轻型货车离合器的设计说明书docWord下载.docx
《轻型货车离合器的设计说明书docWord下载.docx》由会员分享,可在线阅读,更多相关《轻型货车离合器的设计说明书docWord下载.docx(24页珍藏版)》请在冰豆网上搜索。
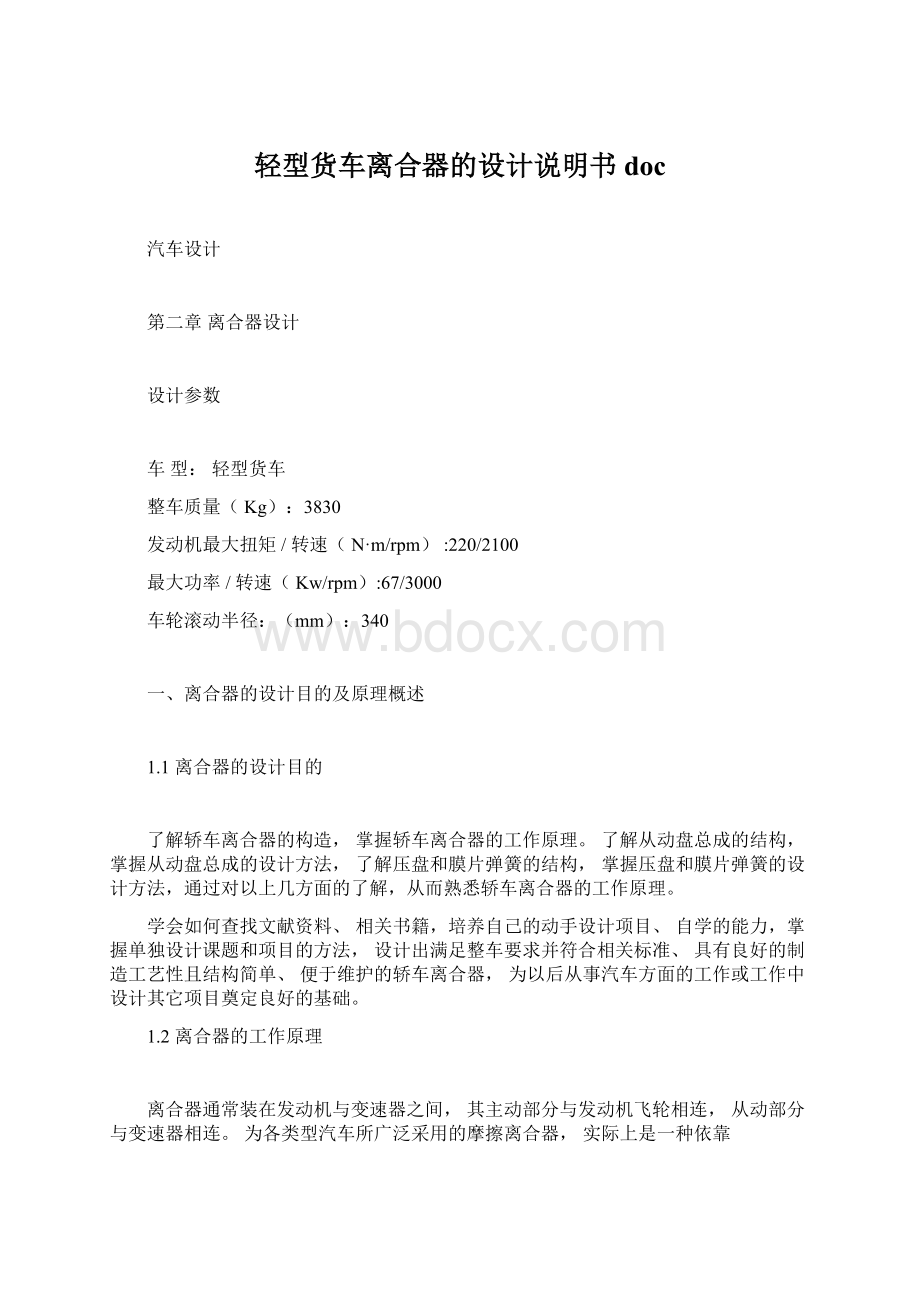
(4)由于膜片弹簧大断面环形与压盘接触,故其压力分布均匀,摩擦片磨损均匀,可提高使用寿命;
(5)易于实现良好的通风散热,使用寿命长;
(6)平衡性好;
(7)有利于大批量生产,降低制造成本。
但膜片弹簧的制造较复杂,其精度要求高,其非线性特性在生产中不易控制,
开口处容易产生裂纹,端部容易磨损。
近年来,由于材料性能提高,制造工艺和
设计方法逐步完善,膜片弹簧的制造已日趋成熟。
因此,选用膜片弹簧式离合器。
2.4膜片弹簧的支承形式
我们选用了拉式膜片弹簧,图为拉式膜片弹簧的支承形式—单支承环形式,
将膜片弹簧大端支承在离合器盖中的支承环上。
2.5压盘的驱动方式
在膜片弹簧离合器中,扭矩从离合器盖传递到压盘的方法有三种:
1)凸台—窗孔式:
它是将压盘的背面凸起部分嵌入在离合器盖上的窗孔内,
通过二者的配合,将扭矩从离合器盖传到压盘上,此方式结构简单,应用较多;
缺点:
压盘上凸台在传动过程中存在滑动摩擦,因而接触部分容易产生分离不彻
底。
2)径向传动驱动式:
这种方式使用弹簧刚制的径向片将离合器盖和压盘连
接在一起,此传动的方式较上一种在结构上稍显复杂一些,但它没有相对滑动部
分,因而不存在磨损,同时踏板力也需要的小一些,操纵方便;
另外,工作时压
盘和离合器盖径向相对位置不发生变化,因此离合器盖等旋转物件不会失去平衡
而产生异常振动和噪声。
3)径向传动片驱动方式:
它用弹簧钢制的传动片将压盘与离合器盖连接在一起,除传动片的布置方向是沿压盘的弦向布置外,其他的结构特征都与径向传动驱动方式相同。
经比较,我选择径向传动驱动方式。
三、离合器主要参数的选择
3.1后备系数β
后备系数保证了离合器能可靠地传递发动机扭矩,同时它有助于减少汽车起步时的滑磨,提高了离合器的使用寿命。
但为了离合器的尺寸不致过大,减少传递系的过载,使操纵轻便等,后备系数又不宜过大。
由于所设计的离合器为膜片弹簧离合器,在使用过程中其摩擦片的磨损工作压力几乎不会变小(开始时还有些增加),轻型货车是在城乡间公路运输,使用条件较好,宜取小值,由《汽车设计》书表2-1,初取β=1.4。
3.2单位压力P0
单位压力P0决定了摩擦表面的耐磨性,对离合器工作性能和使用寿命有很大
影响,选取时应考虑离合器的工作条件、发动机后备功率的大小、摩擦片尺寸、
材料及其质量和后备系数等因素。
P0取值范围见表:
摩擦片材料
单位压力p0/Mpa
模压
0.15~0.25
石棉基材料
0.25~0.35
编织
铜基
0.35~0.50
粉末冶金材料
铁基
金属陶瓷材料
0.70~1.50
摩擦片材料选择石棉基材料,模压制造取
P0=0.2Mpa。
3.3摩擦片外径D内径d和厚度b
摩擦片外径D(mm)可以根据发动机最大转矩Temax(N.m)按如下经验公式
选用
DKDTemax16.5220
245mm
KD为直径系数由《汽车设计》书表
2-3选取为16.5
Temax为发动机最大转矩Temax220Nm
离合器摩擦片尺寸系列和参数表
1
外径D/mm
160
180
200
225
250
280
300
325
350
380
405
430
内径d/mm
110
125
140
150
155
165
175
190
195
205
220
230
厚度b/mm
3.2
3.5
4
c=d/D
0.687
0.694
0.700
0.667
0.620
0.589
0.583
0.585
0.557
0.540
0.543
0.535
1-c3
0.676
0.657
0.703
0.762
0.796
0.802
0.800
0.827
0.843
0.840
0.847
单位面积
106
132
221
302
402
466
546
678
729
908
1037
摩擦片标准系列尺寸,取D=250mm,d=155mm,b=3.5mm,c=d/D=0.620
3.4计算校核
3.4.1单位压力P0验算
Tc
Temax
1.4
308Nm
fp0ZD3(1
d3
3)
12
D
p0
308
0.19Mpa
ZD3(1
22503(11553
f
0.26
3)
式中,f为摩擦因数取
0.26;
p0
为单位压力(MPa)Z为摩擦面数取2;
为摩擦片外径取
250mm;
d为摩擦片内径取
155mm;
计算结果与前面所选择的
单位压力P0相差不大,选择合理。
摩擦片的工作条件比较恶劣,为了保证它能长期稳定的工作,根据汽车的的使用条件,摩擦片的性能应满足以下几个方面的要求:
⑴应具有较稳定的摩擦系数,温度,单位压力和滑磨速度的变化对摩擦系数的影响小。
⑵要有足够的耐磨性,尤其在高温时应耐磨。
⑶要有足够的机械强度,尤其在高温时的机械强度应较好
⑷热稳定性要好,要求在高温时分离出的粘合剂较少,无味,不易烧焦
⑸磨合性能要好,不致刮伤飞轮及压盘等零件的表面
⑹油水对摩擦性能的影响应最小
⑺结合时应平顺而无“咬住”和“抖动”现象
由以上的要求,目前车用离合器上广泛采用石棉塑料摩擦片,是由耐热和化
学稳定性能比较好的石棉和粘合剂及其它辅助材料混合热压而成,其摩擦系数大
约在0.3左右,在该设计中选取的是石棉合成物制成的摩擦片。
3.4.2最大圆周速度vD
vD
nemaxD103
3000
250103
45m/s65~70m/s
60
m/s);
nemax为发动机最高转速取
式中,
vD为摩擦片最大圆周速度(
3000r/min;
D为摩擦片外径径取250mm;
故符合条件。
3.4.2单位摩擦面积传递的转矩Tc0
Tc0=
4Tc
d2)
41.4
0.0029
(N·
m
/mm2)
Z(D2
2(2502
1552)
式中,Tc为离合器传递的最大静摩擦力矩
Nm;
当摩擦片外径
D210~250时,[Tc0]=0.0030N·
m/mm2>
0.0029N·
m/mm2,故符合要求。
3.4.2单位摩擦面积滑磨功
为了减少汽车起步过程中离合器的滑磨,防止摩擦片表面温度过高而发生烧
伤,离合器每一次结合的单位摩擦面积滑磨功w应小于其许用值[w]。
汽车起步时离合器结合一次所产生的总滑磨功(J)为:
W=
π2ne2
marr2
)
(
22
1800
i0ig
根据公式ua
rn
0.377
i0
ig
汽车的最大爬坡度为i=16.7,将爬坡度带入公式
Pe
Gfua
Giua
CDAua
3
mua
du
3600
76140
3600dt
,式中,忽略空气阻力,=0
T
dt
将Pe
67Kw,G
9.8
37534N,滚动阻力系数f取0.02代入计算得
到一档时汽车的速度ua
18km/h
igi0
0.377rn
21.36
ua
π2ne2
marr2
3.14215002
38300.342
)=11960(J)
2
)=
i0ig
式中,W为汽车起步时离合器结合一次所产生的总滑磨功
(J);
ma为汽车总
质量取3830kg;
rr
为轮胎滚动半径,约等于静负荷半径0.34m;
ne为发动机转速
(r/min),商用车ne取1500r/min;
[w]=
4W
=
411960
=0.197J/mm2
πZ(D2
3.142(2502
式中,W为汽车起步时离合器结合一次所产生的总滑磨功取11960J
满足
w<
[w]=0.33J/mm
2要求。
摩擦片的相关参数表
摩擦片外径
摩擦片内径
d
后备系数β
厚度
b
单位压力
Po
250mm
155mm
0.20MPa
四、膜片弹簧的设计
4.1膜片弹簧的基本参数的选择
4.1.1截锥高度H与板厚h比值H和板厚h的选择h
H
为了保证离合器压紧力变化不大和操纵轻便,汽车离合器用膜片弹簧的h
一般为1.5~2.0,板厚h为2~4mm
故初选h=2mm,h=1.7则H=1.6h=3.4mm.
4.1.2自由状态下碟簧部分大端
R、小端r的选择和R比值
r
当d
0.6时,摩擦片平均半径Rc=D
d250155
101.25(mm),
对于拉式膜片弹簧的R值,应满足关系
RRc=101.25mm,故取R=105,再结
合实际情况取R/r=1.25,则r=84m。
4.1.3膜片弹簧起始圆锥底角的选择
=arctanH/(R-r)=arctan3.4/(105-84)≈10.3°
,满足9°
~15°
的范围。
4.1.4分离指数目n的选取
分离指数目n常取18,大尺寸膜片弹簧可取24,小尺寸膜片弹簧可取12。
取分离之数目n=18。
4.1.5膜片弹簧最小端内半径r0及分离轴承作用半径rf
r0
由离合器的结构决定,其最小值应大于变速器第一轴花键的外径。
f应该
大于r0。
4.1.6切槽宽度δ1、δ2及半径re
取δ1=3.4mm,δ2=10mm,re满足r-re>
=δ2,则re<
=r-δ2=84-10=74mm
故取re=74mm。
4.1.7压盘加载点半径R1和支承环加载点半径r1的确定
R1和r1需满足下列条件:
1RR17,0r1r6
故选择R1=100mm,r1=88mm.
4.1.8膜片弹簧材料
制造膜片弹簧用的材料,应具有高的弹性极限和屈服极限,高的静力强度及疲劳强度,高的冲击强度,同时应具有足够大的塑性变形性能。
按上述要求,国内常用的膜片弹簧材料为硅锰钢60Si2MnA或50CrVA。
4.2膜片弹簧的弹性特性曲线
假设膜片弹簧在承载过程中,其子午线刚性地绕上地某中性点转动。
设通过支承环和压盘加载膜片弹簧上地载荷P1(N)集中在支承点处,加载点
间的相对轴向变形为x1(mm),则膜片弹簧的弹性特性如下式表示:
Ehx1
ln(R/r)
R
x1R
h
P1f(x1)
(R1r1)
2(Hx1
R1
)(H
2R1
6(1
r1
式中,E――弹性模量,钢材料取E=2.06×
105Mpa;
b――泊松比,钢材料取b=0.3;
R――自由状态下碟簧部分大端半径,mm;
r――自由状态下碟簧部分小端半径,mm;
R1――压盘加载点半径,mm;
r1――支承环加载点半径,mm;
H――自由状态下碟簧部分内截锥高度,mm;
h――膜片弹簧钢板厚度,mm。
弹性特性曲线图:
膜片弹簧弹性特性
3500
2500
N
/
F2000
力
压
作1500
工
1000
500
5
6
变形λ1/mm
膜片弹簧的相关参表
截锥高度H
板厚h
分离指数n
圆底锥角
3.4mm
2mm
18
10°
五、扭转减振器的设计
扭转减振器主要由弹性元件(减振弹簧或橡胶)和阻尼元件(阻尼片)等组
成。
弹性元件的主要作用是降低传动系的首端扭转刚度,改变系统的固有振型,尽可能避开由发动机转矩主谐量激励引起的共振。
阻尼元件的主要作用是有效地耗散振动能量。
5.1扭转减振器主要参数
目前,在柴油机汽车中广泛采用具有怠速级的两级或三级非线性扭转减振
器。
三级非线性减振器的扭转特性如下图所示。
5.1.1极限转矩Tj
极限转矩受限于减振弹簧的许用应力等因素,与发动机最大转矩有关,一般
可取
Tj(1.5~2.0)Temax
对于商用车,系数取1.5,计算得Tj1.5Temax1.5220330Nm
5.1.2扭转角刚度K
由经验公式初选K13Tj
K13Tj133304290Nm/rad
5.1.3阻尼摩擦转矩T
可按公式初选
T(0.06~0.17)Temax
取T0.1Temax0.122022Nm
5.1.4预紧转矩Tn
减振弹簧在安装时都有一定的预紧。
Tn满足以下关系:
Tn(0.05~0.15)Temax且Tn
T22Nm
而Tn(0.05~0.15)Temax
11~33Nm
则初选Tn17.6Nm
5.1.5减振弹簧的位置半径R0
R0的尺寸应尽可能大些,一般取
R0=(0.60~0.75)d/2
则取R0=0.7d/2=0.7×
155/2=54.25(mm),可取为55mm.
5.1.6减振弹簧个数Zj
当摩擦片外径D250mm时,
Zj=4~6
故取Zj=6
5.1.7减振弹簧总压力F
当减振弹簧传递的转矩达到最大值Tj时,减振弹簧受到的压力F为
FTj/R0330/(5510-3)6082.9N
5.2减振弹簧的计算
在初步选定减振器的主要参数以后,即可根据布置上的可能来确定和减振器
设计相关的尺寸。
5.2.1减振弹簧的分布半径R1
R1的尺寸应尽可能大些,一般取
R1=(0.60~0.75)d/2
式中,d为离合器摩擦片内径
故R1=0.7d/2=0.7×
155/2=54.25(mm),即为减振器基本参数中的R0
5.2.2单个减振器的工作压力P
PF/z6082.9/61013.8N
5.2.3减振弹簧尺寸
1)弹簧中径Dc
其一般由布置结构来决定,通常
Dc=11~15mm
故取Dc=12mm
2)弹簧钢丝直径d
38PDc38776.612
d=[]=580=3.45mm
式中,扭转许用应力[]可取550~600Mpa,故取为580Mpa
d取3.5mm
3)减振弹簧刚度k
应根据已选定的减振器扭转刚度值k及其布置尺寸R1确定,即
k
4290
242.94Nm
2n
0.054252
1000R1
4)减振弹簧有效圈数i
Gd4
8.3
104
(3.5
103)
i
3k
8(12
103)3242.94
103
8Dc
5)减振弹簧总圈数n
其一般在6圈左右,与有效圈数i之间的关系为
n=i+(1.5~2)=6
6)减振弹簧最小高度
lminn(d
)1.1dn1.133.110.23mm
7)弹簧总变形量
P
1013.8
l
4.17mm
242.94
8)减振弹簧总变形量l0
l0lmin
l10.234.1714.4mm
9)减振弹簧预变形量
l'
Tn
17.6
10-3
0.2mm
kZR1
242.94654.25
10)减振弹簧安装工作高度l
ll0l'
14.4-0.214.2mm
11)从动片相对从动盘毂的最大转角
最大转角
和减振弹簧的工作变形量
'
(l'
'
ll'
)有关,其值为
2arcsin(l"
/2R1)4.19
12)限位销与从动盘毂缺口侧边的间隙
1R2sin
,式中,R2为限位销的安装尺寸。
1值一般为2.5~4mm。
所以可取
1为3mm,R2为41mm。
13)限位销直径d'
d'
按结构布置选定,一般d'
=9.5~12mm。
可取d'
为10mm
扭转减振器相关参数表
极限转矩
Tj
阻尼摩擦转矩
Tμ
预紧转矩
减振弹簧的位置半径
R0
减振弹簧个数
Zj
330N·
m
22