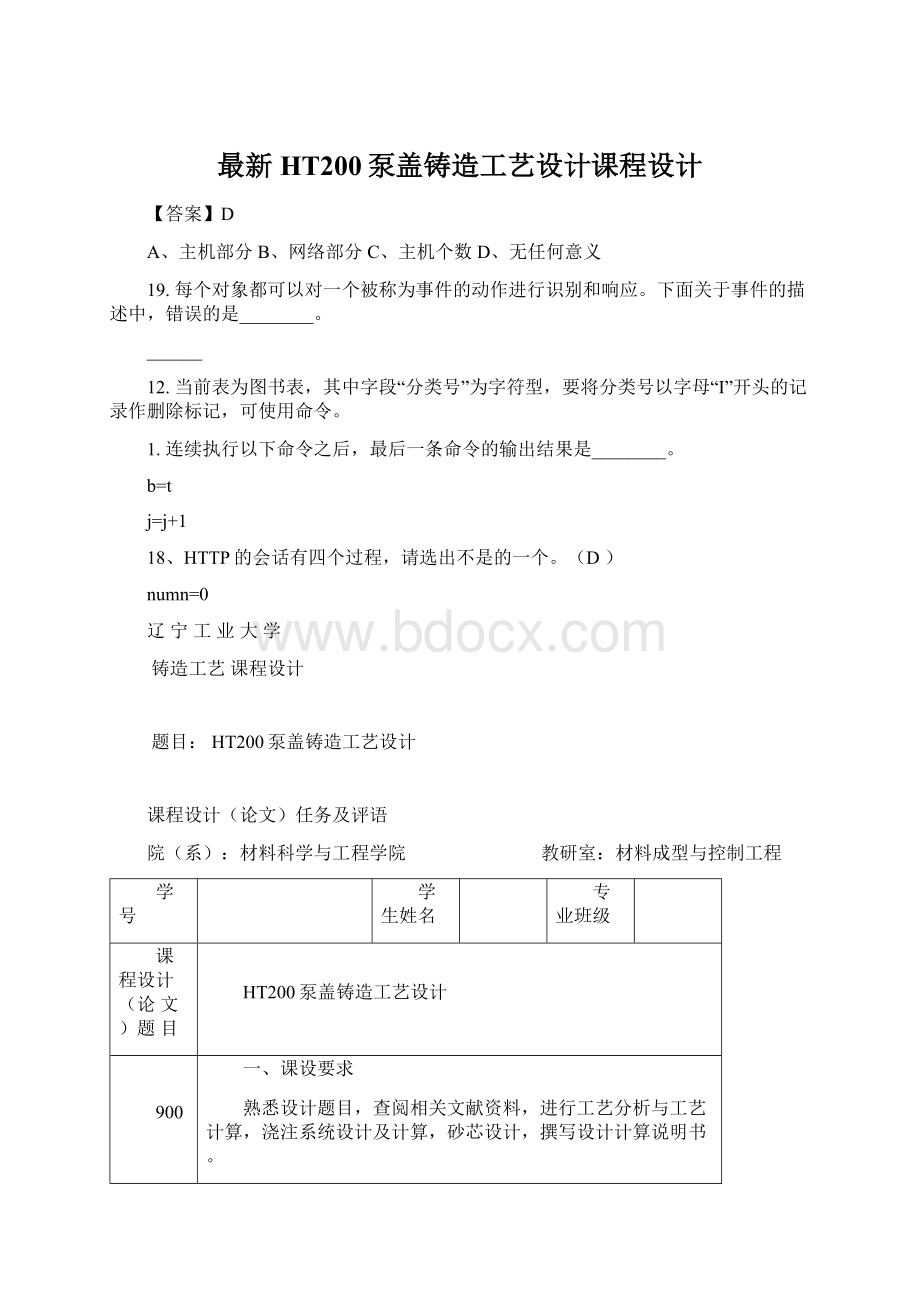
指导教师签字:
年月日
1铸造工艺及工装课程设计概念3
1.1铸造工艺及工装课程设计概念3
1.2铸造工艺及工装课程设计依据3
1.3铸造工艺及工装课程设计内容3
1.4设计任务的分析3
1.4.1铸件结构分析3
1.4.2生产性质、材料及技术要求3
2.1造型方法的选择4
2.2浇注位置和的确定和分型面的选择4
3砂芯设计及铸造工艺参数的选择7
3.1砂芯设计7
3.2铸造工艺参数选择8
4.1浇注系统的设计11
4.2浇注系统的计算13
5.1设计与选用砂箱的基本原则15
5.2砂箱类型的选择15
5.3砂箱结构15
前言
铸造是指熔炼金属,制造型腔,并将熔融金属浇入铸型,凝固后获得具有一定形状、尺寸和性能金属零件毛坯的形成方法。
铸造是世界历史上最悠久的工艺之一。
青铜冶炼技术的发明,使人类进入了青铜器时代。
伴随着青铜冶炼技术的同时,出现了铸造技术。
我国的铸造及技术已有近6000年悠久的历史,是世界上较早掌握铸造技术的文明古国之一。
随着现代科学技术的发展,要求金属铸件具有较高的力学性能,尺寸精度和低的表面粗造度值;
要求具有某些特殊性能,如耐热、耐腐蚀、耐磨等,同时还要去生产周期性低,成本低。
因此铸件在生产之前,首先应该进行铸造工艺设计,是铸件的整个工艺过程那个都能实现科学操作,才能有效的控制铸件的形成过程达到优质高产的效果。
铸造工艺设计就是根据铸造零件的结果特点,技术要求,生产批量,生产条件等确定铸造方案和工艺参数,绘制铸造工艺图,编制工艺卡等技术文件的过程。
铸造工艺设计的有关文件,试生产准备,铸件管理验收的数据,并用于直接指导生产操作。
因此铸件工艺设计的好坏,对铸件品质,生产和成本起着重要作用。
我们在铸造工艺学课本中学到的都是理论知识,为了加强对内容的理解,学校给我们安排了课程设计,让我们在进行工艺设计的过程中全方位考虑,从砂型,模样设计,浇注过程都有实际的体验,本次课程设计的目的是掌握铸造工艺设计的基本理论、基本原理和方法,了解砂型铸造的工艺设计内容,掌握零件结构的铸造工艺性,以及铸件结构包括的方法;
掌握如何确定铸件正确浇注位置,从而保证铸件质量;
掌握铸型分型面的选择应遵循的原则;
了解型芯的种类和材料,以及型芯的数量;
熟悉芯头设计是对砂芯的要求,芯骨、芯撑级排气在铸件红的作用及影响;
掌握铸造工艺包括的内容;
深刻感受和体会设计存在的问题,写出相应的设计小结。
1铸造工艺及工装课程设计概念
1.1铸造工艺及工装课程设计概念
铸造生产是一个诸多工序集成的复杂过程,包括金属熔炼、型砂配制和处理、造型制芯、含型浇注、落砂清理和回砂回用,人们往往把铸件的生产过程称为铸造工艺工程,对于某一个铸件,编制出其铸造生产工艺过程的技术文件就是铸造工艺过程。
1.2铸造工艺及工装课程设计依据
在进行铸造工艺设计前,设计者应先充分掌握客户的要求,熟悉企业和工厂的生产条件,这些是铸造工艺设计前的基本依据。
此外,要求设计者有一定的生产经验和设计经验,并应对铸造先进技术有所了解,具有经济观点和可持续发展观,才能很好地完成任务。
1.3铸造工艺及工装课程设计内容
铸造工艺设计技术会根据对铸造零件的要求、生产批量和生产条件、以及对铸件结构的工艺性分析等,用文字、图样及表格说明零件的生产工艺过程和工艺技术文件的过程。
1.4设计任务的分析
1.4.1铸件结构分析
此铸件为端盖,主要起定位,防尘,密封作用。
重量为5kg,结构对称,零件最大尺寸为220mm,高度为98mm,其主要的壁厚为12毫米,最大壁厚为12毫米,属于小型件。
1.4.2生产性质、材料及技术要求
(1)生产性质
铸件为大批量生产。
(2)材料
铸件材料为HT200。
2铸造工艺方案的确定
2.1造型方法的选择
2.1.1造型方法的选择
选择原则:
优先选用湿型。
应于生产批量相适应。
造型方法应适应于工厂条件。
要兼顾铸件的精度要求和技术。
常用的铸型方法有:
干型、湿型、水玻璃砂型、树脂砂型、表面烘干型、双快水泥砂型、石灰石砂型。
综上所述,最终选用机器造型湿型造型方法。
2.1.2造芯方法的选择
制芯方法有手工制芯和机器制芯。
机器制芯方法有:
震突式及翻台震实式:
微震压式;
挤压式;
射芯式。
手工制芯方法有:
芯盒制芯;
刮板制芯;
减皮制芯。
2.2浇注位置和的确定和分型面的选择
(1)铸件的浇注位置是指浇注时铸件在铸型中的位置。
浇注位置选取原则:
铸件的重要部位、重要加工面应朝下或呈直立状态铸件下部金属在上不金属的静压力作用下凝固并得到补缩,组织致密。
使铸件的大平面应朝下铸件大平面朝下既可避免气孔和夹渣,又可以放置在大平面上行程内砂眼缺陷。
如果将铸件的平面朝上,操作方便,但铸件平面部分的质量难以保证。
因此,应选用铸件平面朝下的方案,而浇注时,可采用倾斜浇注的方法。
应保证铸件能充满较大而壁薄的铸件部分应朝下、侧立或清下以保证金属液的充填。
应有利于铸件的补缩对于因合金体收缩率大或铸件结构厚薄不均匀而易于出现缩孔缩松的铸件,浇注位置的选择应优先考虑实现顺序凝固的条件,要便于安防冒口和发挥冒口的补缩作用。
厚大部分尽可能安放在上部位置,而对于中、下位置的局部厚大处采用冷铁或侧冒口等工艺措施解决其补缩问题。
避免用吊砂、吊芯或悬臂式砂芯,便于下芯、合箱及检验应尽量少用或不用砂芯,若需要使用砂芯时,应注意保证砂芯定位稳固、排气通畅和下芯级检验方便,应尽量避免用吊砂、吊芯或悬臂式砂芯。
应使合箱位置、浇注位置、和铸件冷却位置相一致这样可以避免在合箱后或浇注后再次翻转铸型。
翻转铸型不仅劳动量大,而且易引起砂芯移动、掉砂,甚至跑火等缺陷
(2)分型面是指两半铸型相互接触的表面,选分型面是应注意做到“四少两便”。
即,少用砂芯、少用活块、少用分型面、便于清理、便于合箱。
分型面选择原则:
铸件全部或大部分置于同意半型内,分型面主要是为了取出模样而设计的,但对铸件的精度会造成损害。
一方面,它使铸件产生错偏;
另一方面,由于合箱不严,在垂直分型面方面总会保持一定的“厚度”,在最小的精度下,这个分型厚度加大了铸件的偏差。
尽量减少分型面的数目,机器造型的中小件,一般只许可一个分型面,以便充分发挥造型机的生产率。
分型面应尽量选用平面,平直分型面可简化造型过程和模底板制造,易于保证铸件精度。
便于下芯、合箱和检查型腔尺寸,在下芯、合箱是,造型工需要检查型腔尺寸,在调整砂芯位置,才能保证壁厚均匀。
为此,应尽量把主要砂芯放在下半型中。
不使砂箱过高,分型面通常选在铸件最大截面上,意识砂箱不致过高。
高砂箱,造型困难,填砂、紧实、起模、下芯都不方便。
几乎多有造型机对砂箱高度都有限制。
受力件的分型面的选择不应削弱铸件结构强度。
注意减轻铸件清理和机械加工余量,要考虑到打磨飞翅的难易而选用分型面。
此外,选用的零件是一个端盖,重量为5千克,轴对称型,零件最大直径为220mm,零件的高度为98mm,属于中小型件。
零件内腔也是轴对称型,比较容易设计分型面和浇注位置。
以下是设计的两种方案
方案一,见图1
1.此方案将大平面置于底面,符合浇铸位置的选择原则;
2.铸件全部置于同一半型内,解决了铸件产生错偏和合箱不严的问题,整体性好,减小了铸件的偏差;
3.只有一个分型面,适于用机器造型,生产效率高;
4.分型面是一个平面,保证了铸件的精度,便于下芯、合箱和检查型腔尺寸;
5.砂箱选择合适,造型方便、填砂、紧实、起模;
铸件的重要部位、重要加工面呈直立状态;
6.能保证铸件充满,有利于铸件补缩;
图1分型面图
方案二,见图2
这种安排方式容易产生砂眼等缺陷,铸件可能会充不满,不利于铸件补缩,气孔和夹渣较多,砂芯固定不牢且要加工表面底面和侧面的质量无法保证。
综上所述:
为了使铸造更加方便,简化铸造工艺,方便工人操作,选择方案一比方案二好。
图2分型面图
3砂芯设计及铸造工艺参数的选择
3.1砂芯设计
3.1.1选择原则
砂芯的功用是形成铸件的内腔、孔和铸件不能出砂的部分。
砂芯应满足以下要求:
砂芯的形状尺寸及在砂型中的位置应符合铸件要求,具有足够的强度和刚度,在铸件形成过程中砂芯产生的气体能及时排出型外,铸件收缩是阻力小和容易清砂。
选用原则:
保证铸件内腔尺寸精度;
保证操作方便;
保证铸件壁厚均匀;
应尽量减少砂芯数目;
填砂面应宽敞,烘干支撑面是平面;
分型面选择应优先保证铸件质量,并方便造型下芯;
砂芯形状适应造型制芯方法。
除上述原则外,还应使每块砂芯有足够的断面,保证有一定的强度和刚度,并能顺利排出砂芯中的气体,使芯盒结构简单,便于制造和使用。
3.1.2芯头设计
芯头是指伸出铸件以外不与金属接触的砂芯部分。
对芯头的要求是:
固定砂芯,使砂芯在铸型中有准确的位置,并能承受砂芯重力及浇注时液体金属对砂芯的浮力,使之不致破坏;
芯头应能及时排出浇注后砂芯所产生的气体至型外;
上下芯头及芯号容易识别,不致下错方向或芯号;
下芯、合型方便,芯头应有适合斜度和间隙。
间隙量要考虑到砂芯、铸型的制作误差,又要飞出飞翅、毛刺,并使砂芯堆放、搬运方便,重心平稳;
避免砂芯上有细小突出的芯头部分,以免破坏。
(简图见图3)
由文献[1]《铸造工程师手册》表6-56、6-57得表3-1
表3-1芯头尺寸
L
h
a下
α下
S
98
15
5
7°
0.2
图3(砂芯简图)
3.2铸造工艺参数选择
铸造工艺参数通是指铸造工艺设计时需要确定的某些数据。
这些参数是:
铸造收缩率(缩尺)、机械加工余量、起模斜度、最小铸出孔的尺寸、工艺补正量、分型负数、反变形量、非加工壁厚的负余量、砂芯负数(砂芯减量)及分芯负数等。
工艺参数选取得准确、合适,才能保证铸件尺寸(形状)精确,使造型、制芯、下芯、合箱方便,提高生产率,降低成本。
工艺参数选取不准确,则铸件精度降低,甚至因尺寸超过公差要求而报废。
3.2.1铸件尺寸公差
铸件尺寸公差是指铸件公称尺寸的两个允许极限尺寸之差,在这个允许极限尺寸之内铸件可满足加工、装配和使用的要求。
铸件的尺寸精度取决于工艺设计及工艺过程控制的严格程度,铸件尺寸精度越高,对因素的控制越严格,铸件生产成本相应地也要提高,必需有科学的标准来协调供需双方的需求。
查表6-25铸件尺寸公差等级表得HTCT8-12
查表6-27铸件尺寸公差数值表得CT10长6mm高4mm
3.2.2铸件重量公差
铸件重量公差定义为以占铸件公称重量的百分率为单位的铸件重量变动的允许值。
查表6-35铸件尺寸公差质量等级表得HTMT8-10
查表6-34铸件尺寸公差质量数值表得MT910%
3.2.3机械加工余量
铸件为了保证共加工面尺寸和零件精度,应有加工余量。
即在铸件工艺设计时预先增加的,而后在机械加工时又被切去的金属层厚度,称为机械加工余量。
查表6-37机械加工余量等级表得HTE-G
查表6-38得机械加工余量取G级为
3.2.4铸造收缩率
铸造收缩率K的意义是:
式中
——模样(或芯盒)工作面的尺寸
——铸件尺寸
由文献[2]表2-17查得,铸件的自由收缩率K=1.0%,受阻收缩率K=0.9%
3.2.5起模斜度
为了方便起模,在模样、芯盒的出模方向留有一定斜度,以免损坏砂型或砂芯这个斜度,称为起模斜度(示意图如图4)。
在铸件加工面上采用增加铸件尺寸法;
在铸件不与其他零件配合的非加工表面上,可采用增加,增加和减少或减小铸件尺寸法;
在铸件与其它配合的非加工表面上,采用减少或增加和减少铸件尺寸法。
由文献[1]表3-24,查得表3-2
表3-2金属模样的起模斜度
高度(mm)
α(度)
0°
30′
a(mm)
1
3.2.6最小铸出孔及槽
零件上的孔、槽、台阶等,究竟是铸出来好,还是机械加工出来好,这应从品质及经济角度等方面考虑。
一般来说,较大的孔、槽等,应铸出来,以便节约金属和加工工时,同时还可以避免铸件局部过厚多造成的热节,提高铸件质量。
较小的孔、槽,或者铸件壁很厚,则不宜住铸出孔,直接依靠加工反而方便,有些特殊要求的孔、槽,如弯曲孔,无法实行机械加工,则一定要铸出。
可用钻头加工的受制孔最好不铸,铸出后很难保证铸孔中心位置准确,再用钻头扩孔也无法纠正中心位置。
经查表6-44零件中有9个M12深12的孔不需要铸出。
3.2.7工艺补正量
在单件,小批量生产中,由于选用的缩尺与铸件实际收缩率不符,或由于铸件产生了变形,,操作中的不可避免的误差等原因,使得加工后的铸件某些部分的厚度小于图样的要求尺寸,严重时,因强度太弱而报废,因工艺需要在铸件相应非加工面上增加的金属层厚称为工艺补正量。
3.2.8分型负数
平砂型、表面烘干型以及尺寸很大的湿型,分型面由于烘烤、修整等原因,一般都不很平整,上下型接触面很不严密,为了防止浇注时跑火,合箱前需要在分型面之间垫以石棉绳、泥条或油灰条等,这样在分型面出明显地增大了铸件的尺寸。
为了保证铸件尺寸精准,在拟定工艺时,为抵消铸件在分型面部位的增厚,在模样上相应减去的尺寸,称为分型负数。
3.2.9反变形量
铸造较大的平板类、床身类铸剑时,由于冷却速度的不均匀性,铸件冷却后常出现变形。
为了解决挠曲变形问题,在制造模样时,按铸件可能产生变形的相反方向做出反变形模样,使铸件冷却后变形的结果正好将反变形抵消,得到符合设计要求的铸件。
这种在模样做出的预变形量称为反变形量。
3.2.10砂芯负数
大型黏土砂在春砂过程中砂芯向四周涨开,制涂料及烘干过程中发生的变形使砂芯四周尺寸增大,为了保证铸件尺寸准确,将芯盒的长、宽尺寸减去一定量,这个被减去的尺寸称为砂芯负数。
3.2.11非加工壁厚的负余量
为了保证铸件尺寸的准确性,凡形成非加工壁厚的木模或芯盒内的肋板厚度尺寸应该减小,即小雨图样尺寸,所减小的厚度吹吹牛称为非加工壁厚的负余量。
4浇注系统设计与计算
4.1浇注系统的设计
浇注系统是指铸型中液态金属流入型腔的通道,通常由浇口杯、直浇道、横浇道、内浇道等单元组成。
基本要求:
应在一定的浇注时间内,保证充满铸型,保证铸件轮廓清晰,防止出现浇不足缺陷。
应能控制液体金属流入型腔的速度和方向,尽可能使金属液平稳流入型腔,防止发生冲击、飞溅和漩涡等不良现象,以免铸件产生氧化夹渣、气孔和砂眼等缺陷。
应能把混入金属液中的熔渣和气体挡在浇注系统里,防止产生夹渣和气孔缺陷。
应能控制铸件凝固是的温度分布,减少或消除铸件产生缩孔缩松、裂纹和变形等缺陷。
浇注系统结构应力求简单,简化造型、减少清理工作量和也题金属的消耗。
4.1.1浇注系统类型的选择
(1)分类:
按浇注系统各单元截面积的比例分类,可分为封闭式、半封闭式、开放式和封闭开放式等四种类型。
封闭式:
金属液容易充满浇注系统,挡渣能力较强,但充型液流的速度较快,冲刷力大,易产生喷溅。
一般地说,金属液消耗少,且清理方便,适用于铸铁的湿型小件及干型中、大件。
开放式:
充型平稳,对型腔冲刷力小,但挡渣能力较差。
一般地说,金属液消耗多,不利于清理,常用与非铁合金、球墨铸铁及铸钢等易氧化金属铸件,灰铸铁件上很少应用。
半封闭式:
浇注系统能充满,但较封闭式晚,具有一定的挡渣能力,由于横浇道截面积大,金属液在横浇道中的流速减小。
充型的平稳性及对型腔的冲刷力都优于封闭式,适用于各类灰铸铁机球铁件。
封闭开放式:
有利于挡渣,又使充型平稳,兼有封闭式与开放式的优点。
适用于各类铸铁件,在中小件上应用较多,特别是在一箱多件时应用广泛。
按金属液导入铸件型腔的位置分类,可分为顶住式、中注式、低注式。
顶住式:
适用于结构简单的小件及补缩要求高的厚壁铸件。
中注式:
适用于壁厚较均匀,高度不太大的各类中、小型铸件。
底注式:
适用于形状复杂的铸铁件。
综合比较,选用底注式半封闭式浇注系统。
(2)浇注位置的选择
从铸件薄壁外引入适用于壁薄而轮廓尺寸又大的铸件。
从铸件厚壁外引入使用于方向性凝固,有利于补缩铸件,达到消除缩孔获得致密铸件的方法。
内浇道尽可能不开设在重要部位。
内浇道要引导液流不正面冲击铸型型壁级砂芯或型腔中薄弱的突出部分
应该使金属液在型腔内流动的路程尽可能地短,避免因浇道过长金属液的温度降的过快而造成浇不足现象。
内浇道开在非加工面上时,要尽可能开在隐蔽的、不宜看到的或同意打磨的地方,尽可能地保持铸件外表美观。
4.1.2内浇道位置和数量的确定
见图4
图4浇道简图
4.1.3直浇道位置的和高度的确定
(1)浇注时间的计算
计算10t以下割裂铸件的浇注时间,常用公式如下:
——浇注时间,s;
——包括冒口在内的铸件总重量,Kg,
;
s——系数由铸件壁厚确定取s=2.2,计算得
=4.9s,
由文献[2]查表2-8,知符合允许的最小速度。
(2)平均压头的高度
由文献[1]查表3-59、表3-60,得表4-1
——平均压头高度
——剩余压力头
——铸件最高、最远点至直浇道中心线的水平距离
——压力角
表4-1平均压头高度(mm)
L()
α
50
200
150
4.2浇注系统的计算
阻流阻元截面的大小实际上反映了浇注时间的长短。
在一定的压头下阻流截面大看,浇注时间就短,所以阻流截面的大小对铸件质量的影响与浇注时间长短的影响基本一致。
内浇道的计算:
——内浇道截面积,
——流经阻流截面积的金属液的总重量,Kg,G=5Kg;
——流量系数;
——充填型腔是的额平均计算静压头,cm
由文献[2]表3-4查得
=0.52
计算得
=1.42
=
由文献[2]表3-6查得
由文献[1]表3-42、表3-62、表3-63查得表4-2(直浇道简图如图5)
表4-2浇道截面尺寸和浇口尺寸
a
b
内浇道
14
12
6
横浇道
直浇道
D1=19D2=15L=200
图5
5砂箱设计
根据铸件的大小、吃砂量、遗迹压头和造型机的选择确定砂箱的内部尺寸,确定具体尺寸,为绘制合箱图做准备。
5.1设计与选用砂箱的基本原则
5.1.1铸造工艺要求
如砂箱和模样间应有足够的吃砂量、箱带不妨碍浇冒口的安防不严重阻碍铸件收缩等。
5.1.2尺寸和结构符合造型机、期中设备、烘干设备的要求
砂箱尺寸、形状是设计或选购造型机的主要依据。
为此,大量生产中应对计划在造型线上生产的全部铸件逐一进行铸造工艺分析,以确定公用砂箱的尺寸和形状。
5.1.3刚度强度
有足够的强度和刚度,使用中保证不断裂或发生过大变形。
5.1.4附着力要求
对型砂有足够的附着力,使用不掉砂或塌箱,但又要便于落砂。
5.1.5耐用性
经久耐用,便于制造.
5.1.6标准
应尽可能便准化、系列化和通用化。
5.2砂箱类型的选择
5.2.1专用砂箱和通用砂箱
专用某一复杂或重要铸件设计的砂箱为专用砂箱,凡是模样尺寸合适的各种铸件均可使用的砂箱为通用砂箱。
多为长方形。
本铸件使用专用砂箱。
5.2.2砂箱的制造方法
依制造方法分类可分为整铸式、焊接式和装配式。
本砂箱为焊接式。
5.2.3砂箱的造型方法
依造型方法及使用条件分为手工造型用砂箱、机器造型用砂箱,高压、气冲造型用砂箱等。
此工艺的造型方法为机器造型用砂箱。
5.3砂箱结构
5.3.1吃砂量
砂箱名义尺寸是指分型面上砂箱内框尺寸(长度
宽度)乘砂箱高度。
确定砂箱尺寸是要考虑一箱内防止铸件的个数和吃砂量。
吃砂量的最小参数参照表5-1.所设计的砂箱长度和宽度应是50或100的倍数,高度应是20或50mm的倍数。
表5-1吃沙量的最小值(mm)
模样高
8
10
25
30
35
40
60
70
90
120
吃砂量
18
20
24
26
28
32
38
45
综上所述,本砂箱尺寸上箱尺寸:
450×
下箱尺寸:
200
5.3.2砂箱壁的断面形状、尺寸影响强度和刚度。
其结构及尺寸参照文献[1]选用。
5.3.3箱带
箱带(箱挡、箱肋)增加对型砂的附着面积和附着力,提高砂型总体强度和刚性,防止塌箱和掉砂,延长砂箱使用期限。
但是紧砂和落砂困难,限制浇冒口的布局,故用于中、大砂箱。
平均内框尺寸小于500mm的普通砂箱、小于1250mm的高压造型用砂箱可不设箱带。
本砂箱不设计箱带。
5.3.4上下箱的定位方法
有多种:
泥号、箱垛、箱锥、止口及定位销等。
机器造型时只用定位销定位,插销多用于成批生产的矮砂箱,座销用于大量生产的各种砂箱。
箱耳多布置在砂箱两端,一端装圆孔的定位套(或销),一端装长孔的导向套。
合箱时上下箱的圆孔套对应圆销,另一端对应方销。
本砂箱采用ψ12定位销定位。
5.3.5搬运、翻箱结构
手把用于小型砂箱,吊轴广泛用于各种中大砂箱。
吊环主要用于重型砂箱。
本砂箱采用整铸式吊轴,其结构及尺寸参照文献[1],上砂箱使用吊轴。
5.3.6紧固方式
为防止胀箱、跑火等缺陷,上下箱间应紧固。
紧固方式有:
上箱自重法、压铁法、手工夹紧(箱卡)法和自动卡紧法等。
实验后,如出现胀箱、跑火等缺陷,根据生产经验及现有条件,可采用压铁。