直线振动给料机Word文件下载.docx
《直线振动给料机Word文件下载.docx》由会员分享,可在线阅读,更多相关《直线振动给料机Word文件下载.docx(30页珍藏版)》请在冰豆网上搜索。
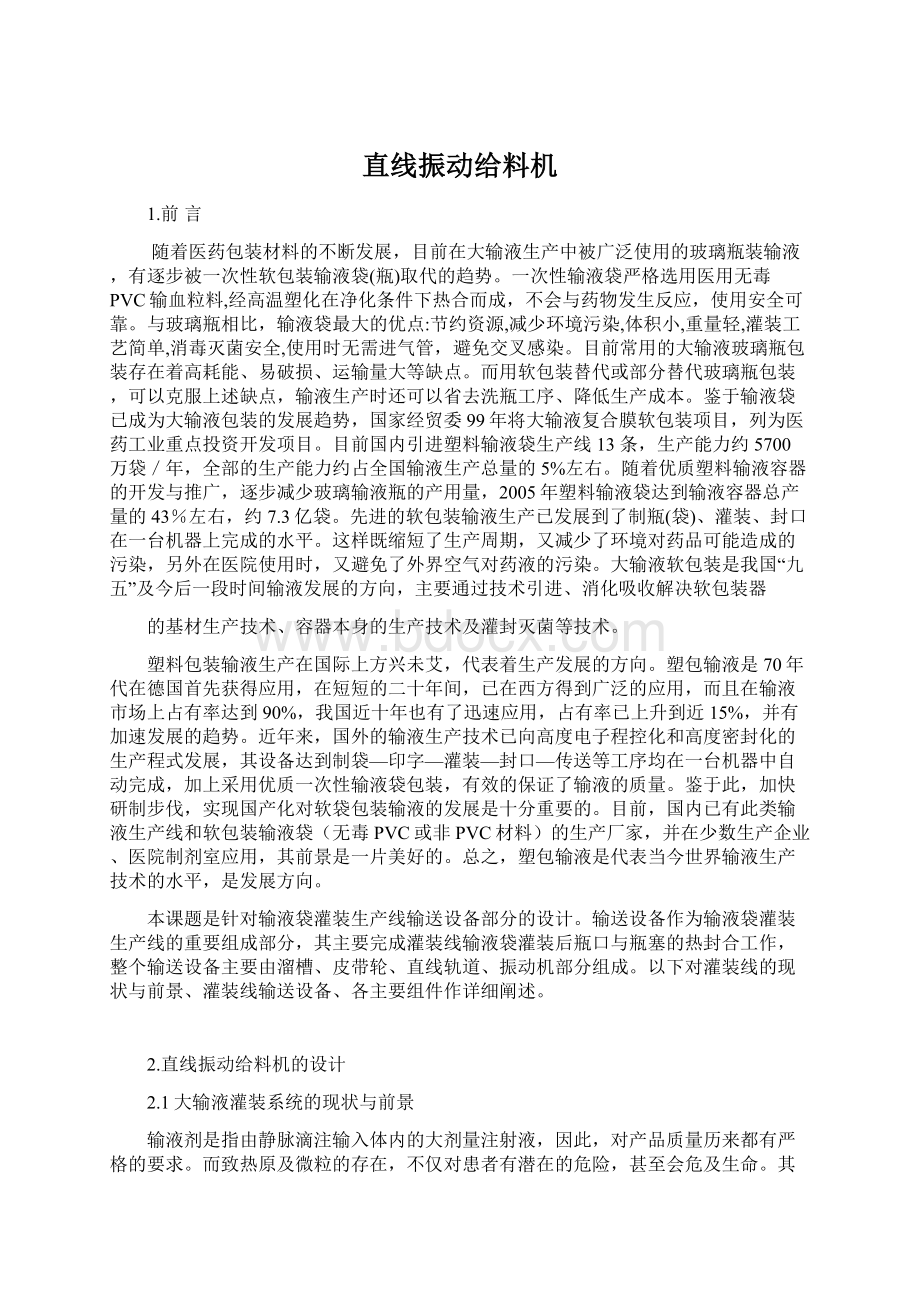
输送设备作为输液袋灌装生产线的重要组成部分,其主要完成灌装线输液袋灌装后瓶口与瓶塞的热封合工作,整个输送设备主要由溜槽、皮带轮、直线轨道、振动机部分组成。
以下对灌装线的现状与前景、灌装线输送设备、各主要组件作详细阐述。
2.直线振动给料机的设计
2.1大输液灌装系统的现状与前景
输液剂是指由静脉滴注输入体内的大剂量注射液,因此,对产品质量历来都有严格的要求。
而致热原及微粒的存在,不仅对患者有潜在的危险,甚至会危及生命。
其来源除与原辅料(包括水质)、配药工艺、药液净化与输送系统有关外,也与内包材料、灌装工艺、设备的选择有关。
以下就灌装生产线工艺及设备的选择以及装备的现状与发展前景作一概述。
2.1.1玻瓶输液生产的洗灌封联动生产线
带有外刻度玻璃瓶是输液的常用容器。
自输液用于临床治疗至今仍在普遍应用。
初始,其生产过程全部都是手工操作,工作效率低,产品质量没有保证,为减少劳动强度,相继出现半机械化的刷瓶机,灌装机和单头简易轧盖机,但仍然是人工遂瓶操作。
国内直到六十年代初出现第一台工厂的革新产品棗滚筒式洗瓶机、转盘式漏斗灌装机,为提高工作效率又用带支撑板的凡布皮带式传送带将其串联,这就是生产联动线的雏型。
80年初,上海医药设计院与重庆药机厂联合设计制造国内的第一条玻瓶大输液生产联动线,实现了机械化,自动化,联动化,降低了人为污染的几率。
尽管在当时的条件仍有许多不足,无疑,这是输液生产的一大进步。
经十几年来的不断改进,不仅完成了落膜、落塞、翻塞设备的配套,而且洗瓶、灌装推出多种型号、规格的设备。
我国玻瓶输液生产近十年来不仅在单机结构、加工精度、材料优化、自控程度、整机性能上有可喜的进步,而且在实现洗、灌、封系统控制,连续作业,采用先进的光电控制以及PC机控制系统而达到机电一体化。
这不但大大降低劳动强度,提高劳动生产率,减少岗位操作人员,有效地防止人为污染。
98'
CWP附录中重申凡与药液接触的设备材料必须是不与药液起反应,其表面必须光洁、无死角、便于清洗与消毒。
这一指导思想也在灌装机,洗瓶机的零部件得到较充分的体现。
这说明GMP已在与药品生产有关的相关行业得到重视,尤其在我国仍有占85%以上的输液产品、产量以玻璃瓶为灌装容器的情况下,而且这种生产方法还得持续相当长一段时期,这对防止微生物和微粒污染确保人民的用药安全,其意义不可低估,人们期待药机行业能再接再厉,进一步改进与完善,推出国际上一流的产品。
2.1.2塑料包装输液生产在国际上方兴未艾,代表着生产发展的方向
随着医药包装材料的不断发展,目前在大输液生产中被广泛使用的玻璃瓶装输液,有逐步被一次性软包装输液袋(瓶)取代的趋势。
一次性软包装输液袋由无毒聚氯乙烯(PVC)原料,经高温(180~190℃)塑化,在洁净条件下,热合而成的真空袋体,无污染、无残留物,为输液的灌装提供了洁净可靠的包装容器,从而在很大程度上能减少输液包装内源性和外源性的污染,保证了输液的内在质量。
塑包输液是70年代在德国首先获得应用,在短短的二十年间,已在西方得到广泛的应用,而且在输液市场上占有率达到90%,我国近十年也有了迅速应用,目前,国内已有约26家工厂引进了各类塑料软包装输液生产线,其中软袋输液生产线13条,塑料生产线13条。
分布在北京、天津、上海、山东、广东、湖北等省市。
全部的生产能力约占全国输液生产总量的5%左右,预计到2003年底,占有率将上升到近15%,并有加速发展的趋势,因投资大,生产成本高所以应用范围有限,但对高附加值品种及进军国际市场的产品是必要的。
2.1.2.1塑包与玻瓶输液的简要比较
由于塑料包装容器,尤其是非PVC软装,半硬瓶容器已具备GMP对灌装药液的要求,同时又具有重量轻、耐冲击、用时无需回气避免污染药液等玻瓶难以具备的优点,此外,还有制瓶原料体积小、运量少,无需空瓶库的优点,例如3万个500ml玻瓶,体积90M3而同等数量塑瓶的粒料仅1.5M3,其体积比为60:
1,又如产量3000瓶/时的500ml玻瓶生产线为1.8×
27M,占地约48M2,而能力相同的三合一塑包机占地约4M2,其比例为12:
1,所需人员前者约12人,后者为2人。
人员减少意味着微粒、微生物污染比率的降低,产品质量的提高。
三合一塑包机实现制瓶、灌装、封口均在百级层流保护下进行自动化生产,外环境洁净度可以是10万级,而玻瓶生产线则百级区大约13M2,万级区近100M2,10万级区,也近20M2。
由此可见,所节省的空调净化动力费用也就不言而喻了。
静脉输液应用于疾病治疗以来,其容器经历了三代的变化:
第一代全开放式输液容器为广口玻璃瓶。
广口玻璃瓶使用时需打开瓶盖倾注液体,故液体大量暴露与空气中,气载微生物及微粒可严重污染液体。
第二代半开放式输液容器为玻璃瓶(或塑料瓶)。
尽管玻璃瓶是密封的,但在使用过程中仍需插入空气针,建立空气通路,使得输液能够顺利滴注,因此空气中的微生物及微粒仍可通过空气针进入输液,对人体构成威胁。
第三代封闭输液容器为全封闭塑料软袋。
目前,塑包容器分:
硬瓶、半硬瓶及软袋三种,我国早期引进的塑瓶生产线大多属硬瓶,材质有聚氯乙烯、聚乙烯、聚丙烯,现在,已有些企业向半硬瓶过渡。
软袋则多数为聚氯乙烯(PVC)。
近几年来,有些新建输液塑包企业,则采用聚乙烯、聚丙烯袋,多层共挤膜袋也在推广应用,从制膜袋灌装、封口的完整生产线的企业为数不多,更多的是买国外的膜或袋而引进灌装机或国产的塑袋灌装机(上海伟海、重庆均有生产)再热封口。
由于受资金和国产材料的限制,我国的塑包输液生产线起步较晚,但发展速度正在加快。
目前,有些企业相继引进国外生产线,虽然价格昂贵、但科技含量高,主要零部件材料优质(尤其是模具材料)较高,加工精度严格和自动化程度高,总之,一句话:
技术先进。
引进的目的是消化、吸收,为我所用,为的是花了学费,学了知识,来提高我们的装备水平。
我国非药用的普通塑瓶,塑袋生产线五花八门,唯独输液的专用容器较长时间来一直无人问津,尽管利润丰厚,却无国产设备问世。
大输液软包装是我国“九五”及今后一段时间输液发展的方向,主要通过技术引进、消化吸收解决软包装容器的基材生产技术、容器本身的生产技术及灌封灭菌等技术。
2.1.2.2大输液软包装技术与药用丁基胶塞生产技术
(1)大输液软包装技术。
指用高分子材料或高分子复合材料制成输液容器的大输液生产技术。
(2)药用丁基胶塞生产技术。
丁基胶塞是以丁基橡胶为主要原料的药用橡胶塞。
与我国目前使用的天然橡胶相比,具有气密性与稳定性好等优点。
在发达国家已全部使用丁基胶塞。
为保证用药安全,国家医药局已用行政命令停止了部分产品使用药用天然胶塞,我国在“七五”、“八五”相继引进了药用丁基胶塞的生产技术,但是在国产化与产业化方面还存在不少问题。
一是丁基胶合成技术,目前我国使用的丁基胶全部进口;
二是丁基胶塞的生产工序控制、模具及真空硫化机的研制开发;
三是丁基胶塞与各种药物配伍稳定的配方研制;
四是丁基胶塞生产专用的清洗、硅化设备的研究开发。
2.1.2.3三合一无菌包装技术在输液生产中的应用
所谓"
三合一"
包装技术系指将PE或PP颗粒加势制成管胚,然后吹瓶,瓶子在灌装与封口工位由芯棒精确定量灌装药液,芯棒抽出后封口,散后由输送带将药瓶送出,此为全套生产过程。
所有吹注、灌药、封口这三步生产过程均在一台机器内无菌状态下进行,达到无微粒和无发热原质量标准,这是瑞士RommeleagAG公司的生产工艺。
据该公司98在黄山全国输液技术交流会上介绍的bottclpack的液体灌装系统"
设备,整机占地不足4M2,每小时生产能力3000瓶500ml规格的输液,本文就其设备的生产工艺作一简要的概述:
详见附图及其部件标示作如下说明。
首先把经过消毒的PE或PP粒料送至料斗,
(1)由带螺纹和圆柱的挤出机
(2)将已加热至180℃的熔化塑粒挤压成管胚(6),同心的吹瓶/灌装销(5)移入塑料管胚(6),模具的运转速度同挤压机是同步的,吹瓶/灌液销(5)也是同步向下运动至管胚内,并同模具一同运动,模具(10)关闭时,首先封闭瓶底,当吹瓶/灌液销(5),移至下方时,瓶子同管子净化的空气充满药液槽(7),和计量灌液机(8)将定量的药液经管子(13)和灌液喷嘴(14),灌入瓶内,在制瓶和灌液时同时进行排气,当专用复合芯棒退出后立即瓶盖模闭合,将瓶盖封闭(采用真空操作形成密封口)。
对于无菌灌装工艺除采用活塞定量系统外,也有的采用时间压力定量系统、灌装精度可达+/-0·
5%,由于从进料至灌装头,完全是百级封闭环境,这是对外环境无需高洁净度要求的原因,同时,设备本功还配有微粒过滤器(5um)及除菌过滤器(0·
2um),产品管线可进行在位清洗(CIP),还可与空气管线一起进行在位蒸汽消毒(S1P),由于污染的可能性极低,产品的安全性得到很大的改善。
该机还配有塑料粒料,空气质量,药液无菌状态等的自动监控仪器,仪表等,进行有关数据的测试并作记录。
除上述介绍RommclcagAG公司bottelack三合一设备外,国内如四平药厂引进日本的塑瓶灌装生产线,这是七十年代——八十年代产品,其工艺就较繁锁,制瓶后又增加一道净化压缩空气吹洗,以克服制瓶中可能带入的微粒。
据说,日本国内还有注射水洗瓶以确保药液的澄明度。
瓶口及密封设计,可根据地区习惯采用内置胶塞瓶头(即当制瓶灌装一结束胶塞被迅速压入瓶颈,仍处于热融状态的塑料毛坯头部将胶塞包容形成紧密的密封。
此外带有拉环和胶垫(与药液不接触)的欧洲盖及其形成的瓶头,是另一种密封方式。
2.1.2.4制袋、灌装、封口软袋包装输液工艺技术的现状
输液软袋包装60年代虽在国内应用过,如血液、透析液及电解质输液产品,但大多是采用PVC袋,国内“文革”时期,为了适应战备的需要,当时一些输液厂都试制过,80年代初,天津的和平药厂已批量生产,但由于材料、工艺等原因出现过塑袋输液的医疗事故,故在国内推广、应用出现了挫折,随着,国际上制袋灌装封口技术的改进,尤其是多层共挤出膜袋的问世,无疑,为软包输液的发展注入新的活力。
由于非PVC共挤出膜输液袋具有无毒付作用,水、气透过率低,消毒不变色、无环保问题,所以自80年代末90年代初以来得到迅速发展。
过去,输液软袋用的是PVC单层膜,它不仅与药物相容性差,水气透过性指标、灭菌后透明度都差,而且有一定期的毒性,对环境造成新的污染,因此,改由非PVC的复合膜部分取代。
当时,此类膜只能生产单幅平膜,对生产环境要求很高,制袋前要对膜进行清洗、干燥、给生产上带来很多的麻烦。
而后出现的多层共挤出膜则是高温挤出,保证内表面无菌,封闭的筒型膜,内部吹入100级空气保护,保证符合洁净要求,使用方便,现己成为制膜业的发展趋势。
近年来,国外的输液生产技术已向高度电子程控化和高度密封化的生产程式发展,其设备达到制袋—印字—灌装—封口—传送等工序均在一台机器中自动完成,加上采用优质一次性输液袋包装,有效的保证了输液的质量。
目前,国内已有此类输液生产线和软包装输液袋(无毒PVC或非PVC材料)的生产厂家,并在少数生产企业、医院制剂室应用,其优越性不言而喻。
美国是世界上生产非PVC复合膜软袋大输液最早的国家,也是目前此类产品产量最大的国家。
美国PDC公司专业生产非PVC软袋输液的全自动制袋、灌装和封口生产线。
另外,PDC公司也是一家工程公司,可承接全套的药厂,特别是输液药厂的设计、工艺、承造、安装、调试、验证、技术培训等交钥匙工程。
其PDC的非PVC软袋输液生产线技术特点简略如下:
全自动操作,生产过程不经人手,
配备薄膜自动导向装置,变换软袋规格无需更换模具,可多色印刷,
双封口管,确保口管与薄膜有牢固的封合,将制袋和灌封区隔离,以设备自带的空气系统维持灌封区较制袋区的正压,配备HEPA空气过滤器,提供100级层流,采用高精确流量计,保证分装精度,可采用单口管或双口管,
配备大屏幕自控操作界面,采用WindowsNT为操作平台,操作界面可选用中文显示,电脑系统可与PDC主机通过网络连接,进行远程诊断和故障排除。
在'
98黄山全国大输液第六次交流会上德国PLUMAT公司介绍了该公司生产的制袋-灌装-封口生产线,此类设备分全自动与半自动两种型号,可用于PVC、PE或PP的各类型袋,全线由制袋和灌装及封口等设备组成,制袋机又分全自动(能力4000袋/时)半自动(能力700袋/时)两种,灌装机分自动型(2000--6000袋/时)半自动型(600袋/时)这可根据产量要求加以选择,袋口密封既可以通过焊接系统,如高频,超声或热封作选择,也使用不同种类的胶塞或注射器插入口形式。
其生产过程即,筒上的膜送入一个热箔系统对膜按袋的设计要求进行部分或全面印刷后进行外形封口,冷却后进行修剪,然后与接口送料口汇合进行接头封口,完成上部和最后封口后,进入出袋工位,袋可直接进入灌装区的进袋工位,使其处于真空状态,再送入灌装区,完成灌装后产即加盖,结束后出袋。
整个系统可随机检测膜或袋是否合格,对不合格品立即剔除。
此外,也可以使用合格袋,由印刷装置对合格袋进行印刷。
然后进入灌装封口工位,灌装头数日取决于装量及产量要求。
软袋生产线较塑瓶灌装线占据空间体积大。
同时,由于多层共挤膜的生产技术要求高,对原料的纯度配方要求严格,此制膜技术尚未与制袋配套供应,所以,膜的供应及定价仍掌握在外商手中。
故,掌握多层共挤膜的PE、PP及其它膜料的配方及技术是多层膜制造的关键,我们需加快研制步伐实现国产化对软袋包装输液的发展是十分重要的。
总之,塑包输液是代表当今世界输液生产技术的水平,是发展方向,但我们有向己的国情,大众输液仍然还是以玻瓶包装为主,我国的人口仍然有85%以上在农村,城市工薪阶层仍占绝大多数,所以,在加快输液改造时应顾及国情,当然不可否认,对于进入国际市场及高附加值的产品,在资金、物力、技术允许的条件下,采用塑包技术是可取的,但切不可盲目追求,一轰而上,造成财力的浪费。
在发展塑包的同时,不可忽视在相当长一段时期国内市场还是以玻瓶输液为主导。
故玻瓶洗瓶、灌装、封口生产线技术应不断改进,不断提高,使之更加合理,更加先进。
2.2设计基本原则
2.2.1机器设计基本原则
1.使用功能原则
机器应有预定的使用功能。
这主要是靠正确地选择机器的工作原理,正确地设计或选用能够全面实现功能要求的执行机构、传动机构和原动机,以及合理地配置必要的辅助系统来实现。
2.经济性原则
机器的经济性体现在设计、制造和使用的全部过程中,设计机器时就要全面综合地进行考虑。
设计制造的经济性表现为机器的成本低;
使用经济性表现为高生产率,高效率,较少地消耗能源、原材料和辅助材料,以及低的管理和维护费用等。
提高设计和制造经济性指标的主要途径有:
(1)采用先进的现代设计方法,使设计参数最优化,达到尽可能精确的设计计算结果,保证机器足够的可靠性。
尽可能采用CAD技术,加快设计进度,降低设计成本。
(2)最大限度地标准化、系列化及通用化的零、部件。
零件结构应该尽可能采用标准化结构和尺寸。
(3)尽可能采用新技术、新工艺、新结构和新材料。
(4)合理组织设计和制造过程。
(5)力求改善零件的结构工艺性,使其用料少、易加工、易装配。
提高使用经济性指标的主要途径:
(1)合理地提高机器的机械化和自动化水平,以提高机器的生产率和产品的质量。
(2)选用高效率的传动系统,尽可能减少传动的中间环节,以期降低能源的消耗和生产成本。
(3)适当地采用防护(如闭式传动、表面防护等)及滑润,以机器的使用寿命。
(4)采用可靠的密封,减少或消除渗漏现象。
3.劳动保护和环境的原则
(1)要使设计的机器符号劳动保护法规的要求,为操作者提供方便和安全的条件。
因此设计时要按照人机工程学的观点尽可能减少操作手柄的数量,操作手柄及按钮等应放置在便于操作的位置,合理地规定操作方式要符合人们的心理和习惯(例如汽车转向盘向左打则汽车向右拐弯等)。
同时,设置完善的安全保护及保安装置、报警装置、显示装置等。
(2)改善机器周围及操作者的环境条件。
降低机器运转时的噪声水平,防止有毒、有害物质的渗漏,对废水、废气和废液进行治理,根据工程美学的原则美化机器的外型及外部色彩等。
4.可靠性原则
关于可靠性的要求是在机器的组成日趋复杂的背景下发展起来的。
机器的可靠性的高低是用可靠度来衡量的。
机器的可靠度R,是指在规定的使用时间内和预定的环境条件下机器能够正常工作的概率。
机器不能正常工作,即机器由于某种故障而不能完成其预定的功能叫做失效。
和机器的生产能力或额定功率等一样,机器的可靠性是机器的一种固有属性。
机器出厂时已经存在的可靠性叫做机器的固有可靠性。
它在机器的设计、制造阶段已经确定。
作为机器的用户其使用机器的经验、维修能力和技艺都有很大的差别。
考虑到用户的这些人为因素,已出厂的机器(即已具有确定的固有可靠性的机器)正确地完成预定功率的概率,叫做机器的使用可靠性。
作为机器的设计者,当然对机器的可靠性起到决定性的影响。
5.其它专业原则
对于不同的机器,还有为该机器所特有的要求。
在设计机器时,在满足前述共同的基本要求的前提下,还应着重地满足这些特殊要求,以提高机器的使用性能。
机器的各项要求的满足,是以组成机器的机械零件的正确设计和制造为前提的。
亦即零件设计的好坏,将对机器使用性能的优劣起决定性的作用。
2.2.2机器零件设计基本原则
1.在预定寿命内失效的原则
(1)强度
零件在工作中发生断裂或不允许的残余变形统属于强度不足。
上述失效形式,除了用于安全装置中预定适时破坏的零件外,对任何零件都是应当避免的。
因此,具有适当的强度是设计零件时必须满足的最基本要求。
施为了提高机械零件的强度,在设计时原则上可以采用以下的措施:
采用强度高的材料;
使零件具有足够的截面尺寸;
合理地设计零件的截面形状,以增大截面的惯性矩;
采用热处理和化学处理方法,以提高材料的力学性能;
提高运动零件的制造精度,以降低工作时的动载荷;
合理地配置机器中各零件的相互位置,以降低作用于零件上的载荷等。
(2)刚度
零件在工作时所产生的弹性变形不超过允许的限度,就叫做满足了刚度要求。
显然,只有当弹性变形过大就要影响机器工作性能的零件(例如机床主轴﹑导轨等),才需要满足这项要求。
对于这类零件,设计时除了要作强度计算外,还必须作刚度计算。
零件的刚度分为整体变形刚度和表面变形刚度。
前者是零件整体在载荷作用下发生的伸长﹑缩短﹑挠曲﹑扭转等弹性变形的程度;
后者是指因两零件接触表面上的微观凸峰,在外载荷作用下发生变形所导致的两零件相对位置变化的程度。
原则上说,为了提高零件的整体刚度,可采用增大零件截面尺寸或截面的惯性矩;
缩短支承跨矩或采用多支点结构,以减小挠曲变形等。
为了提高接触刚度,可采取增大接触面以降低压力;
采用精加工以降低表面不平度等。
(3)寿命
有的零件在工作初期虽然能够满足各种要求,但在工作一定时间后,却可能由于某种原因而失效。
这个零件正常工作延续的时间就叫做零件的寿命。
影响零件寿命的主要因素有:
材料的疲劳,材料的腐蚀以及相对运动零件接触表面的磨损等三个方面。
零件处于腐蚀性介质中工作时,就有可能使材料遭受腐蚀。
对于这些零件,应当选用耐腐蚀材料或采用各种防腐蚀的表面保护,例如发蓝﹑表面镀层﹑喷涂漆膜及表面阳极化处理等,以提高零件的耐腐蚀性能。
2.结构工艺性原则
零件具有良好的结构工艺性,是指在生产条件下,能够方便而经济地生产出来,并便于装配成机器这一特性。
所以,零件的结构关于性应当从毛坯制造﹑机械加工过程及装配几个生产环节加以综和考虑。
工艺性是和机器生产批量大小及具体的生产条件相关的。
为了改善零件的工艺性,就应当熟悉当前的生产水平及条件。
对零件的结构工艺性具有决定性影响的零件结构设计,在整个设计工作中占有很大的比重因而必须予以足够的重视。
3.经济性原则
零件的经济性首先表现在零件本身的生产成本上。
设计零件时,应力求设计出耗费最少的零件。
所谓耗费,除了钱财的耗费以外,还应当包括制造时间及人工的消耗。
要降低零件的成本,首先要采用轻型的零件结构,以降低材料消耗;
采用少余量或无余量的毛坯或简化零件