防火防爆课程设计Word文档下载推荐.docx
《防火防爆课程设计Word文档下载推荐.docx》由会员分享,可在线阅读,更多相关《防火防爆课程设计Word文档下载推荐.docx(31页珍藏版)》请在冰豆网上搜索。
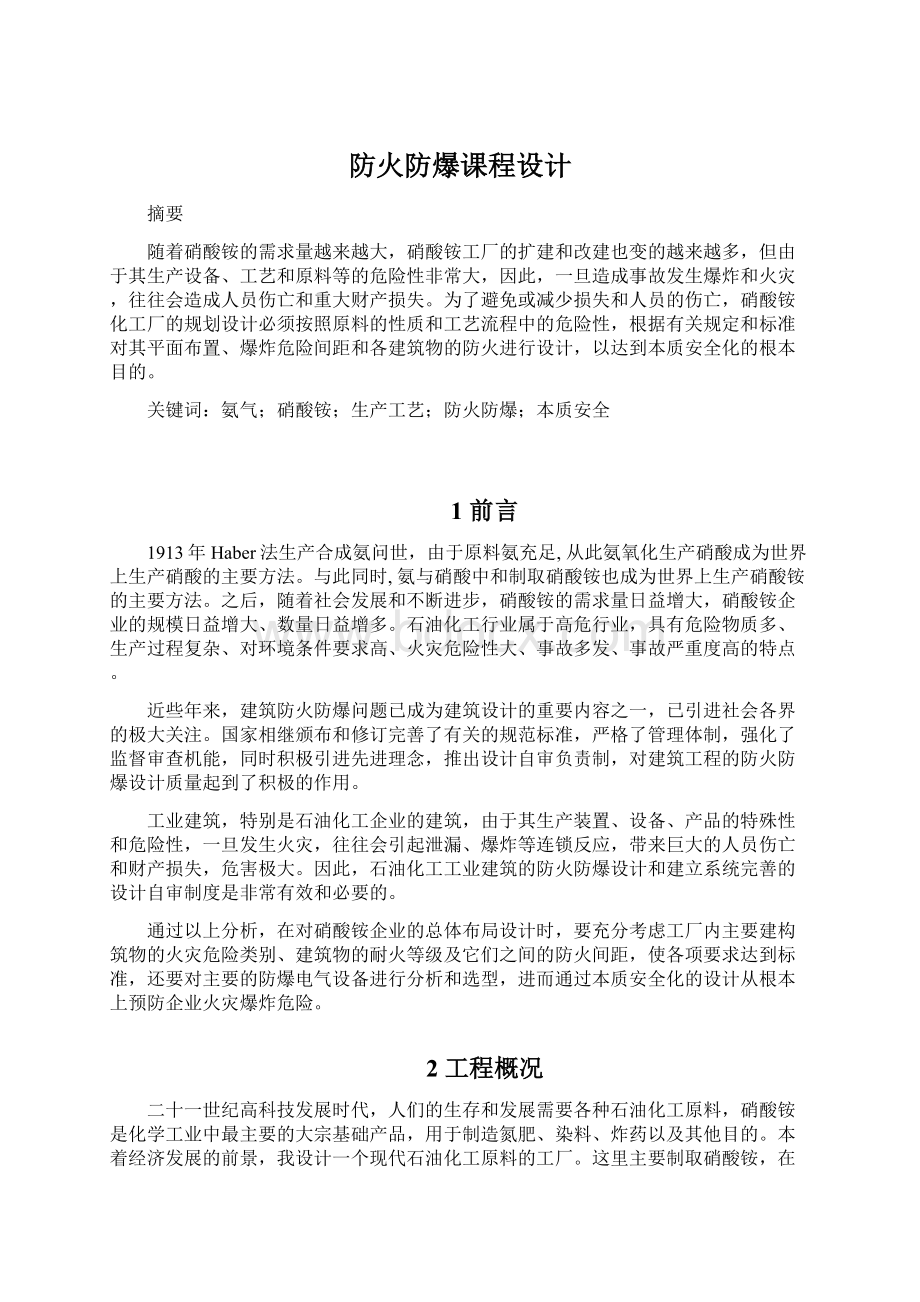
最热月出现在7月份,最热月平均气温26℃;
极端最低气温-21℃,最冷月出现在1月份,月平均气温-7.4℃。
我合理规划布局,选在附近没有居民和人群集中的场所,这样即使发生爆炸或是其他意外事故也不会造成严重的伤害同时也有利于人们的逃生使损失降到最小。
课程设计的依据主要是《石油化工企业设计防火规范》GB50160-92(1999年版)、《建筑设计防火规范》GB50016-2006、《火灾危险环境电力装置设计规范》GB50058-92、《防爆电器设计》GB50058-92、《石油化工防火防爆手册》、《化工厂工艺设计》等等。
3工程项目分析
3.1工艺流程介绍
3.1.1生产工艺简述
该装置以氨气和稀硝酸为原料,合成反应生产硝酸铵。
简要工艺流程是将稀硝酸和氨气加入中和器中合成硝酸铵,在中和器中经分离出硝酸铵溶液和蒸汽,蒸汽进入捕集器,捕集器分离出少量硝酸铵溶液和蒸汽,分离出的少量硝酸铵溶液进入再中和器中合成纯硝酸铵溶液和中和器中合成的纯硝酸铵溶液一齐进入一段蒸发器在真空中进行蒸发,这个过程的蒸发热量由捕集器中的蒸汽提供,由一段蒸发器中流出的是浓度82%的硝酸铵熔融液,熔融液再进入二段蒸发器中真空蒸发,蒸发热量由再中和器的蒸汽提供,二段蒸发出92%的硝酸铵熔融液,最后进行结晶生成成品硝酸铵,其方框流程图如图3.1所示。
稀硝酸氨气
氨气
硝酸铵
抽真空系统
图3.1硝酸铵生产工艺方框流程图
3.1.2安全防火重点部位
1.中和器
中和器底部并非100%的硝酸铵溶液,而是氨、硝酸、和硝酸铵的气液混合物,硝酸铵的浓度随硝酸铵液层高度的增加而增加,靠喷头区域内控制腐蚀的介质仍是硝酸,这样内筒底部两面均为腐蚀性介质,而厚度仅为3mm,极易使内筒承载能力降低,造成撕裂;
中和操作加减量过大、过急等都会造成事故。
此外,)在生产条件下,硝酸铵熔体和浓溶液发生爆炸分解和传爆作用是有可能的,而且危险性很大。
在这种情况下,硝酸铵分解的可能性随温度的上升而增大。
2.硝铵泵
用泵(尤其是潜孔泵)输送硝酸铵熔体的过程是非常危险的,如提高该过程的强度(将输送熔体的质量分数提高到99.7%~99.8%,温度为190℃),爆炸危险也随之增加,因为在这一条件下硝酸铵的热稳定性明显下降,而对各种因素引起爆炸性分解的敏感度却相应加。
潜孔泵在使用时的危险性一方面是由于收集槽内有大量熔体,另一方面是由于泵的运转和零件的摩擦所造成的,在泵损坏或空转压出管线不通畅以及往泵内停供熔体等情况下,泵的运转和零件的摩擦会成为硝酸铵局部强化加热的原因。
3.蒸发器
在现代大型硝酸铵生产设备中,蒸浓过程采用联合蒸发设备(经管壁加热,并带盘式热量交换部分)在热载体(200℃空气)与蒸浓溶液接触时进行。
这个过程中不仅介质温度高(180~190℃),而且还有氧存在,氧会提高硝酸铵的分解程度和对外界爆炸因素的敏感程度。
硝酸铵溶液蒸浓过程的这一温度条件与硝酸铵分解的极限温度很接近,蒸浓过程中若稍微超过硝酸铵分解的极限温度,硝酸铵便会发生危险的均相分解,并可能在极短时间内分解爆炸。
3.1.3安全工作重点
(1)原始开车时尽量降低酸浓度,通过氨时宜少宜慢,绝对不允许一次性大量通过氨,导致中和器在开车初期发生剧烈反应,使设备本体发生不平衡,剧烈震动后损坏内件;
(2)坚决避免液氨进入中和器,发生急剧放热反应,引起内件震动过大;
(3)在生产过程中尽量避免一次加减量过大、过猛,每次操作都要少量、缓慢进行,精调、细调,尽量保持平稳过渡;
(4)在生产中应该考虑高温熔体在设备内停留时间,在生产条件下,185℃的熔体停留时间不应该超过1min。
在生产条件下,备有2台中和器的工艺装置往往共用2~3台蒸发设备,主要就是考虑用一段蒸发设备和二段蒸发设备,主要就是考虑减少硝酸铵在设备中的停留时间。
但是,当遇到突然停车、个别生产工序发生故障等,必须采取硝酸铵热分解的措施。
。
(5)提高检修质量,及时停车对腐蚀内件(如氨喷头)及时进行检查更换。
(1)在造粒系统过程中,必须提高输送熔体部件的可靠性和安全程度;
(2)熔体输送应使用可靠性高的泵;
(3)为减少泵沿加入和压出管线传爆的危险,泵与邻近设备之间最好用特殊的防传爆板隔离。
3.2工艺环节的划分
3.2.1生产区
硝酸铵的制造过程由中和、再中和、一段蒸发、二段蒸发和结晶五个工序组成。
将稀硝酸和气氨的中和器和再中和器设置在1车间,再分别将硝酸铵溶液的一段蒸发、二段蒸发和真空结晶过程设置在2和3车间。
各个车间的功能和规模见表3.1。
表3.1各个生产车间的功能与规模
编号
生产车间功能
长(m)
宽(m)
高(m)
面积(㎡㎡)
1
稀硝酸、氨气的中和与捕集器的提纯再中和
40
30
10
1200
2
硝酸铵溶液的蒸发提纯
3
硝酸铵的结晶
3.2.2仓储设施
为方便工厂的生产和产品管理,在厂区内设有原料储存车间和成品储存车间。
原料储存车间是为了储存生产所用原料硝酸和氨,成品储存车间是用来储存成品结晶硝酸铵。
下面对各物质的化学性质以及储存注意事项做简单介绍。
1.氨气
氨气常态为气态,属于易燃易爆气体,与空气混合易形成爆炸性混合物,因此,存储时严加密闭,储存于阴凉、通风的库房提供充分的局部排风和全面通风,避免与氧化剂、酸类、碱类接触,远离火种、热源,避免光照,包装要求密封,不可与空气接触。
应与氧化剂、酸类、碱类、食用化学品分开存放,切忌混储。
库房采用防爆型照明、通风设施。
可用钢瓶储存。
爆炸极限为15%~28%。
2.硝酸
是一种有强氧化性和强腐蚀性的无机酸,易溶于水,常温下稀溶液无色透明,浓溶液显棕色,硝酸不稳定,见光分解,在空气中可挥发,应在棕色容器中于阴暗处避光保存,严禁与还原剂接触。
3.硝酸铵
无色无臭的透明结晶或呈白色小颗粒,有潮解性,易溶于水、乙醇、丙酮和氨水,不溶于乙醚,具有刺激性,氧化剂,助燃,常温常压非常稳定,即使高温也是这样,但如果有纤维素之类的有机物存在,100℃开始分解,120℃分解显著,遇可燃物着火时,能助长火势,与可燃物粉末混合能发生激烈反应而爆炸,受强烈震动也会起爆,急剧加热时可发生爆炸,与还原剂、有机物、易燃物如硫、磷或金属粉末等混合可形成爆炸性混合物,储存于阴凉、通风的库房,远离火种、热源,应与易(可)燃物、还原剂、酸类、活性金属粉末分开存放,切忌混储。
储区应备有合适的材料收容泄漏物,禁止震动、撞击和摩擦,对环境有危害,在地下水中有蓄积作用。
根据硝酸铵的生产工艺流程要求及原料的性质和储存方式,将原料及成品划为两个储存区,根据它们的储存要求,分成以下两个储存区,成品储存车间和原料硝酸储存车间分为一个储存区,原料氨储存车间分为一个储存区,车间编号分别为7、6、5,各个建筑物功能与规格如表3.2所示。
表3.1储存车间的功能和规格
储存及成品车间的功能
面积(㎡)
4
40
1200
5
硝酸
1200
6
硝酸铵
25
750
3.2.3其他设施
为了使厂区设计更加完善,更加规范,在厂区内设置门卫室(建筑7)、食堂(建筑物8)、办公楼(建筑物9)、技术安全科(建筑物10)、科研楼(建筑物11)、消防水池(建筑物12)、职工公寓一(建筑物13)、职工公寓二(建筑物14)、浴池(建筑物15)、招待所(建筑物16)、礼堂(建筑物17)、污水处理站(建筑物18)、废气处理站(19)、水泵站(建筑物20)、锅炉房(建筑物21)、变配电站(建筑物22)。
各个建筑物的规格如表3.3所示。
表3.1其他设施的名称和规格
名称
层数
7
门卫室
10
1
50
8
食堂
30
3
900
9
办公楼
技术安全处
20
2
400
11
科研楼
600
12
消防水池
13
公寓一
1500
14
公寓二
15
浴池
800
16
招待所
17
礼堂
18
污水处理站
19
废气处理站
水泵站
21
锅炉房
22
变、配电站
4区域划分
根据《石油化工企业设计防火规范》,在进行区域规划时,应根据石油化工企业及其相邻的主导风向为北风石油化工企业的生产区,宜位于邻近城镇或居住区全年最小频率风向的上风侧,以便生产过程中的废气及时排除和扩散,以减少对本企业和邻近企业和居民的环境影响。
第3.1.1条
在进行区域规划时,应根据石油化工企业及其相邻的工厂或设施的特点和火灾危险性,结合地形,风向等条件,合理布置。
第3.1.2条
石油化工企业的生产区,宜位于邻近城镇或居住区全年最小频率风向的上风侧。
第3.1.3条
在山区或丘陵地区,石油化工企业的生产区应避免布置在窝风地带。
第3.1.4条
石油化工企业的生产区沿江河岸布置时,宜位于邻近江河的城镇、重要桥梁、大型锚地、船厂等重要建筑物或构筑物的下游。
第3.1.5条
石油化工企业的液化烃或可燃液体的罐区邻近江河、海岸布置时,应采取防止泄漏的可燃液体液入水域的措施。
第3.1.6条
公路和地区架空电力线路,严禁穿越生产区。
区域排洪沟不宜通过厂区。
第3.1.7条
石油化工企业与相邻工厂或设施的防火间距,不应小于表3.1.7的规定。
5总平面的布置
5.1分区布置
工厂建立在辽宁省锦州市的锦州港,常年风向为东南风,强风向为南风,次强风东南风,因此,根据工厂生产生活的要求,充分考虑人身财产安全和火灾爆炸危险等多方面因素,把整个工厂划分为4个大区,西南部属于下风向,因此将生产区放在这个位置,东南为上风向,将生活区建设在厂区东部,将储存区放置在工厂的中部,西北方向为附属设施区。
生产区分为生产车间1、生产车间2、生产车间3、储存库3;
储存区主要有储存库1和储存库2;
生活区,分别有职工公寓一、职工公寓二、浴池、招待所、技术安全科、办公楼、科研楼和礼堂;
附属设施区包括消防水池、变配电站、水泵站、污水处理站、废气处理站、门卫室和锅炉房。
5.2火灾危险类别的确定
5.2.1硝酸铵及生产原料的理化性质简介
是一种无色气体,有强烈的刺激性气味,极易溶于水,常温常压下1体积水可溶解700倍体积氨,常温常压下爆炸极限为15~28%,自燃点651℃,可燃,氨气遇火星会引起爆炸危险,有油类存在时更增加燃烧危险,有一定毒性和腐蚀性,火灾危险类别为乙类。
是一种有强氧化性和强腐蚀性的无机酸,易溶于水,常温下稀溶液无色透明,浓溶液显棕色,硝酸不稳定,见光分解,在空气中可挥发,火灾危险类别为乙类。
无色无臭的透明结晶或呈白色小颗粒,有潮解性,易溶于水、乙醇、丙酮和氨水,不溶于乙醚,具有刺激性,氧化剂,助燃,常温常压非常稳定,即使高温也是这样,但如果有纤维素之类的有机物存在,100℃开始分解,120℃分解显著,遇可燃物着火时,能助长火势,与可燃物粉末混合能发生激烈反应而爆炸,受强烈震动也会起爆,急剧加热时可发生爆炸,与还原剂、有机物、易燃物如硫、磷或金属粉末等混合可形成爆炸性混合物,储存于阴凉、通风的库房,远离火种、热源,应与易(可)燃物、还原剂、酸类、活性金属粉末分开存放,切忌混储,火灾危险类别为甲类。
5.2.2生产工艺火灾危险分类
根据《建筑设计防火规范》表3.1.1(见附录中表A1生产的火灾危险性划分)可知硝酸铵的生产工艺为甲类生产,理由如下:
在生产几乎整个过程中都有硝酸、氨气和硝酸铵,硝酸和氨气属于乙类物质,硝酸铵属于甲类物质,因此,为了提高安全性,将火灾危险性提高到甲类。
5.2.3存储区火灾危险分类
根据《建筑设计防火规范》表3.1.1(见附录中表A2贮存物品火灾危险性划分)有:
1.氨气常温常压下爆炸极限为15~28%,大于10%,因此氨气库的火灾危险性为乙类;
2.硝酸是不属于甲类的氧化剂,因此,硝酸库的火灾危险性为乙类;
3.硝酸铵具有受撞击、摩擦或与氧化剂、有机物接触时能引起燃烧或爆炸的性质,而且是遇酸、受热、撞击、摩擦以及遇有机物或硫磺等易燃的无机物,以及极易引起燃烧或爆炸的强氧化剂,因此,硝酸铵库的火灾危险性为甲类。
5.3耐火等级的确定
5.3.1生产区
根据生产区厂房的火灾危险类别,依据《建筑设计防火规范》第3.2.1条表3.2.1(见附录中表A3厂房的耐火等级及厂房面积)确定各厂房的耐火等级及厂房面积。
本次设计厂房全为单层厂房,1至3号生产车间火灾危险类别都为甲类,选择耐火等级为一级,厂房面积均为1200㎡。
5.3.2储存区
根据库房的火灾危险类别,依据《防火与防爆》书中表4-7(见附录一中表A4库房的耐火等级、层数和占地面积)库房的耐火等级、层数和占地面积确定各库房的耐火等级及库房择耐火等级均为一级,库房一和库房二面积为1200㎡、库房三面积为750㎡。
综上所述,生产区、存储区各建筑物的火灾危险类别与耐火等级如表5.1所示。
5.3.3生活区
根据《建筑设计防火规范》,生活区的建筑可以依据民用建筑确定耐火等级和面积(见附录一中表A5民用建筑确定耐火等级和面积)。
办公楼、食堂、浴池、技术安全科、礼堂、公寓、招待所、消防水池,确定耐火等级均为三级,面积分别为食堂—900㎡、招待所—900㎡、办公楼—600㎡、浴池—800㎡、科研楼—600㎡、技术安全科—400㎡、礼堂—600㎡、公寓一和公寓二—1500㎡、消防水池—400㎡。
表5.1化工厂内各个建筑物的火灾危险类别、耐火等级、层数、面积
项目
类别
建筑物名称
火灾危
险类别
耐火
等级
面积(m2)
生
产
区
生产车间1
甲类
一级
单层
生产车间2
生产车间3
成品库
750
存
储
储存库1
乙类
储存库2
活
三级
三层
四层
技术安全科
四级
二层
二级
五层
附属
设备
5.3.4附属设施区
根据《建筑设计防火规范》规定:
锅炉的蒸发量小于等于4t/h的燃煤锅炉房课采用三级耐火等级的建筑外,其它锅炉房均采用一级、二级耐火等级的建筑,所以设计的这个锅炉房可选用二级耐火等级的。
消防水池因为是露天的,不考虑它的耐火等级,面积为400㎡。
规范规定油浸变压器室、高压配电装置室的耐火等级不应低于二级,所以变、换电站可选用二级耐火等级的建筑,门卫室采用三级。
结合以上所述,化工厂内各个建筑物的火灾危险类别、耐火等级、层数、面积见表5.1所示。
5.4防火间距
5.4.1防火间距设计原则
本次设计各建构筑物之间的防火间距的设计主要根据《石油化工企业设计防火规范》表3.2.11石油化工企业总平面布置的防火间距,除另有规定外,不应小于表3.2.11的规定。
工艺装置或设施(罐组除外)之间的防火距离,应按相邻最近的设备、建筑物或构筑物确定,其防火间距起止点应符合本规范附录六的规定。
高架火炬的防火距离,应经辐射热计算确定;
对可能携带可燃液体的高架火炬的防火距离,并不应小于表3.2.11的规定,并且只考虑邻近建构筑物只的防火间距。
第3.2.1条工厂总平面,应根据工厂的生产流程及各组成部分的生产特点和火灾危险性,结合地形、风向等条件,按功能分区集中布置。
第3.2.7条全厂性的高架火炬,宜位于生产区全年最小频率风向的上风侧。
污水处理场的隔油池加盖,且设有半固定式灭火蒸汽系统时,其防火距离可减少25%;
生产区和存储区主要考虑厂房和库房的火灾危险类别,该工厂的生产区内只有甲类厂房。
可以看作丙类设施,它与变电站之间的防火间距应符合丙类设施与全厂重要性设施之间的防火间距。
每个分区内各建构筑物之间的防火间距确定以后,要对分区之间的各建构筑物之间的防火间距进行确定。
本次设计主要考虑全厂重要性设施与甲类厂房、库房之间的防火间距要求,根据规范应为35m。
5.4.2防火间距的确定
依据以上原则,再考虑工厂整体布局的整齐美观,工厂内各建构筑物之间的防火确定见表D1。
所有建构筑物的面积及它们之间的防火间距,再综合考虑总体布置及甲类厂房和库房与厂区围墙和厂内主要、次要道路之间的距离,对工厂总平面布置见详图。
6防爆电气的设计
6.1划分爆炸危险区域
本次设计选择3号车间进行爆炸危险区域划分,该车间的主要释放源是氨气,根据氨气的性质,在生产过程中氨气与空气混合易形成爆炸性气体混合物。
依据《防爆电气设计规范》对生产环境进行爆炸危险分区,根据本规范2.2.3条可知该区域存在的释放源为第二级释放源。
根据规范2.2.5爆炸危险区域的划分应按释放源级别和通风条件确定,存在第二级释放源的区域可划为1区.
6.2防爆电气选择
6.2.1爆炸性混合物分级、分组
根据《防爆电器设计规范》气体或蒸汽爆炸性混合物分级、分组。
可知氨气为ⅡA和T1组,按危险程度较高的级别ⅡA和组别T1选用防爆电气设备。
综上所述,该厂房的防爆电气类型应选择ⅡA级T1组,具体规格根据爆炸和火灾危险环境电力装置设计规范第2.5.3条厂区内主要防爆电器根据(附录Ⅱ)要求进行选。
6.2.2防爆电气选择
根据《爆炸和火灾危险环境电力装置设计》规范第2.5.2条规定如下:
爆炸危险区域的分区、电气设备的种类和防爆结构的要求,应选择相应的电气设备;
所选用的防爆电气设备的级别和组别,不应低于该爆炸性气体环境内爆炸性气体混合物的级别和组别,当存在有两种以上易燃性物质形成的爆炸性气体混合物时,应按危险程度较高的级别和组别选用防爆电气设备;
爆炸危险区域内的电气设备,应符合周围环境内化学的、机械的、热的、霉菌以及风沙等不同环境条件对电气设备的要求。